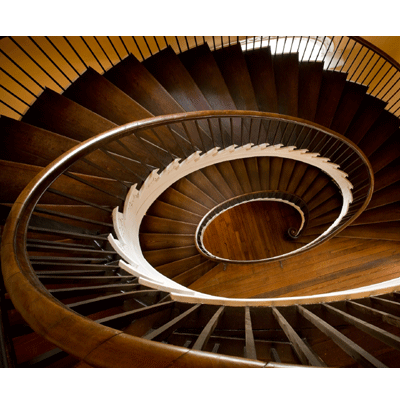
Charleston, S.C., is my favorite city in the world because of the food, architecture, history, weather, furniture and people.
I was first sent there in 1990 to write about the aftermath of Hurricane Hugo and fell in love with the Holy City. I’ve returned there every year since. Lucky for me, I have a built-in excuse – my father now lives there downtown.
If you’ve never been to Charleston, here is a chance to do it, woodworking-style.
This month, March 28-29, Lie-Nielsen Toolworks is holding a Hand Tool Event at Charleston’s American College of the Building Arts, which is currently located in the city’s old jail (an incredible structure). While that is reason enough to come to Charleston, Deneb Puchalski at Lie-Nielsen and I created a special program for the day before the event – March 27 – to introduce you to the city, the food and the furniture on the peninsula.
There is limited space; we can take only 20 woodworkers, so sign up using the instructions at the end of this blog entry. Note: All the following events are on the lower peninsula. No car is necessary to get from place to place.
Here is what we’ve planned for March 27.
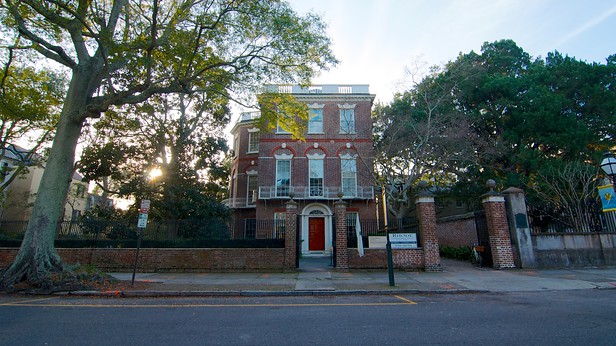
Noon – 1 p.m.
Curatorial Tour of the Nathaniel Russell House Museum
https://www.historiccharleston.org/Russell.aspx
51 Meeting Street, Charleston
Cost: $35 per person
In this specially curated tour of the Nathaniel Russell house, we’ll take a look at the furniture of this impressive home, much of which was made in Charleston. Charleston pieces can be difficult to identify and find. This house has one of the best (if not the best) collections of Charleston pieces. We will all meet at the front gate of the house about noon and go in as a group.
1 p.m. – 2 p.m.
Lunch on your own. We’ll recommend several good places in walking distance that will fit any budget.
