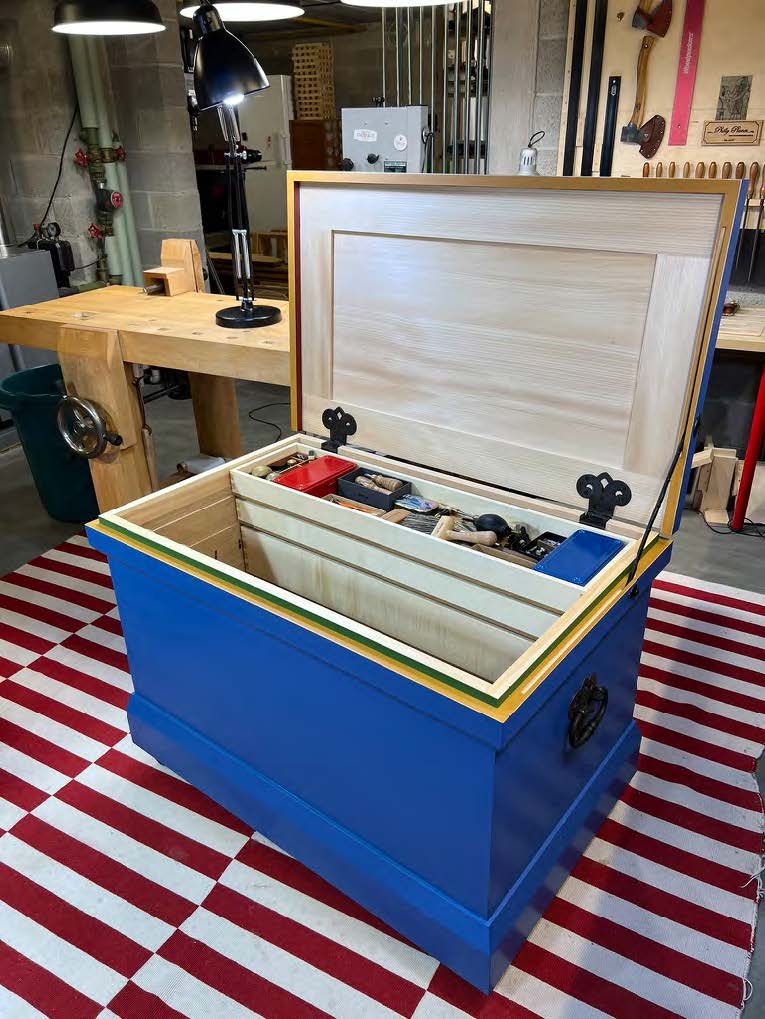
The below was written by our good friend Mattias Hallin, who lives in Belgium (though he would, I think, want me to let you know he is Swedish). You might recall that he is our non-resident expert in linseed oil paint, from this 2024 post (and he wrote for us about overseas ordering, for those few Lost Art Press items not available through our international stockists).
His tool chest – which we’re calling the Archivist’s Tool Chest because that’s his profession – is a study in meticulous planning of storage (and hardware). We asked him to write about it for the blog, and he kindly delivered.
I’ve posted an goodly excerpt below, with a link to download a pdf of Mattias’ entire write-up.
When I was in Covington for a chair class in 2022, Megan kindly lent me a Dutch Tool Chest (DTC) for temporary storage of all the tools I’d brought, and I found that I really liked working out of it. At the same time, I got a good, close-up look at Chris’ and Megan’s full-size Anarchist’s Tool Chests (ATC), and decided there and then to one day build an ATC myself (and a DTC, but that’s a different story) – except, in my case the A stands for Archivist, as that is what I do for a living, while I have nary an anarchic bone in my body.
And now I have built that chest.
This blog post, though, is not about the chest build as such, which, bar some personal tweaks and touches, is pretty much straight out of ‘the literature’ (The Anarchist’s Tool Chest and its addenda here on the blog and in Megan’s videos on the ATC interior and a traveling ATC). Rather, it is about how I approached designing the tool storage, and the ideas and solutions I came up with in that process, as these offer some ideas not suggested in the ATC book.
