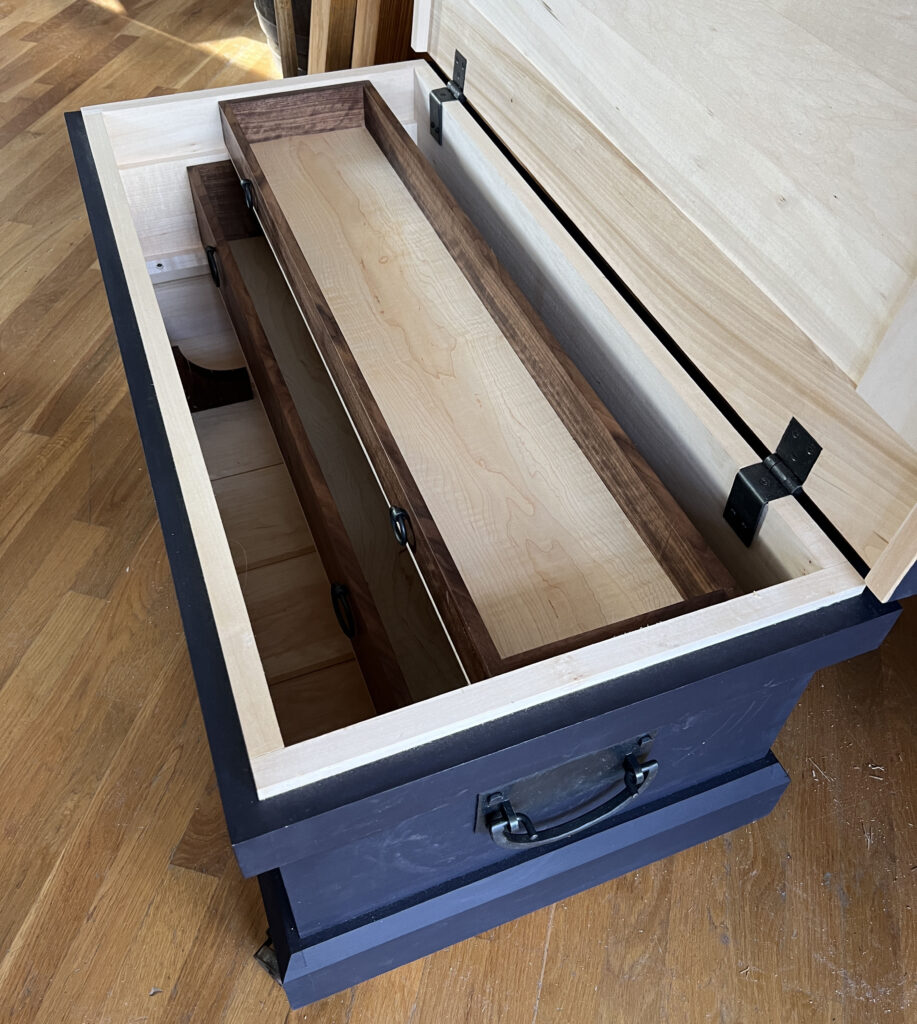
It’s Open Wire time, where you can pose your woodworking questions in the comments section below and we’ll do our best to answer them.
Chris is also getting ready for a class that starts Monday, and I’m getting the class pages ready for the July-December 2024 classes (they’ll be announced soon!)…and finishing one last thing I forgot about on the chest interior shown above: a plane cubby. One simply must have a plane cubby. So there may be lag between your question and our answer.
Comments are now closed….
– Fitz
Good morning and thanks so much for taking your time to answer questions. Is your 2″ Barr chisel long enough to use without a mallet for paring?
Absolutely. And it has a good deal of weight, which is helpful with paring cuts.
I have a very small shop. I mostly use a hepa “dust extractor” and cyclones for sawdust control, but there is still some very fine dust that gets through. I don’t have the ceiling height to hang a dust filter – would a Corsi-Rosenthal box on the floor work ? (they’re really light and easy to move around).
Thanks
If you have the floor space, it will work fine. The boxes are a bit fragile.
When you use linseed paint you mentioned doing a primer coat of oil. Do you use purified linseed oil or boiled, or does it not make a difference for indoor furniture
I haven’t noticed any difference. I’ve used boiled and purified.
Love that color. Are the dimensions for that size of chest available?
Thank you. This one is 16″ tall, 39-3/4″ wide, 19-3/4″ front to back – or thereabouts.
Dear Chris and Fitz,
I have a few questions for Open Wire tomorrow please. I’ve never ask on Open Wire so I probably send one each Saturday?:
I’ve coloured in the main question without my caring on…
Coping Saws – SORRY!
I am tuning up an Olsen coping saw (India it says) from LV and, as you mentioned, added a lock washer on each end on the outside of frame which I rounded/smoothed over the sharpness of the ring ends with small file and steel wool.
The part about “filing flat(?) areas where the blade clamping mechanisms meet the frame” is where I’m lost. Could a pic be posted of what those look like? With a triangular saw file or rectangular needle file at certain angles or…? And is the area to be filed on the outside of frame just under the added slit washers?
Band Saw Fences for my 1060’s USA Powermatic 14” Band Saw (my only power tool and from my Dad) –
ANSWERED IN AMERICAN PEASENT – Thanks!!
Swan Neck Chisel Use? –
In one of your inside your chest blogs but never read in my copy of your ATC book but maybe it saves narrow bench chisels edges from flipping out the waste in mortises? Are they worth it?
Stanley No.45 Combination Plane ? –
Curious as I’m thinking I could use a larger plow plane than my wee Record 43 and read where you use a 45 for a plow plane “hate them” I believe is the word Patrick Leach used in his write up of the combination planes and that’s where you found yours!).
Are you happy with the Stanley No.45 after some use and does it make since to purchase without the cutters and add them as needed? It seems a boxed 45 with the full gear is as much as or more $ than a new LV Combination plane? Maybe the Stanley No.50 or even 44?
Tongue and Grooves –
With my LN no. 3 arriving today (with shipping and customs to Canada as much as the listed plane making LN in the future bleak) from LN I’m afraid a LN 48 T $ G is out of the question and I’m not too keen on tuning up a Stanley 48 unless they don’t usually require much. Done all the tuning up I ever want to do
and my artistic hand can’t take old blade flattening, etc… I read from Wood and Shop where a T & G can be made with a plow plane in the quantities I need such as a tool box on my list to build – I’m tired of all my tools on walls!
Or, can the bottoms and sides that are T & B be ship lap? We have ship lap and T &G made here in Newfoundland from local Black Spruce but it definitely has knots. What would the thinest board width be for tool chest…5/8”
Polissoir –
Do you still use? I haven’t read the entire Stick Book but can’t find mention of the Polissoir and wax finish in The Anarchist Design Book.
Czeck Vs Blue Spruce Marking Knives –
In PWW you reviewed the Check knife and seemed to like it. Still like it? It seems to be a fictional and beautiful knife as well. The curves on the BS look nicer but I don’t like the only way they come know with a replaceable blade and cheaper looking ferrule. I’m only looking at photos mind you since there are no woodworking stores within 1,000 km of me – none in the province of Newfoundland so your mentorship through your generous post and of course mainly your books have saved (haha!) me dollars – well maybe not yet but they will as I will by buying once.
Spokeshaves – Fitz, ow do you feel about your LV low angle shave that does curves and flats/concave? I was thinking about one of those and a flat LV or LN. Or, Should I skip the low angle? Doe either of you use/recommend the little LV Preston or small LN curved or flat?
Low Angle Block Planes – I noticed Fitz has the 102 LN low angle block plane. Is this better for smaller hands like mine or is the adjustable mouth too much to give up?
