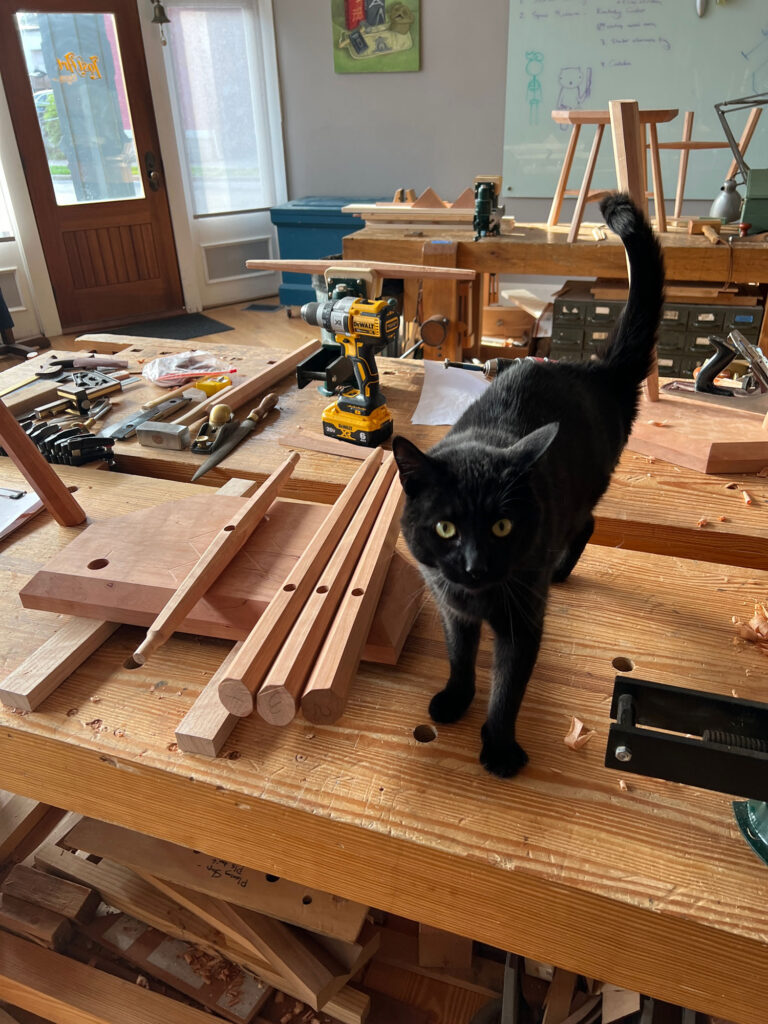
The Open Wire is now open and ready for your woodworking questions.
Every Saturday, I post a new blog entry that calls for questions. Write them in the comments section below, and I’ll do my best to answer them.
Before you ask a question, a few requests and comments.
- So far no one has posted a defamatory, troll-baiting comment. Thank you!
- If you could limit the number of questions you ask each week to one or two, my fingers will appreciate it.
- Long, multi-part questions with multiple digressions and links I have to click to understand your question make my brain hurt. Just saying.
- If your question is your first comment here, it will automatically be flagged for moderation. Your question will appear after I approve it.
So here we go…. Note that comments for this entry will close about 5 p.m. Eastern.
Comments are closed. See y’all next Saturday.
— Christopher Schwarz
I, like many woodworkers, do not find receiving information from the written word easy. Video tutorials and practical courses are thus essential to my woodworking education. Your series of videos on sharpening is a wonderful example of how to demonstrate skills. Your pace, ease, perspective and down-to-earthness is great.
As a musician I was taught to play instruments partly by learning to play scales and arpeggios. Playing a musical instrument is much, much more than playing scales and arpeggios, but the skills required to play these simple patterns are a good basis for the development of greater abilities.
So perhaps I can make an analogy between basic woodworking skills and the musical skills of playing scales and arpeggios. That is to say the sharpening videos show us the equivalent of scales and arpeggios for sharpening.
The LAP blog this week gave us a page from the Charles H Hayward books on dovetails. This took me back to my early teens in the 1970s when I bought these books and found them fascinating but remote and unmemorable.
If you were looking for a project to fill up some spare moments over the next few years there is a market for an excellent series of videos showing the scales and arpeggios of the Charles H Hayward (and of course many others) world. A series as well presented as the sharpening videos illustrating the basics, the woodworking scales and arpeggios, would be a tremendous asset for me and, probably, others. You would have the opportunity to build upwards from the most basic skills, knowing from the beginning where you are going and knowing what the end is. I am proposing a video “book” with a beginning, middle and end. The books already exist.
Would LAP consider devising what the scales and arpeggios of the woodworking world are (with perhaps the help of the LAP community) and then filming a series of videos illustrating these skills?
It’s not a bad idea, and we will consider it. We are a publishing company, so books will always be my primary love.
Video is difficult for me to produce because I have a hard time consuming it. Most how-to-videos could be compressed to a few minutes. But yet I have to scrub through 20 minutes of faff and etc. (Some people, however, do video VERY well, I might add).
Perhaps a video presentation of “The Essential Woodworker” would be helpful. Like I said, we will give it some thought!
I like it. We have audiobooks, now it’s time for videobooks.
Good morning Chris! I’m slowly building up the courage to try out chairmaking, and decided the Moravian stool you did for PopWood a while back would be an excellent place to start.
My question: Is the 1 3/8″ mortise crucial, or would 1 1/4″ work as well? I’d like to get the Veritas tenon maker and it doesn’t come in 1 3/8″. (Or would 1″ work? Might that be a more versatile tenon cutter to own?)
Thank you again for all you do Chris. You seriously make a huge difference with all the woodworking knowledge you share.
Courage in short supply this AM
May I respectfully suggest that the measure of another’s courage is a very difficult undertaking? Requiring, as it does, understanding of the other’s perspective, experiences, burdens, desires, and, of course, fears and trepidations?