The Chest: Some Basic Facts
Before diving into my big box, though, just a few words about its general construction.
It is mainly built out of Pinus strobus, i.e. Eastern White or (as it is usually known over here) Weymouth Pine. Runners and till bottoms are oak (Querqus spp, probably robur). The sliding till walls and tool racks are hard maple (Acer saccharum), and finally there’s some boxwood (Buxus sempervirens) for boxing the lid stay slots, while the block plane cubby is pear (Pyrus communis).
Dovetailed carcase and skirts as per TATC. Through-tenoned lid frame, as per same. Bottom boards nailed on, as per, etc. and so forth.
The hardware (except a set of vintage cast iron casters, bought online) is blacksmith made, designed and forged by the fantastic Tom Latané.
The finish is Ottosson linseed oil paints on the outside, and the company’s oil/wax paste on the tills and racks.
The internal space of the empty shell is 36-11/16″ long, 22-1/8″ wide and 23-15/16″ high. Nothing magical about those oddish numbers: they’re simply what aiming for 36-1/2″ x 22-1/4″ x 24″ ended up as.
Mock ‘em Up!
I barely know my way around SketchUp et al., and while I think I can safely say I’m not bad at figuring stuff out just in my head, for many things I also like to check that thinking by mocking them up. This is particularly true for anything three-dimensional.
Planning for tool storage in my chest began with a considered decision on the dimensions of the basic shell. The larger that shell, the more tool storage potential, so bigger may seem better. That, however, is not the whole story. For starters, a larger chest eats up more space in your shop and becomes more unwieldy to move about. Also, if it is too wide and/or too deep, it becomes hard to reach the bottom or the rear corners. And Chris and Megan warn from experience that the longer the chest, the more likely it is the sliding tills will rack.
So, my initial instinct to throw space at the problem and go large was quickly reined in.
The simplest way forward would have been to just go with the measurements from ATC, but in order not to box myself in too soon, I decided to make the rough panels well over size by some 5″ or so in both length and width. This let me show them to one another and get a much better feel both for how large different sizes of chest would be and how well (or not) I would be able to reach into them.
