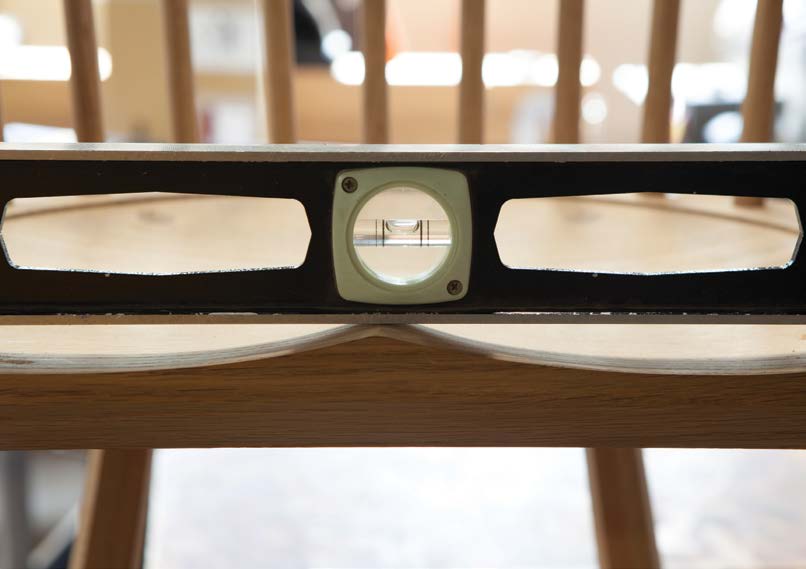
Got a woodworking question? Post in the comments below between now and 5 p.m. Eastern, and we’ll do our best to answer. In between answering, Chris is getting ready for an upcoming class and video shoot with Jerome Bias, and I’m working on a personal project (so if we don’t answer right away, that’s why).
— Fitz
Comments have been closed. See you on April 19!
Can you explain your process on how to make cylindrical tenons with a hand plane? I think I’m the Stick Chair Book you say something along the line of “think circles”, but more detail would be great! Thanks.
First draw a 1″ target on the end grain of the leg. Plane or shave down almost to this line all while rounding the tenon.
What you’ll have is a taper. You need to un-taper it. When you create a taper, your plane a short stroke at the end of the leg, then make longer strokes until you are planing the entire taper.
To untaper, you basically reverse this process. Take a short stroke at the fat section (this will be a stopped shaving). Then take a slightly longer stopped shaving. Then a full stroke. This untapering process begins about 6″ from the end of the tenon.
Next time I’m doing this I’ll shoot a video.
In reversing the taper I’m introducing convex entasis on the stick a the 6” section unavoidably, correct? Video would be great, perhaps including drawknife as well? Thank you
Yes.
A bit of a weird question, but I was wondering if Megan had a good design for a building a cat litter box, or at least something to encase the ubiquitous ugly plastic variety? 🙂 I think both my wife and cat would appreciate my building some sort of upgraded version…
Um…I do not. But if I were making one, I’d probably look to something in the arts and crafts realm and just leave it open at one end. And hinge the top.
Thanks for continuing to do this 🙂
Do you sharpen the enormous Barr 2” bench chisel with a 35 degree secondary bevel like any other chisel and do you use your wet stones or something else?
Do you use your drill bits, like your Lee valley set, interchangeably in your powered and non powered drills and are some more suitable for one over the other and how can you tell?
Lastly Megan, are you using the coping or fret saw from Knew concepts. Their range is a bit confusing. Do I want to cope or fret out the waste?
Thanks 🙂
Shawn
On the Barr chisel, yes to a 35° secondary bevel. On waterstones.
The small Lee Valley bits work in hand drills. But if you use a brace, you might need to use augers that have a tapered square shank for the large sizes of holes.
I’ll let Megan answer the coping saw question.
I use both a coping saw, and a Frisa, depending on the wood and the thickness of the wood. I tend to use a fret saw, one with the swivel blade holders, on 1/2” stock or fairly soft wood up to about 3/4”. On 3/4” + hardwoods, or thicker stock altogether, I use a coping saw. I use Pegas blades no matter the saw. If I had to buy only one, it would be a coping saw. Then I would get some 18 TPI blades for soft wood and thinner stock and maybe 8-12 TPI for thicker stock and harder woods.
