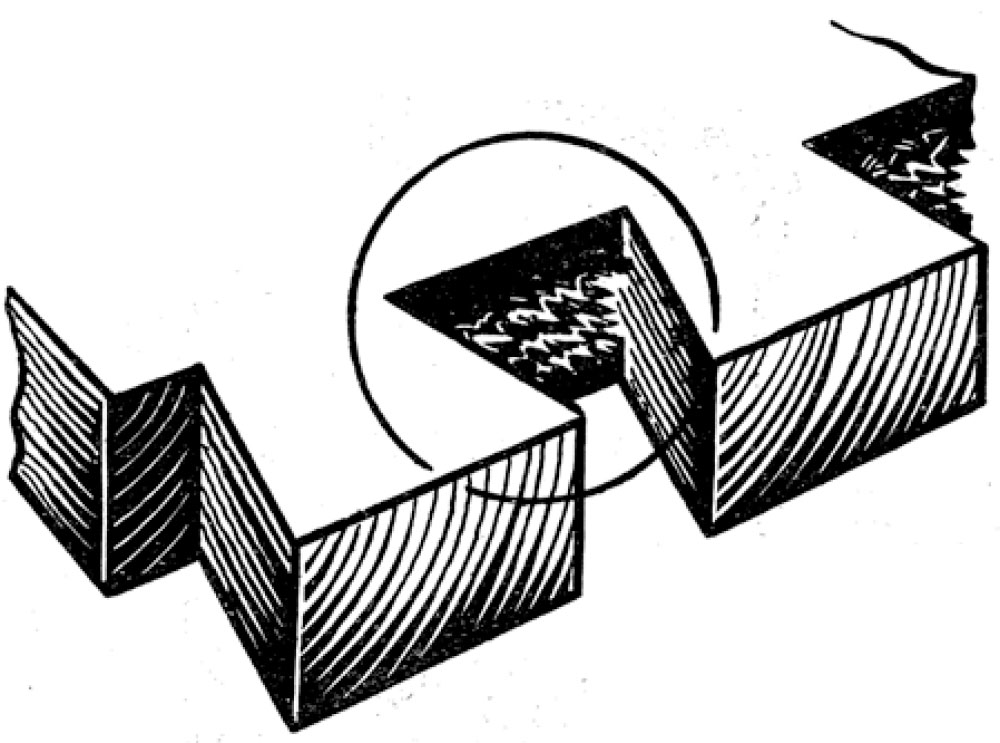
This is an excerpt from “The Woodworker: The Charles H. Hayward Years: Volume III” published by Lost Art Press.
This is a common fault even amongst experienced men who should know better. The wood between the dovetails is torn out, leaving an unsightly gash which robs the joint of much of its strength. In nine cases out of ten it is concealed when the joint is assembled, and this is probably the reason why so many do not take the trouble to avoid it. There are cases, however, when the blemish is seen, especially when the wood tears just below the surface. When the joint is levelled it is easily possible to plane into it with the result that an unsightly gash is disclosed. The fault is easily avoided as explained below.
