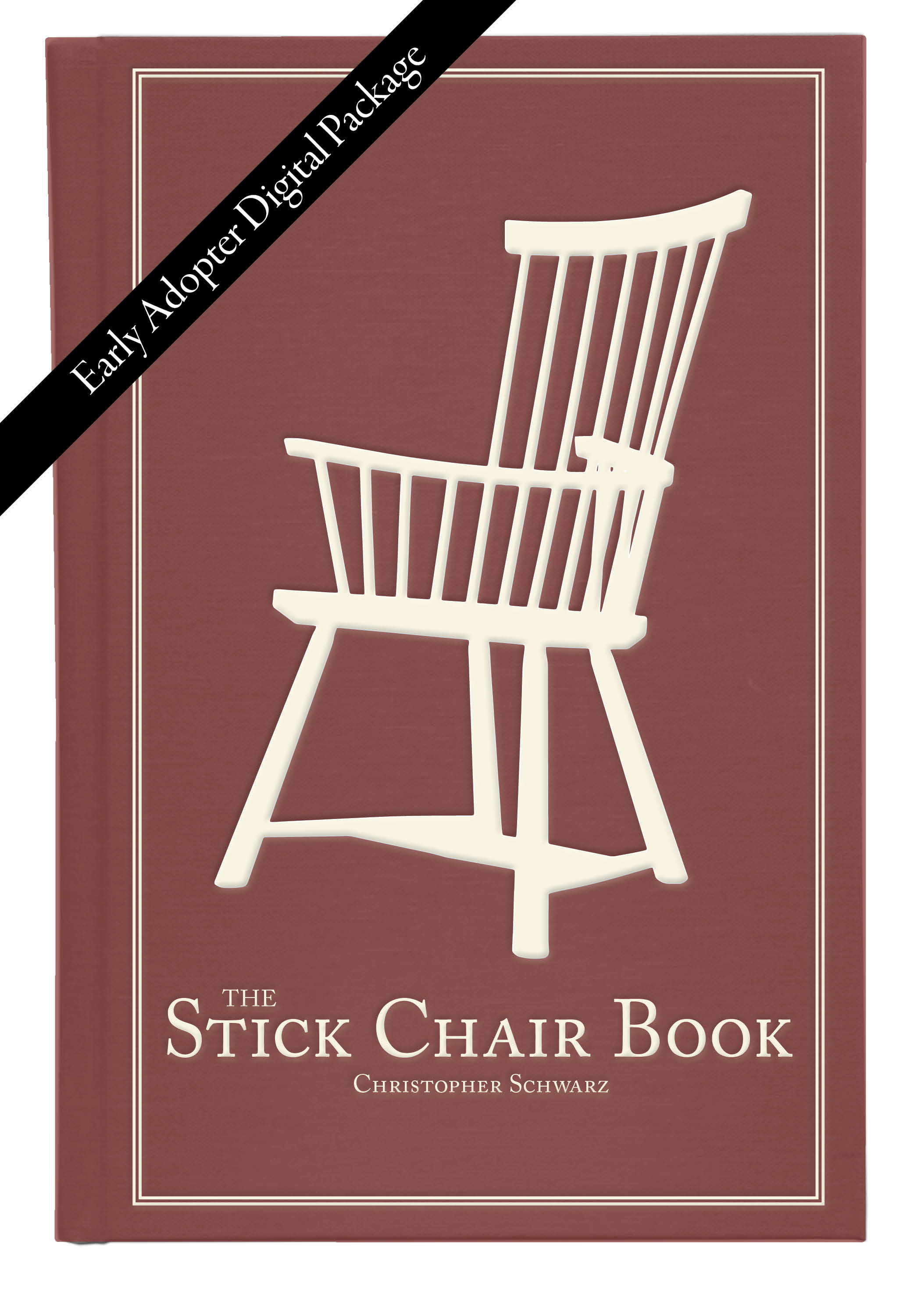
When I fell in love with stick chairs in the 1990s, I was unable to find a teacher or a book that would help me make them using simple tools and readily available materials.
So I read a lot of books about other kinds of chairs. I took a few classes. And I began piecing things together with research, trial-and-error and talking to a few other people who shared my love of this vernacular form. And after 18 years of building these chairs, I decided to write the book I wish I’d owned in 1998.
