
If I ever write a book on finishing, I’ll probably call it “Farting Around With Finishes.”
One of the things I like to do on a Sunday afternoon is mess around with dumb ideas. About 100 percent of the time, my results are ugly or unremarkable. But every once in a while I discover something interesting that eludes the rounding error of “about 100 percent.”
One of the things I love about old vernacular pieces are the (rare) unrestored finishes. The best of them have a dark and mellow glow that verges on black. They have a low luster, but it’s nothing like dried linseed oil, which can look flat and starved.
After talking to experts on furniture and finishing, I’ve concluded that many of these finishes are the result of soot from the hearth (consider what coal soot did to the buildings of the U.K.). And the shine? Burnishing from use and the natural oils from the body of the sitter. There also could be waxes. Grease from food. Soil from clothing. Water damage. Children. And on and on.
(The original finish on these pieces could have been anything from nothing/nekkid, to an oil, a linseed-oil paint or a wax. These made-at-home pieces were unlikely to have a fancy film finish applied by the builder, though anything could have happened to the piece in the 20th century.)
Last fall I took a trip to Europe to travel around with Chair Chatters™ Klaus Skrudland and Rudy Everts. We drank a lot of Belgian ale and talked non-stop about chairs for about a week. Near the end of the trip as we were driving back to Munich, I wondered aloud if it would be possible to create a finish that would somewhat mimic old finishes on vernacular pieces (without dangerous chemicals or a 32-step process).
I had a dumb idea. Perhaps the finish could be based on a plant oil that is similar to sebum, the oil and waxes made by our sebaceous glands to keep our skin moisturized. As it turns out, jojoba oil is similar to sebum. (There is synthetic sebum out there, but the sources I have found are too expensive to use as a furniture finish.)
Jojoba is inexpensive, widely available and edible (but not digestible). Like linseed oil, jojoba is a drying oil. It is combustible, and there is a small risk of it auto-igniting if you foolishly bunch up your rags. So take the same precautions as with all drying oils and dispose of the rags as recommended on the oil’s Safety Data Sheet.
So jojoba is indeed a good candidate for a wood finish.
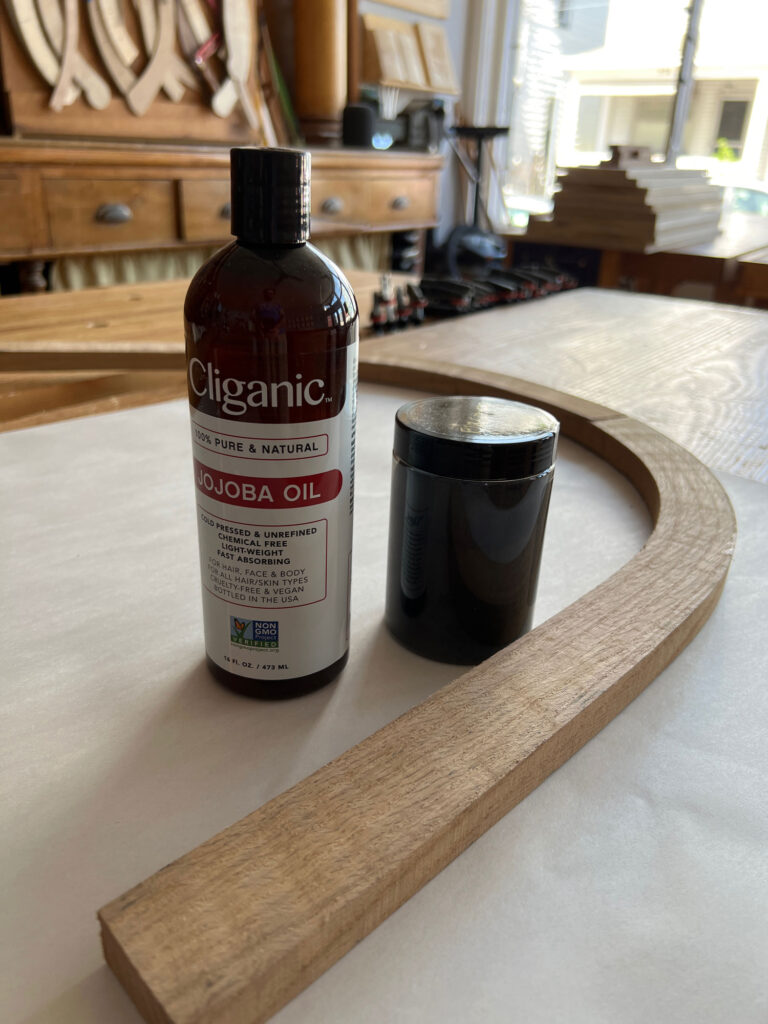
The next hurdle was how to get the hearth smoke into the finish. My first thought was to grind up lump charcoal or simply get some ashes from the fireplace and mix it into the jojoba. My experiments with those sources didn’t go well. The finish felt really gritty.