THANK Y’All (I’m from Lexington originally) VERY MUCH for your time and care of us out there!!!!!
Stephen Wiseman
Lumsden, NL
Canada
I do these one at a time.
I can’t vouch for the Olsens anymore. They were very decent. Now, not so much. I don’t have one handy, I’m afraid, and that was a LONG time ago. But I believe the intent is to file grooves in the flat to improve the grip of the metal bits. Use a small triangular file. Or the long edge/corner of any file on hand. Just make parallel grooves that are close together – every 1/16″ or so.
Thanks Chris and sorry about bringing up this. Maybe time for a KC or BS if I can justify it. I’ll try these tricks first.
ah, Thanks. I can chop a mortise decent with my 5/16″Ray Iles so thanks for helping me not spend on that save up for a decent coping saw.
Thanks Fitz. I’ve heard from others that the LA spokeshave is not easy but I wanted to hear it from someone (not just someone but you!) who actually uses tools to make furniture. Many , Many Thanks! I’m planning on filling up a chest like the one you are finishing and only keep or acquire tools that it will hold other than a few “wall tools”.
Thanks Chris. I may have to stay away from that finish due to my arthritis in hands and shoulders. Love the look though! I may make one sometime just to try out on a small project. My wife’s still asleep so I’ll go look for a broom….
Thanks! LV’s are much less expensive for Canadians as well. I had a LV small spokeshave just to see shipping and it was well over$100 USD for a one tiny tool. Love LN and just received my no.3 (it was the last iron one) but that cost more than I’d admit here after shipping, exchange rate, shipping and still dinged at customs. Still the no. 3 fits my hand like a glove and finally no fettling which I’ve had enough of and will be my only and last smoother. On the shaves, its LV for me then and looking forward to trying out PMV-11 blades as well. Again, Thank you both for helping me to direct purchases on what’s needed and what works!
Swan Neck: Skip it. It’s an emergency tool that I have to help students who have made a really awful mortise.
On the LA spokeshave and 102: I do not like that spokeshave; I bought it a long time ago, and keep trying to like it, but…I’m going to buy the flat Veritas shave (05P3373). It’s much friendlier in the hand, and the adjustments are superior.
The 102 is more comfortable, and it was my only block plane for many years – but I bought the 60-1/2 when I built a stick chair, and now I love it (because of the adjustable mouth). But I do reach for the 102 when the mouth doesn’t matter much.
Combination Plane: I had a 45 as my plow for years. Loved it. No complaints. They are quite common on the secondary market, so keep looking. You do not need all the cutters. Get a 1/4″ cutter to start – that will do about 90 percent of your work. Check with Lee Valley because their cutters for their combination plane work with the 45.
They have a T&G cutter, which answers your following question:
https://www.leevalley.com/en-us/shop/tools/hand-tools/planes/blades/75781-tongue-cutting-blades-for-veritas-small-plow-plane-and-combination-plane
The chest bottom can be shiplapped. I recommend 3/4″-thick stock.
Thanks Chris,
Would you recommend the 45 over the LV small plow or combination plane?
The combination plane from Veritas is fantastic. That’s what I now have. But that and the 45 both do the job just fine. The weight is helpful, which is why I don’t use the small plow.
Polissoir: I do still use them. They are great for finishing small surfaces. They are a workout to use, however.
In Ingenious Mechanicks, you describe many work-holding options for low benches: metal planing stops, the palm, the block and belly, side stops, dogs at the end for traversing, holes in a narrow V for edge planing, installing a vise, etc. You’ve also later mentioned a carving vise.
If you were to build a new Roman bench with only your favorite features, which would you include? Corollary: which have you decided are not worth it or not a convenient way to do that particular task on a low bench?
I am going to build one this year for a video. It will have a removable Hulot block, a movable crossbar planing stop, a removable palm, holes for dogs, carver’s vise, and a simple twin-screw. Basically the low bench I work on now.
I use the bench mostly for chairmaking and other staked work. Casework… not so much.
Any Dimensions available for the Hulot Block overall, the little steps, etc…
Thanks!
It’s in the book Ingenious Mechanicks. Search the blog. I’ve written about them before.
And I thought I looked – sorry about that.
Czeck Vs Blue Spruce Marking Knives: They are both great knives. There are a million good knives out there now. Back in the day when I was writing about them, there weren’t. I use the Blue Spruce, but it’s one they don’t make anymore (fixed blade that is long and thin). The ferrule is not cheap. It’s very high quality.
Don’t stress about it too much. Just buy one and use it. They all work. Even this one:
https://www.leevalley.com/en-us/shop/tools/hand-tools/marking-and-measuring/marking-tools/69870-veritas-workshop-striking-knife?item=05D2005
Thanks Chris!
Spokeshaves: Skip the low angle. Skip the Preston copy. Skip the Lie-Nielsens. I recommend spokeshaves with adjusters based on the Stanley 151. Lee Valley’s versions are excellent/perfect/no notes.
Low Angle Block Planes: I suspect Megan will chime in here. The adjustable mouth and the mass of a larger plane such as the Lie-Nielsen 60-1/2 are extremely helpful for helping to reduce tear-out.
I’ve been using Peter Galberts drilling guide for chair seats and I’m looking for options on bit extensions. Will the Go-Drilla grip round stock securely?
Nope. It is designed for 1/4″ hex shank tooling.
I’m working on my first stick chair, and have a question about the tenons on the sticks. I have an old 1/2 inch tenon cutter from my grandfather, that I’d like to put to use. I’m using straight-grain red oak for the whole project. Is it foolish to use 1/2 inch tenons instead of 5/8 tenons? Thanks so much!
You’ll probably be just fine with 1/2″. If it were me, I might throw in a few more short sticks to the design (if possible) just for insurance.
Very nice looking chest! Do you mind me asking where y ou obtained the hinges?
Thanks in advance.
Thanks – Horton Brasses (hand forged iron)
I’m making dove tails. I am switching from my two cherries chisels to ones made lie-neilson. The latter are beautiful chisels. Should I flatten the backs even though they are new? their primary bevel is 30°. They recommend putting a micro Bebel of 35° on them. Do you agree?
The backs shouldn’t need flattening – if a new LN chisel is noticeably out of flat, let LN know and they’ll replace it. But I do polish the back up at the business end every time I sharpen (if only when knocking off the burr). And yes, we both use a secondary bevel of 35°. Or 34.76°. or 35.21°. (In other words, don’t overly fuss.) Because it’s a lot easier to hone and polish a small amount of bevel than the entire ground surface.
Yes, Could you please provide more detail on the chest hardware and a picture of the face of the plane cubby? thank you
I can’t show this plane cubby yet…haven’t installed it! (It’s just a thin piece of wood to cordon off a block plane area(s) in the top till). I’ll post mine on my instagram in a sec (@1snugthejoiner).
The hardware is hand forged iron from Horton Brasses.
HF-51 Small Black Iron Ring Pull
HF-52 Large Black Iron Ring Pull
HF-46 6″ Black Iron Chest Lift/ Pull
HF-49 Black Iron Hinge
Question about the fine Crucible card scraper: I vaguely seem to recall (in sharpening tutorials?) that Chris or Fitz advising not to bother sharpening the ends of a card scraper since you don’t (shouldn’t?) use it for scraping. Personally, I find the Crucible card ends VERY useful for scraping small or narrow areas, plus it fits well in one hand while holding the work with the other. Am I missing something, or is my technique simply bush league?
I don’t know what Chris will say…but I sharpened on end on one side of mine two days ago, so I could get into a narrow space. But that’s the first time I’ve needed it. Your needs may vary!
