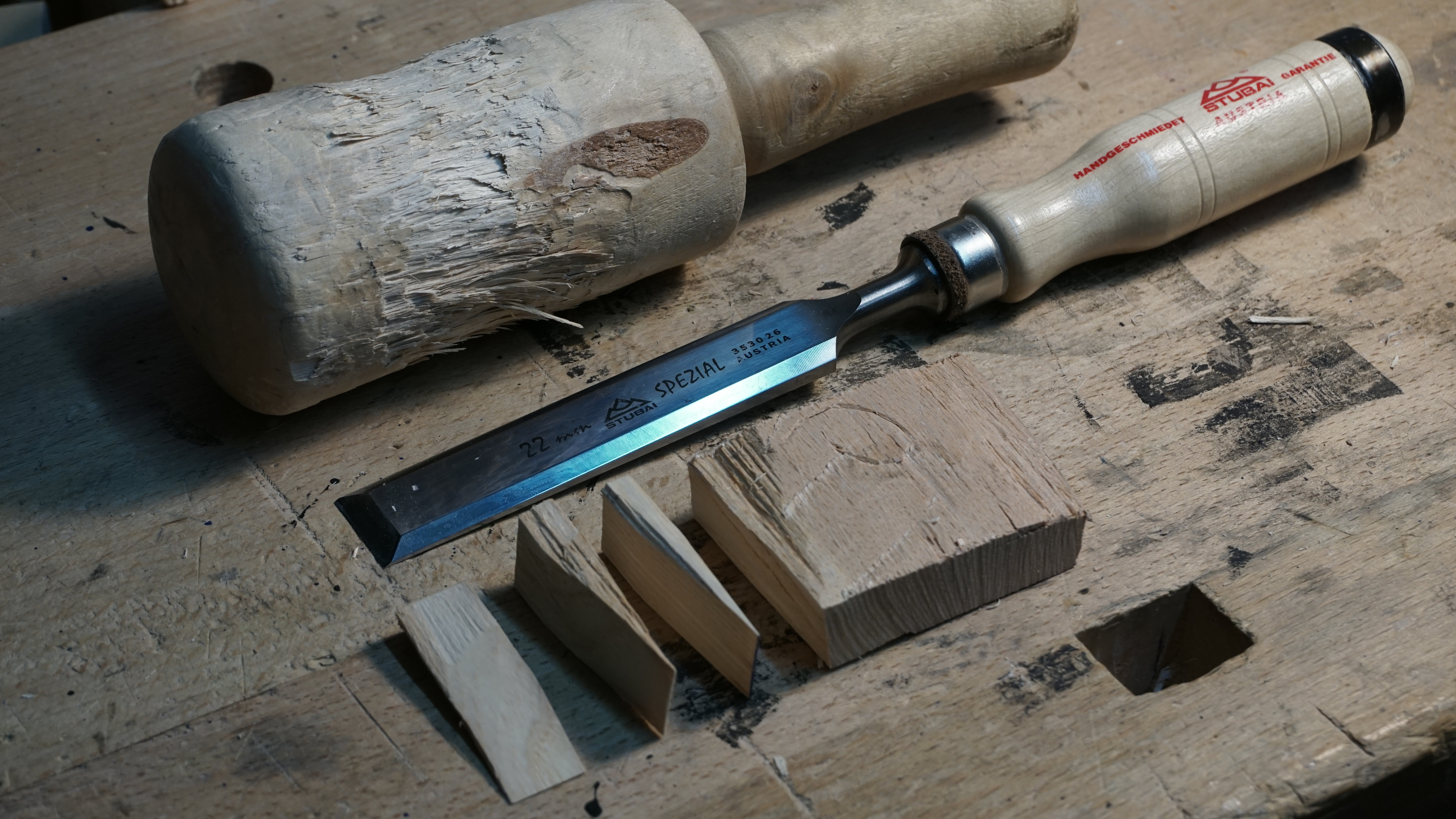
Not everybody who has to make wedges owns a band saw. In the third instalment we take a look at how to make them without power tools.
See the first and second instalments of the series here and here.
Making wedges without a band saw is not any more difficult than with a band saw. In fact it might even be easier. Especially if you don’t own a band saw.
You will need a chisel and a block of wood that you clamp in your vise.
Making wedges with a chisel
Select a suitable piece of wedge-wood. I usually use oak, as this is abundant where I live, but you can also use hickory or ash if that is available to you. Make sure you use dry wood; you don’t want your wedges to shrink after installing them.
The final size of the wedge is approximately 1-1/2’’long, 5/8’’ wide, and 3/16’’ at the thick end. I start with a board of around 5/8’’ thick, sawed to the length of the wedge (1-1/2’’ to 2’’).
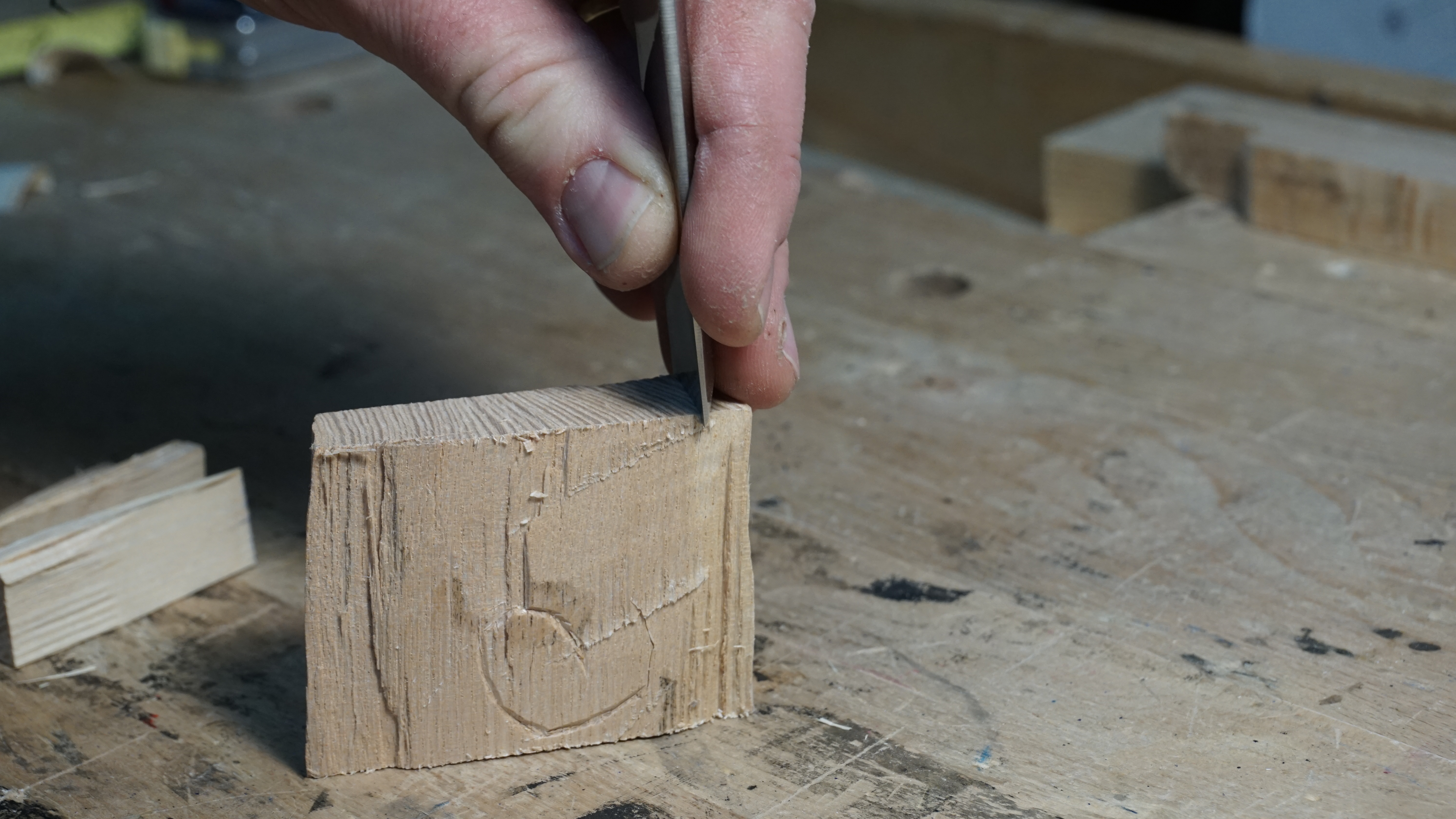
Stand the board upright on top of your workbench (use a piece of scrap wood if you are afraid of damaging your workbench) and split the piece into 1/4’’ billets. These are your (slightly oversized) wedge blanks.
