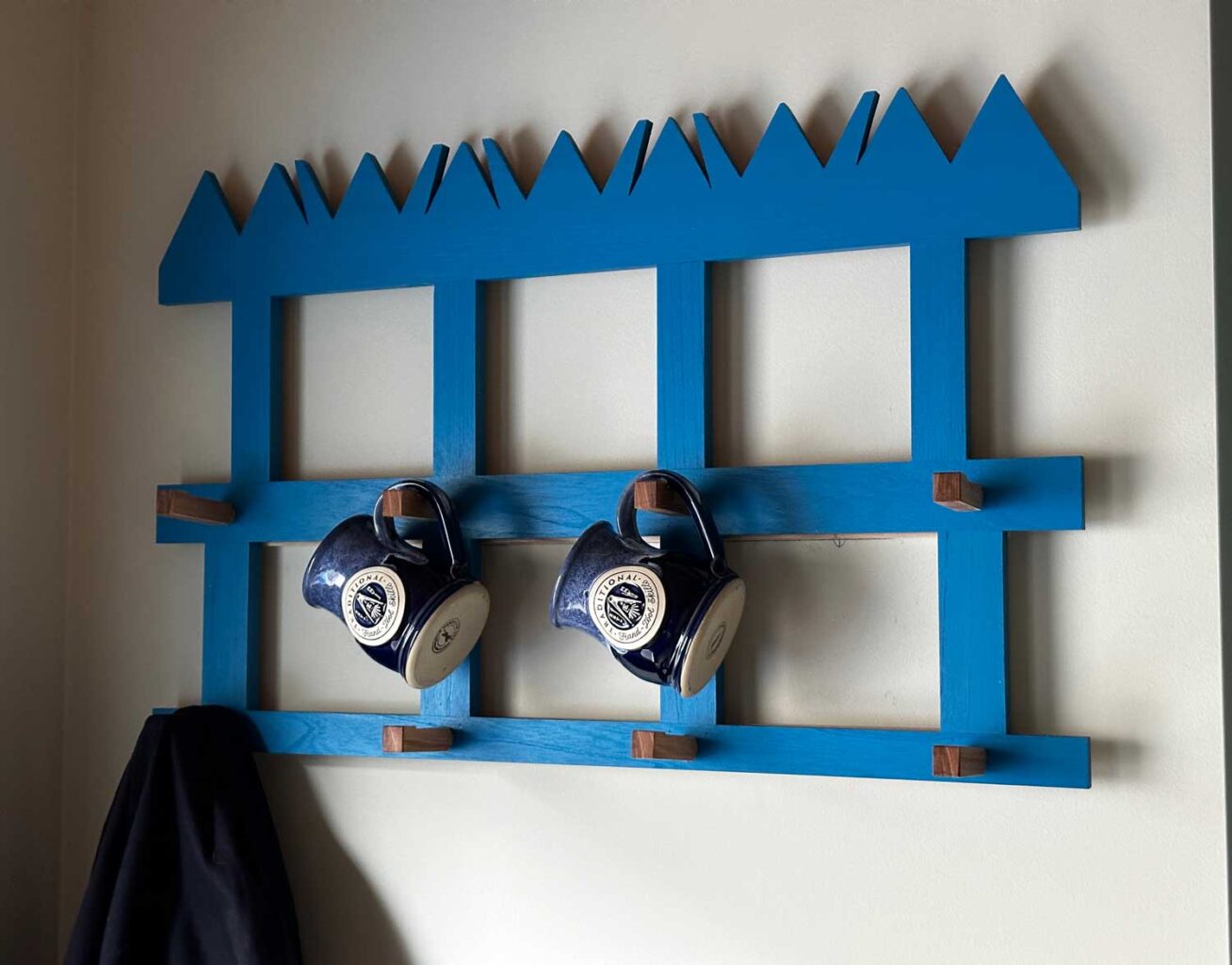
Update: Comments are now closed. Join us again next week for more woodworking Q&A merriment.
The final project for Chris’s next book, “The American Peasant,” is done, dusted, painted and hung on the wall – the coat and mug rack shown above. (The coat is the Lost Art Press Chore Coat, made in Cincinnati; the Lost Art Press Coffee Mugs are handmade for us in Minnesota.) So now Chris needs other distractions to keep from finishing the book. Help him out by posting your woodworking questions in the comments below (preferably about chairs – as that pretty much lets me off the hook…so I have time to complete the current project on my bench).
(Chris writes: Please ask Megan about how the Dutch tool chest book is coming.)
Also, note that there may a lag between your asking and our answering.
But let me help you with answers right away to a handful of common questions:
• What’s on deck for 2024 (includes Stick Chair Journal 2 and Dutch Tool Chest)
• What wood for a workbench
• What wood for a workbench, snark edition
• 52 Workbench Questions & Answers
• What finish for a tabletop
• This bandsaw blade, 1/2″
Comments will close at around 5 p.m.
– Fitz
Are there still plans for a finishing book by I think it was done Williams?
Alden Butler
Thylacine@homesc.com
Thank you
Don mentioned it to me the last time we chatted, so yes. But no ETA on that one yet.
In one of Chris’ books he described the Janka hardness test and there was additional info in the appendix. Anyone know what book this was in?
thanks,
Les
In case you want to go down the Janka hardness scale rabbit hole, the USDA Forest Service’s Forest Products Lab does a great deal of the work and establishing standards. Here’s a related paper. https://www.fpl.fs.usda.gov/documnts/fplrp/fpl_rp643.pdf
thank you
Maybe also download a copy of the Wood Handbook. It has a bunch of those kinds of numbers if you want em: https://www.fs.usda.gov/research/treesearch/62200
Anarchist Workbench
thanks
The link to 2024 things isn’t working for me (rest do)…
I re-linked it. Should work now. Sorry!
