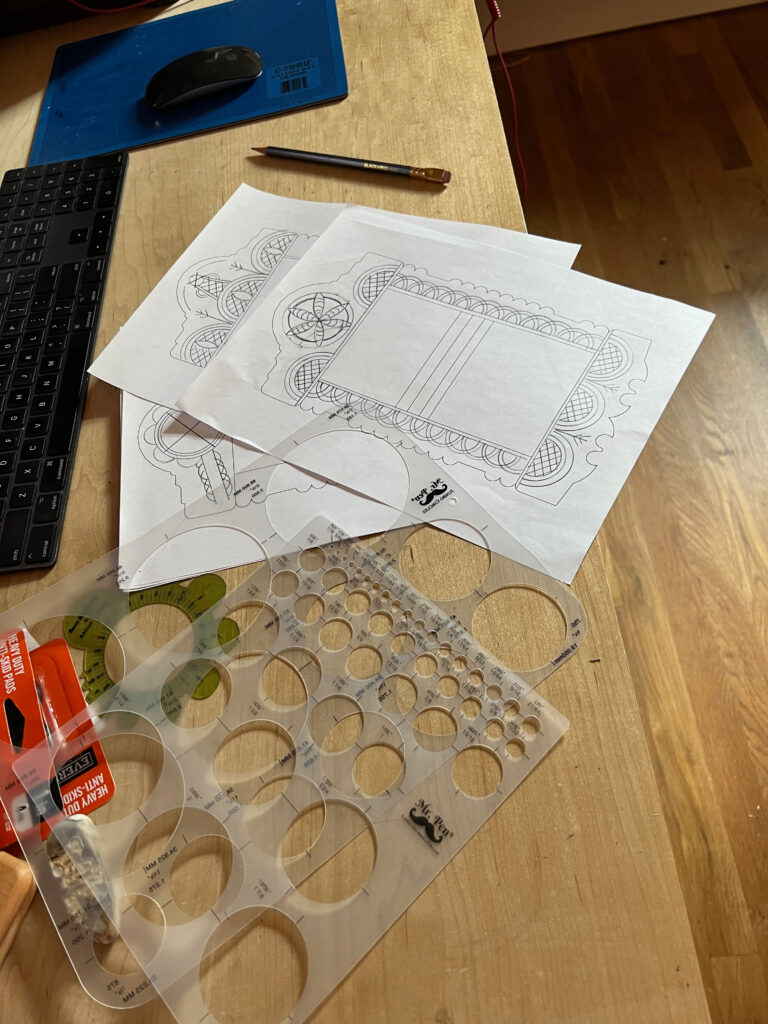
You are stuck with me again for the LAP Open Wire this week. (We have a special guest lined up for next week, however.)
So let’s hear your woodworking questions.
Here’s how it works: Type your question in the comment field. I will post my answer. It is that simple.
Before you ask a question, please read this.
- If you could limit the number of questions you ask to one or two, that would be appreciated.
- If your question is your first comment here, it will automatically be flagged for moderation. Your question will appear after I approve it.
Comments have been closed. See you next week!
— Christopher Schwarz
Hi Chris, i have a tool question if you dont mind. What do you recommend the LN 48 or the 49? My first project will be the shelf for a Roubobu im looking for versatility.
Depends on the scale of projects you are interested in. Casework, the No. 48. Small boxes and delicate cabinets and chests, the No. 49. I have both and use both equally.
I feel like there could be a second volume to Euclid’s Door. Perhaps Euclid’s Courtyard… What would the next additions be to your list of projects in addition to those in Euclid’s Door (I hesitate to use shorthand as the abbreviation is most unfortunate)?
You’d have to ask George or Jim, who hosted last week…..
Thank you!
Good morning Chris. I’ll get you started with an easy one this morning.
I have an opportunity to get a few black walnut logs. I have been interested in making a chair from a green log. Would the Stick chair be a good choice or would another design lend itself to working with green wood. If the Stick chair works, what adjustments should I make as opposed to working with kiln dried wood.
Have a great day
Stick chairs were made with Whatever Wood is Available™. I would rive it out into chunks that are slightly oversized. Keep them in a garbage bag that you open every day or so (to let excess moisture out). After a couple months, you should be able to take them out of the bag to air-dry. Monitor them until they stop losing weight. Then you can use them as per normal.
Another option: have someone kiln-dry it for you. We have a couple kilns that take small batches.
