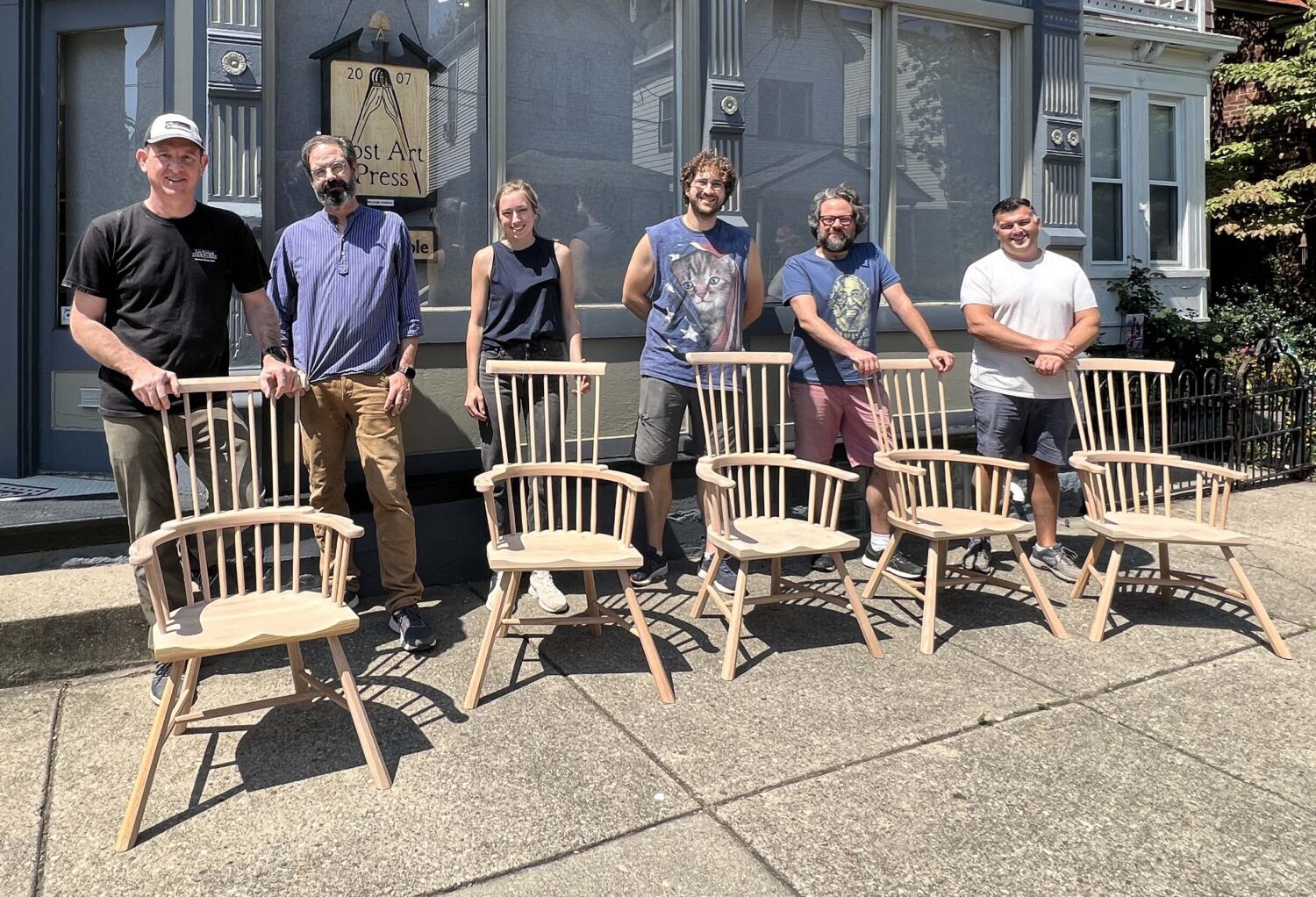
We are here today and happy to answer your questions about woodworking, cats, our books, Shakespeare, linseed oil paint, the Anthe building restoration, or Jayhawks songs. This week’s open wire is hosted by Chris and me. Here’s how it works: Type your question in the comment field, and we will do our best to answer it. And know that concision is much appreciated.
So ask away. Note that comments for this entry will close at about 5 p.m. Eastern.
Note: Comments have been closed for this edition. See you next week.