The solution was to switch to carbon black. Carbon black is essentially soot that is used as a pigment in inks and paints, and to color the rubber in your tires. It’s cheap, and you can get it as an extremely fine and consistent powder.
So what happens when you mix together jojoba oil and carbon black? I started with 1 ounce of jojoba oil and mixed in 1/2 teaspoon of carbon black. I stirred it with a popsicle stick and within a few seconds the carbon black was evenly distributed in the oil.
Then I ragged it on a scrap white oak chair arm that has been hanging around my shop for a year.
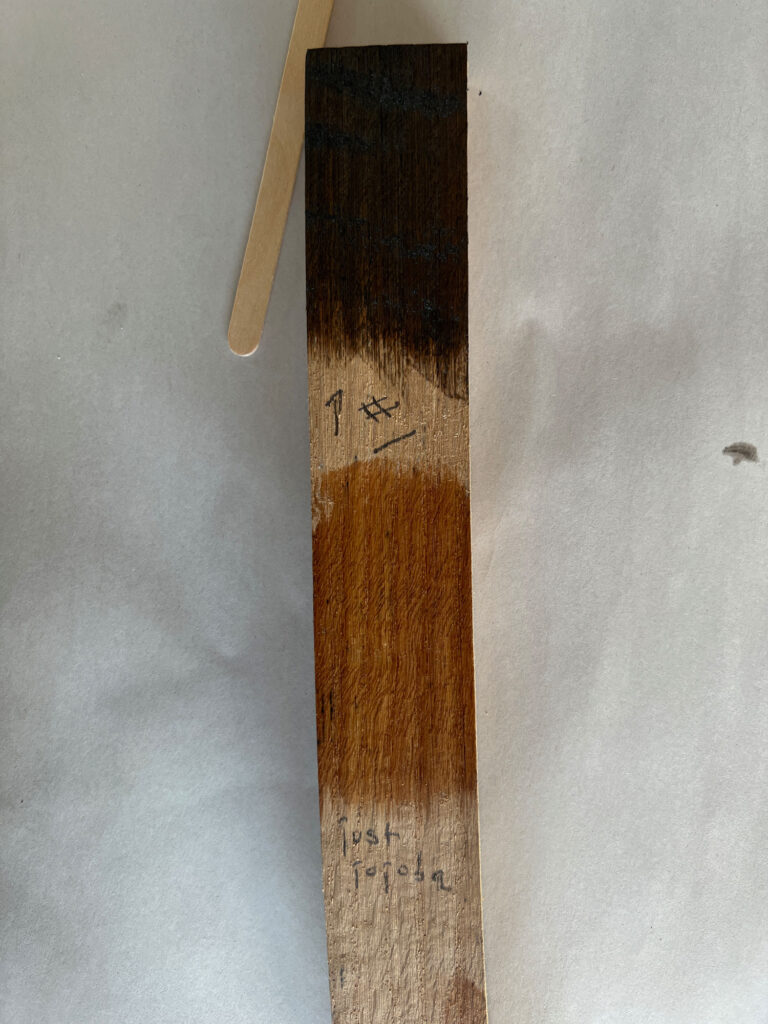
Surprisingly, it looked pretty good. The oil gave the wood an orange color, and the carbon acted like a pigment stain – collecting in the wood’s pores and sitting on top of the wood. I let the finish dry for a couple hours then checked it again.
The downside is that the carbon black rubs off on your clothes a bit. After the oil dried to the touch, I rubbed it quite a bit with clean, dry rags. The finish on the wood didn’t get any lighter, but I continued to get some carbon black on the rags. (Though it was less and less the more I rubbed.)
So next, I’m going to reduce the amount of carbon black in the mixture and see what happens. And I’ll try adding a spit coat of shellac to the sample boards to see if it locks in the black color. Third option: cook up some soft wax with jojoba, beeswax and some carbon black.
All this might be a dead end, but I enjoy the process (and I hope that maybe Lucy will get me a lab coat for Christmas – ooooh, and a clipboard).
