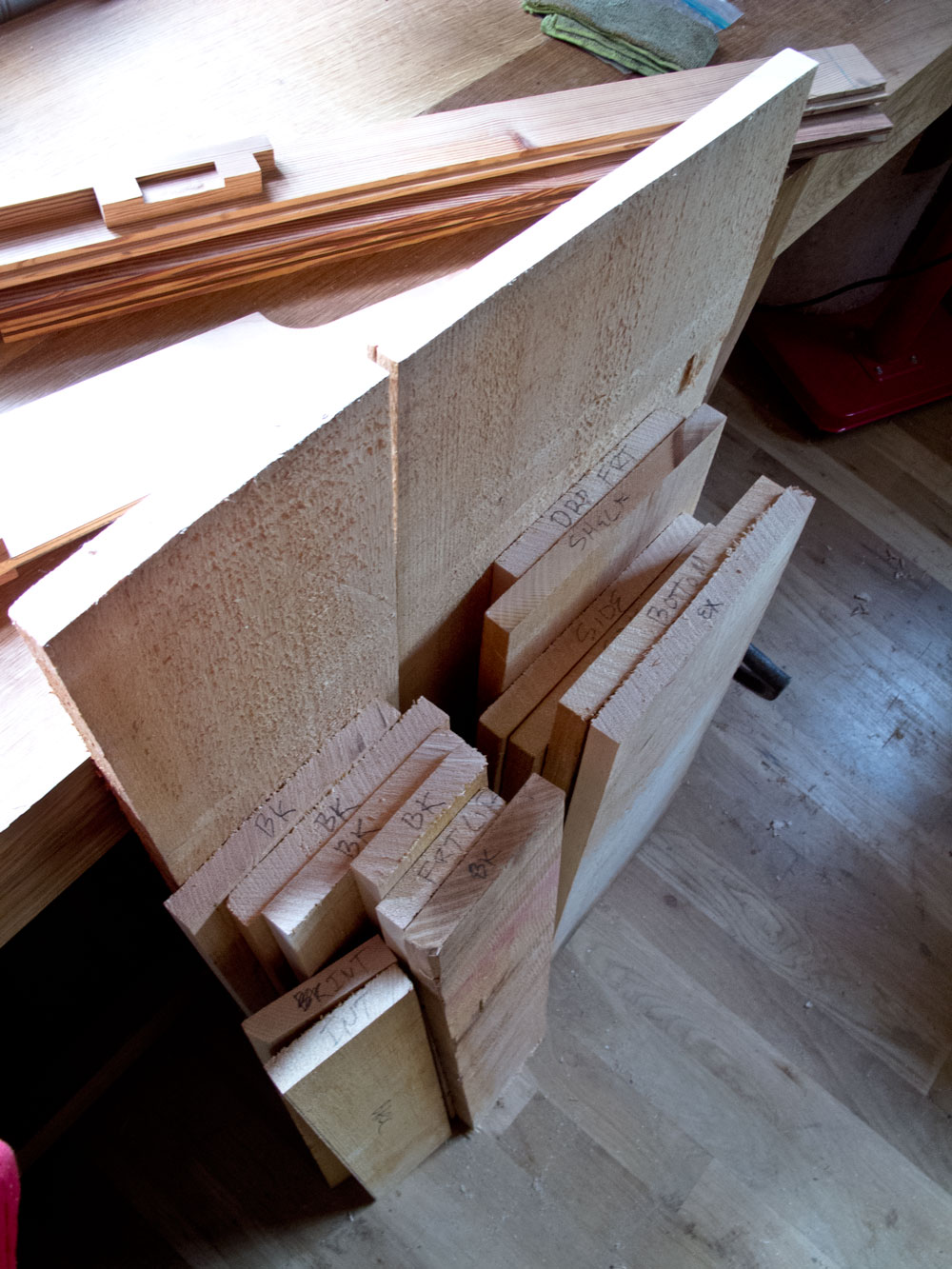
Call me sick (or call me “cute as a button”) but I enjoy breaking down rough stock with a handsaw. Part of it is necessity. I don’t have a miter saw, and many boards I work with are outside their capacity in width or thickness.
But more important than the tooling is that handsawing the stock forces me to slow down a bit and it gives me a good feel for how much moisture and tension is in each board. I’ve found some real stinkers when boards tried to pretzel my handsaw or choke it to death.
Today I broke down all the stock for another Dutch Tool Chest. I drive up to Maine on Wednesday morning for a three-pronged mission.
1. Teach a class on building the Dutch Tool Chest on July 5-6.
2. Film a DVD on building the Dutch Tool Chest with the Lie-Nielsen crew the week of July 7-10.
3. Attend the Lie-Nielsen Open House on July 11-12. Both John Hoffman and I will be there with books, T-shirts and Dutch Tool Chests. If you’ve never been to an Open House event, it’s like a huge Lie-Nielsen Hand Tool Event with factory tours (I tour the factory every time) and a lobster bake. Plus Maine is particularly nice this time of year.
Check out all the people who will be there via this link. Dang. Make your reservation for the lobster bake before July 1 (it’s just $25). The Open House is free and open to the public.
I’ll also be bringing some campaign furniture I’ve built to show off.
— Christopher Schwarz
Like this:
Like Loading...