You are fine. I don’t sharpen the ends because sometimes I grab the scraper by the ends, and I don’t want to get sliced. But if you are happy, I am happy.
I am building a Herculaneum workbench with a slab of white pine 3.5″ thick. Since the wood is soft, would it be a good idea to put in hardwood inserts where the holes are located and drill holes in the inserts for strength?
thank you
Nah. We have a white pine workbench here. It gets dinged more, but it holds its own and the holes don’t get wallered out.
Don’t make a clock out of it.
Hi! And thank you for doing Open Wire.
So I have made a pine side table that I am thinking of staining. However I have read that (1) pine is difficult to stain (too porous) and (2) you can’t make a cheap wood looks expensive. Are there stains you have found work well on pine? Is some kind of primer helpful? Thank you.
Staining pine is just about the last thing I would do to that wood. It blotches horribly, and the grain reverses in color. If you want to go on this adventure, you need to learn about wood conditioners, which reduce stain penetration and blotching. Bob Flexner has written many articles on this topic over the years. Here is a start:
https://www.popularwoodworking.com/article/wood_conditioner_confusion/
Pine will mellow with age. Add a shellac finish and it will turn a beautiful pumpkin color in time. And painted pine is great.
Gel stains are the best I’ve tried for pine…and it still ain’t great IMO. Do a test and see what you think. Beauty/eye/beholder etc.
“Doormaking and Window making” has been on my list mostly for the doormaking aspect. But something recently got me to thinking, is it feasible to make your own windows for a modern house? Have any of you ever done it? I know it’s technically possible, people did it for hundreds of years, but is it possible for a normal person to make a window that is comparable to what one might now buy? I’ve heard of the quotes people are getting for replacement windows and it’s astronomical and wonder if it’d be worth doing oneself?
Of course you can. By hand, the tooling isn’t all that big a deal for a simple window. I’ve made several transom windows for our building.
But if you are making something fancier (or a whole houseful of them), you need to invest in specialized tooling (either shaper cutters or specialty planes).
Thanks. What about efficiency? I’ve never made a window at all but can you approach the efficiency and longevity (not sure I believe all commercial windows are built for longevity) of modern ones?
If you can source the glass, then maybe. The Venn diagram overlap of people who make their own windows and people who are after energy efficency is pretty tiny. The best reason to make your own windows is for historic accuracy.
Do you guys have any thoughts or experience with the blue spruce mortise chisel? Looks like they have a strike plate on the butt of the handle and a metal rod that mates with a tang and there’s also a socket. Seems new and interesting but also a lot of removable pieces for something expensive that I would bang with a hammer.
I use the Ray Iles mortisers. Simple. Correct side geometry. A joy to use. You don’t need a steel rod through the handle. You just need to keep the chisel sharp.
If replacing windows for energy loss issues, keep in mind that the best modern windows being made have an energy efficiency rating only about 25-30% of that of an old R-11 2×4 stud wall. You won’t be able to get anywhere near that with a homemade window. Windows and doors carry a U-factor energy rating- simply stated, that is the mathematical inverse of the familiar R-value of insulation. In other words, a window with a .32 U-factor is similar to an R-value of just over R-3. (1 ÷ .32 = 3.125) If building windows from scratch for other craftsmanship/pride/emotion reasons, then I say go for it. But a lot goes into modern window and door construction for energy conservation, even with the crappy, overpriced ones.
I have made several reproduction windows for our house based on “Doormaking and Window-Making”. Once I found the book, the process was generally enjoyable.
If you make your own reproduction windows, you likely live in an old house. Unless an old house has been extensively renovated, windows are rarely the leading source of energy inefficiency. If the windows are an energy issue, then installing multi-pane glazing without stopping air leakage around the old windows is unlikely to be effective. (In my case, I made some attic windows to replace existing jalousie windows. That certainly improved energy efficiency by reducing airflow.)
My interest was to match the appearance of other windows while preserving the full window openings. All the contractors we found wanted to insert odd windows or install windows with fake muntins. No contractor we found had any interest in matching the existing profiles or construction.
I have also made some windows that combine interior windows with exterior storm windows: old-style double glazing.
Our house mostly has wood windows that are right around 100 years old. The original windows that have not been subjected to running water due to bad gutters are all in excellent condition. That’s true because of excellent construction and exceptional wood. In some places, previous owners installed plastic or aluminum windows that were “fancy” for their time. I suspect those windows now approach 50 years in age. These “new” frames are not in good condition and cannot be repaired. Many had to be reglazed because broken seals had produced foggy glass.
Make some windows. See how you like it. If you choose good wood and use the joinery described in the book, your windows likely will outlast many modern windows.
I somewhat disagree, if you can source the high performance glass and draught proof the window you’ve made with additional seals etc overall performance should be very good. High performance timber windows made by personals aren’t necessarily much different to historical examples and their performance is excellent.
Starting on Linseed Oil paints (allbeck). Working with hard maple the schedule is Linseed oil base, paint, buff with mirlon, then wax. One coat each not deluded. I don’t recall hearing of your use of the wax. Dry times are long due to shop hovering around 60f (I’ve been allowing multiple days for the paint and wax). Does this process sound reasonable?
Wax is always an option. Soft wax or renaissance wax looks great over linseed oil paint.
Looks great. What are the dimensions for the small chest?
Lou
Thank you. This one is 16″ tall, 39-3/4″ wide, 19-3/4″ front to back – or thereabouts.
Think there will ever be another Woodworking in American event?
Not from us. Check at PopWood; I hear they’re planning one.
Yikes.
This sounds like a, “Name by any other rose” kind of situation.
With Chris’ interest in chairs Has he considered doing a piece on Swedish stick chairs (or did I miss it)?
Mattias wrote a great piece on them:
https://blog.lostartpress.com/2022/12/11/the-flavour-of-wood-in-sweden-mats-palmquists-trasmak/
Klaus covered the root stools and Scandinavian examples:
https://blog.lostartpress.com/2022/01/05/norwegian-wood/
And Jogge Sunqvist has built many of them. (Follow his Instagram to see them.)
I have a few Swedish chairs that I want to build. So stay tuned.
Did you need to tune your Veritas tenon cutters when you first got them? If so, what was your process for dialing it in? Mine came set up to take a rather large bite toward the outside of the cut which is difficult to control.
As always, thanks for taking time to answer!
Read the instruction manual, and you will learn a lot (I did). I simply follow the instructions, which are very clear.
I tune the power tenon cutters every time I switch drill bits to get a good fit. The blade of the tool has two holes so you can shift it up or down. And the brass shim stock (included) helps you tune it even more.
Stick chair seat grain direction: front-back or left-right?
Usually left-to-right. But sometimes front-to-back.
I’m looking to make the three legged drinking table from Anarchist’s Design Book, but with 4 legs instead of three to accommodate 4 people without anyone having a table leg in their crotch. I’m thinking I’ll space the legs at 90 degrees instead of 120 and maybe increase the diameter a couple inches. Does this seem a reasonable plan?
Yup. Sounds good to me!
I’m looking at wood pricing and budgeting for my first chair builds. When you are wood shopping for your stick chairs, about how many board feet of wood do you buy on the average? Thanks so much for Open Wire, and all that you folks share.
This is my Sunday column for the American Peasant. The short answer:
A comb-back needs one 10′-long 8/4 board that is 9″ wide that has dead-straight grain over 48″ of the board. That gets you everything but the arm. The arm is from a 6′ long 5/4 board that is 9″-10″ wide. Curvy grain is better for this board.
Thank you, much appreciated. Again, enjoying this Q and A column so much!
