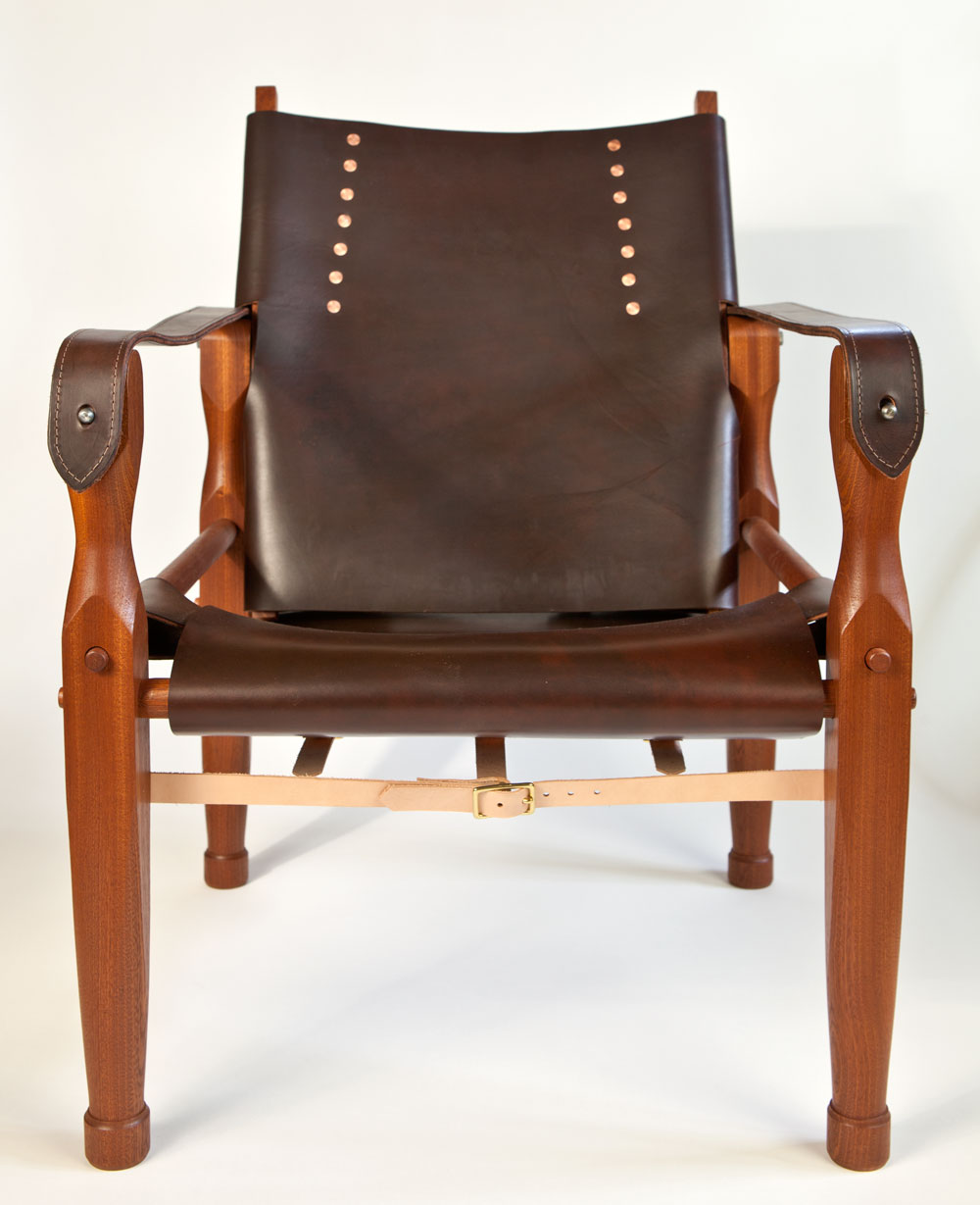
When your wife can control her urge to even slightly roll her eyes when you talk about the East India Company, and your hemorrhoids are as big as baseballs, it is time to cease work on your book.
I do not like sitting on my butt for hours, days and weeks. In fact, that was the reason I never fully enjoyed being a newspaper reporter. I adore a good millworks fire (who doesn’t?), but there were weeks when I would sit on my rump, handset smashed to my ear, saying, “And how did you get that candle dislodged from your insides?”
I’ve spent every waking hour of the last month on boring minutiae that isn’t worth writing about. I have executed more than 75 hand drawings. Processed hundreds of photos, and scanned more than 200 pages of material for the appendices to “Campaign Furniture.”
It sounds like I’m whining. I’m not. I enjoy the complete control over every pixel of a book, but I also know that you don’t want to read about the Pantone swatch I chose for the duotones in a book. This is a blog about woodworking. And killing Raney Nelson.
So here is a quick update on things you might be interested in.
1. I’m on schedule. “Campaign Furniture” will be designed and to the printer by the end of January, which means it will be released in early March 2014. I am trying like heck to bring in the book at less than $32 retail, but it is a challenge. We need to use matte-finish coated paper to reproduce the color and duotone photographs, and we won’t skimp on the binding or cover.
2. We are working on a special promotional piece of hardware. We plan to offer 100 U.S.-made tri-bolts for making campaign stools at a really nice price – $12. I have installed one of these on a camp stool, and I like it more than the eye-bolt solutions I’ve been using in the past. Stay tuned.