For shaping the wedges, you will need to make a simple block with a notch sawn out of it. You rest the wedge against this block when you shape it with a chisel.
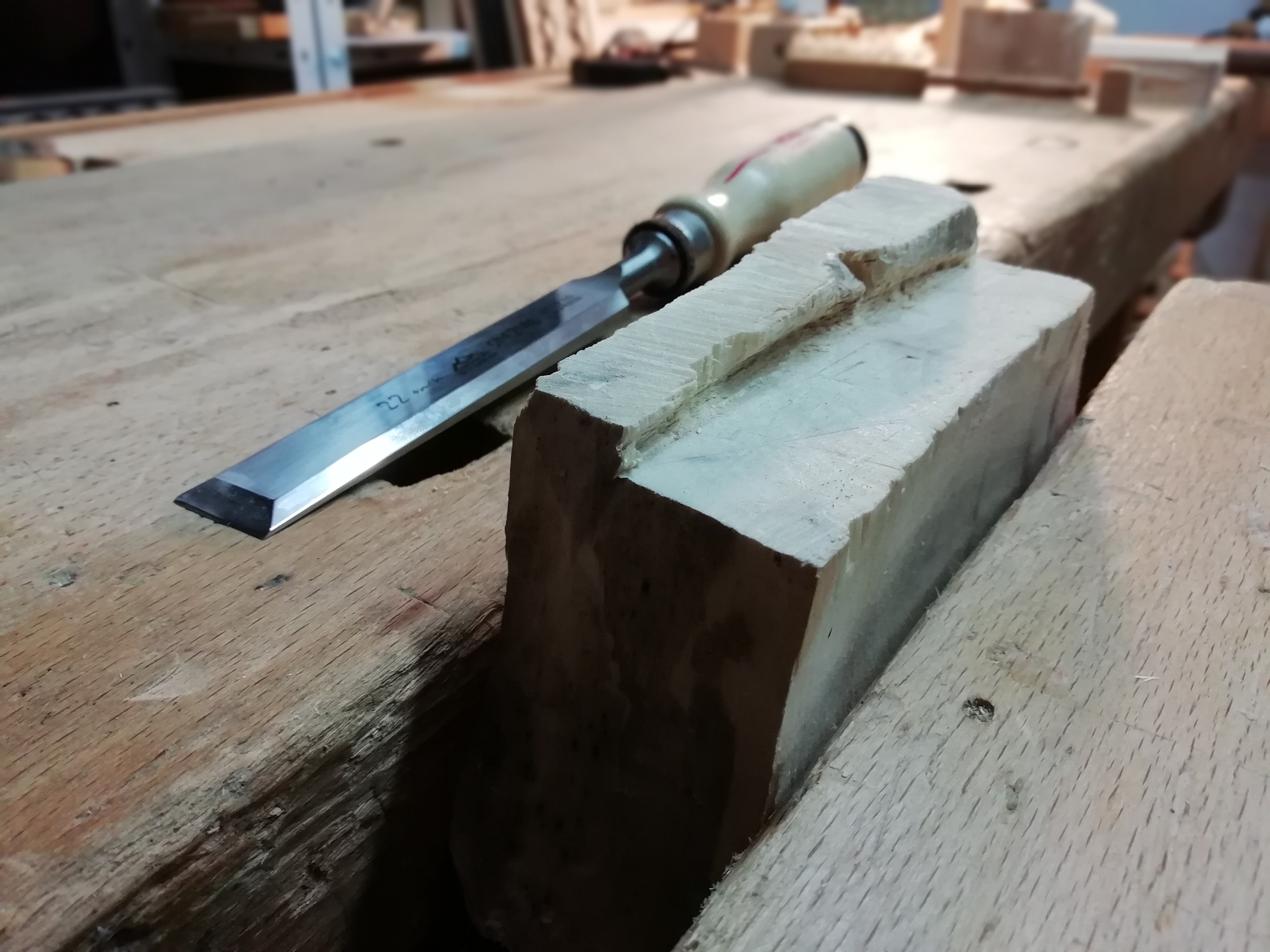
Secure your wood block in your vise and lay the wedge blank flat on it.