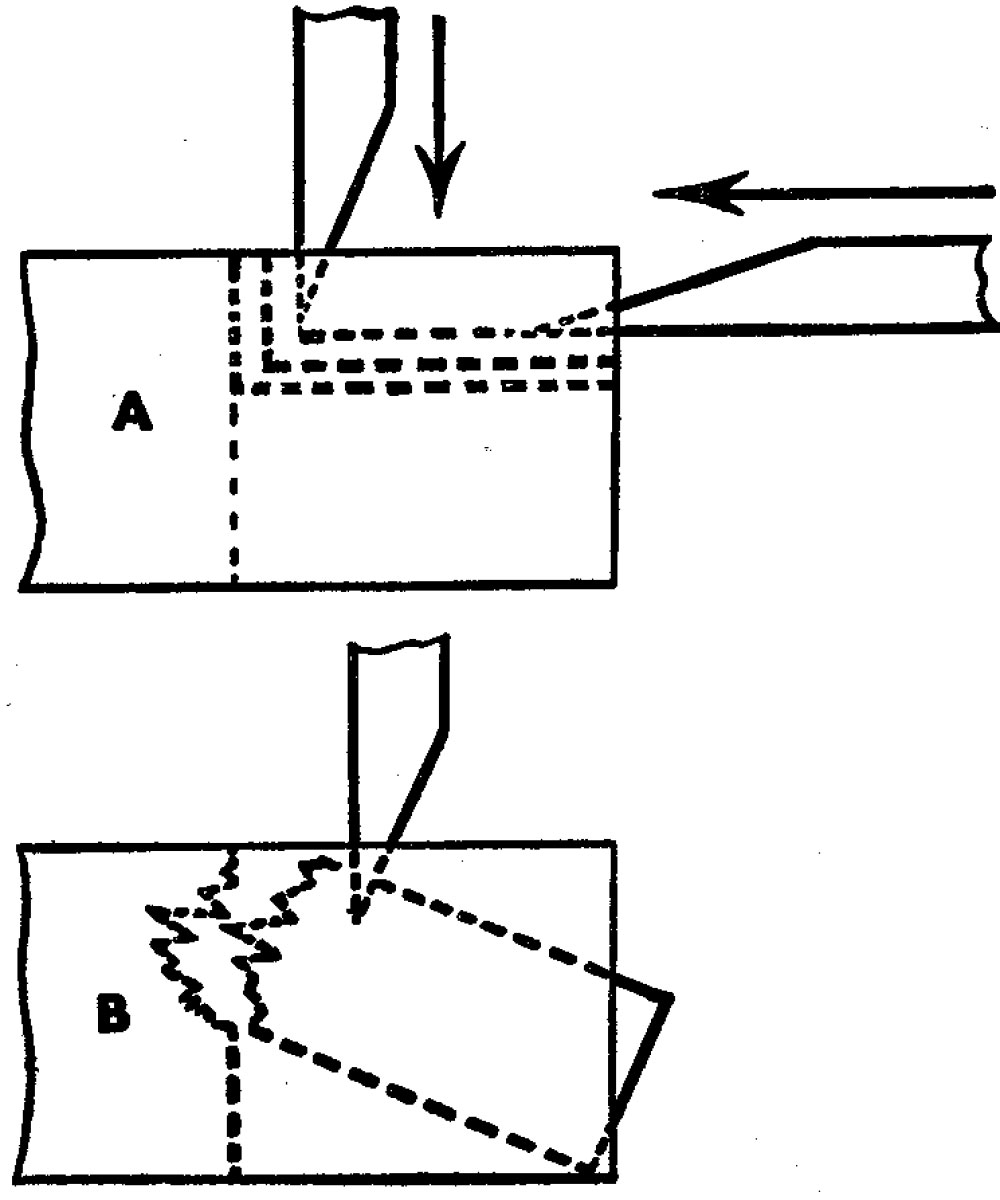
Let us first consider the reason why the wood tears out in this way. There is first the downward chop short of the gauge line across the grain, as at (A), Fig. 2, followed by a horizontal cut which splits away the waste piece. Next is another chop right on the line and a second horizontal cut. So far no tearing out has taken place, yet it is this preliminary cut that is the cause of all the trouble. The wood is now reversed and a similar chop made, as at B. It is easy to see what happens. The shock of the blow causes the unsupported waste to bend over, and it tears out the fibres from the shoulder as shown. If the chisel happens to be blunt the defect is so much the worse. It is all due to the projecting waste piece having no support when the wood is reversed and the second cut made.
The remedy is simple. Begin by chopping down across the grain short of the gauge line as before, and then make a sloping cut to meet it as at (B); Fig. 3. Make a second cut a little nearer the gauge line followed by a second sloping cut, and finally right up to the line, as at C. Note that sloping cuts leave a short piece of uncut wood at the corner. On no account cut away the waste horizontally from the end. If now you reverse the wood and chop down, the grain will not tear out because the waste piece is supported. You can ease the work too by splitting away the waste at the end. It does not matter once the wood has been reversed.