(Here, by the way, is as good a place as any to say that I mostly don’t work to a cutlist and try to use as few measurements as possible. I do almost all stock prep and dimensioning with hand tools, so usually work to the largest thickness commonly available between a set of parts and make them to fit each other rather than be exactly some pre-defined size.)
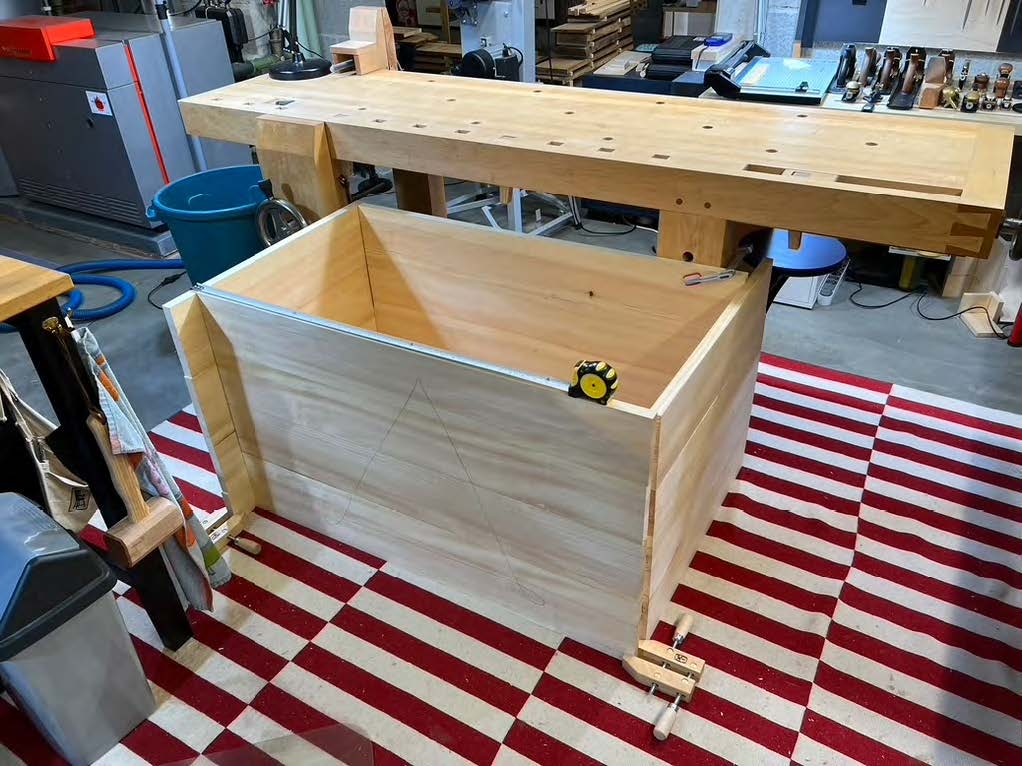
Other than overall size and internal reachability, I also knew already at this stage that I wanted:
- For the sliding tills to measure at least just over 8″ in internal width (because my woobie box is 8″ long);
- to have full access to two sliding tills at a time with no overlap; and
- to hang my backsaws between the front wall and the front tool rack.
I did not yet know the exact outer dimensions of the sliding tills, or the thickness of the surface-mounted hinge leaves, nor would I for quite a while, but to get 8-and-a-bit ” internal would likely mean 9″–9-1/2″ external width per till, so 18″–19″ for two tills to open with no overlap.
Add to that at least 2″ for the front rack with room behind for saws, plus a margin for the hinges, and I suspected that the 20-1/8″ internal width in the drawings in ATC would risk being a tad on the tight side.
For final dimensions I therefore decided that all four panels should be 24″ high (same as in the ATC), the front and back 38-1/2″ long (so 1/2″ more than in the book) and the ends 24″ wide (so 2-1/8″ more). Everything else would follow from there.
Thinking Inside the Box: Basic Premises
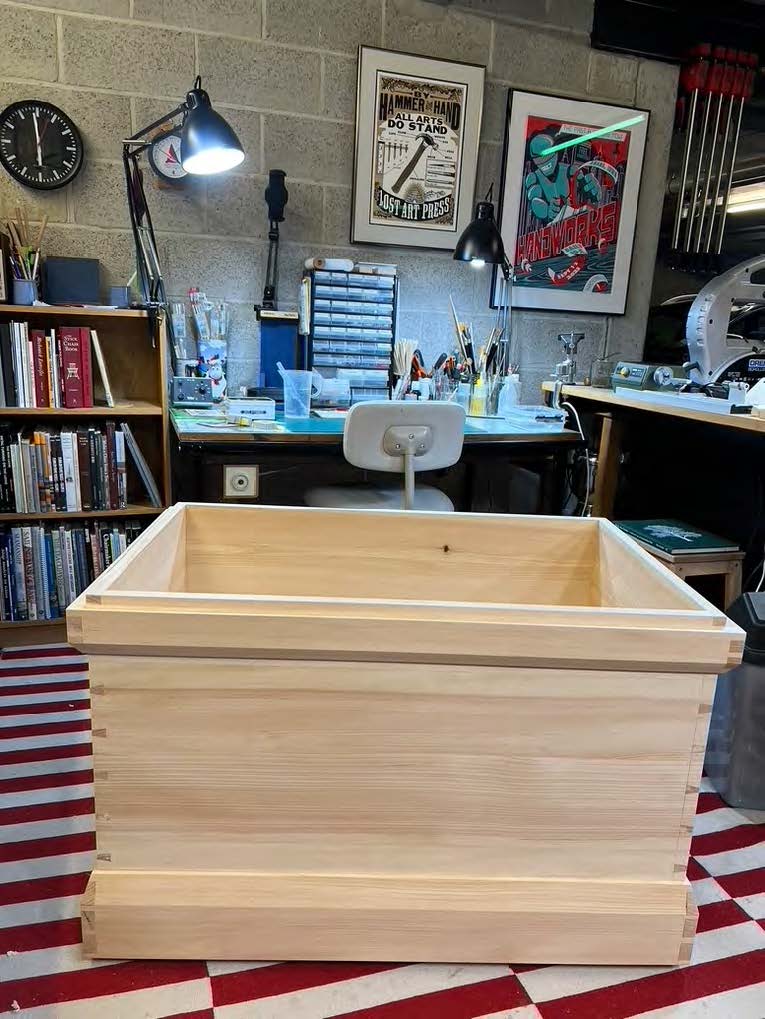
While things followed, and the basic carcase came together, I had plenty of time to think ahead and consider the basic premises for how I would want to organize the tool storage. On the one hand, I have a strong tendency towards a place for everything, everything in its place and the skates go in the fridge. On the other hand, I had no wish to French-fit the interior. To use an extreme comparison: I am in great awe and admiration of the Studley tool cabinet, but I wouldn’t have it if you paid me to.
In daily practice I will most likely put a tool back in more or less the same spot where I picked it up, but over time where that spot is may well move around.
Basic Premise #1: Tool storage should be flexible.
That said, my tool set is by now quite stable. I have acquired most of the tools I need or see a future need of. I have also sold or given away a number of tools that I either upgraded or didn’t expect ever to use (again). By now, I think what I have left are the keepers.