I was afraid you were going to say that ….
The 1-1/4″ will be perfectly fine. I used 1-3/8″ because I was making a copy of a stool at Old Salem.
For what it’s worth, I made one a few years back before I had any chairmaking tools. Seat was a walnut offcut. Legs were all 1-1/4 relatively straight sawn ash. I didn’t have a tenon cutter, and rasped them round from tapered octagons, testing them as I went. Got too bold and made one tenon too small. Didn’t have enough wood to make an extra leg. Just kept rasping until it fit my 1″ bit.
The top looks a little funny, but it’s stable. I sit on it every morning to put on my shoes. Still waiting for that ‘crack’ to happen one night and make it authentic.
Morning Chris… have an amazing day and thanks for taking the time to moderate this forum.
Back at you, Brian.
Thanks for taking the time to take all these questions! My question: I want to build a Moxon vise. Should I go for a harder or for a less hard wood? Cheers!
It doesn’t matter much. Just avoid the softest woods (white pine, basswood) and the hardest (purpleheart etc.). Something cheap and plentiful
Thanks. I have a fair amount of both hard maple and SYP. Sounds like either will work. Cheers!
I used home center yellow pine and the tools for working wood screw kit to have a very usable easy to make vise. Fairly economical also.
I’m getting my courage up to build a dresser. Drawers etc. But figuring out what length of which piece to start with seem daunting. Do I start with the finished height (or width) and work backwards ? Or do I start with the drawers and what I need to store and work out from there? Has anyone written about this Drawings are good… Thanks
Chests of drawers are pretty standardized (with some variations) – about 20″ deep, depending on the wood available. About 40″-44″ tall. And about that in width. When I build one, the depth is determined by the widest and prettiest boards I have. The rest relates to tradition and how many drawers are needed. However, this isn’t how a first-timer should do it.
My advice would be to get “Illustrated Cabinetmaking” by Bill Hylton and study all the different forms in the book. It will give you a great feel for how casework should go together. Then find an antique piece you like the proportions of and use that (with Bill’s book) to help you sort out the part sizes.
Good morning, first time commenter, but I like your work and your attitude. I need to replace my grade school compass and I’d love to get one that will hold the (eventual) crucible grooving cutter. What recommendations would you make?
Vintage ones off eBay. I like the Starretts, which allow you to swap out the points with pencils (or a grooving compass). But lots of people made them.
I prefer a wing compass above all other forms because it locks firmly.
Thank you sir, for the reply and the time you’re taking Saturdays to indulge our random questions!
Would you remember an article being published somewhere, maybe in Popular Woodworking, on building Drew Langsner’s and Tom Donahey’s shave mule? I’m hoping to build one and I remember the article’s pictures explaining a difficult miter saw cut. Thanks!
Here are the free plans from Drew’s site http://www.drewlangsner.com/cw/muleplans2013.pdf
Here’s a link from Drew’s site for building the shave mule, http://www.drewlangsner.com/cw/muleplans2013.pdf
I hope the other poster’s link is good because I do not recall that article.
Tom Donahey has also posted a (free) 16-part video series on how he makes his shaving horse / mule. https://www.youtube.com/watch?v=p14v3zfvnts&list=PLX8WstgO3XdWJtoMNdb0RJGoiXkOJzEvP
Thanks for sharing the stool plan the other week. On a round stool do the sight lines for the legs all run through the center? Glenn
Yes they do!
Who was your favorite cat ever, and why? I won’t ask about your children.
Bean and I connect on a spiritual level.
I’ve got a cat like that. When she was a kitten I used to perch her up on my shoulder. Now as an adult she likes to hop my shoulder. I get to go around the house with a cat up there and pretend to be a pirate.
It’s kind of funny when I’m in a Zoom meeting and she does it.
We all appreciate your passion for preserving the craft and traditional techniques. How do you feel about tool innovation and its role in superseding traditional techniques in furniture building? Surely Roubo would have owned a router and Domino if he could?
I’ll be honest, I don’t buy the “Shakers would have had biscuit joiners” argument much.
I don’t have a CNC, even though I can afford one and it would make my life So Much Easier. I also don’t have a Pantorouter or Multirouter. I haven’t used a router table in years. Or a wide belt sander or a drum sander.
And I am not in any way, shape or form a historical re-enactor. No tools are “off limits” to me.
Woodworkers get to choose what tools they use. And they don’t have to default to the most technologically advanced ones. My aim is to dust off the old methods that have been forgotten and put them back in circulation. So that we all have more choices and a richer life in the shop.
Fair enough. Personally, I think there is integrity in the old methods and their reliance on craftsmanship (craftpersonship) that can’t be replicated by machines. Put simply, a piece made in this way has soul, and attaining the skill required edifies the soul of the creftsman. Thankyou St Chris.
You are a very generous and kind person, Chris.
Awww, thanks Keith. The Open Wire makes me feel less guilty about not having public email.
Did you come across footstools that were used with the stick chairs?
Thank you for your time.
Oh sure. Short three-legged creepies – sometimes covered in sheepskins – would be used as a footstool. Or the creepie would be used by children for sitting.
Last week I asked about drying rack and stickers. All is well on that end; 825 board feet of red oak is now stacked and air drying. My question is related to after drying and storage. Am building a new shop and have an open slate relate to how to store the dry wood. What is suggested for storage given no restrictions? Thank you
There is no correct answer, only arguments. The world is divided between vertical racks and horizontal racks. We use a combination of both. Horizontal storage for long-term stuff. Vertical for stuff we will us in the next month or two.
For horizontal racks, I like ones that are wall-mounted with prongs sticking out to support the wood. And a forklift to assist in the digging.
More important than all of the above is humidity control. A mini-split or HVAC system will make you happy when you start using the wood.
The dehumidifier in my shop was life changing.