I was asked to make a live edge cookie project (three tier serving tray) for a friend. One of the pieces that I need has the bark delaminating. I was planning on using a tung oil finish. Now I need a method for securing the bark and still using that finish. The crack is as large as 1/4 inch in places. Any and all suggestions are welcome. And the friend knew ahead of time I don’t like live edge.
Michael- if I may… these are log cross sections? The circumference of the wood is drying and shrinking from the circumference of the bark. You’d need to cut the bark to a length (with a fine-tooth saw) to match the wood circumference whenever the wood finishes drying, then try to glue it back in place (if it still bends), and keep your fingers crossed. Then as time goes by, hope deteriorating bark doesn’t flake onto the food being served. It’s projects like this, where my confidence of success is low, that has taught me to check my pride and say no even to friends and loved ones. They get over it.
I made my daughter some log cookies for her wedding decorations 5 years ago. After I got them dried I finished with shellac. It really soaked into the bark and kinda glued it. We still have some and the bark is still good.
Visiting an exhibition of works by the Brueghel Family last week, I noticed in a lot of paintings a piece of furniture I had never seen before: A low table (or high stool) made out of round wood, three vertical legs, a solid wooden top (or seat) and a very distinctive set of stretchers. You can find it in The Triumph of Death, for example, left and right of the round, white-clothed table.
Not having read “Cricket Tables,” are these maybe the “krukstoelen” Derek mentions in his interview with Meghan?
Hello Dries,
I helped Derek to the best of my ability with some etymological research on “krukstoel”, and the below is what I came up with for him to use. I take the liberty of assuming from your name and the fact that there is a Breughel Family exhibition on right now in ‘s Hertogenbosch that you might understand Dutch, but if not, you’ll find my translations of the key findings in square brackets, while I’ve highlighted he main result on “krukstoel” in bold, based on which I’d say that the triangular tables you refer to in The Triumph of Death are not likely to be “krukstoelen”.
The below is based on Historische woordenboek Nederlands en Fries [Historic Dutch and Friesian Dictionaires] (https://ivdnt.org/woordenboeken/historische-woordenboeken/). This is a collection of five dictionaries, the ONW covering Old Dutch (500–1200), the VMNW for Early Middle Dutch (1200–1300), the MNW for Middle Dutch (1250–1550), the WNT for Dutch (1500–1976) and the WFT for Friesian (1800–1976). It is possible to search in all five together, using the modern spelling of words.
“CRUC, CRUCKE
Woordsoort: znw.m.,v. [noun]
Modern lemma: kruk [modern lemma: kruk]
Middelnederlandsch Woordenboek: crucke
Oudste attestatie: West-Vlaanderen, 1285 [oldest source]
Aangetroffen spelling: cric(k), cricke (steeds met ontronding van -u- tot -i-) [spelling variants]
Korte betekenis: T-vormig stuk hout; Kruk [basic meaning: T-shaped piece of wood]
+↪1. (Vr.) T-vormig stuk hout, stuk hout met een dwarsstuk aan de bovenzijde. [T-shaped piece of wood, piece of wood with a crosspiece at the top]
CRUCKE
Woordsoort: znw(v.) [noun]
Varianten: cricke, crocke [spelling variants]
Modern lemma: kruk [modern lemma: kruk]
(cricke; ook crocke), znw. vr. Mnd. krucke, krocke; mhd. krücke, krucke; ohd. chruccha; hd. krücke; ags. cryce; eng. crutch. Zie verder de Wdbb. van Grimm, Kluge, Franck en E. Müller.
–↪1. Kruk, een dwarsstuk aan het boveneind van eenig voorwerp. [a crosspiece at the top of an object] — Ook haak. [also hook] Nog heden heeft kruk de bet. vuurhaak (Van Dale 763).
↪Ook in den zin van iets met een dwarshout. [also in the sense of something with a wooden crosspiece] Vgl. kruk b. v. in de uitdr. “vogel op een kruk”. Zoo b. v. van eene galg eener bepaalde gedaante (vgl. crucgalge) [a certain type of gallows]; ook van een kruis, in den vorm van eene T. [also a cross in the shape of a T]
–↪2. Bepaaldelijk een stok met een dwarsstuk of kruk [particularly a stick with a crosspiece or crutch], krukstok, bij verkorting ook kruk geheeten [krukstok also shortened to kruk]. Vgl. hd. krückenstock, krückstock, krückenstab. Vooral als steun voor hen, die moeilijk gaan. [mainly as a support for those who have difficulties walking] Teuth. crucke, stelte, schaitze, staca, gipsa. Kil. krick, kriecke, j. krucke, scipio, baculus; krucke, scipio, fulcimentum subalare; krucke Becano dicitur scipio cum transversario ligno ad rectos angulos imposito. Nos Belgae hodie bacillos in crucis formam, quos aegrorum brachiis sustentaculum subjicimus vocamus cruckas; krucke j. stelte.
↪Ook in den zin van staf, rechterstaf, het zinnebeeld der rechtsmacht van den “cruchoudere”, d. i. den baljuw, amman of schout. [also in the sense of staff, judge’s staff, the symbol of the judicial power of the staff holder, i.e. different sorts of officials]
As we can see, one of the main meanings of ”kruk” is thus crutch, both literally what we today would call a crutch, and crutch-like objects in general, i.e. something with a short crosspiece at one end.
Then there is rather long article in the MNW (Middle Netherlands Dictionary, 1500–1976), which I will not copy-paste in its entirety here; you’ll find it at https://gtb.ivdnt.org/iWDB/search?actie=article&wdb=WNT&id=M035746.re.37&lemmodern=krukstoel&domein=0&conc=true. Of most interest is this:
In de bet. 18) is kruk een verkorting van krukstoel; zie de opm. bij deze bet. [In meaning 18) kruk is an abbreviation of krukstoel; zie comment under this meaning.
