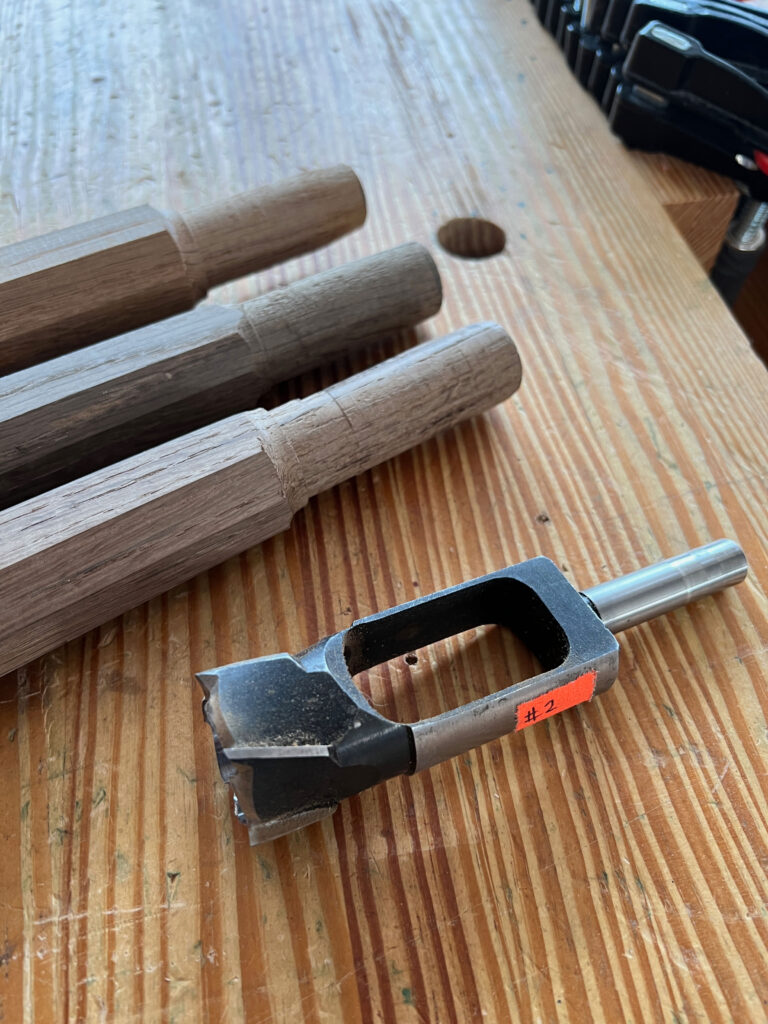
We have now opened the floor for woodworking questions this morning.
Every Saturday, I post a new blog entry that calls for your questions. You can write them in the comments section below. I’ll do my best to answer them.
Please read the following before you post a comment.
I reserve the right to ignore questions that are obviously hate mail or cross the lines of decorum. Also, if you post a comment and it does not immediately appear, it likely has been flagged for moderation. First-time commenters are always kicked to moderation. Also, posting a lot of links, using hateful language or excessive length causes the software to flag it for moderation.
So your comment will appear after I approve it.
In other words, there is no need to keep posting a comment over and over.
So here we go…. Note that comments for this entry will close about 5 p.m. Eastern.
— Christopher Schwarz
What is the tool in picture
It’s a tenon or plug cutter. You can buy them in a variety of sizes from a bunch of different makers.
In this style, Freud and Fisch are two more reputable companies that make them but you can find cheaper versions elsewhere on the web.
Lee valley makes some similar to this as well.
It is a 1″ plug/tenon cutter. Made by CMT. https://factorydirectsupplyonline.com/products/cmt-529-254-31
I use it in a cordless drill. But they recommend you use a drill press.
No question comes to mind, but thanks for doing this. It’s very generous, and a crapload of time you are giving up.
I am happy to do it! I wouldn’t be here if it weren’t for all of you.
Hey Chris! Thanks for doing this! Do you have a resource for learning more about spells or glyphs? I want to make some of my own.
thanks.
Josh
You posted a really nice “little black stool” on instagram the other day. Will this be a project in a forthcoming book? If not, any chance of some more measurement/ construction details, please? Thanks
It is the subject of tomorrow’s blog here.
Little black stools go with everything, from formal to casual. Or it could a sign of a bleeding ulcer or esophageal varices.
Have you ever made a children’s Welsh stick chair? Do you have any tips on how to scale the dimensions down?
Thank you for doing this! I really appreciate your books.
I’ve made some slightly smaller ones that were for juveniles. But not for small children.
If I were going to do this, I would buy plans for a child’s Windsor and adapt them for a stick chair (i.e. simplify them). This would be a good starting point. https://www.leevalley.com/en-us/shop/tools/plans/74154-childs-windsor-chair-plan?item=01L5043
This is on my todo list too. I did make a small stick chair for my grandson’s stuffed animal, a teddy bear. It has unusual dimensions due to it being made for a non-human. It sits next to a small rocking chair my dad made for my daughter when she was small. My suggestion is to go for it.
Okay, I am officially a fan.my only hope is none of granddaughters hear about Teddy’s chair!
I made a roughly 3/4 scale version of the Stick Chair desogn in The Anarchist’s Design Book for my 4 year old son, and it’s a pretty perfect size for him. I kept the components at the same thickness for strength, just shrunk down the length/width.
If for the next twenty years you had the choice to either (A) continue as you are Covington/LAP/Crucible Tool OR (B) be time transported back to 18th century France where you would work in Roubo’s workshop which would you choose? Assume your family could time travel with you if that’s a factor.