– Fitz
Most of the stuff I build starts with piece I see somewhere which I then tweak and build, frequently making changes as I go. Still, it is clearly derivative of the original. Recently, someone asked about me making a version of one of my pieces for them. I feel a little strange about the idea. While there are changes that I have made, it is still clearly heavily influenced by someone else’s design. It leaves me uneasy. Suggestions on how do I handle this? I know that, in reality, all work is derivative. Am I obsessing over nothing? Or is it something? Where do I draw the line>
You are obsessing over nothing. As long as you are clear with anyone who asks about where your pieces come from, you are in the clear (in my book).
Some commercial pieces are protected by trade dress, patents or copyrights. They should be clesrly labeled as such. Even so, if you modify it noticeably, you are in the clear.
If any of your pieces involve my designs, everything I make is open source. Sell it, use it, change it, whatever. No worries.
What are your preferred finishes on cherry. I know it is wax 2.0 and your shop finish. Anything else? And what is your preferred finish on white oak?
Cherry looks great with almost any finish. Especially after exposure to UV. Mostly we use soft wax, our shop finish or shellac.
For white oak, we usually color it with some kind of medium brown stain, then soft wax or shellac.
Alternately, shellac and a black wax to fill in the pores and provide contrast. White oak is glorious to finish.
I am a monthly subscriber of LAP and see a monthly request for questions and comments, but where do I go to see any of the community input? Is this a one on one question/reply offer or is there a forum link?
I have yet to find any questions posted or answers provided. What am I missing?
Scroll up?
I see said the blind man! Apparently you have to first ask a question to get enrolled
into the system. After making the above inquiry I received an email confirmation and seemed to be enrolled into the system. I now for the first time am seeing email forum questions and alerts.
Hi Danny,
It’s not a forum. We post a new Open Wire and invite questions in the comments (almost) every Saturday.
Past Open Wires can be found here:
https://blog.lostartpress.com/category/open-wire/
If you have a question, write it in the comments and we’ll answer it.
Ive asked plenty of questions before abd i probably will ask pleanty agin, right now I just want to say thanks.
You are most welcome.
Good morning! Thank you for the smiles, education and tips….enjoyable reading always. And good luck with the new building. My question concerns eastern cedar outdoor furniture. I acquired 3 pieces last year and am trying to find a good finish. Boiled linseed oil was mentioned first but will need repeated treatments every couple of years. Another was Behr penetrating oil, tinted or not and the last one was automotive wax. What are your thoughts?
Take care and be good…….Chuck
Surface waxes (automotive or furniture) will do little to nothing. Linseed oil will penetrate but do little to nothing for sun and daily/seasonal weather protection. You need surface protection.
Hardware store spar varnish (i.e. “long oil” varnish) is relatively inexpensive and results could differ from brand to brand, and probably not as you’d hope for. Research spar varnishes from the marine and boating realm. They will be more expensive but will have superior UV protective additives than the hardware store brands, and more likely to contain phenolic resins as well, which are more durable than the common alkyd and polyurethane resins.
If you are looking for durability: paint or deck stain.
If you want to see the wood, marine varnish (very expensive because of the UV inhibitors).
We just leave ours with no finish. The stuff turns a nice gray.
I’m building an 8′ workbench and have a pair of the Gramercy holdfasts and a few 3/4″ dog hole accessories for it (veritas wonder dog and planing stop b additions to homemade dogs)
I was just gifted a pair of crucible holdfasts and now now I’m pondering over a layout for dog holes that incorporates 3/4″ and 1″ holes.
Any suggestions for layout around a leg and wagon vise?
Thank you for generously offering your time to OpenWire and for the excellent work LAP and Crucible do.
You don’t need both. I’d choose one or the other 3/4″ or 1″. Both work fine.
My preferred layout is here:
https://blog.lostartpress.com/where-to-locate-your-holdfast-holes/
But I add a third row (which matched the back row) near the front of the benchtop.
Hello there! I’m about to finish my workbench build. Any tips on how to hammer in the drawbore pegs. I’m afraid of not getting them trough the legs and stretchers.
Have a great day and a good weekend.
Timber framers rub wax/paraffin on the pegs (no glue). I do this when building a workbench. Works great.
I got a tip from Mark Hicks of Plate 11 to rub beeswax onto drawbore pegs, and have had great success with it.
The friction when the peg is driven home melts the wax and lubricates its passage nicely; when the wax cools and sets again, it gets sticky, whereas paraffin stays slick.
That said, the drawboring effect will hold the peg anyway, so slickness is not an issue as such; I just found it neat to get both lubrication and sticking fast in one product.