And this is what we find in that comment:
Een stoel zonder leuning, een tabouret; dergelijke krukken, en wel op hooge pooten, worden o.a. bij kantoorlessenaars gebruikt. Eene verkorting van krukstoel (zie de Samenst. in de bet. 18), oorspronkelijk een driepootigen stoel met een rechtop staande lat als leuning: die lat, van boven van een dwarslatje voorzien, had den vorm van eene kruk. Krukstoel is dus eene samenst. met kruk in de bet 5). [A chair without rest, a tabouret; such stools, on high legs mind, are used by i.a. office clerks. An abbreviation of krukstoel (see Meaning 18), originally a three-legged chair with an upright batten as back rest: said batten, at the top equipped with a crosspiece, was in the shape of a crutch. Krukstoel is thus a composite with kruk as in meaning 5) {i.e. crutch}]
And here I think we have it! Or, at least, I now have a theory!
Once upon a time there was a form of chair called a krukstoel, which had three legs and a simple back rest in the form of an upright batten with a crosspiece handle at the top. Most likely it also had a round seat. With time the word also came to be used about back rest-less seats, i.e. stools, that were also round, and often enough had only three legs. Some of these stools were quite high (think bar stools, or indeed those of office clerks).
Apart from the many variants in spelling, including cricke, crice, cric and so on, the at least modern Dutch pronounciation of kruk is much closer to an English y-sound than a u-sound, probably somewhere in between creek and cryck, so from there to it sounding in English ears more like crick(et) than cruck(et) or crock(et) seems rather likely to me. In any case, languages in general and loanwords in particular tend to lead a life of their own.
I therefore think it rather likely that a smallish three-legged table with a round top would be associated with a three-legged seat with a round top, that the distinction between a kruk (a regular stool with no rests or supports) and a krukstoel (a similar seat but with a crutch-like batten as back rest) had become blurred, if ever it was truly understood or respected, and that from a krukstoel table (i.e. a table that looks like a stool writ large) could emerge the name cricket table.”
I defer to Mattias on krukstoelen! But on those triangular stools, see Follansbee:
https://pfollansbee.wordpress.com/tag/3-legged-stool/
and Follansbee on The Woodwright’s Shop:
https://www.pbs.org/video/woodwrights-shop-troublesome-triangle-stool/
Wow, thank you for all the information! Yes, I visited ‘s Hertogenbosch and searched online for some information. Turns out you’re better at finding stuff in Dutch than this Dutchman here.
The Fight Between Carnival and Lent shows some real “krukstoelen” then, I guess. And it appears the modern Dutch word for a stool is actually the word used for the backrest that’s not present anymore… Makes perfect sense! To add to the confusion, asking for a “stool” in the Netherlands gets you a chair, in Czechia it gets you a table.
The videos of Peter Follansbee are very helpful should I want to make some. Thanks for pointing them out.
You’re very welcome, Dries! Although I’m Swedish, I’ve lived in Belgium for the last 26 years, so it was fairly close to home, as it were, although I was very lucky to find those older dictionaires of earlier forms of Dutch online – my Dikke Van Dale (almost) only gives modern meanings.
And yes, you are right: those must indeed be krukstoelen in that painting, not least the one on which Lent is sitting! Fits the description to a T! (Or should that be “to a T-shaped back”?) Although they don’t have round seats, like I surmised, coming at the question blind and from the cricket table perspecive, from a construction point of view they make complete sense: if you want to add a backrest to a triangular stool, that is of course how you would do it: make one leg longer and add a crossbar on top, both for shoulder support and to facilitate handling.
It is also pretty obvious how they came to be named “crutch chairs” – that back rest really looks like a traditional crutch (of which there are also pleanty of visual evidence in said painting).
As for how the words and word combinations (stoel, kruk, krukstoel) changed in meaning and usage over the centuries is, I fear, far beyond my understanding, but that such changes occur is a fact.
Cheers,
Mattias
We are constantly reminded by engineers that the triangle is the strongest form. However, I see very few triangles in stick chair designs (although the Gibson sticks have a bit of triangularity). Why do you think this is? Too hard to assemble the tenons? Just doesn’t look right?
I don’t see too many complete triangles in furniture construction. But partial triangles are everywhere in chair construction. And those help immensely with strength.
There probably is some visual aversion to the form, as well. The A-frame house is always an oddity.
A agree with Chris; I’m going to put my civil engineer hat on again and say that there’s a difference between “strongest” and “strong enough”. Most design is a series of compromises among numerous factors and aesthetics is an important one. This reminded me of my favorite professor at Cal (a structural engineer) who commented about one of the newer tall buildings in San Francisco that used exposed triangular trusses. Very strong, but his comments was “it looks like the box someone else’s building came in.” It’s at One Maritime Plaza if you want to look it up!
Good morning Chris and Megan,
A couple of questions on Piggly No Wiggly glue:
It says in the description to avoid letting it freeze. How essential would you consider that injunction to be? The reasons why I’m asking is that (a) my bottle has travelled as air freight across the Atlantic, and I believe a cargo hold at 33,000 feet can get purty darn cold, and (b) when I did a three-block glue strength test, I got glue failure. I have a second three-block test glued up which I will whack with a hammer tomorrow to control against user error, but wanted to ask already if you think freezing might be a culprit, should it be found wanting?!
After heating it to about 65°C ≈ 150°F, the glue flows nicely out of the bottle, but within less than a minute it starts going gummy in the glass jar (pre-heated to the same temperature) that I use to bring it to the joint, so that applying it feels kinda like painting on rubber cement. Would you say that that is expected behaviour? My only previous experience of hide glue is with OBG, which I’ve found stays runny and smooth to apply for rather longer. I am of course aware of the instructions for how to make it runnier or extend the open time, so this question in no way implies any criticism, but is just about better understanding what to expect of PNW as sold.
Cheers and all best,
Mattias
Hi Mattias,
You might have a couple things going on here. Either the glue was frozen during transit or we didn’t skim the air bubbles sufficiently. Also, if it’s gelling too quickly there might not be enough salt in the mixture.