I love modern medicine and wouldn’t be alive without it. So I think I’ll stick to the 21st century.
I would love to visit earlier times. But I’m not a historical reenactor. My core interest lies in discovering old/forgotten techniques that can help us today.
Wheeler
Meant for search box. Oops
Were you attempting to see if Chris had posted any blogs reviewing the music of Wheeler Walker Jr.?
Hello. My wife always complains that whatever finish I use “stinks”… any recommendations for one that smells like roses and freshly bathed newborns? Or close.
Not Chris but I know he’s a fan of soap finishes. It’s quite literally soap, so about as close as you can get to that fresh newborn smell. He’s got a few videos on them of YouTube and the like.
As mentioned by a reader, castille soap smells great but offers little protection. What you are smelling is usually the solvent. If you switch to a finish that uses a citrus solvent (such as soft wax) then the smell is minimal and pleasurable. Another option: Shellac has alcohol for a solvent. That dissipates quickly.
Also consider beeswax. I like the dark variety and after application it is ready to go with no dry time. I use a heat gun to make it thinner and the warm wood really soaks it up, providing deeper penetration. Use a polissoir to burnish.
Do you have any thoughts on the A. A. Woods hollow auger for chair making? Looking through the blog archives it appears you used to own one but sold it in 2010.
Yes. It was fussy. I much prefer the new Veritas power tenon cutters. Or using a tenon/plug cutter. All these tools can be used in a brace.
Is it necessary to use sliding dovetails or other complicated joinery for drawer dividers instead of stopped dados, when the carcass is constructed with dovetails on larger pieces? Thanks.
Nope. It is not necessary to dovetail your drawer blades. But some high-end pieces used a full or half dovetail to do it. Typically the other casework joinery does a fine job of keeping the case square and true.
Thanks for your time and help. Love all your content.
Do you fill the grain when finishing campaign furniture made from mahogany?
Historically, it can go either way. I’ve seen both. I do not. I prefer shellac and then some black wax, which gets into the pores but doesn’t completely fill them.
Perchance a post about this type of finish?
Every piece in “Campaign Furniture” is finished this way. Apply two coats of shellac, sanding between coats. Then add a dark wax with a steel wool pad or non-woven abrasive. I use Liberon Black Bison Wax in Dark Oak. After you wipe it on, wait only a minute and then buff off with a huck towel. Done.
A question on the 3-legged stool in the campaign furniture book. I’ve made one at the dimensions shown, but I want to make a taller one using the same techniques. Did you see any that were taller in your research? I’m talking 26 or 27 inches for each leg. I’m using hickory, for strength, but I worry that if you found none that were this tall, there’s a reason. I’m using the doohickey sold by Lee Valley for the connection.
I have not seen taller ones. I think the issue is both strength and stability. But I haven’t made one that tall so I am just talking out of my butt.
Can you carve Peter Folonasde carvings in kiln dried oak?Are plan tracks ok?
You can carve kiln-dried oak, it’s just much more work and difficult to get a nice surface. But until you can get green oak, by all means work with what you have.
On plane tracks, I am fine with them on secondary surfaces. On primary show surfaces I set my plane to avoid them. Or I scrape/sand them out.
Peter Follansbee’s carvings are also aided by using riven green wood; the riving makes for very consistent grain. In kiln-dried you might look for quartersawn (he brought some to a box class I took once). But yeah use anything you have. On his blog he uses sycamore (a period choice too), walnut, Alaskan cedar; likely others I’ve forgotten.
I am replacing the wood on my wife’s fancy wind chimes because it came with a film finish that has failed and one piece of wood is warping. I have some white oak which should be suitable for outdoors. Would it be a good idea to use a finish like linseed oil for additional protection or do you think white oak is fine on its own?
Probably not much wood on a wind chime. Get a small piece of teak. No finish necessary. Weathers to a silver color.
White oak survives nicely outside without a finish. But a yearly coat of linseed oil will make it look better and last even longer.
When adding dovetails for strength rather than beauty, is there a ratio of dovetail size (width and height) and guidance of how many dovetails to use on an edge?
For strength, Frank Klausz uses equal-sized tails and pins. It looks odd to our eyes, but it how many utility pieces were made in Europe. If you search for old coffins you can see some of this.
I know there are rules that have been posited about dovetail spacing (check out Rob Cosman’s channel for more on this). But I have seen enough old work spread out over the last 1,500 years that I know those rules are barely guidelines. The joint is overkill in its strength, so there is GREAT elasticity in what works and survives.
Me, I like the base of my tails to be a little wider than my thumb on regular drawers. Then I scale that up for case pieces and scale it down for small drawers.
I’ve noticed you tend to make the same types of chair. Don’t get me wrong- I like them. But what motivates you with each new build? What are you shooting for?
They all look very different to me! For now, I am staying in the realm of stick chairs, which are vernacular forms. There is so much to explore, and the moves I am making are iterative. Small changes to get to another form. For me, it’s the only way to really really know a type of furniture. If you saw my chairs from 20 years ago you would see clearly how I’ve changed. But it is like erosion in its speed.
Did you know that Archers of Loaf put out a new album after 35 years, last year?! It is surprisingly, stunningly good from start to finish.
Yup. And I own it!
I’m trying to learn to steam bend chair arms, I have a sawmill and some cypress logs salvaged from a road widening project.any advice
A class is the best way to learn because it is a tactile, hands-on and detailed process. To get started, get this book: “Wood & Steam: Steam-Bending Techniques to Make 16 Projects in Wood” by Charlie Whinney. Whinney sometimes teaches classes in the U.S. Taking a class with Greg Pennington or any of the other chairmakers who specialize in steambending arms would be a great start.