I’d suggest air drying at least some of it. Kiln dried walnut is, of course, gorgeous but the colors you get with air dried walnut have to be seen to be believed.
I’ve been thinking a lot about finishing lately, and share your opinions about nonviolent / non threatening finishes. Are there any U.S. based finishing courses you would recommend? Thinking the most about shellac / french polishing.
(If it helps, I’m based in Arkansas.)
The Marc Adams School of Woodworking is always a great place to look for a class. They have everything.
Honestly, however, you can start with Derek Jones’ book “French Polishing” and you might not need a class.
Classes I looked at for 2023:
PA – Acanthus Workshop – June 26 (Chuck Bender)
VA – Wood and Shop – July (Don Williams)
ME – CFC – October
Don Williams is obsessed with French polishing and shellac. He has a couple of upcoming courses on it and will also be peddling some of his wares at handworks. He’d be a great resource to reach out to.
Have you ever considered creating a trade sign for your shop(s)? I saw a very large plane in the trade sign exhibit at Shelborne Museum and was wow-ed by it. Couldn’t post a photo here. What would your trade sign look like if you were to build one?
I hired a guy to weld up some dividers about 36″ tall. He got about halfway through the project and then disappeared. I’ve always liked the trade signs that have no words. At the Sign of the Dividers (Pig, Chair, Dingle-butkus).
Something like the misericord photo on https://blog.lostartpress.com/2020/11/14/and-the-choir-sings-workbenches/ would be dandy.
Good morning Chris, i have one question about wedging, when i have to saw the kerf in the tenon for wedging, do i absolutely have to follow the grain of the wood ? Or can i cut in every direction i want ? Thank you and have a nice day.
There are people who have sharp opinions about whether the kerf should be parallel to or perpendicular to the annular rings. I am not one of those people. Vernacular chairmakers did it all different ways and all the joints have survived. So I don’t pay it any mind. Mostly, I am concerned about what face of the leg/stick/stretcher faces the viewer. And I base my kerf off that.
Hi Chris, as always, thanks for this! I just got my first bottle of Old Brown Glue but have not yet tried it. My only other experience with hide glue was a bottle of Titebond. I found that straight from the bottle it was a bit thick to use, and when I heated it in hot tap water it had the consistency of water and ran all over the place. What viscosity should I expect and strive for?
When heated, Old Brown is the same viscosity as yellow glue. I’ve never had it go watery…. Titebond has chemicals that allow it to be used at room temperature and does not need to be heated.
I have used your “shop finish” and have been happy with its appearance, especially on walnut.
In your post providing the recipe (https://blog.lostartpress.com/2020/01/23/our-shop-finish-recipe/) you state you would use something more substantial for table tops.
Do you have a suggestion for what you may use on a desktop?
Thanks for your time!
Omit the oil and make a wiping varnish: Equal parts varnish and odorless mineral spirits. Wipe on thin coats until it looks like you want it to (and sand lightly between coats to remove dust nibs and provide a smooth surface for the next coat).
The odorless mineral spirits that you use, it’s probably not that white, milky stuff? Also, could the wiping varnish be applied if I’ve already applied the shop finish? I would like to get a little more protection on a seating bench that I finished previously with the oil/varnish blend. Thanks!
Odorless mineral spirits is not milky. It’s clear. You can apply the wiping varnish over the oil/varnish blend with no problem.
This stuff is milky: Klean-Strip Green Odorless Mineral Spirits.
Whatever they do to make it green makes it milky and act differently.
I don’t use the green stuff. It’s fairly awful.
Chris: thanks for doing this. Have been using your/Flexner’s shop finish on several projects – a great gateway finish. Is it OK to add color to the mix, either by adding stain or dye, or is it best to keep those processes separate? (I realize the color won’t be as saturated due to dilution, but thinking of a way to add some tone to plywood casework (currently building a built in closet system).
You can tone the finish no problem. The first coat should have no color, however. And make sample boards first….. please!
Morning Chris, do you have any experience with how a stick chair holds up outdoors, mostly uncovered? I was thinking to angle the seat such that water doesn’t pool and possibly consider a finish that gets refreshed each season. Any other ideas for a long lived, outdoor stick chair?
I’ve never made one for outdoors. If I did, I’d use white oak and paint it. Or raw linseed oil.
Still, outdoor furniture never lasts forever.