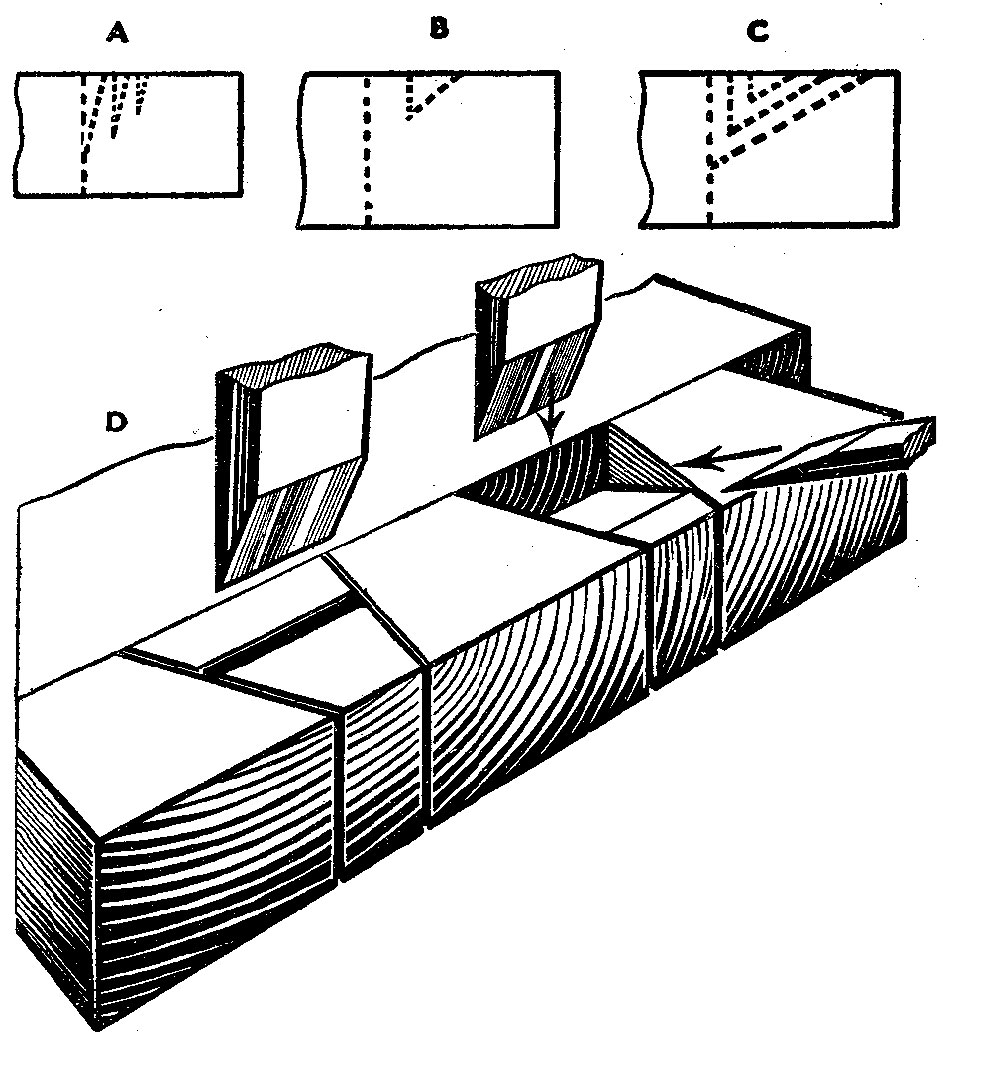
Wedge shaped piece is removed leaving the corner Intact
It will be realised that in working in this way the removal of the wedge of wood enables the chisel to penetrate easily when the second chop is made closer to or right on the line. The idea is shown pictorially at (D), Fig. 3. In thick wood or extra hard wood it may be necessary to make several cuts, easing away a wedge of wood after each, as at (C), Fig. 3. The great point in avoiding tearing out, however, is to leave the wood untouched at the corner so that it is not forced downwards when the wood is reversed. The corner supports it, as shown in Fig. 4. Chopping in with the grain at the end after the wood has been reversed however enables the chisel to penetrate more easily.