I’ll send you a couple bottles on Monday via FedEx and we will see what happens. Sorry for the trouble…
Thank you, Chris! That is exceedingly kind of you, although my sense of fair play rather thinks I ought to say “shucks, there’s no need for that” – not least given that with FedEx it’ll run the same risk the previous bottle did with DHL of catching a stratospheric cold.
I’ll drop you a line tomorrow after I’ve taken a lump hammer to the second three-block test glue up, and we can decide together based on how that goes if any more glue ought to go on a journey, or not.
In the meantime, please accept my sincere gratitude for both the reply and the offer!
Cheers,
Mattias
Another thought…in case it is foam…after you heat the glue up, skim off the top 3mm or so and try it again.
In making a three-legged staked stool, the diameter of the top is 10-12 inches of laminated hard wood. How do you joint the faces without a 12″ jointer before running through the planer to get the mating faces flat? Most available jointers are 8″.
I use a jointer plane, or a smoothing plane – whatever I have handy. If the wood is rough, I dress it with a jack first.
Good morning! Two ATC question. 1) how exactly does Chris store his joinery saws between his panel saws? Extra slots in the till? 2) for the lid panel, I have enough clear short pieces to glue a center panel with grain oriented parallel to the short axis of the lid. Would you do that or pick up longer pieces so the grain is oriented with the long axis.
They hang down between, with the handle catching on the top of long saws, or the toe resting on the floor. You can see it if you scroll down to the saw section in this post: https://blog.lostartpress.com/2023/01/01/the-anarchists-tool-chest-at-age-11/
On the lid panel – I’ve never thought about running the grain f to b on the center panel. Depending on the number of pieces and how much your species is likely to move seasonally, I might leave a little extra room in the groove to accommodate? It would look odd to me…but because I’m used to it running lengthwise. I don’t see why it couldn’t work.
1) I have my joinery saws in sheaths to protect the teeth. And I put them toe-first between the blades of the panel saws.
2) No problem as long as you accommodate the wood movement in the panel. It will be more significant with the grain running the other way.
Hi- Happy New Year. After building a few Stick Chairs the traditional way, I am now attempting to build one via Chris’s design from his book with a steamed bent armbow. I’ve never bent wood before and was wondering if I should stay away from kiln wood? Unfortunately, it’s the only thing available locally for me unless I try to attempt to harvest green wood which (again) I’ve never tried. And if I only have kiln wood are there any tricks that can help me be successful? Soaking it? I’ve read soaking it with fabric softener? Thanks, Charlie
Yup. You have it right. Soak it (I have a PVC pipe that capped for this). Fabric softener seems to help. I’ll soak it for a week or two, and then bend it. If you can afford it, you might consider using the cod-bend hardwood instead. All you need is a form. No steambox. No soaking.
https://blog.lostartpress.com/2023/12/27/cold-bend-hardwood-why-and-how/
Maple Syrup or Cane Syrup?
Waffles or pancakes?
Pizza or calzone?
Scrambled or Fried Eggs?
I wish all the Open Wire questions were this easy: maple syrup, waffles, pizza, fried.
If you have access to some hickory bark, homemade hickory syrup is easy to make and well worth it– your first answer may change!
Woodworking adjacent question here. I recently was catching up on the ShopTalk podcast and came across the episode informing that FWW has been acquired. As a reformed corporate man myself I heard the too familiar tropes of “new opportunities” and the ability for them to all work together to come up with great content…. aka “synergies” (shudder) all the while trying to sound positive but probably really freaking out inside.
As folks that were editors of a similar magazine that was acquired by the same corporate overlord (I think) what are your thoughts on the future of FWW. Personally I’m pessimistic, I’ve been in the room for M&A discussions no matter what is said publicly. I’d like to hope I’m wrong but publishing seems much more cutthroat and brutal than the industry I was in.
If AIM (the new owner) leaves the current staff in place and lets them continue to do good work, the magazine will be fine. I think the current staff there is really fantastic. I wish I could hire the lot of them.
AIM did lay off two FWW editorial employees, so that sucks.
Other than that, I can’t say much without being that a-hole on the internet who is talking out of his butt. I’m keeping my subscription. I’m hoping for the best. But I won’t be surprised if things don’t go well.
AIM didn’t acquire PW until rather long after I was gone – so I have no experience with that group as an owner. And I am hoping for the best! That is, AIM keeps the staff in place and lets them do their jobs, which they do well. Don’t mess with a good thing. So fingers crossed!
Just a quick note to wish you all a happy new year and say thanks for the inspiration.
I have a Lee Valley tapered reamer that is 4 sided at the bottom. My drill has 3 prongs. I can’t seem to tighten my drill enough to keep the reamer from falling out of the drill. In your chair video you don’t appear to have any problem with your reamer staying in the drill. Is there a trick or procedure that you use to overcome a 4 sided bit working with a 3 sided drill head?
It sounds like you have the Professional reamer, which is designed for a brace. The standard reamer, which I use, has a six-sided post and fits easily into a modern chuck.
You can hacksaw off the four-sided post and you will be left with a round post, which will work OK in a drill.
Is the Crucible Claw Hammer an idea in the works or is it more of a definite? I very excited about it.
Keep up the great work
The programming is done. The engraving has been designed (yes, there will be a deluxe version with engraving).
The problem is the handle. I need to finish designing it and make the prototype handle for it. So I’m the problem. There are just not enough hours in the day. And stabilizing the Anthe building continues to occupy all our extra time and money.
This week we’re having to rebuild part of the back wall of the third floor. We’re not doing the masonry, but coordinating the contractors and work is a lot.