Locust, mulberry (heartwood) Or cypress would be good options for wood as well.
Accoya for outside wood
Will the carver’s vise work for holding sticks for tenoning or do you just shave sticks on it and use the benchcrafted vise for tenoning sticks?
Also thank Megan for our tour and visit last week, my family and I really enjoyed looking around.
Yup. I use the carver’s vise for tenoning. And shaping. It holds like crazy!
Glad you enjoyed the tour!
Two vise questions?
Any chance you have a link to the previous post where you recommended the carver’s vise a few months back? I searched but couldn’t find it; maybe because it was mentioning a sale price and has since been deleted?
The face vise on my English joiner’s bench starting closing with a slight gap on one side, so I simply tapered it to account for that (instead of making a new face or guide bar). Is that the right approach?
Thanks for doing this.
That post to the carver’s vise was to a sale at Inifinity Tools, which ended. The Grizzly sale price right now is the cheapest I have ever seen it. Buy now or….
And it’s no problem to adjust the jaw to match the bench. Good work.
Would like to see you write an article about shadows. Why crisp lines have sharper shadows. How deep to cut your spells into the wood for example.
Would also like to suggest guest hosts of Brendan Gaffney or Roy Underhill.
The spells are about 1/16” deep.
We invited all LAP authors to participate. We did not hear from Brendan or Roy. They are likely busy….
(If I may)
I read an interesting bit way back when on this topic. I can’t really remember where.
There are a bunch of factors that go into shadows. During the day, there’s an overabundance of light that reflects off of everything. Sharp shadow lines seem to come more from sharper point sources, later in the evening, or from a particularly bright source, at a particular angle.
The article in question brought up the point that a lot of the old sea-cost fancy stuff, with carved shells and whatnot, were designed to be more impressive by candle light. They typically have sliding shelves to hold candle sticks and so on… but the shells and other decorations would have much more dramatic shadow lines due to those candles.
The light isn’t so bright that much gets reflected off of walls, as you get from the bright lights we use today. So, the shadows on those shells were darker, and deeper, and moved more when the candles guttered.
I’d be curious to get Naryan’s perspective: this is definitely the sort of thing a photographer deals with on a regular basis.
Good morning Chris,
Thanks for taking the time to do this again. Your dedication to spreading knowledge is amazing!
I have made 2 staked stools following the ADB staked stool instructions (mostly). These get generally use at work as an extra place to sit at my desk. Unfortunately, both of them had the legs fall out after about a year. One had stretchers the other did not, both had the tapered tenons wedged through the seat. Any idea on how to stop the legs falling out? I have not had this issue with the other staked things I have built.
Hard to say. Did the glue fail? The wood? Did the legs shrink out? That will give you your answer. Legs need to be as dry as possible.
Doesn’t seem like the wood for the legs failed. The tenons still seem to fight tightly, but is there a good way to tell the difference between glue failure and shrunken joints? I don’t mean to be obtuse, just trying to wrap my head around the specifics of staked furniture. I have only built a few pieces so far.
Still, it’s hard to say without seeing the joints. But I am guessing that it’s glue failure. Perhaps due to moisture or bad glue.
Hi Chris, thanks for taking the time to respond to questions and for all of your work on vernacular furniture. I recently read an article you wrote about Moravian stools and had a couple of questions to ask before building one myself. Why do the legs on the Moravian stool pierce both the battens and the top as opposed to just the batten like you have in your staked work desk design in the Anarchist’s Design Book? Your explanation in the book about facilitating wood movement made sense to me and I thought it would apply to any staked piece with battens. Also, is there any structural reason for cutting the notched sliding dovetail battens as opposed to one with just a regular trapezoid cross section? Thanks again. Cheers.
Historically the tenons would go through the seat most times. The pieces survive fine, even if the seat cracks a little.
For the work table, that was a new piece. Not historical. So I was free to do as pleased design wise. Also, in larger work tables of old, the tenons are blind.
I suspect the notched ones are a bit stronger, though I have no proof.
These are great. Thanks again for answering questions! I’m cutting some dovetails in pine and am struggling with the endgrain crumbling/tearing when chopping out waste. I am using a coping saw to cut out most of the waste, but then chop to the line. Even with a sharp chisel, it still crumbles a fair amount. Any tips? I saw the post “Does This Happen When You Chop Dovetails?” with content from Charles Hayward, but that approach doesn’t seem to apply to those of us who cope/saw out waste. Much appreciated.
