Publisher’s note: For the release our new video “Build a Stick Chair,” I’ve written this short essay that explains one of the many reasons these chairs are first in my heart. I apologize if it sounds like I’m on a soapbox. Or, worse, that I am trying to sell you a time-share condo in Monkey’s Eyebrow, Ky. For me, encountering these chairs in the 1990s changed the way I interpret furniture. And how I choose to sell my work and make a living. I can’t promise you that these chairs will change your life, but they will keep your butt dry.
— CS
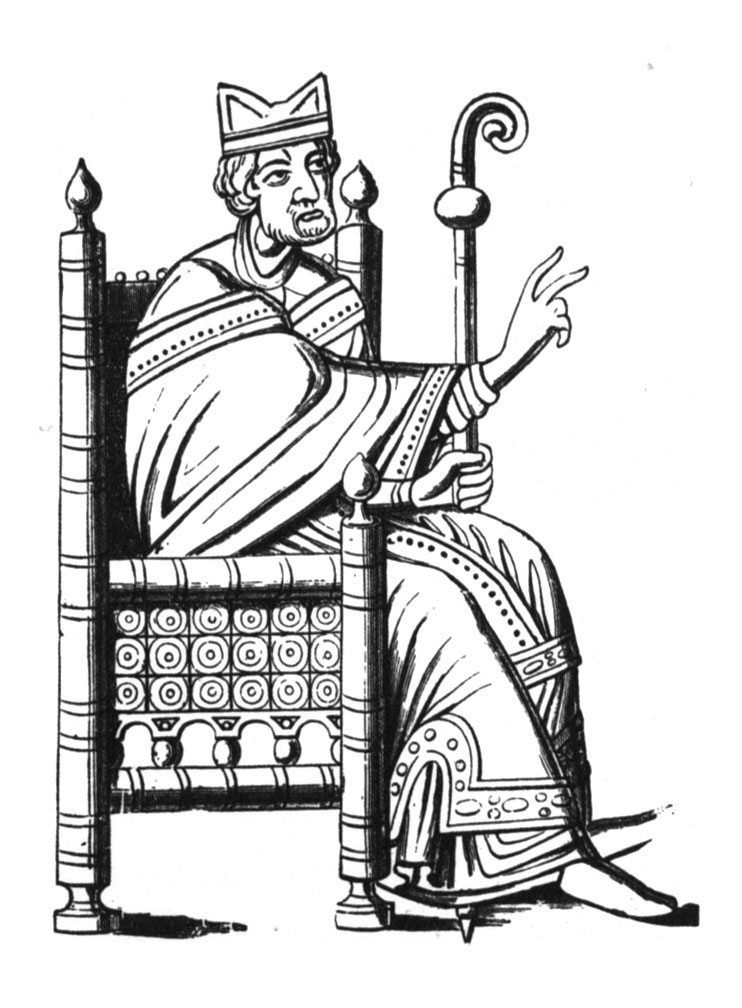
For me, the history of seating furniture reads like a history of oppressors and the people they held down.
For most of human civilization, chairs have been a symbol of authority or dominance. I can go back further in time, but let’s start with the curule – the sella curulis – which was a folding chair that literally represented the seat of power in ancient Rome. Only certain powerful people were entitled to sit on a curule. This idea – that a perch represented power – spread quickly across Europe and all the way to China by the 2nd century CE.