Hi, I wanted to ask what drawknife you use and what you recommend. I know you. Posted that drawknives arent your jam but i cant find any really good information out there. Thanks!
I have the Lie-Nielsen curved drawknife. And I sharpen it with the DrawSharp (amazing little gizmo). Green woodworkers have particular tastes in drawknives and what works best for their work (bevel-down, bevel-up, handle orientation). But I can say that the LN works great as an all-purpose tool.
Straight or curved?
Read my response again.
Oops, my bad
I have found tapered tenons to be a more reliable means to achieve a strong, well fitting leg to saddle joint in Windsor chair construction.
I find that tapered tenons for the leg/saddle joint in Windsor chairs provide a more reliable fit than round tenons.
This is for a stool. And vernacular chairs have survived just fine for hundreds of years with cylindrical tenons.
Yes, I agree! Both joint types are durable. My comment addresses the ease of achieving an accurate, tight fitting joint. I’ve found the tapered tenon process to a less troublesome approach. It’s pretty easy to get a wiggly joint with a cylindrical tenon that is only few thousands of an inch smaller than the mortise. Whereas, this does not occur with a tapered, e.g. conical, tenon on either a chair, table, bench or stool.
Ever since Lost Art Press has been holding stick chair classes, I have tried very, very hard to attend one. But, it seems impossible to get a seat/chair at the table.
I will continue to offer them regularly until there is no more interest. I hope that other chairmakers will start offering classes in stick chairs. I am training a few people who I think will be excellent teachers.
Sorry you are having trouble. We are not a school and so there is only so much we can do when it comes to teaching.
Can you carve Peter F. Carvings in kiln dried oak? Thoughts on plane tracks? Favorite cookbook?
Brash wood has surprised me a couple of times late in the process of building chairs. How could I have identified the problem earlier? Is the “hammer test” the only way?
Avoid fast-growth oak. It is more likely brash. And if the board feels lighter than it should, it is more likely to be brash.
Hey Chris, thanks for doing this. This blog is my daily respite from a hectic life. My sincerest thanks. I built the 21st century workbench in 2009. It’s been great but I was limited to 6’ in length. Also, it’s 30” wide, as you said in the accompanying video, that’s too wide. I’d like to add 2’ in length, remove the tills, and add a leg vise. My question is about adding length. Would you have any reservations about adding 12” on each side using dominoes and flattening afterwards? Any other advice is appreciated but I understand this might be more complicated than a simple reply. All the best.
I would have no reservations about adding length. It’s a bench and is an open experiment. You might need to add some braces underneath the extensions (lag screws) to prevent deflection. But other than that…. go for it.
Have you built furniture with redwood (new growth, kiln dried). Any advice on construction or finishing?
Yes. It is VERY fragile. Splits and splinters like crazy. So be careful with driving fasteners – you can split surprisingly large pieces of wood with a screw.
It glues great and takes a beautiful finish with handplanes. Other than that….
This was my question, too! Have you ever built a chair from redwood? We live in Northern California and have access to tons of it. Would be fun to craft from local wood but not if it’s too weak. Thoughts?
I haven’t used redwood for a stick chair. If you bulk up the components you can use almost anything (even white pine). But you run up against your parts looking…. inflated. My choices in your area would be tan oak, big leaf maple, madrone, or claro walnut. All are strong enough and beautiful.
What is your preferred way of making a mortise and tenon joint?
When there are four, saws and mortise chisels. When I have more, I now use a Domino.
You have mentioned that some surfaces of furniture are left rough planed at times. Can you explain more about which sides and what types of furniture would not ‘finish/smooth’ plane all sides?
Can you elaborate when and where nails and tacks would have been historically used in furniture?
Can you discuss when paint v stain/natural finish would have been used? Do you believe much of our antique stock would have originally been stained?
Michael,
This question is unanswerable by a comment, blog entry or even book. But the answer is free. Go to an antique store and start opening the doors and drawers. Photograph what you find. You will see that these questions are answered by when the piece was made, who made it, what technology was available, who the customer was and what tools the maker owned.
As to stains/dyes anything goes.
Sorry I don’t have a good source to help.
Perfect! Thank you
Or can you suggest some LAP books with this info. I have Joiner & Cabinetmaker which led to the above questions.
Hello, i have a question about drilling in chair seats, i use beautiful and wide ash board that are not straight (+/- 10mm in the middle of a 45cm wide board) and i’m wondering if traditional (Welsh) chair makers would have spend so much time and effort flattening it ?(knowing that you cannot see one side and the other would be saddled). Then keeping it not flat changes the drilling angle of each leg (if the board is not flat and twisted) so what could have been the trick to have good angle for legs using only a sliding bevel or two? Thank you very much.
The real answer is they would get it as flat as necessary to drill the mortises so they weren’t visibly wonky. A little wonkiness is acceptable (even appreciated). But it’s not intentional. It is the result of doing your best and accepting the result.
And that’s the way I work as well.
When I start trying to sell things, should I form an LLC, or would a DBA (Doing Business As) suffice? Not a big business, just selling a few items in addition to a day job.
Set up an LLC – cheap in most states – limits liability – you can always get sued – and sometimes for the stupidest shit. Getting sued is a low-probability high-severity risk – get insurance – limited liability is great insurance.
Business tax lawyer here–seconding Robert Jennings. d/b/a vs. LLC won’t make a tax/economic difference, as long as you’re the sole member. But the liability protection it offers is well worth the (minimal) upfront cost.
While an LLC is the “safe” choice, most people who just sell a few items here and there operate as sole proprietors. Setting up an LLC isn’t hard, but there usually is some reporting and paperwork to do every year.