I don’t care if it crumbles. That’s what pine does. If you are concerned, saw and then pare the waste, which takes longer.
Hi Chris. If you were building a Roubo workbench today which vises would you add? Benchcrafted criss-cross? Simple homemade one? No tail vise, correct?
I would build the Anarchist’s workbench again. Benchcrafted leg vise. Cris Cross. No tail vise.
Every chairmaker seems to have differences in parts of the process, and often in tools. Can you say something about what Chris Williams is currently doing that differs from what you’ve been writing about your work, and your videos?
We are very different. He saddles with an adze. I use a scorp. He doesn’t use sightlines. He shapes his tenons by hand. The differences would fill a book. In fact, they do.
Can I make a Gibson chair with pine?
For the seat, arms and backrest, yes. You need something stiffer for the sticks and legs. Yellow pine, Douglas fir, oak – something along those lines.
What about hard maple for the legs, sticks and comb? Using poplar for the seat.
Absolutely yes.
Currently working through my first Gibson – on the arms I have added 1/4 laminations to support the back area where the post passes through. After drilling I’m surprised as how precariously close those mortises are ended up to the edge – and noticed the same thing on your examples in the video.
I’d be curious to hear your thoughts about changing the mortise location or shape of the arms to give it more meat surrounding the post.
Did historic examples also pass through this closely?
The posts did come that close to the edge at times. You can move the mortise, but not much. Once the chair is assembled, it will be quite strong.
I will be making the long drive from Pittsburgh, Pa, for my first ever Handworks this coming September. Looking forward to meeting the folks from LAP and other vendors during those two days. What has the crowd size been for this event? I’m curious to see the interest in hand tool work as opposed to power tools and jigs. My last several (company paid) experiences at an event like this was the Photoshop World seminars in Las Vegas and Orlando. Thousands of people and long lines. Not to mention no craft breweries nearby.
Expect 5,000 hand tool nerds. It will be epic.
How soon do you apply linseed oil paint over the primer coat of the linseed oil?
A couple of hours? A day or two?
Thanks
An hour or so.
Jumping on to ask because painting furniture scares me still: for the “base coat” of linseed oil I’m assuming rag on, and rag off immediately then wait an hour or so to paint?
Wipe on a thin coat. Wipe away until it is dry.
Good morning, and thanks for doing these. I’m just starting to get comfortable with making poorly executed shop projects, but I’m interested to learn more about different design styles to try. Where do you go to find new pieces to learn from? I’m in the Midwest, in Central Indiana, and I wouldn’t mind a weekend trip to see work in person, and I also do plenty of searching online.
I go to antique stores, museums and libraries (check out the books on furniture).
Consider a trip to Milwaukee to the art museum to see the Chipstone collection.
https://chipstone.org/module.php/64/326/American-Collections:-Furniture-Gallery
Visit South Union Shaker Village in Western Kentucky.
https://www.southunionshakervillage.com/
Once you find a style or two that speaks to you, dive deep. Books, auction sites, museum collections.
Thank you so much! I’ll do all of the above.
Love your American Trestle Table (dining table)!
My wife wants to make the table wider with hopes of seating eight – do you see any design issues with going with a 40″ wide tabletop (so 80″x40″), as long as the braces & feet are proportionally longer (i.e. will the table be tippy side-to-side)?
Any helpful hints to flattening such a large tabletop with hand planes?
Seems like the prototype (your dining room table) has breadboard ends, while pictures from the article detailing the build does not. I’m thinking no breadboard ends to keep the look more contemporary (unless you suggest otherwise).
Anything else you would change with this table (outside of your blog post, ‘A Thousand Meals; Five Lessons’)?
Thanks so much!
No issue in making it wider. As to flattening a top with handplanes, use the smallest smoother you have (I use a No. 3, though a No. 2 would be even better). I don’t have any other suggestions or changes. You don’t need breadboards unless you like the look.
I’ve built two. One for a gift and one for my family.
It’s a really fun project and looks great.
Hi Chris, just wanted to say I’m finishing up a Gibson chair I built using your great videos and drawings. Based off your arm lamination idea, I decided to use two 1/2 inch pieces glued together for the arms with grain crossing as much as possible. The chair will be painted. Also, after struggling with a crappy spade bit, I ended up drilling all the mortises with a Wood Owl tri-cut bit with the screw tip. I imagine you’ve used those, but I have to say it worked great. Very clean holes and other than my first arm, I backed all the holes to prevent blow out. Worked like a champ. Thanks for your great work. I’m a stick chair junkie now.