Morning! I am planning on doing some wainscoting in my new home office. I have two questions:
Can you guys recommend a guide? I searched “Chris Schwarz wainscoting” and I only found the infamous “wainscoting in a weekend” Earlywood article and the not particularly helpful PW article from 2007 (sorry, I need visuals).
I have taken a big interest in researching how it was done before the advent of sheet goods. Was this someone’s entire specialty? I can’t imagine how long using solid wood stock would take in a whole house.
I hit send before including this: is there a book on historical wainscoting?
I don’t know of one on just wainscoting, but a lot of books on interiors include it. Here’s an excerpt I just found online that looks pretty good: https://chestofbooks.com/architecture/Cyclopedia-Carpentry-Building-1-3/Wainscoting.html
Thanks Fitz!
Hiya, folks. I’m just finishing up my ATC and looking forward to moving into it soon. Question… where does one find decent tool rolls for long tools such as rasps? Most of the ones I see are for short tools like little files and such. I don’t (yet) have the skills to make my own. Thanks!
For longer tools, I like the ones Jason at Texas Heritage offers: https://txheritage.net/generalstore/tool-rolls
I’m using up my existing hide glue before I take the piggly plunge. I grabbed my jar of hot hide glue out of the fridge and noticed it had some mold on top. Any guesses what would cause that? I made it from granules about 2 years ago. I’d guess it’s been 6 months since I last heated it. It’s kept in a lidded glass jar in the fridge. I have a similar jar of old brown glue that hasn’t molded, though I heat it more often.
Just to be clear, this is hot hide glue from granules and is NOT the piggly no wiggly recipie.
With a lid, you’re trapping moisture. Mold likes moisture. A fridge dehumidifies the air, but because of the lid your glue probably didn’t dry out all the way. I’ve learned from a cheese maker that he will age cheese in the fridge by keeping the cheese in a a container with a lid.
If mold is growing then you didn’t have a good seal. It’s basically a food, so sometimes you lose some to hungry microorganisms.
Last week I started shaping the 26” long octagonal sticks for my first six stick comb back all in Cherry. The short sticks turned out fantastic, mostly shaped with a drawknife, and LN spokeshave wherever grain direction changed. First long stick shaped beautifully!!! Second stick, the drawknife found where the grain changed direction, and quickly ripped the stick in half from grain runout. Grain looks straight where you can read it, but not as easy to see runout with Cherry than Oak. Second stick the same thing happened. Clearly my long sticks do not have as straight of grain as I’d like. I will finish the remaining long sticks with a block plane instead of drawknife, which won’t rip the sticks in half when the grain direction changes. However, this has me concerned about strength…. I have some dead straight White Oak stock split out from a log, fairly dry that was prepped for other projects. I’m thinking about making the two outer long sticks out of White Oak, and painting them Seafoam green? Black? Something to contrast and complement the Cherry. I’d have a nearly full chair in Cherry, with two painted sticks. I could also make all the long sticks from White Oak, see how it looks against the cherry, paint them if needed, but zero strength concerns. White Oak doesn’t look terrible with Cherry. I have options. This is more a question of final aesthetics. What would you do?
I’d make long sticks and hit them with a sledge (as shown in the book). If they survive that, they’re fine for long sticks. Or I’d switch to oak sticks and live with the contrast, (which will mellow over time). Or paint the chair….
Say a local lumberyard had a sale on end grain butcher block countertop. Is that a horrible choice for a workbench top? If so, why?
Might be. Some of those are screwed together and have a lot of metal in them. You find it when you drill mortises and dog holes. So I’d ask before buying.
Sounds like hell to flatten!
Just finished my first stick chair. Thank you for the confidence to take that on. Now I’m planning on making a set of dining chairs. I want less splay for these, and I will make a model, but for stability is there some point you shouldn’t go beyond.
For the front legs, there aren’t any rules. They can be straight up and down and the will work (but be ugly). For the rear legs, they need enough rake and splay to prevent the chair from tipping back. A good place to shoot: put the back feet in the shadow of the sitter’s head.
Any chance you’ll do another run of the pullover style workshirts again?
Unlikely. They weren’t a big hit. Chris has several shirts that are similar that he loves…we’ll have to wait for him to chime in on where they’re from…somewhere in Ireland or Scotland, I think.
Lee Valley of Ireland. https://www.leevalleyireland.com/
Greetings from Denmark.
Have you experimented using different shoe-designs in stick chairs that can give maximum lumbar support? Maybe adding a wide lumbar-area sections as you see in low-back chairs? Or making it more/less soft or angeled?
I have used big shoes, little shoes, angled, rounded over and etc.
I don’t like a big lumbar support. A little will do for most people. I focus on supporting the shoulders comfortably and then introducing a bit of lumbar support. It’s very easy to overdo it.
What’s a good place for lumber around Cincinnati?
We usually drive up to Muterspaw in Xenia for large amounts of wood. If we need a lot of QSWO, though, we’ll make the trek to Frank Miller. For small amounts, Frank Paxton in Madeira.
Hello, I’m looking to pick up a few handplanes. I just want a good basic set and not really wanted to get a large collection of them. I already have a LN 60 1/2 block plane and after doing a lot of research, I think I would be pretty well set with a #4 1/2, #5 1/2 and a #7? The 4 1/2 being a dedicated finish smoother, the 5 1/2 for GP & shooting board and the #7 for flattening? What are your thoughts? Thank you
FWIW, that’s exactly what I have, except an old #3 that I got cheap, and haven’t wanted for more.
You can see all the tools in Chris’s chest here:
https://blog.lostartpress.com/2023/01/01/the-anarchists-tool-chest-at-age-11/
and mine here:
https://blog.lostartpress.com/2023/01/08/an-anarchists-tool-chest-at-age-11-5/
But in short, both Chris and I use a No. 3 as a smooth plane, old Stanley Type 11 jack planes (no. 5). He has an LN No. 8, I have an LN no. 7. And we have dedicated shooting planes, but I sometimes use my block place for a small piece when perfection isn’t needed. (The blades on our bench planes are cambered, so not set up for dead-nuts accurate shooting.)
Thank you. Those links and this whole page will keep my busy for days of reading! lol
For my two cents, the 1/2 sizes are too wide, and too heavy. It takes a lot to push. I have a 3 and a 4 LN. I go back and forth on which I like better. I like the #7.
Agree on the 1/2 sizes…..
Ok, Piggly question: let’s say you had an overzealous glue up that left a 1/8” gap between two 3” x 1” stretchers (ie T-joint), utilizing a floating tenon. Preliminary diagnosis, maybe too much glue (Piggly definitely no wiggly) and an ill conceived clamping strategy. Is there a procedure you would suggest to try to loosen the glue and pull the pieces back together. This would pleasantly avoid my gerbil brain solution of wanting to cut the tenon and using screws. What temperature would you need to get things moving again? Thank you.
The best way to loosen the glue is a wet rag and a heat gun. Start on the lowest setting. It takes time to plasticize deep joints. So patience is the word.
Hey LAP team! Thank you as always for taking the time to answer questions.
How do you deal with a lack of motivation to start or complete projects (if you ever do, that is)? I’m only a hobbyist, so my time to do woodwork is already limited. The list of projects I want to pursue seems to grow longer every day, and it’s fairly frustrating how the sense of “I’ll never get around to all of these projects” seems to kill the drive to start on any one of them.
I know that the answer is probably something to the tune of “just pick up some tools and start chipping away at the projects one at a time”, but part of my problem is indecision when prioritizing the projects to work on. With limited shop time it feels incredibly important to prioritize the projects that “need” to be done.
What is your approach to deciding what projects you will work on next, especially if you have a daunting backlog?
Large projects require small bites.