Check your state’s LLC filing requirements. Here in California it will cost you $800 a year for an LLC. You may be able to file it in another state.
This is the reason God made Delaware
I find it very difficult and expensive to obtain straight grain wood. I worry that the legs of a chair might fail over time. Do you think I am taking a chance using wood that is not straight grain? I have not I used stretchers in the past, but would they help the longevity of the chair?Thanks for all you do—-Lyle
I really insist on straight grain for legs, sticks and stretchers. If it’s not straight from the lumberyard, I straighten it by splitting it with a froe.
Try buying firewood. It’s split. Straight. And nearly dry.
Thanks for the information—Lyle
Hi Chris – I recently purchased a lathe and I’m looking for a grinder for the HSS tools. I’m approaching 60 and I’m sure a Chinese grinder will outlive me however I prefer to buy American. Any thoughts other than a Baldor? The Tradesman maybe? (I’ve not had the best luck buying used)
Buy a used grinder. There are lots of them out there. I have an old USA-made Craftsman grinder. There will never be a shortage of old grinders at garage sales and auctions.
Have you had success applying “true” milk paint (the type that begins as a dry powder to be mixed with water – not the latex substitute) with a spray gun? I assume it requires a thorough filtering to avoid clogging the spray gun.
In your opinion does the finish suffer from the lack of brush marks that is pretty typical with the usual method of application? Does spraying it make it look too homogeneous?
Thanks for taking your time to create this forum!
You can definitely spray true milk paint. It might be the fastest and best way to apply it. If you want brushmarks, brush on the final coat. Or spray the last coat and run a brush through it.
Hi Chris,
I’m currently working on my first stick chair. It’s going well enough and I feel as if I’m learning enough to build a GOOD chair next time. I have this idea about building a bench based on the WSC design. Sort of a double-wide stick chair. Do these exist? What would I need to do to make it beefy enough for two people? Enormous legs? I would rather keep it to four legs rather than six. Is this just a bad idea? Any thoughts?
Thanks! Jim
John Brown and Chris Williams both made many Welsh settees. I’ve never seen an antique one, but theirs were very nice. I know there is one shown in Chris’s book on page 75. JB called it a “double-seated chair.” I don’t know of any other published photos of it on the internet. Though JB’s old columns had a few more.
So yes, it can be done!
Thanks for doing this! What a great resource.
My question is about Sharpen This. I have some sort of undiagnosed learning disability that makes it very hard for me to conceptualize things I read. But if I see it done, I can almost immediately pick up whatever is being demonstrated. I have a few tricky tools (spokeshaves, narrow chisels, huge slick, drawknife) laying on my bench that I’ve been procrastinating sharpening and wanted to see what The Schwarz had to say about sharpening them. Would I be better off with the video or book?
I just had a mental image of a t-shirt with Chris decked out as the Terminator and the legend “The Schwarz”. Sunglasses, leather jacket and a #8 stanley plane over his shoulder.
I’m not Chris but I have the Sharpen This video and highly recommend it for your situation. It covers everything in good visual detail.
My 2-cents worth – if you are a better visual learner, definitely get the videos. I have and find value in both and I am a “read and visualize” learner. The videos are clear, short enough to grasp the concept easily, and you get the added bonus of Chris’s personality coming through. You won’t regret the videos.
Likely the video. Or get someone to give you an in-person lesson. That’s the best way to learn quickly in my experience.
I’m starting my second stick chair and Im using “roasted poplar”. It’s a great chocolate color but I’m a little concerned that the legs will be stong enough. I’m Planning 1 7/8 tapered octogon legs with tapered tenons.
If the grain is straight, you should be fine.
Hit some with a sledge and see what happens!
I am planning on building a simple but functional workbench. What would you recommend to fix the top to the frame? Thank you.
I like to tenon the legs into the top. Then drawbore the joint. Barring that, I like to use hex-head bolts, nuts and washers to create a reversible but stout connection.
My least favorite method: gravity and dowels for locating the top.
Depends. Simple (like the torsion box design English workbench): nails. Predrill, incl. a 5mm deep larger hole for the nail head. Sink the nail good and deep. Constantly check when flattening the top (otherwise you’ll nick the iron or plane body). Nails have flexibility to account for wood movement. Good luck!
Hey Chris, thank you for being so generous with your time.
I was searching yesterday for the photo of the finished cottage table that you posted (the one you didn’t end up liking). Do you recall where I can find that?
Also, there was a thread about clenching nails. You said you might make a video on how to do it. Wondering if that made the todo list.
The drawing of it is here:
https://christopherschwarz.substack.com/p/project-no-1-cottage-table?utm_source=%2Fsearch%2Fcottage&utm_medium=reader2
You can see the photo here: https://www.instagram.com/p/Cqx4EuROlzB/?utm_source=ig_web_copy_link
I haven’t done a video on clenching nails yet. Need to do that.
Thanks, Chris.
You mentioned the tenon/plug cutter above, and that you use it with a cordless drill. Have you ever used a 2″ one? (I’m thinking about your staked desk design. I’ve made one before, but don’t own a lathe and found shaping and fitting the round tenon pesky).
The biggest one I have used is 1-1/4″. If you shave closely, it should be do-able. But wow. That’s a lot of tenon. When I make tenons that big I use a lathe.
On building a slab top Roubo, I see a lot of benches with a sliding dovetail coupled with a second tenon for the legs. Is this a better option than the draw bored mortise and tenon you used for the Anarchist’s Workbench.
I really appreciate your time.