I’m new to grinding chisels/plane irons and had some variation in results between my chisels and bevel up plane irons. I used my chisel to dial in my tool rest for a 25deg grind but got a slightly smaller bevel on my low angle Jack (maybe 20?) and a more obvious hollow grind.
Could that be attributed to my technique (or lack there of) or the difference in thickness of the iron and the chisel, since the wheel won’t touch the midpoint on both with the same tool rest setting?
Quick follow up: Do you change/reset your tool rest depending on what you’re grinding to 25deg? Or do you just set it and forget it and small changes in that angle are inconsequential?
Sharpen This was one of the most informative books I read in 2022 and really cleared up a lot of confusion (and gave me the confidence to get a grinder in the first place). Thanks for writing and publishing it!
Hi Jon,
The different may be that the plane iron and chisel are different thicknesses. You need to adjust the tool rest to hit the middle of the bevel (ideally). Though as long as the primary bevel is lower than the secondary, you are in good shape.
Good morning!!! Do you have any new books being released in the next six months? Have you considered a book on the historical usage of hidden or secret compartments in furniture? Thank you.
In about two weeks, “Karvsnitt” by Jogge Sunqvist will come out. We are designing Derek Jones’ book on Cricket tables. I am writing “The American Peasant.” And Megan is finishing a book on Dutch tool chests.
I have zero interest in secret compartments (I don’t know why). But if someone wrote a book on them I know it would sell well.
Hi Chris, thanks again for this forum. I recently got an Osborne #38-C compass to start playing with Spells until you publish the book. To say it is dull in an understatement – basically no real edge. I know you put in a blog post on sharpening it but I don’t think you mentioned if you needed to go to the grinder first? My concern is if I grind first, because of the tight curve of the geometry of the blade, and the akwardness of grinding the tool attached to the wing I may wind up rendering it unusable. Did you just go at it with course sandpaper to do the initial grind or did you take it to the grinder? Thanks – Frank
Try #200-grit sandpaper stuck to a piece of wood to shape the bevel. Then polish it up with higher grits. Mine needed that sort of work as well.
Someone asked about rules for drawing the musical clefs last week and I gave a hurried type-on-phone answer around 4:45. The useful URL’s on a real computer are: Treble: https://ultimatemusictheory.com/draw-a-treble-clef/ , Bass: https://ultimatemusictheory.com/draw-a-bass-clef/ , and C: https://ultimatemusictheory.com/draw-c-clef-signs/
Notice in all cases these are properly not random squiggles, certain parts must touch or bracket certain lines. For base or treble you really don’t have to be perfect since given which one you just read along, but given C clef moves a lack of precision could be a problem.
Chris- Have you ever given thought to making a complete index to the Charles Hayward 4-5 volume set? I gotta say I would buy it in a second. It’s the single best source of woodworking information out there and the hardest to find what you are searching for. I’ve searched in vain for articles on technique that I’ve read earlier but now can’t locate. Maybe a pdf only version? or whatever will not bleed you money. Somebody please back me on this.
I have the same problem. The practical information contained in vol I-IV is incredible, but I always feel like I’ve spent way too much time looking by the time I locate the article I want.
It’s probably a good idea. But a big project for us right now. It’s something I hope that AI would be able to handle for us someday soon.
When using my smoothing plane, it tends to leave an uneven sheen. It will feel flat and smooth, however, there are lines of what looks like burnished wood along the path I planed. Any ideas on how I could prevent this? My best guess is that the surface isn’t completely flat because of the slightly cambered iron, and the sole of the plane is burnishing the high spots.
Could be that. Could be high spots on the plane sole that are burnishing the wood. If you keep planing, do they disappear? If so, then your guess is correct. If they don’t go away, try flattening the sole of the tools and looking for any bumps on the corners of the sole.
Hi Chris –
Thank you (and Megan and your authors) so much for taking time to do this.
My question is about handplanes, specifically my LN #4 and #7. After sharpening, as I tighten the screw that attaches the chip breaker to the plane iron, the chip breaker usually moves out of the desired position relative to the sharpened edge of the iron; the movement is parallel to the length of the iron and away from the sharpened edge.