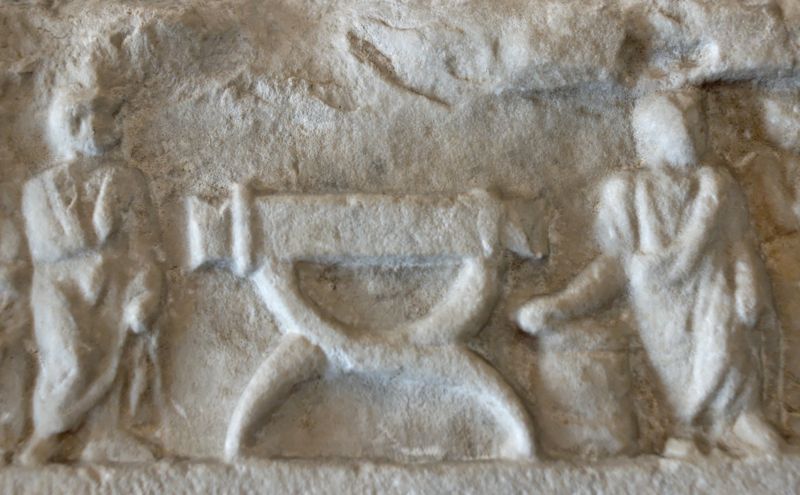
Even our language is embedded with the idea that chairs represent authority: chairman, seat of power, first chair/second chair, to get a seat at the table, to take a back seat to someone, the driver’s seat, and the catbird seat – to name a few.
Chairs weren’t just a symbol for the throne room and the royal rear ends. Before mass manufacturing made chairs cheap and plentiful, the head of the household in even the humblest home would sit in a chair, while the other members of the family sat on stools, rocks, stumps or dirt.
But we’re past that now, aren’t we?
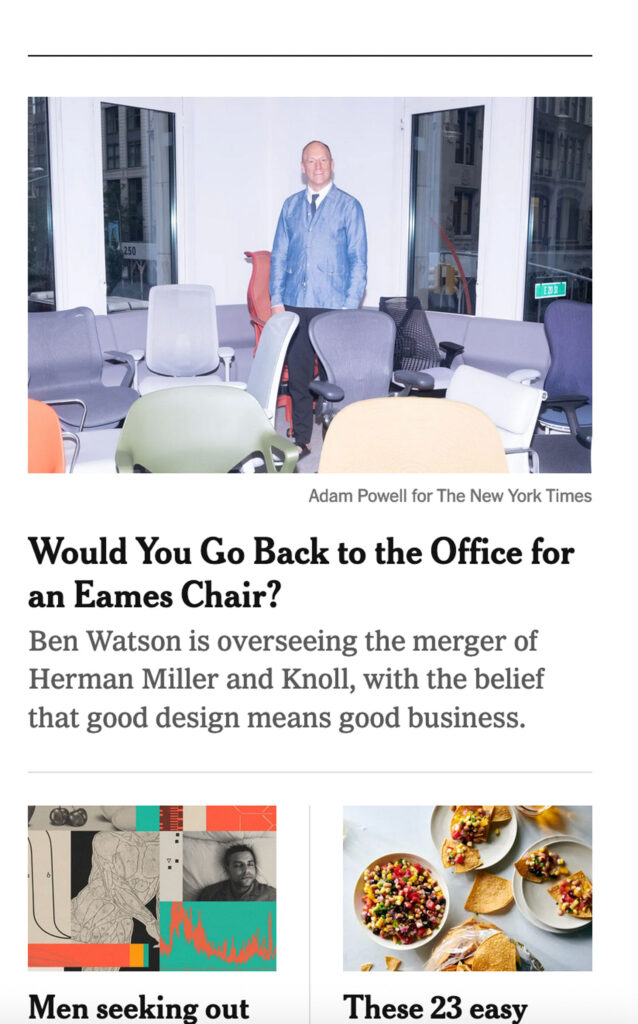
Nope. If you have spent any time in the corporate world, you can tell exactly where someone sits in an organization by the chair in their office (cloth, leatherette or carbon fiber?).
So yes, in some ways, chairs have been democratized. Mass-manufacturing has made them available to almost everyone. But market forces have ensured that they still represent hierarchy. You might own a chair, but it’s not an Aeron 8Z Pellicle with elastomeric suspension.
That’s why I like stick chairs. These vernacular chairs aren’t found in catalogs or department stores. Your purchasing department cannot order a gross of them for the office in Dubuque. You might think, “Ha! I am rich and can buy one.” But it will be that – just one chair.