I listen to Podcasts from your contemporaries when I am working in my shop. Would you consider a Podcast on a regular basis? Maybe you and Megan chatting about woodworking, tools, shops, or books?
To be honest, I’m not a good talker. Either I’m too quiet or my mouth flaps like a duck’s ass and I talk in circles. I think that’s why I’m a writer and have shied away from video and audio. We are starting to do more video because I know that is how some people learn best.
We have discussed a podcast. But I don’t want to do one that is like all the other podcasts. What’s on your bench? Answering listener questions? And topic or guest of the show. The above is a great format. I just don’t think the world needs another one.
We began doing a podcast called “The Afterlife of Trees” with Popular Woodworking years ago. Then they flamed out. The idea was for it to be more like Radiolab or This American Life. Short stories. With interview clips. I think they lost interest because it is So Much Work. Anyway, I should have answered: Maybe?
Thank you for the very concise answer to my question. I will continue to enjoy the information that you currently provide.
My son and I built a Nicholson style bench last year and we have been using it viseless ever since. I really like the bench, it is dead flat and massive enough to stay put even under heavy planing with a scrub plane. I haven’t used the crochet very much and was thinking of replacing it with a leg vise. Also considering building a bench mounted shaving horse that uses a holdfast to anchor it to the bench. I do a lot of whorl with drawknife and spokeshave. Your thoughts please.
A leg vise makes a lot of operations easier. It is my favorite face vise. The Benchcrafted Classic with a criss-cross is my favorite setup.
I don’t think I’ve seen a bench mounted shaving horse. Do you mean a shaving pony with the pedal on the floor? I used a shaving pony for years and it works fine. I prefer the bench-mounted carving vises for spindle work nowadays because it does so many other things for me.
Yes the Shaving pony is what I was referring to. What specific type of carving vise are you talking about? I would rather have something that could be mounted with a holdfast and removed easily when finished with it.
Also considering a portable bench top to elevate work for relief carving. I built the bench for basic hand work. It isn’t ideal for carving.
Instead of a portable bench top, I just lower myself and use an adjustable-height stool to sit and work at a comfortable height.
What kind of stool do you use? The one that is hinged to the bench leg or a free standing stool?
Both. I have a piano-like stool that moves up and down that I like.
The one I use mounts in a holdfast hole. They are green or red and can be found at Grizzly, Infinity Tools or Stewmac.
Thank you so much!!
This vise has been invaluable for my carving. I clamp things in it directly or using a cleat on the back if they are large (it was stable even about 20 inches outboard from the vice’s center, when carving a 42” wide eagle). A work board can be held with a cleat on the back and carvings can be held to it with double-sided tape or pegs and wedges. I’ve seen them on sale at Woodcraft, too.
Thanks for opening this channel! Yesterday we broke an arm while doing the glue-up of a chair. The part just wouldn’t go lower and we hammered too hard, I guess. We didn’t clamp the mortises for that part, only for when we put the wedges in… Do you have any tricks for that besides clamping? what do you do when the arm won’t go lower in the tenon during glue up? During the dry fit everything went in place with ease. Thanks in advance for your reply!
I found that a broken arm happens because of a few things:
I’ve had a few broken or cracked arms over the years. In time you will figure out how tight things should be. Hope this helps.
You forgot “the upper carriage falling off the chair onto the sidewalk.” 😊
Hi Chris. I really appreciate that you are doing this. If my question is to much for this format i get it, and apologize for imposing. Ok here it goes. I own a veritas skew rabbet plane. I cannoy seem to get the blade dialed in for cross grain rebates (get the blade cutting tip in line with the wheel cutter, as well as even to the sole). I dont think this should be a 30+ minute set up process. Do you think you could give any tips on setting up this plane?
Also, is there any chance this might be a video topic on sharpen this?
Thanks
Both the nicker and the iron need to protrude from the side of the plane to cut a square rabbet. Once I have the nicker in place (a one-time job), I try to put the iron in line with it – without fully cinching it down. I use a 6″ rule, laid across the round nicker, to check to see if they are in-line. I use my fingers to push the iron in place and then increase the pressure on the iron at the lever cap.
When the iron is fully cinched, I make small adjustments with a hammer.
There is a learning curve. I struggled with it when it came out. After a few months it became second nature.
I’ll put it on the list of videos to consider.
On aging, you once wrote that when you got old, you hoped your nurse would wheel you into your shop to touch your tools every day. Realistically how will you ease into retirement from your current frenetic pace? Which of your many endeavors will be scaled back first? Writing, publishing, tool-making, chair making, instructing? What will be the last before the tool touching phase?
I hope to die at my bench while working. I have no desire or plans to retire – ever. This is what I do. It’s what I love to do every day. And I would be lost if I didn’t do it.
When Megan teaches a class on the Shaker tray how does she attach the bottom?
She glues 1/4″ x 1/4″ strips of wood all around the inside of the tray. Then the bottom drops in and is removable.
When I make them I groove the interior surfaces and the bottom floats in the grooves.
Question on marquetry: hiw did the craftsmen account for wood movment when gluing marquetry panels? Im talking about before MDF, plywood, etc..
This is a question for Patrick Edwards. Short answer: the marquetry you are applying is wood that moves. And the ground is also wood that moves.
Yes but i mean what if the marquestry design requires cross grain pieces? Does. Marquetry fail down the line over this?
The pieces are tiny, so the movement is minimal for each piece.
Again, pester Patrick for a better answer.
I recently purchased your sharpening video series and in one of those you said “I’m not a fan of glass ceramic stones, buy me a beer and I’ll tell you why”. At the moment, I’m too far away to buy you a beer, so could you elaborate here?
They are not a good value. They don’t have much abrasive on them so they don’t last very long. And they are all the same color so they can be confusing to use. It’s easy to mix them up on the bench. I don’t get them one bit.
And sometimes they are touted as better for A2 steel. That’s BS.
