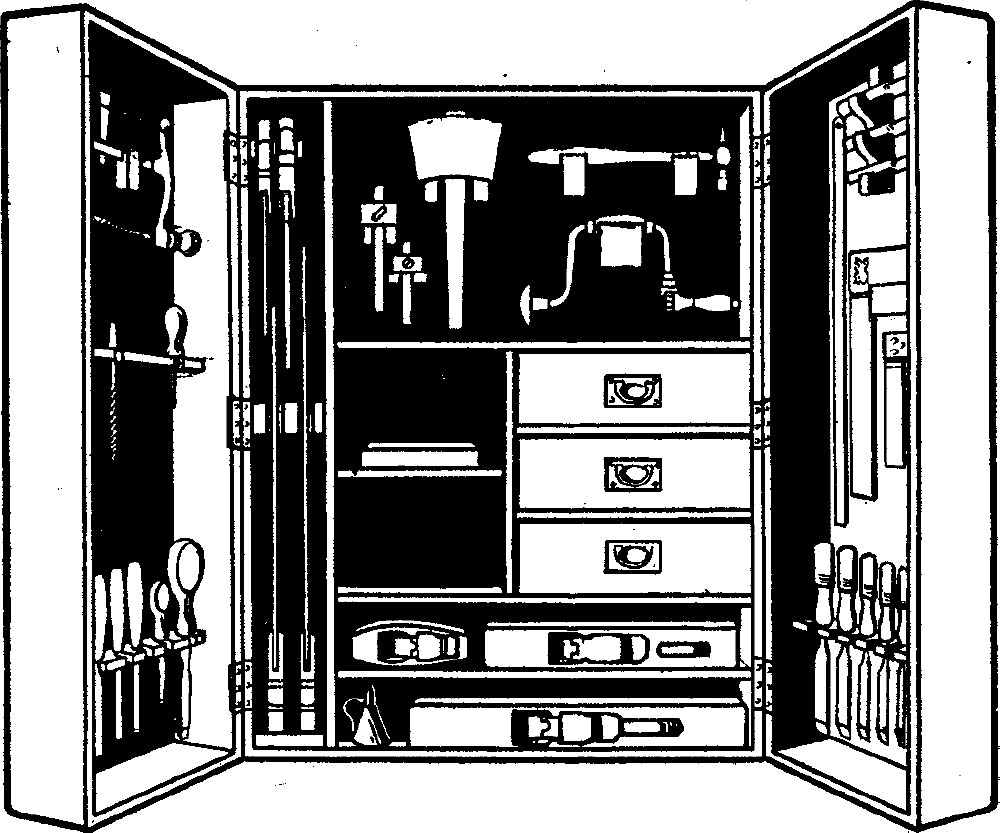
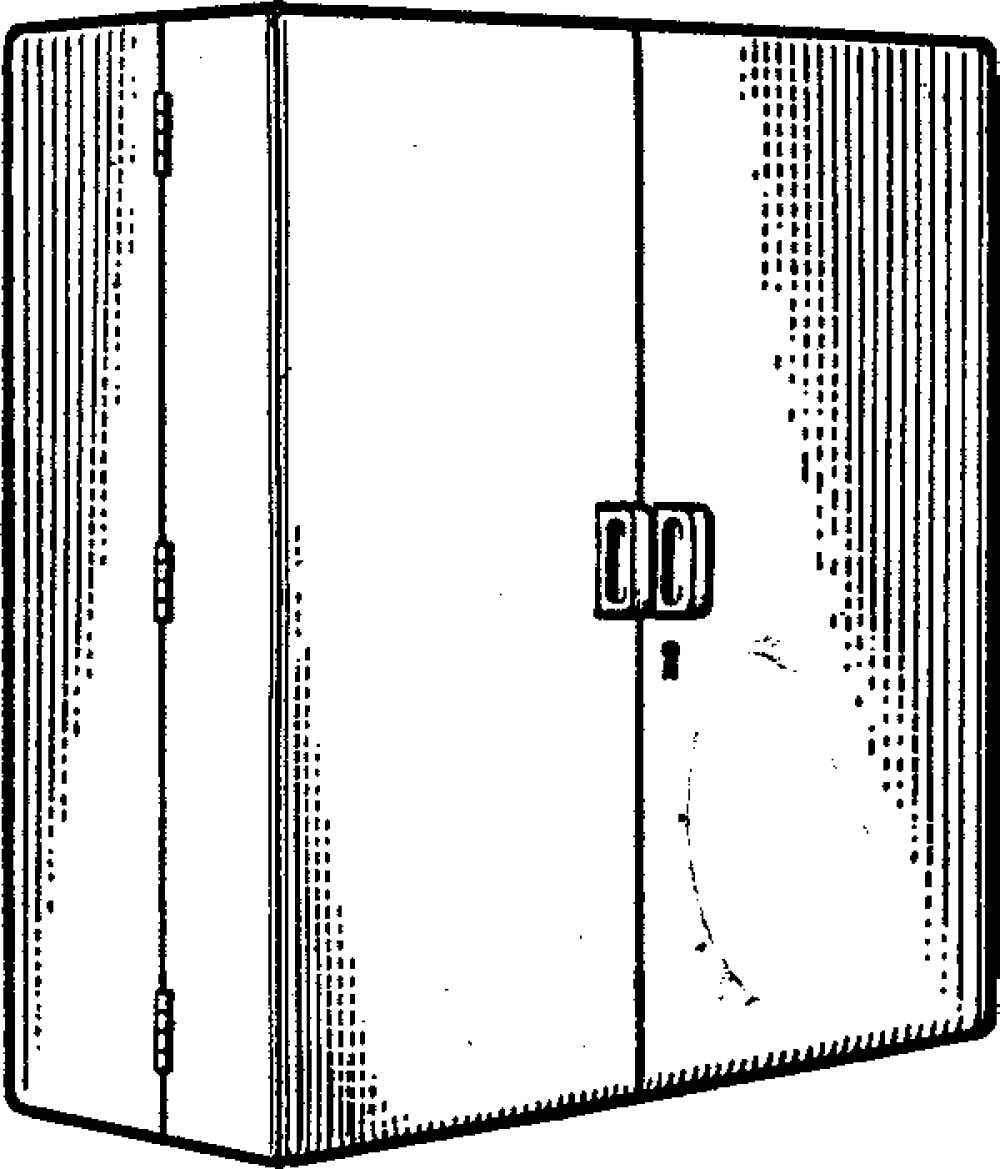
This is an excerpt from “The Woodworker: The Charles H. Hayward Years: Volume IV” published by Lost Art Press.
A sense of orderliness in woodworking is an important factor contributing to good work. For instance, the bench should be clear of tools, excepting those in immediate use, and when a tool is no longer required it should be replaced in the rack or tool chest. By far the most convenient arrangement is to have a tool cupboard fixed to a wall at the back of the bench and above its level so that shavings are not swept into the cupboard. With such an arrangement, the tools are within easy reach of the worker and, when not required, can be safely stored.
In the tool cabinet shown in Figs. 1 and 2, the tools in frequent use are arranged so as to be close at hand. The heavy tools are accommodated in the cabinet proper, and the relatively light ones in the boxed-in-doors; thus, no undue strain is placed on the latter. The three drawers are intended for screws, nails, and various small tools. As most workers prefer to use a combination plane instead of separate tools for such operations as ploughing, rebating, etc., a space is provided for the box in which the tool is usually kept. It will be noticed that the saws are placed edge-wise in the cabinet.
This effects considerable economy in space as compared with the usual method of laying them flat. Incidentally, the tools shown comprise a useful kit, enabling a variety of work to be done.