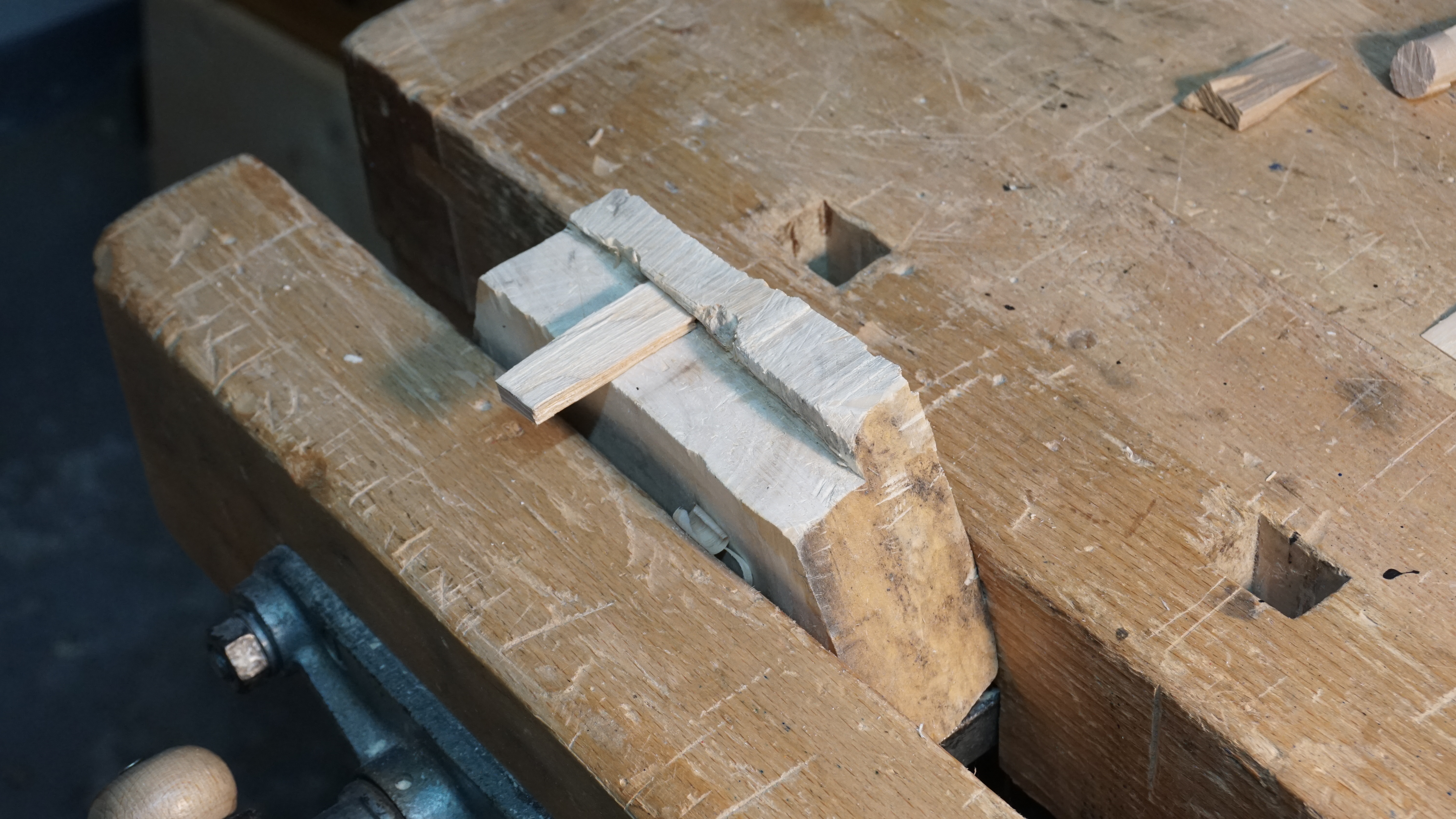
Use tapering cuts to make the wedge shape. I don’t use a mallet for this step. First, start a cut near the tip of the wedge (closest to the block). Then move slightly away from the tip and make another cut. The third stroke starts around the middle of the wedge and last stroke near the end of the wedge.
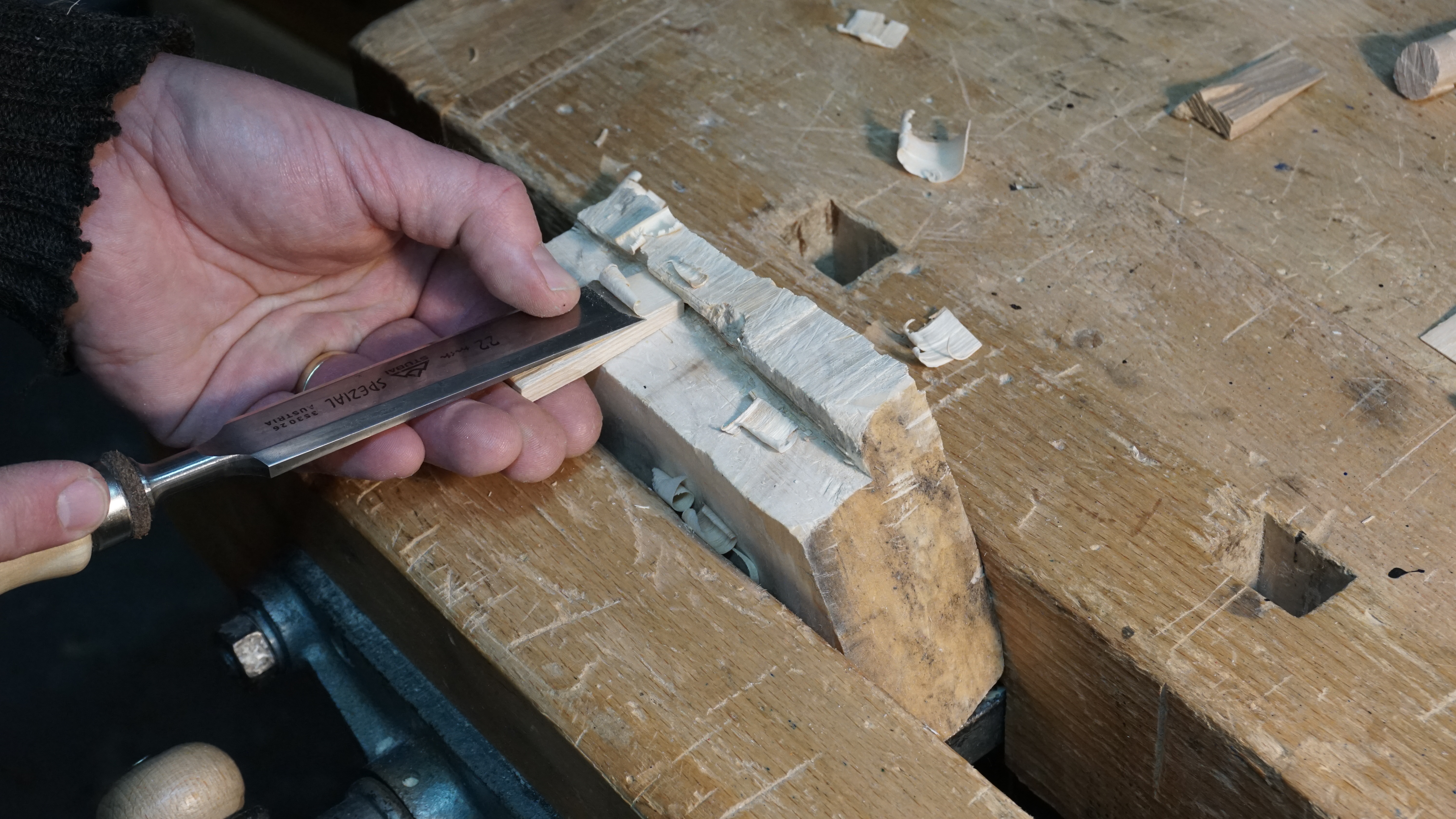
Turn the wedge over and make the same tapering cuts on the other side. It takes about two times on each side to make a wedge, depending on how much material you take off. Better to take it slowly if you’re a beginner.