In the Anarchist’s workbench you mention that you like hardwood chops for your legvise. It also looks like you’re using a chop thicker than the minimum 2.5” benchcrafted requires. Can you share more about your preferences for a chop? Is it aesthetics or function? I’m using a 2.5” thick SYP chop, so I don’t know what I’m missing. Thanks!
My chop is two pieces of 8/4 maple that are face-glued. I prefer a massive chop that will not bend or deflect under extreme pressure. It makes a difference.
There’s a stretch of walnut MCM cabinets that was my grandparent’s, my parent’s, now mine. My folks added a marble top to fancy it up. I subtracted it, because in my smaller dining room I need to place the four 34″ modules in two stretches. The top of the original cabinets is a bit effed up now from dremeling off the marble’s epoxy. I have one inch thick walnut slabs, now seasoned, I plan to dress and attach. Now the question: I’m wondering how to attach them. Can’t use buttons as there is already the original scratched up top in place. I think, through the top of the old cabinets, I’ll need to drill holes I can pass a screw through into the slabs. Should I lengthen the holes at the back edge of the cabinets? At the front? (Both or just one?) Also, should I wait now until fall to do this? The front edge, toward the room, will overhang by about an inch. The back edge facing the wall doesn’t need to, but could, as I haven’t cut the boards yet. Given baseboards it could push back 1/2″ or so.
Crazy question!
I would attach the new tops with screws. Use straight holes at the front of the cabinets to fix the position of the new tops. Then use slotted holes in the middle and the back to allow wood movement and push it to the rear of the cabinets. Hope this helps…
Unless a top was removed before the marble was added, replacing the marble with 1” walnut will produce a top much thicker than the original design.
You might be used to this odd appearance because you are used to the marble. But I would pause and think carefully about the intended and most attractive thickness of the top.
I would consider alternatives that stay closer to the design thickness of the top.
You could plane the top and add back a thin veneer.
You could remove and replace the scratched-up wood top. (That can be hard or easy, depending on how the original top is attached: dovetails, miters, screws, etc.)
If a top was removed prior to the marble installation, what’s left after the marble removal is a substructure. If that is solid wood, you can simply screw a new top to the substructure as long as you keep the same grain direction (likely) and a similar wood species (sounds like it). The new top and the substructure will move together. If you are nervous about this, there is no serious harm in some elongated holes.
If the substructure is (veneered) plywood, it would be very nice to use the elongated holes Chris describes.
The top was not removed; the marble was just glued on. It was 3″ high, an inch or so thick marble with a fancy routed edge front and sides, and wood supports behind. Didn’t love it, but might have used it anyway if it had fit, just for simplicity.
It is a veneered case so removing the top would be tricky, and would eff up the case fronts too; right now the damage is confined to the top (by me front & sides, but also from whoever screwed the wood supports through the top at the back). The drawer and door fronts are very nicely book-matched so most of the visual appeal of the piece is there.
I hear you as to design; I’d have let it be, if my folks had. But I’ve had the boards sitting up there for a year to acclimate, and they work. I’ll plane a chamfered front & side edge that will be style appropriate. And I do like the way a single top unifies the modules. The challenge was finding wood that was 4/4, not 8/4 or 16/4. It’ll end up 3/4, maybe 7/8. I did feel matching the thickness of the marble would not work well.
Thanks, much appreciated! Such a particular question I wasn’t sure how to Google it.
For us non-military types, acronyms can be hard. It took a minute but I got MCM is mid-century modern.
Oh, sorry. I’m not military either. I’m used to it from helping move my kids into apartments, and furnishing them with cast-offs (and a few builds too). Try a search on it on Facebook Marketplace! In the Northeast it’s been a long-running vogue that Madmen started.
In the January 1 post about the contents of your tool chest
https://blog.lostartpress.com/2023/01/01/the-anarchists-tool-chest-at-age-11/
you mention a “a shop-made pencil gauge that is indispensable, especially for chairmaking. It works on flat edges, inside curves and outside curves. I wish we could make these for sale”
Could you expand on how you use that? Is it for copying layouts from one hand to the other? If it’s not feasible to make the gauges for sale, might you consider selling plans instead?
Thanks for taking time for this every week.
Take any marking gauge. Drill a hole in the beam so it will accept a pencil. Then nail a couple half-dowels to the face of the gauge. Voila!
The gauge is used for marking lines off of a curved or straight edge – think the line of mortises in the seat for the spindles. Or the limits of the saddling. Or the centerline on the arm for mortises.
The particular shop-made gauge I have would be expensive to make. And it’s easy to modify any cheap gauge to work well.
Building a Moravian workbench. Your thoughts on a tail vise? If yes, do you have a favorite?
I don’t use a tail vise in my work. But in the past I have used (and like) the wagon vises that are integrated into the benchtop. Those are a lot of work to install.
The simple route I like is to install a quick-release vise at the end. And add a big wooden chop for the dog (so that the dog holes can be near the front edge of the benchtop).
Thanks. Being a bit slow on the uptake here, “wooden chop”?
The “chop” is the movable jaw of a vise.
I’m going to be trying out your 3-legged staked stool design today, but I’ve only got 8-1/2” wide 8/4 stock. Would you make the legs shorter if the top was scaled down? Thanks!
Probably, yes. Mostly for the visuals. I start with long legs and then cut them down at the end until I got to something that looked right and sat right.
Thanks, I’ll do that!
Yesterday I used a panel saw to crosscut a 30″ long by 3″ wide piece of oak and the saw pinched/binded a little. Earlier in the day, when I ripped the same board to the 3″ width on the table saw, the board pinched again just past the saw’s blade and splitter. I stopped the saw and put a small wedge in the far end. Is this what they call “tension” in wood? Any way to avoid it? The oak was air dried outside for three years then another five months in my shop before I started using it.
This is very typical. It can be caused by a lot of things. Tension in the wood being released. Uneven moisture content (the center is wet). Case hardening. With handsaws, lubricating the sawplate helps. On the table saw, make the cut in two steps.