I will not be able to fit every single keeper into this chest, but then I never expected to. There are, however, keeper tools that I am as certain as makes no difference will live in this chest for the rest of my days. Some of those tools may as well have a permanent place specially fitted to them.
Basic Premise #2: There can be duly motivated exceptions to Premise #1.
Notwithstanding tool set stability, I am no exception to the general rule when it comes to mental shopping lists. That is to say, I have one. Mine may be much shorter than before (cf. stable tool set), but there are tools I know I shall want to get in the coming years. If I know that now, and that I shall want to store them in the chest, I might as well plan for that.
Basic Premise #3: Try to think ahead.
Then again, you never know, so racks and tills should be as easy to replace as is commensurate with safe and solid storage while they’re in use.
Basic Premise #4: Don’t over-fix the fixtures – they may have to come out.
Finally, no matter the solution selected for individual tools, they should come out and go back in easily, blocking each others paths as little as possible. The more frequent the use, the easier the access should be. Edges shall be protected, as shall fingers, hands and arms when rummaging through the depths of the chest. Space should not be wasted, though, but a happy medium sought between efficient storage and effective use.
Basic Premise #5: Aspire to conduct a well-balanced tool ballet.
With these premises clear in my mind, I could start to purposefully mockup dummy versions of the fixed racks and tills and put my ideas and these premises to the test.
Front Tool Rack
The first questions to which I sought answers were, what distance should there be between the front wall and the front tool rack to best store my backsaws, and how high should the rack be above the floor?
My longest backsaw is an 18″ tenon saw. It will live in the saw till on the chest floor, but I still wanted to make sure it could also hang behind the front tool rack if needed. On the other hand, that tool rack should not sit any higher than necessary for that to work. In part because some tool handles are rather long, but mostly to make sure there will be room enough above the rack to fit a crab lock to the inside of the front wall.
