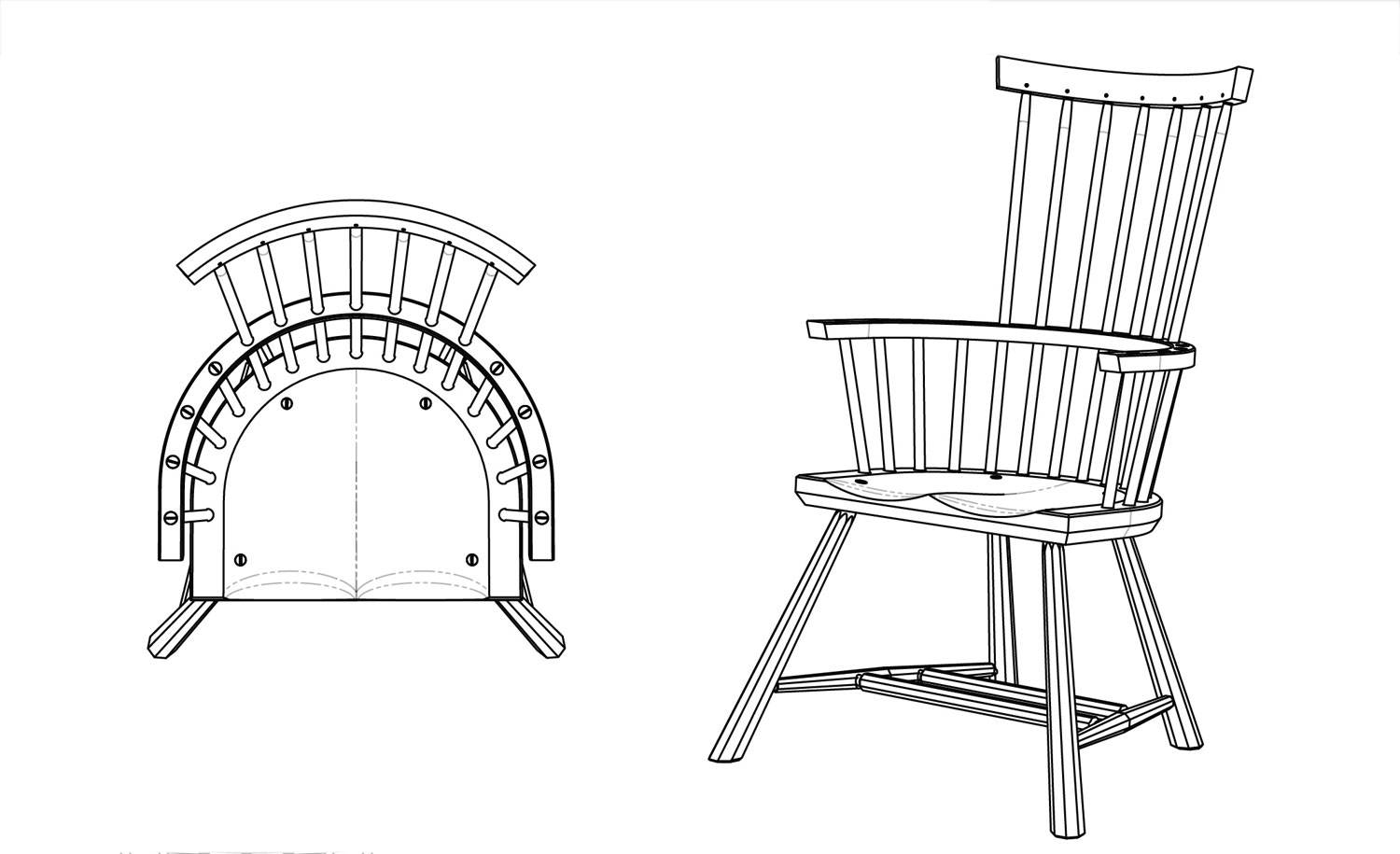
On most Sundays, we try to provide a non-commercial, thoughtful piece of writing, such as Nancy Hiller’s “Little Acorns.” This Sunday, however, I am interested in your thoughts.
I am finishing work on “The Stick Chair Book,” and it should be off to press in a few weeks. I’m working on the book’s “backmatter” – appendices, bibliography, acknowledgments etc. One of the sections I’d like to add is “Commonly Asked Questions” about chairmaking. This will be similar to the one in the back of “The Anarchist’s Workbench.”
If you are someone who is getting started in chairmaking, or is hesitant about diving in, I would like to hear the questions you have about the process. What aspects of chairmaking seem unclear, difficult or beyond your reach?
In general, I’m looking for questions that are fairly broad. If you ask me about how to drill the sticks for a hoop-back Forest chair (aka Windsor) with a 1/4” Gramercy spoon bit, that’s not something I can use in the book (or even answer, except to say: Ask Mike Dunbar).
Some of the common questions I get include:
Do I need green wood to make a chair?
How do you figure out all the drilling angles for the legs and sticks?
What glue should I use?
Do I have to own a drawknife, adze and travisher to make chairs?
Are wooden chairs comfortable?
Why don’t chairs fall apart because of wood movement?
You can post your questions in the comments below. The comments will close on Friday, June 11. If you include your name with your comment, I will gladly credit you in the book. Thank you in advance for sharing your confusion.
— Christopher Schwarz
What do you look for when you’re choosing a board(s) for the seat?
Does it have to be a single wide board or is a well matched glue up acceptable
https://www.theonion.com/report-confirms-no-need-to-make-new-chairs-for-the-time-1819576693
Excellent.
So no more playing musical chairs in USA?
You’ve already mentioned “how to figure out the angles”, but I would like to hear more about how do you actually get those angles when drilling? Some sort of jig? Piece of scrap cut to that angle held against the piece? Thanks!
To add to that, Do you have to have someone else to stand 90 degrees to you watching your site line, to let you know if you need to tip forward or back, to get the proper angle or is there a way to do it working alone?
Living in the suburbs, I can’t go out to my own private woodlot to select and cut the right tree or trees for the project. Do you have any recommendations for where I might find a good enough wood for a stick chair project?
This. Getting wood for the legs and such is doable with a bit of ingenuity (and extra cost), but where can a city-dweller find seat blanks?
Again this. Former Cincinnatian who was spoilt for choice and now in a place that while rural, no one sees a tree that seemingly by law can’t be hacked up into 18” firewood pieces. And the couple of big box sores are so atrocious it makes me ill. I hate to say it but I need a kit.
Not incredibly specific but I really hope Edwardian and Victorian style chairs are discussed in the book : )
What are the chances that someone will sit in one of my chairs and it collapses in splinters under their weight? How do I make sure this never ever happens?
Good question. What are we talking about for weight capacity on chairs like these?
I, like many others have always found the idea of building any type of staked chair overwhelming. Not necessarily too difficult. I can’t claim it’s too difficult because although I’ve read extensively and watched all the videos I could get my hands on, I still find myself overwhelmed by something I’ve yet to attempt.
So, because I just need to get started, my question is.
What’s the step before step one?
