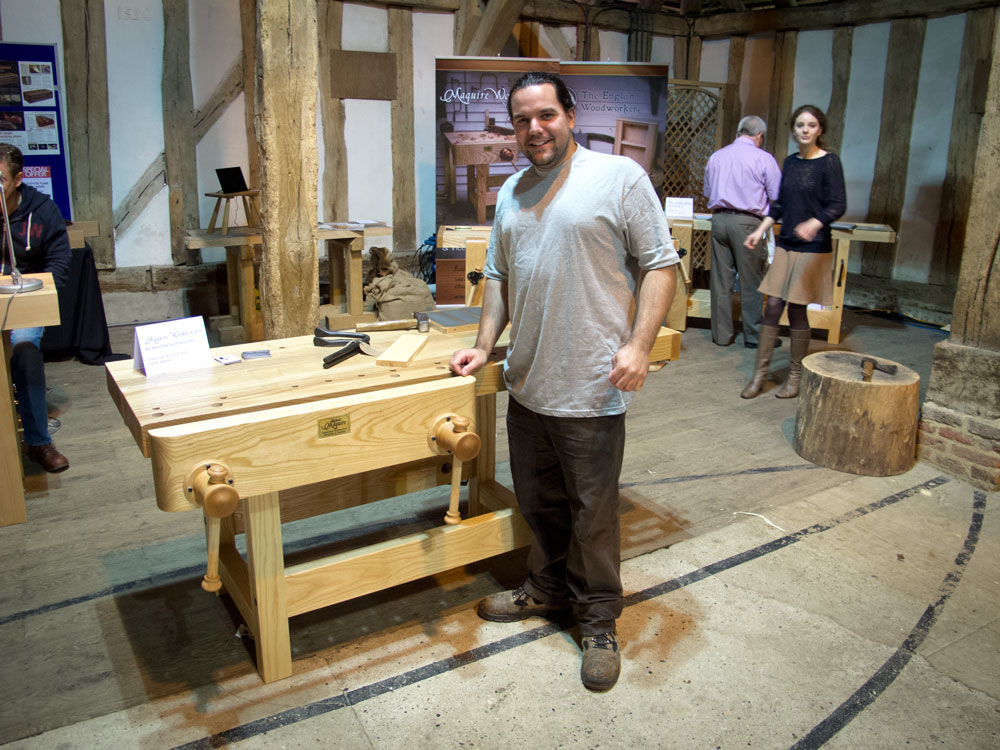
During the last 15 years, I’ve met a lot of woodworkers who like workbenches, but I’ve met very few who delight in poring over paintings of old benches while in a noisy pub surrounded by rowdy friends and colleagues.
But that is Richard Maguire exactly.
Yesterday evening as Richard and I were in a pub trying to decode a wack-a-doodle 1505 Nuremburg bench that was half Roman, half high-tech and half fantasy, a light kept flashing in our eyes. Finally, we looked up and saw a guy taking photos of us, shaking his head and saying something unprintable about a whale’s sex organ.
Richard grunted and went back to the computer screen.
It is not easy being a workbench nerd. And when you get two of them in a pub, the excitement can be somnambulistic.
For the last couple years I’ve admired the work that Maguire and his partner, Helen Fisher, have been putting out through their company, Maguire Workbenches. David Charlesworth and other English friends have told me how wonderful the benches are. But I’d never seen one in the ash until Friday.
They are seriously nice. Incredibly well-made. And overbuilt to perfection. (Example: In his custom designs that use slab tops, Richard doesn’t trust glue completely. So he adds a loose tenon to the edge joint that is drawbored into the mating edge. That is serious, fantastic overkill.)
