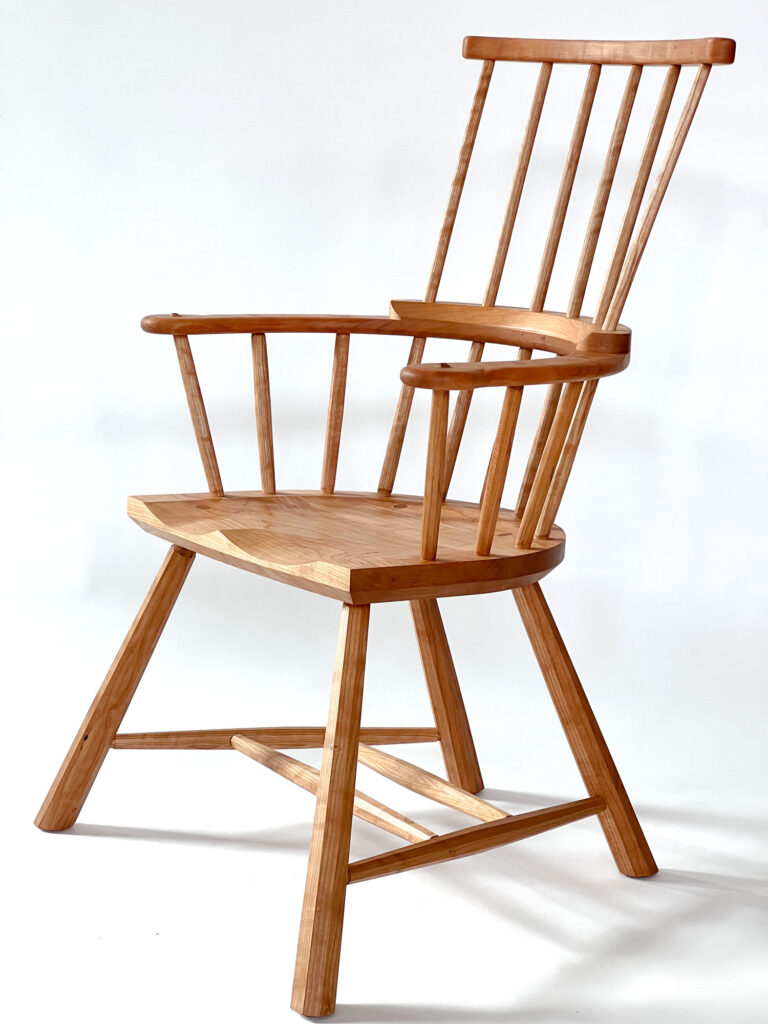
This cherry stick chair – one of my favorite designs – is for sale this week via a drawing. If you are interested in purchasing it, please read on.
This chair – built using black cherry from the Ohio River valley – is influenced by many gorgeous Welsh examples I have inspected during my travels. But I wouldn’t call it Welsh – it has far too much Kentucky DNA.
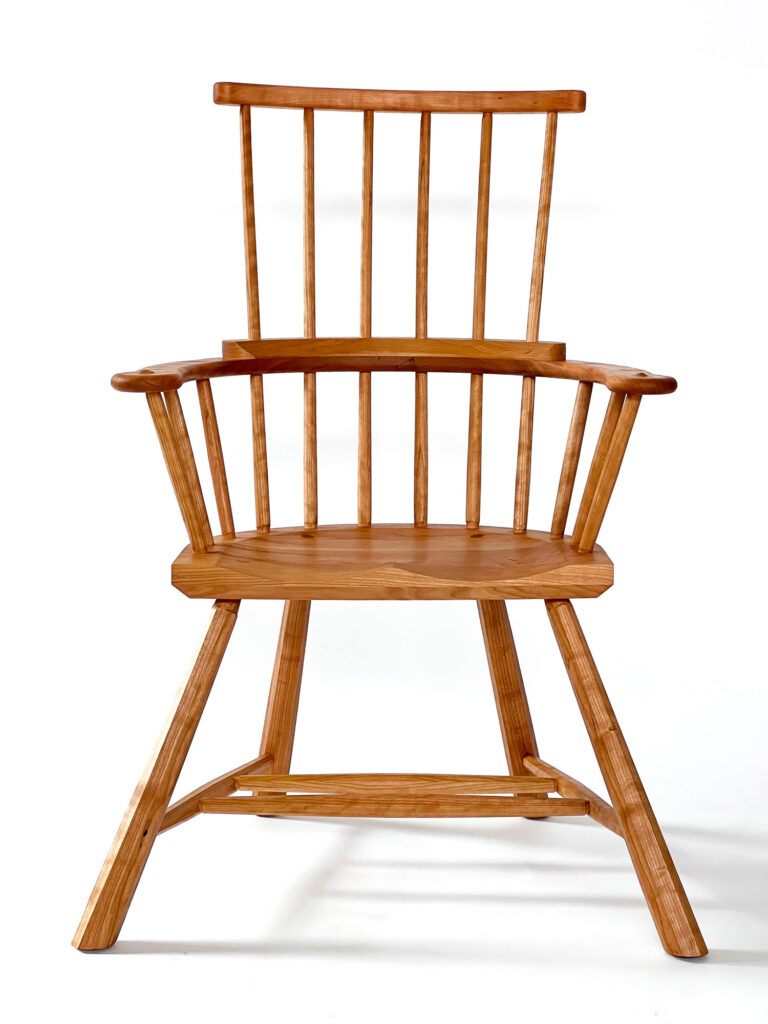
The chair’s seat is 16-7/8” from the floor. The overall height of the comb is 38-5/8”. The dramatic rake and splay of the chair’s legs make it ideal for a fireside, but the seat and back angle (14°) make it completely usable as a chair at a desk or dining table as well.
