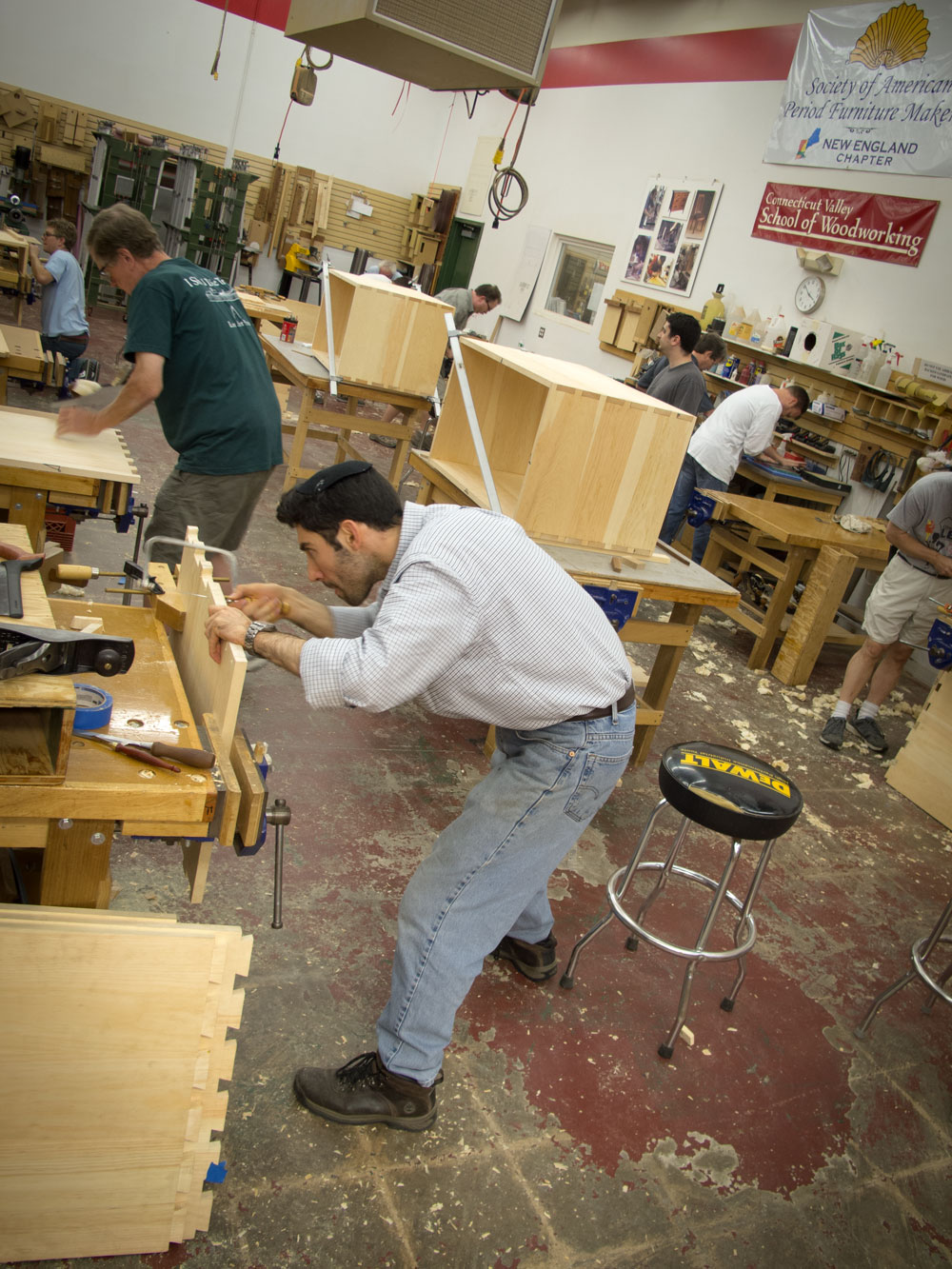
The real challenge in teaching a class on “The Anarchist’s Tool Chest” is this: How can I make woodworkers cut dovetails as fast (and accurate) as possible?