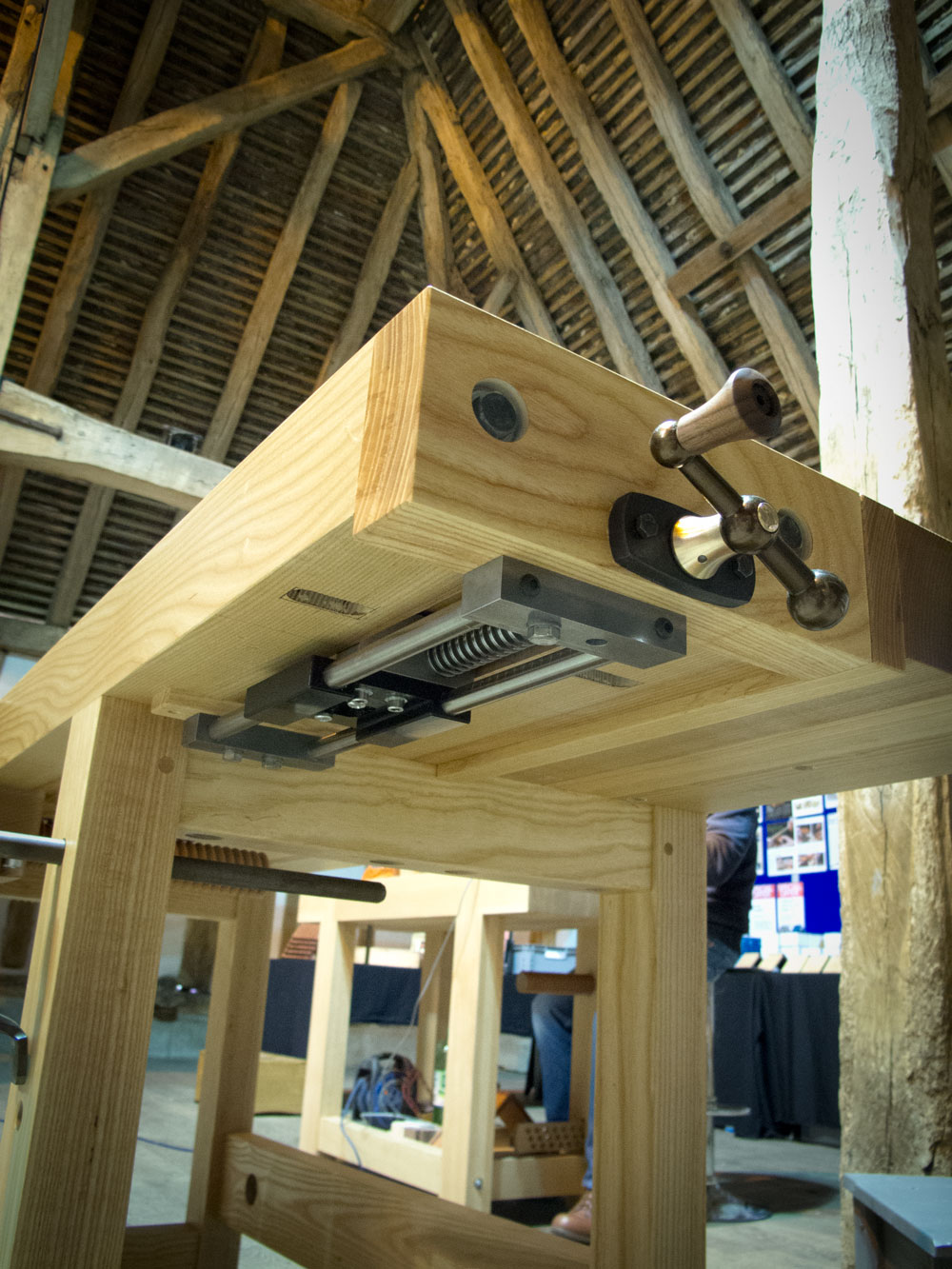
Richard and Helen use ash for the most part in the benches and add traditional workholding, such as leg vises, wagon vises, twin-screws and the traditional English wood-jawed face vise. The surfaces are of a furniture quality with a nice smooth finish – all touches that bench customers appreciate.
The vises were designed by Helen and (until recently) entire made by her in their workshop.
What is interesting about Richard and Helen is that though they work to a very high level using some machines and mostly hand tools, they are interested in researching and building (for sale) common furniture forms that were built entirely by hand.
Stuff, Richard says, that “would be built by a farmer for his family.”
And so, as their workbench business has grown and matured in the last couple years to the point where they are building about 50 workbenches a year, Richard says they want to return to building more furniture using hand tools exclusively. And, he says, he thinks they can make a living at it.
“I’m interested in proper handmade stuff that is made quickly and in a wholesome manner,” he says. “I feel I can build a table as fast as a machine woodworker and for the same price. It won’t be the same table. And it will be done by working with the wood in the way it wants to be worked.”
If you don’t think that’s possible, then you probably haven’t met Richard and Helen at one of their few public appearances.
Richard left school at age 14, barely able to read and write, and took up apprenticing under his father in joinery, carpentry and furniture-making. Richard worked with his father for five years before setting out on his own.
“I hated every minute of it,” Richard says of the apprenticeship. “But he taught me everything I know. As I finished, I set up on my own making furniture. Once I started doing it my way I realized it had got into my blood.”
Helen, on the other hand, studied interior design, received her degree and began working at an architectural firm until the recession hit and she was laid off.
Neither had a business background, but they began their workbench building business in earnest together, working from their old shepherd’s cottage in rural Lincolnshire.
The business has grown steadily, and recently the two started a blog that shares many of the things they have learned about the craft and workbenches. They have started filming videos (many of them excellent), which Helen posts on the web site she designed for their company.
After talking to them amongst the benches they brought to the European Woodworking Show at the Cressing Temple Barns in Essex, England, it’s clear they are proud of the benches they make, though Richard is constantly trying to talk customers out of buying one of their benches and instead building one of their own.
And you can’t help but think that this remarkable pair is on the verge of something very interesting. They have the benches – beautiful, nearly perfect benches – to sell to customers. But it’s clear they are only at the beginning of the journey.
And as the pub closed down at 11 p.m. (as per usual) and the bartenders chased everyone out, Richard and Helen were still animatedly talking about their most recent adventure that just might become part of their future: old line-shaft equipment.
In any case, please be sure to subscribe to their blog. Whatever happens next is sure to be something to see.
— Christopher Schwarz
Like this:
Like Loading...