Good morning
I just finished building a chair I’d like to paint. I was wanting to spray it rather than apply by hand. Could you recommend an inexpensive sprayer? Thanks a lot
We like the Earlex 5500. Inexpensive and provides great results. I used the earlier generation of this sprayer for more than a decade.
https://www.leevalley.com/en-us/shop/tools/supplies/finishing/applicators/114652-earlex-spray-station?item=03K0320
Good morning! If I use a mortising machine to make the 1-1/4″ mortises in my Anarchist’s Workbench build would it be better to make two passes with a 5/8″ chisel or three passes with a smaller chisel leaving the middle of the mortise for last? Thank you for doing this!
If your machine will drive a 5/8″ chisel without complaint, do it that way. The chisel won’t deflect, like some of the little ones.
when do we get to see a blog post with a sample draft of some DTC chapter(s)?
Erm… leavemealone!!!!
Goodmorning!
I am probably being dumb but I am confused as to the seemingly conflicting advice of a very closely fit chipbreaker on a smoothing plane and having a slight curve to the iron. I have been just setting the chipbreaker to where the curve ends on the edges of the iron, am I on the right track?
I guess the question is how to set a chipbreaker on smoother with some camber to the blade?
Thanks!
Hi Jace,
Some people sharpen a curve on their chipbreaker to get the sucker even closer.
For me, it all depends on results. If your process is delivering perfect surfaces, then stick with it. If you are still getting tear-out, curing the breaker a bit will allow you to inch even closer.
In one if the links Chris recommends that for a workbench top the heart of the wood should point up. Why is that?
For the same reason that the heart side goes out (ideally) on casework 🙂 (think cupping direction)
Any plan to make a Crucible travisher?
Nope. There are so many good ones out there, I have no idea how ours would be different.
In my shop I work at my bench with my tools on the wall. I like this way of working and do not see me ever changing. However, the Dutch and Swedish tool chest forms really have me interested in converting my grandfather’s slant lid carpenters tool box made from pine into a Swedish style box. It needs a new lid that will hinge from the top instead of the bottom. I have 2 questions. Would you build drawers at the top like in the examples you saw overseas or would you build a pull out till that goes the whole length of the box? Second question, I thought about using it like a traveling tool chest putting my chisels and brace bits in tool rolls but I really don’t foresee myself taking a woodworking class so how could I incorporate it in my shop? Maybe design it for tools more infrequently used? I will probably build a stand for it to elevate it some.
Hi Jeff,
We haven’t built a Swedish chest yet, I’m afraid. It’s on the short list. Our first stab at it will be to build it to the print and then use it to see what we would change (if anything). That’s what I did with the Dutch and English chests. Usually you find that the dead woodworkers got it right and there’s not much to change.
The way we use the Dutch in our shop is the open top is for everyday tools for students. The bottom compartments are for tools we don’t need frequently.
Sorry I can’t answer your question directly – we just don’t have the experience yet to make a comment.
Are there any go-to sources that you use for culinary inspiration? I understand LAP may not be an obvious publisher for cookbooks, but looking at the Mechanical Library posts*, I can’t help wondering if your kitchen libraries offer any fun surprises.
thank you for sharing some love of my hometown, Madison Indiana!
I loved Cooks Illustrated until my former boss took it over and ruined it. I do like Chis Kimball’s 177 Milk Street, though a lot of issues read like “white person visits exotic country and is amazed by the food,” which gets old.
Probably my personal favorite source is Kenji López-Alt, who reflects my sensibilities about experimentation, tradition and questioning conventional wisdom.
https://www.kenjilopezalt.com/
Good morning. This is random but I have been searching for slotted screws that are not brass or aluminum. Or at least not shiny brass. I have found a couple internet companies that sell them but with the cost of the screws and the absolute junk screws I’ve experienced in The last decade, I figured I’d ask someone who uses them if they know of a company they trust or a product line they like. I appreciate your time. Thank you, Chris
blacksmithbolt.com is where I usually get slotted (and other) screws…as long as I remember to order ahead of when I need them!
Thank you! I’ll check it out
Chis/Megan – Good morning to you both! I just ordered several books from LAP, one of which is Nancy Heller’s book, “Kitchen Think”. I have seen several pictures that have been posted of your wonderful kitchen at Willard and was wondering if you would share what kind of paint was used on the kitchen cabinets, and a follow-up please, how has it held up and would you use it again?
Thank you…Andrew
It’s a colored conversion varnish. It is as tough as nails and had held up well. It will fail someday and look like hell. But the cabinetmaker wouldn’t hand over the cabinets without a finish (I wanted to milk paint them).
Inspired by “Ingenious Mechaniks” I have built a low workbench, and am now adding a shaving horse to use with it. One confusing aspect to the instructions in the book is comment that the example in the book was designed to accommodate existing wedge shaped cutouts on the sides of the bench. Does that mean that there is no need for cutouts at all, or just that if starting from scratch one can place the cutouts at a different location if desired?
You don’t have to have the cutouts in the benchtop for the shaving horse to work. The comment is only to note that I had to make slight modifications to the shaving horse’s parts because of the cutouts. Sorry for the confusion.
Good morning! I’m building the AWB. And probably overthinking things. The current over think concerns the 5/8 drawbore pegs. The book says to use white oak. But the big box stores dowels are just labeled oak, and they are red ish. I finally found a batch of dowels that have the grain dead straight (yay!) but the dowels are all bowed about 1” over 3 feet. Are these ok to use? If yes, should I care how the bow in the pegs is orientated to the offset in the joint? See I told you I overthink! Thanks for the help.
Red oak will work if the grain is straight. And the curve in the dowel won’t matter much. The bores will have its way with the peg.
Thanks!
Chris,
I have two questions. Does the cold bend hardwood take finishes as regular wood and where are the dimensions for the jig you use to bend the arm bows demonstrated in your books. Thank you
Hi Joe,
It finishes just the same when it’s dry.
The dimensions are on page 512 of the Stick Chair Book, which you can download for free here.
https://lostartpress.com/products/the-stick-chair-book
My wife inherited an old gateleg type table from her grandparents similar to this one (https://blog.lostartpress.com/2017/04/30/the-not-ikea-gateleg-table-its-for-sale/). I’ve always found it awkward to use as a dining table because the central base does not permit someone’s legs to sit under the table. Is someone meant to sit in this spot?