No. It is not. But it looks cool. I prefer a blind tenon because it is simpler and movement of the top doesn’t interfere with the benchtop. You have to flatten the top of that tenon/dovetail quite a bit as the bench breaks in.
That’s what I was hoping to hear. Thank you
Me, too. I did a blind tenon and every time I see that chunky dovetail, I wonder if I am inadequate in some way. I am sure that I am, but not in this particular way.
Hi Chris,
After 7 years of woodworking with hand tools, I’ve decided to go from my metallic planes to wooden planes. Mostly like the lighter weight and wood on wood feel. Not selling the metallics so I can go back. Two of woodies have arrived and they are the transitional ones. I dislike that the advancing and retracting of the blade is opposite direction from the metallic ones.
Q1 Have you ever heard of anyone trying to alter this advancing and directionality in the transition planes so same as metallic ones?
Q2 Now that I have some spare parts coming (double sided screw thingy, adjustor wheel, yoke) designed for metallic ones, if they don’t just screw in place, do you know a machinist who could make me a Franken double thread so one end screws into the metal part on transitional plane and then takes the new adjustor wheel? I will have orignal bits so we know the thread and pitch to screw in that direction and will have new parts so we know what pitch and direction I need for that end.
Many thanks for the help.
Sincerely,
Joe
PS I lived in the UK for two years and never fully adjusted to the opposite road directionality. Kind of feel the same way about the advancing and retracting on the transitional planes vs. metallic ones.
Hi Joe,
I’m not a fan of the transitionals. They are the worst of both worlds (though some people LOVE them). As a result, I have little skills or knowledge about them.
All the work you describe sounds more like toolmaking than woodworking to me, so it’s not something I would chase, personally. Any machinist with a lathe can make the parts you desire. But it’s the money, time and headaches I would want to avoid. There are fantastic wedged planes out there. And fantastic lightweight metallics (especially early Stanleys). I’d sooner investigate those than try to reinvent the wheel.
Sorry I’m no help.
Thanks Chris. I will know in a few years if I really love them. I considered going to wedged planes but decided to start with these. All good problems.
I will be attending the Staked Sawbench class next month. Is there possibility of connecting with other students Friday evening? or helping prep for the class Friday afternoon? I am driving from Alabama and want to maximize my immersion in the LAP universe.
I would recommend stopping at Pleasant Hill Shaker Village on your way up. Or the South Union Shaker village. Both are well worth your time.
Next time I reach out to the students I’ll also make the offer of y’all hooking up beforehand.
I bought a Veritas Power Tenon Cutter, 3/4″, to make legs for some slabs. I’ve tried it on red oak sticks I’ve cut from a log. I’ve used it on an electric drill at low speeds and higher speeds. It wants to make a spiral cut that reduces the diameter. I’ve tried adjusting the blade with the shims they provide but it hasn’t helped. Is there a skill to using this cutter? I’ve looked for clues to what I’m doing wrong on YouTube and a video you did but haven’t found a solution. I’m using red oak from a log I have. Some of it has high moisture and some is dried but that hasn’t made a difference.
It takes a lot of skill to do it right. Ed Sutton has a great tutorial here:
https://edsutton.substack.com/p/better-than-sex
Thank you. That tutorial is excellent. So the fault isn’t the tool, it’s the operator.
I’m using a taper tennon cutter and draw knifing them close… Is it right to cut a kerf around the bottom where I want the tennon to end, or should I be doing it some other way?
I don’t kerf the tenon’s shoulder, but I suppose you can. I want the tapered tenon to blend into the taper of the leg.
Is LAP going to publish John Walter’s Third Edition of Stanley Tools Guide to Identiy and Value that has been rumored to come out the past 30 years?
Nope. We talked John about it. He wanted to do it himself. And so it is on his shoulders alone – by his choice.
Responding to Mr. Hansen from last week. I have been doing woodworking with visually impaired people for the last 8 months. One on one works best. Perhaps Mr. Hansen could reach out to stick chair teachers to see if one of their former students would be willing to work one on one with Mr. Hansen to explore how to make a stick chair. It can be tremendously rewarding.
You previously described people making stick chairs as something like a mouse hole in a corner of a room in a woodworking house. How many people in the US do you estimate are building stick chairs today? It sounds like that answer is at least 400 since all of the stick chair badges are gone.
That’s probably about right. We’ve sold about 4,000 copies of the book.
Back in Nov. ’21 in a blog post about your new bevel gauge, you mentioned a 7″ blade was in the works. Is that still the case? (And thanks for doing this!)
Hi, I’m thinking of linseed oil paint for some solid pine kitchen cabinets. Is the color consistent from one batch to another from Allback? I don’t want the color to be different between the face frames and the drawer faces if I do them at different times or from different paint cans.thank you!
The traditional solution is to mix all the paints into one 5-gallon bucket to keep the color consistent. I have no idea how consistent the color is from batch to batch. But mixing everything solves that problem.
Any progress on the new distribution building?
Yup. We have a contract on a building. We close this month and will then be able to talk about it publicly.
Back around 2015 or so, you did a blog post about how you bought a Lie Nielsen #2 and made a different tote for it and said you were going to try to use it for a year instead of a block plane. Just curious how that turned out for you. And forgive me if I misquoted or got the story somewhat wrong.
It turned out to be mine, if that tells you anything 🙂
Ah. Well, then, Ms. Fitzpatrick, another query—do you use it? Or were you just determined to give it a home?
Was wondering the same thing myself. I love the size of my No 3 metallic plane and was also wondering if slightly shorter would be better. The transitional I just received is about an inch shorter than my No 3 and I’m excited about that.
