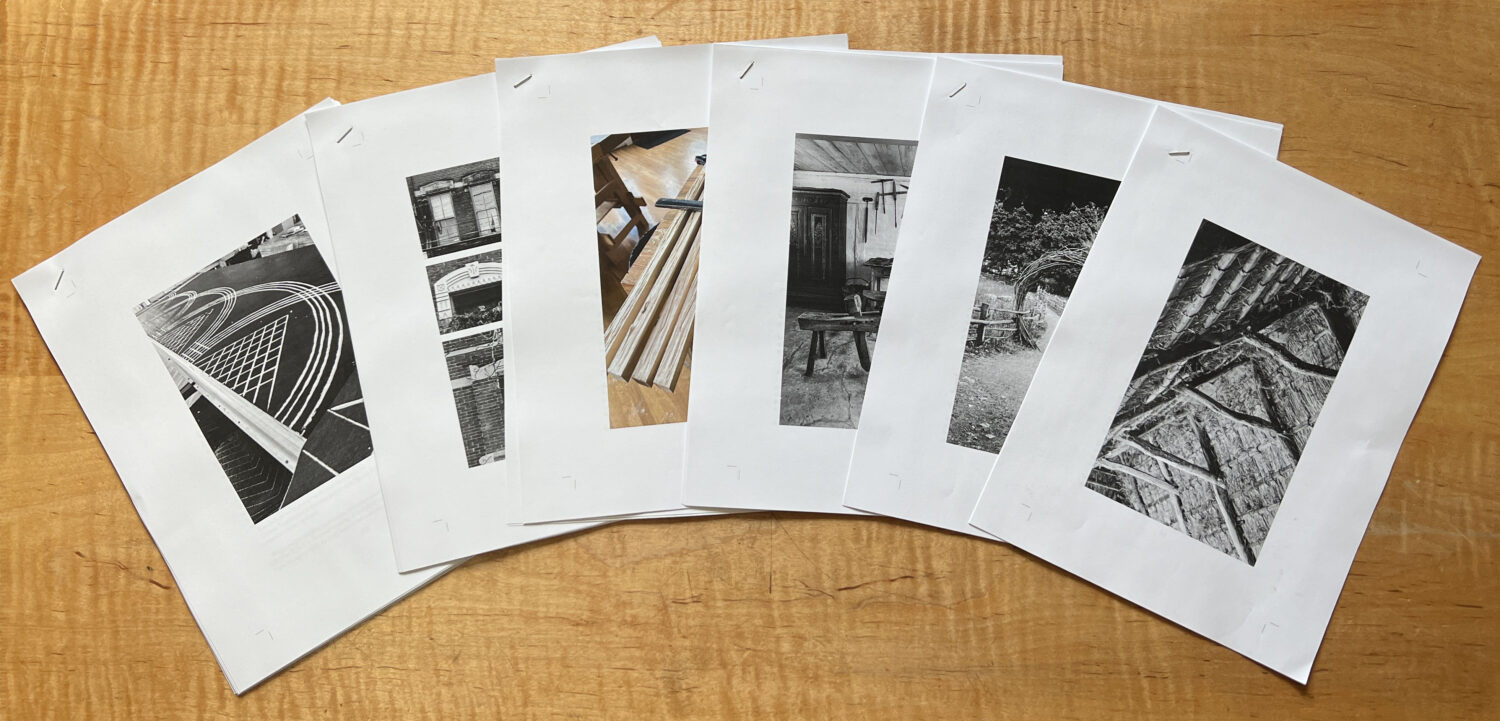
Update: Comments are now closed. And I remembered today that next weekend, I’m teaching a class on Sat.-Sun. So I’m afraid the next Open Wire will be on March 16…unless I can cajole one of our authors into doing it next Saturday.
Chris is in Florida through next week to teach two classes, and is then taking a few well-earned days of vacation with his wife, Lucy May. (I expect he’ll pop in from time to time to answer, or comment after hours on chair questions and the like.) In the meantime, I’ll be here editing his first six chapters of “The American Peasant,” and today and next Saturday, answering your woodworking questions.
So post ’em in the comments section below, and I shall do my best.
Comments close at around 5 p.m. … though possibly earlier if a personal commitment gets rescheduled for the afternoon. So don’t leave it until late to pose your question!
