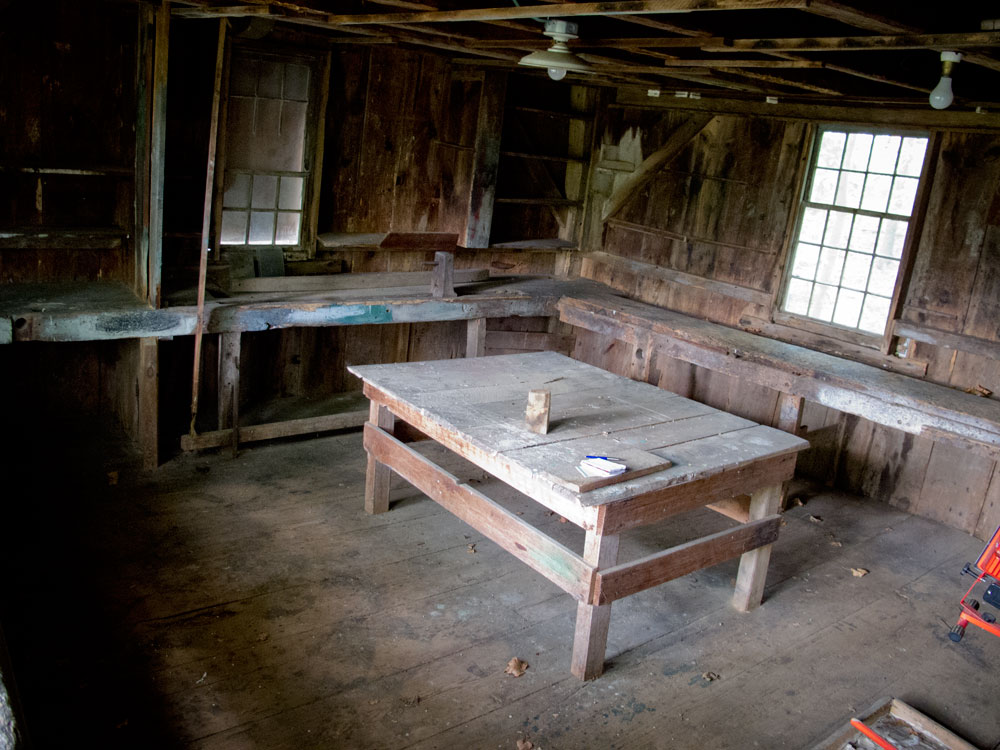
The discovery of an intact 18th-century joinery shop in Duxbury, Mass., set off a storm of interest last year in the small outbuilding behind a school.
Now, months after the discovery, preservationists and employees at Colonial Williamsburg have begun to piece together the interesting story of the site, to document every peg and nail and take the first steps toward stabilizing and preserving the building.
This week I took a tour of the site with Michael Burrey, the restoration carpenter who discovered the shop while working nearby, and Peter Follansbee, the joiner at Plimoth Plantation.
The working area of the shop is about the size of a single-car garage, yet almost every inch of the room is packed with clues about the work that was done in the shop, the tools that were in use and how they were stored. There is so much detail to see that after two hours of rooting around, my senses were overloaded and there was still much more to see.
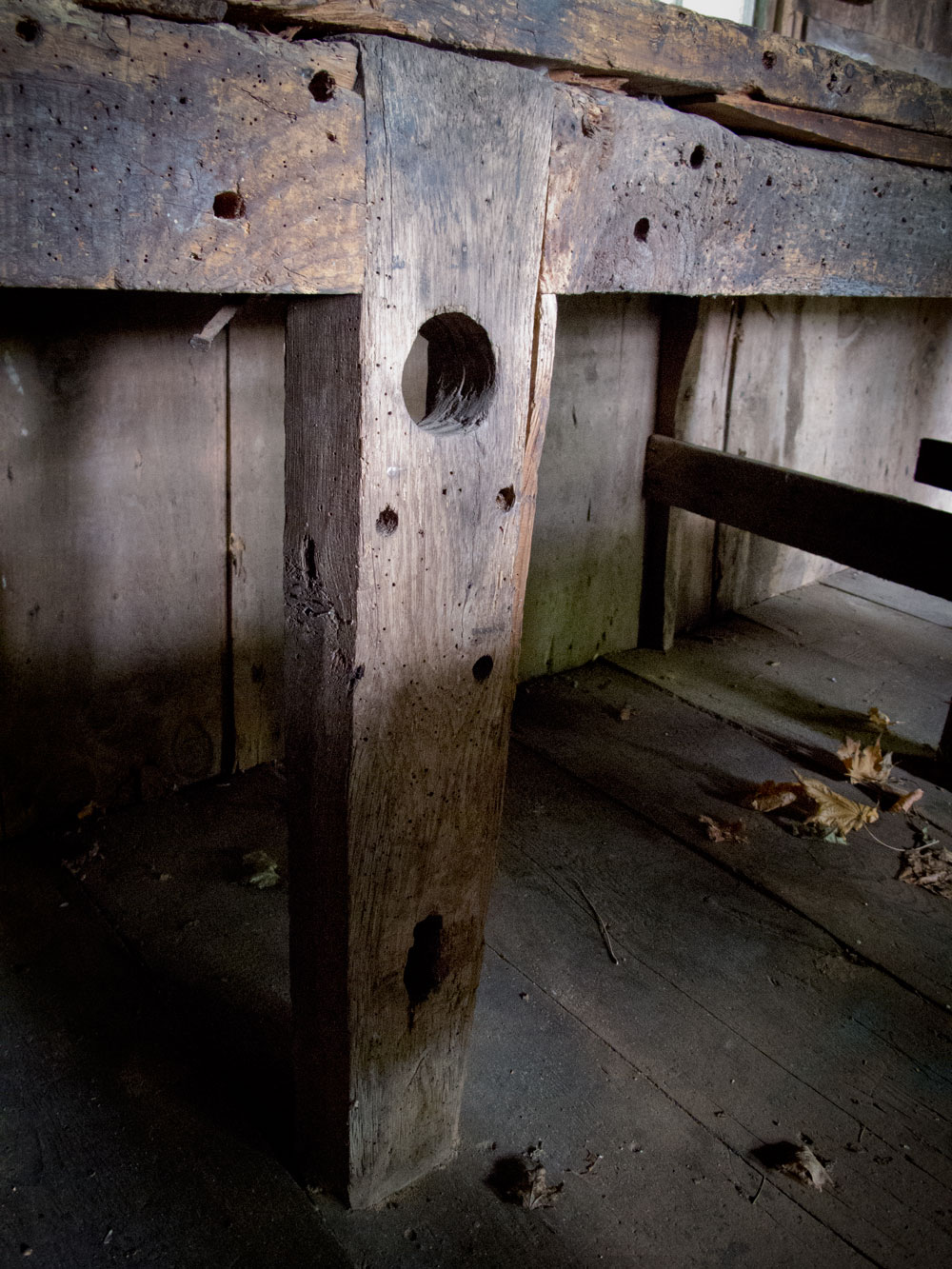
As a workbench enthusiast, I was quite interested in poring over the benches that lined three walls of the shop, creating a U-shaped ring of working sufaces along the outer wall.