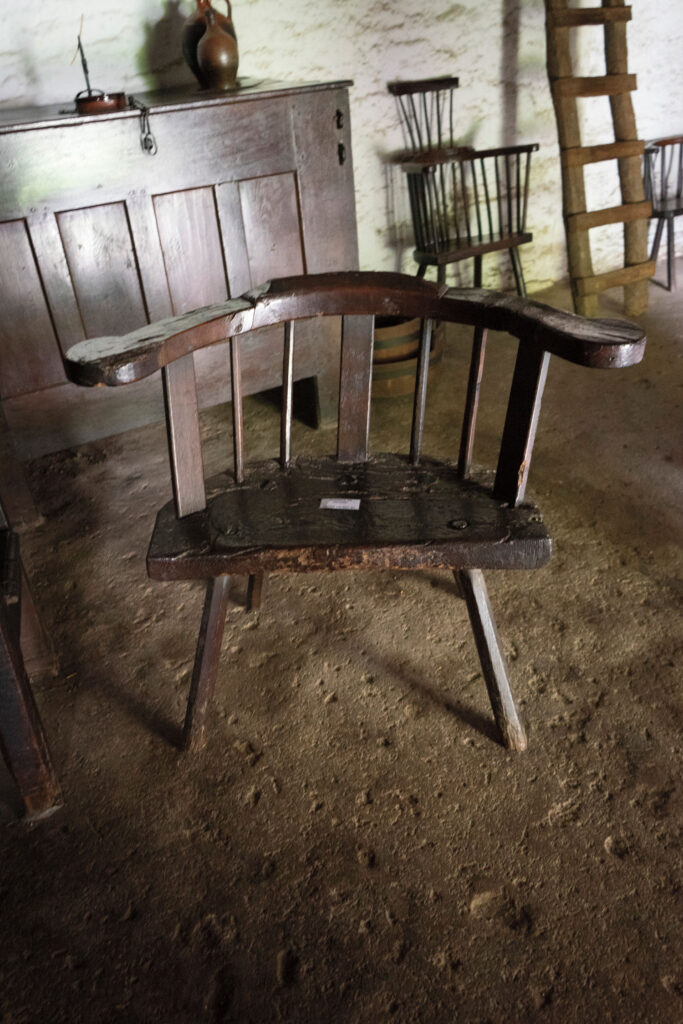
Sticks chairs were usually built by the owner of the chair. Perhaps they were made for someone in the chairmaker’s family. Or for someone in the village. To obtain a new one, you had to know the chairmaker. And the chairmaker had to agree to the transaction because – and this is important – the chairmaker didn’t have a boss. That’s because stick chairmakers weren’t typically professional woodworkers working in a chair shop. Chairmaking was a side business or done out of necessity.
This (and sorry for the economics lesson) isn’t capitalism. This is the same arrangement that has been in place since at least Medieval times.
“Hello, you make something I need. And I have something to exchange for it. If you are willing.”
Aside from the way you obtain a stick chair, there are other odd aspects to them, such as the raw materials used to make them.
What are they made of? Whatever was on hand from the hedge, the forest or the firewood pile.
This tied the chair to the land. To the species of trees that were easily available to the chairmaker. Or to the bits of wood that could be swiped from the local kingswood.