– Fitz
Is there an Easter egg in the blog photo from last Saturday’s Lie-Nielsen event? In bottom center of the frame on the corner of the bench closest to the camera, the mythical Lie-Nielsen marking knife appears to be making a new product announcement. This same knife also appears in the Lie-Nielsen catalogs in the double page spread of “Core Tools” from at least 2015 to 2019 without label or attribution and certainly not for sale. Were you party to this tomlienielsenfoolery? Will the knife be on sale soon?
The wooden handled marking knife, on the corner of the bench? It’s not a Lie Nielsen tool, though I think they made the handles. The blades were from Nic Westermann. A few years back they sold a limited supply of these, but when they were gone, they were probably gone forever. It is a beautiful little knife.
My favorite Lie Nielsen unicorns that I have actually handled over the years were a prototype Millers Patent plow plane, and their version of a Stanley 72 chamfered plane. I don’t need either one, but I’d probably buy them anyway. They were pretty sweet.
I was also drooling over the plow plane and yeah I’d probably buy it too even though I’d have to do some mental gymnastics to justify to myself how I really, really do need it. I do keep hoping it shows up on the website one day.
I think that’s simply the knife in the travel box, sorry. (That blade is by Nic Westermann – never a production knife.)
You’re no fun. Next thing you’re going to do is tell me Roy Underhill and Tom Lie-Nielsen aren’t really the same person.
When making a chair, is there a reason to use non-tapered tenons vs tapered tenons?
What makes a Windsor chair a Windsor chair and not just a fancy stick chair?
Or a forest chair . . .
Re stick chairs: https://lostartpress.com/pages/an-introduction-to-stick-chairs
Most of the vernacular stick chairs Chris has seen use straight tenons, but tapered tenons are more forgiving. https://blog.lostartpress.com/2020/03/07/reason-enough-to-ream/
Thanks!
Has the elevator in the Anthe building been approved yet? Have the sales provided any more room? How is Kale doing with her toolchest?
We don’t have an elevator. We have a materials lift. (And I don’t know yet if it’s all finished) And yes, the ADB sale cleared a lot of room…but not quite enough. Hence this ATC one.
Kale has been busy all week helping with a class, and is working in the warehouse next week, so there’s been no more time to work on her chest. But the dovetails look great!
While we are talking about her, is her name pronounced like the vegetable, is it an “interesting” spelling of the sound “kay-lee” or something else that hasn’t occurred to me? hate to have a ton of folks garbling a name…
Esther whose mother was Barbara Jean when both names were popular and made it a point to try to give 5 daughters both ordinary and unusual names..
I asked her the same question at the Lie-Nielsen event. Kale is pronounced like the vegetable.
Thanks for the updates.
What is Chris’s fovorite block plane? He mentioned it in a video, the LN ??
Thanks.
Yes, the Lie Nielsen.
LN 60-1/2.
https://www.lie-nielsen.com/products/adjustable-mouth-block-planes-?path=block-planes&node=4072
Good Morning Megan!
Thank you for doing this. It is awesome. I am making a staked stool out of a half walnut log. I started drilling out tapered tenons with the large tapered reamer but then I wasn’t sure if the holes for the tenons needed to be through the top. Drilling them to enable the tenons to protrude through the top and be wedged would make the holes really deep (the log is 6” at its thickest) and I would have to widen the tenon holes to accommodate the width of the leg below the tenon so the tenon could go all the way through the top. Do you think the tenons need to be through and wedged? Or will the leg joints be strong enough if they are just tapered and not wedged? Any other advice?
Thanks.
Josh
I’ve seen plenty of half-log benches on which the legs didn’t go all the way through. And sometimes those legs fall out when you lift the thing, but they’re easy to glue back in! (You could, I suppose, “fox wedge” them – but that’s a bit of fuss that likely isn’t needed here)
I just cut down a 24″ diameter silver maple and am getting it slabbed up. It’s on the light side so I thought it might make good chair seats?
Scott, I just finished turning a large bowl in silver maple. As it dried it moved a bit and it is soft (though not as soft as white pine). I would think it would make very nice seat wood.
A quote from the Book of Chris:
• almost any species
• air-dried, kiln-dried or vacuum-dried
• a softwood or hardwood
• sawn or riven
• ring-porous, semi-diffuse-porous or diffuse-porous
• from the lumberyard, the log yard or your backyard.
Put another way, almost any wood can be used in a chair as long as it is strong enough, dry enough and the right size.