Thanks Megan. Hope you are feeling better.
That’s where I got confused. I didn’t think you could put a Pegas blade on a Knew “fret” saw as it’s a thinner blade. The Knew “coping” saw takes Pegas blades. What am I missing.
I called Lee Valley prior to purchasing and they are now confused as well.
Loading…
Reply
I have fretsaw blades on mine. Maybe KC changed things. A question for them, I’m afraid. (I use these: https://toolsforworkingwood.com/store/item/MS-FRETDT.XX?searchterm=pegas)
How thin would you recommend making a top for a small table or a large table with wedged staked legs if I didn’t want to add a sub top or battens?
Thanks!
Depends on the size and function of the table. But in general, you need 1-3/4″-thick stock for something sturdy. Maybe 1-1/2″ for a side table.
The battens are serving two functions: Making a better joint, and supporting the top’s width from cracking down the middle. So you need some meat.
My planing sucks – It was okay for awhile but has gone downhill – can you point me to a good section in one of your books – or elsewhere – so I can get a refresher on how to plane boards flat.
Thanks
“The Joiner and Cabinet Maker” has a good section on processing rough stock to flat. As does “Handplane Essentials.” I’m sure there are free video tutorials out there, but that’s not info I go looking for….
Hi, I’m looking to build a saw bench, the type that you’ve demo’d and built. Do you find that the splayed legs interfere with rip cuts? Or do you always rip down the center between the “birds mouth”? Thanks
I don’t rip on sawbenches. I think it is much easier to rip on the bench (search for “overhand ripping” to see how).
Some people who rip on sawbenches make two of the legs un-splayed to assist in rip cuts.
So I have managed to find a U shaped branch of English Oak which is fresh from a tree that has just been felled (branch is about 4″ diameter). Perfect for a continuous arm on a stick chair. Now what? Never worked with green wood before so not sure whether I need to cut to rough shape first and then let it dry or let it dry and then cut it, etc. Or just crack on with the wet wood and let it dry once the chair is made. Can you provide some guidance as don’t want to take a wrong step and ruin the wood/ chair. Is there a good book that explains how to manage green wood in a stick chair context. Thanks for your guidance.
You are in the wilderness on this one a bit. I’m not far enough on this path to give you any advice. Chris Williams has been doing it for years and will be covering this in his next book. Jogge Sundqvist has also been doing this for years. He discusses it a bit on video (search YouTube), but not enough to walk you through the whole process.
A basic summation of what’s out there is this: Let it dry. Resaw it – discarding the pith. Gradually reduce the width of the stick to the desired shape.
Maybe someone else has written about this in detail, but I don’t know.
“Next time I’m doing this I’ll shoot a video.” A video would be very helpful. So this tenon has no shoulder, correct?
Correct
I am planning to start making your Irish Stick Chair featured in FW. Is the location of the arm over the seat intuitive, or can you provide some guidance on how to align the arms on the drilling jig? I understand the 25 degree angle of the back, but it appears there is also left-right lean for the long back stick, and a compound angle for the short front stick also. If I get these two right, I’m assuming the other short stick will just fall into place.
Thank you
Page 451 of “The Stick Chair Book” (a free download) shows the position I used. That chair is on the same chassis as the FWW chair.
Good morning. Have you used the Zinsser premixed shellac products? Either the Bullseye Shellac or the Bullseye SealCoat. I believe the SealCoat is just dewaxed at a thinner cut.
And what is your preferred method of applying shellac? Brush or wipe on with a pad?
I’m thinking of using the clear shellac as a finish for an “anarchistic”bookcase I built in white oak because that’s what I had in hand.
Thanks once again for your generosity!
Sam
We’ve used the Zinnsser stuff. It’s fine as long as it hasn’t expired (you’ll know if it’s expired because it won’t dry). I always prefer a dewaxed shellac. I like to pad it on if you don’t have a sprayer.
I greatly prefer to mix my own. Fresh quality shellac has no equal. We use Tiger Flakes from Tools for Working Wood. There are lots of other good brands of flakes out there.
Many thanks!
I am building a very loungy and stickchair for reading at the fireside. Maybe with a small glass of whiskey in my company. This is my 3rd stickchair.