I don’t think so. But a child’s highchair goes perfectly there.
There are always going to be compromises when you have furniture that folds up.
Hey Chris,
I attempted to glue up the undercarriage on a stick chair, but the legs refused to seat into their mortises (and not from lack of force — I hit them with a lump hammer, hard, and wound up splitting the seat). I took everything apart to try and figure out what was going on. I cleaned the glue off the tenons, tried to seat a leg again, but it still wouldn’t seat with much hold.
I’m wondering if I over compressed the mortise during dry fits? Has this ever happened to you? Any thoughts?
Some extra details if they help:
– Legs are ash with tapered tenons
– Seat is white pine
– Tenons were tight in their mortises during dry fit
-John M.
Usually this problem is because the stretchers were drilled too wonky. Their misalignments prevent the legs from seating.
Investigate the stretchers one at a time. Try to assemble without the medial. Then try without one side stretcher. Then without the other. The error will reveal itself (usually).
Greetings Chris and Megan, Do you have a projected time frame for the brass Warrington hammer in 2024? Thank you.
Not yet. We have to get all our current tools in stock first before using machine time on that niche product.
I have been exploring building period pieces, watched videos, read some blogs and purchased Tony Kubalak’s “Build a Philadelphia Chippendale Dressing Table”. What I’ve been searching for is someone that built such furniture with hand tools only from start to finish (ok fine, they didn’t chop the tree down but did dress it). Reason being is that’s how I’m set up and I’ve leaned into for the last few years. Obviously I know it’s doable but I was wondering if anyone does do this today? I heard from Chuck Bender that he more or less does this but it hasn’t been recorded in any way. Know anyone that did?
P.S. Chuck is the man
Chuck is great. But Chuck uses a LOT of machines in his work.
If you are looking period hand tool purists, join SAPFM. Go to their forum. You will find them.
Shot in the dark here, but maybe one of you or a reader will have ideas. My wife is getting into sewing. I would like to get her some good books but it’s hard to find the good stuff vs the dross. Does anyone here know of a good author or a good publisher to find good information?
That is completely out of my area of expertise. We didn’t have any sewing titles at F+W (we had everything else). So I don’t even have any good secondhand knowledge.
When I have questions like this, I usually go to the newsstand at a very good bookstore. Magazines vet writers. And good magazines are still very valuable sources of information.
Thanks, I’ll do this!
The publishers of “Fine Woodworking” magazine Taunton Press (recently sold) also publishes a magazine called “Threads”. You may want to look for an issue. My daughter sews and has said “Threads” is pretty good. The print version is the same quality as FWW. All the back issues are available on a thumb drive, too.
First, I would recommend getting a very simple pattern and just following the directions on it. Get some gingham and just sew along the lines if you haven’t gotten a feel for how using a sewing machine works.
Second, take a sewing class or two.
Third, check out videos on You Tube (Sewing with Nancy for one).
Sewing is not difficult. Following the steps and taking your time are key.
Best of luck.
Over the last few Open Wires I’ve found that in writing my question out and editing for clarity, I realize that I already know the answer. I’m just reaching out for assurance from my fearless stick chair leader. I haven’t sent these questions to save everyone’s time. But I love reading through the Open Wire questions and answers, so I thought I’d go ahead and post this one anyways, because I’m sure many others have it during their first stick chair builds, and I’m currently building my first two in full Cherry. And the might be a differing perspective I haven’t considered.
I’m about to drill the 5/8” stick mortises in my first two chair seats. I’ve had Woodowl tri-cut augers for the longest time, but acquired some Star-M bits last year, to couple with a Go-Drilla, just for this task. I also have the Tenon/Plug cutter from Lee Valley. I decided to make a test joint in scrap cherry, and realized the plug-cutter tenons drop into the Star-M holes really easily with hand pressure. Almost too easily, no twisting of the stick required. To test further, the Woodowl auger mortise fits the plug-cutter tenon so tightly, it takes some hammering to seat it (in a good way), and I can literally not remove it, no glue required. This seems too tight for assembly, but I know I could use a wrench to press the tenons down a little smaller. To test further, I tossed some glue onto the looser fitting Star-M joints’ tenon, and this added swelling made the joint much tighter, requiring twisting to fully seat. Within five minutes, the joint was too tight I also could not remove the stick, even though I knew the glue still had open time.
I’m thinking the looser fitting joint has a lot of advantages during assembly. It also allows room for glue to actually be present in the joint instead of just being squeezed to the bottom of the mortise. Lastly, it seems more repairable long term, in blind mortises. Those same advantages also make me worried about how long the joint could last.
These are all good tools, and I don’t want to keep chasing some other drill bit combination, like the recently suggested BB custom bits and extension. Although I do think the BB custom bit extension would work well with the Woodowl augers… (“Don’t tempt me, Frodo!”) It’s so easy to think the answer is just another tool. In a production environment, getting the tooling right can mean time savings that compound with each build. But that same mentality can also starve projects of the creativity. I’m an amateur woodworker, not a production shop, an American peasant if ever there was one.
So here’s my plan. I’m using the Star-M bit mortises. To counter my concerns about longevity, and the fear of one day picking the chair up by the arm bow and the whole upper assembly peeling out of the seat, I’m going to drill the middle of each of the short sticks as a through mortise, and wedge from underneath the seat. I’d do the same for two of the long sticks, but didn’t plan for that in their overall length. Maybe on the next chair. I’ll likely just pin two of them from the back of the seat. I know all the differing angles of the sticks should be enough to hold it all together, but these little details are what will make this set of chairs unique.
If you are a chairmaker, you will struggle with bits and the fit of your joints. And you will find your way through to what you want and stick with.