Is this typical, and is there a way to prevent the chip breaker from moving when tightening the screw?
Thanks.
It is typical and is the result of the iron or breaker bending a tad. You get used to compensating for it in time. I don’t even think about it much now.
Hi, the other day I downloaded the video about the interiors of the ATC, is there or will it be one about the chest itself, the exterior?
Thanks
I did one on the smaller version of the same recently for The Wood Whisperer Guild. So it already exists! (The only difference is the size of the parts).
https://thewoodwhispererguild.com/product/traveling-anarchists-tool-chest/
This is not so much a question as a recommendation for the book lovers here, which I assume is most of you.
I’m live San Francisco and I’m planning making the haul to Iowa for Handworks. I’m going to start the trip a few hours away in Madison, staying with my in-laws, who built the first LEED platinum house in Wisconsin and are lovely, smart people. I’m gonna borrow one of their cars and drive to Amana, which can be done in a little over three hours, but I’m gonna take it slow and use most of Thursday for the “there” portion and most of a Sunday for the “back again” stretch, keeping my eyes peeled along the way for sightseeing opportunities and a few good fly fishing spots. But—here comes the recommendation I promised!—the one thing that’s definitely on my agenda for one leg of the trip: a return visit to Driftless Books & Music in Viroqua, Wisconsin.
https://driftlessbooks.com/
Holy crap, what a place! This is the largest, most sprawling, best organized but least pretension collection of used books I’ve ever seen in my life. The owner (great, kooky guy) started accumulating used books and ended up taking over this giant old brick building that started its life as a tobacco drying warehouse. The bookcases are like a maze, and they’ve gotta be ten feet tall, but you never feel lost because you always feel like you’re exploring. And there’s great art and furniture all over the place. And a really active live music calendar. It’s like the Anthe Building on psychedelic steroids, except they don’t make books, they sell them. (And they don’t have heating, so they let everything, books and all, freeze over the winter!)
So if you’re going to Handworks and you’ve got a gap in your schedule, or if you’re driving through Wisconsin on your way to the event, or if you’re ever in the southwestern Wisconsin in the future, get yourself to Driftless Books, and give yourself some time to take it all in while you’re there. (Also, Viroqua is an interesting town that’s got a few legitimately excellent restaurants and some cool stores, including a good fly shop.)
After all that, I guess maybe I should ask a question. I don’t think I’m gonna know a single person in Amana; anyone wanna get something to eat?
I don’t use hide glue (vegan) but envy the repairability aspect. Aside from that, would you recommend PVA for stick chair joints? Would epoxy be as good or better (gap-filling, longer dry time, etc.) of an option? Thanks!
Epoxy is nasty stuff, and I use it only when backed into a corner. PVA is probably the best choice for people wanting to avoid animal products. Less nasty than epoxy.
Chris, can I ask you (and anyone else reading this!) for two product recommendations?
The first is a small one: I notice in the Gibson videos you wear a pair of wrap-around earplugs. Do they work well? I’d love something to always have with me as opposed to my bulky headphone-style model.
Second, a bigger one: I’m looking to add a bandsaw to my workshop. For context, chairs and similar items are about as large/complex as my work gets. Any specific maker / model recommendations, or guidance on minimum size/power to consider?
Thanks!
The earplugs I use are fine. Just home center ones. They don’t deaden the roar as much as muffs. But they are always around my neck. I don’t have a favorite brand. They are all uncomfortable. Some people get custom ones made for their ears with sound deadening technology. I’m not that fancy.
My favorite new band saw is the JET 14″ metal/wood cutting band saw. That’s the gray one we use in our shop.
https://www.northerntool.com/products/jet-vertical-wood-and-metal-cutting-band-saw-14in-1-hp-115v-model-j-8201k-426404
If you prefer vintage, get a USA-made Delta 14″ band saw. I don’t like any of the sheet metal band saws, I’m afraid. Only cast iron for me.
Thank you!
Hi Chris, one more today while you are on about the Osborne 38-C. There are two adjustment knobs on it. One to set the radius. The other, on the fixed arm appears to be some sort of fine tuning? I checked on-line and on the Osborne site but could not find any reference to it. Do you use it or ignore it? Thanks, Frank
The fine-adjust knob is a problem with the Osborne. It allows the tool to vibrate in use, which is no big deal in leather. But in wood…
Crank the fine adjust knob down as tight as it will go so its spring is not part of the equation. Then use the main knob only to adjust the radius.