As chisels are more in use than gouges, the former are placed on the right hand side of the cabinet and the gouges to the left. It will be seen that the setting-out tools are together on the right hand side, excepting the marking and mortise gauges. All of the tools will be easily recognised, except perhaps the bevel shown at Fig. 3 (a).
The tools shown in Fig. 3 are all drawn to scale and the cabinet is dimensioned to suit the layout of the tools.
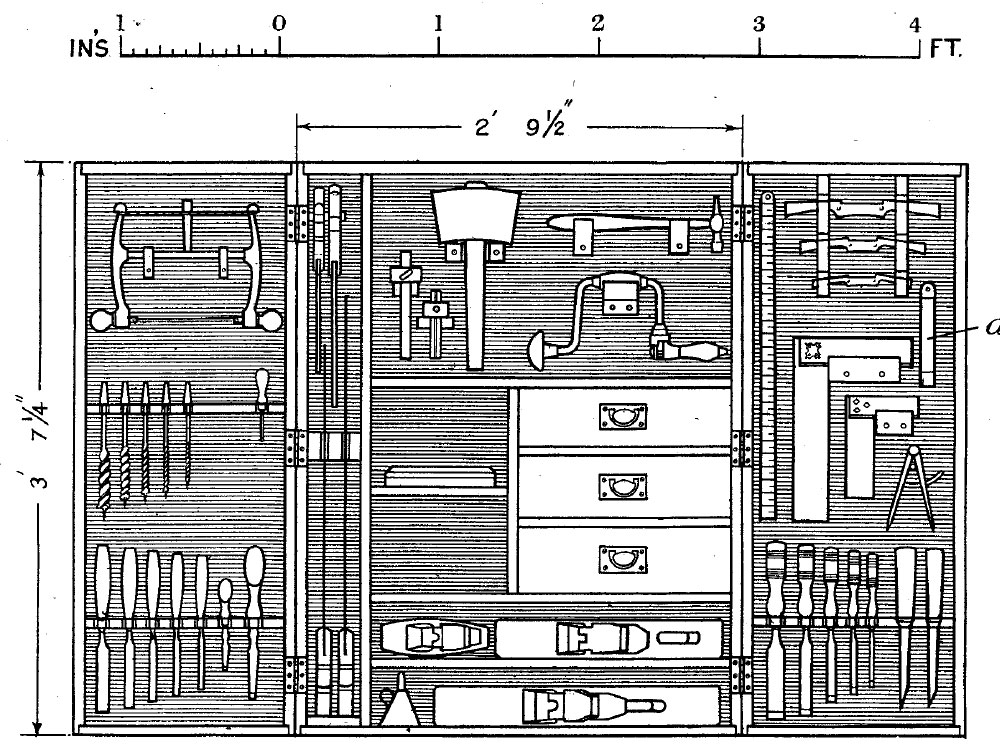
Construction. The carcase, Fig. 5, can be made from 7/8 in. stuff, finishing 3/4 in. As the cabinet is divided by shelves and partitions, a good fixing for the back can be obtained; therefore this may be of 3/16 in. ply. It is not possible to form the carcase and door frames in one and separate one from the other, as would be done in making a box, since the two doors frames have to fit closely where they meet centrally. If they were made with the carcase, sufficient material would not be available for cleaning off, to obtain a good fit. If possible, it is advisable to true up the stuff for both door frames together and rip the stuff down for the sides and ends for each frame. Rebated joints will suffice for the sides and ends of the carcase, and also for those of the door frames. The parts, of course, could be dovetailed.
The partitions (b) and (c) are secured by stop housing; as also are the shelves (d), (e), (f ), and (g). Although this may seem an unnecessary elaboration, it is well worth while since, if the grooves are set out accurately, the shelves will be found to be parallel and no trouble will be found in fitting the drawers. This might not be the case if the parts were nailed together. The plywood back is fixed and pinned in a rebate, as shown in Fig. 6, and it will be necessary to reduce the width of the shelves and partition by an amount equal to the depth of the rebate. The drawer rails which can be 1-1/2 in. by 3/4 in. are ploughed on their near edge, as shown in Fig. 7, the ends of the runners being tenoned into the grooves. The rails and runners are glued together and pinned to the side of the cabinet and the partition (c).