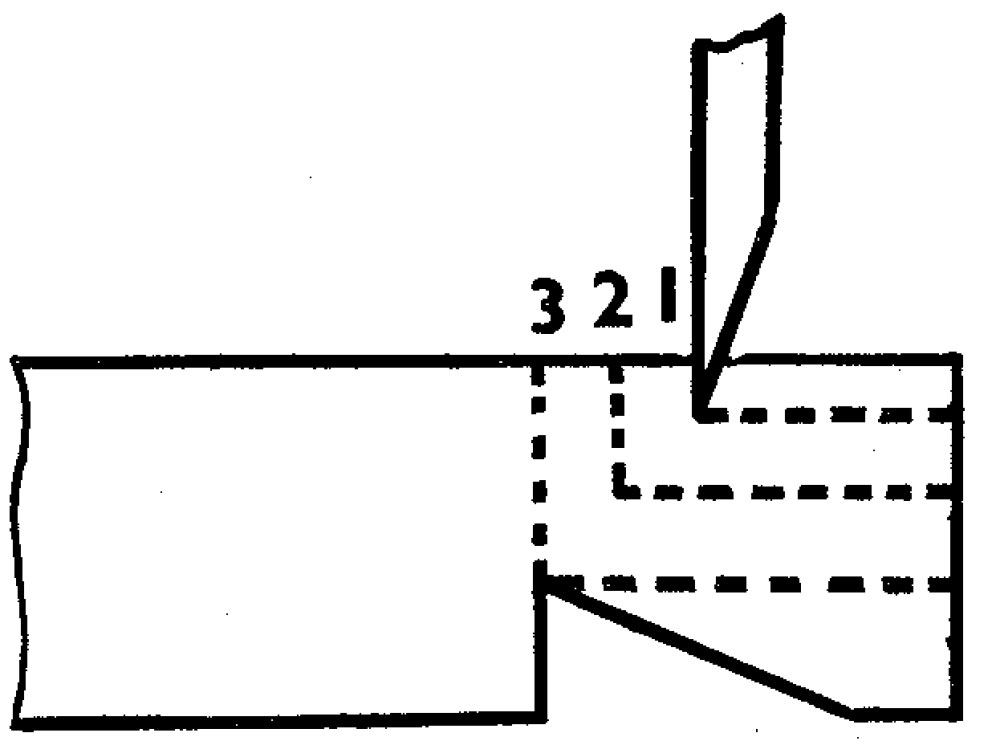
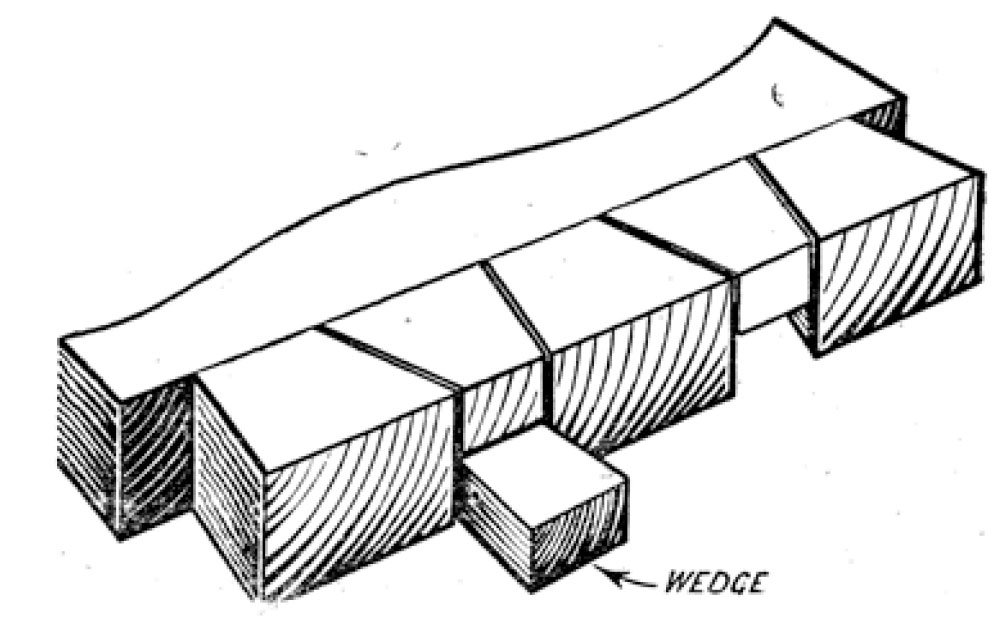
If for any reason you have cut away the waste right to the end in the first chopping, you can still prevent tearing out by inserting a little wedge of wood beneath the overhanging waste as in Fig. 5. This gives support and prevents it from bending over under the force of the blows and so wrenching the fibres.