My question is similar to that posed by Justin . What will be different in this book from what has been presented in The Anarchist Design Book ? Will this book begin as a more introductory text for beginners ?
Build a pair of staked sawbenches. Same wood / tools / angles, no pressure. Read Anarchist Design Book…
Why do chair seats have that rise in the front middle where it can hit one’s testicles? It doesn’t make sense at all.
I’ll second that. It doesn’t serve comfort, or any useful purpose, as far as I can see, but is purely stylistic.
I think that little rise is called the nib.
pommel
the questions I would have is: how did chair dimensions change over time and what are good dimensions for today e.g. for seat height, seat width, angle for the back rest and what is a good radius for it ? I see a lot of chairs which look good but are not comfortable at all. I guess there are some best practice values which makes a chair comfortable.
My questions are probably common ones:
Can I use lumber from the big box stores? My local stores have construction pine, plus a limited selection of maple, poplar and red oak.
What about recycling parts of old chairs?
I have an old set of kitchen chairs stacked up in the garage; they have the usual loose spindles, cracked arms, etc. The seats are solid maple and in good shape. I thought of reusing the seats with a new back and legs. Any tips, thoughts?
I have a tree on my property I want to turn into a chair. How should I cut it and store until I can start my project?
That’s an excellent question!
If I copy an existing design of chair (like Ercol for example) are there copyright issues if I want to sell it?
I know this should be simple, but when referencing resultant angles, I often stumble at setting my bevel gauge.
Do I reference off the right or left side of the Bevel Monkey? Why is 90 degrees actually zero degrees, etc.? It’s surprisingly difficult to find a reference photo or video on this.
I reference off either side of my homemade bevel monkey. It just depends which way I want the bevel blade to be relative to its body.
Thanks. I think it’s worth elaborating within the book, if possible. If someone is using a protractor, an angle would not read as 21 degrees, for example, but 111 degrees (or 69). It often throws me off, and maybe others would find that information helpful.
Is it possible to rig a Speed Square for resultant angles instead of a bevel with a monkey?
Can you experiment with the angles without sacrificing stability and comfort? Or better in which parts of the chair you can leave your imagination free without affecting it?
What is the easiest back to put on your first chair?
You Dave maybe not everyone has testicles. Just sayin
I have the same problems with the angles and stuff the math scares the you know the stuffing out of me
Do I need a shaving horse to make a chair?
Are cylindrical tenons problematic? Will the legs just drop out, and do I have to buy the crazy expensive tapered reamers to make a chair?
… and: what kind of wood should I use?
-What species of wood are best for chairmaking?
-Can I copy someone else’s chair design? For profit?
-Must I own a lathe to make a chair?
-How do I know if my design will be comfortable?
-How may I scale the chair for my body type?
-Are chairs expensive to build?
-Are purchased dowels suitable for chairmaking?
-What type of paint will be durable enough for a chair?
-Will his estate have me kneecapped if I make and sell a “Maloof style” chair?
-Can I make chairs without a dedicated workshop?
-Should I sign my chair?
-Can I eat serial with a spoon bit?
-How long will a wooden chair last?
-Is it cheating to use power tools to make a traditional chair?
-Does Adam Cherubini make both chairs and beanies? In a bakini?
Yes, I know Adam’s name is pronounced with a “K” sound and not a “Ch”. I stretched a little for that one.
Is the Old Kentucky Bourbon Bar still open?😁
Yes
As a purchaser of “chair makers notebook” I would like you to go into a little more detail about how to prepare or procure stock for seat blanks. How do I go about gluing it up? Where do I find a solid piece of wood that size? If it’s even available. Thanks.
The one challenge I had was getting the tapered tenon to match the tapered hole for the legs. I am tapering the legs by hand with a draw knife and a block plane and using a tapered, hand turning reamer after drilling the holes in the seat. Taking little by little so the leg fits in the hole from the underside but then there is a gap in the top hole. How do you judge the two so they fit nice and snug when shaping by hand?
Can you describe the method you use to drill the holes for the legs in a chair? I have seen a power drill make the entire cut with a backing board and used it myself with mixed results and trying to stop the drill tip just as it pokes through the front and then finish the drilling from the other side. That has also resulted in mixed results. I have only made a few chairs but the process of drilling a 3/4″ hole at the proper angle without chipping out the top finish side is the most difficult process in chairmaking for me. I have also had interesting results in using a brace with a reamer. Any suggestions would be greatly appreciated.
Larry Malohn
Can I build a chair without a workbench or only a low workbench?
On the subject of pinning the sticks. I don’t remember reading anything about it in your books, or from other authors? I see on your drawing above that the sticks are pinned to the crest rail. I guess you talk about the need or not of using them in this book? So a few questions: Why use them? What wood to use? Is it necessary to pin all of the sticks? How do you drill them so they go right through the centre of the stick? What about pinning the sticks to the seat and the arm bow?
My apologies, you do mention to pin the spindles in the chapter Staked Chair of The Anarchist’s Design Book. I could not remember, because I went straight to the Armchair chapter of your expanded edition to build my first chair.
Before building a chair, is there a list of other projects you suggest that help to refine the techniques of chair making?
Not a beginner, have built several stick chairs, but I find myself often having to go back and fix leg angles. How can I (jig or some other tool) get the angle correct every time?
I’ve been making Windsors for the past two years (shoutout for Elia Bizzarri in NC for anyone in the southeast looking to learn). Here’s many of the questions I’ve had to work through at some point. While I have my answers for most of them (I still haven’t come to a conclusion about how terrible a rolling swivel comb back would look), I’d be curious your take on some of these. I’m looking forward to the book!
-s
-How deep saddling is too deep. Where do you measure the depth?
– Won’t that center spindle be uncomfortable on my spine?
-Cracks formed on my bent parts as they dried in the form; can I still use them?
-Can I put a staked chair outside, under an awning and what would you do differently for such a chair (different wood, glue, finish)?
-I’m making a chair for a smaller[larger] than average person. What dimensions need adjusted and how do you adjust them?
-Ok, so I’ve built a couple chairs and they look and sit good. What should I focus on to refine my chairs to the next level (assume the design stays the same).
-I’m using KD boards for chairmaking; how straight does the grain have to be?
-Now that I make chairs and understand how comfortable a chair can be, how do I survive in a world filled with uncomfortable chairs.
-Would you judge me if I put the top of a Windsor or staked chair atop a rolling office chair base for my desk at work?
-If I want to mainly build chairs, how should my workbench be different for a typical cabinetmaker’s bench.
-My {relation} wants me to make them a chair; what’s a fair price?
-How long does it take to build a chair?
-Everything I read on Windsor chairs says to superdry tenons to make strong joints. What will happen if I don’t?
-How long do dry parts (in equilibrium with shop) need to be in a kiln to superdry?
-How accurately do I need to drill angles?
Related to Stephen’s question on drying the wood for a chair. In Roy Underhill’s book (The Woodwright’s Shop p. 69) where he talks about making chairs, he suggests that the rungs should be dryer than the back splats and that the legs should be done last and be “greenest.” How much of a problem will there be if all the wood has a similar level of moisture in it? (Thinking of the occasional woodworker (me) who stores wood in one place and can only work on it once in a while as time allows.)