Thanks to the position of the armbow and comb, this chair provides nice lumbar support as well as supporting the shoulders. It is comfortable for a good long sit.
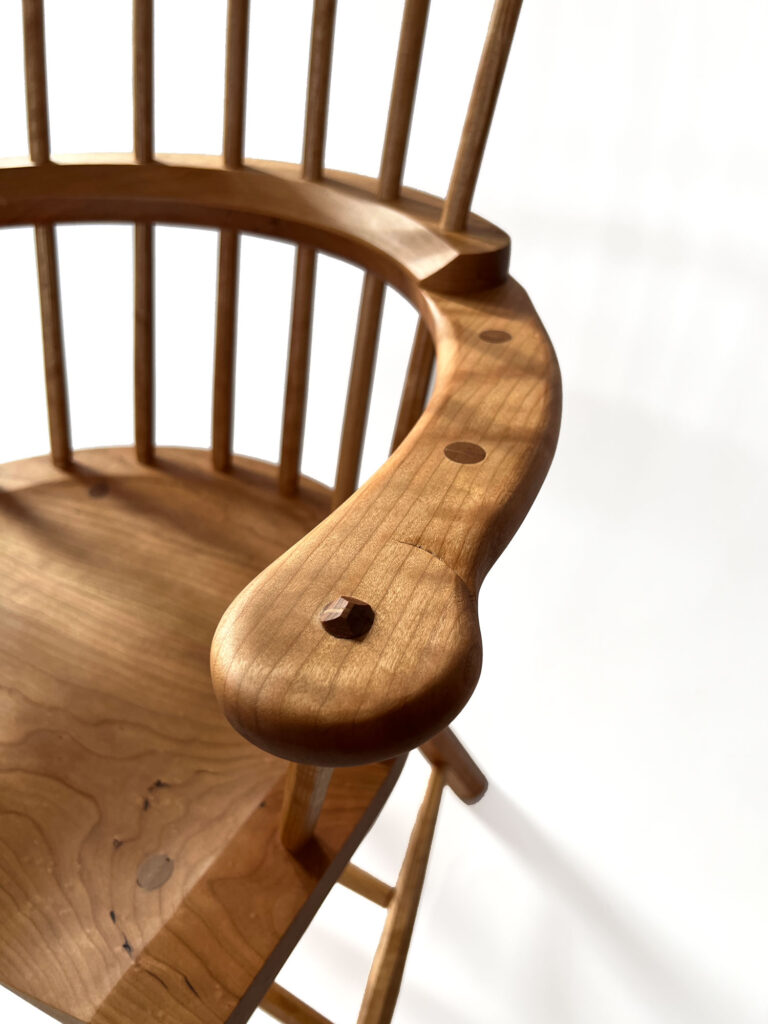
All the joints are assembled with hide glue, which allows the chair to be repaired many years in the future. All through-tenons are wedged with white oak. The finish is an organic beeswax and linseed oil finish, which is free of harmful solvents. This finish is easily repaired, should it ever become scratched or damaged.
All the chair’s parts have been split and sawn so the grain is as straight and strong as possible.
Purchasing the Chair
This chair is being sold via a drawing. The chair is $1,400 plus domestic shipping. (I’m sorry but the chair cannot be shipped outside the U.S.) If you wish to buy the chair, send an email to fitz@lostartpress.com before 5 p.m. (Eastern) on Thursday, Dec. 30. In the email please include your:
- First name and last name
- U.S. shipping address
- Daytime phone number (this is for the trucking quote only)
After all the emails have arrived on Dec. 30, we will pick a winner that evening via a random drawing.
If you are the “winner,” the chair can be picked up at our storefront for free. Or we can ship it to you via common carrier. The crate is included in the price of the chair. Shipping a chair usually costs between $150 and $250, depending on your location.
Selling a chair via a drawing is one of the ways I’m trying to balance fairness and price. I want my chairs to be affordable to as many people as possible. But I also need to feed my family. So we are experimenting with a variety of methods to find ones that make both customers and me happy.