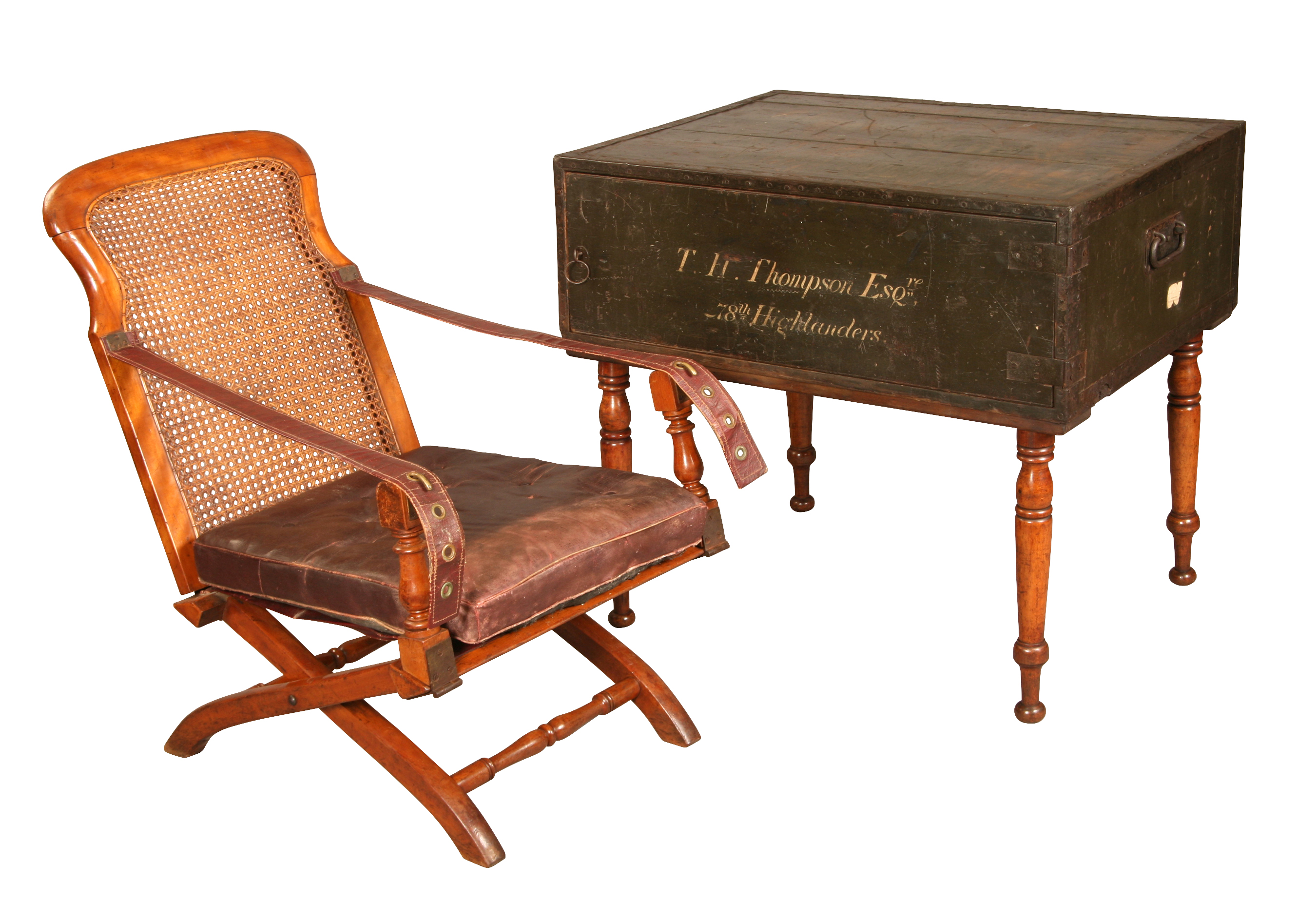
2 p.m. to 3:30 p.m.
Campaign Furniture, Its Surprising Origins
American College of the Building Arts
http://buildingartscollege.us/
21 Magazine St., Charleston
Cost: free
Christopher Schwarz leads a presentation on campaign furniture that shows its surprising 18th-century origins and traces its evolution – plus its connection to Danish modern. Chris is bringing original campaign pieces, plus pieces he built for his book “Campaign Furniture.” The lecture and multimedia presentation will be followed by a question-and-answer session.