Hello, I have several books and read several blogs but i have not seen what i am asking in one place but maybe i missed it. My question is, is there some type of “chairmaking addendum to the ATC tool list” or something like that? I have based my tool list around the ATC plus some machines. I want to try making some stools and later chairs, and have slowly been picking up tools from various blog posts. But would be nice to see a comprehensive list in one place for making chais and stools
My chairmaking tool kit is small. All the tools in my chest are here:
https://blog.lostartpress.com/2023/01/01/the-anarchists-tool-chest-at-age-11/
Additional tools or alternate choices are in “The Stick Chair Book.”
Can you recommend any sources for learning about glyphs or spells? I want to carve some of my own. Thank you!!
There is no big book of historical glyphs. Wish there were. My research is being done the hard way, culture by culture. Translating the native language with Google translate. Searching bibliographies.
Jogge’s new book “Karvsnitt” which comes out in English next month has a great chapter on Scandinavian ones. But there is no central resourse on pattern language that I know of.
I have a hard time finding stock thick enough for a chair seat. Whenever I google “glue up a chair seat blank” it is always about stock that is already thick enough. What if I, for instance, took four sections of 2×12, glued them into two 4x12s, then glued them together into a 4×24? (Real dimensions, 3×22.) Assuming it was glued up correctly, would that hold up for a chair seat?
It will definitely work. But any 8/4 stock is thick enough for a chair seat. Ask for 8/4 poplar or red oak – the most common and universal species in the US. Those are great for seats.
Thank you! I will give it a go at some point.
I guess I should say that it isn’t necessarily impossible for me to find 8/4 stock, but I often have a reluctance, as a hobbyist, to spend on stock that thick because it’s so pricey, at least until I someday get to the point where I can confidently tear into a 250-dollar hunk of wood without the fear of ruining it.
I am super intrigued with turning cheap lumber into amazing furniture!
Patrick, I too had trouble finding thick & wide stock near where I am even at the specialty lumber place. I glued up 2×12 stringer material, but I did them as a panel first (2×24) and then glued those panels together offset so there wasn’t a long joint all through the seat. It worked–I’m sitting on chair, and I’m 225lbs with my 6yr old on my lap–but I had a hard time flattening the panels to glue them together. I thought avoiding tenons would be be less work. It likely wasn’t.
Chris are there not enough chairs in the world already?
Let ye who is without sin cast the first stool.
Surely you meant to say: “Let ye who is without seat cast the first stool”?!?
Oooh. Better
I’m going to start making an anarchist workbench. I’ve already made a Ruobo from on of your other books (the red one, I think) in SYP, so I’m familiar with the basic process. Last spring, I picked through the 2x12s and got some good ones. I ripped them and have had them stacked and stickered since then. They’ve obviously and expectedly moved. Some of the boards for the top are going to be really pushing it to get in my target thickness of 4 3/4-5” as a result. I’m wondering your opinion on if it’s ok to have a couple of boards staggered in length throughout (think of a bowling lane)? Cutting a couple of the boards shorter would greatly reduce the amount I need to joint off and will let me have the thicker top I want. I know even going down to 4 1/2” would be more than sufficient, but I’m trying to maximize the thickness. I can reinforce the butt joints with dominos. I’d be planning on having them strategically located by flanking them on either side with full length boards and not in the main working area/where dog and holdfast holes would be. The bench is going to be oversized as well to act more as an assembly table too (target specs of 9 feet by 38” and 5” thick). I wouldn’t go crazy on the number of boards I do that with, but even a couple of them would greatly help. Is this a less-than-ideal solution that is still fine to do if appropriately accounted for? Thanks!
Cheers,
Dan
Scarf joints are a valid way to do it. I might skip the dominos and use construction screws instead (deep in the lamination).
Good luck!
Good idea. Thanks!
This spring I am planning on making a couple of replacement ledge doors for our hundred-year-old barn using the instructions in LAP’s doormaking and window-making book. Am I remembering correctly that you had at one point considered adding a section on these doors to the 2d edition of the Anarchist’s Design book, but then decided against it? Do you have any additional insights on making these doors not already covered in the doormaking book? Many thanks!
Not really. Use clenched nails because they are fun. And pay close attention which way the diagonal braces run. About half of builders do it wrong.
Any plans or designs out there for vernacular beds? Is there a good text in existence covering that subject?
Most vernacular beds are built-ins. Or are rope beds. I don’t know of any books on the subject. I have a couple favorites from Ireland I should post. (Making a note now.) They are beautiful, but you might not be able to move them.
Other vernacular beds are basically a box filled with bedclothes.
I don’t know of any books on the topic. But Victor Chinnery and Chris Gilbert have both dealt with these beds in their books on English furniture. Worth checking out their books from the library.
Thanks Chris! I know mattresses are a modern luxury so I was thinking info may be fairly limited or non existent. I’d like to tackle beds from a mostly hand tool perspective, looking forward to the Irish examples.
Plans or measured drawings of the Jonathan Fisher secretary and the card table? Also it would be a cool vid or article on how to do the fake wood grain. Also one time in the blog you mentioned the smoke finish were they used candle smoke.
This question would be great for the author, Joshua Klein. They make videos all the time. So please let him know your enthusiasm!
Will do Chris thank you
My neighbor just (very unfortunately) cut down two mature live oaks, and I grabbed a few big pieces to try to save them from the chipper and to try my hand at green woodworking. I can’t seem to find much info about working live oak. Do you have any experience?
I love live oak. It loves to split as it dries, so paint the ends ASAP. It is almost as difficult to work as black locust. It is GREAT for mallets and making warships. But other than that….