Hey Chris and Megan,
1. Any drawbacks to using eastern white pine for stick chair seats?
2. What’s the best way to teach satire comprehension? (Asking for a friend)
Thanks for the LAP open wire!
-John
I’m a big fan of safe and repairable wood finish. I’m in the homestretch of a new dining table build. Is there any repairable finish that would offer enough protection on this surface? I have two kids, age 1 and 6.
I recommend shellac – safe and repairable. There’s a learning curve to apply it. Or some kind of soft wax, easy to apply, safe and repairable.
Tage Frid said that the hardest task when selling furniture is finding the first customer. How did you all at LAP find your first customers?
I sold my first piece – a Morris chair – on eBay in October 1999.
thanks. Of course we now have Etsy as well.
Good morning Megan and Chris,
According to Frank Klaus you should cut pins first when making dovetails. My question is for restoring a drawer with half blind dovetails in the front panel. Assuming the draw side is beyond hope or missing altogether how do you lay out the tails? If you can reference a website or video that would be great to save you writing a thousand words.
Thank you for all you do,
Richard
If you want to cut them a la Klausz, then you do it by eye. No layout.
I cut dovetails tails-first. I lay out my joint using dividers.
Then transfer the shape to the drawer front with a knife.
Do you have Hayward 3 (Joinery) by any chance? If so, check out pg 1071 (it’s pins-first half-blinds – so the repair would be the same approach. Mark the baselines, stand the drawer front on end aligned to the tail board baseline, then get in there with a sharp pointy thing (awl, a la Hayward, marking knife a la me and Chris) to transfer the shape. Edit: I posted this excerpt in April! Scroll down about halfway, and you’ll see a pins-first half-lap:
https://blog.lostartpress.com/2023/04/18/lapped-double-lapped-dovetail-joints/
Richard, Are you saying that you are restoring an old drawer, from which you have a drawer front with 1/2 blind dovetails, but need to make a replacement drawer side and are wanting to know how to lay out the matching dovetails on the new drawer side? If you are, then I am interested in that as well.
The link in my last response should answer your questions. It’s just a pins-first 1/2-blind.
Are there any appreciable differences between your stick chair videos and the wood whisperer guild version (apart from production quality/editing as hinted in the description of it)?
From my reading of it, the LAP stick chair videos are a little more geared towards making everything yourself – and the WWG video is a slightly different chair with home center / premade dowels as sticks – more accessible for a first time chair maker than making octagons then shaving into sticks. Also only tool needed for seat is a travisher in the WWG vs the scorp/travisher etc of the LAP version. I haven’t seen the LAP Gibson chair video (yet) so I’m not sure about that reference.
I’ll probably buy the WWG even though I have the LAP stick chair video. More instruction never hurts until I can afford to come down to KY from Ontario for a class.
They are quite different:
I think that was my conclusion as well. Sounds a little simpler than the LAP stick chair video version. I’ll likely buy the WWG version too, despite owning both Lap chair videos too, as I agree on quantity of information (and supporting both outlets)
Thanks again for doing Open Wire. When putting together the case for a bookcase could you use dominoes to join them?
Absolutely! I’ve done it many times myself.
Any chance you would give up a few sources for the sugar pine you use for the tool chests?
We use Shiels in Cincinnati. It’s a commercial yard, so you have to be a business to purchase there.
https://www.shielslumber.com/
And Steve Wall Lumber, which ships nationwide:
https://walllumber.com/products/fine-softwoods/
Wall carries Eastern White Pine, which is functionally the same.
Thanks – as always – for doing this today!
I just started building a new workbench yesterday. On page 208 of The Anarchist’s Workbench, you provide a recommended layout of dog holes for a 22-inch-deep bench: three rows, with the second row offset the first and third. For a deeper bench – say 36-inches – would you add a fourth row, repeating the position of the offset second row?
Sure!
Hi, I attempted to build a set of stools following your plans/explanation for dummies (— oops beginners) in one of your books (don’t remember which right now). The legs were out of (fairly straight) construction lumber — yeah I know that’s an oxymoron. I thought they turned out fairly well for a first attempt. However the wifey and some grandchildren didn’t think so. They said they were to wobbly/unstable. My wife says the legs stick out to far so I don’t think I got the angles to shallow. Assuming that the angles are mostly correct should’ve I used something other than “plain ‘ole 2x4s” for the legs? I’ll recheck the angles against what you said to be sure they’re somewhat close to correct.
Thanks!
