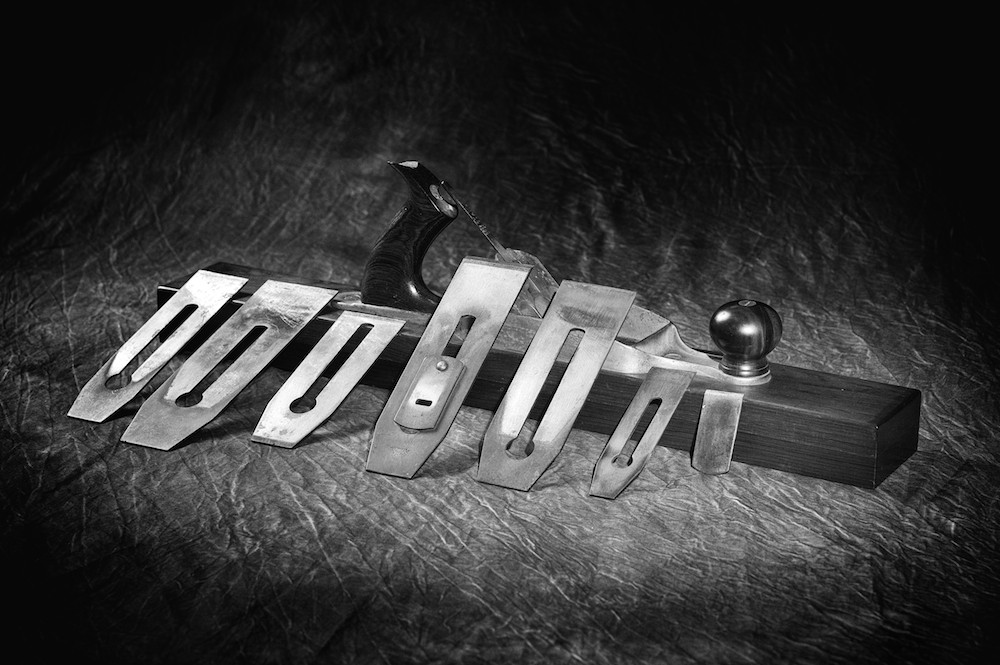
The point of this blog entry is that you can sharpen a tool in a dozen different ways – your way, my way or the way of a dead guy. In short: Don’t be a dullard.
For the last few days I have immersed myself in the cutting edges made (presumably) by H.O. Studley, a Massachusetts piano maker who created a legendary wall-hanging tool chest. His tool chest is a testament to his skill. It is flawless in almost every way, from the design to the tools’ composition to the craftsmanship of the chest itself.
So what sort of sharpener was he?
To take a stab at this question, I spent most of today looking closely at every cutting edge in the chest. From what we know about this chest, the tools have been mostly on mothballs since Studley left the trade in the early part of the 20th century. So there is a chance that the edges on the tools are actually his edges.
I looked at every edge in the chest under high magnification and compared them all to one another. I suspect Studley was the last sharpener of many of the tools based on the consistency of many of the edges, from the augers to the planes to the chisels to the marking gauges. The pattern of scratches left on the tools was quite consistent. So if I were H.O. Studley, here is what I would tell you about my sharpening regimen.
1. I like a convex bevel. Nearly all of the edges I observed had a slightly convex bevel. A couple tools had evidence of a hollow grind in the middle that was in the process of being removed by sharpening the bevel (making it convex).
2. I like cambered edges on my planes. Nearly every edge of the plane blades (blocks, smoothers, jacks and try) had a cambered cutting edge. Many of the edges were significantly relieved at the corners.
3. I sharpen the entire bevel. Only one tool had any evidence of a micro-bevel.
4. I lap the backs of my irons and chisels. All of the tools in the chest have lapped backs. The lapping is not to a mirror sheen, but there is evidence of significant and continuous work on the backs.
