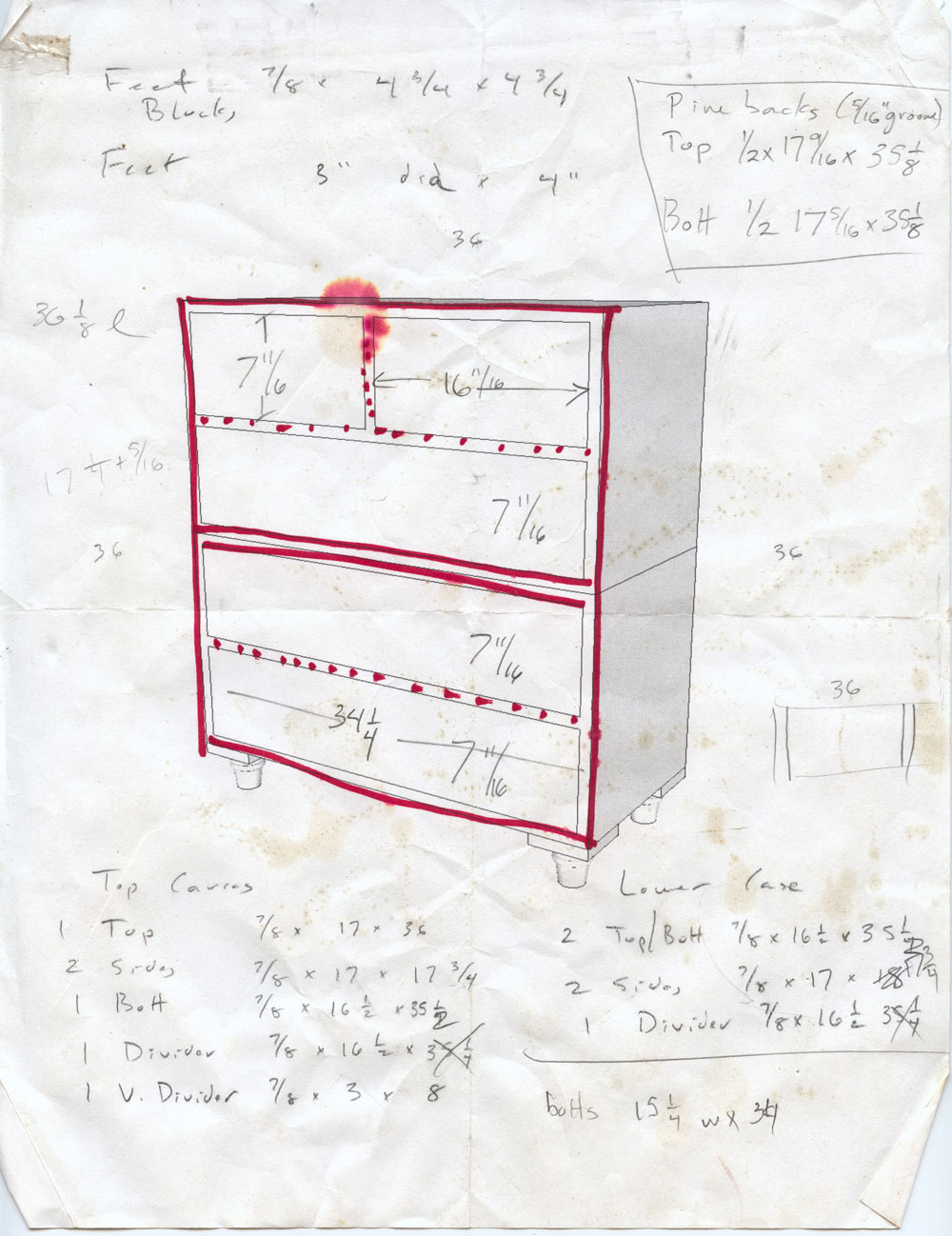
The best thing I ever learned about furniture design came from my mom while we were driving the family Suburban somewhere in the Florida panhandle.
My mom is absolutely the best cook I have ever encountered. She can do anything with nothing. She makes it all look effortless and taste amazing. She, quite frankly, opened my eyes to the possibilities of food in the way my dad introduced me to wood.
So anyway, we’re driving back to our beach rental place one summer in the 1980s, and my mom and I are talking about food. And I describe some fruit smoothie. It’s stupid, really, but it’s a fruit smoothie with some weird combination of fruits and juices.
I say: I think that would taste good.
She says: You can visulaize that?
Me: Yeah, no problem.
Mom: That’s cooking. Right there.
That moment has stuck with me for almost 30 years now, both as a cook and a furniture designer. And after much thought, I’ve concluded there are two kinds of designers: cooks and bakers.
I have always been a cook. I am interested in combining different ingredients until I gradually achieve a perfect balance when making a sauce or casserole or carcase. I taste and taste. Modify and modify. And I’m never satisfied until the very last, when I place the food on the table.
My wife, Lucy, on the other hand, is a baker. She treats ingredients like a chemist. She measures. Measures again. And makes fantastic cookies and cakes that I cannot ever hope to make. But – and this is not a criticism – her cookies always taste the same. My shrimp and grits always tastes different, depending on what’s available and my mood.
What the heck does this have to do with woodworking? Everything.
When I design furniture, I am willing to alter the details at any stage. I refuse to use a cutting list. I simply feel my way through the project, step by step. I can do this because I have a vast library of furniture books and images in my head and in my house that I use to guide me. I start with a basic recipe that is based on the material I have, the photos of similar objects I’ve culled from my library and the desires of the person I’m building the piece for.
When I build this way, I am always happy with the result.
During my years at Popular Woodworking Magazine, I tried to build things according to more of a baking paradigm. I took the print, developed a cutting list and stuck to it. At times this process worked. The baking soda was right to the granule. Other times, I felt like I was simply reproducing someone else’s mistakes.
So, bottom line, I want my mistakes to be my own.
The problem with my approach is that it’s hard (no, impossible) to teach to others. I much prefer the approach of George Walker and Jim Tolpin in “By Hand & Eye,” who teach woodworkers to develop their designer’s eye through exercise and exploration.
My approach is more like Anthony Bourdain. Eat everything. Make yourself sick again and again until you you can find the balance between beauty and botulism. Yeah, sometimes you’ll throw up on the street, but sometimes you’ll find something that can silence a room.
— Christopher Schwarz
Like this:
Like Loading...