I would welcome some help making a “tough” decision. I am getting ready to make a Welch chair and am in the best of positions. I have access to slabs of both red and white oak. Both slabs are wide enough for single piece seats, very straight grain and each slab actually has enough wood for two seats. I like working each of these woods and either is going to work given the chairs destination.
Thoughts on which wood I choose to work with…
I am the wrong person to ask…because I will choose white oak over red oak every time. I just think it’s prettier! But red oak will also make a perfectly nice chair seat. So make two of each!
Fitz, I was looking for a reason to not use the white oak. Given your response, white oak it is. Thanks!
No question, just a comment. Thank you all so much for putting on the Lie Nielsen event! It was great! I went on Friday and it was a wonderful day. Took your advice and went to Libby’s; yum! Thanks again for opening up your shop for us to visit and hang out!
Hi, I have a book query. Who names the books you publish, and is choosing a title simple or a cause for agonising?
It’s usually a discussion between the editorial team and the author(s). Sometimes it is agonizing, and other times not.
Tenonned shaker style knob: do you use glue or is friction enough to hold the knob in place? The instructions from the maker « The tenon is pushed or tapped into a ⅜” drilled hole. It is a time-honored method for mounting which does not require a screw. This traditional alternative endures because of its simplicity, reliability and strength. »
I turn my own, have them protrude a good quarter inch on the inside, and wedge them. My 2 cents.
I ave always either used glue in a blind hole or wedged them from the back in a through hole. But there’s no harm in following those directions. If it ever does pull out, simply glue it back.
Another option which I do on occasion – Leave the knob’s peg long; install the knob and mark the inside of the drawer face on the peg; remove the knob and drill a vertical hole through the peg partially on each side of your mark; reinstall the knob, drive a pin through the hole and then trim it shorter. It’s really just a small scale tusk tenon and takes longer to describe than do.
Happy Texas Independence Day. I have an anarchist workbench question. For the vice chop I was thinking of laminating several pine boards together. Why are they never laminated together perpendicular to the bench? Meaning, If I laminated 5 pieces at 1.25” x 3” x 30” I can have a nice wide chop and the area for the crisscross brace can be beforehand like the tenons on the legs. Is this a good idea or am I just creating more problems for my self?
Huh. Never thought about it. It seems like more work, but I can’t see why it wouldn’t work as long as the wood is dry and well prepped (wouldn’t want cupping). FWIW, though, I’ve never longed for a vise chop wider than the 9″ one on my petite Roubo – more chop, more to run into while planing.
Finished the exterior and moving to the interior of my ATC. Exterior is pine with a few tight knots. What wood combinations do you think look best for the interior? Thanks!
Chris likes a prosaic combo of pine, with white oak for the bottoms and runners. I guess I’m flashier…I like walnut with hard maple (and figured hard maple for the till bottoms…even though I curse my choice every time while planing it).
Hi, Megan!
When using the figured hard maple do use one wide board, or tongue and groove to join narrower pieces, or something else?
I usually use pine and quarter sawn oak, but really like the look of the maple and walnut!
Thank you and Chris for spending your Saturdays answering questions!!
I’ve done both – single board and two boards (shiplap joint). The two boards are arguably easier to fit because you have to fit only one 4″ (or so) wide board; the other can be a hair short.
I’m building the AWB, except 6’ long. I’m planning on 1’ overhangs on each end, with a 4’ base. What are the considerations for scaling down the planing stop location?
It’s typically an inch or two to the left of the leg vise chop (if you’re right handed…to the right of the chop if left handed, and the chop/stop is on the right-hand end)
I have been eyeing up Chris’s Shop of the Crafters Morris Chair project from his Popular Woodworking days. White oak is apparently a very hard commodity to come by where I am, but cherry is plentiful and cheap. So I am thinking about substituting cherry for the project. Should I be at all concerned about the strength of cherry for the slatted seat base?
Don’t take this to the bank, but I think you’ll be fine with 3/4″ cherry (I believe those slats are 3/4″, anyway – haven’t looked at that projects in ages). I have bed slats that are slightly less than 3/4″ and poplar, and they hold me and a heavy mattress.
Hi, any word on a release date for the saw sharpening book? Thanks!
I am done with the initial editing and design, and am awaiting a few image things to be wrapped up. Then, Chris will have a look, and I’ll tidy up any problems he spots. Then it’s back to the author and a copy editor, then final cleanup. So, with that in mind, my best guess is late May. But don’t hold me to that!