I was inspired after reading the ATC and Campaign Furniture to build a smaller 1:2 size travelling ATC out of sapele with some vintage corner brasses i found on Etsy. Its slow going (all hand tools), but the bottom skirt is now done!
If this goes well i want to make the campaign dresser from the book. I like your point about avoiding a panel glue up for this. Would you recommend using a sapele slab if i can’t find 18″ wide sapele. Are slabs of sapele even a thing? Thanks!
Sure! You can find really wide African species that are very mahogany-like. And it will look FANTASTIC.
I would like to make a stool using construction lumber, 2×4, lumber. If I laminate several pieces for the seat, what do I need to be aware of in order for the saddling of the seat to turn out ok (will a scorp work ok on pine)? I would like to rive some 2×4 material for the three legs; what issues can I expect with this.
With the seat, make sure the grain runs the same direction in all the boards. You can scorp/travish almost anything.
With the 2×4 material, use Doug fir or yellow pine. It’s stronger than white pine.
You will learn SO MUCH by attempting this project! Have fun!
Chris, What is your aversion to rocking chairs? Please do not cast me out of the LAP world
Ralph
Mostly it’s just a joke.
My interest is in Welsh, Scottish and Irish chairs. And rocking chairs are a VERY American thing.
We own one! (From Greg Pennington). It’s very nice and I enjoy it.
So don’t make too much of anything I say i don’t like as far as furniture forms go. It’s just smack talk. Like the way Follansbee insults my campaign chests….
Hi there –
I really appreciate the depth of research that you’ve put into your work – the mash up of academic curiosity + applied skills is awesome.
Could you point us in the direction of /the/ book or website you would consider to be a good, holistic primer of furniture styles and forms? I’m looking for something that I can use as a jumping off point to anchor from in order to build my understanding of different styles and eras of furniture – both vernacular as well as “high style”.
Cheers!
I know of no comprehensive book on styles. It’s just too much information to cover in one book. It would be an encyclopedia. I have a whole library with about 50 percent of the books on styles. And it is still very lacking.
My advice is to pick a country and start there. You can probably do the U.S. with about 15 or 20 books as a good start.
The Wallace Nutting books (Furniture Treasury) are a good place to start with the early stuff. Then get the American Antiques series from Highland House. One of Evans’s books on Windsors. That will get you up to 1800.
Perhaps someone else has an ombibus book suggestion. Sorry.
Thanks – I guess in the context of a full on encyclopedia, I’m looking for the “book of contents”. Seems like an interesting project…
Thanks!
A few more questions to fill your queue:
1) Radial arm saws – after lots of research, I don’t think they’re anymore dangerous than a table saw. Any experience using them?
2) Pure Tung Oil – worth the effort and time?
Thanks!
Radial-harm saws? Yes. I started on them. My father and grandfather both had them. Every cut is a climb cut toward you. It’s like the blade is chasing your fingers to cut them off. And ripping is inaacuate at best. They don’t hold 90° or 45° worth a crap. Dust collection is shit.
But other than that…. they’re cheap.
Tung oil is fine, like all the drying oils. I like linseed oil because that’s what I grew up with and am very familiar with every property it has.
Is there a good reason not to use tapered tenons in the sticks of a chair? I’m starting up my chair building kit and wondering if I can get away with just a 5/8” tapered tenon cutter to start for all the joints (it’s a six-stick combback).
It seems like a lot of unnecessary and fussy work to get the holes reamed right for all the small joints. A 5/8″ tenon/plug cutter is cheap as chips. Lee Valley makes nice ones.
Makes sense; thank you. Could I stick with 5/8” cylindrical tenons only for the sticks, or are the 1/2 tenons specified in the book advantageous?
5/8″ is fine!
Thanks again. You’re the best!
Hello Chris.
I know this guy — let’s call him “Paul”. Well, Paul made a stick chair out of ash and then finished it with Katherine’s soft wax. But he’s not crazy about the washed out color of the ash and there is a repaired crack in the seat he cannot unsee.
Is there any easy Paul can strip the wax and paint it with either milk or linseed paint?
Appreciate any input you can offer.
Paul
Have your brother wipe down the chair with mineral spirits. That will remove the wax and oil. And you will be ready to go.
Chris
In one of the sharpening videos you mentioned that you stopped using Shapton glass stones. Why did you change water stones?
I Use Shapton Pros, or Kuromaku stones. The glass stones are too little abrasive for the money. And they are all the same color, which can cause mistakes.
Hi Chris,
Will the Softwax 2.0 work as a finish for a workbench?
Thanks.
Rob
Sure. But it would be cheaper and just as well to use Boiled Linseed oil. The wax adds a little slipperiness that I would rather not have on a bench.
How do you do the “shoulder” of your chair dowels and legs, i.e. that transition between the octagon and the tenon/plug cutter? Thanks for giving us your Saturday.
—Claus
If you are asking about a cove detail, that is cut on the lathe. When I do it without a lathe, the octagon flows into the tenons. The shoulder is not visible, but you can feel it.
Thanks for the gift of an AMA! Love the new Peasant pieces.
Seat 2-1/2” thick, legs started as 1-5/8” octagons. Roughed out tenon to cylindrical with 1” Veritas Power Tenon Cutter to fit into 5/8” Veritas Tapered Tenon Cutter that cuts a max of 1-1/8”. Mortise pilot 5/8” for Lee Valley large Standard Taper Reamer (3/16″ to 1 3/16″). Problem: plenty strong but gap underneath—mortise is wider than 1”. Question: any suggested solutions I didn’t see? (1) don’t flip the chair over to look. (2) make longer 5/8” tenons ending over 1” on a lathe that I don’t have. (3) what I did on my next piece—bored 3/8” pilot and lengthened the 5/8”-ended tenon with 3/8” Veritas Tapered Tenon Cutter.