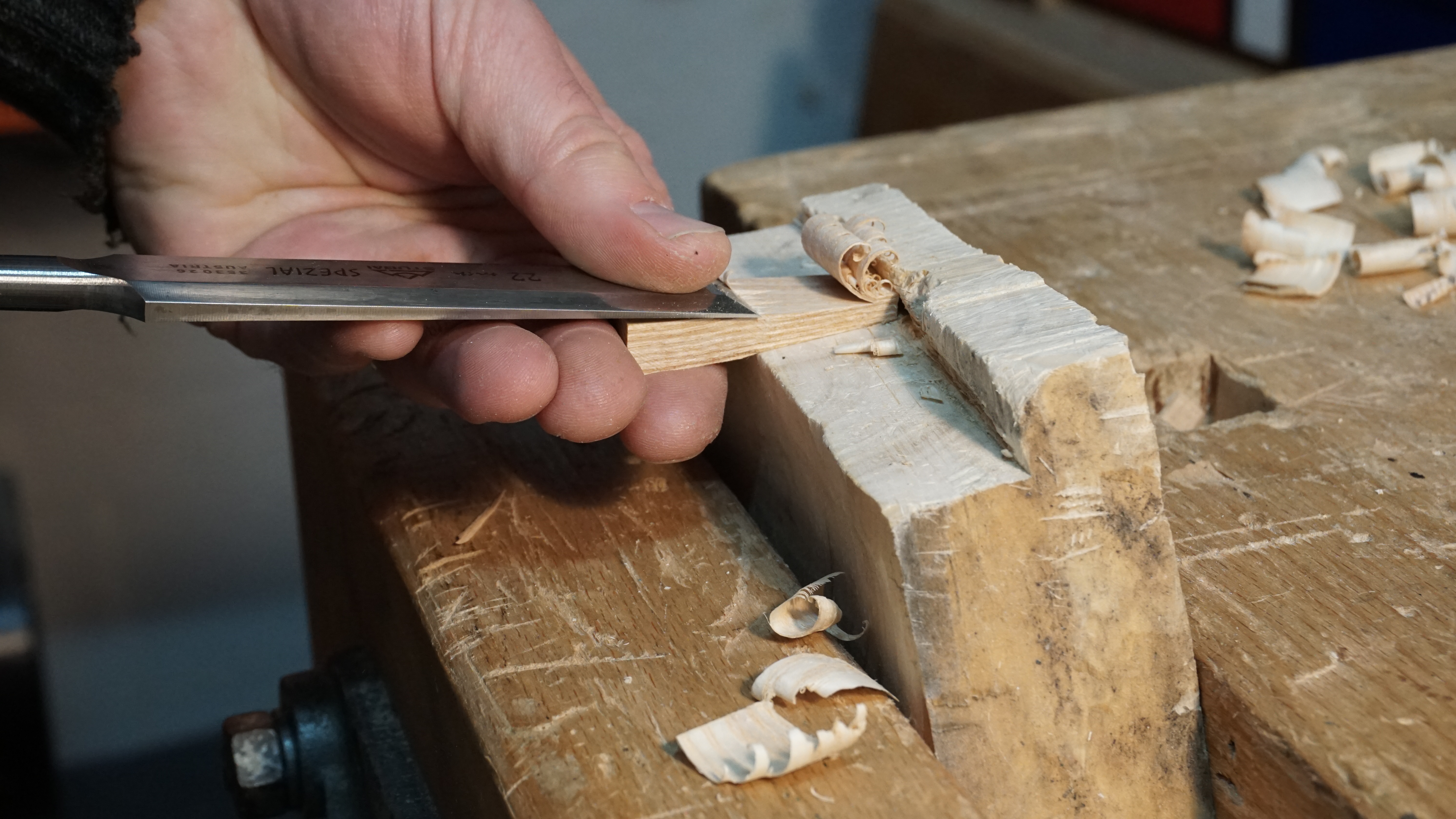
I usually make a bunch of wedges rather than making just enough for one project. Even if you don’t make that many pieces of furniture, it is nice to have some extra wedges on hand.
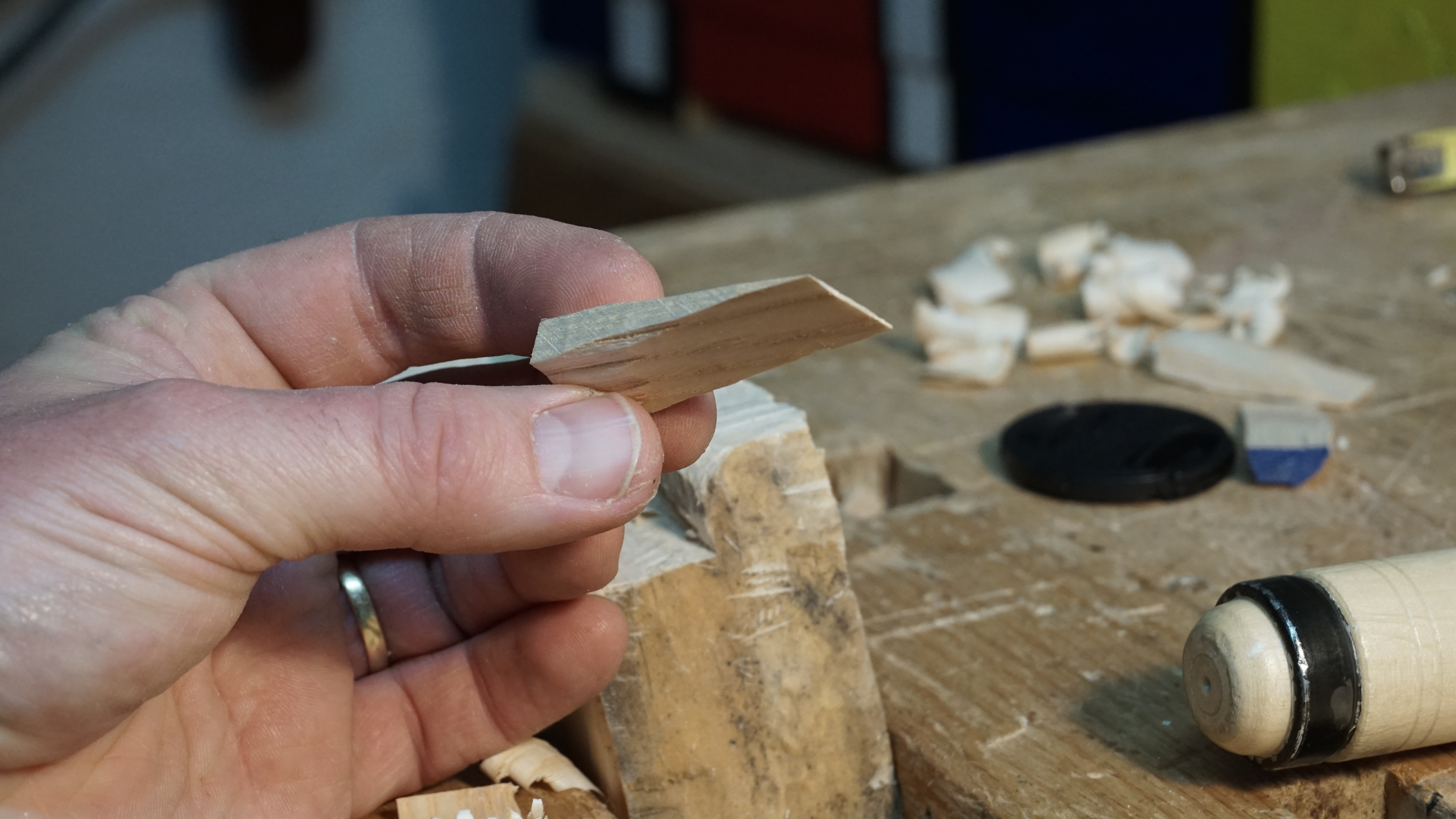
Re-using old wedges
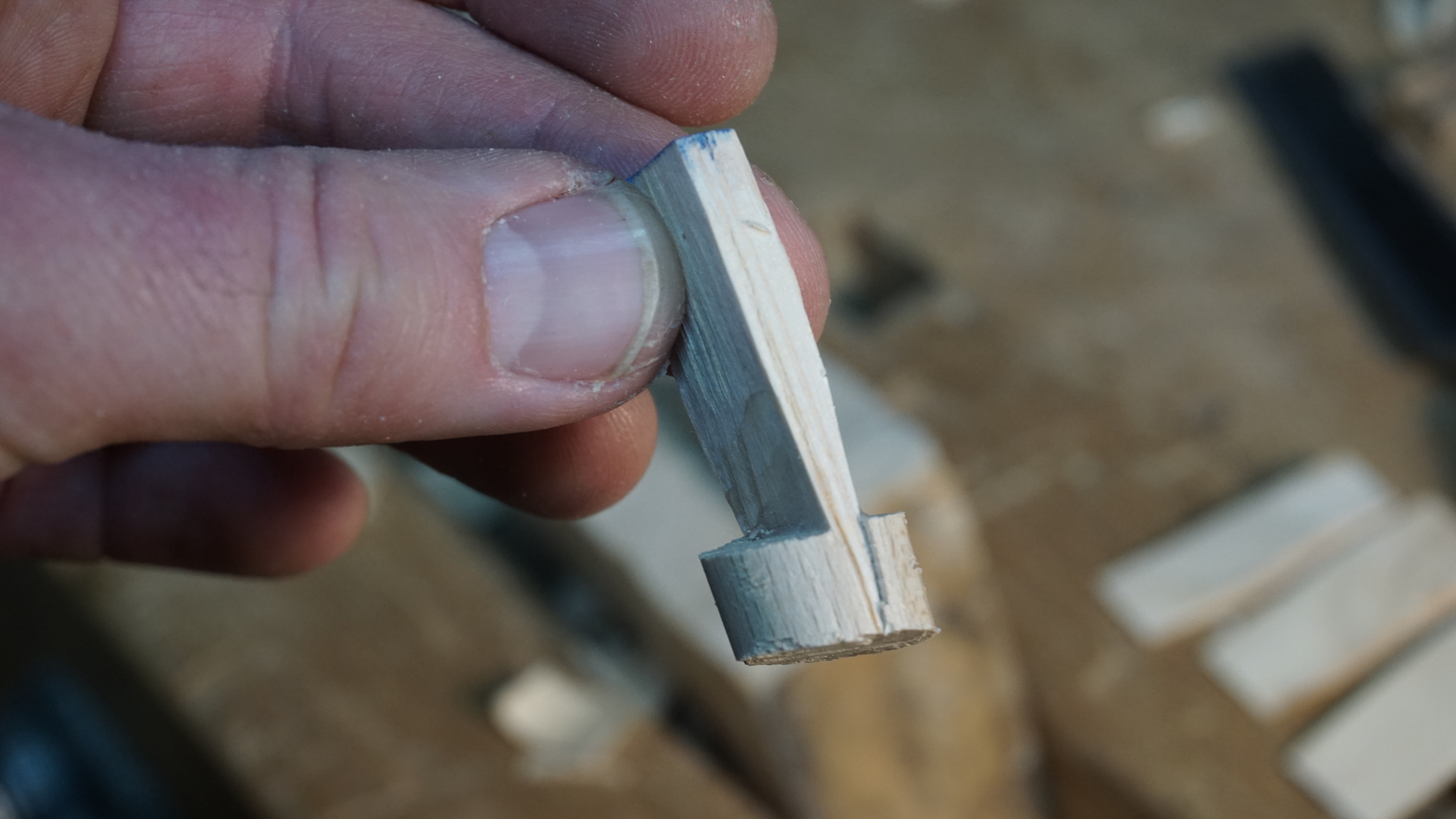
After I trim the tenons on my chairs, I don’t throw the excess away. It is very easy to make another wedge out of them, providing they aren’t too short. This is another reason to make your wedges slightly longer to begin with — you might get two or three uses out of it.
Place the amputated-tenon-wedge on your block of wood and use a chisel and mallet to chop away the bits of tenon glued to the sides. They should come off easily. Mind your fingers as you do this step. I find it easiest to rest the back of my chisel against the wedge and tap it from above.