I tried to cook a batch of your Piggly No Wiggly recipe yesterday. Either I’m blind, or the blog post introducing it didn’t say whether the 4 parts of both water and gelatin were by weight or by volume. I tried weight first as it was easier to measure precisely, and ended up with a chunky goop the consistency of marmalade that was nigh impossible to stir, let alone shake. As I didn’t know the expected consistency, I didn’t know how much water to add to salvage it without potentially ruining it, so I chucked it into the trash.
I tried again by volume, and this time got a thick liquid. It still didn’t really slosh in the bottle when shaking it, but after a single sous vide cooking and a night in the refrigerator, it’s looking decent.
The instructions say to cook it a second time the next day for it to be ”done”. Can this second cooking be postponed until the glue actually gets used, or does it always need to be done on the next day as a part of the process to make the glue viable, even if it goes right back in the refrigerator for long term storage?
By volume. And you need to cook to a second time before using it. (I don’t understand why – but I do know you have to!) I don’t know about postponing it…I’ve never postponed the second cooking for more than a weekend. But my guess it that it would be OK to leave it for awhile.
Ahah! The volume thing was also in the comments of the recipe post, which I neglected to check. And thanks for the process confirmation! Time to fire up the sous vide again…
Also, hide glue is pretty forgiving. You can add water later if the glue is too thick. If it’s too thin, you can reduce it like a sauce in an open vessel as long as you don’t overheat it. Don’t fret too much over the actual recipe. In my experience, recipes don’t transfer exactly between different types of glue granules. They are more like guidelines. The recipes, not the granules 😉
Good morning. I drilled 1” dog holes in my bench to use the crucible holdfasts but would also like to use a couple Veritas hold down clamps which are 3/4” Do you know of a way to get 3/4” holdfasts or other hardware to work in 1” holes?
You could make a “sleeve.” Cut a 1″ dowel, and drill a 3/4″ hole in the center.
I would try Lewis’ suggestion. Or drill a 3/4″ hole where it’s needed (I have both sizes of holes in two benches. It stops looking weird after a few days.)
Hello…
When building a workbench, generally, is it better (stability-wise) to add weight to the legs/stretchers or the bench-top i.e thicker legs vs thinner bench-top or vice-versa?
And are they any knockdown joinery examples for securing a bench-top to the base? my workbench has to be knockdown so I was thinking of using a variation of a tusked tenon joint of sorts to pull the bench-top on to the (short) top stretchers of the table legs…
Thanks!
Lino
I like a thick top so it doesn’t flex. I’m happiest with 4″-6″ (cue the jokes), but you then need thick legs to hold it up. I have not seen a knockdown bench with a top that thick, though. And every solution I have seen has been sub-optimal (because it allows movement, at least over time). Your tusk tenon idea might work though, but I suspect you’ll have to knock the tenons tight every so often (which is easy to do, of course). But Chris has seen and built many more benches than have I, so perhaps he’ll weigh in tonight.
Thank you!
This is a quick sketch of what i was thinking, roughly to scale with a 3″ top.
https://imgur.com/a/85dsF8j
My first bench was (and still is) a variation on Will Myers version of the Moravian workbench. I sometimes need to give the tusk tenons a whack. The bigger issue was that the opposite end of the top (which sits on pegs) kept kept levering up when I was planing heavy stock. In the end, I drove some screws in from the bottom to keep it in place.
There’s Chris’s knockdown Nicholson bench, which uses threaded hardware and clever chunky bracing.
Oh sure – I was just thinking thick tops.
Just throwing this out there. Truper, a Mexican brand, sells new spade bits with the spur cutters like the spades of old. They are not Wood Owl or Irwin quality, but they cut, and are sharpenable. Are they obtanium in the USA? ¿Quien sabe?
No clue; haven’t Googled those. not heard Chris mentioned them. Perhaps a reader knows?
Might I ask when Matt Cianci’s book on saw sharpening will be coming out? This month? I remember it was supposed to be Feburary, but I understand publishing delays (I’ve been through them myself). Thanks, Megan!
I am done with the initial editing and design, and am awaiting a few image things to be wrapped up. Then, Chris will have a look, and I’ll tidy up any problems he spots. Then it’s back to the author and a copy editor, then final cleanup. So, with that in mind, my best guess is late May. But don’t hold me to that!
