Thanks to everyone who entered the “Calvin Cobb: Radio Woodworker” chapter-spot contest. Some of your (wrong) answers were really funny – so I had a lot of fun going through the responses.
Two photos, numbers 7 and 24, flummoxed everyone. A few of you were close on 24 with “chisel” … but not close enough (I’m a tough grader – just ask any of my former students). No one really came close on 7, a vacuum-tube tester.
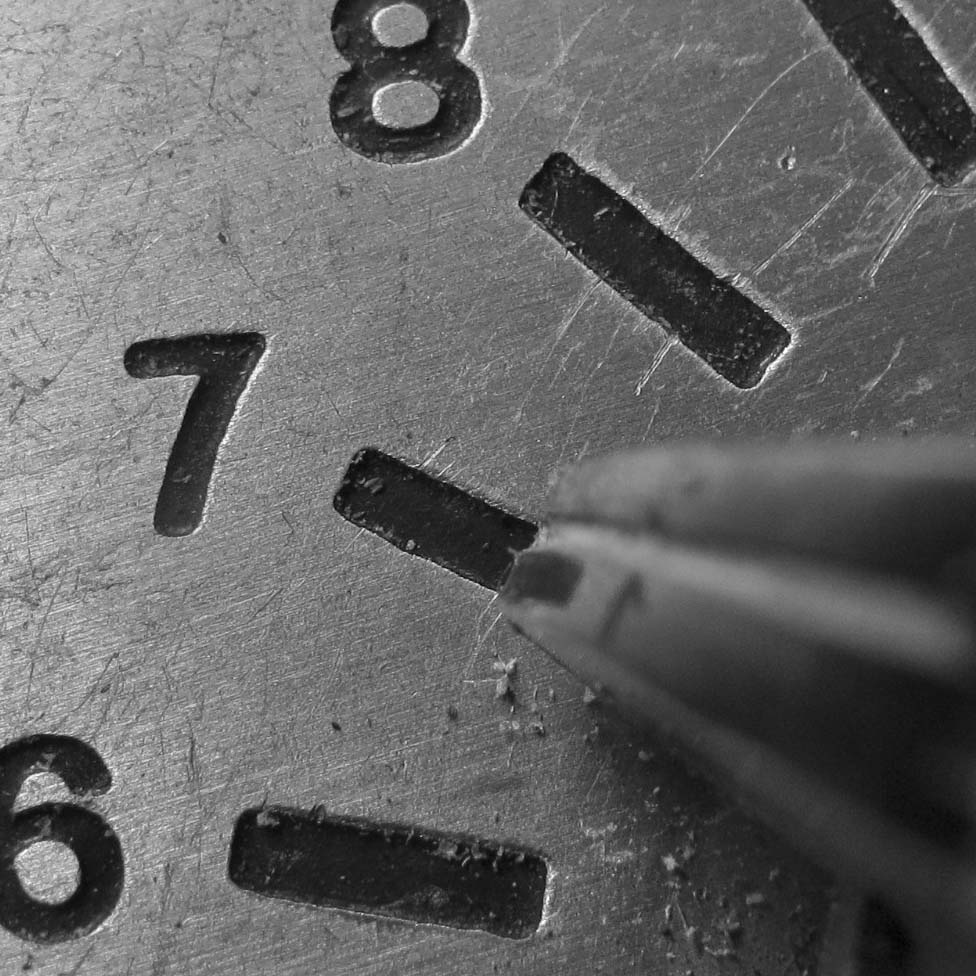
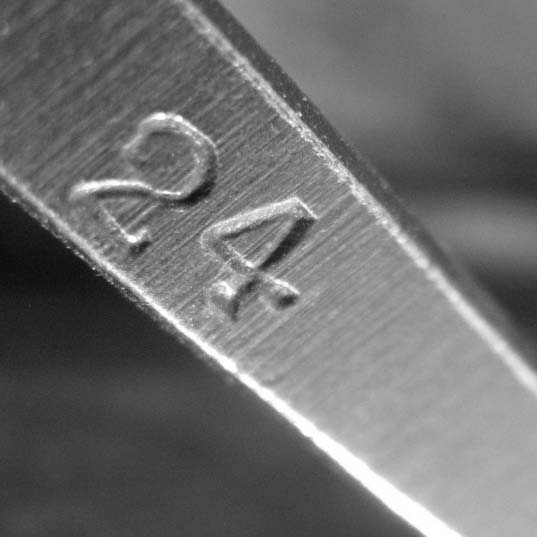
The correct answer on 24 is “carving gouge.”