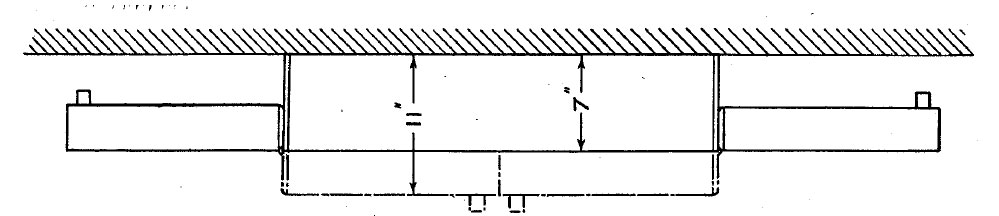
Drawers. The construction of the drawers is shown in Fig. 8. The fronts are made from 3/4 in. stuff and the sides 3/8 in., the back being of similar thickness. For the bottom 3/16 in. ply is suitable. This is ploughed into the front and sides and pinned from underneath to the back. If it is desired to have one or more partitions, it is best to stop house them into the front and back, as shown, rather than nail them in position.
If the worker is uncertain of making a success of the lapped dovetails, the fronts could be rebated at the ends and the sides secured in the rebates by gluing and nailing, using 1-1/2 in. oval nails. If possible, 3/8 in. or 5/16 in. ply should be used for the door panels, as ply of the thickness stated will enable the outside edges of the doors to be rounded which will have the effect of improving the appearance of the cabinet.
Tool Supports and Racks. The profile of one of the spokeshave racks is shown in Fig. 9. In order to avoid short fibres, the grain should run lengthwise. The semi-circular rests can be formed by boring with centre bits according to the size of the spokeshaves, and then cutting to shape with a bowsaw and finishing with scribing gouge and chisel. Fig. 10 shows one of the supports for the hammer. The two are made together by boring a central hole and then cross cutting.
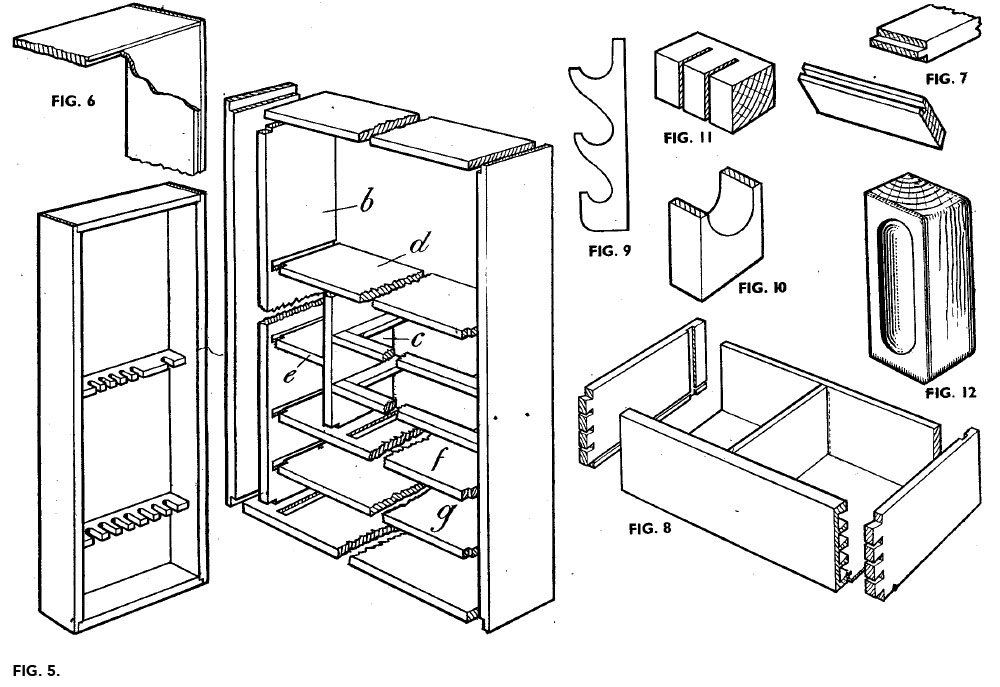
In order to position the rip and handsaws in their pocket a block is positioned centrally, Fig. 3, the blades of the saws resting in saw cuts in the block. The block is shown in Fig. 11. The tenon and dovetail saws are hung on a wooden peg which should be slightly recessed on its upper surface in order to prevent the saws slipping off the end of the peg.