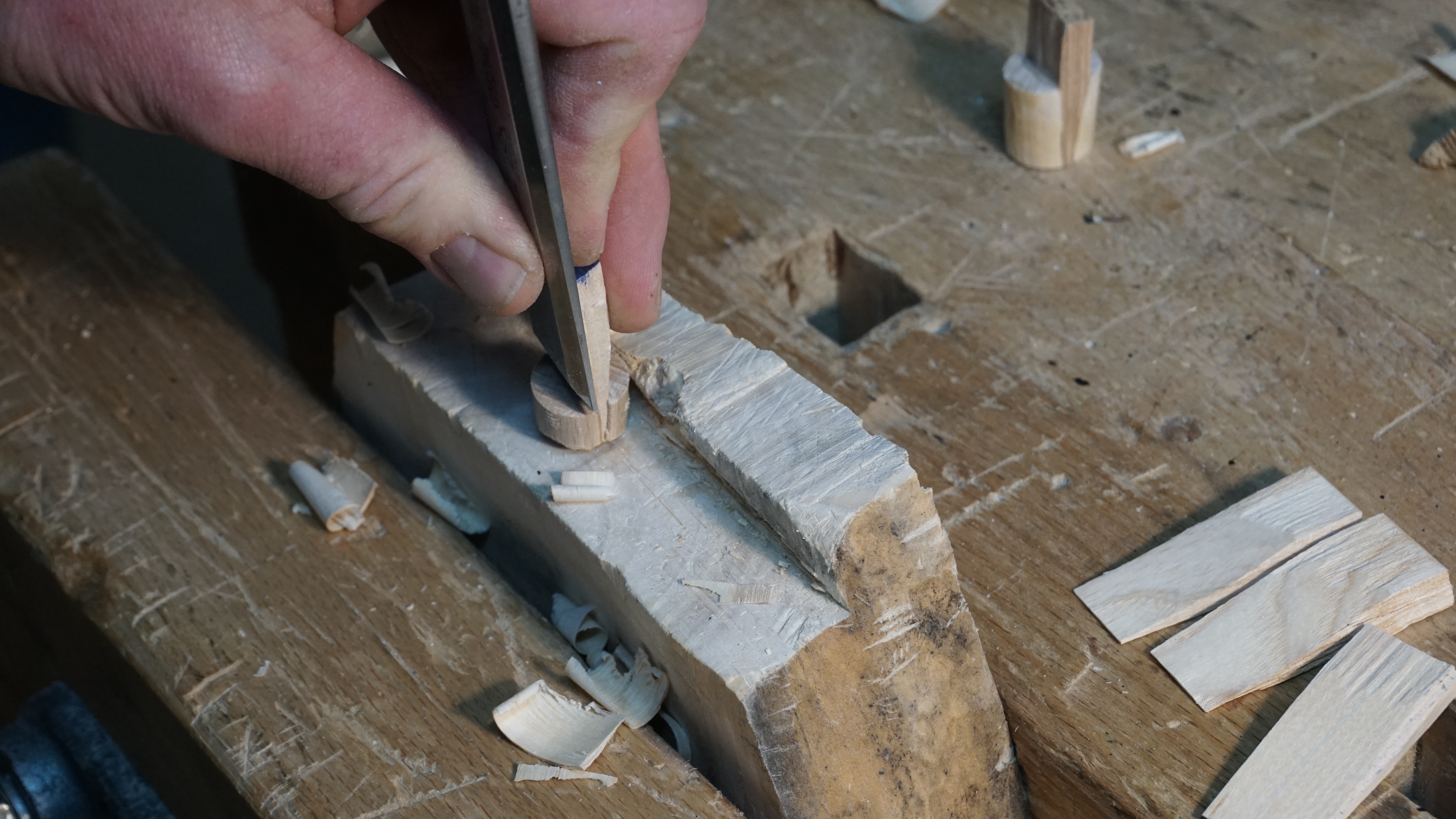
Re-shape the wedge as described above, using the wood block in your vise. This only takes a stroke or two, so you have a new set of wedges in no time.
Using scraps as wedge material
I often have pieces of oak leftover from chairmaking or other projects. This is perfect material for making wedges. Part of an old oak leg or stretcher can be an excellent source of wedges. I have also used old oak tool handles and offcuts from levelling chairs. Make sure the wood is in good condition, especially with older tool handles.
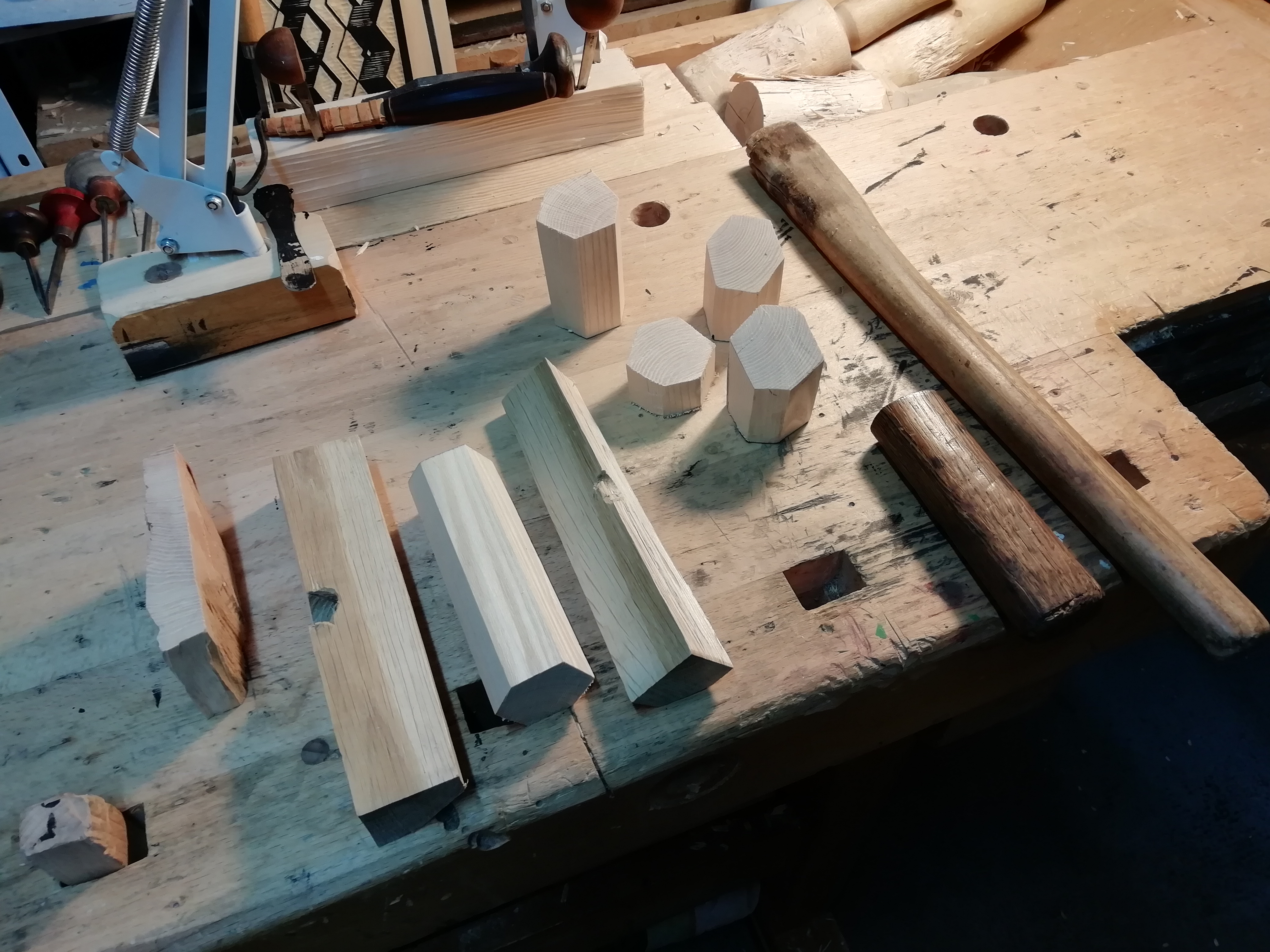
Saw the wood across the grain into the length of your wedge (1-1/2″ – 2″) and shape it as described above.
