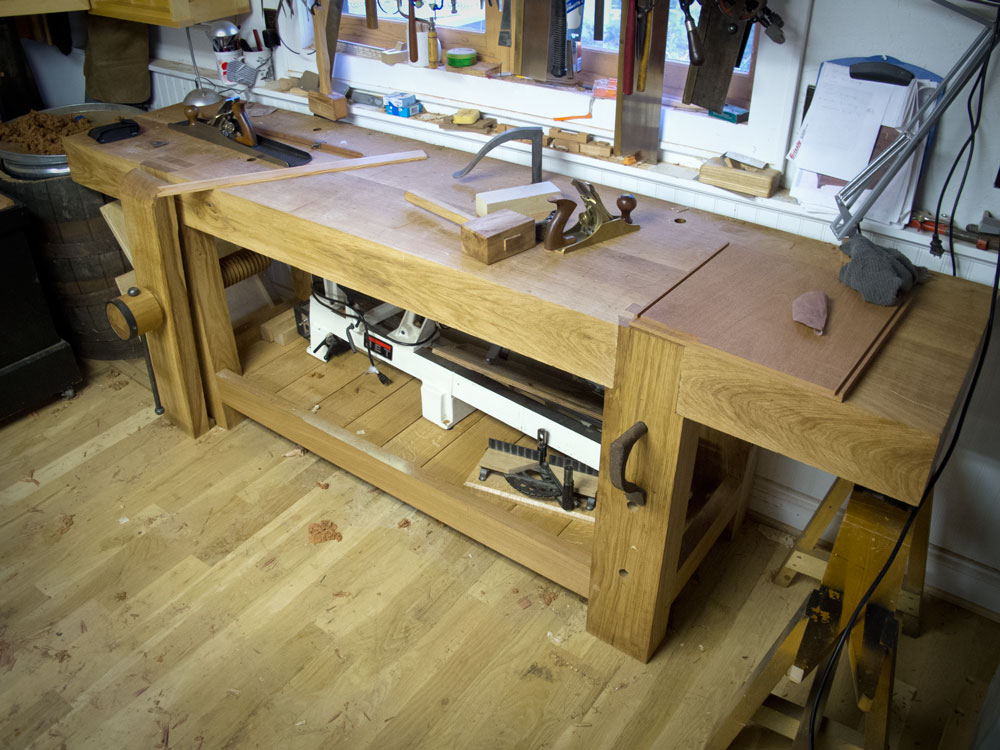
Whenever I build a workbench, I try to work with stock that is as dry as possible. But I’ve never shied away from wood at 15 percent moisture content (MC). Thick timbers can be tough to dry, and all of the benches I’ve built with slightly damp wood have turned out fine.
Turns out, I think I might be a little too conservative on moisture in workbenches.
When we built the French oak workbenches in Barnesville, Ga., this summer, we were shocked at the moisture content of the timbers. Despite the fact that the trees had been felled for more than 13 years, the numbers on the moisture meters were alarming.
My benchtop was 30 percent MC. Other benchtops were 60 percent MC, which was off the charts for our moisture meters.
But we had only one week to build these benches, and we couldn’t wait another 10 years.
My workbench is still wet by furniture standards. Most areas of the top and legs register about 15 percent MC, and my meter reads only 3/4” deep. My suspicion is the center of my 6”-thick top is much wetter. I suspect this because my holdfasts rust immediately when left overnight in a hole in the benchtop.