The formation of the other supports and racks will be clear from Figs. 3 and 5. As it will be difficult to obtain a good fixing for the supports and racks from the front, it is a good plan to first glue them in position and then when the glue is set pin or screw each from the back, taking careful measurement in order that the pins or screws will enter each part.
Finishing the Cabinet. A pleasing form of handle for each of the doors is shown in Fig. 12. A recess is cut with a gouge on each side and the projecting edges of the handles are rounded. The handles are secured by gluing and screwing from the back. A satisfactory finish to the cabinet can be obtained by sizing and then applying two coats of knotting, or, alternatively, the cabinet can be painted according to the taste of the worker.
As the cabinet with its tools is of considerable weight, it would be as well to support it on two iron brackets, the attachment to the wall being effected by plates positioned towards the top of the cabinet.
— Meghan B.
Reblogged this on Preindustrial Craftsmanship and commented:
Arranging your workspace and tools is critical, and one of the most difficult things to do. Here is a good post of an excerpt from Charles H. Hayward – The Woodworker. It is pitching a reprint of the book but worthy of a read nonetheless.
never tried to work out of a chest like this. I think I have to many tools.
This would look really nice if the interior was made out of mahogany and ebony. Maybe some ivory accents. Then we could really layer the tool storage to maximize interior space. Hmmm.
I was surprised at the mention of a combination plane. I guess I’ll continue to use both of mine.
I think the chest will suit my woodworking style.
Thanks for the article
I don’t understand what Figure 7 “Runner Fixing” means and I don’t see where in the diagrams something like this is used. I would love to know what that is.
Thanks for the terrific article.
It’s not the most straightforward explanation but it is in the text-
“The drawer rails which can be 1-1/2 in. by 3/4 in. are ploughed on their near edge, as shown in Fig. 7, the ends of the runners being tenoned into the grooves. The rails and runners are glued together and pinned to the side of the cabinet and the partition (c).”
It seems that the idea is that the crosspieces below the drawers (side to side) are to have a groove on their back edge for their full length with the drawer runners (front to back) having short tenons. That group is pre-assembled then pinned to the side and the vertical divider.
“Near” doesn’t make sense in that case but I suspect a typo and think that “rear” might have been intended.
The use of ‘near’ is correct. It is referring the to the edge nearest to you in the 3d sense of figure 7. The sad part is that I’m old enough to remember talking about perspective drawings in this manner. Using ‘rear’ would totally make sense if you think of standing in front of the completed piece. 🙂
If I understand these last 2 replies-thank you-the 2 rails shown in fig. C are both supporting the drawers which have tenons on the bottom (of the drawers) which fit into mortises on both side rails on which the drawers glide back and forth. I don’t see the mortises in the drawing C.
I haven’t seen this article before despite collecting Haywards writing when ever I come across it. I have made a similar wall cabinet. The carcasse is dovetailed sapele and I have added a second pair of “doors” behind the first. I say doors yet they are simply panels that give extra hanging space. I use what some call “French” cleats to hang it and these have not moved despite them holding a huge weight. The finish is wiping varnish on the outside only. There is no sign of the tools rusting despite our shop being very damp.