Clamping Question
I would like to glue up laminate some walnut (about 5 ” x 2″ x 36″) with final dimensions of 24×36; my F-clamps are not long enough so was thinking of using/making some sort of wedge clamp assembly, just not sure if the force is enough to get a good glue up…
(and anyone who has done this, your experience, results would be appreciated)
Lino
It worked for Roubo, so I say go for it. https://blog.lostartpress.com/2022/05/03/roubo-on-panel-glue-up-glue-clamps/
Megan,
Picked up a chest that someone has partially stripped the stain off. We would like to paint it with linseed oil paint. What is your latest recommendation on how to use linseed oil paint on a project like this.
Thanks, Joe
Erm…I don’t really have any experience using linseed oil paint over a stain. My understanding is that it performs best on raw wood, because the oil soaks in. So based on that singular bit of knowledge, I’d strip it first. Or, I’d spray or brush a coat of shellac as a sealer, then use faux milk paint over it.
According to both Allbäck and Ottosson, linseed oil paint will adhere to almost any surface, including previously finished wood. I have painted with linseed oil paint on top of modern acrylics, with excellent results, even for something (my Stevenson screen, to be exact) that sits outdoors in all weathers. So I’d say, maybe try it on a small patch first to be sure, but otherwise, go for it!
Hi Chris and Megan! I have a question about the pristolnic. Per your post, I’ve made a couple of them—they’re great fun and, as you said, a great way to practice carving lines and circles. But now is time to carve the imprint on the bottom: you had a picture on IG of one. You claimed the process was “Midwestern interesting” which I read as “Giant Pain in the Ass.” Any tips or tricks for doing it the first time? Looks like you used chisels for it—any certain ones? I’ll take the plunge eventually, but would love some advice. Thanks again so much!
Jake
All I can say (having not tried it myself) is that he used sharp LN chisels and some choice words.
Design question. I am planning to make a Boggs style ladder back side chair and am thinking about what table suits it best aesthetically. I am really interested to hear any specific recommendations for my situation or the general process others follow to come up with a complimentary table design. This question is for Fitz and Chris but I hope others chime in!
I think the lightweight look of a Shaker-ish trestle table looks great with those light-looking chairs – and maybe “modernize” it a bit by having the feet take curve cues from the chair slats?
Hi Megan!! Do you have any experience with frame saws for joinery and ripping and the smaller bow or turning saw for cutting curves? I am fixing to add both to my shop.
In the absence of a band saw, they work great. Dunbar used to cut seats that way – that video we shot for PW is probably still on the interwebs somewhere! But I haven’t used a large one for resawing, other than to try it out a time or two.
I’ve had an issue when I glue up panels (usually 1/2″ or so) that when I go to work with them later, some of them come apart along the seam. They appear fine when I test them after the glue dries. I use liquid hide glue for all my joints. Someone told me that it’s not good for panel glue-ups and I should use PVA. Thoughts?
Well, panel glue ups used hide glue for centuries, so…
We use PVA for many panel glue ups simply because it can come out of the clamps sooner, and when we’re doing panel glue ups, it usually for a class and we need a lot of them as quickly as possible. But I almost always use liquid hide glue for my own work, and haven’t had any trouble.
Are you doing a spring joint? And if so, is it possible there’s too much spring?
I used liquid hide glue for all my panel glue ups for my six-board chest a few months ago. They turned out great and held together really well. Are they coming apart at the ends or the middle of the glue line? Partial separation or complete failure of the joint? How cold is your shop? I had the luxury of time and my garage was 60 F. Concerned the glue would need more time to cure in the relative cold, I left them in the clamps overnight and didn’t stress them for another day after that while I worked on something else.
Just a smart-purchase question… I’m considering a few items from Lee Valley. Do you know of any discount opportunities? Perhaps discounts are offered to tool collector club members somewhere?
I do not.
I believe if you subscribe to their newsletter, you receive a one-time 15% discount on your first purchase.
Don’t they do a discounted gift certificate once in a while, like a $600 gift certificate for $500? (Don’t quote me on exact figures!) I think it’s at year’s end? Essentially you can buy a discount code for a future purchase.
I’ve meant to buy them when they’re available and then sit on them until I was ready to get something, but because I’m a spaceman I’ve never done it. And then the next time I pay full price on a big order I feel like a dummy.
Enjoy you time in Florida Chris.
I’ve got a bunch of walnut log splits waiting to be turned into Design Book drinking table legs. I’m thinking my next step is milling them square-ish on my Delta 14” bandsaw, which I’ve not done before. My current plan is to make a sled that rides in the miter slot, and somehow fix the splits to the sled.
Any helpful hints for that process? Start with the sapwood down and log center pointing straight up? Split face down?