— Christopher Schwarz
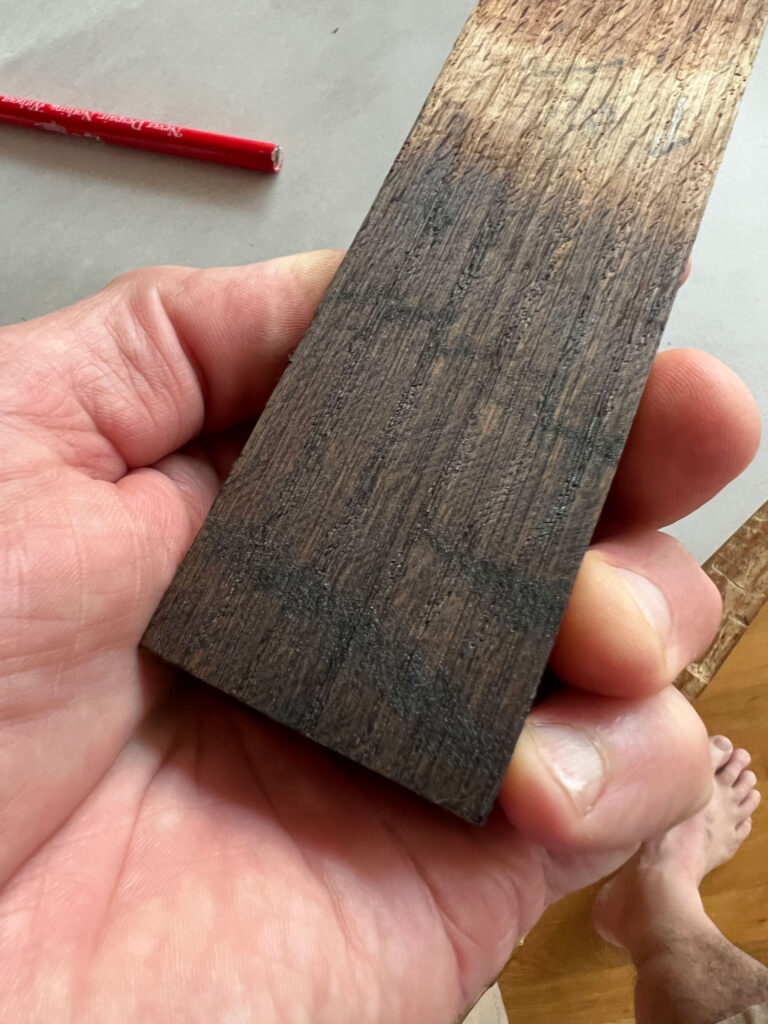
I was unaware that jojoba is a drying oil. What precautions should I be taking with my wookie, which is saturated with jojoba?
The risk is tiny. I have never had a rag soaked with jojoba even heat up a bit. And I have been using it for more than a decade.
So maybe don’t crumple it up and throw it into a pool of gasoline?
Oh crap. I’ve been using the Paul Sellers “oil rag in a can” thing (bit cleaner/neater to handle than your oil rag in a bag, Chris) but now realize it’s mostly soaked with jojoba oil. That’s a wookie-like rag tightly wound into a spiral and stuffed into an old 8oz tomato sauce can, with the end of it sticking out so you can lube things like irons by grabbing the can like a big crayon and rubbing the cloth “tip” onto the surface. Now I am going to lose sleep over it, so I am going to have to start storing it in a metal bucker and lid.
Vinegar and fine steel wool results in an appealing ‘stain’ as well; like tea, the longer it sits and the more steel Wool, the darker. Used it on a small bookstand made from pallet wood boards, and it came out surprisingly well. Doesn’t look like fake stain.
Will give the carbon black method a try as well.
Hmm, i may try mixing some jojoba oil and Van Dyck crystals for a project, thanks for the idea. If it doesn’t work i’ll use it to get rid of my grey hairs.
I really like these kinds of posts; being curious and deconstructing stuff to make something new or rediscovered happen. Thanks for sharing it, bumps and all, out in the open.
I once lived in Columbus, Ohio, where a lot of older homes had very chunky trim, stair parts, and doors with that ancient super dark look to them. In my time, all were natural gas heated … but I imagine it was probably coal at one time.
In Cleveland (close to home), there is an Old Stone Church, which is both name and description, on the Public Square. Used to be black. They cleaned it, to the natural light grey of the stone (sandstone, I do believe). The church was prettier with the black soot of tens of thousands of heats of iron and steel. I like your “aged” from a prior age finish idea.
