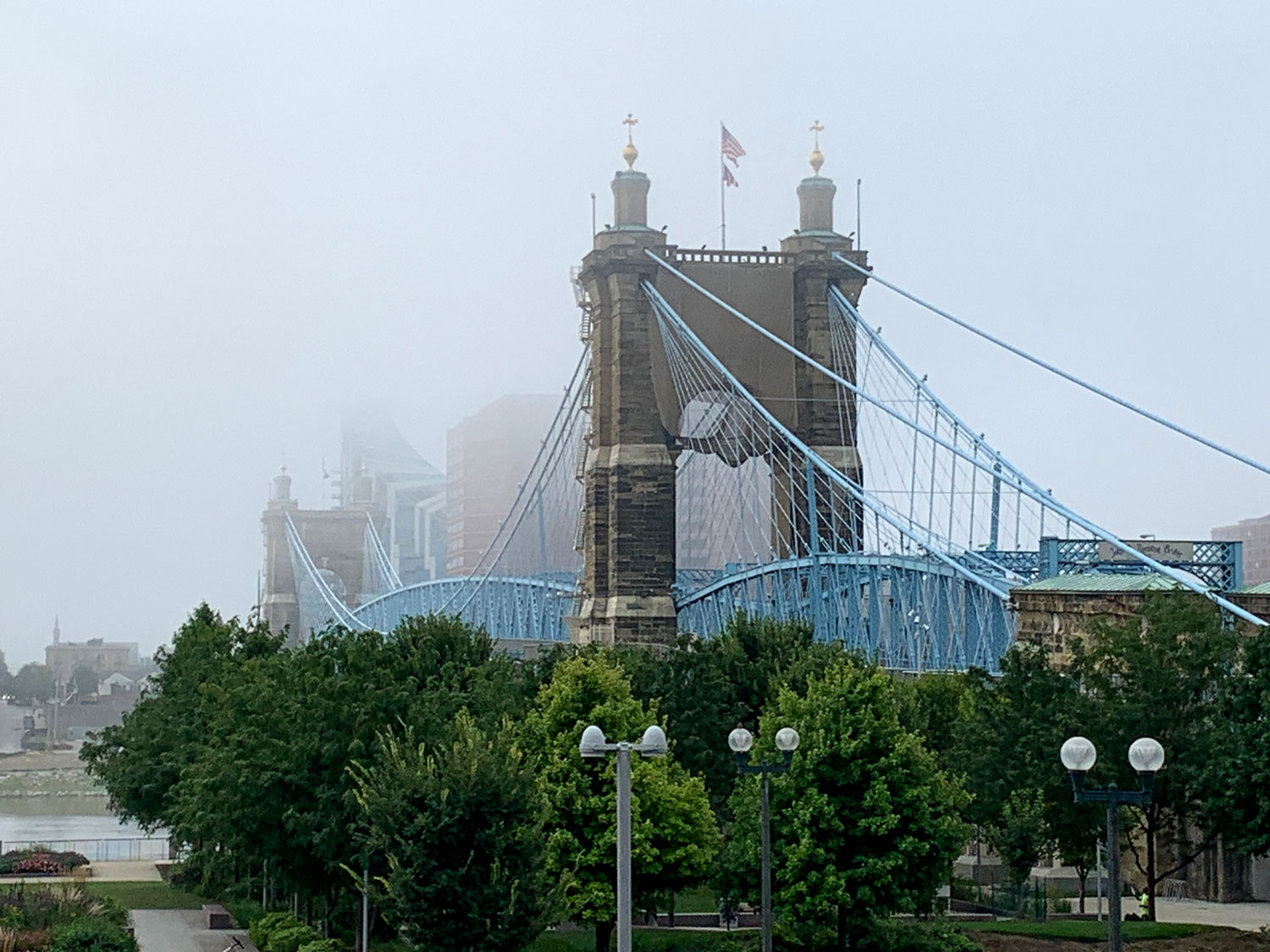
Registration for 2021 classes at our storefront opens at 10 a.m. (Eastern) tomorrow, May 17. We have only a few classes scheduled as we are trying to ease back into the new world. As you can imagine, a lot has changed both in Covington and with our business.
Some of our favorite restaurants have closed, but new ones have opened. We’re working on some new kitchen and bathroom facilities for visitors. And Brendan Gaffney has left us for Upstate New York.
One of the biggest changes has been the strange new barrier that has emerged between Ohio and Kentucky because of bridge construction. The old Roebling Suspension Bridge is closed entirely for repairs. The main bridge, the Brent Spence, is being fixed and repainted, so getting across the river is more difficult than ever because of continual lane closures and the giant condom that has enveloped the structure. As I write this, even our pedestrian bridge across the Ohio River is closed because a large stone fell from one of its piers.
It’s enough to make you consider taking the Anderson Ferry. Or swim.
So if you do plan to take a class, I recommend you stay on the Kentucky side of the border (no, you don’t need a passport, just bring a jug of corn liquor). There are lots of great hotels and Airbnbs in Covington that are walking distance from the storefront.