When I first began teaching tool chest classes, we weren’t able to glue up the carcases until late, late Wednesday night or Thursday. Then it was a mad rush to get the rest of the chest completed.
Since then I have learned to put away the “encouragement whip” and get out the “punishment whip.” (I wonder why women rarely take my classes?)
Today – the second day of the course at the Connecticut Valley School of Woodworking – we have a third of the 15 chests glued up. The rest will be glued up on the third day before lunch. This is a frickin’ cake walk.
What has changed? Well, to be honest, I am a poor teacher at best. Honest and true. But I have learned a few tricks from some fantastic teachers. Here are two of them.
1. Teach the information is small, manageable bites. Send students back to their benches to perform one operation. Repeat. This is from Trevor Smith, a high school physics teacher in Troy, Mich. The dude is an amazing teacher. I watched him teach for one day and learned more about teaching that day than in any other time period.
2. If you say it will happen, it will happen. Advice from Doug Dale, one of the outstanding assistants and teachers at Marc Adams School of Woodworking. If you set the goal for the day as “you will finish this particular operation,” then – surprise – the students achieve that goal. Weird.
And there is one thing I bring to the table: debasing the dovetail joint.
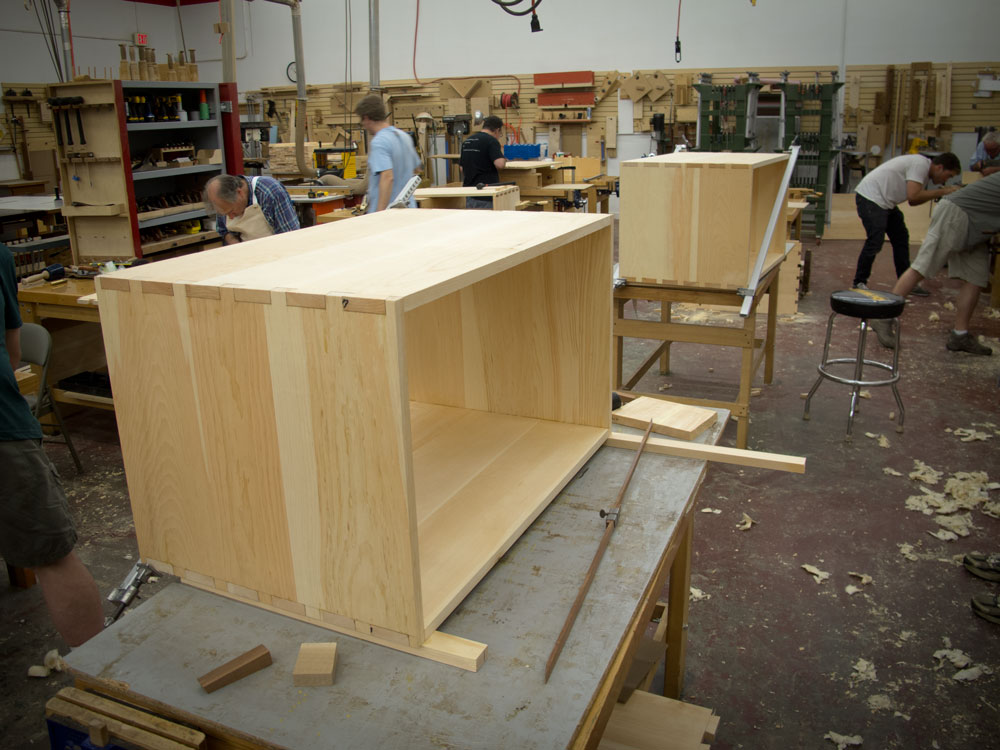
I do not treat this joint as a holy relic – St. Christopher’s duodenum. It’s a mechanical joint that is easy to cut if you break it down into small bites (thanks again, Trevor). None of the operations in cutting a dovetail is hard. The only thing that is difficult is being consistent with every operation.
With five chests together today, and all of them looking really, really good, I feel justified in drinking a beer.
— Christopher Schwarz
Like this:
Like Loading...