Wood is mostly just carbon. Carbon black is carbon. Seems like there should be some chemical that would bind them together. Then add your jojoba oil.
Turns out you should be using biochar. Both are used in black ink by printers. You have lots of books printed on wood/paper. https://scholarworks.rit.edu/cgi/viewcontent.cgi?article=11283&context=theses
interesting idea. i’ll try this with a rubout using wet/dry sandpaper. drives the pigmented oil slurry into wood pores, lightens edges & darkens recesses. 280 to 350 grit gets a nice feeling surface . I think.
Random observations:
Thanks for the reminder that jojoba us a drying oil.
Graphite powder might be an alternative to carbon black.
Both graphite powder and carbon black can be used to lift fingerprints.
Carbon black was one of the traditional pigments for milk paints, along with iron and copper oxides. Not sure I’ve seen it in a transparent finish before. Now I’m wondering what an iron oxide version of your experiment would look like.
Appears that you are reinventing lithographic ink which consists of: Raw Materials % by weight Pigment 23.00 Bodied Linseed Oil (20 Poise) 41.00 Phthalic Alkyd Resin 10.00 Phenolic Modified Penta Ester of Rosin 15.00 Polyethylene Wax (And/or Modified with Microcrystalline Wax) 3.00 Petroleum Distillate (C12-C16 Range, IBP=535F) 5.00 Cobalt and or Manganese Drier
I knew the comments would make my brain hurt.
Translated from chemistry speak, that recipe is basically 23% pigment, 5% Cobalt or Manganese drier, with the rest being an oil or wax carrier. I suspect the proportions of the oils and waxes are mainly there to regulate drying time and final texture/sheen. Since you see’m to be happy with jojoba as the carrier, you don’t need to worry about percent oil vs wax vs alkyd resin. Also, for what it’s worth (or not), I used to formulate epoxy for the construction industry during a summer job in college. Some of it was colored with carbon black. My memory is that it was about 0.5%-1% carbon black by weight as the colorant. That percent may not work for staining chairs, but the general rule would be that a little carbon black goes a long way.
I like the direction this thread could go.
Sign me up for the “Farting Around With Finishes”. I’d like a signed copy, in exchange for binding one for you in leather with gold titling!
As for the carbon black, I happen to have some for the exact reason of tinting kozo repairs for older books when certain dyes just won’t come out right. If it’s a case where they are too bright or lack a depth, carbon black and sun exposure can balance the tinted Japanese paper (kozo) to where I need it.
Last thought. What if you did it in two steps? I use canning paraffin to seal the end grain of wood I’m drying. I use a clothing iron set on low to melt drops off the paraffin and then I iron it into the wood as it cools quickly and hardens upon contact. So melt paraffin at a low temperature, add just enough to give it the semitransparent look you want, apply it to the wood with a brush, iron it in, and rub off the excess with a rough cotton rag. Step 2 is to find what looks good over that, bees wax or jojoba oil. Over time both should dissolve into the paraffin.
When I was a lad, which was a long time ago, I lived in rural England. My aged great aunts lived nearby in houses without any piped utilities. Such houses typically did not have open coal or wood fires but had ‘ranges’ cast iron Aga like stoves which were used for heating and cooking. They hardly smoked. However, lighting was typically provided by candles and oil lamps. Both of these could produce an oily soot. The walls and ceilings of the houses were often a dingy brown which was difficult to clean because of the nature of the deposit. Candle soot is easily obtained from holding a cold object over a candle. It is likely that tallow candles would be traditional.
Good thought on candles as being part of the coloration!
Aga stoves were an early 20th century addition to homes. Before then, open hearth cooking was the dominant form from 1600 to the end of the 19th century, when wall stoves and boilers were everywhere. (At least according to my reading.)
And in Ireland, many rural homes went without chimneys as a way to preserve heat, so smoke was an even bigger problem there.
One hundred years or so ago, ceilings got dingy fast from heating, cooking, and lighting with all manner of burned things. Painting over the sludge was impractical, so they used calcimine — a mix of calcium carbonate, glue, and water. It made a handy whitewash that could be renewed often.
But it’s horrible to paint over. They make special calcimine coater paints, but they don’t work well. They reactivate they glue in the calcimine and peel off in short order. I hate calcimine.
Very interesting topic indeed. I must think of the Mackingtosh furniture which is almost black and the oak shines orange where the black is gone.
On early nighnteenth century mahagony wax was mixed with Bitumen (Right English?) (Bitume de Judee in French) which gives the wood more liveliness.
a coat of clear laquer will lock it in. smoke from a torch was used for the soot for an effect in old custom car and bike paint jobs, then cleared.