Hi Tim,
Did you build an Irish creepie? Specifically a 3 legged version? I love those weird little guys, and I teach it’s construction to the freshmen in the highschool where I work, so I have seen my fair share of them. The three leggers are great for sitting on, but I have noticed that they can be unstable for standing on if you put your weight on the wrong spot.
The other thing that may be a problem is if your stool, chair, bench, etc is slightly off level, you might not notice much if you are sitting on it. However, due to the magic of geometry, your center of gravity is MUCH higher when standing on it, so a little wobble that is hardly noticeable when sitting becomes very obvious when standing. Try holding the stool up and placing the legs flat on a pane of glass. The glass should be flat enough to show any wobble if it is not quite level enough.
Good morning
I am building a low back stick chair using the templates and the red Stick Chair Book. I have cut out the seat and drilled the mortises. I have made several chairs using the ABD. I followed the instructions but the rake and splay looks 25 and 28 degrees looks extreme right now compared to the 16 and 22 . Am I missing something?
I did use a lot more rake and splay in the Stick Chair Book than in the Design Book. Your eye will likely get used to it and appreciate it (I hope).
Thanks I guess I am a little worried as I did not make a wire model first. I have just trust the process and see where it takes us.
My LAP shop coat has a damaged cuff. Could I get this repaired by the people who made it?
Thanks.
They don’t do repairs, I’m afraid. I would consult a local tailor. If it’s due to a defect in workmanship, we will pay for the repair or replace it.
Not a manufacturers defect. I simply wore it out.
Sounds like a great opportunity for some visible mending.
After reading about your love for pmv11 if you could do it over again would you get Veritas chisels instead of your lie Nielsen set?
Nope. Chisels are – for me – not about how long the tool holds an edge. It’s how comfortable and balanced they are. (Chisels are easy to sharpen.) The LN chisels fit my hands like they were made for them.
What are your “go to” places for small quantities of lumber in the NKY/Cincinnati area? I’m wanting to buy small but ongoing quantities of ash and poplar as I need them vs. a large quantity up-front to avoid storage. I’m working on an interior trim project for my home. Thanks!
Muterspaw in Xenia – or if we truly need only a stick or two, Paxton Lumber.
Are there any plans for Chris to write a book on the history of the stick chairs as well as any books on the Gibson chair? I know there are some stick chair books already out there but I was wondering about a book from Chris’ point of view and history that he’s learned.
Maybe someday down the road. Tim and Betsan Bowen’s book (which we carry) has some good history. As does Richard Bebb’s “Welsh Furniture.” Each culture has books about their tradition (“Trasmak” in Sweden; “Scottish Vernacular Furniture” for Scotland, “Irish Country Furniture” for Ireland).
But distilling all those cultures into one uber history of stick chairs? That is on down the road for me or somebody else.
I actually own those books. They are a good read. If you sell it I pretty much buy it because I know it’s vetted and a good educational read. But I will say, I like your writing better. You give a different perspective, to me, that’s very relatable. A Gibson book from you would be legendary in my mind and a first.
I hope that Mark Jenkinson will have time to write that book some day.
For the cat lovers: I have three cats that get mad when I don’t let them into the garage shop to roll around in shavings. One will stay in for hours and get mad when I make him leave.
For LAP: I laid out an ATC months ago but my shop is small (functionally 10×10) And with a Roman Workbench/sawbench, it crowded the space. I opted for some shelves above my main Workbench. They’re fine, but I don’t love them, and now the bench is crowded. Do you have any space saving recommendations for tool storage?
The Dutch tool chest holds a ton of tools and takes up little space. I have seen people mount it on the wall so it works like a tool cabinet. Wall cabinets are another way to conserve floor space and protect tools. There are lots of ideas in Jim Tolpin’s “The Toolbox Book.”
Thanks for the recommendation!
I second the suggestion of the Dutch tool chest. My shop is also small (a 7′ x 10′ shed) and the DTC, supplemented by some holders on French cleats behind the bench to hold tools I’m using on the project but not right that second, works great.
Hi Megan and Chris,
What food do you cats eat?
Thanks
I’ll have Megan field this one. Lucy is in charge of the cats’ diet. I just pet them and play with them.
Both sets of cats eat Iambs kibble. The LAP cats eat a mix of wet foods (each has a favorite flavor). Wally subsists mostly off treats. Olivia eats only Friskes Shreds chicken wet food…and I’m still trying to find Toby’s fave, but he’s not terribly picky.