They’re split already? Then I’d just split them to slightly oversized for the legs. (Walnut splits pretty easily.) That way, you’ll have grain with no runout. But if you want to saw them, I wouldn’t use a sled – you want to be able to saw them at whatever angle needed to end up with no runout, so you might need to make adjustments as you saw.
I’ll have to remind my logs – the one I was wailing on yesterday seems to have forgotten 🙂
These logs aren’t exactly green. I scavenged them from a neighbor before the tree service could take them away – they may have been standing dead before that – and after splitting I had them sitting under a tarp for a few months. I’m trying to get them down to about 3” square so they can finish drying out a little more quickly.
Anyhow thanks for the reply – I’ll watch out for runout.
Chris recently posted a video where he was experimenting with locust lumber. In that video he was splitting the wood with a hacking knife. Where does one get such a thing?
That one is blacksmith made…and while there are commercial hacking knives available, they are comparatively lightweight. (Also sold as glazier’s knife, I think.) So if you want one for splitting pins and the like, I’d find a blacksmith. (Or use a 2″ chisel, which also has enough heft for the work)
Sounds like a Crucible Tool opportunity 🙂
Clark,
Jason Lonon toolmaker makes some. He calls them wood cleavers
He makes some very useful tools.
Plus one for Jason Lonon.
Hi Megan,
Please consider this question as arising out of a case of completely unwarranted but no less real for that heebie-jeebies: when making an ATC, what would you consider an acceptable margin of difference in length between opposing pairs of panels? Obviously one should, would and will shoot (literally, given the involvement of a shooting plane) for perfection, but I dare say a few gnat’s whiskers off from that pinnacle of achievement won’t spell disaster?
(I know; everything willimmediately implode, opening a black hole into which the entire workshop will disappear, but let’s put that to one side for the moment.)
In other words, how heavy a gnat with how much of a handlebar moustache would, in your experience, still pass muster, were perfection not to be achieved?
Cheers and all best,
Mattias
If they’re off by a gnat’s ass, it won’t matter a great deal. More than that, though, and the case might be a little too much out of square to make it easy to fit the till bottoms. But you can be a bit out of square and kick the problem down the line, for sure. If that’s the case (ha), do a two-part till bottom (floating shiplap down the middle), and you have to fit only one of those 4″ wide (or so) boards to the runners – and that’s pretty easy to do with a judicious use of taper planing on the end grain. And that might be the easier solution when doing everything by hand than making the 24″ wide pieces dead square to one another.
Thank you, Megan! We’ll see where it ends up, but the 27” capacity shooting board I built over the last few days seems to be holding up – at least everything is coming out square according to my 24” square, so hopefully I’ll be able to go gnat’s ass hunting with sufficient success. But I’ll keep in mind the two part till bottoms (which I were planning on, anyway) as a potential remedy if the carcass doesn’t turn out square enough (there’s still the joinery and assembly to go awry on me).
Cheers and have a great weekend,
Mattias
Hello, I have been wondering for quite a while, have you considered republishing The Handyman’s Guide (there are other names for it too) by Paul N. Haslack? It is a wonderful book
I’ve heard rumor that someone else might be republishing one of Hasluck’s books. And it’s easily available on used bookstores and online as a print-on-demand book. So it’s not likely one we’ll offer.
Thank you. Yes, it is easily available, only that the quality is very poor. It deserves better!
I’m gonna make a few rulers and yardsticks with some waste. I want to decorate them, at least with numeric legends but maybe also other designs. Do you have a suggestion on paint for this? I was thinking I’d do whatever paint for the legends and then a layer of BLO and soft wax over that, but I’m happy for any suggestions.
Hmm…I would probably choose acrylic, for its quick dry time and not much bleeding if painting on the numbers/tick marks. But I might also paint the whole thing with linseed oil paint, then carve through it. But that would be fussy, delicate work!
I actually am thinking of carving it, I just would rather it be black on wood than wood on black, you know?
Japan colors might serve you – fast drying oil paint favored by sign painters.High quality pigments. Bone black Is a true black.
I’ll see if I can get it!
Is there a “preferred” wood for rulers/yardsticks? Or is this a case or the best wood to use is the wood you have.
I don’t know! I mostly just have offcuts just the right size. I’ve already made some out of hard maple and will use red oak next.
Most quality places use quartersawn hard maple for rules.
