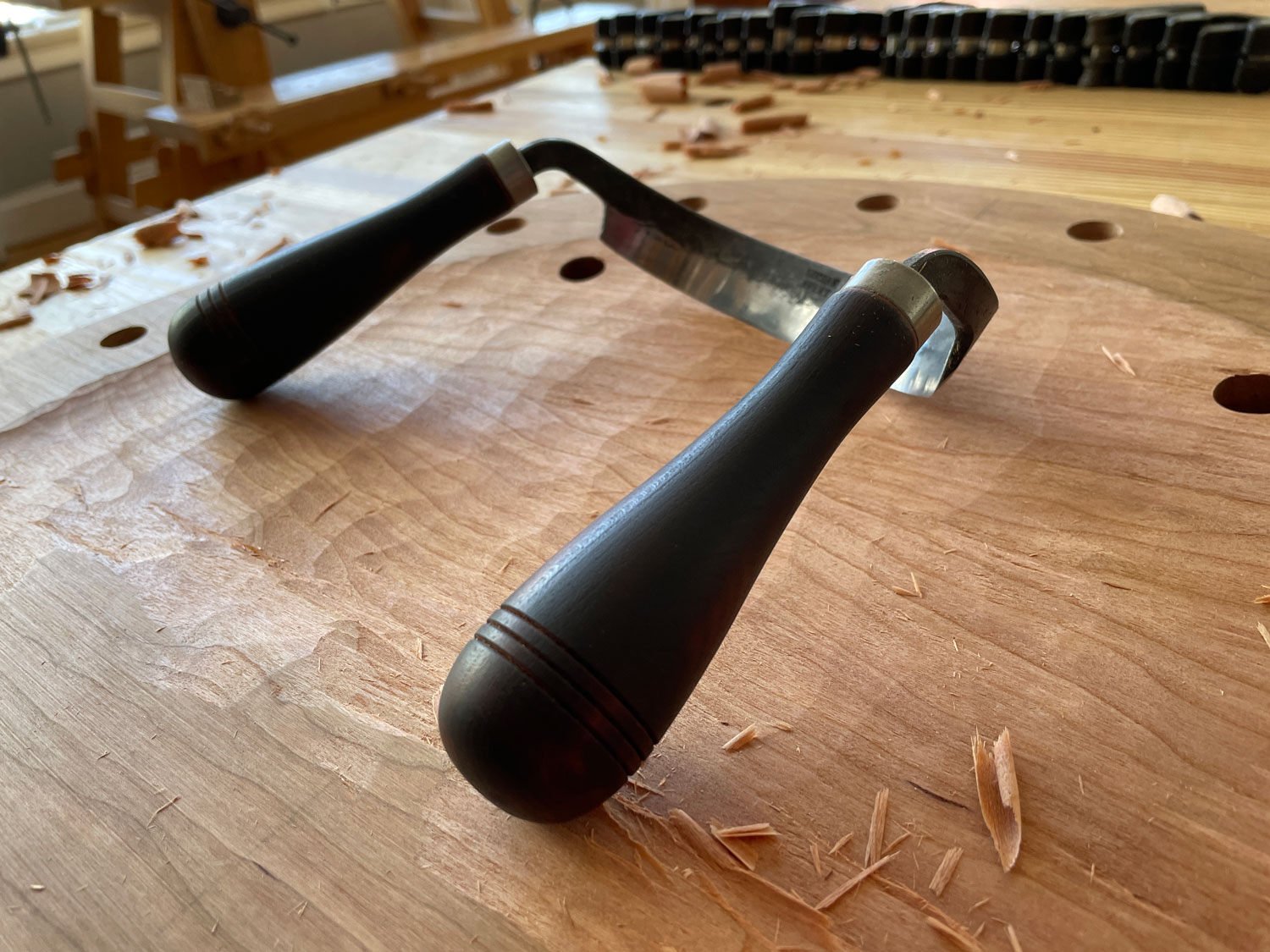
Since we started making tools at Lost Art Press under the Crucible name, I have avoided writing anything that could be considered a tool review, save for my annual Anarchist’s Gift Guide. It doesn’t seem fair for a toolmaker to pass judgment on other toolmakers.