Making wedges with an axe
I made my first wedge when I had to handle an axe and needed a wedge. I didn’t have any idea what I was doing at the time so I grabbed an oak stick and shaped it into a point on one end with my single bevel hatchet.
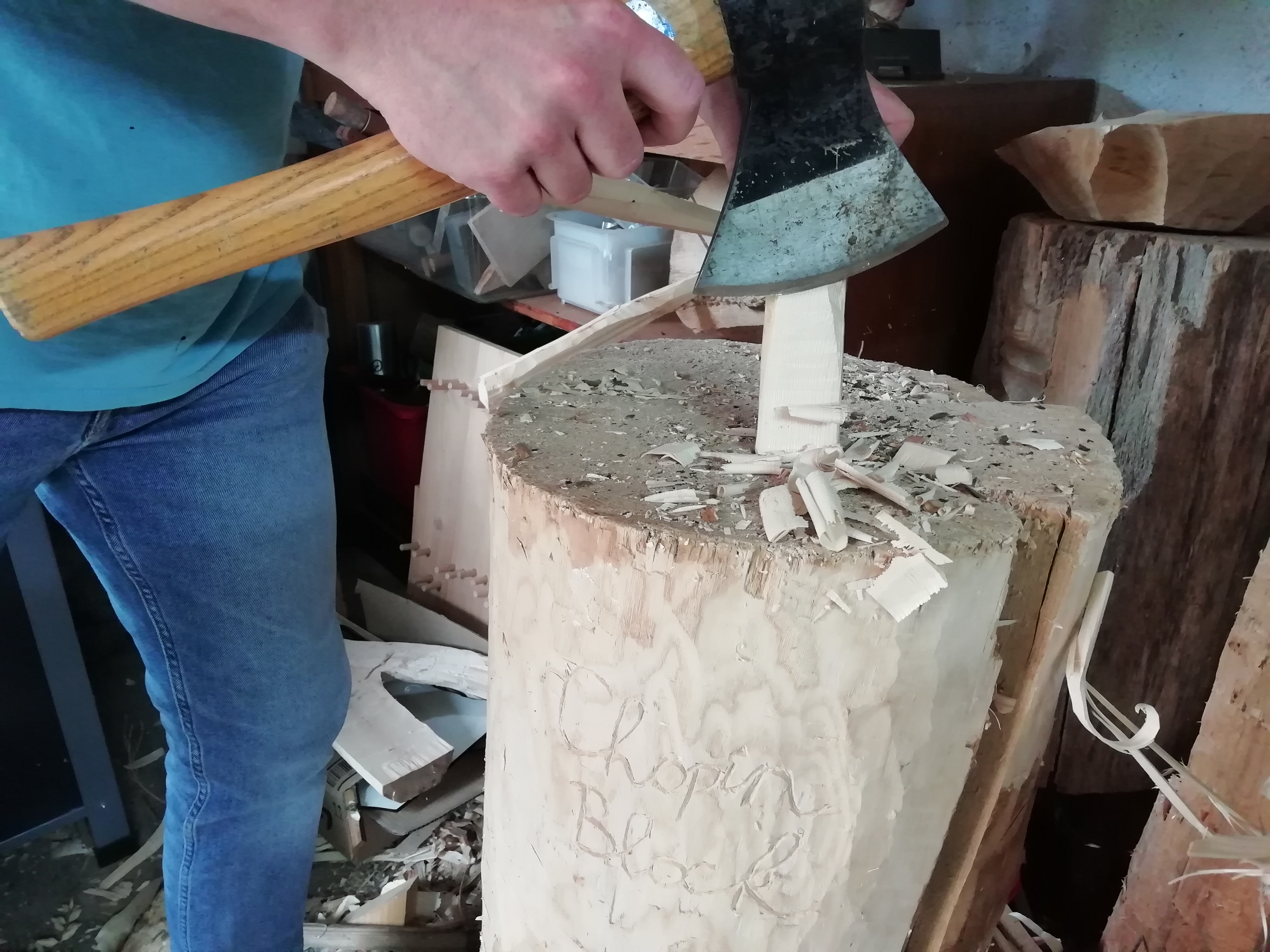
Once you glue the wedge in place, you can saw off the excess and make it into a point again. Et voilà: Another wedge.