I set a VERY VERY reasonable goals for my day. I write them on our whiteboard. One might be: Rip out the legs. When I achieve my goal, I’m working and I say: Why don’t I also octagonalize them?
For me, it’s about momentum. Once I get going, stopping me is difficult.
Just make a list of 10 short easy projects to start. When you finish one, add another to the list. The priorities will sort themselves out.
After trimming some trees, I have some curved branches that may work for combs or arm segments but they’re only 4-6″ diameter. Is that big enough? Do I have to avoid pith or sapwood? Thanks.
Those could work. I’d resaw them through the pith and let them dry. You’ll know in a few months if they will work for a chair.
It’s no problem using sapwood. Some old chairs even have the pith in the arms.
Hola, I’d like to make your 32 x 26 x 33 AP cupboard. Would you have any hesitations using 8/4 red oak for the top and posts? It’s some pretty nice straight-grained red oak and I’ll be using poplar for the rest of the panels. I’m a bit torn on leaving the top thick vs planing it down to 6/4 or less.
Red oak is fine. Usually the tops were thin. But you can make that call when the time comes to put the top on.
Hi Chris and Megan, I hate to ask this week because it seems pretty busy with questions today already, but I have been wondering about this for a while. I have pretty much everything (or similar things) that you both have listed in your ATCs exempt:
Megans ATC contents write up mentioned veritas edge-trimming plane and Chris’s ATC contents also said “ there’s a Veritas edge plane, an occasional life-saver.” I am wondering why it’s useful enough to make it into both ATCs?
I use it most often when teaching – students have trouble planing a 90° corner after cutting the angles at the top of a DTC. And sometimes, so do I!
Yup. It’s an emergency plane for fixing student errors.
Still starting out I am trying to limit the number of specialty tools I have to acquire for budget and clutter. I have a number of projects that it would be useful to have a plow plane to cut grooves for box/drawer bottoms and door panels.
In a pinch I assume I could get away with just a Veritas box makers plow to cut a groove for tongue and groove and then a rabbit plane for the tongues? (Low volume, only for a couple projects).
Thanks for your time on a Saturday.
Yup! Good plan.
Hi Chris and Megan! As always, thanks so much for wonderful dedication and faithfulness in answering these questions each week. Mine is related to seat tenons in the chairs.
I’m a fan of 1″ tenons in the seat since (as you’ve mentioned before) they’re more historically accurate (which is fun). However, sometimes I have a hell of a time getting them out after a dry fit. I’ll compress them before install with soft jaw pliers, knock them in (when working on stretchers, etc.) but then have to wallop them really hard to remove. Any tricks to mitigate, or do I just wallop away? None have ever broken yet, but it feels like courting disaster.
And do you ever have 5/8″ tapered legs “bounce” out during glue up? When I’ve used the 5/8″ tapered tenons on the legs, dry fit seems perfect after everything is in place, but once glue is applied there’s always one leg that seems to not want to stay put. Thoughts?
Thanks again.
Jake
Hi Jake,
A good tight fit is awesome. Continue on as you are with the loose tenons.
On bouncing legs: It can be a few things. Usually it’s a stretcher that has been misdrilled that is pulling the leg out. Or one of the stretchers is too long. It can also be that the tapered tenon and mortise don’t match exactly and so the natural tension in the chair is pulling it out during gluing.
If a leg is bouncy, usually wait a few minutes for the glue to tack up. Then I hit it again. That usually works.
Thanks so much! I’ll continue walloping then 🙂
Jake
Good morning and thank you again for the opportunity about asking Woodworking questions.
Being new to woodworking I was wondering if Chris can help me decide which brand of 1/4” Swan-neck chisel should I get. I am not an expert on tools, so I am not looking into buying a vintage one (because I wouldn’t know if I am getting a good deal or not). After reading Chris’ article on PW “Everything You’ve Ever Wanted to Know About Chisels” I am convinced I need the 1/4” size. For what I can tell in the photo Chris may have an original Henry Taylor.
In my research I have only found two new swan-neck chisels:
1) Tooksforworkingwood has a two cherries made in Germany (apparently Rockler sells them too, even though the handles look a bit different) 2) LeeValley has a modern version specifically made for them by Henry Taylor in England.
If you were to buy one of these two options which one would you get? Or do you have a better (new) brand option?
I just want to buy the better tool, (buy once, cry once mentality).
Thank you again for your teachings and guidance.
Skip the swan-neck chisels. Get good mortising chisels, learn to use them and the bottom of the mortise will clean itself.
Are linseed oil-based products amenable to wipe-on approaches, or is brushing always a better way to apply them? I’m curious if linseed oil paint can be wiped on, or if that would generate too much variation. Thanks!
I wipe on linseed oil. But I can’t imagine a situation where I’d wipe on linseed oil paint. But to be fair, I don’t wipe on any paint. I’ve sponge painted a few times, and that’s how Travis Curtis applies milk paint (if I recall correctly), but that’s the closest I can fathom.
I have never wiped it on. Anyone else?
I have wiped paint off. We used paint like a stain: brushed it on, let it sit, wiped it off. It was part of a complicated, multi-layer finish with stain, paint, glaze, and polyurethane. It was intended to give an antique effect. The paint was probably what we used to call oil-based enamel.
Chris,
Maybe a dumb question. Thanks for your patience. Just bought my first band saw. It has wheel guides. In your recent substack post, you talked about cleaning the wheel guides. What do you use to clean them? Thanks.
Light machine oil and a wire scrub brush.
Thanks for all you give to the craft! For a simple traditional bookcase how would you recommend attaching the top? Will be heavy, and I can imagine people lifting from the top to move it.
Probably cleats. Screwed to the inside of the case and screwed to the top (screws going both ways through the top if aesthetics allow.
I’ve been asked to make a “tack box” for a local horse barn. The dimensions are a bit smaller than an ATC, but I am thinking of using the basic design. My question is if you have any recommendations for wood? This will sit in a tackroom (unheated)….covered but slightly exposed to elements at times. Desired properties are similar to tool chest. Durable but light enough to be moved.
Would Linden still be desirable in this application, making extra sure to have durable (oak) rot strips? Or is there something else you’d think about? Also, at what point does chest become small enough that you can think about decreasing 1 inch thickness of the carcass? I’m thinking here that people will need to load these into trucks every so often, so weight is def. an issue (where it really isn’t in my own workshop, where the chest rarely moves).
Hope this makes sense. As always, much thanks for your wisdom.
James
If you can get it, my first choice would be white pine; best weight to strength ratio for a tool chest/storage chest. And 7/8″ – don’t need a full inch. With linden (also a decent choice), you could get away with 3/4″ thick for sure (and probably in pine, too), since it will be picked up a lot. I used to help tack 20 horses every morning at a summer camp – those bits/saddles/etc add up in weight – so make the case as light as you can! And yes – white oak or another species that holds up to water for rot strips.
Are there any plans for more Sharpen This videos? I just picked up a LV skew rabbet plane and would love to see how you sharpen the skew irons. Do you jig it up? I’m less afraid of honing free hand but I worry about messing with the geometry when grinding.
Ch. 8, Hand Sharpening, shows Chris honing the Veritas skew rabbet plane iron, jigless. LN makes skewed jaws (I think at two different angles), but I have no idea if they fit the Veritas skew iron…I know they weren’t made to fit it. Has anyone else here tried that combo?
I’ve tried it, and it doesn’t work. The Veritas skew rabbet is 30 degrees, but the blade is oddly shaped. The full width cutting end is only an inch or so long. The rest of the blade is a much narrower shank. With the cutting edge in the Lie Nielsen jig, with the 30 degree jaws, it doesn’t project far enough. Imagine putting a spokeshave blade in the regular plane jaws. With the shank end of the Veritas blade in the jig, it projects too far. Plus, the angles don’t seem quite the same.