It was a close finish for first place and second place…particularly because the first-place winner declined to answer 36, 37 and 38. But it didn’t hurt him in the end.
Even with skipping three of them, Stumpy Nubs had the most correct answers (30).
Congratulations, James! You win an autographed copy of Roy Underhill’s “Calvin Cobb: Radio Woodworker (A Novel with Measured Drawings),” a Lost Art Press Logo T-shirt in your choice of color and size (from available stock) and an autographed Roubo Bookstand in Walnut, made by Roy Underhill.
The second-place finisher (28 correct) is Sawdustandwoodchips, who wins an autographed copy of “Calvin Cobb: Radio Woodworker (A Novel with Measured Drawings)” and a Lost Art Press Logo T-shirt in his (I think “his” … but I don’t actually know) choice of color and size (from available stock).
For third place, there was a tie. So I resorted to giving “pluses” for hyper-correct answers to each of the entrants with 23 correct responses. Matt Rae got five pluses; lblack2x4 got four pluses…but lost one for “Rabone folding rule…because it’s a Zig-Zag.) So, Matt Rae gets an autographed copy of “Calvin Cobb: Radio Woodworker (A Novel with Measured Drawings),” and lblack2x4 gets a Lost Art Press Logo T-shirt (choice of color and size from available stock).
I have no doubt you will disagree with my grading methods – students always did. (But I beg you: Don’t have your parents call me to complain.)
If one (or more) person gave the exact correct response, answers that were vague did not get full marks (e.g. No. 1 is the exposure counter on a Robot 1 camera, which several people identified correctly, so “camera dial” alone did not make the grade).
Winners, please send your mailing address and T-shirt choice (where applicable) to: meganfitzpatrick@fuse.net. I’ll get them off to Roy and Christopher Schwarz immediately.
And remember: You’re all winners, just for playing (do you think kids really believe that?).
Below, you’ll find the key to all 38 of the chapter spots images, as provided by Roy:
1 Exposure Counter, Robot 1 camera
2 IBM Punch Card,
3 Audel’s Carpenters and Builders Guide, vol 3,
4 RCA console Radio, ca 1939
5 Shutter Speed Dial, Robot 1 camera
6 Stanley #6 Bench Plane
7 Vacuum Tube Tester, ca 1948
8 Bell Systems Pay Telephone Dial
9 Steel Zig-Zag Rule
10 Toledo Scale (drugstore model)
11 Exposure Guide, Robot 1 camera
12 Focus Ring, Robot 1 camera
13 Folding Rule
14 Exposure Counter, Robot 1 camera
15 Wurlitzer Juke Box, 1946
16 Wurlitzer Juke Box, 1941
17 Auger Bit, 17/16 inch
18 Try Square
19 Zig-Zag Rule
20 Tuning Dial, Atwater Kent Radio, ca. 1921
21 Adding Machine
22 Wurlitzer Juke Box, 1946
23 Adding Machine, Remington
24 Carving Gouge
25 Coin Slot, Bell Systems Pay Phone
26 Gearing Tables, Barnes #3 ? Screw Cutting Lathe
27 Steel Folding Rule
28 F-Stop (Iris diaphragm) Setting, Robot 1 Camera
29 Stanley Rule & Level # 29 Transitional Plane
30 Langdon Patent, Millers Falls Miter Box
31 Zig-Zag Rule
32 Post Office Box Window
33 Stamp Vending Machine
34 Two Plow Plane Irons
35 Stanley Rule & Level # 35 Transitional Plane
36 Adding Machine, Remington
37 Stanley Rule & Level # 37 Transitional Plane
38 Two Steel Number Stamps
Like this:
Like Loading...