Here are the three classes we’re offering this year:
July 30-31: Build a Cricket Table with Derek Jones
Aug. 2-6: Build an “Anarchist’s Tool Chest” with Megan Fitzpatrick
Nov. 8-12: Make a Carved Oak Box with Peter Follansbee
Dec. 3-5: Build a Dutch Tool Chest with Megan Fitzpatrick
We hope to offer a few more classes before the end of 2021, but we are waiting to see if instructors will be able to travel. And if students are willing to sign up.
I’m not going to teach here or anywhere – at least for now. One of the after-effects of the pandemic has been how our publishing business has grown (almost four-fold). Keeping Lost Art Press running smoothly is more than a full-time job for me and John.
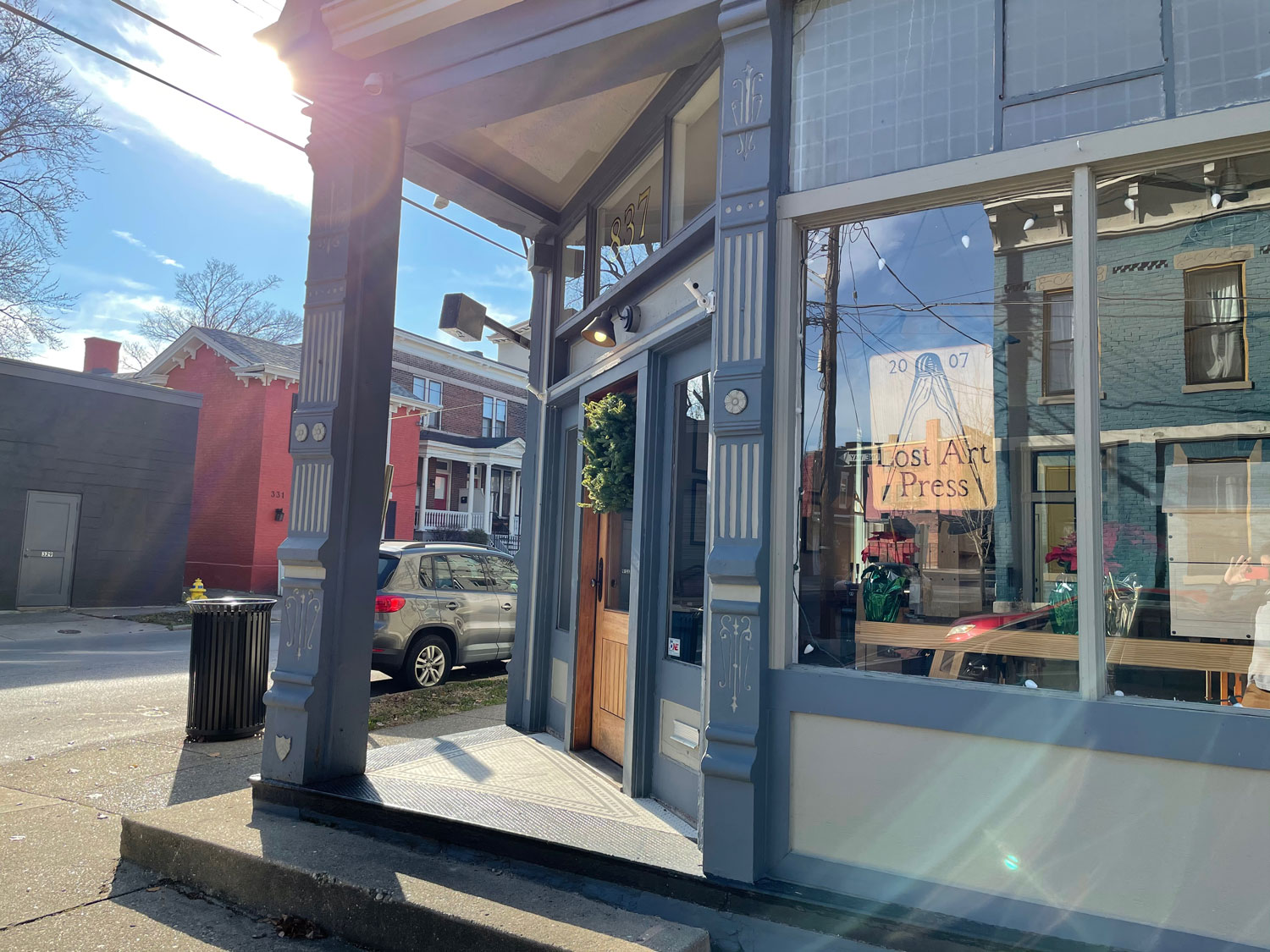
Like it or not, however, I’ll still be helping the instructors out during the classes. That means making sure there’s enough toilet paper, helping students who need assistance and occasionally brandishing the “encouragement whip” when the dovetailing slows down too much.
If you haven’t taken a class here, it’s important to remember that we are not a school. We don’t have an ice cream machine or a masseuse. But we do offer high-quality instruction, tiny classes with only six students, excellent workbenches and a walkable historic neighborhood to explore.
Plus Bean, the three-legged shop cat.
So if you are ready to travel and to attempt talking to strangers, I hope you’ll consider joining us. All we ask is that you be vaccinated against COVID-19. You can read more about that decision here.
— Christopher Schwarz