Any advice on creative block? Or when you can’t to the lumber yard to get material? I’ve made about 276 boxes and looked at about 2.5 million furniture pictures.
It happens. When I feel blocked, I usually sharpen and tune my tools – get my hands working with my brain on some mundane task. Or I do some small task that improves the shop that I’ve been meaning to do.
For me, working is what helps me through it.
Thanks for doing this, Chris. You’re a real gent and LAP has given me very many happy hours over the past few difficult years as I try and learn. I’m going to try a door seat in my next chair (I’m broke again) – a rebated (rabbeted) frame with a panel as your Stick Chair Book says. Is there any guidance out there? Would I be mad to try and saddle it?
I don’t know of any modern maker who has made one. I haven’t, so I am no help. I’ve never seen one that was saddled. However, saddled Irish chairs are very rare.
If it were me, I’d do it. Jump in and see what happens.
Good morning! Thank you for taking time to interact with everyone through this format. I am currently working on my hand tool skills and tools. Could you help me with when it is best to use a low angle jack vs. a standard Jo 5 jack plane? Especially when flattening lumber in preparation for use.
Either tool works the same for typical jack plane work. The low-angle tools are favored by beginners because they are simpler to set up (fewer parts) and cheaper. You don’t need both.
Just finished the Sharpening video series and it is great.
You emboldened me to dust off the bench grinder that I was afraid to use for a decade or two and hadn’t yet purchased an expensive set of jigs for so thank you. As a result of my initial efforts I am now the proud owner of a skew chisel but I am getting better and I see the beauty of the system.
Where did you get the cool bench grinder stand? It is a heavy thing and having it at the ready will increase its use. I don’t remember if it has wheels? I haven’t been able to locate a similar one.
Thanks.
My grinder (my grandfather’s) came with it. Grizzly sells a wide variety of nice grinder stands.
Hello Chris
I’m building a bench that’s about 15” wide x 60” long and 16” high. The seat is cedar, just under 2” thick.
I’m using staked legs. The leg blanks are currently 2 1/2” square (mesquite, i think). They’ll be tapered octagons of some sort.
Will 1 1/2” round tenons (using Veritas power tenon cutter) be suitable for a bench this size? I know you used 2” round tenons in one of your low benches.
If 1 1/2” round tenons are suitable, would i need an undercarriage?
Thanks very much for your time.
1-1/2″ round tenons, wedged, will be plenty strong. You don’t have to have an undercarriage. But you can add one if you want insurance or for the bench’s design.
MiniCab update- how do you like it? Do you use it as much as you thought? What dealer did you get it from?
I love it to bits. I don’t drive much, but when I do, CatBus is the default. It is simple, reliable and insanely useful. I wish I could get a second one simply because they are so much fun. Sadly, we don’t need a second.
I got ours from Duncan Imports.
https://www.duncanimports.com/
The salesman was Lucas. They do an outstanding job of cleaning up these cars and selling them.
I really appreciate the focus you and LAP put on vernacular furniture. You often celebrate the irregularities (wonkiness) in pieces. I’m with you on that. That said, I don’t see it in your own work. Is that because availability of better materials, better tools or just your perfectionist tendencies?
Or, do you selfishly keep your more soulful pieces hidden away. Only taking them out after a long day in the shop, to admire and caress the asymmetries of the riven legs and spindles.
My furniture sure looks wonky to me.
I don’t have different modes of wonk. No wonk, some wonk, full wonk. I do my best and at full speed. I have been doing this for my entire adult life, so my wonkiness is not the same as when I was 24.
Any chairmaker would find flaws with my work. Angles that don’t match perfectly. Spindles that aren’t identical. But it’s not like a comb that is 1″ off horizontal.
When y’all are at handwork this September, I’d like to buy a few of your books and get a few I’ve already purchased autographed. How do you want me to identify my already purchased books so you don’t think I’m shoplifting? They already have my name and the date of purchase in them.
Hi Chris! Thanks gor answering questions.
Why a race knife instead of v-gouge for the American Peasant engravings?
The furniture I’m studying uses a race knife/timber scribe for the cuts. Plus, it is fast: run it against a fence and it makes a perfect line. It’s not like carving. It’s more like drafting.
We trust people. If you say you bought them, we say Great!
Back when you did commission work, how did you quote for things you had never built before?
I might know have built X, but I have built X Adjacent. I know how long it takes to make a table and a drawer, so I can make a good guess as to a nightstand. (Old price books used to list how many minutes/hours it took to perform EVERY operation in a workshop. These were used for estimating. We don’t have those anymore.)
Then it’s just Materials + Time (Hours x rate that auto mechanics charge) + a Little Profit
If someone asked me to do something nutso – sculpture, perhaps – I would ask for time+materials with weekly reports on the progress.
Years ago you talked about how during a power outage you sat on the floor and looked at the shadows of furniture. (Candlelight?) Since then you moved into your new place. Do you ever go down to the shop and look at your work in the moonlight, and if so, any revelations?
Some stuff looks better by candlelight. The Eastern European stuff I have been carving lately comes alive with candlelight. It’s impossible to photograph. But nice to behold.
Hi Chris,
This might be too personal of a question, but over all the years you’ve been making chairs, how many of them failed, and for what reason(s)? I’ve just started on my third one and split the seat when putting in the wedge. It was bound to happen, I’m sure. Comparative analysis with the failure of others helps soften the blow 🙂
I greatly appreciate all you do. And is it too early to say “May the Schwarz Be With You”?
I’ve lost three or four chairs over the years. All my fault. The joints were too tight. Or the wood was too weak and I ignored it. Once you’ve had a few failures, they will become VERY rare.
Hey Chris
At what point does a chair become your own design? My local wood working club has an annual show, but the rule is you can only enter your original work and designs. Ive made several stick chairs from your plans and Curtis Buchanon’s. At this point I’m doing serval things different with each chair but still feel anxious entering them in the show.