Question. Until now my armrests have been parallel to the seat. Is there any reason I haven’t seen any of your chairs or stick chairs in general that has the arms parallel to the floor? My seat angle is two fingers and backrest is about 20degree
With stick chairs, the arms typically are parallel to the seat OR with the hands higher at the front of the seat (to lower the lumbar support). I’ve never seen one with the arm higher at the back. I suspect because this would press hard above the lumbar, but I haven’t ever done this so I could be speaking out of my butt.
Mock it up with scrap to get your answer.
Thanks. Knowing no shoulder makes it make much more sense to me!
I’m building a bar stool and plan on using box stretchers to strengthen the legs, stop it twisting and to provide a footrest. What’s the best way to drill the mortices in the legs for the stretchers? Drilling the first mortice in a leg is easy (if the angle is off slightly I can twist the leg a degree or two to compensate), but this isn’t possible for the second mortice once the leg is fixed.
I thought about treating it a bit like drilling mortices for the sticks in the seat/arm in a stick chair with someone spotting me bit this isn’t perfect as I usually have to ream the underside of the arm to get everything to fit. Any other suggestions? Would a H configuration actually be strong enough to stop the twisting and avoid this altogether?
I’m looking for your thoughts on reasons not to try something. Rather than repeatedly mounting a carver’s vise on my bench, I’ve wondered about using a tool stand. A company called Trick-T tools makes a portable one. The stand mounts to a steel plate that you stand on when you work it, giving it stability, and then you can roll it out of the way. This seems like it would be convenient, but as you do this kind of work every day, I figure you might see pitfalls in such a setup. Here’s a link to show what I’m talking about: https://tinyurl.com/versamount
Did earthly cabinetmakers use sliding dovetails to attach dust frames to the cabinet. And if so, how did they start cutting the tails?
It is a fairly common practice. The tails can be cut with a dovetail plane, a common wooden plane still made today. You can also cut the shoulder on the tail with a saw, then cut most of the slope with a rabbet or shoulder plane. Then finish up with a chisel.
The dovetail plane does the job in seconds.
I just scored some strait grained 8/4 mahogany, would you recommend making a stick completely out it? What backrest spindle thickness would you recommend, and also the legs?
Absolutely. I have made five or six stick chairs from mahogany. Its interlocked grain makes it excellent (if a contrarian choice) for this form. Just use the stock thicknesses shown in the books.
I have a vague memory of somebody putting an access hole in the end of a six board chest to contain the litterbox. Open the lid for maintenance. OTOH my sister’s new house has half long storage closet doors with relocated hinges in both bathrooms, bottom half is open for the cat to get to the litter box in the storage closet. If somebody catless buys the house they just replace 2 standard size doors, just happen to have 3 hinges not two.
I started using linseed oil paint this summer. I love working with it and how it looks newly painted, but after only a few months the areas of high wear have worn through. Is this your experience or did I do something wrong?
I used Ottosson paint and followed the directions. The wear is where hands rub against a table. Nothing abrasive.
Hey Chris what is your current iron choice for a Stanley no 5 type 11 plane and if replacing the old iron, do you advise replacing the chip breaker as well for a perfect fit or only if it’s condition requires it. Thanks
I used the stock iron and chipbreaker until I used up the blade. Now I have a replacement blade (it’s a Lie-Nielsen, but there are many other good brands). And I still use the stock breaker. You don’t have to go all premium on the jack plane. In fact, I don’t think it’s ideal to.
Thanks Chris. I’m more concerned with it fitting properly. Just ordered an old Stanley and the iron is shot. Does the Lie Nielsen stock #5 blade fit the Stanley without modifications? Thanks
Depends on the individual plane. Maybe yes. Maybe no. Mine worked. But other people report problems (mouth needed to be filed open… blade adjustment dog couldn’t reach the breaker). If it doesn’t work, send it back and order a thinner blade that will work.
I have 2 DFM Tool Works irons, “CPM 10V 2″ Plane Blade”, thickness = .1″.They will work in most of my Stanley #4s & #5s but a couple don’t work well.
I replaced the original iron in an old Stanley #3 with a Magnacut from Lake Erie Tool Works. I used the original chip breaker. The new iron was thicker and I had to open the front of the mouth. It was unnerving but I pressed on and did it a little at a time until the iron fit. The only remaining issue is that the screw for the cap iron is barely long enough – if I loosen it, it comes out. Having said all that, it’s my current go-to smoothing plane.