Hi. What do you think about a PARF table as an alternative to a 600 pound workbench or a table saw. The thing is big in Europe. I built 2, one for clamping and one for cutting. The trick to making it as solid as a traditional workbench is to clamp a 1 x 6 across the stretchers on the trestles I use to support the top. I find that a track saw is safer than a table saw, the dust collection is better and it is easy to store, great for a small shop. Also the accuracy is phenomenal. You can get tons of great accessories from Benchdogs, Axminster and TSO.
I’m sure it would work fine. Not my bag – I prefer traditional tools, appliances and workbenches.
But as I’ve written before: If it can easily hold boards so you can work on their faces, edges and ends, then it’s a good bench.
Hi. I have a Portable Moravian Workbench too, thank you Will Myers.
Chris; looking for a bit more information on ‘barley twist’. I have info from Australian Woodworker, barley twist, part 8 and The Woodworker, by Hayward. Would you have in mind another book (s)or article (s) that I could read? Thanks
I know exactly nothing about barley twists. Sorry!
Techniques of Spiral Work by Stuart Mortimer – THE book for carving twists!
Thank you
jew
jdw
Roy Underhill on The Woodwrights shop did 2 episodes on barely twist
https://www.pbs.org/video/woodwrights-shop-barley-twist-table-pt1/
Is there a finishing section in any of the Hayward books, did he even write much on finishing?
He wrote an entire book on finishing titled “Staining and Polishing.” It is widely available on the used market.
Chris and Megan,
Thanks as always for your time and wisdom. I’m about to tackle an ATC, and I have struggled (for a while) with getting the lumber. I live in Michigan, and despite having the white pine as our state tree, where I am it is a rare commodity. I do have access to some very nice Linden, however. I had a look at the hardwood dealer yesterday and he has 4/4 and 8/4. What do you think about this? Or put another way, how close to 7/8 do you think you need to be? the wood looked pretty twist-free, so I’m hoping to get the 7/8 out of 4/4, but it’s always possible that you are a bit under, right? With resawing and movement, not sure it would be smart to try 8/4 because if it cupped too much, you’d be under.
Guess it’s a long winded way of asking where the demarcation point is with strength and thickness.
I keep missing out on your stick chair class. When is the next class scheduled and when would it be advertised? Ps; Hope to see you all in Amana.
Megan should be announcing our classes for 2024 soon. And there are chair classes on it. I am teaching a stick chair class at the Florida School of Woodwork next year. Not sure when that schedule will be posted.
Was it a hard decision for you to decide on doing chairs full time and kinda give up on case work? I have the problem of wanting to make everything lol. Take care Chris have a good one
I still do a lot of casework! Everything in The American Peasant so far is casework: coffers, chests, arks, cupboards, wall cabinets. etc.
I LOVE casework. The last five years have been chair-centered (on the blog) because of “The Stick Chair Book.” I’ve been building stick chairs for 20 years and are just now to the point where I am confident I can teach them.
I plan to make chairs and casework for the rest of my days. (And some other stuff that’s coming up)
Do you suggest using a stain on figured maple prior to using your wax finish to emphasize the grain?
It depends on the effect I want. I usually don’t add a lot of additional color. So I would just use soft wax and be done with it.
When making more early American pieces, I used JD Lockwood dyes to make the figure prominent. Then a topcoat such as shellac.
This is just like the old “Car Guys” show on Saturday morning on NPR only with this format one can read it all day – thank you both for doing this. Chris, I loved your last “playlist”, any plans for another one (please)…and one from Megan would be good too. Ear·worms wanted!
My most-played playlist would have a lot of the same stuff as Chris’s Anarchist’s Playlist…but I do have an enduring soft spot for some ’90s stuff that Chris doesn’t particularly like, so perhaps I’ll make an anti-Anarchist’s Playlist
Here’s one I made called “Growing Up Alternative and Gen X.” Music from the 1980s up until Nirvana.
https://open.spotify.com/playlist/5yKUmifZtz1pejtynKeljn?si=3ed50af31a744793
What’s the best way you know of to clean linseed oil paint off of paint brushes? So far I’ve tried soap and water, mineral spirits, and citrus solvent, and nothing seemed to work great. The problem could certainly be that I’m using the right cleaning product in the wrong way. Any advice?