As to your “bent parts” – you should probably consult a medical professional
I purchased the outstanding design book and have decided to go straight to the back stool to make a couple bar stools. Back stools with longer legs, the way I see it? Anyhow, waiting on my giant pencil sharpener from Lee Valley then I jumps in it. Thanks for the great books/efforts.
Hi Chris,
A question that has been on my mind lately is what techniques and/or settings you use when drilling with WoodOwl UltraSmooth auger bits in a hand-held power drill, as I’ve seen you do in many a photo.
I’ve tried it myself, with so far non-disatrous but not great either results, while feeling decidely unhappy about the process. With the lead-screw on the bit pulling it in with much force, the torque as the bit startes to bite is quite impressive, to the detriment of control and precision both on angle and depth of cut. How do you handle that? “Just” skill and strength? Or is the power drill set to a very slow speed, or a very high speed, or is there something else you do from that point of view to avoid it pulling everything out of whack? Are there features that the power drill should or must have for it to work well with these auger bits?
For my part, after every attempt with WoodOwls in the power drill, I’ve gone back to the brace, which of course works fine, albeit rather more slowly, so the full low-down on how you do it with electron assistance would be valuable indeed!
Many thanks in advance and all the best,
Mattias
I second this question. I was intrigued when Chris started posting about Wood Owls, but I decided not to try them after this post from Elia https://handtoolwoodworking.com/testing-drill-bitsclass-opening/
I’d love to know more about how Chris gets them to work well.
A problem for any chair, to figure out how much wood to purchase. Can you expound on this theme? What (how much?) do I need to purchase?
How would I go about making a tapered reamer with a compass saw blade, but without a lathe.
Just like making a tapered octagonal leg. Make a tapered square, the knock down the corners to an octagon, again to a 16-gon, 32-gon, 64-gon, to whatever degree of circularity you want. The geometry of the compass saw blade sets the cut, not the reamer body. You just need to knock down the corners enough so that the difference in radius between the middle of a flat and an arris is less than the depth of cut you want to take.
Thanks for taking these questions. Looks like you’ll have enough for a two volume ‘backmatter’.
How does one reliably glue seat boards together? Fixing those after N years (or months) seems to involve complete disassembly of the chair.
I second the question about whether I should taper the tenons/ream the mortises. Do I need a commercial reamer? Which BTW, they seem to give a rather small hole for a leg. Do you need to scoop out the seat? If so how do you do that with a normal tool kit.
I am just above the beginner stage. Meaning I am gathering my courage up to cut my first dovetails. That being said I am in the middle of your design book and am reading through chairs at the moment.
My question is this.
Why do I need to angle the legs at all. Why not just but my wood auger in my drill press and drill straight through, tenon the legs and drive them home. I want to build a chair not a “sexy” sitting chair which by the way I think Welsh chairs are sexy.
Just need to understand.
Is a lathe helpful in chair making?
When setting out to make a set of dining chairs (4 of them, let’s say), how would you alter the process as far as batch operations or using any additional jigs, etc. to make construction more efficient? I would think it is best to complete one chair before committing to a set, then optimizing an efficient build process for the other three chairs.
I built five for a four chair set. I tested each step on #1, then corrected as necessary for a run of four. At the end I had a ‘shop chair’ plus the set I wanted to give away.
How do you add a slip frame upholstered cushion to the seat and back.
A few questions I’ve gathered from making stick chairs lately.
I would love to hear a treatment on why you drill the leg holes from the bottom of the seat. I noticed that you and John Brown do this, and Peter Galbert doesn’t (my chair book collection). I’ve tried it both ways and have found pitfalls and successes in both approaches.
You mention slight saddling of the seat increases comfort, but I’m very curious why exactly. I’ve never seen or heard an anatomical explanation for saddling, and especially for the various styles of saddling out there, but I expect that there is one!
I would love to hear more about the details of repair! Walking through the replacement of a broken spindle, for example, would be much appreciated by many who want to be prepared in case the situation ever arises.
I would love a treatment on the longevity pitfalls of not using the perfect wood for the specific part. For example, should I be worried about using elm spindles instead of ash or oak, if elm is what I have laying around? I like not being too dogmatic about wood choice, but I want to know what risks I’m taking on.
Thanks!
Do I need to rive the lumber for the legs and spindles, or is that just a nice to have?
Remember what happened to the guy’s chairs in the movie “The Patriot “ those legs were not Riven
How do you choose the high of the chair ?
What species of wood are best, for legs, spindles, and seat? Any that are acceptable, available from big box store, or commonly available on either coast?
I live in California and would be interested in making chairs out of woods that are found more commonly on the west coast. Would be interested to hear suggestions on favorable woods for chair making in different regions of the country or even abroad.
Claro, live oak, Oregon white oak, persimmon maybe. There are a lot of interesting woods here on the west coast.
Part of my question piggy-backs off Justin Freeman’s. One of the most intimidating things about chair-making for a tyro like myself is the number of new skills (chair angles, reaming/forming matching shapes, splitting/shaping sticks, wood bending, seat shaping, etc) that all need to come together. It may already be in the book (Design already has some great coverage of some of this), but are there projects to build up each of the unique skills before tackling the the combined set? Looking forward to the book!
Hi Chris,
Maybe this is already covered in the book but I’d like to know if it’s worthwhile to insert the legs into dovetailed battens ala Peter Follansbee’s brettstuhls (or a scaled down staked table) in order to use thinner or softer stock for the seats.
Thanks,
Jon
For those of us that have never saddled a chair,
some guidance concerning that actual shape,
as opposed to the tools and techniques, would be helpful.
When saddling a seat, I can see the curve at the front edge,
but how the curve changes as it progresses to the back of the seat is a bit of a mystery.
Maybe a drawing like a topo map, just to give a starting point, would
be helpful.
Probably easier than taking plaster casts or 3D laser scans of peoples bottoms.
If you’re interested in Windsor chairs, Curtis Buchanan’s plans come with a topo map of the seat contours. Jump to time 3:47 for an example https://youtu.be/ej4DU-GeakE
Do you adjust the thickness based on wood species?
Which way should grain be oriented for strongest joints?
what is the unending fascination with milk paint about? What was/were the common finish(es) on chairs over time, say from 1700 forward. How did the finishes vary in across the world over this time line.
as a person who started directly with chair making, I’ve never made a square joint in my life. Thus joining two or more boards together to make a seat remains one of my biggest challenges, as I may get around to making a seat every few years as time allows. I guess the answer must me to learn how to tune and use one of my garage sale plane nightmares…..But I always wish for a shortcut short of buying a power tool/joiner….