However, during my research for “The Stick Chair Book,” I have been purchasing and using all manner of new-to-me chairmaking tools in order to understand different approaches to the craft. Some of them have been duds, of course. But some of them have opened my eyes.
Because a book is a terrible place to review a tool, I am going to publish my thoughts on many of these tools here on the blog. As always, I pay full price for all my tools. I don’t exchange reviews for anything. And I hope that this is one of the reasons you are still reading this ancient blog.
The first tool I’d like to talk about is the inshave made by blacksmith Lucian Avery.
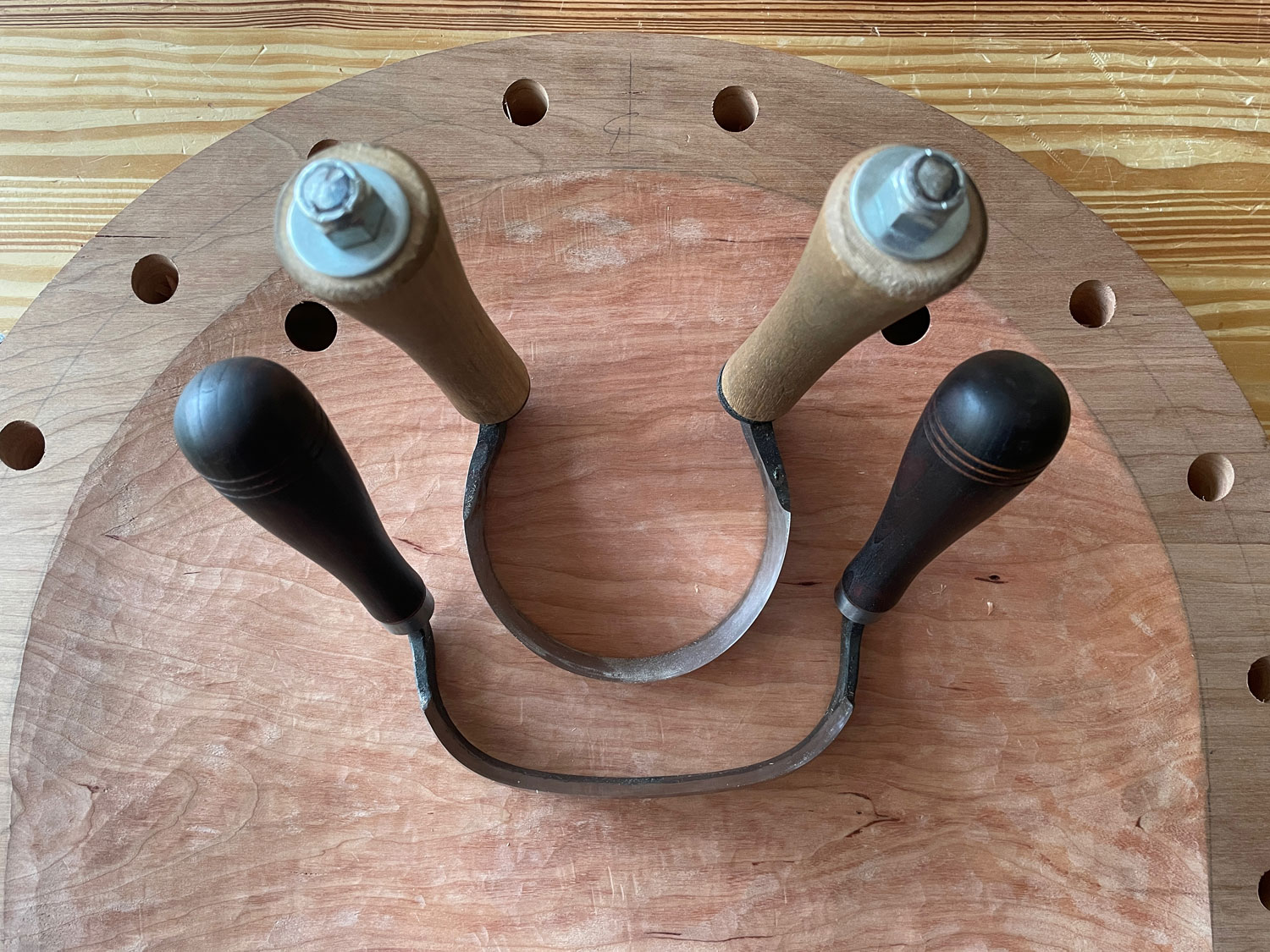
Lucian Avery Inshave
For almost 20 years, I’ve used the same inshave/scorp from Barr Tools to saddle all my chairs. Barr Quarton doesn’t make this exact scorp anymore, though he makes a similar one called the Mike Dunbar-Style Scorp.