Linseed oil soap!
https://www.leevalley.com/en-us/shop/tools/supplies/finishing/112235-allback-linseed-oil-soap?item=56Z1225&utm_source=free_google_shopping&utm_medium=organic&utm_campaign=shopping_feed&utm_campaign=USA%7CPLA%7CPMax%7CTools%7CMidPriceTier&gclid=Cj0KCQjw0IGnBhDUARIsAMwFDLmho_9T9vSUojBLTaSrSJ45bzsSTLx0Aq_Ier6uCREH8HwQ1odps_waArErEALw_wcB
(But, um, I admit to sometimes buying inexpensive brushes…and not cleaning them)
Not Chris or Megan, but another frequent and enthusiastic user of linseed oil paints.
The answer is linseed oil soap. Works an absolute treat!
It will take five to ten minutes to clean the brush, depending on how heavy your painting session has been, and how much paint you have gotten into the brush, but the linseed oil soap will get it clean: just work it in with your fingers as many times as needed until the suds are no longer discolored by the paint.
You can also hang the brush in raw linseed oil between painting sessions (enough to cover the bristles), and then just wash out most of the oil with linseed oil soap when next you start painting (with the same colour).
Cheers,
Mattias
Just to be clear: if you store the brush in raw linseed oil between sessions, you don’t need to clean it first.
Hi Megan , How is the stick chair looking that you used the Linseed Oil paint on ? Any suggestions for those of us considering doing the same ? thanks
So far, it looks good! I missed a few spots that I’ll touch up shortly – but the paint is laying out nicely. It’ll be a few days until it’s dry enough to sit on though!
Did you do a light coat of boiled linseed oil first, a day or two before the green linseed oil paint? If so, did it have to be dry before the paint?
Hi Chris, any update on the availability of the machined knife holder and the pear shaped cutters for American Peasant work? I think you said “end of August”?
-Frank
I think closer to mid-September now.
There will be a full update tomorrow on The American Peasant. The knives are being machined now and should be done by Sept. 8. The cutters are here and packed. The instructions are written. The kit: knife handle (which can be installed in a compass or used freehand) plus two cutters plus instructions: $27.
Hi – I mixed up a batch of soft wax. Easy to make and great to work with. When I came back to it a few weeks later, the concoction looks almost like it has separated. Kind of like tiny beads of wax, and a firmer consistency. Any thoughts? Sorry, I’d post a picture if I could. Thanks!
Popping in to say thank you for insisting on quality construction in all you make at LAP and Crucible. In the middle of my first stick chair. (six stick comb back from the book in white oak) Many other books would have fallen apart by now what with fan blown shavings in every chapter and pencils-as-bookmarks and me slamming it shut and tossing it aside having found my answer. I’m extremely lucky to have come across the company and blog some years ago.
Additionally, in lieu of much scraping and sanding I may say I invented a new finishing technique and leave all the mottled grey spots where my sweat drops and moist hand grips have landed on the oak. Clear coat and call it distressed and depressed lazy leopard. It’s been a hot summer in Phoenix. 🙂
Thanks guys.
Morning everyone. I’ve noticed in the more recent stick chairs on the blog that the thickness of the arms and doubler seems a little thinner. In the parts list in the book they are listed as 7/8. Would 3/4 for the arms and 1/2 for the doubler be a good idea?
Some of that is an illusion – I have been shaping the arms a lot more lately. For the arms, 7/8″ is about as thin as I will go. The shoe/doubler can be as thin as 5/8″. A thin shoe is easier to glue to the arms. Rather, it is easier to clamp out any gaps….
Would the Allback boiled linseed oil be an appropriate pre-coat for their linseed oil paint? I know you’ve said raw linseed oil in the past, the Lee Valley near me only stocks the boiled stuff.
I’d use the boiled stuff as the precoat. Or skip the precoat altogether. We’ve been thinning the linseed oil about 10 percent with low odor mineral spirits and it does just fine without a precoat.
Hello Chris & Megan.
If working with woods that do not possess the strength of oak you have recommended adding 1/8” to sticks and arms. What about the tenons and holes? Can they remain 5/8” or should they go up to 3/4”.
Thank You again for doing this each week and be well.
I would go to 3/4″ – just to be safe.
Megan, Chris,
Have you ever made furniture for your cats? Like cat trees or houses? (Toolchest? shaker tray? That chair you were about to sit in?)
If so, what is your favorite piece? (More importantly, what’s theirs?)
I seem to recall a picture of an anarchist tool chest with a hole in the side and a litter box instead of tools. Megan, was that you?
https://blog.lostartpress.com/2014/09/05/the-anarchists-litter-box/
Nope. I am fond of the Rubbermaid-container-as-litter-box approach. Cheap, easy, and everything is well contained.