Good morning all and thank you for all the good info. I have been using plywood and power tools for building cabinets and such. Now that I am using hand tools (much quieter), I was unsure of how plywood and handsaws and plane work together. Do i have to worry that my nice carcass saw dulling quickly when it hits the plywood glue? Similar concerns with planes reacting badly to plywood. John
There’s a lot of glue in plywood, so yes, it might dull the tools more quickly – but if you know how to sharpen, no problem. I’ve used my planes and saws on plywood, and both survived. (But I don’t surface plane plywood, because I’d be afraid of planing through the top layer (the nice layer) of veneer).
Do you guys have any recommendations for swing-arm lamps for a workbench? I’m looking for a buy-it-for-life type of thing.
Thank you both for creating this community. I live in Los Angeles and wish I lived close enough to drop by your events.
Good question! Following.
Every time I think Chris has found his Ideal Lamp, he buys a new one. So I have no idea what he’d say. I still like the one he gave me 20 years ago – a vintage (late 50s or early 60s I think) Luxo magnifying lamp. That one lives at home…I’m afraid if I bring it in here he’ll swap it out for something else in his quest for perfection!
If you meran to buy new, I have been very happy with the Luxo L-1 E27, visually famous from the Pixar logo. Alas, like so many other classic products, these days it is “Designed in Norway. Made in China”, but for all that it is still very good.
For obvious reasons (I’m not dead yet, is what I mean) I cannot say with authority just how for-life it will be, but compared to the Ikea knock-off that I used to use, I’d say it’d odds-on it’ll outlast me. No sagging springs, no issues.
I have a total of five in my workshop, and for the one on my bench I also bought the heavy, round base. I know many people, Chris and Megan included, just make an adapter to fit in a dog or holdfast hole, but I like the complete freedom of positioning that the round base gives.
Please note that there are two versions of the L1 on the market; the E27, which takes any standard lightbulb of your choice with that fitting, and the LED with a built-in LED light source. The latter is about three times a expensive, and as I like to be able to pick the light source to fit my needs (high colour temperature and good RA value in combination with a suitable lumen rating), I have gone for the classic model. I’m not saying the more expensive LED version is bad, but I wouldn’t buy that without having seen it for real first, not least given the price. The classic should retail in the region of $125–150, while the LED one is closer to $400.
I don’t know where top best buy them in the U.S., but some googling paired with due diligence ought to find one a suitable vendor.
With all this said, second hand architect’s lamps are likely to be great value for money – including vintage Luxo L1s!
Just wondering the location of Chester Cornett’s presidential rocker he gave to Richard Nixon? Does it ever come out for display? (It is an election year) Such a humbling gift for our nations highest office. Always loved that picture in the Oval Office !
According to “Beyond the Narrow Sky” (2014), it was in the Nixon Presidential Library collection in Yorba, Linda, CA. https://scholarworks.moreheadstate.edu/cgi/viewcontent.cgi?article=1012&context=kfac_exhibition_catalogs But I don’t know if that remains so.
Hello Megan
I was putting away my tools last night and I pulled out the blade/chipbreaker from my LN No. 4 to clean and wipe down with oil when it slipped out of my hands… and landed on the concrete floor of my garage. I really need to put down some rubber horse stall mats. The left corner of the blade/chipbreaker seems to have been the point of impact, probably 1/16” ding there with a tiny gap between chipbreaker and the blade. Would you just file the ding on the chipbreaker down then try to flatten it on a granite stone with abrasive? Marching that 2 degree angle would be tough for me I suppose. Maybe just rounding the corner of the chipbreaker would help some. The blade has a small ding too but I think honing the primary angle and microbevel can easily correct the issue. I’m also considering swapping the stock blade and chipbreaker from my No. 5. Even if the repaired chipbreaker isn’t perfect it should probably be sufficient for jack plane use, right? And the corners of the curved jack plane blade rarely if ever see wood…
Currently the stock blade sits unused because I use one of their curved irons, so once I hone a slight smoothing plane iron camber on it it should be good.
Bummed, but just trying to think out solutions here. Any advice is appreciated
Regards,
Adam
Yep – I’d file (or light passes on a grinder), trying to match the angle, then clean it up on a stone. If it works out, awesome! But if it gives you trouble: https://www.lie-nielsen.com/products/chipbreakers-2-chipbreaker
On the blade, grind it out, then sharpen and hone.
My horse stall mat has saved me several times, FWIW (well actually, it saved my chisels)
Horse stall mat? Please say more; this sounds like something I need at my bench.