The 30 degree Lie Nielsen jaws are made to fit their side rabbet pairs. Those blades are long, narrow, and straight sided.
To add to the confusion, for the right-hand Veritas skew rabbet, you’d need the left-hand LN jaws.
I think skewed blades are easier to sharpen (when thick) by hand.
I would add, when grinding, never let the grinding wheel touch the cutting edge, unless it has a chunk taken out. Stop grinding 1/16 or even 1/8 back from the edge, then finish on bench stones. There’s no reason to hit the edge of a normal-use blade on the grindstone.
Happy Saturday!
I have a Veritas pullshave.
https://www.leevalley.com/en-us/shop/tools/hand-tools/spokeshaves/54888-veritas-pullshave?item=05P5073
It works ok… To make it work better, I have read some people round over, or grind down the ridge in front of the blade on the sole. Supposably it helps by opening up the cutting angle. Right now it’s difficult to engage the blade into the wood because of the sole geometry. Wondering if you’re familiar with this tool and this hack? I would like to try this, but, would hate to ruin an expensive tool with my ad hoc “improvement “.
Thanks!
We had one for awhile. I could never make friends with it. So I switched back to the travisher. Sorry. Maybe someone else here has some intel.
I have the Veritas pullshave and did round off the sole, I think mostly behind the blade. It definitely improves it. I just did it freehand with coarse then fine sandpaper on granite. Basically using the tool as I would to hollow except on sandpaper instead of wood (blade removed of course). The other thing that seems to help a lot is to shorten the rear handle as that tends to get in the way when sweeping it back and tilting. I had a friend turn a new one for me. Hope this helps. It’s a nice tool, but not my first choice. What I like probably best is the blade is a heck of a lot easier to sharpen than a travisher as it’s basically a jack plane.
I checked and I did round it off in front of the blade, too. Basically, make the shape that works smoothly as you would use the tool. I was surprised at how easy it was.
I have a Lv shave and I can’t keep the mouth from clogging. Any advice would be very helpful.
The all come tight. File it open about 1/16″. Mark the line for the new opening with permanent marker. File to the line.
Thanks for spending Saturday with us! My workbench is finally “done enough” so I’m on to planning the next project: I’m about to build the American Trestle Table base for an existing top. The top is 60×36 and I’m trying to figure out how to adjust the plans: should the legs and supports be extended to maintain the same end gap? Do I need a center stretcher for a top that short? How does one decide that? (I also don’t understand how you used a dowel to secure the central bridle joint…)
Your changes involve balancing aesthetics and use. Will someone sit at the end of the table? You need an overhang so their legs don’t straddle the post. Draw it out and your eye will tell you if the base is too small. (You don’t need the central stretcher, but it doesn’t hurt.)
The dowel/peg for the central bridal is just drilled through the joint. Drill a hole through the center of the joint from the outside. Drive in the peg with some glue. If I’m missing something here, let me know.
Thanks. Yes, I’m planning to keep the 12″ spacing at the end – I was wondering about the length of the legs and upper braces. This is headed for an environment where small children may hang off it (your description of the stability of the design is part of why I’m interested) so I’ll probably extend those to avoid making it tippy.
Ok, that dowel explanation makes perfect sense! I just didn’t see it in the drawing/photo.
Ah. Extend the legs and braces almost to the long edges of the top.
Good morning LAP. Another question about the Anarchist’s Workbench, if you would be so kind. I’ve finished the top and base and now onto the vise (workbench crisscross). For the chop: how critical is the 3 1/4″ thickness? Would 2″ suffice? Your thoughts on edge glueing two pieces to reach the 8″ width? You mentioned face glueing to 8/4 pieces together to reach the 3 1/4′ thickness. Are there any tricks, tips or techniques or pitfalls to avoid? Ok, that’s enough. Thanks for all you do. This woodworker in Monterey really appreciates you guys.
If you use a stiff wood, such as maple, you might get away with a thinner chop. But thick chops are worth the extra effort. They hold noticeably better.
There isn’t much trick to laminating board face-to-face. Orient the annular rings so they both face the same way. Cut the pieces slightly oversize in case the boards shift during clamping (or better yet, screw the boards together while gluing so they don’t shift.) Flatten the mating surfaces. Add glue and clamps. Even if you get some tiny gaps the lamination has so much glue surface that they’ll never come apart.
I read rumor about a Dutch Tool Chest book. Is this still to be?
Is it.
Is there a bench brush you all recommend? I bought a horse hair one from Amazon but every time I use it the hairs like to pop out. They seem to be folded then horribly glued into place. Thank you!
For cheap: https://blog.lostartpress.com/2023/11/12/2023-anarchists-gift-guide-day-1/
For nice: https://thebestbrushes.com/cart.php?m=search_results&search=bench+brush
For saddling chairs: https://blog.lostartpress.com/2022/11/17/2022-anarchists-gift-guide-day-10-corn-whisk-brooms/
Bonus polissoir on the back of the Berea broom.
Thank you! You all are teaching so many of us and I am very grateful, just wanted you to know that too.
Any tips for using th sorby sizing for ool on a lathe?
Sorry “for ool?”
Speaking of tables … I guess that the Anarchist’s new normal would adjust the top to be 28″ high instead of 30 … At least, that’s what I remember Chris saying, but I’m totally failing to find that post.
First, excellent presentations at Williamsburg, Chris!
A question about reproduction brasses. I just priced some from Horton for a lowboy I’m making and went into sticker shock.
Do you know of, or have used, comparable brasses from abroad that are worth a look?
Not that are less expensive. Only more expensive.
For hardware I do a lot of looking on eBay. And architectural salvage. That’s really the only way to save money on hardware I’m afraid.
Good morning, wondering what you think of old growth southern yellow pine for stick chair seats? If ok does it take linseed oil paint well?
Thanks.
It will be a bear to saddle it because of the density difference between earlywood and latewood. But it takes linseed oil paint just fine.
What Chris said. I did my first few “practice” chairs with SYP construction lumber for seats. It’s OK unless you’re saddling, then it’s a pain.
Same with me. My seats were flat sawn syp and I gave up trying to get it right. Might be different though if the old growth syp was quarter sawn. I’d try another syp seat if I had old growth quarter sawn lumber.
I’ve used it for seats and it worked fine – but I didn’t even try saddling it.
Good Morning all.
Megan, my apologies in advance for not capturing your answer from an earlier Open Wire . . . Can you please repost the link to information regarding dimensions/plans for the dovetail shaker tray? I believe it was from P-W, but I could not find it. Thanks and have great day.
NEVERMIND! I stumbled across it when looking for something else (No, not my missing 4″ combination square . . . That’s still missing).
Have a great day and all the best.
https://www.popularwoodworking.com/projects/silverware_tray/
If you were stretching out the boarded bookcase as described in the ADB to 48″ or 60″ would you make any changes to the design?
Thanks!
I would add some sort of support in the middle to prevent the shelves from sagging.
Will is sag? Go here to find out:
https://woodbin.com/calcs/sagulator/
Happy Saturday and thanks for answering questions. I am making a tool tote similar to Roy Underhills. This is going to be nailed together with nails each end at 90 degrees from each other at the corners so the side are joined on each side and end. I was thinking of trying to source cut nails, but all I can find near me (UK) is carpet tacks. Do you think these would be strong enough, or would wire nails and a bit of PVA be strong enough? Thanks for any insight you can provide!
You can get cut nails in the UK here: http://www.glasgowsteelnail.com/
You can use wire nails, but cut nails are so much better.
If you do use wire nails be sure to orient them at slight angles. Like the slopes of dovetails. This always helps.
