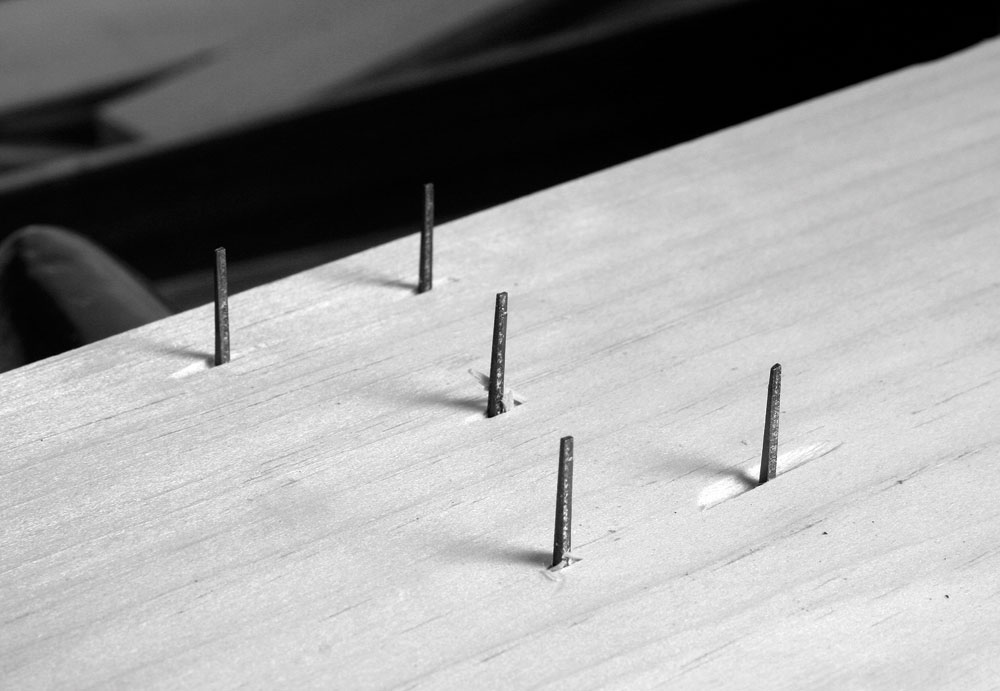
This is an excerpt from “The Joiner and Cabinet Maker” by Anon, Christopher Schwarz and Joel Moskowitz.
Clinching (sometimes spelled “clenching”) is when you drive a nail that passes through both thicknesses of wood you are fastening. The tip of this nail sticks out about 1/4″ and is bent over and driven into the wood.
Clinching adds remarkable strength to a joint. A 1948 study by the U.S. Forest Products Laboratory concluded that clinching can increase the holding power of a nail between 45 percent and 464 percent – depending on a variety of factors, including the species of wood and its moisture content.
Also interesting: The study concluded that bending the tip across the grain increased the holding power by 20 percent compared to a nail clinched along the grain.
But how do you best clinch a nail? There are several methods.
Four Ways and a Trick
Here’s how automated clinching machines do it: They fire a nail in at an angle, and there’s a steel plate waiting for the nail’s tip when it emerges. When the nail hits the steel it bends over into the wood – essentially it ricochets like a bullet or pool ball.
I’ve never tried this with a pneumatic nail gun, but it sounds like fun on a Friday afternoon.
For the hand clinchers, there are at least two common techniques. The first one is to first drive the nail through the work. Rest a steel plate, anvil or a second heavy hammerhead on the nail’s head. Then tap the tip of the nail with your hammer. It will curl over. Then you can drive the drooping tip back into the wood.
The second technique is similar to the machine process. You drive the nail through the work and against a waiting “bucking iron,” which curls the tip and forces it back into the wood.
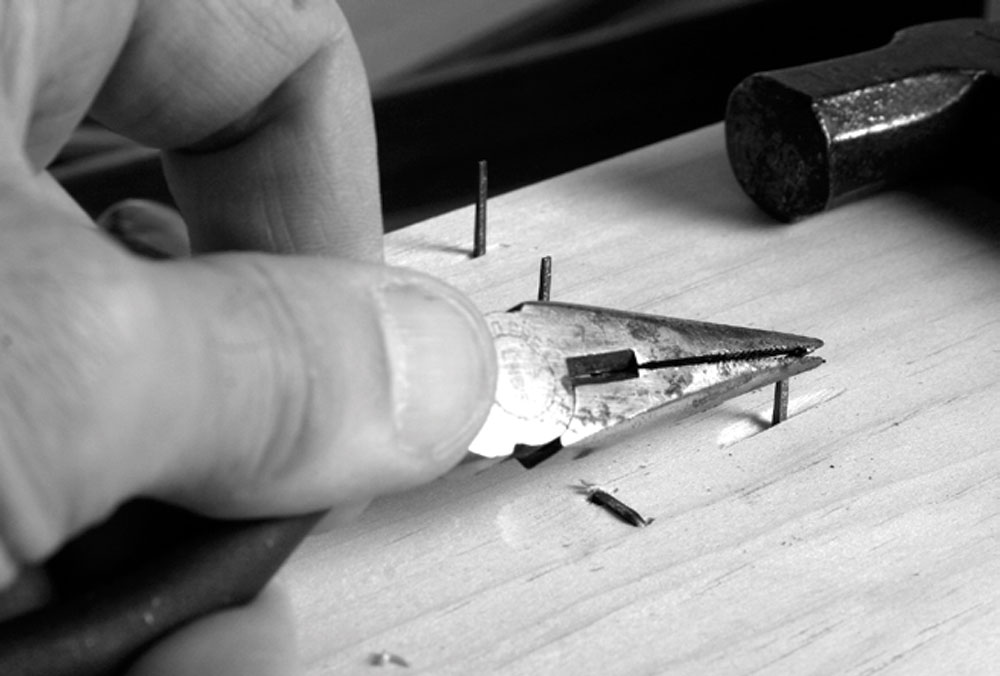
There’s one more technique I’ll sometimes use when I’m being really, ahem, retentive. I’ll drive the nail through. Then I’ll use needlenose pliers to bend the tip to the angle I want. Then I’ll drive it into the work. This results in a tidy appearance. I admit it’s a bit much.
When I have a lot of clinching to do, I’ve found that a cast iron table saw wing can be your best friend when clinching at work – doors, lids and the like. Lay the cast wing on your bench and you have a nice big area to support your work as you merrily clinch away. And no, the clinching does not really mar, crack or otherwise defile the cast iron wing.
— MB