Thanks for all you do.
Travis
I consider a design to be my own when I cannot see the work of others in it. I have changed it enough that all of Dave Fleming, Don Weber and John Brown are gone. Like pornography, you’ll know it when you see it.
That’s my take. Others have a different level – probably less strict.
Thank you!
Hey Chris! I’m working on a staked backstool. My seat is poplar, finishing out at 2 5/8″ thick. While I was reaming out the mortises for the legs I realized that, in order to ream out the mortise out fully, so that the reamer’s 5/8″ thick section met the top surface of the seat, the wide shoulder of the reamer would be below the bottom surface of the seat. (Does that make any sense?) i.e. the reamer isn’t long enough to fully contact the entire length of the mortise in a piece that’s this thick. (I’m using the Veritas standard taper reamer.)
Anything I should do to adjust for this?
Don’t ream the entire depth. Ream until the base of the tenon fills the mortise opening. You will have s section of the hole that remains at 5/8″. So when you make your tenon, make sure you have a section that is a straight 5/8″ cylinder. Once you make a couple joints, this will become obvious.
Ah. Makes sense when you say it! Thank you.
You may have answered elsewhere, but some version of your log had and “E” in it. What for?
The image of the dividers comes from Moxon. The dividers are figure “E” in his book. Nothing sneaky or spooky, I’m afraid.
Greetings. Newbie chair maker question… I have just started making the templates for the ADB stick chair (without arms) and am struggling with determining the back radius of the seat and comb. I’ve been bouncing back/forth between the back stool and chair chapters and just can’t seem to work it out. Thanks in advance.
The radius of the interior of the comb is 15″. Hope this helps.
I had the same question. The bending form in the ADB showed a 12″ radius, and the No Fear Chairmaking mentioned a 14″ radius.
Thanks
Hi Chris,
Thank you for taking the time and effort to answer questions – very generous of you.
Are you still using Everclear 190(?) as the alcohol base for your shellacs? Are you still happy with its performance over time? If not, what do you currently use?
Thanks in advance.
We use everclear (a generic brand of it) for all alcohol applications – especially shellac. I try not to use anything with methanol as it is poisonous.
Hi, Chris,
Gosh, this forum is just such a wealth of knowledge and thought. I read through it every Saturday. Quick questions: 1. Why did you stop using your hand-turned grinder (if you did)? Because it’s slower or clumsier? 2. Is the width ratio of dowel to board similar of tenon/mortise to board, i.e., 1/3, as a rule of thumb? I’m trying to using hardwood dowels for anchoring angle braces for a leaning barn (after we right the barn) in half-lap jointed oak 2×4’s. Thanks!
I still use my hand-cranked grinder all the time. It is set up for dealing with profiled irons (such as beading planes). Either is one is quick and handy.
Maybe a timber framer could supply a structural answer. In furniture, it’s visual. I’ve seen enough pegged furniture that I know what looks right and will hold. Small frames and doors: 1/4″. Larger casework: 3/8″. Workbenches: 5/8″ to 7/8″. But I really would consult a timber framer.
Thank you! Now to find a timber framer in my area (the Missouri Ozarks)…
My next (third) chair will have a saddled seat, if the gods allow. What’s the best way to hone a Scorp?
Barr Tools has a pretty good video on the subject:
https://youtu.be/kMTm_Qgr0-s
Yup. I do it on the table saw (covered in my videos). Before that, I used diamond abrasives stuck to dowels. It’s all about keeping the edge in order so you never have to grind. Constant polishing.
I follow your milk paint prep method and, after filtering the paint through a paint filter, I find that the majority of the paint mixed seems like it gets caught in the filter. The paint that passes through works well but I was wondering what is considered to be the typical amount of byproduct discarded from the initial paint mix?
I don’t get a ton of solids. If you do, you might need more mixing.
If you want the ultimate milk paint tutorial, check out Peter Galbert’s video on it. It is a masterclass in using the stuff. I’m a piker.
Hi Chris . I have finished building the Irish-y Armchair and am preparing stock for the Curved-Back Armchair . I learned on the Irish-Y chair that increasing the seat width from 20 inches to 22 inches made the seat a better fit for me . On the Curved-Back chair is there any simple method for calculating the longer radius of the Backrest associated with the wider seat ? Or should I just draw a scale version ? thanks
If it’s just 2″, I would use the same radius. Just make the piece longer.
If it looks weird, draw a flatter radius on some paper or plywood and see how it looks. There are no formulas.
Thank you for the books, blog posts, and videos. I know very little about woodworking except for their contents.
I purchased a 16 3/4″ wide catalpa board last weekend thinking it would make a good chair seat. The downside is it is only 6/4. Should I do sliding dovetail batons? Should I save it for a different wide board project? I appreciate your input!
It might be a little thin. Is it full 6/4 (1-1/2″)? If so, then you could try to use it. If it’s thinner, I probably would use battens below
It is full 1-1/2″, a hair over even. Not quite 1-9/16″. I will evaluate again after I process it but I will give it a try. Thank you!
Thanks so much for taking time to do this every Saturday! Its so generous, and is a real testament to your love for teaching.
My question is regarding legs for chairs. You recommend only using wood where the grain is running straight along the length of the leg… and I understand that if the grain were to curve off to the side it would represent a weak spot in the leg. But what would you say about using really twisted grain (not sure if that’s the right term)? Basically, I have some nice cherry that doesn’t really have any really straight grained sections. When I tried to split it with an axe, it was really difficult as the grain was so interwoven and twisted. That makes me think it would not be weak and susceptible to breaking… but I am asking you since I am still new to all of this. Would this wood make suitable legs, or should I plunk down for some new lumber?
Twisted grain can be weak because there might be short sections where is moves dramatically. Save the twisted stuff for the seat, arm and comb. Straight stuff for the sticks, legs and stretcher. I promise, this is not theory. I have had some parts fail when I stepped away from this maxim.