In thick seats, the reamer makes a hole that is too much for the tenon cutter – as you have discovered.
In those cases I drill 5/8″ through the seat. Then ream until the mortise is 1-1/8″ in diameter. Then cut the tenon. You might have a stub at the end of the tenon that looks like a 5/8″ dowel for a bit, but everything will work.
Also, your joint is probably fine as-is. Fill the gap with glitter and epoxy.
Peals of laughter from my ladies; they love glitter. “Finally, woodworkers are allowing glitter to see the light of day!” Me: thanks for nuthin’ 😉
So, artist-engineer says, “glitter will strengthen the epoxy” and other artist says, “you’ve never seen a unicorn fall, now have you?”. Survey says Chris is correct! Srsly, thanks for the fix—that geometry of mortise and tenon will work well structurally and visually.
Hi Chris! I have a newbie question. I have a problem with wood grain that shows up mostly when drilling holes. I use an awl to mark where I want the hole. In doing this I find that as I press down on the awl, it will sometimes drift a bit. The grain in the wood seems to have harder parts and softer parts. As I press down, the point of the awl will not go into the hard part, but drifts toward the soft part. I want a fairly substantial hole because the drill will also tend to drift if I don’t give it a good place to start. This is frustrating because the hole does not end up where I want it to be. I do not own a drill press, I just work with hand tools for the most part.
A centerpunch will usually ignore grain density. Also, a birdcage awl allows you to steer the hole as you twist it because it cuts a divot.
If you could only build 1 thing forever starting tomorrow, what is it?
Stick chairs. There’s enough variation there to keep me going for decades.
Hi Chris, thank you so much for all that you have given and continue to give to the community.
I’m planning to build a trestle dining table. The 8/4 horizontal top battens and feet being open tenoned and drawbore pinned (not sure how else to describe this joint) to 12/4 vertical legs. Would a tapered dovetail housing joint, as described in The Woodworker pp. 1085-1095, be a wise choice in attaching the top to the undercarriage? I’m unsure about the fact that only one side would be cut at an angle, although makes this operation a bit easier. Am I planning my own misery – would you suggest a better way not involving screws to achieve this task?
Thanks again!!
Benjamin
That is one way to do it. And it would be a fun joint to cut. It’s what I use with my worktable in the Design book.
Curious as to your aversion to screws and buttons. A great way to do it and be able to remove the top to refinish it. Or to make repairs to the base.
The other historically correct method is 6d rosehead nails. Through the top and into the base. The nails bend to accommodate wood movement. Looks cool. Might be too rustic.
I’ve also made threaded wood screws that pass through the base and into the top.
I am overcome with the woodworking equivalent of writer’s block every time I attempt to start a piece with coopered doors. Any suggestions?
I have never made one! The Krenov School people are the experts. Might follow some of them on IG and then pick their brains. Or take a coopering/bucket course.
When your daughters start having your grandchildren, you think you might make one more Anarchist title: “The Anarchists Toy Box”?
Would be funny!
Good Afternoon Chris,
Thanks for taking the time out of your day to answer questions again today. I know that you’re currently using a Record 043 as a plow plane, but I wanted to see if you had any experience with, or would recommend, the Veritas Small Plow Plane (I’m referring to their original plow and not the new Box Maker’s version)?
Thanks again,
Jacob
I do. The depth stop slipped a lot. I believe they have addressed that. And sometimes the brass nuts on the fence lock up (Veritas may have remedied this as well). But it’s a good tool.
What is the “right” way to round over the edges and corners of a chunk of wood? I have a little cornering plane that is nearly useless, I have an s-shaped kinda drawknife with oval holes, sharpened on the inside, that works okay, often, and I have used my random orbit sander or a sanding sponge to round over edges. I’m tired of pulling up a big splinter or doing the sanding routine, and I am pretty sure a tiny round-over bit in the router would work great, but is a lot of work to set up.
If you only want to take off hard edges, a block plane or #4 works perfectly.
Block plane. Sandpaper glued to a block of wood (creates a nice bevel). At times a burnisher works.
Hi, I made your limonene/beeswax/linseed finish from your recipe… it goes on well w/ a furniture pad and looks good. I was expecting a consistency like vaseline but it came out more solid; it feels like oily candle wax. Did I overshoot the temperature or is there expected variation in the product based on the specific wax or oil I use?
Thank you for being such a consistently invaluable and down to earth resource!
Small variations in the solvent can make the product firm or loose. Add a little more solvent (and remelt it if you like) and you will get something more like peanut butter.
What’s your thoughts of a Gibson type chair with a little less back slant for dining chairs? I am fixing to build my wife a Walnut dining table and 2 benches with 2 chairs for the ends of the table?
There were variants on Gibsons that I examined in Ireland, including side chairs. So go for it.
I bought a couple of vintage Stanley 2′ rulers. Two questions: 1) Some of the joints are loose – can I just take a punch and peen them to tighten them up or is there a better way? 2) What’s a good, nondestructive way to remove some of the grime from the faces.
Hi Chris, I am making 6 dinning chairs and want to get a handsaw to cut the curve in the seats. The seat will be 7 quarters hard maple – will the blue spruce ultimate coping saw be able to handle cutting through this well? I could not find the recommended thickness range for this saw. Is a bow saw better for this operation?
Definitely a bowsaw. Gramercy sells a nice kit: https://toolsforworkingwood.com/store/item/GT-BOWS.XX/+Gramercy+Tools+Bow+Saw+Kit