Megan,
It has been a struggling using my shooting board as none of my vintage planes have sides square to their soles. I see up above that both you and Chris have dedicated shooting planes however I wonder what you use for shooting miters.
Would a LN low angle jack be sufficient for a dedicated shooting plane or would it be too light.
Thanks for your help,
Jim
I use my much-lighter block plane for shooting sometimes…so I think the LA jack would do fine.
I know Chris said something about the heft of the 5&1/2 veritas custom bevel down before. This is what I use and tend to use for hogging off material and nearly all of my planing. Its sweeet on 2″ thick quartersawn white oak ends. Building my miter jack now and its a godsend; takes awhile to get used to the norris adjuster though. I own the 4&1/2 and its too light and my 7 gets used rarely in the shop. Match up the weight to the LN and see if its similar to the 5&1/2.
I use my low angle jack for shooting and it works fine (as does my block plane for small pieces). And, the jack does double duty as opposed to a dedicated shooting plane.
You can also get a clamp on shooting handle for the LN low angle jack plane.
Taking a (long’ish) break from working on my staked barstool (very loosely based on a model from the Anarchists’ Design Book) … I’m petrified, just a rabbit caught in the headlights, too scared to make the final mortice cuts on the stretchers and go to glue-up). I’m trying to use my time well by building my meagre skills making some boxes (basic argument … don’t practice, make … then make better).
Can you recommend a good text on box-making, preferably covering the range from basic to more advanced construction, and with a focus on hand-tool working?
I have found quite a few promising texts while digging around but they all (quite casually and leisurely) emphasise power tool ownership and methods (table saw, band saw, pedestal drill, etc., etc.). I have a small shop, well-equipped with decent hand tools, which I personally prefer in use. I’m also located in Africa where good larger power tools are hard to come by and very expensive to import. I am comfortable hand tooling my way around dimensioning and smoothing the rough-cut but beautiful stock I can get here without a planer or jointer … but it’s frustrating to find every next piece of advice assumes I have at least a table saw and a band saw set up and ready to go.
I like Doug Stowe’s box books: https://www.dougstowe.com/publications/
He does use power tools at times, but his heart is in teaching hand tool skills with kids. A lot of the fancy stuff on those little boxes is VERY jig-centric. So I don’t know if you are going to find detailed help in doing it with hand tools. But converting the boxes to a hand-tool set and mindset is the better path anyway.
Sorry I don’t know of a specific book for your needs.
Thanks for this. I’ve come across two or three books Doug has written and they all seem to be very well thought-of. But reviewer comments suggest that they are all more oriented towards power tool users.
I guess, I should get hold of one of one of them and see what design- or work-arounds make most sense to get the best out of a different way of working.
You all are the best, and the Crucible stuff is also the best. On that note, is the tool roll wide enough for brace bits? Currently mine are just kinda rolling around in one of my chest drawers.
As long as they are less than 11″ long, yup.
I’ve experimented making paste wax from beeswax, pure tung oil and mineral spirits. I’d like to use a solvent not-from-petroleum that’s considered food-contact safe when dry. Do you know if turpentine from a big-box store would be considered such? Or citrus solvent?
I distilled a tiny amount of turpentine and rosin from resinous wood once – but won’t be collecting any amount of pine sap or resinous wood for the foreseeable future.
Thank you!
I am not a turpentine expert. The stuff I use is from Diamond G, which is guaranteed from pie tar.
http://www.diamondgforestproducts.com/~shop/16oz-100ure-gum-spirits-of-turpentine/186771/
D-limonene is much less nasty (both in smell and as an irritant). As far as I know, it is not petroleum-based.
D-limonene is derived from citrus fruit peels
Good Afternoon Chris and Megan,
Thank you both for taking time out of your Saturday to answer questions again. I was curious if you would recommend the Knew Concepts Coping saw. I saw reference today, in the comments, to the newer Olson coping saws. I purchased one a few years ago and have never been pleased with it (despite adding the lock washers). I don’t think that Blue Spruce offers their version anymore and, from my perspective, the Knew Concepts appears to be one of the only options for a “last” coping saw.
Thanks,
Jacob
The Knew Concepts is a step up. But the blade clamp is too fragile for my tastes. I’ve broken it a few times. Also, I’m not wild about the handle. You might consider making a bowsaw that is coping saw sized (Tools for Working Wood has the hardware). Colonial Williamsburg has one in its shop. Works great.
Thanks for the perspective on this. That was actually one of the thoughts I had previously (using the Tools for Working Wood hardware). Your recommendation is the confirmation I needed.
Thanks again,
Jacob
A ww friend of mine made a pair many years ago as Christmas presents for his children by taking the plans for bugbears bowsaw (search on that phrase, the original is a pdf on oocities) and hitting the 50% button on everything but the handle and thickness. I believe the blade holders were chunks of hacksawed .25 (6mm) brass rod epoxied into the handles. If you have not made a bowsaw before, it is crucial to have the centerlines of the thickness of the sides and stretcher, and of the handles in the same plane (don’t ask me how I know this..)
Kudos for Chris’ video “Super-Tune a Handplane” and some discoveries.
The last couple nights I finished the process Chris describes to take an old Stanley and make it a great user. I did a 3 (post WWII Bailey), two 5s 1890 something non-Bailey and 1902 Bailey), and a 7 (1910 Bailey) all purchased from the guy Chris recommends in his book, the one who refers to “the kid”, a few years back. Can’t say enough good about him.
An unanticipated benefit of the process was that after I had cleaned the tools I discovered that the 7 was well used and well cared for by a professional whose left thumb and first and second fingers had polished the Japanning around the front tote to a mirror finish.
Another unanticipated benefit was discovering the “peasantness” of these old planes. They were built in the very early days of machining cast iron and steel, right before the automobile revolution changed that, and have endured for 120 years in their present form. That meant they were designed around the machining limitations of the time which revealed something that has been lost of the makers’ intent. The blade/breaker/cap intentionally bows the whole sandwich so it can’t possibly mate flat to the entire frog surface. The front 1/4-1/2 inch are critical the rest doesn’t matter. Blasphemy I know. Blasphemy #2. You don’t want the machined surfaces of the frog to be smooth, just flat. The roughness helps keep everything from moving.
More mundane discoveries. Dress the hardened steel blades on the sandpaper first while the grit is still fresh and sharp. A steel brush is your friend, especially with finer grit paper, to frequently unload the soft cast iron from the paper. The diagonal joint of the belt sander paper has zero effect with regard to flattening the body. You can stack fresh paper on top of the glued paper and it will stay in place. Leave the handles on but take the frog off when flattening the body. This gives you a better hold and protects the lateral adjustment lever from getting bent. Jojoba oil coagulates into weird puffballs floating in the bottle at temps below 55 degrees, camellia oil doesn’t.
A big thanks to Chris and to the LA team for my virtual education!
Just wanted to thank you for releasing the Crucible scraper (and the videos on its sharpening) to the world. I’m nearing completion of a 120 by 70 cm table top and just finished scraping the whole underside with it. Planer marks, tearout, plane tracks and glue seam unevenness—all gone. I expected to have to sand all that out. Yes, I know, it’s the underside, but I’m a perfectionist dumbass.
A good workout, and I can start with 120 rather than 80 grit. (And probably stop at 120, because underside…)
One question: Bob Flexner says there’s no need to finish unseen sides of pieces just to stop bowing: it won’t stop it, all the moisture exchange will happen eventually even if both sides are finished. Has this been your experience?
There is no need to finish the underside. Almost nothing stops moisture exchange (and most of it is through the end grain.
Look at old antiques with their original finish. You won’t find paint or finish on the undersides.