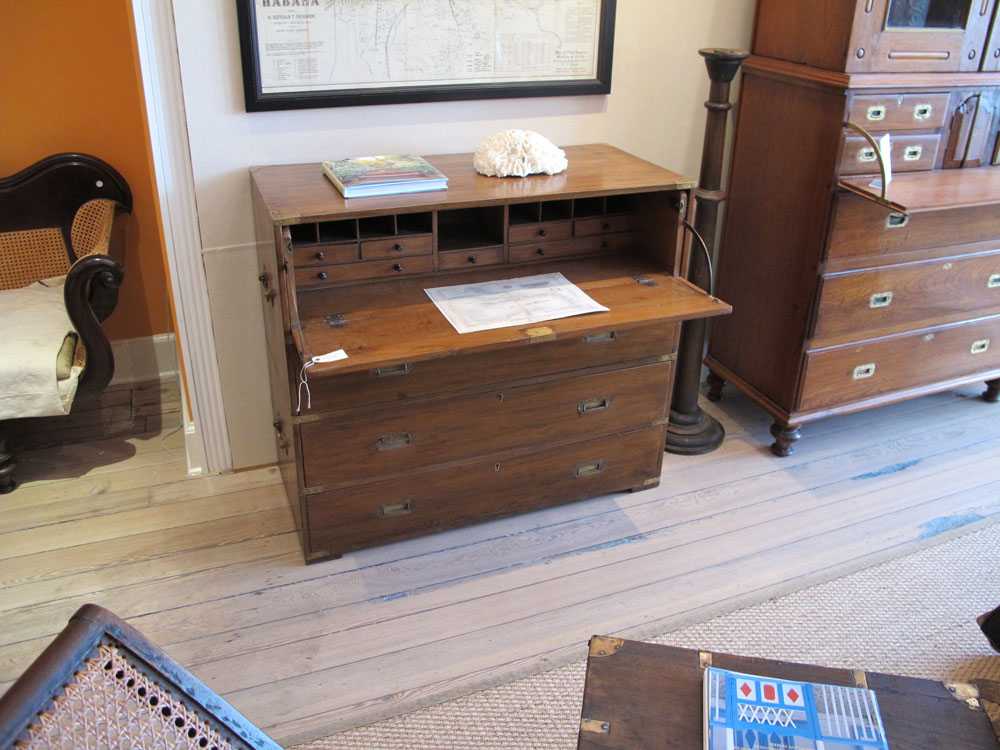
3:30 p.m. to 5 p.m.
Antique Shops of Lower King Street
Cost: free
If you would like to explore some of the best shops for English and American furniture in the South, we’ll give you a map of the stores that have museum-quality antiques that you can examine and study. Many of these shops are filled with amazing pieces you can actually touch – open the drawers (ask first and be gentle) and look at how real furniture is made. We think that even an hour looking at real antiques will improve your own designs.
5 p.m. – whenever
Drinks and dinner at the Craftsmen Kitchen and Tap House
http://www.craftsmentaphouse.com/
12 Cumberland St., Charleston
Cost: Up to you….
Afterward, we’ll all gather at the Craftsmen, which has one of the best draft beer selections in the city, not to mention very good, reasonably priced food. We have a section of the restaurant reserved. Come for a drink, then you can get dinner elsewhere if you like, or stay with us and close the place down.
As I mentioned above, we have room for only 20 woodworkers. The only cost is paying for your food and your admission to the Nathaniel Russell House (I arranged for a discount). I hope to bring my father along on the tour because he used to be a docent for Preservation Society.
The Hand Tool Event itself will also be great. I will bring my Dutch tool chest and will teach and demonstrate handplanes all weekend. Not just bench planes, but also joinery planes, complex moulders and hollows and rounds. Also, carver Mary May and chairmaker Caleb James will be there. Mary is a fantastic carver, and I have been eager to meet Caleb (he is helping us edit Peter Galbert’s chair book).
These Hand Tool Events are free and are a true public service for the woodworking community. These events are always casual. There is no hard sell. Heck, there is no soft sell. Just tools, benches and people who will answer all of your questions.
For more information on the Hand Tool Events, visit the Lie-Nielsen site here.
To register for the March 27 pre-show events, please read the following with care.
1. Send an e-mail to me at chris@lostartpress.com with the subject line as “Charleston event.” Do NOT just reply in the comments that you’ll be there.
2. In the email, please include your name, mailing address and best phone number to reach you in case the schedule changes. This is not to spam you or register you for some stupid mailing list. You know me better than that.