— Meghan B.
Thank you. One day I will acquire those books .
Cheers to all at LAP.
Un-huh, yea, that’s the way I’ve always done it. Yep, sure have. I’m just going to copy this–for a friend.
Charles H. Hayward wrote:
“…The wood between the dovetails is torn out, leaving an unsightly gash which robs the joint of much of its strength…”
I have to take a bit of exception with the latter aspect of this quote…
I can more than accept (and respect) that there are those Craftspeople that obsess over the…”internal particularities and preciseness”…of there joinery and want the inside of the joint to look as pristine as the outside…
Nevertheless, the only thing this grain tear is indicative of is poor approach angle and/or dull tool…
IT HAS no bearing what so ever on the strength of the joint, especially when glued. Unless this tear out is grossly extravagant and spills out onto the surface of the work, thus being both unsightly and a weakening of joint strength for sure.
This view reflected that it is…” a bad fault”…is strictly an opinion and state of mind.
Like perfection itself, which too is a state of mind, this is but one perspective of good joinery. I would further offer that “undercutting” (a common practice among we Timberwrights) is an excellent way to achieve extremely tight joinery on the surface and grain tear out in the internal aspects of a joint usually only mean your chisel is dull…LOL…It has no real effect on overall joint strength (marginal at its very best with certain possible joints) and these are highly structural unions, to say the least!!!
As such, if making the inside of a joint is important to you…???
By all means obsess over it, as your work will most likely be of extreme precision, but I would suggest no more beautiful or strong than someone that doesn’t obsess over such things. I was taught the speed of execution, efficiency, and…”structural precision”…(not internal aesthetics) was the goal set. As my teacher pointed out to me…”The inside of most things…be it a finely tailored suit or your gut…seldom look pretty…but they get the job done…”
Food for thought from a different perspective…
j
Funny that you should bring this up. I just published my first attempt at dovetails and I must admit, it was a healthy challenge. I’ll leave you a link to it, just in case you would be interested in seeing how it turned out:
https://elementsworkshoplife.wordpress.com/2018/04/30/dove-tail-jewelry-box/
I find your posts insightful, keep up the good work.
Anyone tried that technic …?
I’ve been practicing dovetails for only a few years and recently tried Bob Cosman’s technique (can be found on YouTube), and this runs totally counter to that. He uses a coping saw to cut most of the waste out, which saves time chopping it out by hand, and makes it less likely you’ll bruise the edges of the dovetail that will actually be seen. He’s able to knock out a simple joint (admittedly in pine) in like 15 minutes, that fits first try. I agree with another poster here that having some tearout does nothing to the strength of the joint, since the glue is on the edge, not the end grain.
That being said, this could be a better strategy for really soft wood that might tear out past the scribe line.
Wow. Thanks for bringing this up. This just may solve a lot of my tear out problems. Cool.
I changed to the coping saw method a while back, but I’m going to give this a go to see how well it does. Best advice spot on LAP I’ve seen so far! 🙂