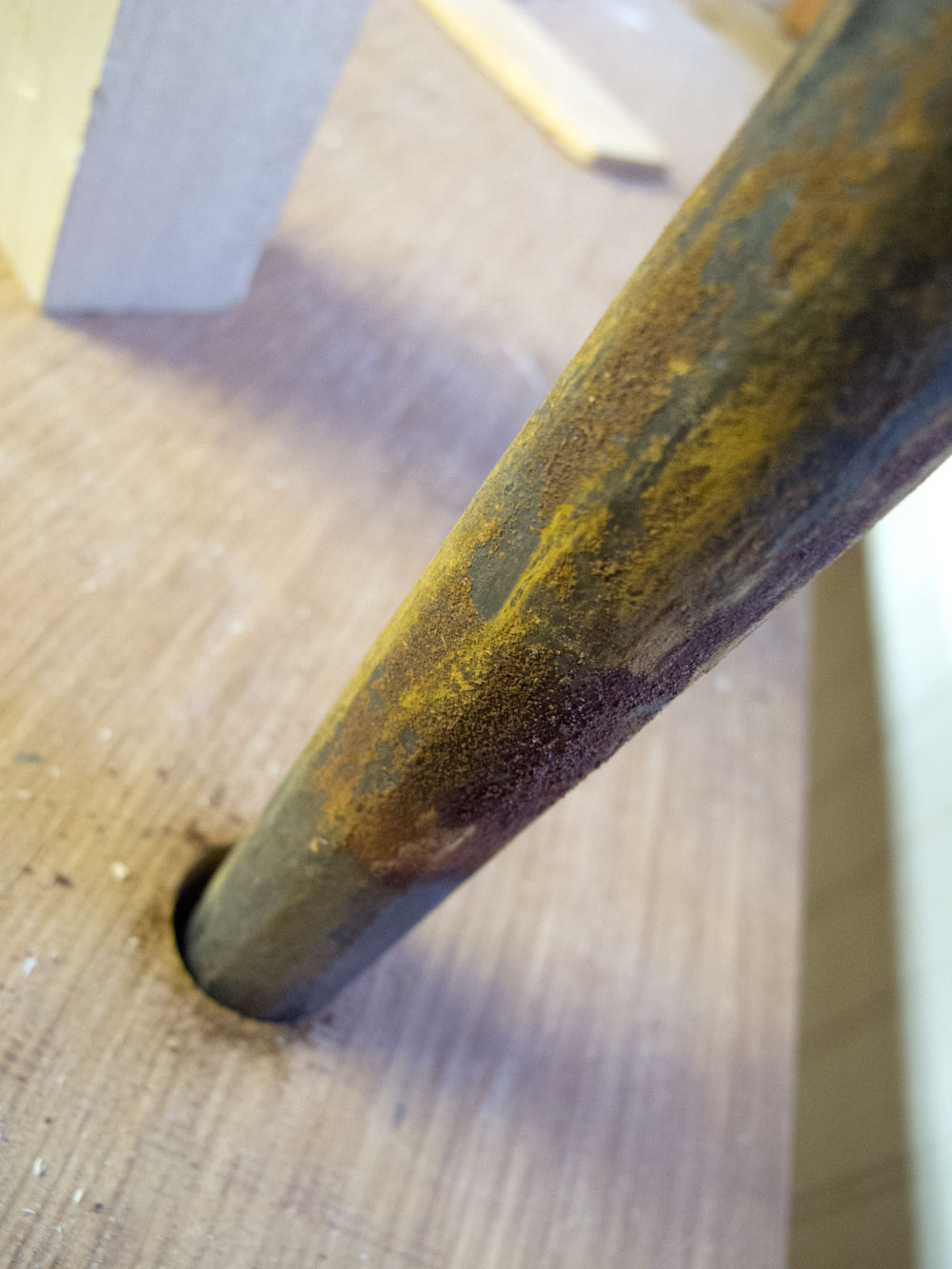
Despite all this, the top has not moved significantly enough to warrant a reflattening. Today I planed a bunch of 1/2”- and 5/8”-thick panels and it was clear the top was still in spec for this high-tolerance work.
The only evidence of shrinkage or movement in the top is at one of the four joints where the legs pierce the benchtop. While three of these joints are as perfect as the day I finished the bench, the top has shrunk about 1/32” compared to the dovetail and tenon in the front right corner.
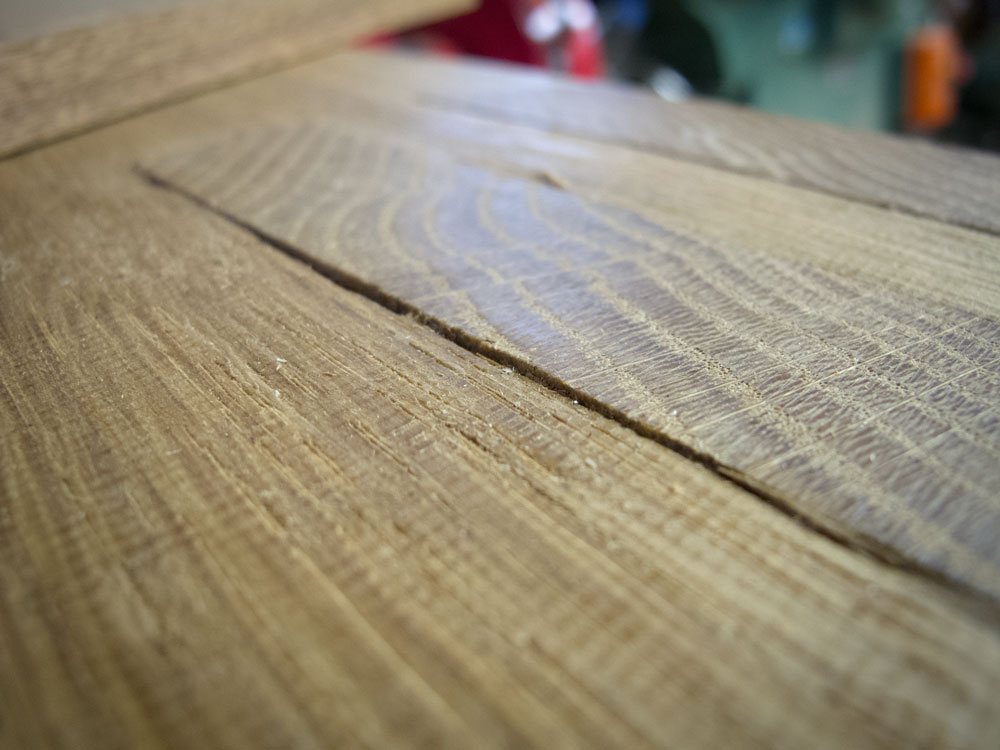
Oh, and there hasn’t been any additional checking, and the single existing check in the top hasn’t increased in length or width.
To be honest, I had experienced more wood movement on Douglas fir and cherry workbenches of the same design.
We will see how the bench fares as it makes the transition to equilibrium MC. But my suspicion is that the thick nature of the timbers and the joinery will help to make a bench that settles in gently.
— Christopher Schwarz
Like this:
Like Loading...