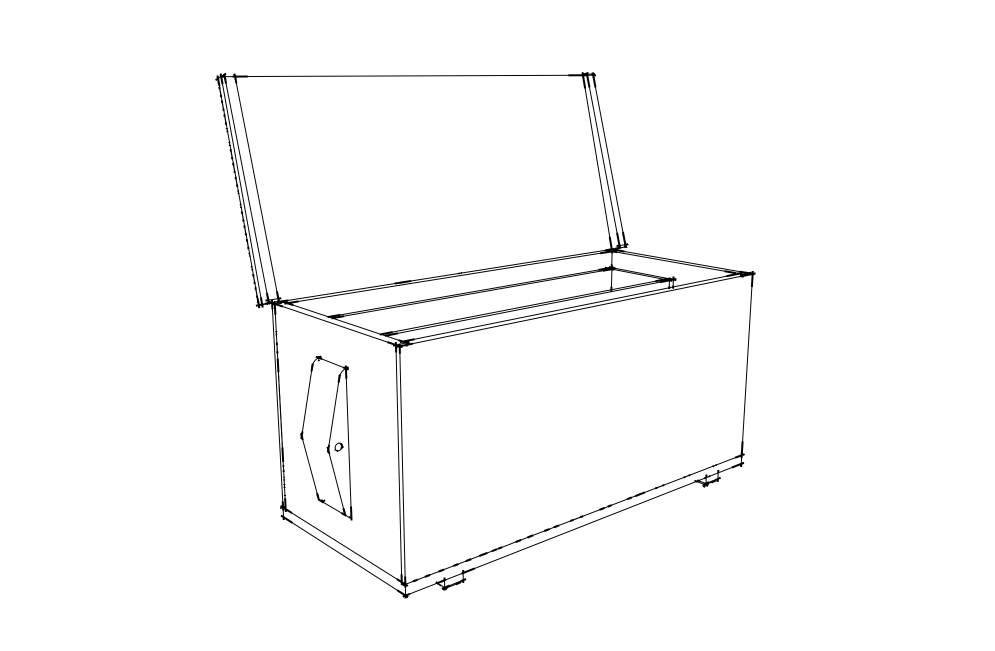
A common bit of advice on building tool chests goes like this: “You should build the chest to fit your tools.”
I’d like to amend that melba-toast statement to this: “You should build the chest to fit our tools.”
Woodworking tools come in standard sizes, and the standard tool kit hasn’t changed much since Joseph Moxon laid it out in “Mechanick Exercises” in 1678. So if you are in the craft to build furniture, your tool kit probably looks a lot like mine. If you are in it for type studies and patented tools, ignore the rest of this blog entry.
When I started studying tool chests (several years before writing “The Anarchist’s Tool Chest”), I noticed that they were built in some fairly standard sizes. Most of the outliers were actually for other trades or specialists. In truth, there are more than three basic sizes of chests, but I’d like to discuss three sizes I have found most compelling.