Thank you! I truly appreciate it.
Thanks for doing this again!
I’ve got the crucible planing stop and am building the AWB after having built another Ruobo (and Nicholson, though I’m not a fan of that one). Why do you recommend the planing stop block being a foot long? Seems overkill when it will likely only be a half inch or so max above the top of the bench when in use. If it’s for installation to prevent splitting when driving the planing stop in, fine. But then why not cut if shorter after it’s driven into the block? Seems to me 8” would be plenty long for a 5” thick top. I like to keep stuff under the overhang of the bench, so I want to make the bottom projection no longer than necessary. I’ll just “disobey you,” and make it shorter. I guess I’m just questioning your rationale. Many thanks!
Cheers,
Dan
If you make the block 12″ long, you can use the planing stop for edge planing of wide boards, which can be faster than using a crochet or face vise. But if you never plan to do that, make it shorter.
Have you come across the ‘dovetail pencil’? I keep a pencil to mark dovetails. Just an ordinary pencil planed flat and thin down to the lead on both sides, then the point on one side sharpened at an angle on an old carborundum stone using a wedge. The other side remains flat as a reference face. This marker gets into the finest of pins. I’ve been using it for years but haven’t come across mention anywhere. Have you?
I use a half pencil for a lot of things, which is basically the same. For dovetails, I use a knife.
I’m seeking clarity when finishing with shellac & oils. I know i can use oil to pop the grain prior to shellac (e.g., raw linseed oil). I also know with some woods it’s helpful to use a “wash coat” of shellac to avoid splotching prior to oiling, like with cherry. So, it seems you can go both ways – shellac before oil or oil before shellac. Are there any fundamental principles to be aware when mixing shellac and oils?
I don’t put oil over shellac (or any film finish). Maybe a wash coat of shellac below will work as you suggest. But it’s not something I do.
When applying shellac over oil, I allow the oil to cure fully first. Usually a couple weeks.
Great Days
Does grain orientation matter on pins used in drawbored mortise and tendon joints?
The pegs need to be dead straight – I prefer to split them when possible. Any wandering grain can cause the pin to fail during insertion. Hope this answers your question.
Is the clocking of the grain in the bore important?
Some people will say yes. But from examining old work that survived very well…. nope.
What vintage is Bean? I have a modern saimese model and I think its claws are reasonably sharp, but maybe other makes hold an edge better? Sharpening still intimidates me. I know, I know, read the book.
Bean is four (we think). His claws are A2, sharpened at 30° with a 1° back bevel.
You’ve visited and taught in so many workshops. If you had to pick just one or two spaces, which were your favorite for hand tool work?
Hi Brian,
I have spent eight years trying to make this space perfect for us and students. It is built from lessons I have learned from teaching everywhere. So….
The light and wooden floor of Roy Underhill’s shop, but with more elbow room.
The kitchen and library of the Dictum workshop in Germany.
The urban setting and walk-ability of Phil Lowe’s shop.
Good benches.
Thanks Chris. It’s wonderful to see how the LAP Storefront has evolved, and it warms my heart to know that it’s become the perfect shop for you. So many great books, ideas, classes, and chairs coming out of it lately. A true treasure for us all.
How often do you use clear quatersawn eastern white pine ?
If I could get it, I would use it every day. It’s hard to come by here.
I was asking because I come across 1 or 2 trees each year that give me that quality lumber from my sawmill. Thanks for the reply !
Lucky you!
Thanks for doing this! Looking back, what’s your thought on living above your shop/business? Would you do it again? Anything you’d do differently?
Yes. This has been my dream for a long long time. Lucy loves it as well.
There is no separation between my work and life. I am always working. I am never working.
If you aren’t that kind of person, this might not be the life for you.
You say you sharpen everything at 35 degrees. Is that the angle you use on your low angle block plane as well?
I grind at 30° and hone/polish at 35°. Yes, even for bevel-up tools and my low-angle block plane. Works great.
Hi Chris. I know Evanfall Studios had a CA wildfire that burnt down his shop and his parents/in-laws were impacted by a dam that broke in CA. Poor guy. I contributed to the LAP fundraiser many years ago. Do you know what has happened to Evanfall Studios since or could you find out? They no longer have a web presence which is too bad as he made awesome shooting boards. Use mine all the time and am happy to have it. Thanks.
I found this on Instagram: https://www.instagram.com/evenfallstudios/?hl=en
Hope it helps
I don’t know any other way of reaching them, either. Sorry.
Hello Chris, i would like to know
-Why saddling the seat before drilling ?
-What was the most common mortise size for legs in vernicular chairs (considering ash) ?
-Could it be possible to do a small open wire with Chris Williams this summer ?
-Did you find any example of stacked furniture in France (excepting the Alpish stool and Alsacian chairs)
Thank you very very much and have a nice day
Hello Chris, i would like to know
-Why saddling the seat before drilling ?
I saddle at the end, right before assembly. So I don’t do this. Nor do I fully understand why some people do.
-What was the most common mortise size for legs in vernicular chairs (considering ash) ?
1″ diameter.
-Could it be possible to do a small open wire with Chris Williams this summer ?
Doubtful. He truly dislikes the internet.
-Did you find any example of stacked furniture in France (excepting the Alpish stool and Alsacian chairs)
Some stools. But not much else. I was only looking for a couple days, so I am sure it’s out there.
Does the stick chair form have an armrestless form? I haven’t gotten the stick chair book yet, but I don’t recall you ever showing any examples of chairs without arms.
Yes. They are called Staked Backstools. Here’s one I build a lot:
https://christophermschwarz.com/chairs/2ba0hke617iwn2fgz4l3rxr1vfv3x4
Can you recommend or preferably sell a book on making traditional molding planes ( hollows & rounds etc)? Thank you for printing books the way they should be made, my collection is small but growing
Matt Bickford is supposed to be working on one, but I haven’t touched base with him in a long time.