As a Dunbar student from the ’90’s who owns the 1984 version of his book I think milk paint for chairs at least came from him. He really likes the non-totally-flat effect of old paint but couldn’t reproduce it with the original paint recipe because it involves lead (originally oil based lead paint, but slightly translucent). While trying to reproduce the effect he discovered he could get it with milk paint (period pigments) and an oil-based top coat, and recommended it in his book. People today see the chalky effect without the top coat as a feature but it was originally a bug (given the effect he was trying to reproduce). I can tell you from experience if you don’t put a clear coat on top not only is the color off from what you expect from the pigment you get very distinct wear patterns especially on the seat…
You know you are in the Society for Creative Anachronism when you can look at an old milk paint color chart and name the pigments (also used by illuminators 😉
the 73rd Knight of Windsor (http://www.thewindsorinstitute.com/knightly-news-sir-who/)
My great fear is after I build it, my first test sit reveals that it doesn’t sit comfortably. Where do I start in making adjustments? Adjust leg height or saddle a bit more? When do you throw in the towel and declare that it was always meant to have a cushion on it?
How much does rake and splay of the legs affect stability of the char (or any staked furniture, for that matter)?
Even the fairly moderate angles in the ADB look pretty radical to my eye (my brain is used to straight/plumb legs) and the use of commercial taper reamers naturally limits the tenon size. Is sturdy wood like oak, ash, or maple able to withstand such absurd forces that splaying the legs does not matter or is there a real risk of broken legs?
Relatedly, albeit unfit for the The Stick Chair Book, do you have any insight into how splayed legs react to vibration? Is the staked worktable from the ADB a viable design for a sewing machine table?
A corollary to “Do I have to own an adze and travisher to make chairs?”
Figuring that a plane can reasonably stand in for a drawknife… Are there sensible substitutes to allow hollowing?
You can get pretty far with a wide shallow gouge followed by a small (self made Krenov style) compass plane if you aren’t in a hurry. Think something like 38mm number 3 or so and stick to nice wood, The attempt in tulip poplar took twice as long and still not as nice as Eastern white pine or basswood. Your next step would be to get/make a travisher (at least one maker sells blades separately; it’s basically a curved spokeshave for which there are multiple sets of directions online). My experience is Dunbar windsors but I can’t imagine Chris’s chairs are that different. What I would have to have is a spokeshave and drawknife although Chis seems to get pretty far with jack planes. The gutter adze can come later if you go into business.
See adze. scorp, travisher, compass plane as analogous to hatchet wielded by Follansbee, scrub, jack, smooth.
I can make nice casework because I can cut wood square on the tablesaw. I don’t have an artistic bone in my body. Can I make a chair?
H9 Chris,
Here are.some of my questions.
Can the grain run out a little bit on the legs or spindles? Will the legs really break?
Can I make chairs out of any wood?
What is the minimum thickness for tenon? Legs? Spindles?
What are the critical elements of a chairs design that I have to adhere to or the chair will fail?
What can I play with?
How loose is too loose for the spindle tenons?
Hope these help.
Josh
How do you make a chair comfortable for kind of fat people? Can you make one chair which is comfortable for both kind of fat people and not-fat people.
What kinds of wood do you recommend for the various chair parts and what woods should you avoid
Fir. Avoid Fir. It splinters, chips, splits… It sucks!
Hi Chris,
What wood would you use to last the longest and stand the test of time for a chair build?
Thanks,
Joe Erthal
I do my woodworking in an apartment, with a bench I can set on a tabletop. I don’t have room for a shave horse, or anything like that. Can I build a chair? How much space does it take?
Also, I get maybe 3-4 hours of woodworking done in a week. Can I make steady enough progress to make building a chair worthwhile? Do I need to worry about the wood drying too much in between work sessions?
As having never built a chair before , my first question would be what tools do I need, type of woods explanation of the parts ie rake /splay ect. I know that you have made many chairs but for someone that would like to start or try that would be my 2cents worth
In making a personalized chair for one individual what body considerations and or measurements need to be made and how will they relate to the design?
when making a personalized chair for one individual what body considerations and or measurements need to be made and how will they relate to the design?
PS Apologies if this posted twice
I understand the wedges into the top of the legs to secure them into the seat should be at 90 degrees to the grain of the seat however should the wedges be at 90 degrees to the growth rings or parallel to them in the legs? Or does it not matter?
thanks
I cracked my seat driving in the legs. It seems structurally sound for now but I’m guessing it will fall apart eventually. Can I get away with screwing or dowling through the side of the seat to stop the crack from expanding or coming completely apart?
Chris, thank you for asking. Can I rectify a drilling angle error? If so, how? My example: I put a ton of time into a beautiful solid two-inch thick maple seat. I’m satisfied (not thrilled) with the splay and rake of the two front legs. One of the rear legs has ok rake, but insufficient splay. The other, sadly, is inadequate in both. While my wife graciously loves her stool, I’m afraid she’s going to tumble off. Is there something I can do to fix the errant leg, or is it a great learning experience and more beautiful firewood?
John,
Chris might have an answer, but I will chip in a solution… you could make a ‘plug’ out of the same wood species, pound and glue it into the bad hole, then come back and re-drill its hole. Plug can easily be made on a lathe or with a spokeshave. Best of luck with your maple seat!
I’ve asked about the slope of a work chair compared to a relaxing chair before and you kindly answered, but I’ll ask it again for inclusion in the book in case it fell by the way.
Also, it might be helpful to see a comparison of the slopes front to back for the extended family of stick chairs, e.g for laid-back reading, working at a desk, for a dinner table, a bar stool, a workbench stool.
Together with the slopes, it might be helpful to compare the splay angles of members of the extended family, e.g footstool (for reaching higher), the sawbench of course, low stools, relaxing, dining, and desk chairs, and bar stools.
I’ve made a several sawbenches (the first time I believe I have ever followed anyone’s instructions!), and since used the design for ‘bootbenches’: same height as the sawbench (because sitting higher than a standard chair makes snowboot wrangling a lot easier, and you don’t sit there long enough that cutting off blood supply in your legs is an issue). The seat width and depth was borrowed from the Staked High Stool (nice to have the extra seat width to push off from, four legs though). This size works well for the entrance hallways of my kids who live in downtown condos where space is tight and a standard-depth chair would be in the way.
Any other mutations in the family from readers?
I stand in awe of the ADB (read sit). I’m sure the Stick Chair Book will be similarly awesome. Merci à l’avance!.
If I am making a chair for myself (and I’m on the smaller side), how can I scale down the measurements? I am guessing the measurements are to ensure that the majority of people will fit your chairs. So, are there any good ratios to body size that you would advise?
Same question but for extra large person. I’m 6’ 6” tall and 300+ pounds and 99.9% of the stick chairs I’ve sat in are torture implements that get worse the longer I sit in them. I think I’ve got a handle on the heights and how to scale up for my comfort. I think I understand the angles and how to achieve them to get the appearance right. What I’m really struggling with is how to keep it from looking chunky but still strong enough to support me and a grandkid without mom or grandma feeling they need to hover incase the chair collapses.
Second question: I know you don’t like rocking chairs but I’d really like to know why stick-type rockers are always so low to the floor. Is it physics, safety, aesthetics, or what?