“The Stick Chair Book” is intended to be a complete guide to get you going. It explains the different kinds of chairs and how they work, it helps you put together a tool kit of mostly run-of-the mill woodworking tools and it shows you how to use whatever wood you have on hand. That could be stuff from your backyard, the woods, the home center or your lumberyard.
For the last eight years I’ve been splitting and sawing out chair parts from kiln-dried wood. And I’ve been building chairs without a shavehorse, drawknife, splitting brake or hatchet. I’ve nothing against these tools – they’re great. But I grew up making cabinets and tables – and I’m much handier with planes and saws than a drawknife and axe.
The heart of the 631-page book shows how to perform every operation in chairmaking – from saddling the seat to making wedges to cutting tenons – using a variety of simple methods. Make tenons with a block plane, a hollow auger or a lathe.
For me, the most exciting part of the book breaks some very old ground. No two stick chairs are alike, but they share some of the same shapes and parts. After years of collecting photos of antiques and examining originals in Britain, I provide drawings of many of the shapes and options that you can combine into a chair.
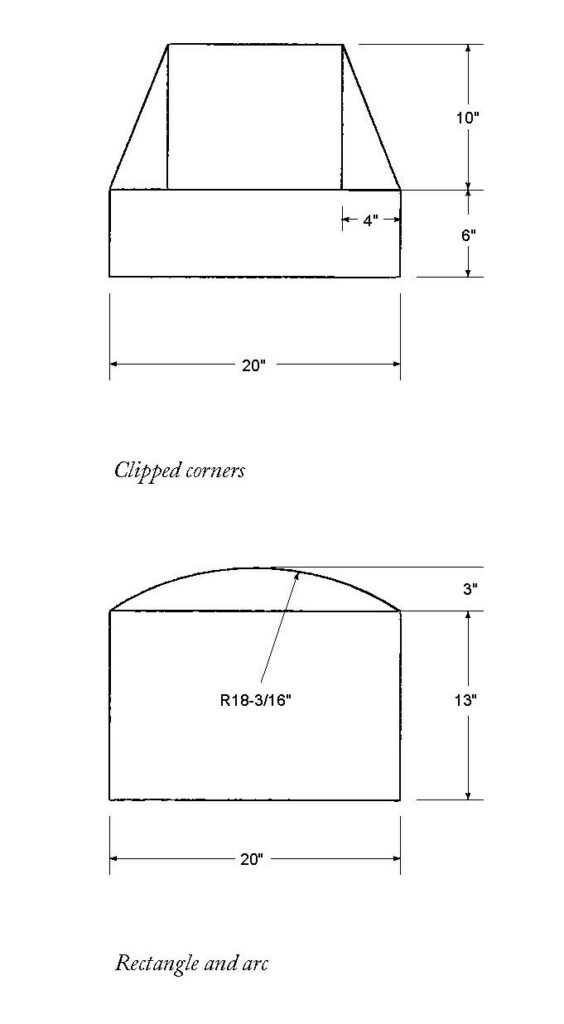
The chapter on seats shows you how to lay out 14 different seat shapes. The chapter on legs has 16 common forms that can be made with only a couple handplanes. Add those to the 11 different arm shapes, six arm-joinery options, 14 shapes for hands, seven stretcher shapes and 11 combs, and you could make stick chairs your entire life without ever making the same one twice.