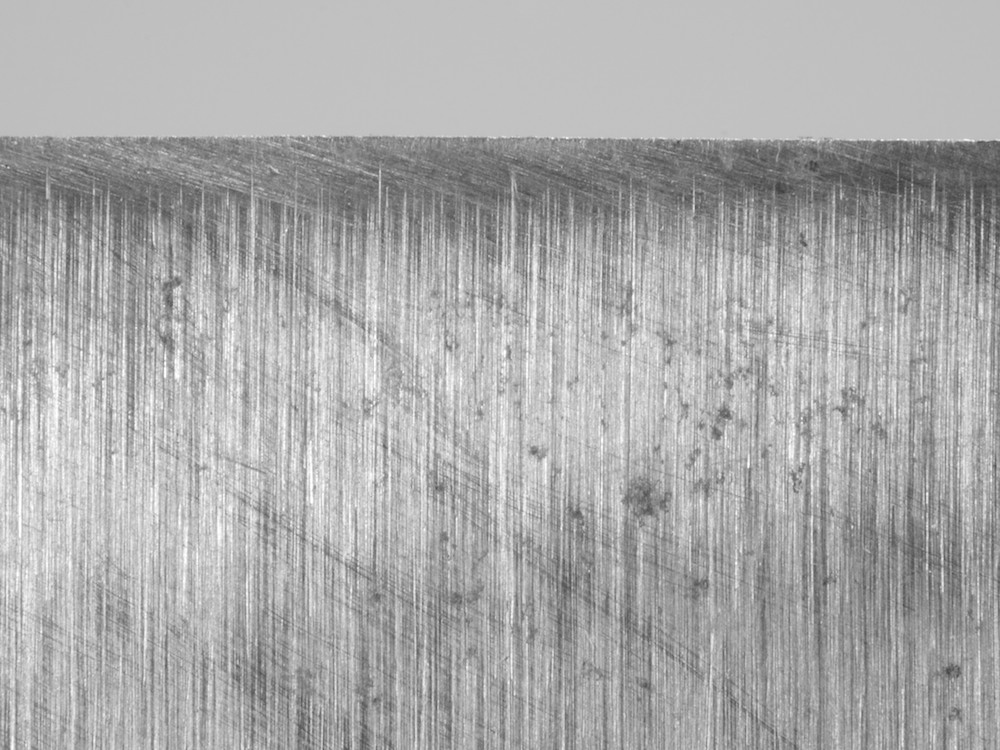
5. I lift my plane irons slightly when I polish the backs. Over and over I saw evidence that the very tip of the back was polished to a higher degree than the metal behind the tip. And (using a machinist straightedge) I could see that the tip of the back was ever-so-slightly dubbed from this polishing. The polishing on the backs was heavier on the bevel-up planes than on the bevel-down planes.
You can take the above information and twist it however you like. Studley was a hand-sharpener. He sharpened the entire bevel. He did something similar to the ruler trick – though he probably didn’t use a ruler. He knew that he needed two intersecting surfaces to create a sharp and durable edge.
Or maybe it was someone in the Studley family who knew this and sharpened all the edges in the chest. Maybe it was the family’s lawyer who acquired the chest. Maybe it was some compulsive sharpener at the Smithsonian who ran wild through the chest while it was in the care of the institution.
The truth is, we don’t know. But we can guess. And my guess is that most of these edges were from the hand of H.O. Studley. And with the help of some incredible photography technology we’re using, you’ll be able to see this for yourself when we publish the book on H.O. Studley in the next two years.
— Christopher Schwarz
Note: All the photos with this blog entry were taken by Narayan Nayar.
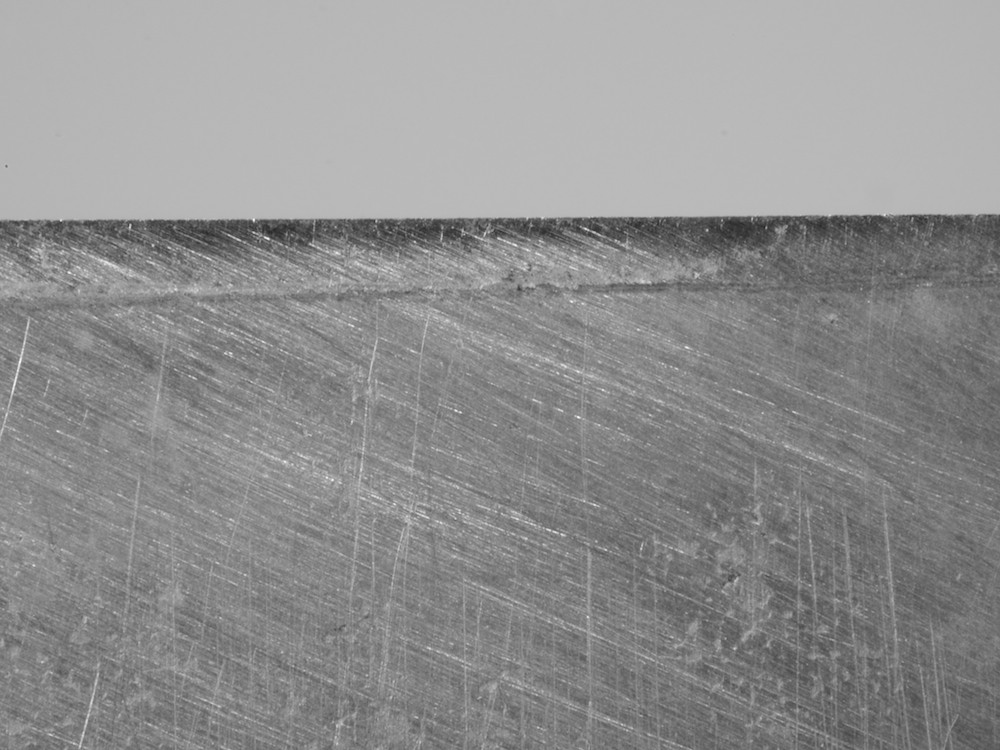
Like this:
Like Loading...