Rockers are supposed to be low to the floor, because you should have your feet flat on the floor through the entire rock. It needs to be lower so that at the back of the rock, your feet are still flat on the ground. The consequence of this is that your feet are farther away from the chair than in a normal chair. If a rocker were the same height as a normal chair, you would have to be rocking on your tippy toes, which ain’t comfortable.
The low stick/Windsor rockers are doing it right and the rockers that are at a “normal” height are torture devices.
What are the key elements in construction of a chair that are important to get right in order to ensure longevity of the chair/avoid failure of the structure of the chair?
What are the “Golden rules” for species for legs, seat,legs and back for it to last a long time. Not looking for pretty, just rock solid.
How do first timers usually screw up saddlng a seat…and how can it be fixed? This process has me frozen in fear…
Chris, you might have enough questions here for a half dozen books!
Yup. Swimming in questions today.
Oversized tapered leg tenon holes….any ideas for a fix? Other common mistake corrections would be great. Having a fix may take some of the fear out of chairmaking.
I failed Trigonometry in High School should I even bother trying to build a chair. I ask half jokingly.
How tight do I need to make the joints in a stick chair? Can the sticks have a bit of wiggle in the mortise? Is “close” good enough for the sticks, arm, and crest rail? Is it better to have a loose leg or one at the wrong angle?
Are there any special considerations for creating a set of chairs?
Are there modifications to make to add more lumbar support? (Besides a pillow)
Thanks
Guide lines for seat saddling for comfort – I made one chair but made the saddle too steep and deep at the back area (centre post) and it makes my butt go to sleep.
I’d like a list of suggested approaches to modifications based on how your chair works out:
If your chair feels <<thing you don’t like>>, then next time try <>.
For example: “If your chair feels like you’re leaning back too far, then next time try reducing the resultant angle of the rear legs.”
Of course, there can be multiple suggested modifications for each thing you don’t like.
I agree with Wilbur’s question. Understanding those details makes the reader from a paint by numbers level to real understanding of how the chair works.
A couple of other questions I have:
Can my lumber be kiln dried if I super dry the legs (but not the seat)?
Is there such a thing as too hard of wood for the seat? I struggled to get round holes with a tapered reamer in a sapele seat. I don’t know if that’s because of the sapele or a technique problem.
What is a good, bare minimum tool kit? One thing that has dissuaded me from doing chairs is that there seems to be a lot of extra kit that I don’t otherwise use. Are rounders, travishers, reamers and all really necessary, or can chairs be done with a more basic joiner’s-type kit?
How do you figure out how strong to make a chair? Assuming you don’t want to end up over engineered. Given an available type of wood, how do you vary a design to deal with variations in tensile or compressive strength? Thickness of parts, depth of mortises, angles of strain, etc.
Are there guidelines for matching footstools?
If I planned to match a chair to a footstool, should I make any adjustments to the chair’s geometry?
Which designs will result in lasting chairs when subjected to hard use and big soft bottoms? When a design is deemed ‘durable’, what about the build is critical to get right, and what is less important? What woods do I have to use to get a durable chair when using certain designs? For each design, which tools do I have to have to make a successful chair without taking 10x longer than it should?
We don’t have any traditional chairmaking lumber on Vancouver Island. Without asking specifically what wood would work well, maybe an appendice with a list of woods that would make good choices for spindles, seats, legs, etc. Or even a list of woods that split well, and others that don’t. Perhaps include a list of woods that bend well. Basically 99% of what’s available is douglas fir, red cedar, yellow cedar, and some soft maple. And unfortunately, not even oak 2 x12s at the big box stores…
Anyway, can’t wait to order a copy of the book – cheers!
I honestly have no idea where to start or even what style of chair. If you had to pick a design of chair for someone to begin with, what would it be?
There seems to be a lot of speciality chair making tools available. Which tools are not necessary and which can be substituted with more common tools like a block plane or bench chisel
Why do most chairs have four legs?
When designing your own chair how do you determine if it will be strong enough to hold up to normal use/abuse?
(Precedent / Experience / Instinct / Engineering? A mix?)
Could you suggest ranges for angles of: saddle (from parallel to floor), leg rake, leg splay, back rest sticks, etc., differentiating between chairs used for different purposes (work at a desk, eating at a table, relaxing/reading elsewhere)?
How realistic is it to want to get into chair making without a lathe?
Thank you!
Related to the comfort question: Is it realistic for someone building his or her first chair to expect the result to be comfortable enough to sway reasonable wooden chair skeptic in the same house? If so, what should be done to minimize the chances of that first chair ending up in in the attic or scrap pile?
Do I need to own a lathe for these chairs?
How do I fix these when the sticks loosen? How do I maintain the value and structural integrity?
What is the relationship of the seat to the floor? Parallel? Lower in back?
What is the relationship of the back to the seat? 90 degrees?
Obviously, these things vary chair to chair. Why? What are the aesthetic, comfort, support & stability considerations taken in determining these things? Are there minimum and maximum acceptable ranges that should not be exceeded, regardless of the above considerations?
What’s the first chair I should make as a pretty good woodworker (I can make furniture) but have never made a chair, let alone a stick chair?
I’m someone who has never made a chair before. Please recommend a simple one to start with so I can have an early success before moving on to more complicated ones.
Question 1: With respect to resultant angle, how close is close enough? I just finished the Saw bench from PW article, and once completed, they measure 15 degrees (right on. not sure how that happened), 14.5 degrees, 15.25 degrees, and (mumbles under breath) 20 degrees.
Question 2: Was Stumpy trolling you?
Question 3: Where can one get the plans to that lovely Hobbit chair?
I’m 6’6″ tall. (long legs and long torso) What is the common rule for determining chair height and seat back height for the non average sized person. Most chairs are comfortable but if I want a sittin’ chair just for me what measurements should I take on myself and how does that translate to chair parts?
There are lots of pictures, desciptions, and videos readily availeable about stick and leg layout and drilling and so forth, however most things just say to saddle the seat with no real suggestions or guidance on shape, contour, or depth progression. It may sound silly, but saddling is what intimidates me the most. I have no idea about what to do about separate cups for each cheek, a pommel or not, and on and on. I know I am probably overthinking this.
You may have received these suggestions previously, but here goes. I put off building my first chair until last year. I always hedged, I wanted to make something beautiful but it was so complicated that I always held back and then I took a course from you on the three legged stool and I took a chair design class from Michael Fortune. Both helped immensely. So this last year (about 18 months ago actually) I made my first chair (I made the prototype of the chair I designed with Michael Fortune). Yes it’s a chair and I love it because it’s the first chair I made with my own hands and I display it proudly. But it’s heavy and I’d change a million small things next time. Then during COVID after waiting for you to publish the Jennie Alexander book and missing a class cancelled with Brendan I just decided to dive in and I bought your video and taught myself. I now have 6 Jennie Alexander style chairs in my kitchen table. So the 2 questions that my 2 year ago self was still struggling with were these:
How do I get over my fear of starting my first chair. You will of course have a different answer but I found the following three things helped me. (1) Go for it, what have you got to lose? (2) teach yourself – read, watch videos or the best is to take a class. (3) yeah, it’s fun to make your own design, but don’t overlook the tried and true forms. Start with a winner before you branch out too far.