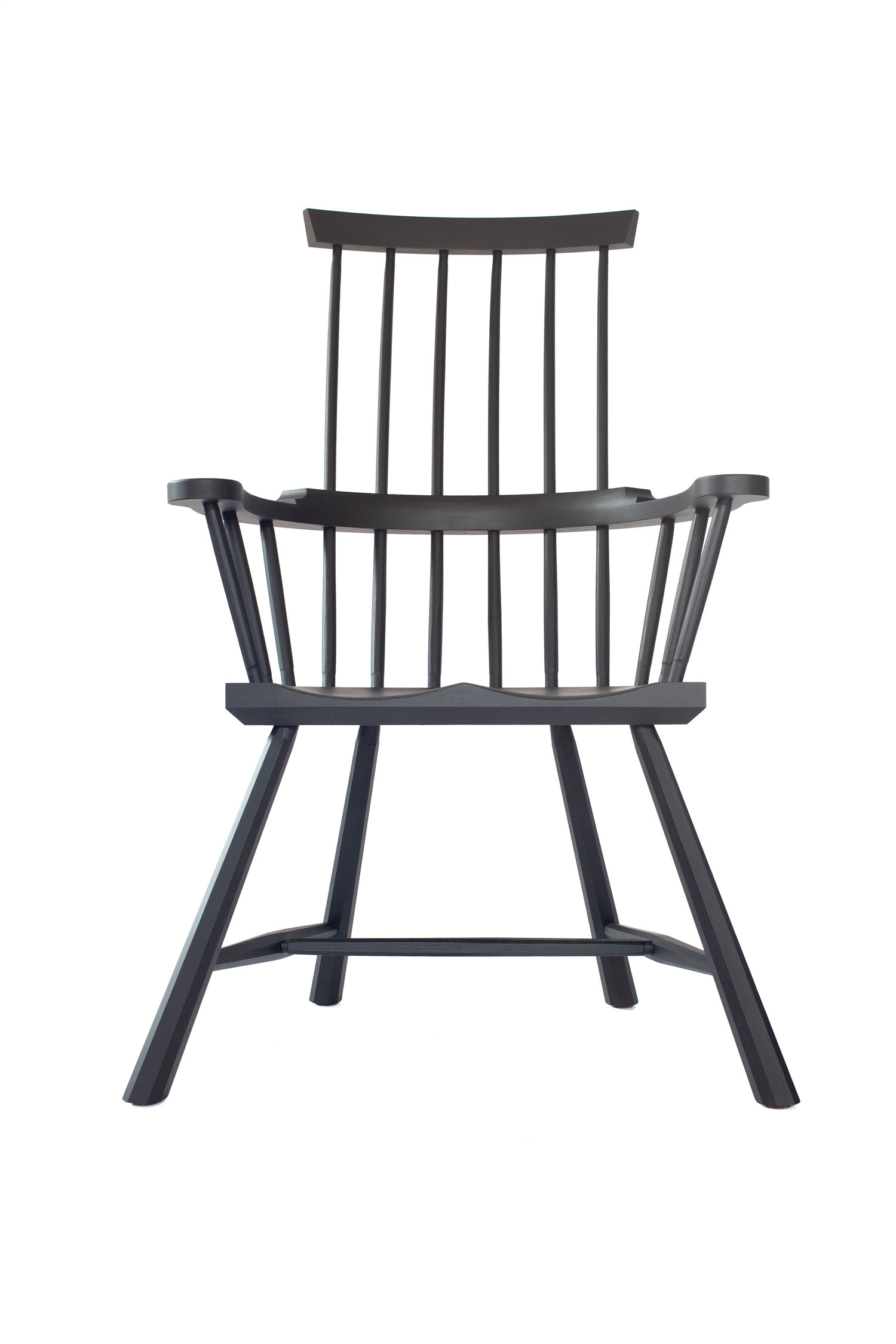
I think anyone can design their own stick chair, but for those who are unsure, I provide complete plans for five original designs that you can make (and sell, if you like). There are two Irish-inspired armchairs, a lowback and two comb-backs – one that is Welsh-based, the other inspired by Scottish Darvel chairs. All are comfortable and fairly simple to build. I include cutting lists and completely dimensioned drawings to make it easy.
There’s also lots of help with finishing, from painting the chairs, to cooking up a soap finish or your own linseed oil/wax finish. And a couple chapters on chair comfort and design to help you design your own comfortable stick chairs.
Plus, as with my other books, there is a good dose of philosophy, history and the occasional weasel joke woven amongst the practical stuff.