Grocery store glue. I’ve made some and it works well, but I had a real problem maintaining the temp range on the stove. I’ve looked at glue pots online, but they all advertise a temp range that starts at 212 degrees. What do you use to make and then heat the glue?
JW
We make it by heating it in an industrial water bath (a medical grade one from eBay). But we used to use a sous vide pump for the home cook. You could also heat it that way, or use a wax warmer, a small crock pot – or a mug warmer to melt small amounts. I want to try this, but haven’t yet, https://www.webstaurantstore.com/carnival-king-single-32-oz-sauce-topping-bottle-warmer-with-squeeze-bottle-200w-120v/382SBW1B.html
That one looks interesting, but this is what I used and it works well. https://www.amazon.com/gp/product/B007ROD298/ref=ppx_yo_dt_b_search_asin_title?ie=UTF8&psc=1. Pretty inexpensive, just use a digital thermometer to “calibrate” the dial and mark it for the temp you want. I keep the glue in a glass mason jar sitting in a water bath in the main chamber.
Then I’d carve then carefully paint with acrylic.
Can you point me at a guide or source, or just give me some advice on using shooting boards? I’ve made one and tried to use it to square the ends of legs. I must be doing something wrong.
I use my no. 5 with it. I think I’ve struggled to set it correctly—too fine a cut and it doesn’t bite at all, too deep and it refuses to cut and bounces off. I don’t think I’m that bad at sharpening, but who knows?
Do you keep a less-cambered iron for this?
Our shooting planes have straight irons – no camber, and they both have skew blades, which makes them a little easier to use…but specialty planes are pricey. So if you have any flat-sided plane w/ a straight iron, give that a go. Oh – and sharp – it must be sharp. (FWW has a couple good articles/videos online about making and using shooting boards.)
I like the weight of my #5 plane for shooting – I have a straight iron that I swap in (instead of the 8″ cambered iron) when doing so. That iron also gets used for leveling edges that are too short for my #7.
One of the tills I made for ATC is sticking when move it. What are good ways to resolve this? , it kind of tweaks, but I’m having a hard time even tell what is occurring.
Likely, it’s racking a little bit (which means the bottom is perhaps one or two shavings too short). I assume you’ve already tried waxing the ends of the till bottom? Next (assuming you don’t want to put on a new bottom), I’d add a thin film of uhmw tape to the chest wall where it contacts the till bottom.
My apologies – two items – a comment & question:
In reference to Chris’ Substack post this morning – I noticed in the latest images shared that he is sporting the beginnings of a very excellent two tone, white/black, “evil villain” beard – could this not be his “thing” ? Though this might take some work to maintain the color scheme long term.
As for the question, I know this has been addressed, several times – what brand & grit grinding wheel do you all have on your shop grinder?
Whereas I’m full on white haired these days..but also semi-villainous 🙂
Norton 3X grinding wheel
Do you ever take measurements off chairs you make to see how close you come to the planned rake and splay? I’m starting my next chair and wanted to tweak the splay from the previous chair, but I’m finding I’m a few degrees off of what I intended. I’m not sure if this is more due to inexact reaming or after the fact measurements.
A Chris question, I’m afraid.
Rake and splay are ideas. The reality is always a few degrees different depending on the mortises, tenons and the stretchers. If you want to hit a number bang-on, you are going to have to invest in CNC.
Two questions:
Do you have any recommendations for a good bandsaw for resawing? I know you like the Jet metal/wood models, but their resaw capacity is only 6″. Ideally I’d like something that allows at least 12″.
How do you go about trimming 45° mitered corners, say for a dovetail joint that is mitered at the edges? Or perhaps for a secret mitered dovetail. Is there a good jig/fixture for that?
Thanks!
On the band saw, I can be of no help I’m afraid. We used to have a 17″ Grizzly, but it rarely got used, so we sold it. On a mitered dovetail, I don’t think I can explain it w/out pictures…so I’ll direct you here: https://www.finewoodworking.com/project-guides/joinery/mitered-dovetails … unless you mean full mitered dovetails, in which case: https://www.lie-nielsen.com/products/furniture-making-techniques-secret-mitre-dovetail?path=home-education-videos-david-charlesworth&node=4245
Good afternoon, I wanted to ask if the André-Jacob Roubo Deluxe Edition book will ever be available again? the BIG book. I have missed out on purchasing the book in the past.
Thanks
Mikael Fischer
I seriously doubt it.