Tomorrow morning I start a class I’ve been waiting a long time to teach through the New English Workshop: “The Tool Chest for New Anarchists.” It’s a low-cost class (I don’t think either N.E.W. nor I am making a dime on the course) for 18 new woodworkers.
We’ll spend the week at Bridgwater College in the West Country building a simple tool chest entirely by hand. While the tool chest itself is important, what is more important to me is that we hand off a set of core hand-tool skills.
So in the true spirit of American aesthetic anarchism, I’d like to invite you to follow along this week using all the materials I’ve created for the class.
You can download the 28-page illustrated manual for the class here:
If you wish to build the chest, you can download the complete cutting list here:
Cut list NEW Anarchist Tool Chest MASW NEW – Sheet1(1)
A SketchUp drawing of the chest is here (you’ll need to unzip it to open it in SketchUp):
New Anarchist Tool Chest 2015_explode~
I’ll be posting photos of our progress on the blog and on Instagram using the hashtag #babyanarchists. (You can follow me on Instagram via this link.) I’ve encouraged the students to also use this hashtag if they post photos on social media.
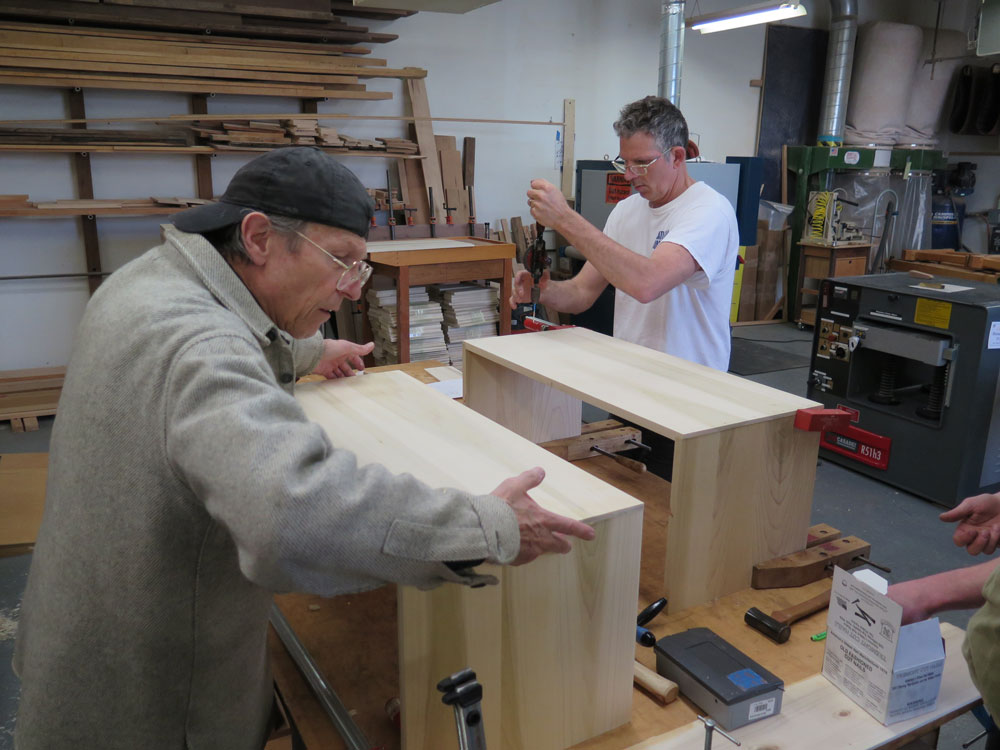
I expect this class to go smoothly. This April I did a trial-run class with the Guild of Oregon Woodworkers to work out the bugs and we managed to build the chest in two days (including painting it). So I am looking forward to being able to work at a steady pace this week with time for detailed instruction. In other words, I left the “punishment whip” at home.
— Christopher Schwarz
PS: Today I had a few hours to walk around the town of Bridgwater and get soaking wet. Below are a few photos. It’s a nice and un-touristy town.
What sort of “timber” will you be using on the other side of the pond?
Poplar I believe.
Reblogged this on The daily skep and commented:
A very gracious offer from Chris Schwarz to virtually build alongside those lucky enough to be in the West Country this week.
A saw till was next on my list, but it looks like my plans may have changed 😉
Chris,
I may be mistaken, but it seems like there has been an evolution in the type of chest you build/teach. The size is a bit smaller and two tills instead of three. I’d be interested to hear your thoughts on this. I’m moving soon, and decided to build a floor chest (glued and nailed) to transport the tools that are going in the moving truck / storage. I had intended to build the larger ATC chest, but before I got started I built a similar sized crate, and realized that I wasn’t going to be able to get the larger chest out of my shop without tipping it over so I built one 32 long, 18 wide and 20 tall, which is similar to the chest you’ve been building lately. I wasn’t happy with the tills I built, so I built another pair, and it turns out that at least until after the move all four will get used.
Along a similar vein, this chest has no dovetails. While I really like the look (and speed) of rabbit joints, you are known for building dovetail chests. I’m not saying you must always use dovetails, but instead I appreciate that we all change things up from time to time. Sometimes the reasons are interesting.
Thanks for sharing.
I teach about five different chests. What you need depends on your tools and where you work.
I like a floor chest that is dovetailed to the nines. But that’s unsuitable for someone who travels a lot or doesn’t have the space for a 25″ x 25″ x 40″ chest. So I also teach two other varieties of square chests and two kinds of Dutch chests.
Thanks for this, and for the comments you made in an earlier post on the “New Anarchists” chest. Even allowing for the enormous discrepancy in skill (mine to a lot of the craftsmen you cite and of course to yours), I thought I must be doing something wrong to take as long as I have been to finish some of the projects compared to time in a class. I usually just blame it on age and arthritis and avoid the whole “you’re not very good at this” discussion!
Pics are cool. Love the door on the church. Bet there are some cool old settles to view and use at the local pub.
I hope your English students have as much fun building their tool chests as we had in your “test build” class at the Guild of Oregon Woodworkers! It was by far the best class I have ever taken. I ended up with a great tool chest too.
Recently I have built several ‘boarded’ pieces and I am very excited to learn more about this and related approaches in your forthcoming book, Furniture of Necessity. Will such a chest outlined here be included in that work?
Great idea – fantastic project and opportunity – I look forward to buying you a pint. Thanks for making this all available – I look forward to giving this a go over the Summer.
I grew up in Somerset – there are some lovely places around – check out Muchelney and Langport if you get a chance – and watch out for the Scrumpy.
Thanks for the gracious offer Chris. I’m planning to “favorite” and bookmark as many of the various posts as I can so I can build this “along with you” in the coming weeks/months. Cheers!
Reblogged this on TheWoodProf.com and commented:
For anyone interested in building their first tool chest, this is the place to start!
From the PDF:
“Boarded Tool Chest
Note: This is a draft chapter and is not for distribution.”
Looks like you disobeyed yourself. 🙂
i’m curious: what is “One Panel; One Clamp” all about?
Looks like you favor the strap hinges for this build and the Dutch build. Would butt hinges be an acceptable design choice or does it really make a significant improvement in the overall stability and longevity of the chest?
This design seems just about perfect for the amount of time I can justify spending on building a tool chest. If one wanted to add a skirt to improve strength, would it be worthwhile to dovetail the skirt only (instead of rabbeting or mitering it) or would that be bass ackwards?