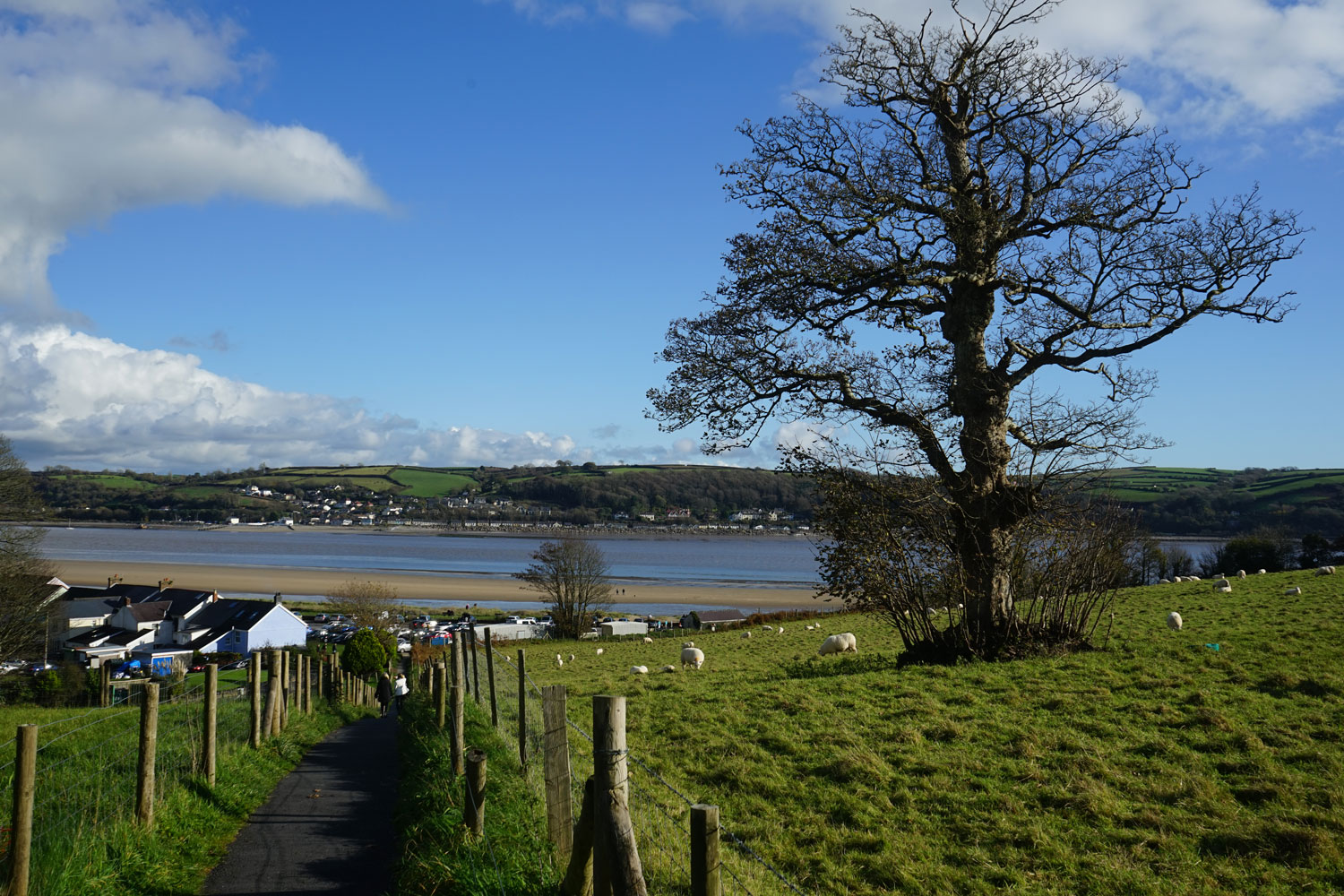
There wasn’t a choice of maple, walnut, wenge or snakewood. The chair was made from the best wood available (even if that was dodgy). If the chair looked weird because of all the different species used to build it, you were welcome to paint it. Or cover it in sheepskin. Or let it sit by the fire for a few years until the soot made it look a deep brown-black.
What about their overall design? Couldn’t you order a six-stick comb-back and get one that looked just like the chair the Davies family had?
Sorry, but no. Each chair comes out a little different because of the sticks on hand and the fact that these things are made one at a time. There are no duplicating machines or mechanical patterns for the chairmaker to follow.
This is not a romantic notion. It’s just how it is.