The benches were all fixed to the structure of the building. I haven’t written much about this style of bench. These fixed benches seem to first appear in the 15th century as best I can tell (see the evidence here). These fixed benches exist at the same time as the typically freestanding Roman-style workbench. Eventually the Roman benches disappear (though not entirely in Eastern Europe), and are replaced by the movable forms we are familiar with now.
The benches in the Sampson shop have seen so much use that the bench along the back wall had been recovered with a new benchtop – you can feel the old mortise for the planning stop by feeling under the benchtop. None of the benches had end vises or even dog holes. There are planning stops and a couple huge holes that may have been for some metalworking equipment, Burrey says. There was at least one leg vise.
Dendrochronolgy on one of the benches indicates the top was pitch pine from 1786, Burrey says. That lines up nicely with the 1789 date painted on a beam in the storage area outside the shop door.
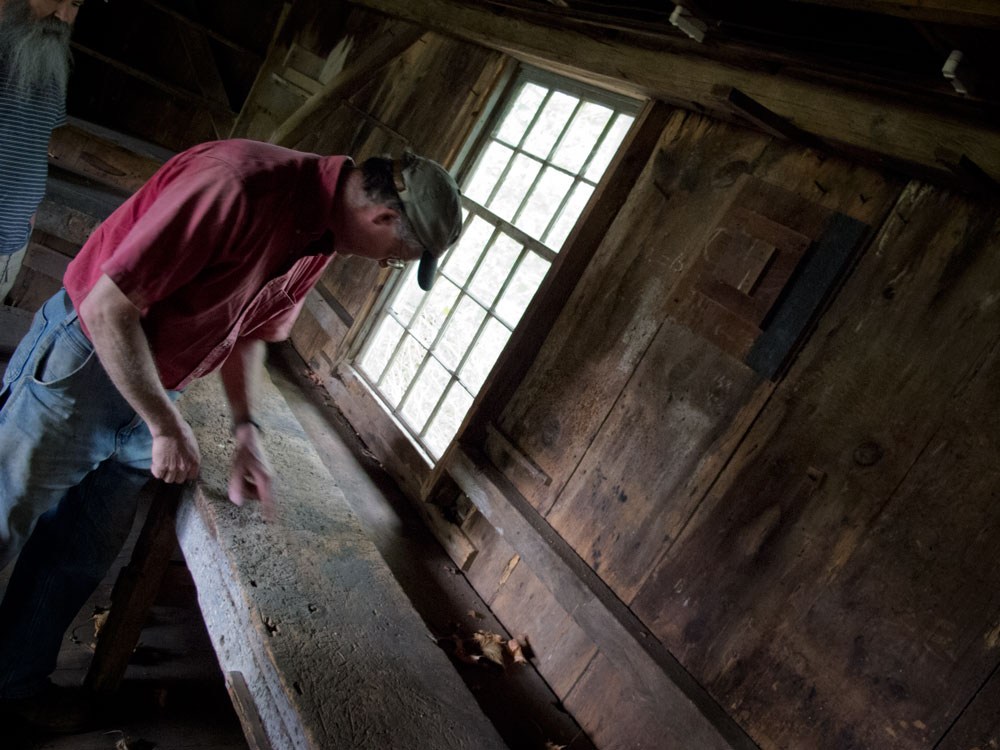
The shop was known in the area as a shingle shop, but it’s likely that a lot of other things went on there. One of the benches has been converted to a lathe, with a large metal wheel above it. The original owner of the shop, Luther Sampson, was (among other things) a planemaker, Burrey says.