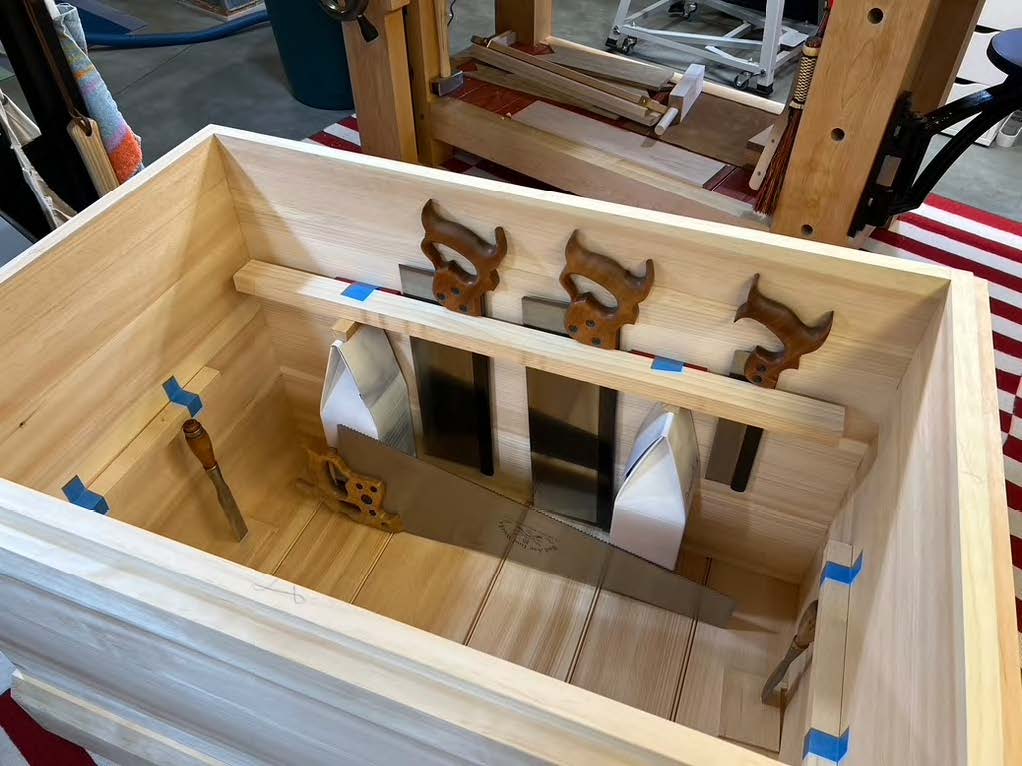
It turned out that 5/8″ was the ideal distance between wall and rack, and that with the top of the rack at 16-1/4″ above the floor my biggest backsaw would fit with 1/8″ to spare. I made a careful note of these figures.
I also wanted to know how wide the tool rack should be, what distance from the outer edge holes would be best for tool holes, and what sizes and shapes of holes would best work for different tools, in particular those that would have a permanent place?
Again, dummy racks made from pine offcuts was the perfect method for me. They were easy to run up from an ample supply of material left over from the panel prep, so I could test as many possibilities as I wanted. The “standard” tool hole suggested in the literature is 1/2″ diameter and is drilled with the center point 1/2″ in from the edge. The latter I found held good, but a 1/2″ hole is too small to hold certain tools as well as I wish. Thus, the socket of a Lie-Nielsen chisel seats perfectly in a 14mm (or 9/16″) hole, while a Blue Spruce chisel needs a 5/8″ (or 16mm) hole for the ferrule to go in deep enough that it won’t wobble in the rack. And for my set of Barr Tools cabinetmaker’s chisels, that have larger sockets, the perfect size hole turned out to be 19mm (3/4″).
(While I mostly work in customary/imperial units these days, I drilled some of these tool holes in the closest metric equivalent if that was the best drill bit for the job I had to hand.)
For my pigsticker mortise chisels, I tested elongated holes in different lengths and widths until I found the particular sizes that would best fit each one of them, taking into account the tapered undersides of the bolsters. And for my two paring chisels I went fully bespoke – but I’ll come back to that in the Photo Gallery below.
I also experimented a fair bit to find the ideal distance between centers but won’t go into any detail on that; suffice to say that, depending on the tools involved, it varied between 1-1/2″ and 2-1/4″.
As for the width of the rack, 1-3/8″ turned out to be right, giving a total width of 2″ including the space for saws. While that does not leave much room between the saw handles and the handles of tools stored in the rack, I tested the setup thoroughly and concluded I would be happy with it. I was in any case anxious not to have the front rack extend more than really needed in order to minimize potential interference with the saw till on the floor below.
