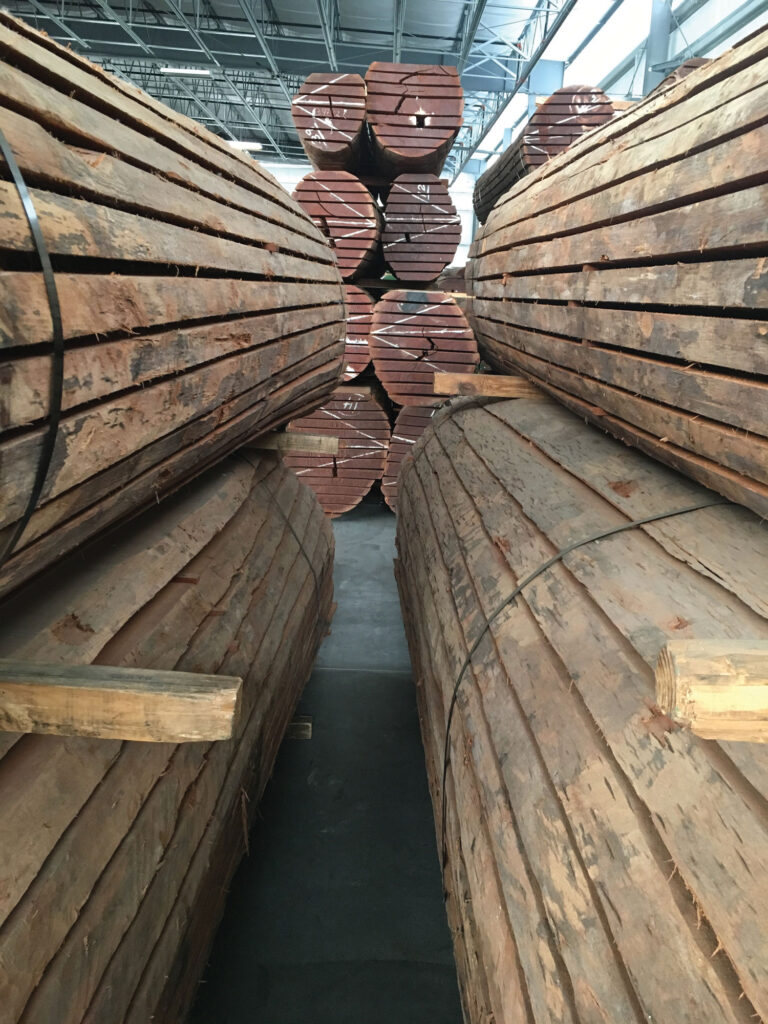
You can build a stick chair with almost any wood. Yes, you can rive it from green wood. But you can also buy it at the lumberyard and get parts that are plenty strong enough.
Editor’s note: What follows is a short excerpt from “The Stick Chair Book,” which is scheduled to be released in hardcover form in early November. Until that date, you can buy an “Early Adopter Digital Package” of the book for $25. This digital package includes lots of extra goodies. When the hardcover book is released, this package will go away forever.
Most chairmakers are ridiculously worried about the wood they use in their chairs. Is it strong enough? Is it dry/wet enough? Is the grain straight enough? Can I get the parts I need from this chunk on my workbench?
But aside from those narrow concerns, there is a lot of flexibility when it comes to the wood you use to make a chair. The wood can be:
• almost any species
• air-dried, kiln-dried or vacuum-dried
• a softwood or hardwood
• sawn or riven
• ring-porous, semi-diffuse-porous or diffuse-porous
• from the lumberyard, the log yard or your backyard.
Put another way, almost any wood can be used in a chair as long as it is strong enough, dry enough and the right size. What follows is how to evaluate your stock in terms of its strength, moisture and size – without turning you into an intern at the Forest Products Laboratory.
