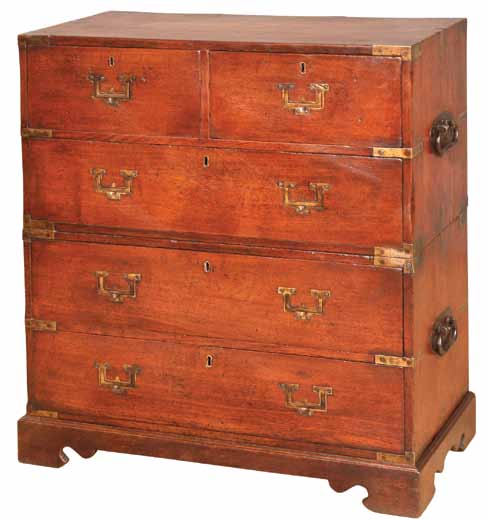
Next week I’m teaching a class on building a campaign chest at Marc Adams School of Woodworking that is a primer on the principles of casework construction.
If you are interested in blowing off work on May 6-10, check out the class description here. This class is suited for all skill levels, whether you are just getting into handwork or into woodworking in general.
An important part of this class is we will be designing our chests around the materials that each student can source. I wrote up this design document for the students and thought that some readers who couldn’t attend the class might be interested.
Materials
Campaign chests were made from a variety of materials. The most common woods were mahogany, teak, camphor and oak (white or English). However, almost any cabinet-grade wood will do and an example probably can be found in the historical record. I’ve even seen them made out of pine.
What is important to note about these chests is that some of them did not have any secondary woods used for the interior pieces. The best examples were made entirely out of mahogany – even the drawer bottoms and backs. This made the chests much more resistant to rot and bugs. It also raised the price significantly.
There are lots of examples out there that did use secondary woods for interior components. Common secondary woods were oak and pine.
As far as thicknesses go, the carcase materials should be made out of wood that finishes out at 3/4” thick to 7/8” thick. These thicknesses work well with the available brasses, particularly the corner brackets and straps. The cabinet backs should be made out of 1/2”-thick material. The drawer sides, backs and bottoms can be 1/2” or 3/8”. The 3/8” stuff is very old-school English.
If you are going to use turned feet, you’ll need some blanks that are about 2-1/2” to 4” in diameter and about 5” long.
Brasses
The most significant investment on one of these chests is in the brass. For the class, you don’t need to have your hardware with you. I’ll have lots of examples for you to examine in many price ranges. You can then make your decisions without having to spend hundreds of dollars on examples from all over the planet (I already did that for you).
If you’d like to get a head start, call Londonderry at (610) 692-5651 – they have a new catalog section devoted to campaign brasses. Also, get a catalog from Horton Brasses (http://horton-brasses.com/). Orion Henderson at Horton is happy to work with woodworkers to get a suite of hardware together that works for you. He’ll order stuff from England on your behalf and color all the brass to the same color.
Design
Campaign chests were built in a variety of sizes. I’d consider building a chest in one of these three basic dimensions:
• Dwarf chests, which were uncommon, would be 31” high, 28” wide and 15” deep.
• Standard chests are about 40” high, 36” wide and 16” to 20” deep.
• Large chests are 40” high, 40” wide and 20” deep (or more).
Once you decide the overall size you want to build, I think the next step is to decide if you want to build one that is on a plinth, sled feet or on turned feet. We’ll be reviewing a lot of these examples in class so you will be able to get a feel for them. Some things to think about:
1. The turned feet are usually removable (via threaded wood screws). They make the chest look less massive – that’s good or bad depending on your eye.
2. In some cases the “sled” feet are not the original way the chest sat on the floor. The chest might have had turned feet that rotted off or were discarded or lost. So you can design this concept into your chest (i.e. make a chest that is lower with sled feet).
3. Plinth bases are less common than the other two options, but there are examples where they were original to the chest. Original examples with a plinth usually have the plinth as a separate component – so the chest would be made in three pieces: top case, lower case and plinth.
When I design casework like this I begin with the material. What is the widest board I can find that is long enough (10’ to 12’) to wrap the grain continuously along the side, top and other side? If I can find 18”, I’ll make the case 18” deep. If I have 16”, I’ll make the case 16” deep – I don’t glue a 2”-wide board to the case to make it 18” wide.
Let the material dictate the depth and focus on finding one beautiful board for the show surfaces of the case. If I can’t find one wide board, my tendency is to look for boards that are 8” wide and glue them edge-to-edge to make the case sides and top.
Next search out the board for the drawer fronts. My goal is to find one board (12’ to 16’ long) for all the drawer fronts. I’ll usually look for something 8” to 10” wide for a regular chest of drawers. And 12” wide if I am making a secretary.
After you get the boards you need for the exterior of the case and the drawers, the rest is easier.
You need solid panels of primary wood for the bottom of the top case, plus the top and bottom of the lower case. These can be glued up from thinner stock as the only thing that will show is the front edge. Count on getting about 15-18 board feet of primary wood for these parts.
You’ll also need some primary and secondary wood for the two web frames that separate the drawers in each case. These web frames are made from pieces that are 2-1/2” to 3” wide. Count on buying 24’ linear feet of this kind of material for the web frames.
The backs can be made from secondary or primary wood. Plan on 10 board feet of 4/4 material for the backs.
The drawer parts can also be made from primary or secondary wood. Plan on 35 to 40 board feet for all the interior drawer parts.
Finally, source some wood for the base – turned, plinth or sled.
The rest of the design process flows from the wood you have on hand and what sort of chest you want: Do you want a secretary or a chest of drawers with four or five drawers? What sort of drawer graduations do you want (there are many schemes)? These are the things we’ll be discussing on the first day of class – so don’t be hung over.
— Christopher Schwarz
Like this:
Like Loading...