Is it ok to not rive your green wood? You may have a different answer, but I found I couldn’t get the hang of riving when building the Jennie Alexander chairs. But I did have access to a ready supply of local small 1 person band-sawmills so I just asked around for anyone who had recently cut some 8/4 white oak that was straight. I bought quite a few boards that were less than a month after cut so they were still green-ish. I then just planed them to get a sense of how straight they were and then I ripped them on my table saw into 1.5 inch square sticks until I had enough for the legs and I did the same thing with the rungs but smaller. Then I canted the blade to 45 degrees to make rough octagons. I cut more pieces than I needed and sorted for the straightest pieces without minimal run-out. Once I got the hang of steam bending I had no real problems. I cracked my first two legs, but after that I tweaked my system soaked the legs for a week, and added a backstrap to the bending form and I never split another leg. The rungs were a bit more hit or miss, because some of them tended to warp when I put them in the kiln, but it was easy enough to expose that early and just cull the bent ones out because I cut a lot of spares. Short answer is I’m sure rived stock might technically be better, but I used modern tools on green wood to get through the grunt work and 6 chairs in a row all worked fine once i took some precautions.
My question: How do you compensate for different sized people? For example, a 5 foot tall person compared to a 6 1/2 foot tall person would probably not be comfortable in the same sized chair.
Similar to above comments, if I am building a chair for someone, is there a method of using their body measurements to set dimensions for different parts of the chair?
Wood seat chairs are often uncomfortable on my tailbone, but some feel great. What’s an adjustment to avoid that problem in the chairs I’m going to build. What’s the magnitude of the adjustment?
My question(s) is. What is the weight limit for your standard stick chair? Are there ways to increase this limit? If so how would you go about it other than increasing the thickness of the parts?
The question I have involves green stock. If I cut up and rive a log for spindles, legs, etc how long will those pieces stay usefull for chair building? Most logs of any size will give you more pieces than you can use in a single chair. What strategies can I use to save the un-needed pieces for another chair? Or do I need to quickly build several chairs to use up my riven stock? If I get a log today but won’t build a chair for awhile, what strategies do I employ to keep that log “green” until I use it? How long is “awhile”? When is the stock no longer usefull for chair building? Basically, if I get a log of any size what is the best way to preserve it until I build, make the most of the pieces (riven or bark on) as I build (say over the winter or longer), make the most of my riven stock so to maximize the use of the log, and what are reasonable time frames before I need to just square up the stock and treat it like air dried lumber? Thanks Chris, I’m looking forward to your book and the new printing of Jeannie Alexander’s book.
I live in the dessert and have very limited access to different types of wood species, will I be able to find good chair making green wood?
How forgiven are the angles of the legs. If you have a few degrees difference, at what level is it going to show?
Steaming of wood so that it can be bent into shape seems to be involved in a lot of chair making and it looks potentially dangerous (Explosions? Scalding?). An idiot-proof, step by step guide to doing it well and safely might be helpful.
Can you do the the entire process by hand, i.e. without a tablesaw, (for the chair seat,), or lathe (for the spindles), and, if you cant find a woodyard to let you pick decent wood, could you use the timber from a big box store ?
I’ve made a chair with straight tenons and a stool with tapered tenons. Which tenon shape do you find easier for beginners to get their minds (and legs….) around? Does either shape have significant advantages over the other?
I know I should use wood with curved fibers for the armbow, but I don’t have any… can I still get away with a 3-piece bow? should I do something special? How should I orient the (straight) grain? Do I need to be worried about splits during assembly?
Also, I already have a loose-tenon joinery machine, shouldn’t I use that for the armbow joint?
To me, the most intimidating part of chair design is the spindle deck. How do you go about finding the angles of the short spindles when designing a chair?
How do the tolerances in chair making compare to the tolerances needed when making fine furniture? In furniture, there are areas where one can be less precise (such as the end of a tenon going into a mortise and tenon). Does chair making have similar areas where one can be less precise?
So many comments already, so these two questions may already been asked… my apologies if so:
1) when to plug a leg mortise in the seat, and then redo it?
— Is it safe to plug a mortise and redo it almost completely on where the plug is glued in? This was my first chair, a learning chair, and did not want to waste the wooden seat.
— Issue encountered, when dry fitting the 4 legs… one leg’s rake angle was noticeably different, by my eye.
2) is there a best method for sawing and gluing up a 3/4in big box store pine board into a seat blank… similar question for the legs. Worried about glue lines and where they intercept the leg mortise in the seat blank.
Thanks much Chris and the rest of the LAP crew… appreciate all your hard work and attention to detail
P.S. I can send pictures if that would help ease understanding of the question.
-Nate Batson
This is probably more common than people would like to admit, yet I haven’t seen it covered in chair making texts in the past. From time to time I have been threatened by someone (usually French) claiming to “fart in my general direction”. Is there a saddling style or curvature that can be used to backfire on them, redirecting the stench into their general direction and leaving them with a taste of their own medicine?
I live in a forest of ponderosa pine. Is there a chair form (other than a stump) that remains robust when built with green or dry soft wood? Or are there modifications to other forms that can be made without turning an elegant shape into something…not elegant? (I’m thinking 3” spindles on a Windsor would detract somewhat from the overall impression of lightness…)
The vertical passing through the center of gravity of the person + chair must remain between the four feet.
What is the correct margin to make sure the chair will not tip back easily.
And, where is the center of gravity of a sitting person (with various back angles)?
You’ve discussed in the past how many chair parts have traditionally been harvested in the needed shape…
Does any pith make it into the project? That is to say, would debarking sticks water sprouts for the back sticks produce an acceptable chair that lasts?
Is there any record of chairmakers manipulating branches while still growing to produce the desired parts? I’m thinking along the lines of bonsai, but on a bigger scale. Maybe the image of stringing a bow is closer than bonsai art. If so, how small should this start and how many seasons might one have to leave it before harvesting?
I’m afraid I’m not experience enough to ask intelligent questions here, but these have been on my mind for a few months.
Hello Mr Schwartz , i am about to start my first chair, i’ve bought Mr Galbert’s and Mr Brown’s book and i’m about to receive Mr William’s one plus the visual record book.
I’ve learn almost everything i need to start making some Welsh Stick chairs but i would have loved to know :
– What would be the minimum diameter for legs without undercarriage (with ash or oak in a 50 mm thick base)
-Conical tenon or cylindrical ?
-About wedging: i have had some little difficulties with wedging i would have loved to have a big chapter about that, it’s the only “lack i find in Mr Galbert’s book”
– I would like to know more about gluing the seat because i do not often have plancks that are big enough.
-I’d like to find out how to make a tapered hexagonal foot as fast (but well) as possible.
As a french woodworker i have access to a wonderful tool that helps me so much and that remain one of the last but not the least made in France tool: the Hand stiched rasp, the curved one was made to curve seats (between the travisher and the scraper i guess) and i never heard of it.