In the meantime, the Lie-Nielsen video on the process (hosted by the Old Street/Clark & Williams team) is outstanding.
I plan to attend Handworks this fall, which will be my third or maybe fourth. I know what I need to do to attend the event, but I was pondering what Venders all have to contend with to make it to this event. No small feat for you or Patrick, or those traveling from England or Australia. Is that something you could provide a glimpse into?
Also, in the past I usually limited my Woodworking related travels to one a year, and these were usually to the Midwest (not a fan of the scary East Coast). This started with Woodworking in America (WIA, which I now really miss), then Windsor Chair making classes with Curtis Buchanan (which, now that he has “retired”, I also miss), which has led to Handworks. So I do tend to keep an eye on your schedules. I enjoyed visiting Covington for WIA and consider each of your classes. However, I’m a bit over Chaired at this point, and I’ve built a Tool Chest, so here’s a few suggestions for classes – Sharp or Breed; Carving a Ball in Claw Leg; Becksvoort; Building something Shaker; or how about Jamel Builds a Mitre Jack (this last one I would definitely schedule!
Always a Fan! (I Dearly miss Woodworking Magazine, and Popular Woodworking [when that amounted to something])
Kevin Schroeder
Schroeder’s Chair Shop & Brewing
Hi Kevin,
Jameel and FJ make it an easy process. They are very organized. We are not a traveling show, so we just load up a bunch of books and shelving into a truck or trailer and go. If you do this only once every couple years, it’s fun. And we probably do it all the wrong way.
Vendors who travel for a living will have better stories of woe and glee, I’m sure.
Thanks for the class suggestions. We are not doing many classes now. You might reach out to Jameel about teaching. I know they want to teach in their new space.
Excellent, and Thanks! I’ll see you at Handworks. And I will contact Jameel and suggest the class.
I am building a massive, custom sized, custom designed woodworker’s workbench. I have read both of your books, 2 articles, and am pulling features from several plans to incorporate into my one bench.
The primary design is the Benchcrafted split top Roubo. If I build the under frame primarily off of your 18th century Roubo, except I don’t do the dovetail top-to-frame joinery (primarily because I don’t trust my handsaw skills enough), and instead do the mortise and tenon joint from your Holtzpaffel bench, will the end frames be rigid enough to hold in place the split top? Would I need to do draw bore pegging or will the weight of the top pieces be enough to hold them in place. They would be glued as I have no future need to knock down the finished bench.
You will need stretchers between the rear and front legs – right below the benchtop – to support the benchtops. I always prefer to drawbore workbench joints because it is a fun form of insurance. But I am sure glue and a good joint will be enough.
Boiled crest rails from white oak an hour and a half in an aluminum roaster on the barbecue. Bent with 11 inch and 13 inch radius MDF forms. (Your ADB is brilliant 🙂 Longitudinal splits in each. Kiln dried, 3/4x3x18”. Suggestions other than air dried?
Pre-soak the crests for a couple weeks (I use PVC pipe) with a tablespoon of fabric softener. Try again!
Thank you for your time Christopher. Question: rewind to the beginning of your woodworking career and imagine you had a open wire day with a Christopher Schwartz 2.0. What question would you have liked to ask for which the answer would have given you the most benefit, in retrospect?
Does it get easier? Yes, after years of frustration you reach a point where you can see for miles.
Are there any Crucible tools in the works you can talk about?
Favorite Beatle?
Thanks!
Nothing I haven’t already discussed on the blog:
Hi,
Thanks for all the time and answers you’re offering. And for making great products locally.
My question is about the leg tenon(s) going into the Roubo workbench top. I’m making my bench from 8/4 ash. So the I don’t have the easy luxury of the 1.25″ multiples. The instructions in your book yield a 2.5″ tenon, half of the leg’s thickness. But say I have 3 layers of 1.5″ for my leg. Would using the middle layer as the tenon (1.5″ tenon) be enough? Or should I actually cut a tenon that’s thicker (e.g. half of my 3 x 1.5″ = ~ 2.25″)?
Thanks again for sticking to classic values.
A 1-1/2″ tenon is fine for this joint. I would also drawbore the joint.
In your scorp sharpening video, you mention attaching some kind of paper to one side of the disc in the table saw. Anything specific?
I’ve tried the brown paper from a grocery bag.
It sort of works, but doesn’t seem to hang on to the polishing compound all that well.
I’m using a generic green rouge.
I use MDF paper from the craft store. Affixed with spray adhesive. You also could go whole hog and use hard leather.
Thank you so much for doing this!
A technical chairmaking question: Why are the tenons of the short sticks usually wedged in the arm bow even when they are not wedged in the seat? They are supposed to keep the chair together when you lift it by its arms, I suppose. Won’t the sticks come out of the seat eventually instead of the arms if they are not wedged down there too? Am I overlooking something?
Thank you!
You can wedge the sticks in the seat if you like. You have to wedge the sticks in the arms to fill gaps and get a better joint (the arm is thinner than the seat.
Also, not wedging the sticks in the seat makes future repairs easier.
Just my 2 cents. Others think differently.
What is the difference between “Mechanick Exercises or the Doctrine of Handy-Works” by Joseph Moxon vs “The Art of Joinery” 2nd addition 2013. The Art of Joinery has Chris’ comments added. Am I missing anything significant by not buying the Mechanick Exercises?
“Mechanick Exercises” is the entire book (woodworking, carpentry, blacksmithing, turning etc.) as it appeared in the 17th century.
“Art of Joinery” is only the section on woodworking. Annotated by me. It is no longer for sale as a print book, but you can download it for free from our store.
Another workbench question (Thanks again!). After you really sold me on nails, I was surprised to see screws for the shelf of the anarchist workbench. Any reason why you prefer screws here?
I was probably out of nails.