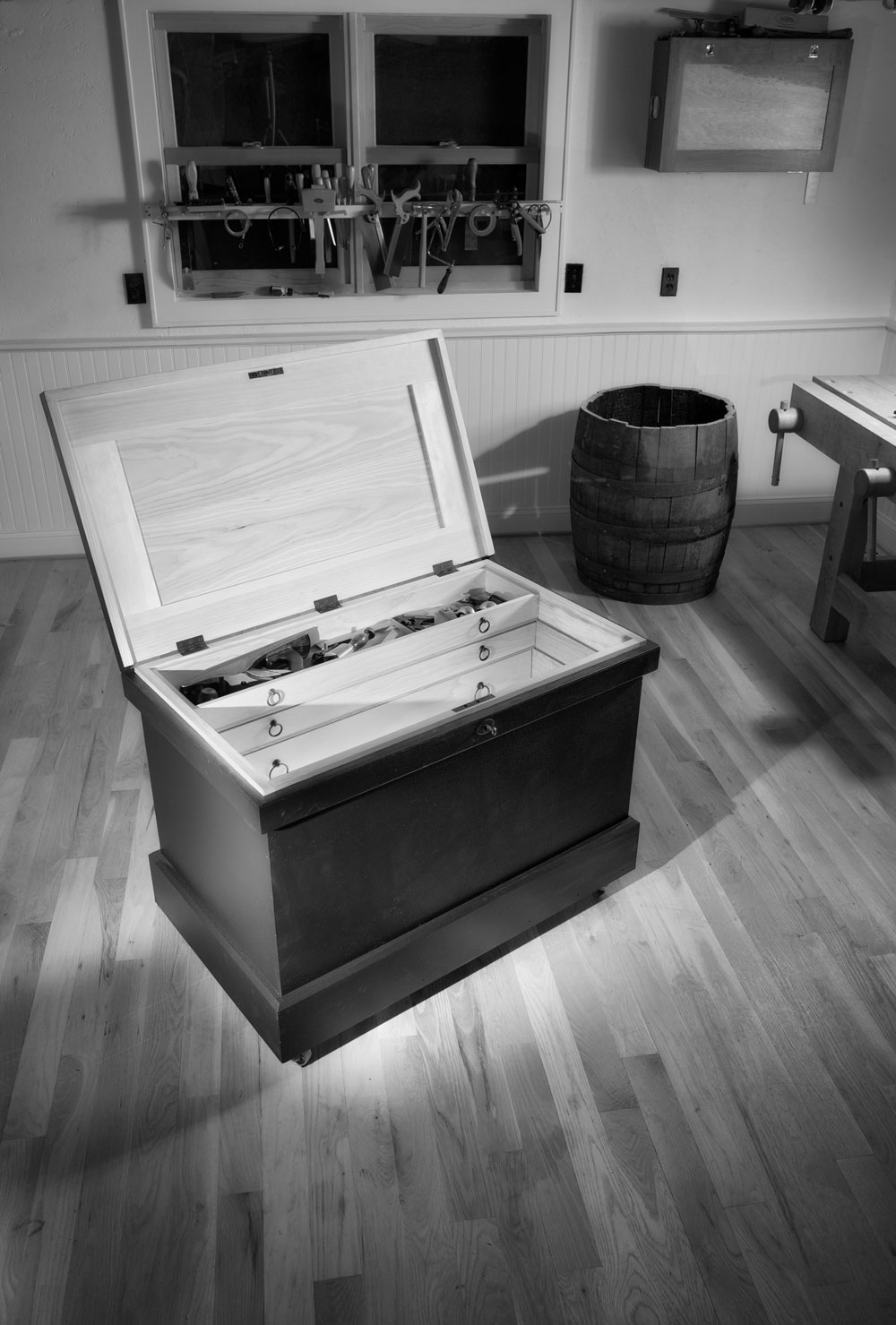
The Floor Chest
This is the massive tool chest I built for “The Anarchist’s Tool Chest” and have subsequently built more than 20 times for classes and customers. It is the Denali of tool chests. It’s bigger than it has to be, but it’s still not big enough.
It is roughly 24” x 24” x 40”. And if you can’t fit a tool in this chest, then you don’t need it. This chest will swallow full-size handsaws, over-sized jointer planes, 18th-century tenon saws, straightedges, a full set of hollows and rounds and all the other tools you need to build furniture.
The standard model usually has three sliding trays, though I have seen them with as many as eight.
During the five years since I built this chest I have modified small sections of it, but it is still basically the same design as when I drew it out in 2010.
What’s the downside to this chest? It is a floor hog, taking up as much square footage as a table saw. If you have a small shop, this chest might be too much for you. But after working out of a chest this size since 1997, I decline to downsize.