Saw Till
Speaking of the saw till, it took a fair bit of experimentation to find the right configuration. For starters, how many saws should it hold? I currently have two handsaws – a 26″ rip and a 24″ crosscut – and as already mentioned, I also wanted to store the 18″ tenon saw in this till. That’s three saws. However, on my shopping list are two short – 18″ or 20″ – handsaws, a rip and a crosscut, so I decided on a five-slot till.
With that made clear, there still remained a number of issues to sort out. The till needed to be roomy enough for ease of operation without gobbling up too much floor space. What would that mean in terms of distance between slots? On testing, I found 3/4″ too tight to allow the easy grab of a saw, 1″ fine but unnecessarily roomy, so 15/16″ turned out to be the Goldilocks number.
And would I want to store stuff below the saws? There’s potential space there, but only accessible by removing the saws, which is not very handy. I first thought it would be a good spot for my roll of saw files, which don’t come out all that often, but found that idea overridden by a more important consideration: the placement of the slotted till uprights should be in function of where the backsaw blades will hang.
The front rack has four spacer blocks to create the 5/8″ slot for backsaws, one at either end and two somewhere in the middle, through which the rack is also screwed to the chest wall. The two middle ones I located to optimize the available room to fit my particular set of backsaws, not forgetting to leave room in the middle for the crab lock.
The saw till uprights were then best placed immediately below the two middle spacer blocks to keep them from obstructing the space available for hanging saws. This turned out to mean an off-center placement, with the two uprights too close together for the file tool roll to fit, even on the diagonal. In the end I decided to leave 2-1/2″ underneath the saws: high enough that e.g. a Trusco box will fit in there if needs be, but not conceived to be a major storage space.
There is still about 1-1/2″ clearance between the top of the saw handles and the underside of the bottom sliding till, so in theory I could have gone an inch or so higher. But that would have had an unwanted effect on the interplay between the innermost slot and the tool rack above. For a saw to come out and go in with full clearance from longer tools in the rack, the slot has to be about 2-1/4″ out from the chest wall. Starting a set of five slots from there, though, would have made the whole till go a full 7″ into the central well.
I bought the 18″ tenon saw for my bench build. It did a great job on the massive tenons involved in that but is not in any way a daily user on furniture-size projects. I am not getting rid of it, but it can certainly be stored in a harder-to-reach spot. Thus, I decided to have the innermost slot at but 1-1/4″ from the wall, in effect between the hanging backsaws and the tools in the rack. To get a saw in or out of there, any long tools must first come out of the rack, but for the very occasional use of the 18″ tenon saw, that’s not a problem. The other four slots have good clearance, and the whole saw till, including the bracing rails, ends at 6-1/8″ into the central well, giving me a full 12″ of width for storing bench planes between the till and the molding plane corral.