Sampson was one of the founders of the Kents Hill School in Maine. And the school has some of his tools and the name stamp he used to mark his planes. Burrey also indicates that they have found shelves in the shop that were likely scarred by moulding planes set there.
Other tool marks suggest some other operations. Along the back wall, Burrey suspects that bench was used for crosscutting. The area is under a window. Right above the bench the wall is pierced with hundreds of jab marks from a marking awl. Above that is an unusual rack that would hold try squares. And the back wall looks like it has been hit by the tip of a backsaw repeatedly.
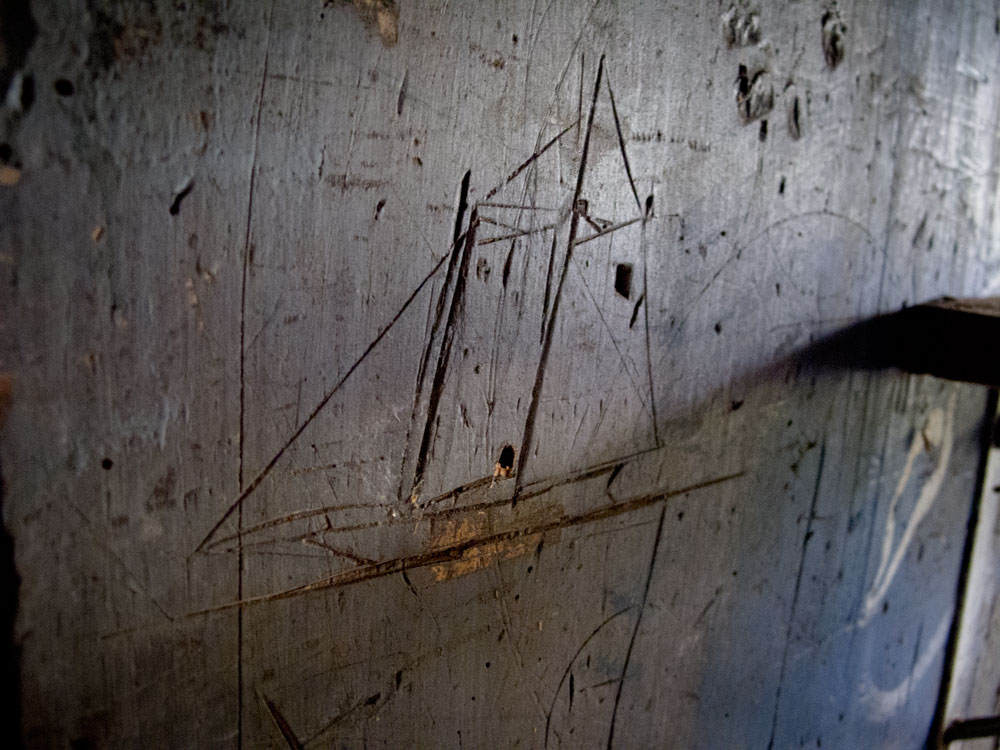
In fact, every square inch of surface seems to hold some message. There are bits of old newspaper pasted in places. The shapes of sailing ships are scratched into the walls with a nail or awl. A hatted figure is painted on one of the shop doors. And inside that painting is a series of concentric scratches made by a compass.
Empty tool racks are everywhere, many of them elegantly chamfered.
Burrey and Follansbee are cautious about making any firm declarations about how the shop was used.
“We’re just looking at ghosts here,” Follansbee says.
Follansbee is correct. The place is haunted. Like many unrestored old places you can still feel the heavy presence of the work that went on inside the walls. And now the really heavy work begins for the people who are not ghosts: Figuring out how to stabilize and preserve the building.
I don’t have any insight into the status of that end of the project. If I hear of any news, I’ll report it here.
— Christopher Schwarz
Like this:
Like Loading...