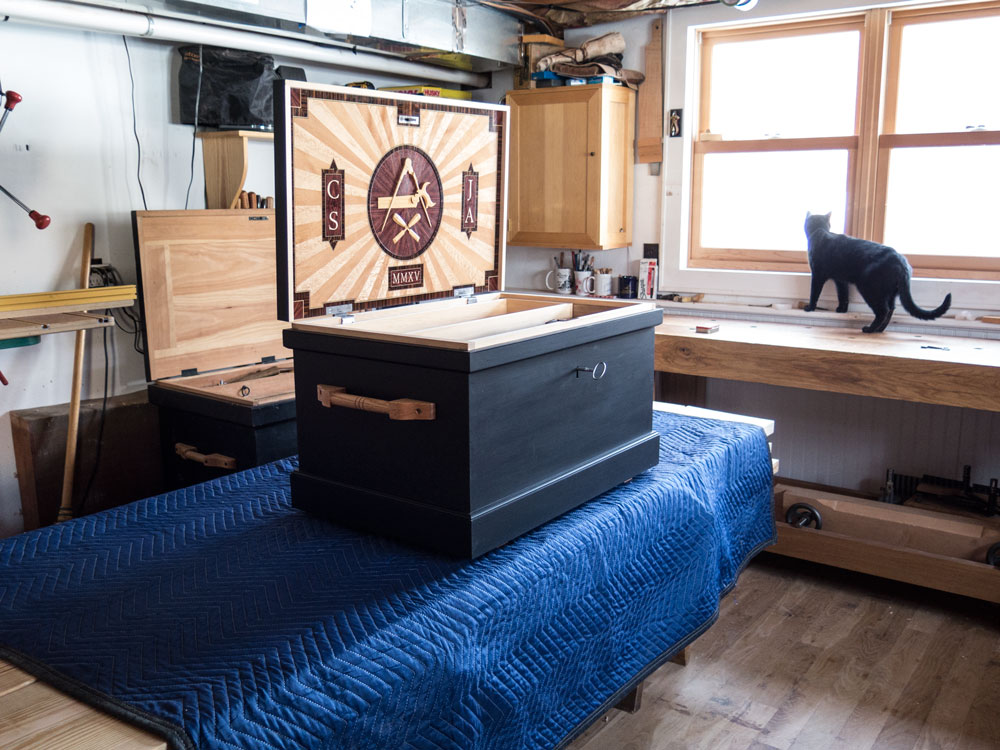
The Traveling Tool Chest
If you need to move your chest frequently, the full-size chest is a heavy burden. Moving that monster by yourself is difficult but doable – if you first remove the trays and heavy tools. If you need to be mobile for work or to attend classes, a scaled-down chest might be the answer.
I just finished building one of these chests for the August issue of Popular Woodworking Magazine. I built the carcase and Jameel Abraham built the marquetry panel for the lid. This chest’s design is based on the length of a panel saw, one of the longer tools in a furniture-maker’s tool kit.
While full-size handsaws are more than 30” long from toe to tote, a panel saw takes up less space – 26” give or take. That’s not much longer than a standard jointer plane. This chest can be 20” x 20” x 30”. That might not seem much smaller than the full-size chest above, but I can tell you that the slightly smaller dimensions allow you to move the chest easily by yourself.
The downside? You can still pack a standard toolkit in the chest if you omit the moulding planes. (OK, that’s not entirely true; you can build a removable tray that holds moulders thereby squeezing every cubic inch of storage out of the chest. It’s just not convenient to work out of.)
These chests typically had two sliding trays for the small tools. And the tool well below held all the bench planes, saws and joinery planes.
The other advantage to this chest is it will fit in the back seat of most passenger cars. The full-size chest will not (unless you first remove the door).