— Christopher Schwarz
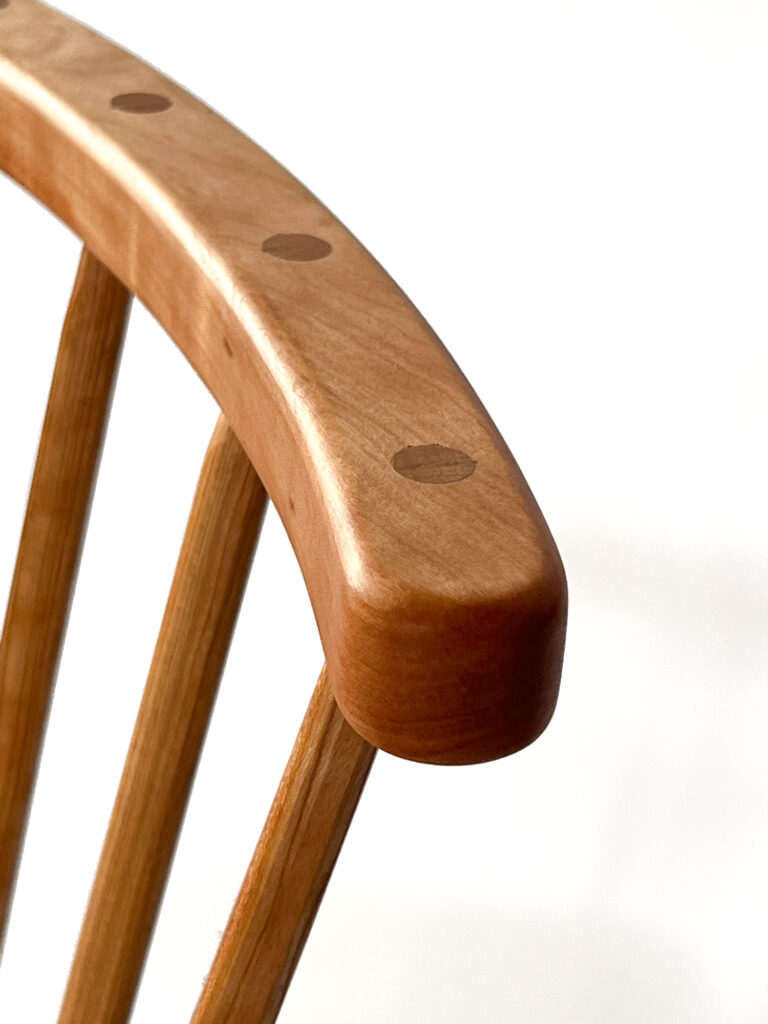
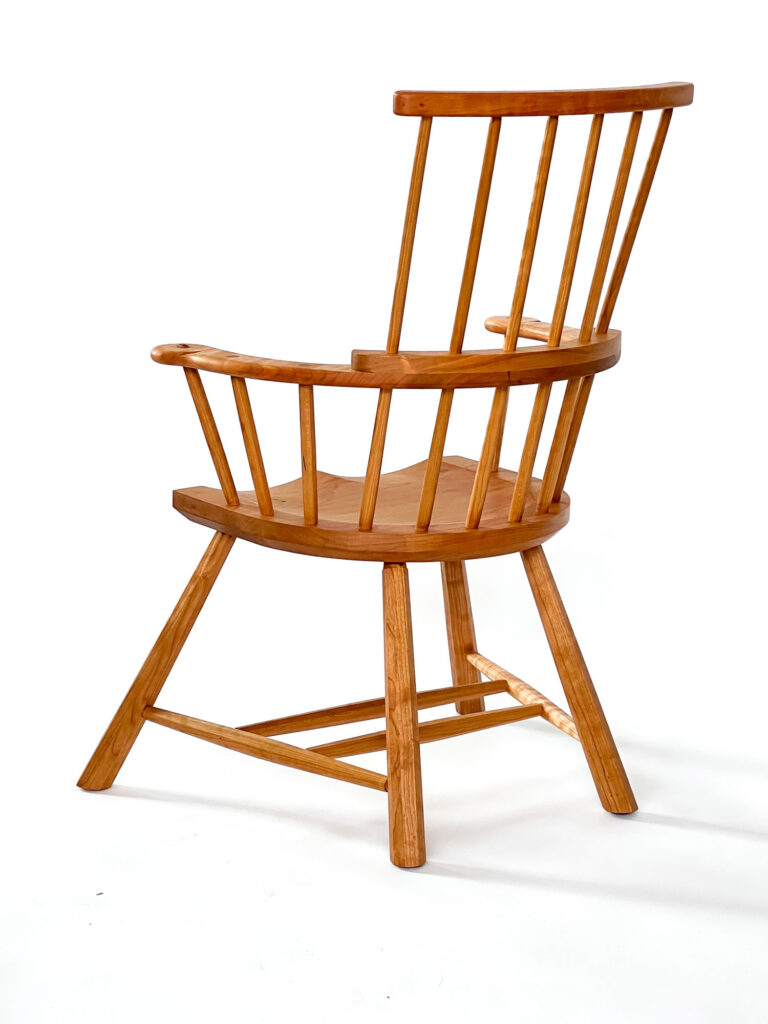