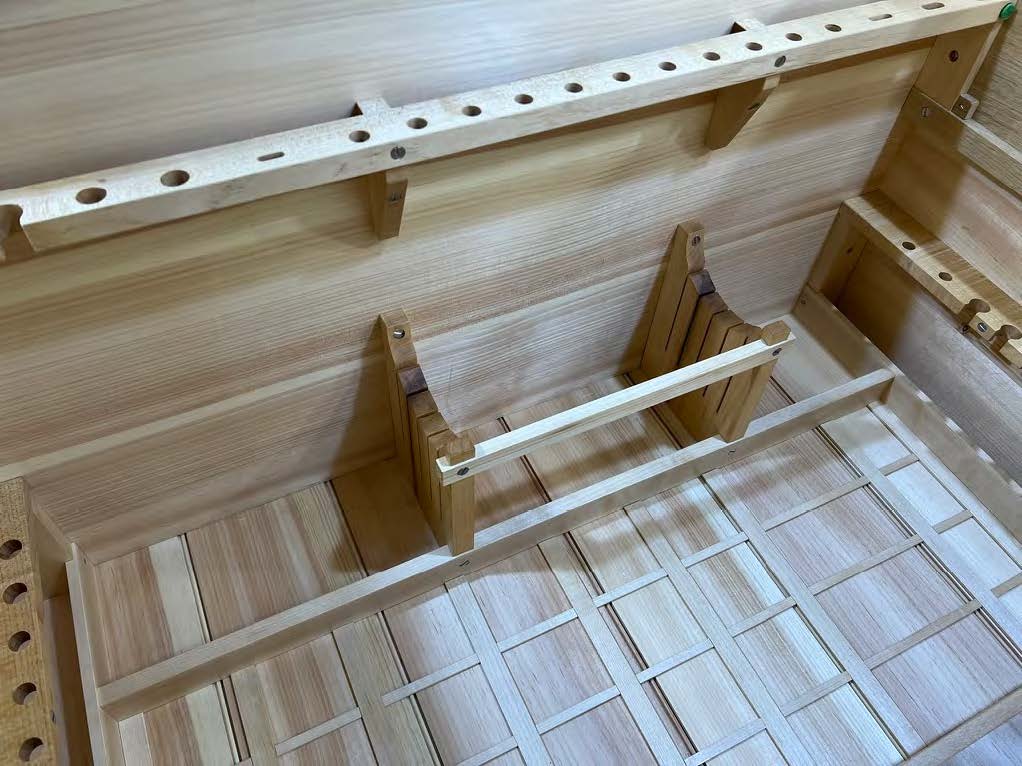
To read more, download Mattias Hallin’s pdf below.
wonderful overview.
Nicely done! That gave me lots of ideas and addressed some of the experiences I’ve had outfitting my DTC.
The most excellent write up. So ideas to apply to the rebuild of my off the floor ‘stand up’ tool chests (aka: plywood mules), thankfully this fine example was posted for the new year.
Rob
Wonderful post. Thank you for sharing here. Also, helps confirm I am not crazy. My exterior dimensions were determined in the class I took from Megan. Sorting out the interior for tool rack, where would the saws go, width and height of the two levels of tills, etc took a great deal of time. I thought folks would think I’m crazy if they knew how much time I spent on that aspect of planning. Glad to see it wasn’t just me. My brain might have exploded if I had also had the ability to modify the exterior dimensions a bit; not that I would have strayed too far from the travel ATC size chest. In many respects, I really like constraints “forced” upon me. It’s a great size for my tools and when I go to woodworking school, this is the chest I will pack up my tools in. However, if I want to go to my dad’s 45 minutes away to woodwork, even the travel ATC is a bit too heavy and big for my needs. As such, I think a Dutch tool chest is in my future as a really good size to travel (think of it like a carry on vs. check in luggage). All good problems to have. Might even be able to talk my wife into storing these in the home when not is use as she proudly has on display her grandfather’s steamer chest in our living room.
This is like an entire supplemental chapter on outfitting toolchest innards. Thanks Mattias!
As musicians say, good gig!
As I’m not sure I would succeed in replying individually (the comments section has been a bit unpredicatble in that way of late) below each comment, please allow me to say a collective thank you so much – you are most welcome for your kind words of appreciation!
And Joe, no. Not crazy. Perfectly acceptable and rational behavior is what I’d call that. And I agree that having to do something within a set of externally enforced constraints can be valuable indeed. If anything goes, well, meh. That said it was at the same time scary, liberating and inspiring to try to come up with my own set of constraints.
Cheers and all best,
Mattias
Many thanks, a great explanation of what you did and why. The photos are excellent and very helpful
Thank you so much for this treatise – very timely as I’m starting to puzzle over and plan out my first tool chest (likely the boarded chest from ADB). My tool set is not yet stable, but getting there; my main goal for the chest is to collect the “regular” woodworking tools into one protected space from the various nooks and crannies currently used. This gives me a big head start on how to organize for now and the future!
Thanks for writing this. It’s great.