Happy Saturday,
Just read somewhere that vinegar can be used to “unglue” (or reverse) Hyde glue.
Have you tried this in your experiments with your adhesive?
(May be an alternative to heat)
I have not tried it. But I will put it on the list.
It works very well. Will also soften Titebond so you can get clean joints if regluing an item. Of course give joint a quick wipe down with water and allow to dry before reassembly.
Hi Chris, I have 3 stick chair questions.
I have some 2″ thick ash boards that are 17.5″ wide. Local Saint Louis lumber with plenty of veining / heartwood / curl. Looks like great seat material to me. I could also see getting a crest out of it.
Going over the boards, however, I don’t find much straight grain. Three questions:
(1) When you’ve built with local ash, have you had much luck finding straight grain for the sticks? Just wondering if it’s a fool’s errand with these urban trees.
(2) With ash, how straight is straight enough? How much run-out is acceptable?
(3) Design help needed! If I need to go to the regular lumber yard to get straight grain for the sticks, any thoughts on how a chair would look with a figured ash seat but then typical white-ish sticks and a figured crest? Or would you match the arm bow to the seat as well? Or just do a figured seat and make the rest in the more regular-looking ash? What’s your process for working through these questions?
Thanks,
Louis
Hi Louis,
1) I buy 4/4 quartersawn ash for the sticks from Muterspaw lumber in Xenia. It generally comes arrow straight. Street trees grow in all directions, Straight stock is extremely rare. But QS ash from the lumberyard is not.
2) If it doesn’t survive the Hammer Test, it’s not straight enough. I don’t have a number for you, I’m afraid.
3) Elm, ash, oak and some other species (honey locust) all blend together nicely with a clear finish and they will mellow in short order to where only an expert will notice. My personal taste (and the tradition) is to mix species that blend – not species that contrast. I find contrasting wood species in a chair to be very difficult to pull off.
Good morning from the Pacific Northwest. Thanks for doing this every week.
I’m just finishing desks for my kids and would like to make chairs to compliment. Between the various LAP instructional choices (staked backstool, Gibson, various chairs in the stick chair book) could you please recommend a chair design or two for a novice chair maker in this application?
The staked backstool from “The Anarchist’s Design Book” is about as simple an introduction to chairmaking as you can get. Plus it has a simple Welsh-ish chair that is the next step forward.
Hey Megan, I love the blue finish on the small chest pictured at the top of this mornings’s blog post. I think I’ve seen it on other pieces of yours? Would you share the name/manufacturer?
Thanks
It is General Finishes “Milk Paint” (really an acrylic) in Twilight, but I’m afraid that color is no longer available. The closest is Coastal Blue, but you’d need to add a drop f three of black to it for a better match. (I reain miffed at GF for discontinuing this and other colors.)
Greetings!
I’ve noticed you don’t install locks on your ATC tool chests anymore. Any reason?
Don
For me, they were an option that I offered to the customer. Adds $150 to $300 to the price, depending on the hardware.
I do add them is a customer wants one, and when they do, I recommend this one: https://whitechapel-ltd.com/178lf3.html But on a smaller chest, I’d push someone who wanted a lock toward a hasp – the “crab lock” takes up too much valuable space in an already smaller chest.
Good afternoon, I am making shutters(decorative) from white oak in a frame and panel style. They will get a lot of sun exposure here in Tampa as well as rain. The wood store guy recommended spar varnish to protect against UV and mold, but i really don’t want a film finish. I would like to stain slightly darker than natural. Suggestions?
Spar varnish from the home center won’t do diddly squat. A film finish is a bad idea for high UV areas (it flakes off). I would use a clear or almost clear deck stain, or an oil/wax.
Do you have any rule of thumb for the angles of wedges that go in wedged joints? Mostly thinking for staked stuff. I have made my wedge too narrow a couple times now.
Right now my wedges are 2″ long and have an included angle of 8°. Dead straight grain ash or oak.
Good Afternoon
Chris, If I remember correctly you have a Lie-Nielsen blade in you Stanley No. 5. Did you have to modify the plane or did the blade fit, out of the box?
Thanks
Brian
I had to file the mouth open. Easy to do. But I had a LN blade lying around — that’s why I used it. I believe Veritas sells excellent replacement blades that are more likely to fit without filing:
https://www.leevalley.com/en-us/shop/tools/hand-tools/planes/blades/42607-stanley-record-bench-plane-blades-made-by-veritas
Great talks at Williamsburg! Are there any period furniture books on the way from Lost Art Press?
Do you know of any adjustable mouth block planes for chairmaking that are maybe 15% smaller than the LN and veritas ones? New or vintage. I sanded down the edges of my 60 1/2 a bit, and could do more, but my hand gets quite uncomfortable after 10-15 minutes of shaving sticks.
I have smaller hands than yours, and I find that if I grip too tightly, that’s when I get tired when using the No. 60-1/2 (I often use the LN 102 if I don’t need an adjustable mouth). I’d try a conscious effort to let the weight of the thing hold it in the cut more and do less gripping/pushing down (which is what I see happening in some classes). Or, you can have a metal worker add a tighter mouth to a No. 102. You might also take a look at the Veritas No. 1 bevel-up bench plane. You could remove the handle and use it as a block plane, I think.
Bridge City makes a tiny plane with an adjustable mouth (HP-8) – but we’ve found it to be too lightweight for making sticks…you have to grip and push down too hard, and that makes one tired 😉
Where do you source the metal cabinets that you use for storage in your shop? The ones that are made like a card catalog in a library. I’ve looked on eBay and those are out of my price range
Erm…eBay, mostly. They’re the Equipto brand. (They do seem to have gone up in price in the last couple of years)
But you can find lots of other brands out there for less at thrift stores. The one under my oak Roubo was $20…..
Thank you!!
C
Sorry, callow sawyer with bandsaw mill and not good with computers – at all. Was trying to ask considering projects rock maple is best suited for, what thickness or thicknesses would you recommend sawing it to maximize desirability to woodworkers?
Thanks to all at LAP for your generosity with your time and expertise.
8/4 and 5/4. Try to get the grain as straight through the thickness as possible. Wider is always better.
Rock maple is great for everything and anything. Tables, chairs, workbenches, beds. Wonderful strong and heavy wood.
Thanks, I’ll do the best I can to get the grain straight.
Hello,
I was wondering if you have ever come across any resources (books, websites, etc) that contain a collection of vintage makers marks? Thank you…
I don’t know of a single source, but there are a lot of books on specific types of tools that include such information. For English planes, for example, “Goodman’s British Planemakers.” And for US ones, “A Guide to the Makers of American Wooden Planes” – so my knee-jerk reaction would be to search for books for collectors of specific tool types. (And join the early American Industries Association – there are many articles in The Chronicle on just such subjects)
Thanks! That’s very helpful…much appreciated
What is Chris’ favorite Birdhouse Book? Or the one he feels is the best.
I can’t say I have a favorite. I love the wild ones – the stuff I would never build. But my faves are the ones that cater to the different species, with different hole diameters (to discourage predators) and other little changes that make it more likely that a bird will take up residence.
Afternoon Chris, Megan. I’ve taken a weekly carving class so I can learn how to carve as I have a fondness for little feet on furniture (lots of time as a kid staring at my grandma’s stuff). I really like the Pfeil carving chisel handles. Thinking of getting a few Pfeil normal chisels to try them out (mostly for handles). I suspect they are good quality. Have you ever used Pfeil chisels as opposed to carving chisels? Many thanks.
Hi Joe,
I know nothing about carving tools. You’ll have to ask Mary May or one of the other carvers out there who aren’t sponsored. Sorry.