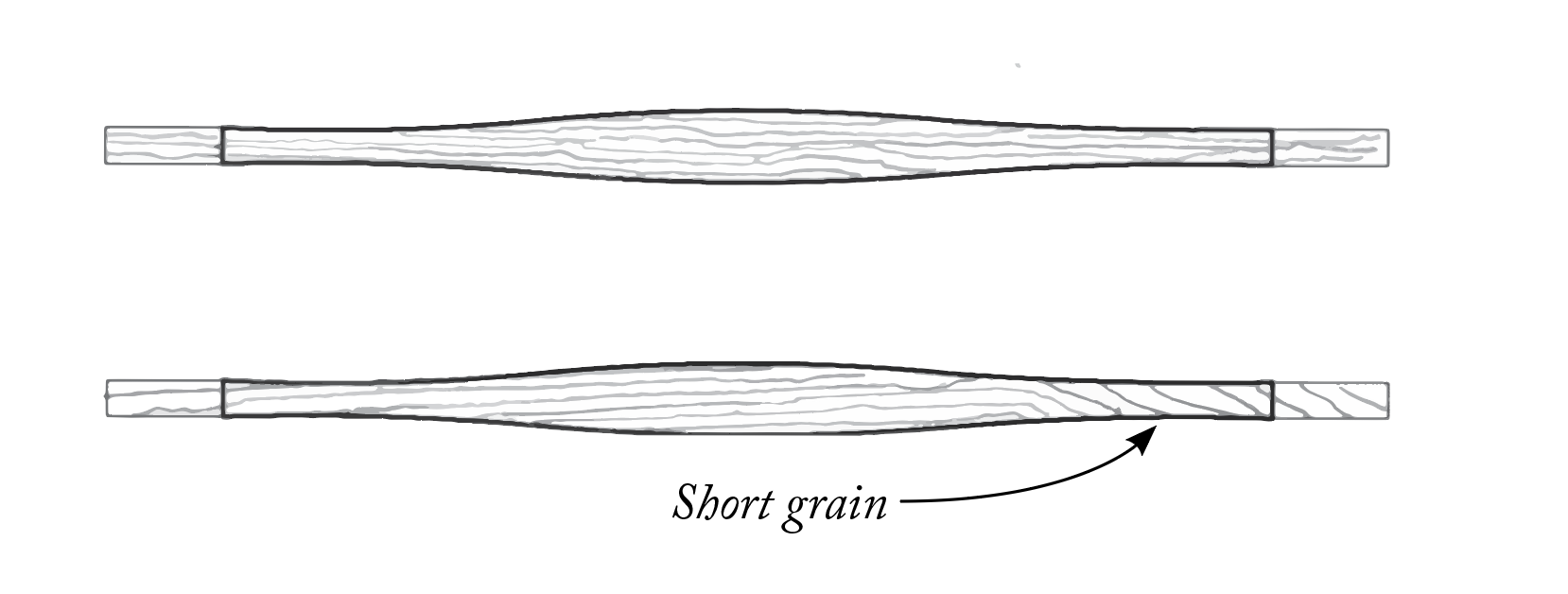
The stick at top has grain running its entire length. The one below has short grain and is doomed to snap. Training your eye to see short grain at a glance is a helpful skill.
Strength
Every stick of wood is a bundle of wood fibers. If the fibers run continuously from one end of the stick to the other, that stick will take far more abuse compared to a stick where some of the fibers run across the width of the board (sometimes called “short grain”).
You can create one of these super-strong sticks using a few methods. You can rive the wood – like firewood – so it splits along its long fibers. You can saw it out by following the direction of the fibers with your saw blade. Or you can use a combination of these two methods.
Neither method is magic. As long as the fibers run straight through the stick, you have done your job.
The other aspect of strength derives from the species of wood. A strong species, such as white oak, can be extraordinarily tough when it is only 1/2″ in diameter and its fibers run continuously from one end to the other. A similar stick of cherry or walnut might have to be 3/4″ in diameter (or larger) to possess equal strength.
While it sounds like I am about to offer a chart, graph or equation to determine the optimal-sized chair part, I’m not. Instead, I’m going to suggest you find a sledgehammer.