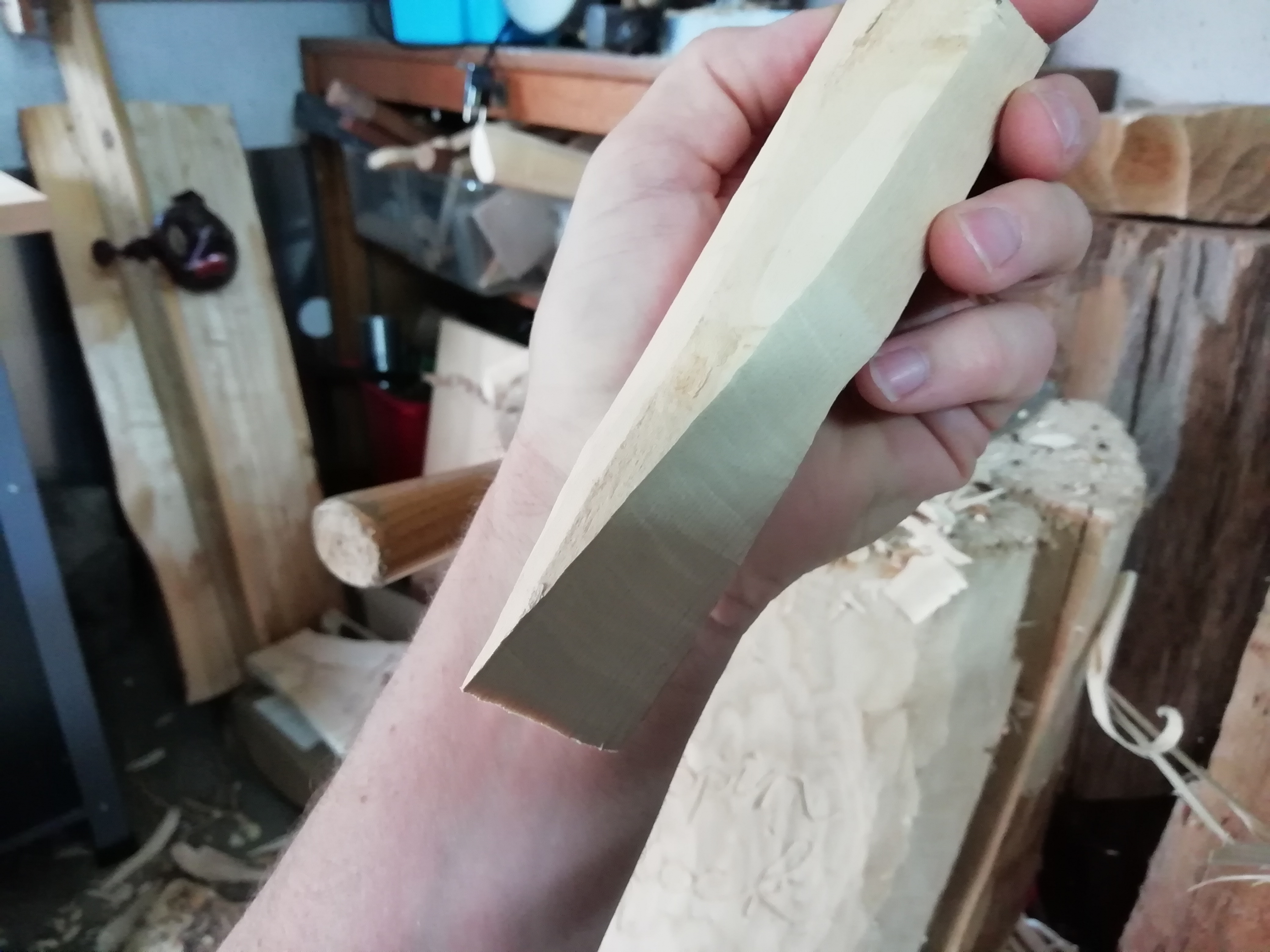
This method is very useful if you need to make wedges that are significantly wider than the wedges you normally use for chairmaking. And they can be used for splitting logs if you make them big enough.
Some uses are:
Wedges for axes / adzes
Wedges for thick table legs
Wedges for yo momma’s a$$
Troubleshooting tips
–The wedge tip has become too thin at the tip or the tip is bent over: Place the wedge flat on your block and use your chisel to remove the tip (across the grain). Shave the wedge again if too blunt.
-The wedge has curved grain: Curved grain is not a big problem in riven wedges. I have used wedges that had a crook in them without any issues.
-I am having a hard time shaving the wedges to their desired thickness: They come out too flat. It is a common mistake to take material away evenly over the whole wedge. Use tapered cuts starting from the tip of the wedge and only remove a little material at the butt end.
Have anything to add about making wedges? Let us know in the comments section!
Looking forward to the next few instalments on how to make wedges with (1) a hollow chisel mortiser, (2) a chainsaw, and (3) a thickness planer. Just kidding of course. Thanks for the informative series.
Dovetail Sawing primer is a great training aid for warming up the the muscle memory.
Wedge cutting is the finished product.
Layout a dozen back to back 7degree and 90 degree lines to the length of your wedges on a scrap of straight grained hardwood and get to it.
You’ll have a box full of wedges in short order
Practice at every opportunity. What a great idea.
Love your blog, Keep it up.
This is the way I do it….chop & chisel…. I how ever just use my bench hook for the chiseling ( My bench hook is kinda big 8″ wide and 10″ long.) I do see an advantage to making a jig like yours.
Having a small block leaves more room for your hand and chisel. Plus, it’s very easy to make.
Thanks for the post. This site is a gold mine.
I was wondering if instead of a rabbet on the jig board, it might be better to notch it with a long crosscut and a short rip to create the bed and the stop. It would give better supprt for the work and make the chisling easier. But I may be missing something.
Thanks again.
You are right that my block of wood is a little on the short side. A bed of 2” is probably better. Nevertheless mine works well too despite less support at the back.
There are enough places to put wedges without going into the familial. Spoiled an otherwise helpful post.
Agreed, this was an out-of-place, uncalled-for and sophomoric attempt at humor.
Thank you!
I laughed heartily, but I may be a cretin.
I concur. It was crude and utterly unnecessary. It makes me uninterested in reading anything else from this blogger.
I agree the joke was a tad on the crude side…but completely dismissing the entire post, or even the author, as uninteresting seems a bit exaggerated to me. We all improve over time. 99% of the posting were helpful, and even if the author insists on cracking one immature joke per post in order to establish that as their personal touch, I would like to read more from them.
Have a great weekend, everyone!
Also, don’t blame Rudy. It’s my fault as the editor for not toning it down. We generally put that sort of joke in a Chair Chat with a warning beforehand. I neglected to do it. So feel free to dump on me. Apologies.
Thanks for your feedback, Shirley. I hope you found the rest of the post nevertheless helpful.
That’s how I do them, Rudy. It def helps to have a big honking chisel, too, as the mass is your friend when shaping the wedges. Another method I’ve used for chair wedges is a much longer very dry stick held in a vise and shape the end into a wedge with a drawknife. You pound in the long wedge, cut it off, and quickly shape your next wedge. You can get all the wedges you need in one stick.
Good point about the big chisel with lots of mass, Kevin. I have not tried shaping wedges with a draw knife but I‘m sure it works great too. An old tool handle would be perfect material for that.
As stated in another comment, many thanks for an interesting entry to this series. When making the wedges for the wedged through tenons on my workbench undercarriage, I built a sort of ramp my handplane can slide on in order to achieve an even taper on the wedges (about 4″ long). Now you state that ‘[i]t is a common mistake to take material away evenly over the whole wedge.’ I did so since the slot for the wedge was fairly long (close to 4″). A wedge made the way you describe would bottom out earlier, leaving a quite large cavity in the tenon. Is it still unnecessary, or even a mistake, to aim for a snug wedge fit?
Thanks for a brief clarification!
Julius
Thank you Julius, I am happy you enjoyed the post.
If the wedge is too thick, it may jump back out when hammered in. If a wedge is too thin, you run the risk of splitting the wood lengthwise as you have to hammer it in deeper before it settles. You also run the risk of breaking the wedge. There is a balance between these two extremes, the resultant angle of the wedge being about 5-7 degrees. If your wedges are 4“ long and the thick end is 1/2“, you end up with an approximate angle of 7 degrees. As I make most of my wedges for chairmaking, they don‘t have to be very long. In your case, a thinner wedge may be the better option, as you have a lot of material surrounding the tenon and less risk of splitting the piece. Does this answer your question?