It’s a hell of a tool. Of all the hand tools I’ve owned in my life, I haven’t owned a tool that takes a better edge or keeps it longer. (Yes, even premium Japanese tools.)
Its handles are dark grey from my sweat and grime. If you own one of my chairs, this tool saddled its seat.
For “The Stick Chair Book,” I wanted to try a different style of inshave, which has a flat curve along most of the blade with tight-radius corners. I did a lot of homework and settled on an inshave from Lucian Avery that was designed with the help of George Sawyer (Dave Sawyer’s son).
I don’t make Windsor chairs, but I thought the flat curve of Avery’s inshave would help me achieve the shallow saddle found on stick chairs – with a lot less fussing.
As I mentioned, I’ve been using the Barr scorp for a long time, which has a tight-radius curve – 2-1/4”. It can hollow out a seat with incredible speed. The downside to this shape is that it’s easy to overdo it. An errant stroke or two adds a lot of work with the travisher later.
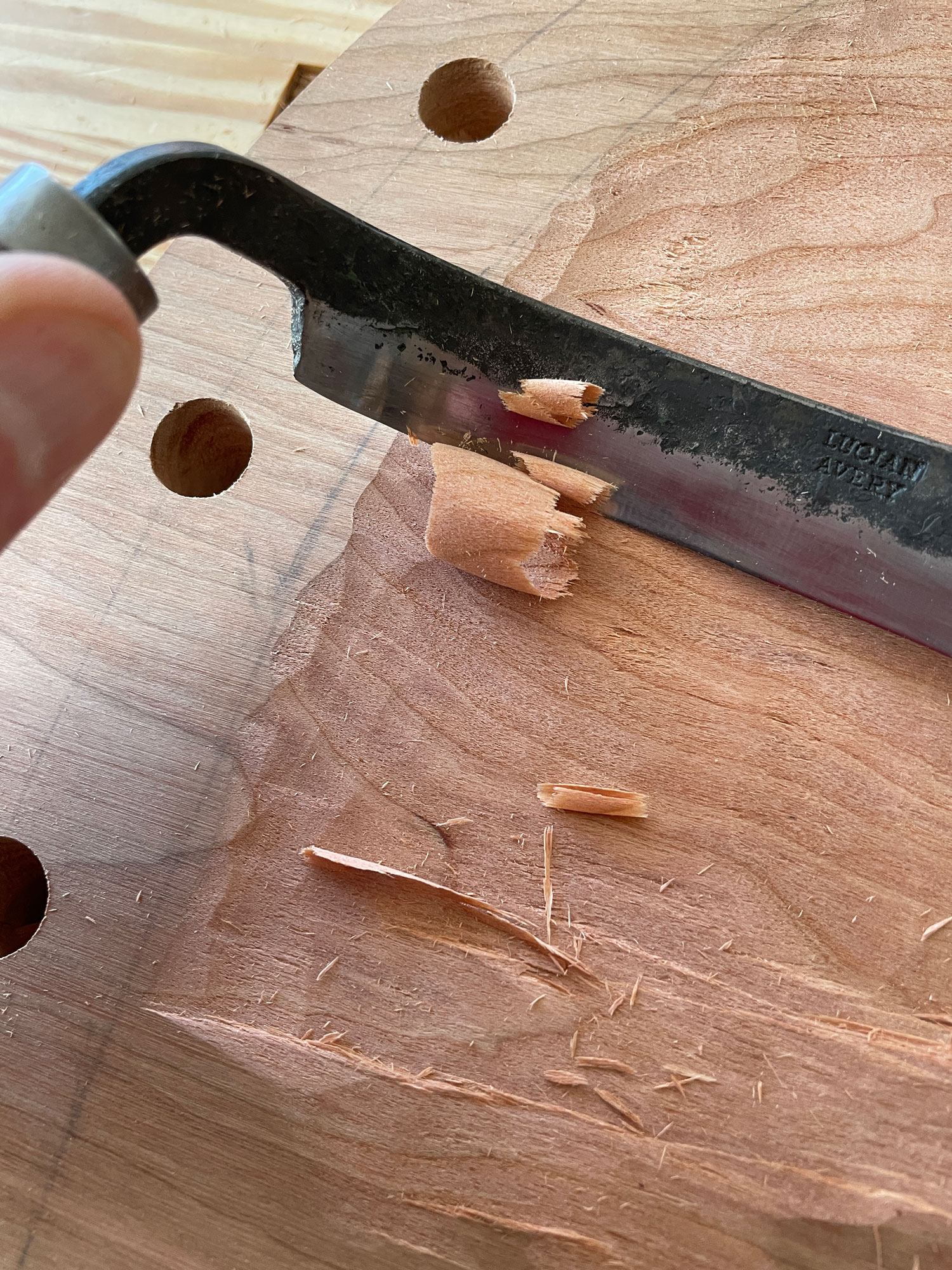
The Avery inshave is different in every respect. The tool is half the weight of the Barr (9 oz. vs. 18 oz). The handles are in a much lower working position (2-3/4” off the bevel as compared to 4-3/4” off the bevel). But the biggest difference is the shape of the blade. The shallow curve is not as aggressive, but it leaves a much flatter and smoother curve behind. Yet, the tight-radius curves at its edges allow you to carve along the spindle deck with confidence.