I like to have one of the tools so it’s adjustable. So spade bit plus plug cutter is a good combo (the spade bit is adjustable). Trident bit plus power tenon cutter is good (the tenon cutter is adjustable). I find it difficult to mix metric with SAE.
You are on the right track. If you worry about the joint, peg it, wedge it, compress it beforehand. And find the right path that allows you to sleep at night.
I’m building a stick side chair, (slowly, I might add). Poplar seat, octagonal tapered legs from maple with 1 inch tenons,maple crest rail and sticks with no undercarriage. I think I have decided to shape the sticks octagonal as well double tapered from the middle each way. Do you make many chairs with sticks shaped this way and if so how do you like this form?
This is how I make most of my chairs these days. I love the shape. The one I showed on Instagram this week has tapered octagonal sticks (below the arm).
I’m not on instagram. Would you please post that picture to your Facebook page?
You don’t have to be on IG to see it. If you look on our blog’s home page, the right rail has a photo of it. Scroll down a bit. You’ll see it
Thank you Chris!!
Has anyone had experience with Allback linseed oil wax? Will this table top finish protect from rings by my cold PBR Beer?
It’s very similar to our Soft Wax. We love it. Low protection but easy to repair, and low toxicity. It is not toddler-proof.
I don’t know if I like building chairs, but on a whim I bought the Gibson video last summer. Maybe I’ll build one or two of them, so I don’t want to go overboard buying a lot of expensive new tools that might see limited use. I know that you have experimented with different tools over time. For example, I’ve seen different drill bits and tenon cutters mentioned in blog articles. If you were a flat woodworker with all the related hand tools, what limited set of chair specific tools should I buy in 2024 based on the assumption that I’m just dipping my toes into chair making?
I caution you against that first chair.
I was going to build 2 last year
I think I built 7, I gave a few away.
Now the wife wants ladder backs and rockers
Oh well is keeps me out of the tavern
Search our blog for “chairmaking on the cheap,” which is a series of how to do operations with spade bits and plug cutters.
What are the proper dimensions for Megan’s tool rail and the gap behind it in the Anarchists tool chest? I’ve seen 3 sets of dimensions, all different.
Proper depends on your saw handle thickness – the gap has to be wide enough that the sawblade fits all the way down so the handle rests on the tool strip…but not so wide that the saw falls through. On the one in my chest at the shop, that gap measurement is 5/8″. I go 11/16″ when I’m building that style for a commission – won’t be too big, and will accommodate slightly thicker handles.
What about the front to back measurement of the rail itself? I know the holes are 1/2″ on 1-1/8 centers except for the really wide blade chisels.
what is the current protocol for using Heron linseed oil paint?
I have a long post on linseed oil paint posting tomorrow. But in short, right now I like to wipe on a coat of purified linseed oil and let it dry, then apply a full-strength coat, or slightly thinned (no more than 10 percent) with low odor mineral spirits (Travis at Heron uses turpentine if he wants to thin).
Are you still planning on an event later this month at the Anthe building?
We are still thinking there will be a Feb event – details to come.
Good morning. Do you have plans to bring back the design curves?
We do not. Sorry.
Ok, thanks. I do see that Lee Valley still has some.
I’m making a strong trunk from Campaign Furniture. Brasses have been hard to get. I got extremely lucky to find high quality vintage hasps from a seller in India. However these appear to have been attached to leather trunks and were riveted on through square punched holes in the hasp. I bought some brass rivets from McMaster and experimented on scrap, but it’s been hard to get a good fit. Would I be crazy to drill out and countersink these holes and just use brass screws?
No. You would be completely reasonable and right to drill them out and add screws!
G’Day Megan and Chris,
Are there limits to hand woodworking? Specifically. The next project I want to make is a Davenport/Captains desk (and then a Captains chair to make Chris happy). The top and base are at right angles that appears to cause difficulty with wood expansion and contraction. It doesn’t appear at first glance that I can make one using the ideas in The Anarchist’s Design Book. I can buy plans that use a frame and panel type construction, but I’m not entirely happy with this idea. Cutting the groves for the panels by hand does not appear to be very user friendly.
If you can show us some links to images of what you want, and then tell us what specifically is not working in your head, that would help me immensely.
Megan, how’s the dutch toolchest book progressing. Chris wants to know, or at least he wants me to ask. I will be building one, but first I need a bench.
Last week I asked about German benches, and per Chris’s advice I did more research and got started, or at least I’ve made some decisions and started some drawings. I have a 30 year old commercial bench top that’s made from Rhodesian teak. I suspect the construction is similar to the Levard bench I read about in one of the blog posts. I’d like to take that top and put it on the undercarriage for the 1505 bench. I’d like to know how you determined the dimensions for the legs. My top is only 16 1/4 x 60 x 3 1/2. I’m shooting for maximum stability, strength and weight. I have all kinds of questions about the angles for the staked tenons, but maybe that’s a question for next week.
There aren’t rules for this stuff. In general, use 8/4 material and use widths that look massive and like other benches. Commercial ones are spindly, so consider 5″ widths for legs and 7″ to 12″ wide for stretchers. At some point it looks ridiculous, back down a little from that.
Thank you for the advice I’ll start with 5 1/4 legs since I can glue up a couple of 8/4 boards for that. I don’t see any stretchers on the 1505 bench, but maybe I can work something out after I get the angles for the legs figured out.
Dear Chris, dear LAP team, dear community,
I am a hobby woodworker from Germany and will be visiting my sister-in-law, who lives near San Francisco, in February. I fear that our time will not allow a visit to Covington, as much as I would love to.
My question is if anybody could point me to a good used/vintage tools trader in the San Francisco / Lake Tahoe area. It is difficult to get any (halfway decent) used tools in Germany, and no metal planes whatsoever (obiously). I would very much like to use the opportunity to at least drool over some nice stuff – let’s see what that baggage allowance will let me actually take home (or my wife).
Any tips will be much appreciated. And many thanks to Chris and the LAP team for their great work!