Do you have any opinions about sizing panel saws? I see both rip and crosscut saws ranging from 22 all the way to 28 inches in length or more, and am unsure when or if I’d reach for one length vs another. I’m only 5’6”, and so instinctively thought that a smaller saw would be more ergonomic, but I don’t know if I’m missing something.
Any chance of a “Backyard/Garden Workshop” book i.e. a shed build, for a workshop. See “Building the Timber Frame House: The Revival of a Forgotten Craft” by Tedd Benson for his drawings. See “Learn to Timber Frame: Craftsmanship, Simplicity, Timeless Beauty” by Will Beemer for the photography. Sheds kept to 100sq ft typically don’t need building permission.
Timber framing is a bit out of our league. We try not to stray too far from furniture because we could make a stupid mistake.
I’d like to build a lowback to replace my desk chair, but my concern is that my current desk chair sits a bit higher than normal at 21″ from the top of the seat to the floor and that’s most ergonomic for my setup. The plans I’d follow from the Stick Chair Book are around 17″ from the floor. My question is, can I lengthen the legs without modifying anything else? Or should I make a commensurate adjustment to the height of the stretchers for either stability or anesthetics?
More broadly, do you think the lowback is a good choice for a desk chair, or do you recommend something else?
Thank you as always for taking this time!
The chair will be fine at 21″. Lower the stretchers a couple inches for good measure perhaps? The lowback is great for keyboarding and dining. Very comfortable for long stretches.
I’ve recently had a spark of interest in nailed furniture after watching some of rex krueger’s videos. Do you have any reading recommendations to learn more about the history and styles of furniture that use primarily nails. Thanks as always for hosting these.
The Anarchist’s Design Book is (about 50 percent ) about nailed furniture and nail technology.
There is no “big book of nailed furniture” book, I’m afraid. Your best bet is to look for books (or on furniture auction sites) on “country furniture” or vernacular furniture. These pieces were commonly nailed. There is a TON of this stuff out there once you start opening your eyes to it.
https://r.search.yahoo.com/_ylt=AwriiwQY7eBkDSIbk8cg7YlQ;_ylu=Y29sbwNiZjEEcG9zAzEEdnRpZAMEc2VjA3Ny/RV=2/RE=1692491161/RO=10/RU=https%3a%2f%2fwww.pbs.org%2fvideo%2fwoodwrights-shop-barley-twist-table-pt1%2f/RK=2/RS=vDMA3HjGR9c.lDgz3GFka4ngXDQ-
Roy under hill did an episode , 2 actualy
Sorry, This was actually a reply for the question about barley twist not sure why it showed up in wrong place and link does not seem right. Old eyes and small phone.
Regarding chair legs. You taper to 1” then taper the last 6”s to the final 5/8” before rounding. Why not just taper the leg to 5/8” all the way…aesthetics?
Thanks
That would remove a lot of wood, which will reduce the strength of the leg. Also, I want the base of my tenon to be 1-1/16″, which is what I need for a tapered tenon. Tapering all the way to 5/8″ doesn’t give me that.
Hi Chris/Megan,
I purchased a nice European style vintage woodie hand plane off HyperKitten, my favorite place for used vintage tools. What size/weight “hammer” should I use to set/adjust the iron? Should the head be brass so I don’t mushroom the top of the iron? Many thanks and have a great day.
Sincerely,
Joe
I use a metal hammer to move the iron and set the wedge. Other people use a wooden mallet to do both. Still other use a metal hammer for the iron and a wooden mallet for the wedge. STILL OTHERS use a special plane hammer that has two striking faces (one for the iron and one for the wedge).
There is no right answer here. It’s up to you and how precious you are with your tools.
Honestly I wonder how hard people hit those irons! I use whatever I have closest at the moment, but when striking metal all it ever needs is the lightest of taps.
Any word on when Megan’s Dutch Tool chest book might be coming out? (I have the wood, I’m holding off the build till I see whats in her book).
We hope by the end of the year.
Hi Chris and Megan,
When Chris built the “Two-bo” and laminated the two countertops together, did he have to plane the two sides that were glued together or was “factory flat” good enough? I’m thinking of building another bench. I thought this was a good idea to save time and wondered if I needed to do the extra step. I’ve never laminated something this big.
Also, if they are flat enough, do i need go crazy with screws in the center area or just concentrate on the perimeter with a few in the center.
Thanks for your help and time.
I didn’t have to plane the mating surfaces, but I did have to scrape off the finish so the glue would stick.