In short, the shape of the Avery tool is much more suited for the type of saddle I carve. The saddle is much flatter, which cuts down on the time I spend with the travisher considerably.
As a bonus, the lower handles and reduced weight of the Avery make the tool less tiring to use.
I’m in love. It’s an extraordinary tool. Light, nimble and responsive. I look forward to using it as much as my travisher.
The current price is $263, which is a beyond-fair price for a blacksmith-made tool of this caliber. It also comes with a clever rawhide sheath that adds no bulk or real weight to the tool.
If you make stick chairs and need an inshave, this one is perfect.
— Christopher Schwarz
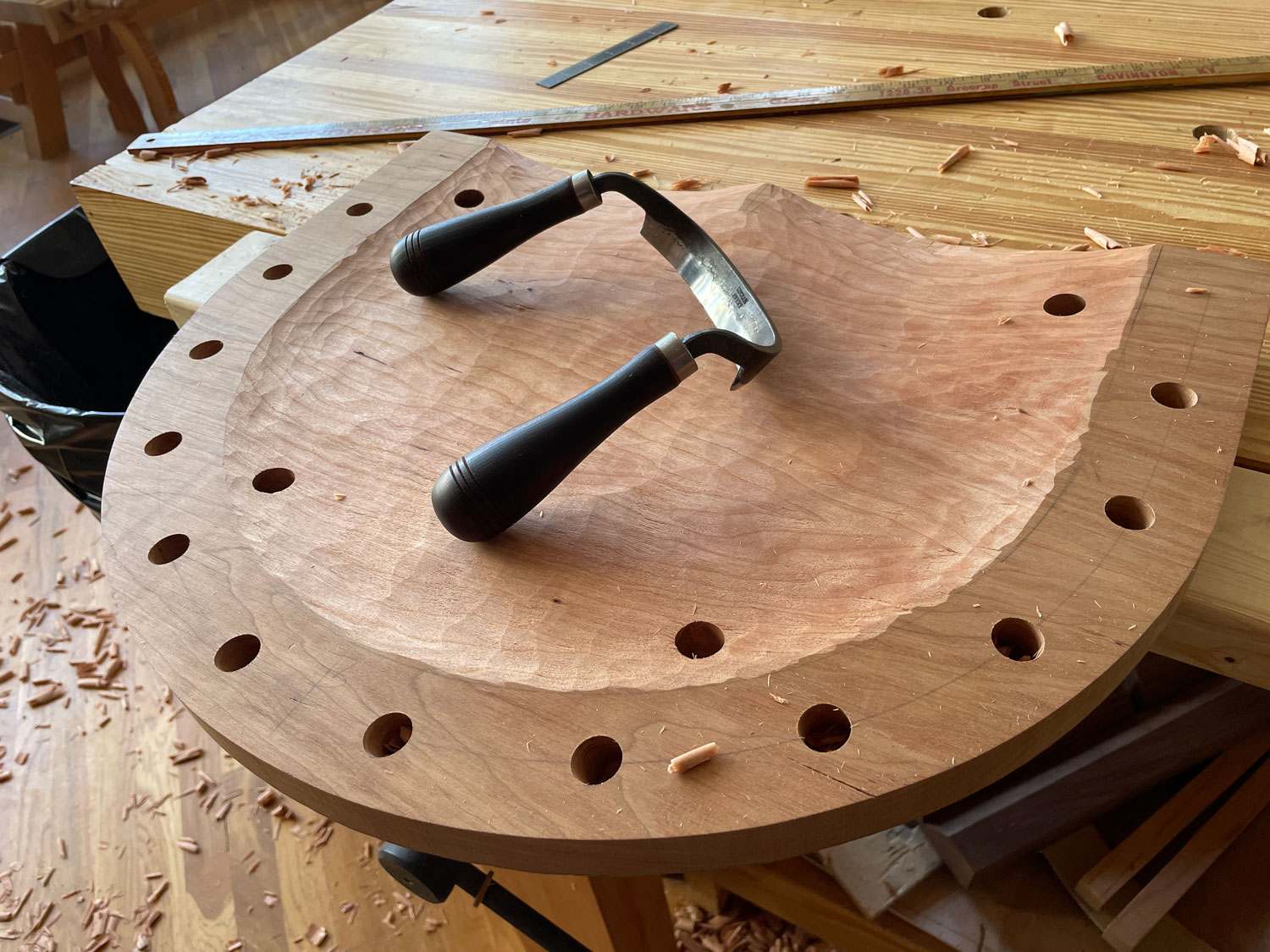
The inshave Matty Sears made for me is a thing of absolute beauty. More like the Barr in terms of radius, holds a wicked edge
what is the secret to sharpening an inshave? best position to hold it to sharpen?
I use two approaches.
Treat it like a carving tool and strop it continually. That’s what I have done with my Barr inshave for 18 years and have never had to regrind it. I just strop with a dowel on the inside curve and a flat stop on the outside.
A hard felt wheel on your grinder with honing compound does the trick marvelously, too. You have to built a little platform for the tool, but once you do it’s cake.
this one was bought used and definitely needs a file on it. can’t find a name on it but is well built in my limited knowledge.
Grinding? I do it on a disc sander with the machine’s table tilted in.