I’ve made stick chairs for sale – off and on – for 18 years. But I’ve probably made only 150 or so chairs. And no two have been alike. Each was made with the materials I had – sometimes wood left over from another job; sometimes home center lumber; occasionally green wood from a tree service. And each one reflected my interests at the moment and the tools I owned. Perhaps I was looking at a lot of Irish chairs or Scottish chairs. Or experimenting with spoon bits or rounding planes.
Sometimes I feel guilty that I sell my chairs. I suspect many makers of stick chairs feel this way. Some of my chairs go to wealthy people and occupy expensive homes. I don’t accept this fact lightly. But I atone for this by teaching anyone and everyone how to build these chairs.
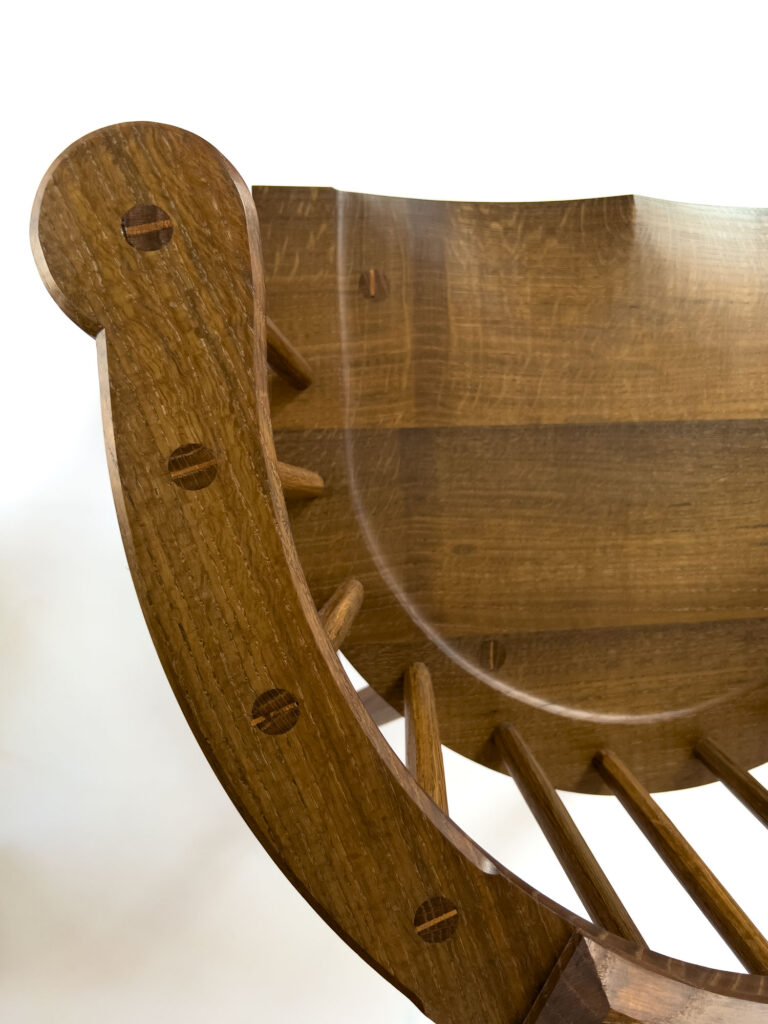
And so I remind myself: It’s a chair you can’t buy at a store for any price. A chair that will outlast all the plastic crap, or the chairs joined with cheap metallic fasteners. It is a chair that will look better and better the more you sit on it. The more you rub its arms. The more dents and abuse it suffers. And it’s likely the chair will be desirable long after you’re gone.
Few people in this world can ever afford to buy a chair with these properties. But you can make one. Ask, and I will gladly teach anyone the following: Join the sticks to the best of your ability. Carve your name on the underside of the seat. Rest your bones in it every night and think about music, religion, life, destiny and the trees that tie it all together.
Remember those lessons because that ability – the skill to make a chair – is the true seat of power. And if they take your chair away? Laugh, and build another one. You cannot be dethroned.
— Christopher Schwarz