You don’t know what’s happening in the middle of the lamination, so I would use screws in the middle as well. You can alwaysd remove the screws after the glue has dried.
Thanks for taking questions, really appreciate it.
My question, in your experience what is a good approach/method to figuring out how much additional wood to purchase in case of mistakes, when starting a project? Being a weekend warrior type furniture maker, I really don’t have much hope of getting back to the original stack of boards I pulled from, when a mistake occurs many weekends later.
-Nate
It depends on the type of project, but 25 to 50 percent overage is typical. Casework is like 25 percent over for me because there are lots of parts that don’t show where you can use imperfect wood. For a chair, I get 50 percent extra because the parts have to be perfect for strength and appearance.
How long does it take to make that type of chair and what skill level is required?
The classes are five days. You need basic competence with hand tools and sharpening. Plus, and this is important, the ability to stand and work at a bench for the week.
Hi Chris and Megan,
I’m installing butt hinges Horton Brasses PB-409 on the ATC and does the big leave go on the chest or the lid?
Thanks Don S
I’m not sure it matters, but both Chris and I have the big leaf on our lids.
Great stuff; I enjoy most of the commentary – thank you. Question – I tried gluing a piece of hard leather to one face of my lump hammer to reduce the risk of marring the work. I used hide glue, but it doesn’t hold well in the long term. Any suggestions for an adhesive? I’ve considered doing the same for my holdfasts and F-clamps, but waiting for the right adhesive. Thanks again.
Try epoxy instead. It is ideally suited for those materials.
(Just another woodworker…). I’ve used double sided tape to solve this…not so “permanent” yet is flexible enough to last longer than a few strikes…there are many grades of 2 sided tape. If you want to get fancy; stick a magnetic sheet to the leather…then use the magnet onto the hammer…
Fish glue is pretty good for gluing to metal. Won’t hold as long as epoxy (probably), but a good choice nonetheless.
Hi! If you’ve used it, is the James Mursell deluxe travisher worth the price difference? The delrin body seems like a drawback (because not wood) but with the brass insert it would be clearly more durable. But is durability even an issue with the wood one (and the number of chairs a strapped-for-time anarchist is likely to make)? Thanks!
I have both and we use both extensively here in classes. They are both fantastic tools.
If I were building chairs for my home – not professionally – I’d buy the standard one. The weight of the deluxe delrin version makes the tool easier to use – it keeps the tool in the cut. The brass is also an advantage when it comes to wear.
But they function the same. Small differences that are more important to someone who does it every week.
Thanks so much!
I am planning to follow the recipe for the linseed oil finish in the stick chair book.
The only quart sized metal can I could find at the home center has a lining on the inside. I don’t know what that stuff is.
Should I avoid things like that and try to find a bare metal container?
We’ve used that very one, with no ill effects (to either us or the oil/wax).
Thanks Fitz.
You might see a duplicate question/post… I apologize for that. I didn’t think my first one went through.
I am following the recipe for the lin seed oil and wax finish in the stick chair book.
However the metal container that I have found has a film coating on the inside of it.
Should I avoid that and continue searching for a bare metal container?
Love what you guys do. Thoughts or experiences with KY Coffee Tree? A recent experiment in riving has left me with a bunch of riven chair-stick-length Coffee- looks and splits a bit like red oak (and doesn’t smell as bad as reported).
I haven’t used coffee tree wood before (it’s a street tree here in Covington). But I know lots of furniture makers who have. Try the sledgehammer test on some sticks and you’ll get an answer. My assumption is that it will work fine.
Is there any article (or public-facing project) you regret? Like opening a door that should have remained closed?
Not really. I was excoriated for my article on Death Row woodworking at Popular Woodworking. We’ve had many projects that barely broke even, but they were worthy things to work on.
If there was one project I wish I could undo it would be “The Book of Plates.” We did it in response to intense reader pressure. The pressure turned out to be intense but shallow. We ended up with so many leftover books. They were huge. Difficult to store. Eventually we sold the lot at a huge discount. We broke even. But I wish I could have all those hours of moving books back.
But even that project had upsides. I am now much less suseptible to customer pressure. And I do far more research now before getting behind a new title.
Do you know if Rivierre nails might return? Any substitute suggestions?
We don’t know. The last I heard is:
We are buying Tremont nails for classes, which are a great substitute (though they look different).
https://tremontnail.com/
They are available on Lee Valley and Dictum. Probably elsewhere. Anything in particular you’re looking for and not finding?
They have been out of several key sizes for months. Most are listed as “no longer available” – at least on the US site.