Curtis Buchanan – chair maker – has a great video of how to grind a scope/inshave. I can’t recall if on his instagram channel or website. He does it with a slow speed grinder if I am not mistaken using a platform similar to what Chris mentioned for honing with a hard felt wheel. The technique works equally well on a wet grinder (Tormek/similar) as well.
All my life’s a circle. Once upon a time, scorps were shaped like this one. I looked in my Woodcraft 1984-85 catalog, and they sold a German inshave with a blade weight, shape, and geometry very similar. The blade simply says Germany, and my guess was Ulmia. That was the year Mike Dunbar’s book came out, and he pretty much drove scorp development after that, as with the excellent Barr tool. Flat bottomed inshaves were considered all wrong, and the circular shape was in. Since no one else made them, a lot of the German shaves were reworked to the circular shape.
I looked in the same catalog, and saw I paid 16 bucks for my Starrett 92. I lived 30 minutes from the only Woodcraft in the country back then.
It seems like I’ve been here before;
I can’t remember when.
Hi John,
I have long shared your bewilderment. After many many M-WTCA tool meets I realized that both shapes were out there and both were common. I think we as a group have made some fundamental errors – like confusing some leather-working tools for travishers. I am tempted to dig into the historical record and try to find some clarity. There seems to be some cooper’s tools that have gotten into the mix.
Chris
A friend in Italy sent my some pics of an travisher / scorp type tool. Liked to have a handshroud , but I noticed it did indeed have this same shape as Lucian’s inshave.
