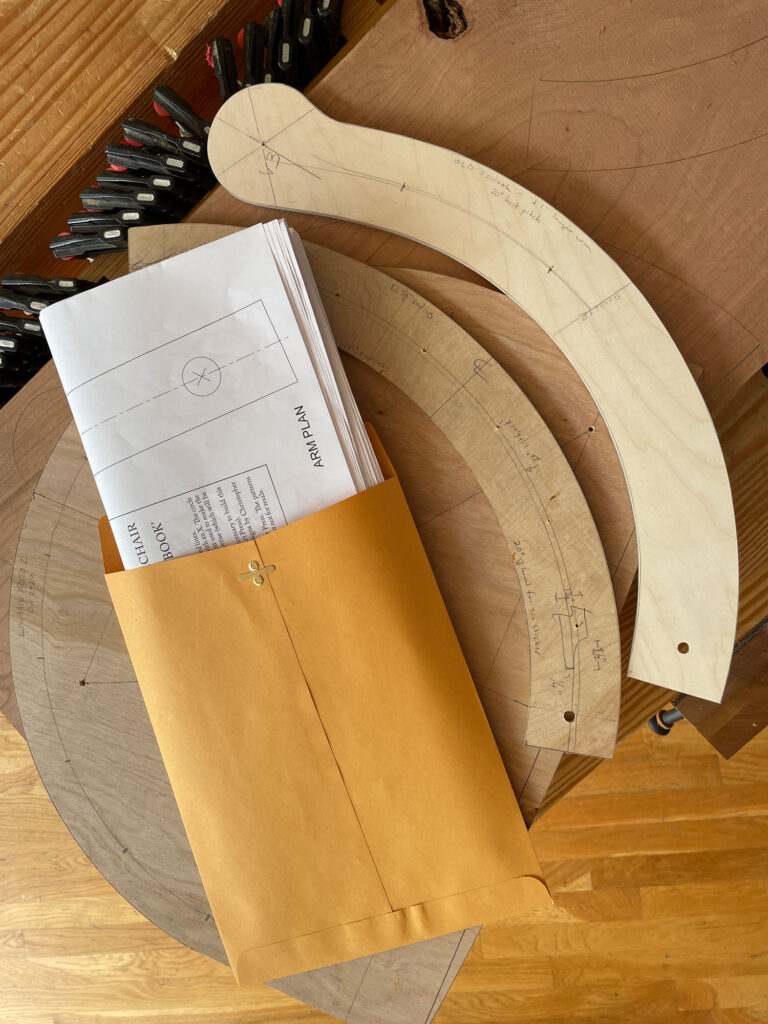
When I think about the things I would grab from my shop during a fire, my chair patterns would be at the top of the list. The patterns I own have evolved during the last 18 years and began with some tracings I made during my first chair class.
These patterns are still my jumping-off point for all my existing and new chair designs.
In order to help readers of “The Stick Chair Book” begin their own collection of patterns, we’ve made five sheets of full-size patterns for all the major components in the five chairs in “The Stick Chair Book.” NOTE: If you have bought the Early Adopter Digital Package for this book, you already have these patterns in your possession. No need to buy them twice or thrice.
We are selling the patterns two ways.
For $20 plus shipping, you will receive five 22” x 34” sheets printed on lightweight paper used for architectural drawings. These can be easily cut out and stuck to thin plywood to make templates. The patterns include mortise locations for the legs and sticks. And the sightlines for drilling the leg mortises.
For $10 you can download a pdf of the five sheets, which you can get printed out at your local copy shop, reprographics firm or office supply store.
You can buy the patterns in our store here.
A couple other updates: We have restocked on Crucible Type 2 Dividers and have another big load on the way to the warehouse.
Also, we were hoping to launch our Lost Art Press beer steins this week, but we hit a snag. We didn’t receive our full shipment of them. So we decided to hold off on launching them until we had our entire order. Stay tuned.
— Christopher Schwarz