3. That’s it. I’ll reply when I get your e-mail. Later in the month you’ll receive full instructions for the event.
— Christopher Schwarz
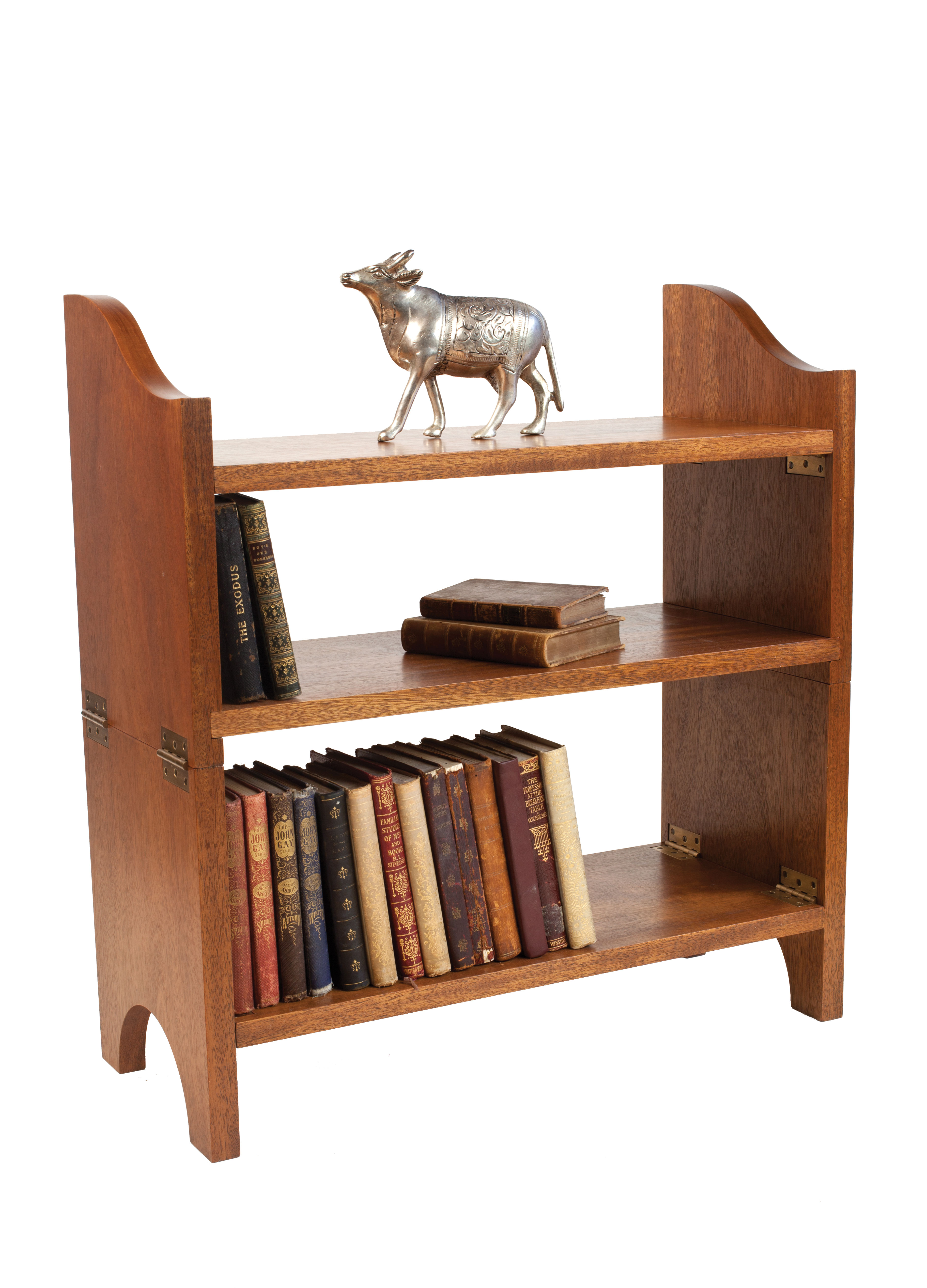
P.S. As we get closer to the event, I’ll post information here about other things to do in Charleston, both for you and your family, even if you cannot come to the March 27 pre-show kidney killer. Charleston has excellent shopping, world-class cuisine, art, nearby beaches and is lousy with historical sites.
Like this:
Like Loading...