My friend is in a big wine region and said that’s what it was for.
Drew Langsner used to sell an inshave that was similar to the Avery model with flatter middle. Drew knows a thing or two about chair tools! And of course, Dave Sawyer was one of the first instructors at Drew’s. I recently bought one of Avery’s, too, and really like it. It takes some getting used to with the lower angle after also using a Barr for a long time (Dunbar style). As an aside, I never understood why Barr had the bevel on the inside of the tool either. As mentioned, Avery’s is very light and nimble, and comes sharp as all get out.
Chris, where do you position the Ray Isles scorp? I have one, and the blade curvature seems to be in the middle of these two. Regards from Perth, Derek
I think as long as you are not advertising the makers with paid-for ads, then your opinions on tools should be honest. It should be ok for them to send you free tools but only give reviews for the ones you like. The not so good ones you just send back and don’t comment on. Collect enough free tools and then put them in a ATC and auction it off, giving the money to a worthy group (The School of Woodworking in Florida scholarship fund comes to mind.). Look forward to what you say about travishers. The one from Travisher.com looks interesting and so do the ones from Claire Minihan.
Hi Eric,
Every person who writes about tools has to wrestle with this issue and resolve it so they can sleep at night. For me, I have to fall back on my journalism training. So nothing for free. Most of the tools that I release back into the wild are given to young woodworkers gratis.
We support Kate and her scholarship with direct donations of cash and books for her auctions.
I have been using one of Mursell’s wooden travishers for a few years now. It’s an unusual design but works very well. Some people really take to that particular design. I am also trying out his new 3D printed (I think they’re 3D printed anyway) tools and will write about those. I have huge respect for Mursell, his skills as a chairmaker, teacher and toolmaker.
Excuse my 2 cents worth, but I haveboth sweeos of the Minihan travisher, and they are a joy to use. I can’t imagine they could be improved upon. And they are just gorgeous objects as well. If I recall correctly, I think Pete Galbert had a hand in designing them.
I bought mine. The only thing anyone has given me is a hard time.
Claire’s travisher is my favorite. I have one of the early ones that she made with Peter. It can be a long wait to get one….
There are lots of travishiers out there that work really well. I’ll be posting about them in the coming weeks I’m sure.
Hi Chris,
Your “never sponsored” stance along with your no nonsense evaluation of tools are certainly reasons that I still enjoy your blog. As a toolmaker myself, I have found insight in quite a few of your posts. One of my favorites was from several years ago when Jeff Burks wrote about David Maydole, the inventor of the adze-eye hammer.
Regards,
Jason Lonon
Inshaves are interesting creatures. Many German ones are flat-ish bottomed. The more round ones often have only one handle. Google “Fasschaber” for some examples. I own the one made by Kirschen (two cherries tools), which has a flat bottom. It works well on seats. I would imagine coopers used their inshaves on the inside of their barrels, where there was not enough space for a wider tool. Some cooper tools look like a combination between a draw knife and an inshave. These were used at the shaving horse to make the barrel components concave. I believe there is a video somewhere online with Swiss cooper Rudi Kohler. “Fass” is the German word for “barrel” so the translation would be barrel shaver. I see a lot of antique ones on eBay and they come in both variations, round and flat bottomed ones. I assume they were used for different tasks in cooperage, perhaps having to do with the size/diameter of the barrel.
Chris, how do you refine the inner perimeter of the spindle deck? Also with the inshave?
The inshave gets me close to the spindle deck. Then I finish the work with a travisher. It works both across and with the grain.
While I can appreciate your high standards of conscience, if you’re not actually in direct competition with them, I think your opinion actually means more. If crucible was making inshaves, it might seem a bit questionable in one direction or another. But when you, as a toolmaker, can offer an honest, but helpful evaluation, there’s a lot more on the page, so to speak.
Because you’ve been there, you’ll have a much better appreciation for value/ dollar, and which corners can justifiably be cut. (ie, this part wasn’t made fancy, because it doesn’t need to be. This part here does the actual work, and it’s clear that they spend most of their money making sure that part is spot-on…)
My .02. Obviously, your conscience has taken you to good places.