Also as a philosophy and holistic woodworking process i was thinking about the chips i’m doing, and now i’m cooking with it using a plancha which is a 3mm thick stainless steel cooking device, it’s so wonderful to light a fire with chips.
Thank you for reading , happy woodworking to everyone,
Have anice day,
Cheers from France,
Jonathan.
Will this book have extensive instruction on how to make a stick chair with plywood and CNC?
how to use molded wood for the seat?
https://www.engelvin-bois-moule.com/fr/mobilier/
How can I reliably identify straight grained lumber?
If I have a decent set of tools for making square furniture, which tools should I start with and what is the minimum set of tools I will need?
I realize comfort of a chair is subjective and has a great deal to do with the size of the person sitting in the chair but given all the chairs you’ve made, have you found a sweet spot for critical dimensions ( seat height, depth and angle, back angle and height, arm height and angle etc.) that help to make the chair comfortable?
I’d like to see more info on tapered tenons vs round tenons for leg construction. Other than the obvious of the tapered tenon snugging up more over time, is there a difference in structural strength between the two? Is one more likely to fail with time and use?
This has likely been asked above, but:
For Riven components, where are you able to readily find green lumber, aside from your own backyard? C.R. Muterspaw didn’t have a lot of leads, and it can be a bit tricky to find a sawyer willing to part ways with small logs or sections therein.
A question as I work on Greenwood chairs and differential drying stringers vs. Tapering tenons:
To what degree do you try to control end-grain orientation in stock which isn’t deferentially dried, or is tapered instead of press-fit. Say for example your Irish Stick Chair from December of ‘19 vs. a Jenny Alexander Chair.
Also comes to mind, specifically for the shaker chairs; For the Seat-Rungs, wherein you’ll weave your seat, do you leave these shaped the same as others, or leave them a bit stouter, more ovaloid, so as to prevent bowing up or down?
Hey Chris, two questions:
– How do I know I’ve found a good dowel at the home center? Does it have to roll perfectly? What does straight grain look like on a dowel?
I want to build a chair from wood that doesn’t rive well (cherry or walnut, for example). What processes in the build need to change?
I live in the mountain west and do not have access to many of the traditional chair making woods from east of the Mississippi, except in a commercially kiln dried form.
What should I look for in a wood for chair making? Thinking about sourcing woods from local tree services, and local saw mills and want to make informed choices for woods and how they can be used best.
I am finding it difficult to find wood wide enough for a seat blank. Can I join two boards together to make up the width and is a simple butt joint strong enough?
I do a 3 piece glue up. I can find white pine in 12-13” and I need 18-19” wide. I cut two pieces to the right length. One will be the center of the seat. The other I rip the bastard grain off the sides of it and flip them relative to the center board so that the grain all runs in the same direction and it you look at the end grain, it looks like [)))][((())))][(((], except those parenthesis should be on a diagonal. This hides the glue joint well and has not be problematic saddling. I make painted Windsor’s, but I would do the same thing for an unpainted chair. By doing 3 pieces vs 2, you shift the glue line away from the center of focus and you are able to have the added bits be entirely bastard grain – no cathedrals to give away the glueup. Additionally, the leg joints are all in the center board, so the glue line does not experience heavy bending forces. Personal opinion is that a 2 piece seat would probably be fine structurally, but I’ve not tried it. If you are very persnickety, plane the jointed edges parallel to grain lines and the joint will almost completely disappear. I just do butt joints.
Chris, This is a question I haven’t seen discussed. You’re thumbing through a book or magazine or whatever, and see a picture of a chair that jumps out at you. Everything about it looks perfect and you think “boy would I like to build that chair… but where do I start?”
How do you go about estimating dimensions, measurements and angles from a picture? Where DO you start?
Chris, when I ream the tapered hole in the seat for the leg, should the entire bore be a shaped like a cone or is the upper portion still a cylinder?
As a fervent ADB reader and beginning stick builder, one of the biggest issues I’ve had is deciphering which woods don’t “rive easily” and have “interlockiong grain” as I believe it says in the ADB for choosing seat species.
Have had a devil of a time down here in New Zealand trying to explain to lumber yards what I’m looking for. Saying “Interlocked grain” usually just gets me the same quizzical facial reaction you’d probably get wearing a Dead Kennedy’s t-shirt to a MAGA convention.
I’ve done the due Google diligence on interlocking grain and riving in woods, but it still has not helped me decipher, and explain, which local options I can consider and/or afford.
Cheers from the bottom of the world!
I have 2 questions and apologize if they’ve been asked above. 1) I see lots of chair-making photos in which lasers are used to determine rake and splay. Are lasers so useful that they tame this most challenging aspect of the chair-making ocess? 2) I love to read the irreverent posts in which you 3 buddies critique old stick chairs; I often try critiquing them before I read your comments. I often can spot charm but can’t translate it into a chair, even in my imagination. What causes the magic?
Hi Margaret,
Rudy, Klaus and I have discussed this a few times when it comes to our “Chair Chats” (more of those coming soon).
By working together, we can usually decode a chair in 15 minutes because we are all trying to figure out how the thing works (or doesn’t). And there are three brains — all with different ideas. When I do it alone, it takes more time. But it’s possible. Usually I open the photos of the chair on a screen and blow them up as much as possible looking for clues as to how it was made.
Maybe for the next Chair Chat we can post the photos a couple days before hand so y’all can play along at home.
I’ve built three stick chairs based on the design from ADB – I repeatedly struggled at one part – the bending of the crest rail. Taking 3/4 stock and the oven roasting method was the only thing I could do at the time. No steam box, no room to keep one. I could get the heat and moisture up, no problem, but when I put it in the form and started to clamp it took an ungodly amount of pressure to bring it in and more than half split using straight grained air dried wood. I tried clamping my form to the tail vise and it would just slip off. I tried using bar clamps with it flat on the bench and this was easiest but the form still wracked on me and without a compression strap, they repeatedly broke which was disheartening. Did eventually get three built with stubbornness and time.
Now I’m working on back chairs like in the ADB Updated, making armbows with doublers and I’m finding a similar singular struggling step. After drilling out holes for the spindles on the armbow and seat blank, using layout sticks and a spotter to get as close to perfect as possible (and plenty of “meat bushing” heat burns), I get everything set to drive on my armbow, get the spindles started, and drive it home. Takes a bit more whacking than it should and the armbow delaminates. Happened twice. Got the third one to stay on by putting tenons fully through the armbow first but it was a fight and even it started to come apart at the end. I have a whole second seat saddled and legged up – ready to have an armbow installed but I’m nervous to keep breaking armbow assemblies until I figure out where I’m going wrong.
As a quick aside, if there is anything similar in MACFAT- I have been learning ladderbacks while above partial stick chair collects dust and I would love to know more about bending forms – I only ever use the one published because I can’t figure out the geometry of curved sticks and how that fit in with the back slats, etc. Sorry for the long post, just wanted to get the details in. Thank you as always for excellent and thorough material.
Sorry – forgot the essential question. What’s the expected failure rate for assemblies for newbies like myself? If this is normal, then I’m happy to keep chugging along knowing it will get better with practice. Thanks!