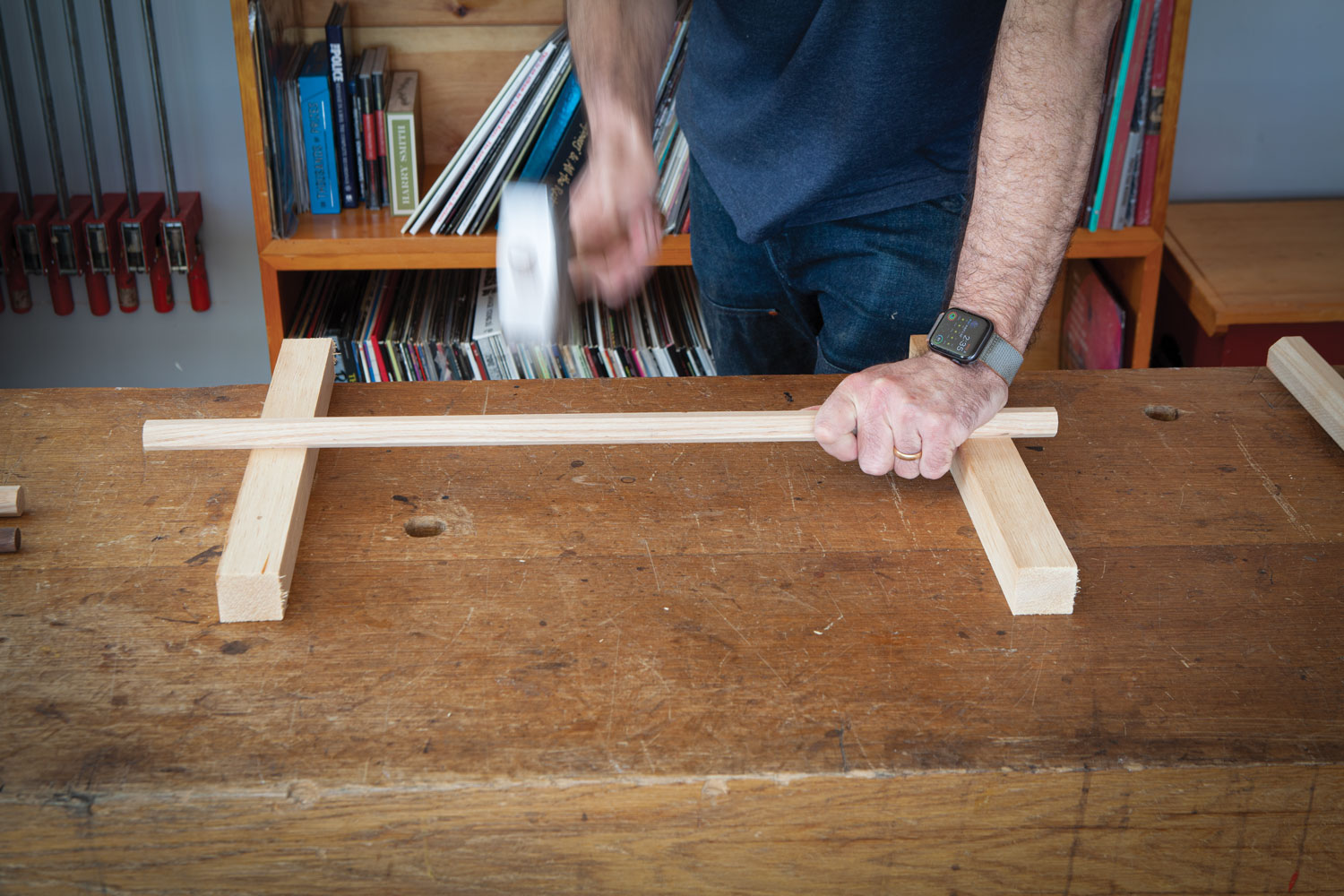
When I make a chair, I make a few extra sticks and hit them with a sledge. I recommend it. You will learn a lot about how wood breaks and how some species (like ash) seem indestructible. Below are two victims. Short-grain walnut and brash cherry.
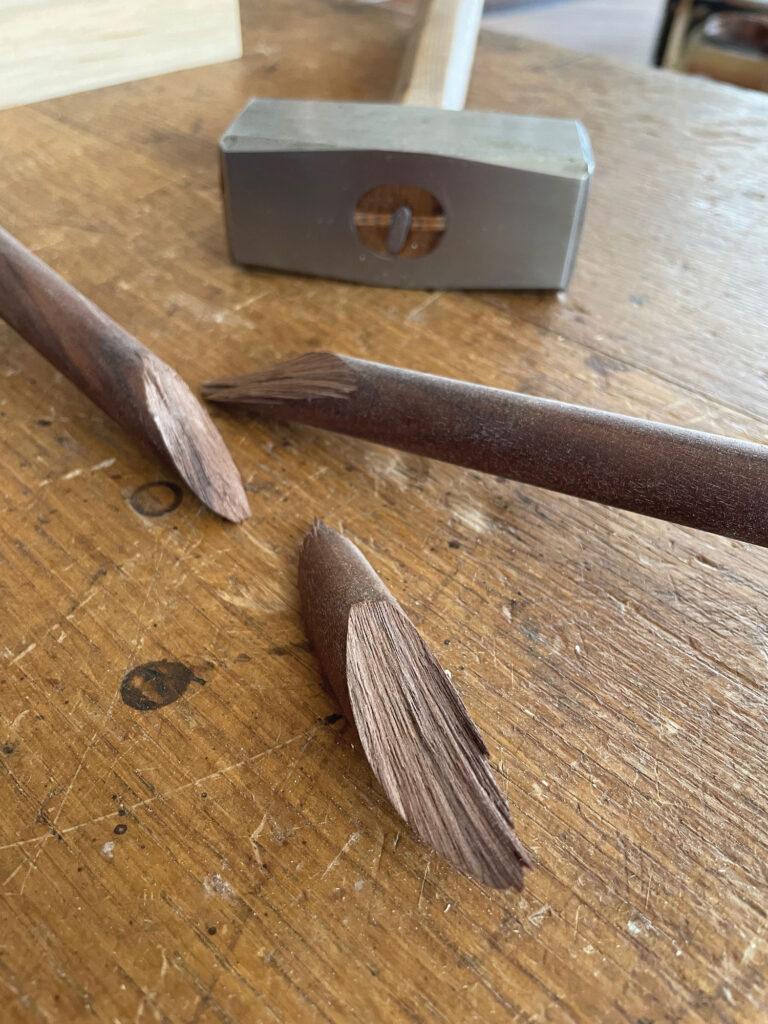
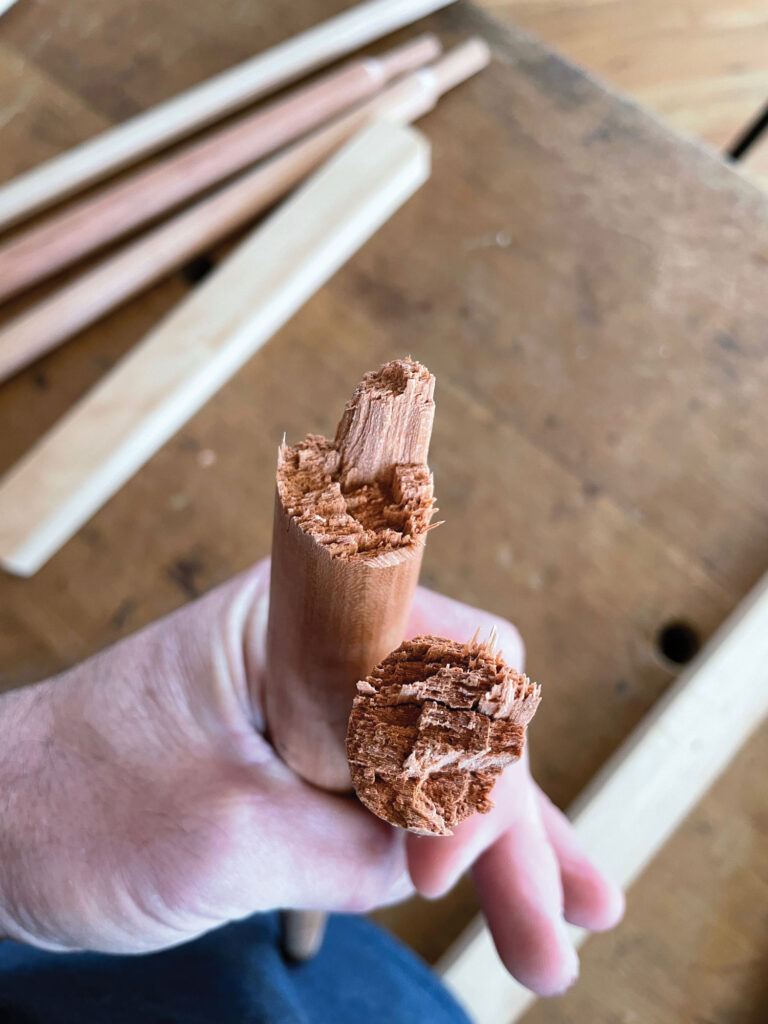
You can easily test a sample chair part by propping it up on two blocks of wood, one on either end of the stick. Hold the stick in place with one hand and strike the stick with a small sledgehammer (2 lbs. or 3 lbs. will do). If the stick survives the strike, the part is strong enough. If it snaps, you should increase the bulk of the stick or find one with straighter grain.
Why isn’t there a Holy Chart of Diameters and Species with recommendations for chairmaking? Because wood is so variable. For example: Slow-growth and fast-growth oak can be radically different when it comes to strength. (Slow-growth oak is far more porous and easily snapped.) How the tree grew, how it was dried and how straight you cut it all play a part in how strong a stick is. But one way to resolve all the variables is to hit a sample stick with the sledge.
The idea for this test came from fellow chairmaker Chris Williams, who was looking for a way to test wood for brashness – a defect where the wood is so brittle it can be snapped like a corn chip. It is also a method that the USDA Forest Products Laboratory has used to test brittle woods.
How hard should you hit the stick? Like you are striking a nail. Should you use a surviving stick in the chair after you hit it? It’s your call, but I usually use them.
— Christopher Schwarz