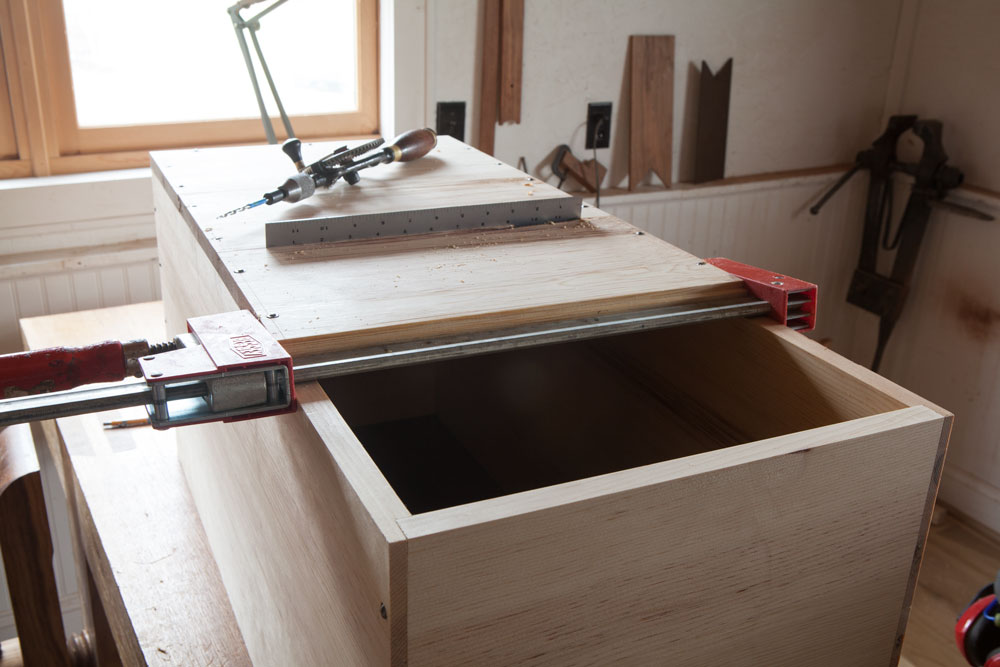
The Tallboy
The other curious chest I’ve been toying with is a mix of the full-size chest and the traveling chest. While I’m sure this chest was made all over the Western world, I’ve encountered most examples of it in North America.
It is generally a nailed-together carcase that is designed to hold full-size handsaws, a full set of bench planes, joinery planes and lots and lots of smaller tools. Like the traveling chest, moulding planes are rarely provided dedicated storage space in this variant. But they still can hold a handful of moulders if need be.
So the defining characteristics of these chests are they are long, shallow and tall. The one I’m building now for a series of classes in 2015 is 15” x 17” x 34”. This chest will easily fit into the back seat of a car. It will accommodate the (less expensive) full-size handsaws and is super simple to build. It’s all rabbets and nails.
All three forms have their charms. But their dimensions depend more on how you live than on what sort of stuff you build.
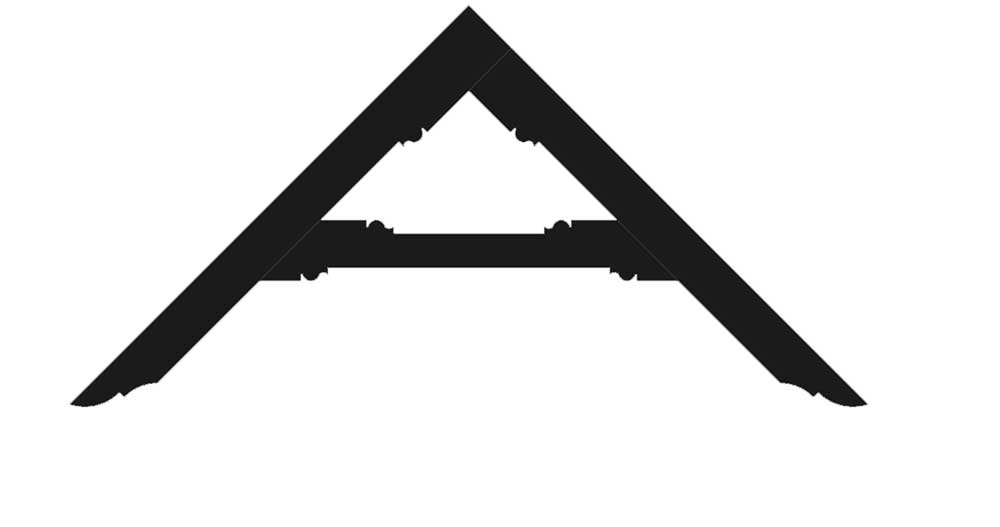
Disobey Me
If you want to design your own chest from scratch and ignore the historical patterns, here’s how to do it:
- Measure your longest saw. That (plus 2”) is the interior length of your carcase.
- Group your bench and joinery planes together into a tight formation that is the same length as your longest saw. Measure the depth of that pile. That is the interior depth of your chest.
- If you have moulding planes, add 5” to that depth.
- Take the interior depth of your chest and make that the interior height. Most tool chests are square in profile view.
My guess is you will end up with one of the three sizes above.
— Christopher Schwarz
Like this:
Like Loading...