Keno
I hope you get some answers to your question! I live in the Central Valley between SF and Tahoe and don’t know of any and would like to know of some. It seems the old time antique/junk shops have disappeared and what’s left is Ebay and other online sellers and estate sales. Not sure if LAP facilitates private communication between commenters, but maybe we could talk!
Dictum carries some nice metal planes (Lie-Nielsen and Veritas), and their showroom in Metten is worth the trip.
I cannot think of any old tool heavens in the Bay Area. I hope someone else here has some suggestions.
I have my grandfather’s toolbox. It is similar to Megan’s grandfather’s toolbox. It has a conventional half-lap chest lock. At some point many years ago. my father let the lid close with the key inside. As you probably know, this type of lock latches in the locked position when closed. He fretted for a while over this then forced the locked. The screws in the catch plate pulled out from the lid stripping the threads with no damage to the lock or catch plate. I have the original key, catch plate, and screws. I want to repair the screw holes in the lid. How would you approach the repair? I have considered drilling them out and gluing in cross-grain plugs from a plug cutter or routing out a strip in the inside of the lid to provide new wood for the screws. The material is approximately 3/4” and appears to be white pine.
We glue toothpicks into the screw holes. Let the glue dry. Cut them flush. Then pilot and rescrew.
Good Afternoon! I’m making a stick back stool along the lines of Tage Frid’s stool. I was planning to make my legs 2” longer than his design since I’m mainly legs too. Are there any rules of thumb for modifying the resultant angles as you lengthen the legs? Thanks!
I would bring the feet in a little bit to occupy the same footprint as the original. That is the safe thing to do….
I am nearing the finish line on my dutch tool chest build (the decision to build it was actually a product of the LAP open wire, so thank you!)
I was thinking of adding a small drawer to the bottom chamber to hold layout and measuring tools. Are there any drawbacks or considerations I should think about before adding a drawer/do you have any other recommendations for how to store things like squares/rulers/etc that wouldn’t necessarily lend themselves to the round holes of the tool rack in the top chamber?
Lots of people who have built a drawer there love it for all the reasons you suggest. No downsides (except you lose a little height in the lower chamber, obviously)
Any new albums or new to you music recommendations from 2023?
If you like the Pixies, the new album by the group Wednesday “Rat Saw God” is one of the best of 2023. Try the song “Chosen to Deserve” for a good sample.
If you are on the Americana side of the fence, Chris Stapleton’s new record, “Higher,” is solid. And I cannot get enough of Lori McKenna’s “1988.”
Those are top of mind right now.
How small of a hole will the go drilla go in? I need to drill a 1/2 in hole deep into oak. My spade bit extension is to big. I bought a ship auger but the lead screw packs with wood and it stops cutting.
5/8″ is the smallest hole I believe. There are other exensions (the Bosch) that have a smaller diameter.
Good afternoon! If you create a rabbet on a tail board to line up your pin board, will this change the overall dimension of your carcass? I’m probably overthinking this, but wouldn’t two 1/16” rabbets shorten a case by 1/8” in total? Imagine I’d have to screw up the depths significantly to throw things out of square, but want to make sure I adjust the size if needed. Thanks again!
It does not change the size of the carcase because you have to reset your baseline for the pin board so it is 1/16″ less.
Glad I asked….I have been setting my baseline before cutting the rabbet. Makes so much sense now. Thanks!!
Hi Chris,
I am looking to build a new desk for my home office, and after a lot of research, I’d really like to do something in line with the staked worktable you have on your website of furniture. How similar is this to the table in the Design Book, and how do you go about adding the single drawer. I don’t suppose you’ve ever released the plans for the worktable have you (sorry if you didn’t and I can’t find….I did have a look).
Thanks again for doing this most weekends. It’s a wonderful service!
Just opened the book and answered my own question. I’m a fool.
I have a new, unused,
LV Veritas shooting plane, with the PMV-11 iron. Are there any suggestions on honing the iron for the first time?
I have 1000,4000,8000, and 16,000 Shapton stones.
Thanks for all if the information you share with the woodworking world.
We hone a secondary bevel (we use 35°). 1K, 4k and 8K. Remove the burr from the flat side.
Hey Chris and Megan have either of you or anyone you’ve talked to used lanolin based products on your cast or steel tools? I know you’ve mentioned jojoba or 3 in 1 on your woobies. I have been using the latter just wondering if there’s any reason not to try it. Thanks!
I haven’t, but I’m sure it will work fine.
I am getting to begin work on a new bench, but my shop is not heated. Aside from the obvious temperature inconvenience, do you have any thoughts/cautions, etc. about roughing the stock and beginning work on it in winter conditions that will likely stretch into springtime (and maybe summer)?
Humidity is more of a concern than temperature (within limits). But if you are making a simple Roubo or the like, then wood movement isn’t a concern with that form. If you are making a fancy German bench with tail vise and lots of sliding bits, wait until it’s more humid to fit things.
Good afternoon. Is there a pdf option for the Anarchist’s Design Book?
It is turned off during the sale. Like my other books, it is transitioning to a free download shortly.
Greetings!
A couple of not important questions concerning beverage containers.
First; I like using mugs for my coffee (like the LAP mug), but suffer from additional wood fiber added to my coffee when I’m working on my bench. Is the LAP mug available with a lid? (like a beer stein…not a wimpy sippy cup)
Secondly; have you ever seen a chair with some sort of a beverage holder?, either a small shelf under the seat or some sort of leathery snap on attachment? (No zippers please!) . Thinking of the guitar player looking for a place to keep their refreshment while they are playing…
I know the collegiate hard hat with twin beverage holders (and straws) would answer both of these concerns, but looking for some sort of more “mature” solutions.
Thanks!
We don’t offer a circle of wood to cover the top of the mug…but make me an offer and I’ll get out my tools. (Or, cut a circle from a scrap).
All kinds of chairs have cup holders; check just about any back issue of PopWood from 1999-2004 or so!