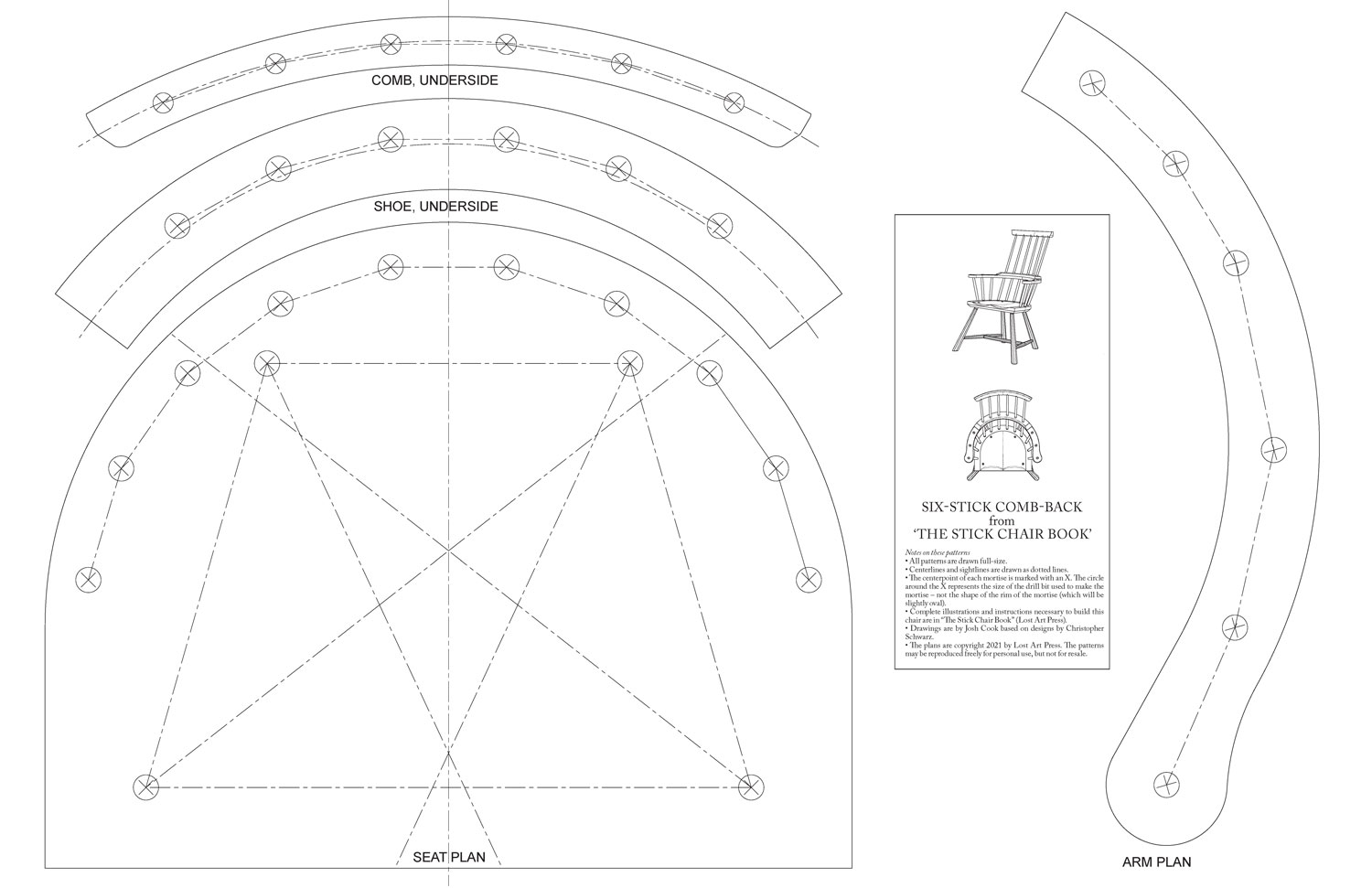
About the Early Adopter Digital Package
The printing industry is currently struggling with unheard-of shortages of paper and other raw materials. Though “The Stick Chair Book” was completed and sent to press in June, the paper shortage has us wondering if it will be printed in November or later.
So in the meantime, we’ve decided to offer a special digital package for $25. This download-only product is available to customers worldwide. Here’s what is in it.
- A high-resolution pdf of the complete “The Stick Chair Book” – all 631 pages of it. The book contains everything you need to start building these chairs. Plus complete plans for five original designs: two Irish-inspired armchairs, a lowback chair, a Welsh-inspired comb-back and a Scottish-inspired comb-back.
- A pdf containing the full-size parts for the five chairs in the book. These 22” x 34” sheets contain every seat, arm, shoe, backrest and comb needed to build the five chairs. The drawings contain all the mortise locations and sightlines needed. This pdf can be printed out at any office supply store or reprographics service. Then you can adhere them to posterboard or thin plywood and have full-size permanent patterns. (Later on this year we will sell these patterns for $20 for printed patterns or $10 for digital ones.)
- A pdf of all the construction sheets for the five chairs in the book. These sheets were generated by mechanical designer Joshua Cook and contain a higher level of detail. Each chair has four 22” x 34” sheets that show all the components in a variety of views. If you have an engineering mindset, these plans will be especially useful.
When the physical book is released, this digital-only early adopter package will end forever. At that time, we will sell “The Stick Chair Book” like we normally sell a new title.
So if you want to get started on your own journey into stick chairs, you can start today. You can read more (including the book’s table of contents) in our store.
— Christopher Schwarz