Hi Chris,
What glue are you using to assemble the armbows? If it’s Titebond Liquid Hide that might be the problem. Lately we’ve had some problems with it in our shop (could just be bad luck). But as soon as we switched to Old Brown or even PVA for the armbow, the problems went away.
Sure is Titebond Liquid Hide glue. I’ll switch it up – thank you for the feedback and really looking forward to the book!
Hello again, an other (and maybe a hundred) question came into my mind, or maybe more a thought:
It would be , to me , very interesting to have your thoughts and experience with your customers, at the end the dream of many of us is to make a living selling chairs (it’s mine) , but the experience of dealing with people when it’s about explaining why the chair (as one of the first) is not perfect but deserve (or not ?) to be sold at that rate is a priceless experience and i’d be happy to read a few words about that when i’ll receive my copy of your book.
Have a nice day,
Jonathan
This may not be applicable, but woven seat chairs. How do you prepare the bark for weaving, which bark is best. Does the bark have to be treated in any way. How long will a woven seat last?
Just modified my shave horse to do chairs instead of bowls. Really looking forward to starting. My first chair is going to be a local design called a Sugán (“Sue-gawn” local to west of Ireland I mean) made of Ash.
Really love the books, Looking forward to the release of make a chair from a tree.
Do you ever measure the leg angles off the floor instead of the seat?
Mainly rake angles when looking at a side view…
This may not be apropos, or it may be too specific. we’ll see. My question/problem is tolerances. Like so many, working in a vacuum, I’m never sure when close enough is close enough. That is particularly true in setting up for and drilling compound angles. Tables, chests, etc square is square. Chairs and benches are another matter. Any acceptable variations?
Years ago in a Krenov book there was a section on correcting one’s mistakes. At the time that section set me free. It acknowledged mistakes. (I had already fixed many and always felt like I was somehow cheating!)
Thanks again for what you bring to the woodworking world.
For a hobbyist who has to approach chair making as time and responsibility allows, do you have any ways to help us stay on the tasks and not get lost in the one step forward, two steps back, oh, “I forgot about that”, or “I wish I was thinking of this earlier.” So much of my hesitance is that I feel the drips and drops of time I can spare don’t allow me to develop a rhythm and flow.
Is it better to have a loose joint so the glue has a place to go?
If a joint is too tight, will it squeeze out the glue and “starve the joint”?
A what angle starts strait grain to be end grain as far as gluing is concerned? I’ve been thinking for a while about gluing a thin continuous armrest together out of wedges, see drawing. S?#$#@! no drawing
I am a big fan of George Walker’s and Jim Tolpin’s ‘By Hand & Eye’, and the use of artisan geometry and classical proportion in furniture design. Can these principles be applied to Windsor and Welsh chair design? For example, proportions for the length, width, and back radius of the seat (when designing an oval, D, or shield seat); a proportion for the radius of the back of the seat compared with the radius of the arm rail? Any useful ratios like these would be great!
It seems angles are a tricky part. Does thinking of the angle as a slope help? By this I mean if I know the height I want and how much behind the seat I want a leg to go, that rise and run defines the angle well enough I don’t need to know what the angle is, as long as I can drill so that the line goes through the points I note. Knowing where I want to put the foot to the side and back can define a compound angle that is easily adjusted as I move around the drilling spot.
Old timers without lasers were doing something by eye that worked well. I wonder if it was something like this.
If you prop up the seat at the height and slope you want to sit, then make a mark on the floor where you want the foot, you could bore from the top, aligning your line with the spot on the floor. That takes care of compound angles.
Not sure if this goes with the book but here goes.
How do you go about caning for the chair seat? Do I have to use hickory, ironwood, or elm? Or could I use hard maple instead?
What tools do I need to cane?
How much time do I have until the tree is felled before it’s too late to collect the strips.
I’m finding very little information on the subject thank you!
Did you ever make those saddled plywood seats? I tried it for some stools and got a neat pattern with those layers, but boy is it tedious and unforgiving work. It brought up some concern that the glue might damage my edge tools, but I don’t see any evidence or I need new glasses.
Does the lightworks template for stick chairs suit both high back and low back or are there subtle differences for that design?
Keep up the good work, looking forward to it.
I haven’t made the plywood chairs yet. But I will (after this book is done).
The plywood templates will be very helpful for three of the chairs in the new book that use the same seat. And the arm and doubler templates will be a good foundation for the lowback and comb-back in the book.
Is it possible to bend the sticks of the seat back to make them ergonomically good for a bad back? In other words, I have to have a chair that forces me to sit up straight with the correct curvature for my spine. It’s hard to do that with traditional chairbacks, which are straight. I want to attempt this but that concern is real.
In contemporary chairs, ergonomically bent backs are common. Not so much in vernacular stick chairs. There are ways to make stick chairs more ergonomic (adding lumbar support, for one). But there are limits to the form, which relies on simple construction and straight sticks.
Carving the seat by hand scares me. I doubt I would make the two halves even. Is there a way to make it symmetrical?
This question concerns wedges and legs with compound angles. Do you drive the wedges in parallel with the seat top, or, try to follow the trajectory of the leg? If one goes level with the seat, the wedge width will have to be wider than the leg width, to make up for the elongated kerf. If one drives the wedge in line with the leg angle, you almost need a compound angle on your wedge so it fits correctly?
The wedge follows the grain of the leg (or stick). Wood deforms quite a bit (even oak). So a wedge with a 2° or 3° included angle that is a little wider than the tenon will cause the tenon and wedge to fill up the hole.
I just sat in/saw the most comfortable chair in the world. What photos/measurements would help me preproduce it?
My white whale is a chair I sat in at a pop up bar in Atlanta and just discovered that it might be a Marcel Kammerer no. 1761 from the atlas of furniture design I Nos 85-111
Do I need to add stretchers?
Mitchell
Seat thickness: From ADB, I started with a back stool 3” thick seat), made a chair (1 7/8”) then the staked arm chair (1 3/4”). Then went to make a cardiganshire type three legged arm chair/smokers bow and grappled with how thick to make the seat. Started closer to 3” then planned it way out toward 1 3/4. Saddling seems to want for a thinner seat but how do you approach it? Do you compare to thicknesses of other parts (arm or doubler?)?
Do I really need to use different species of timber for the legs and seat? Won’t this look silly?
What about the spindles, crest, and arm rest? Should these be the same wood as the seat, or the legs, or do I need a third wood for them?
Can I make a servicable chair using construction lumber?
Braces come in 2-, 3-, and 4-jaw versions. Which one should I get? Do I need all 3? Does this change if I use vintage tapered shank augers or modern cylindrical or hex shanked augers?
Chairs have a lot of parts and funky angles, how many clamps am I going to need?
Are there any specialised chair making tools that are essential, or can I do everything with ‘standard’ tools?
Are there any finishes I should avoid on chairs?
Do I have to use hide glue? Wouldn’t a modern glue like epoxy make a stronger chair?
Steam bending seems difficult and dangerous. Can I just cut out all the curved bits on the bandsaw instead?