One of the Mohawk powder stains likely will get you there. They include black but others such as burnt umber or raw umber might be closer to your desired outcome. Or try Tints All products like #11 lamp black or one of the umbers.
Any that were covered by sheep skins could have picked up lanolin which is from their sebaceous glands and secreted for water proofing their wool. Perhaps one form of the dark patina is just normal dust mixed in with the lanolin? Seems like any oily/waxy substance mixed with anything that turns dark in the substance will do. Just add either ignoring any of the clothes staining effects or 200 years to dry adequately and Bob’s yer uncle. The combinations would vary by region and time. Fun sleuthing all the variations but that isn’t chair building. Sherlock Holmes and the case of the stick chair patina.
Re: “Third option: cook up some soft wax with jojoba, beeswax and some carbon black.” I’m sure you’re going to try that, let us know.
Isn’t that FUN!
I had the opportunity to re-finish a Mahogany Veneered Duncan Phyfe table from the early Thirties and looked for what they might have used for a dark stain during that period; that was a two month experiment in patience in itself.
My first hint was a discussion on walnut shells contained in Roubo’s “With All the Precision Possible” which subsequently lead me to “Van Dyck’s Crystals” carried by Tools for Working Wood.
Long story short, the dark simi-transparency of the stain was perfect, the Client loved it and regardless of my periodic panic getting to the end I had a ball experimenting and Learning.
Pease, Love, Dove
I’ve had good results using tea followed by steel wool dissolved in vinegar.
Carbon black serves as more than a color pigment in tires. It actually bonds and reinforces during the vulcanization process. Another side benefit is that being conductive it allows the static built up to drain quickly. As many have noticed over the last couple of decades they are getting a static shock more often when they touch the door handle to exit the car. This is due to the advent of the “green” tire. No that does not mean it is biodegradable but that the rubber compound used has less rolling resistance and hence assists in better gas mileage. This is due to using higher percentages of silica compounds in the “green” tire. The silica compounds are not conductive
Locking in the pigment with shellac sounds like a promising idea.
Think about the oils in lotions some apply to there skin. I have a hard wood butcher block table top with no finish at all. My seating area has developed a rich dark brownish color from nothing but my forearms and elbows, of which I use lotion on daily. I also use high end oils in my beard and put the residual on my elbows after beard application. I’d be happy to give you more details of the specific oils if you think it would help?
If i Recall, there is a bit about making a black finish with boiled oak shavings on the English Woodworker. Think its the side table video.
Yes its in the side table series
https://www.theenglishwoodworker.com/the-side-table-bridle-guides/
Basically the above mentioned steel wool dissolved in vinegar, combined with oak tea (oak shavings boiled in water), somebody above mentioned using tea instead, which would also be a source of the tannins. It looks really good, (and the table is a great little project)!
some of my old wooden planes are black from tallow. I know they used tallow as a lubricant on their planes, but I can’t imagine that their hands ever got very clean plus all the soot would over time make a great finish on the wood.
Here in Finland that black stuff is called “Kimrööki” (a loan word from Swedish “Kimrök”). Kimröök’s production had first developed in southern Ostrobothnia in connection with tar burning (an old side industry of agriculture): https://coloriasto.blogspot.com/2010/08/raimo-hieta-kimrooki-eras-vanha.html
i tried something similar: used Lockwood dyes from TFWW mixed in with hardware store BLO. it worked ok but the dye did not dissolve as well as i would have liked. got much better results mixing the dye with straight water or alcohol and applying the dye first then the BLO after.
My grandparent’s farmhouse (built early 1700s) had a huge fireplace. kept burning 24/7 for three seasons. In forunt of it was a seat, that was simply a section of log sized to sit on the end. Generations of smoke, soot and butts had darkened and polished the log to perfect, deep, glossy black. All of the corners, cracks and edges were worn smooth.
Nearby was a daybed and a stick captain’s chair, that were similarly polished, but less darkened. Everything in that kitchen smelled of faintly of woodsmoke, and was more or less darkened from the constant exposure.
If you haven’t already, check out Epic Upcyling. He uses stain then knocks it back by sanding then uses black wax.
He shows how he does everything in a stand-alone video, but he does it in almost every vid.
Very interesting. Gonna follow this experiment closely.
Fine Woodworking Magazine has a nice series on pigments and dyes that would help with your experimentation. https://www.finewoodworking.com/2022/05/13/wood-dyes-vs-wood-stains