Any solutions for helping what I guess is heat-damaged salted liquid hide glue to harden? Planing off pins and trails after a week, the glue is still a bit sticky. I had put the glue jar on my dashboard to warm, forgetting that mid-summer sun/windshield/glass jar was likely well over 150F. The drawer the day prior hardened fine.
Wow. I have not encountered this problem. First, I would freak out. Then I would probably use heat and moisture to disassemble the drawer, clean off the old glue and replace it with new.
Sorry I don’t have a magic answer….
Thanks 🙂 I think I’m going to treat it like a long term experiment, and see if it causes problems. I may pilot/drive a headless brad through the dovetail if it starts to open.
Thanks for the generous gift of your time.
Hi Chris,
Which plow plane did you mention that you liked – Record 43 or 44? Seems like it was the 43. If it is the 43 they seem to be “unobtanium” here in the states. The Veritas box makers plane seems to be pretty much the same plane with the usual Veritas refinements & QC – do you have an opinion on this new plane? I usually default to old but in this case I may need to take the new route.
I love the 043. I have not used the Veritas, but I assume it’s fine and dandy. Maybe someone here can chime in. Sorry.
Hey Chris,
What sort of notes do you keep after you’ve completed a chair (materials, finish, dimensions, comfort, etc.)? Do you keep notes pen/paper or digital?
Thanks!
-John
I am Mr. Clipboard. Every project has pages and pages of notes, drawings and photographs. As I work, I write down everything I need to remember about making the project again – adjustments to sizes or drill bits used or techniques. At the end, I consolidate all the information into a written description of the process on my laptop.
Hello Chris. Hope you, the family, and the crew are doing well. No particular question. Just wanted to thank you again for this weekly post. Further, just finished the post on AP, then, which has become a Saturday routine of reading it, them re-reading it to the wife. (She then grabs her “spell” books). Finally, a tad early, happy b-day. Take care.
Thanks Matt!
I just finished the ADB drinking table in hickory. I intend to use it as a dining/kitchen table for the forseeable future. I would like to finish it in either beeswax and linseed oil, or soap. Do you have any suggestions as to which might work best with this wood and in this application?
Thank you very much for your time.
FWIW, I asked a similar question of Chris a couple of weeks ago for a cherry dining room table. He recommended a variation on the soft wax recipe with 60/40 beeswax and carnuba. I made a batch (carnuba requires 180°+ temp to melt) and applied it yesterday using the soft wax application directions. The results are fantastic! The finish is superb. Chris, THANK YOU for the recommendation.
They are both low-protection finishes and will need to be renewed occasionally. The soap will give the wood a white case – totally matte. The beeswax/oil finish will give you a low sheen and a warm glow. So that’s how I would choose – based on the color/sheen desired.
Hi Chris. Based on your recommendations, I now own several Wood Owl bits, both the auger type with a lead screw) and the “overdrive” type that has a brad point. How do I know which one is right for the job? (And how will I know if Megan rolls her eyes when I say I’m looking for an augury on augery?)
They are fairly interchangeable. I thought the Overdrive bits left a cleaner exit hole, but my experience has been shifting on that recently. Try some sample holes and see what happens. One difference is the Overdrive bits cut sideways along the flutes, which can be good or bad, depending. Sorry to sound so mush mouthed.
Hey there. I have a huge amount of books to build bookshelves with. I’ve looked at the Monticello design but that’s so much wood. If you were to approach building larger format bookshelves more like the boarded one in TADB how would you think about it? Is there a good place for me to look for ideas? Thanks
The boarded bookcase can be scaled up no problem. You just have to secure it to the wall.
Our favorite large scale bookcases are the ones we have in our library, which are built with 2x12s and screws. They scale up great. Look at any of Megan’s posts on our library and you will see them. Nor\ joinery. Just screws.
https://blog.lostartpress.com/category/mechanical-library/
The world is filled with good bookcase designs. But these are my two favorites.
Hi Chris, thanks a lot for doing this.
I was wondering if you’ve ever made a version of your soft wax 2.0 with pure tung oil instead of linseed oil–if you have, what were the pros and cons? If not, is it something you think wouldn’t work, or just an unexplored option?
Yup. I have made several batches. It works great. We use linseed because it is less expensive and rooted in the Western tradition (which is what I know). But substitute away…. no real changes to the recipe.