3. Other books are moving along. Peter Galbert is finishing up the writing on his book on chairbuilding. Andrew Lunn is wrapping up his tome on saws. Don Williams is (today) entering his last edits on “Roubo on Furniture-making” before submitting it to peer review. Lots of other projects are stirring, but I don’t have updates on them to share with you.
4. We are building a new Lost Art Press web site. With the help of woodworker/codemonkey Ben Lowery, we will be launching a new web site that is simpler to use. This is a major step forward for Lost Art Press, which is taking a leap from being a tiny company to a significant one. We will still be only two guys with laptops, but we are on the verge of outsourcing a lot of things that have been filling our garages, basements and waking hours with grunt work. Customers will still deal only with us – John and Chris – but we think shipments will be delivered faster and in better boxes – with no additional charges to you. Lest you think we are turning our back on our core principles, we will be using a local and independent company founded by two guys to do our fulfillment. When John called them last, one of the owners had his mouth full of bacon.
5. I need to thank you, our customers. I know it is old hat for a business to thank its customers, but I have a more personal appeal. Thirty months ago I walked out on the best job I’ve ever had – the editor of Popular Woodworking Magazine. I didn’t leave because I was unhappy. I left because I wanted to stretch things further than any sane/solvent corporation would let me. The only thing that has made Lost Art Press possible has been you. If you have bought a book from us in the last five years, your money has gone to support the crafts of woodworking, printing and publishing in the United States. Your support is also funding some incredible research that will become public in the years ahead.
So I need to get back to processing digital photos and find the unexpired tube of witch hazel cream to smear in my nether regions. You paid for that, too. Sorry to bring it up.
— Christopher Schwarz
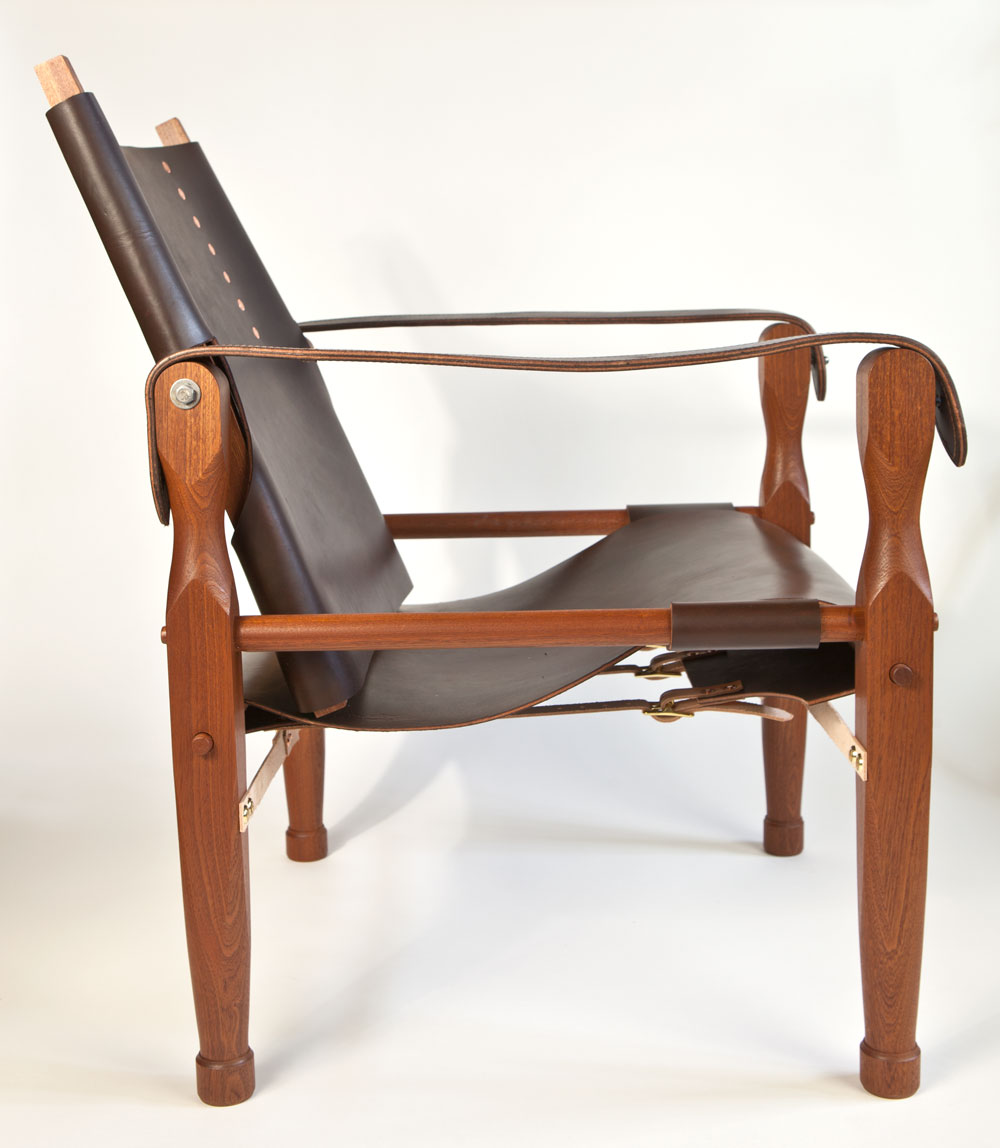
Like this:
Like Loading...