And this is why thinner blades are sometimes the better choice.
Stick Chair Comb Question:
In the stick chair video, Chris shows the 7/8″ rounding of the ends (vertical) and the 7/8 rounding of the top (horizontal). Where the two roundings meet, there is a diagonal line; at least when I do it. Do you leave the line? If not how to you avoid it or remove it?
thanks,
Les
I love the line. But you can shave or sand it away if you want the full pillowed effect.
I started using linseed oil paint this summer and love to work with it and how it looks newly painted, but after just a few months it’s showing signs of wear. I used Ottosson paint and followed the directions. The wear is where hands rub on a table top, nothing abrasive.
Have you experienced this?
I have not. The stuff is tough as nails. You might want to ask the manufacturer.
sorry for the repost. My first try gave me an error and it didn’t immediately post, so I thought it was lost.
Gibson chairs. Why do they have the angled sticks on the back? Aesthetics? Statement of origin? I doubt structural advantage or other chair designs would have incorporated.
Also, is your Gibson design more comfortable than the FWW Irish stick chair design? Admittedly a subjective observation but wonder your opinion.
Mr. Gibson is long dead. So we don’t know. They don’t add comfort. But they do tighten up the back structure as they go in, locking everything.
“Sharpen This” is an excellent book, thanks very much for your work producing it.
The preliminary squaring off the end of a damaged socket chisel,(such as ‘everlasting’ Stanley 40) , is very difficult for me to do freehand on a cambered grinding stone, as you present it. My edge is never perfectly square. It’s easy to remove more metal than you’d like, trying to get the edge square. Similarly, a shoulder plane blade (eg Terry Gordon’s) requires a perfectly square edge to function properly. Gordon demonstrates the use of a large disc sander, the blade side being held on the device’s cast iron table to present a square edge. This however is more cumbersome to do with items that are “handled” such as the everlastings. Is your hand eye coordination just superior? Any other useful tips?
M weiss.
I’ve never had a problem getting a square edge. I makr a line and work to it. Maybe try dressing your grinding stone flat to see if that helps?
Hi Chris and Megan, happy Saturday.
Chris, is there a specific interface pad size or thickness that you usually use on your random orbit sander for cleaning up chair seats? Can you interchange brands of interface pads with different sanders?
We use the Mirka interface pads, which work with any sander and any hook-and-loop abrasive. Mirka, 3M and others also make the squishy pads for the curvy sections.
Dutch tool chest handles: I have the ones you recommended from Lee Valley that come with screws. I’ve been having a hard time finding nuts and bolts that fit, let alone ones in black. Did you ever use machine screws on a project?
Oh sure – and I’ve hacksawed them to length. And used a Sharpie to make the heads black.
I have a small shop and very few power tools, but as I get older, am considering the purchase of a power handplane. Is this a tool you use and find useful ? If so, is there a specific brand that you like? Most of my work would still utilize hand tools, but I thought this might lighten some of the laborious work.
Depends on your work. Toshio Odate uses a power plane for most of his coarse stock removal. But he builds massive slabby things. (Makita makes the best power plane in my experience)
My work (chairs and casework) wouldn’t benefit much from a power plane. I’d get a small band saw.
If you build just casework, a powered suitcase planer would be a good choice.
I have a no. 4 smoothing plane and I control tearout fairly well with the cap iron. I’m going to make a no. 3-sized coffin smoother Richard Maguire/Krenov style which I plan to use more for final smoothing due to the smaller size, but I also want it to be my super smoother / plane of last resort. Should I make the bed angle 50º instead of 45º for a bit more tearout control, or that trade off would make the plane less nice to use in most circumstances and relegate it only for the toughest grain (which I don’t typically deal with, and usually get by with the cap iron pretty well).
I don’t think you’ll a lot of advantage to a 5° increase in pitch. I sure don’t. A 10° increase helps more, but it makes the tool much harder to push.
There is always a trade-off when moving the breaker closer (plane is harder to push), raising the bed angle (plane harder to push) or closing the mouth (fussy, easy for plane to clog).
Congrats on the Anthe building progress! Will it be “soft” open before the grand opening?
Nope. It will be down to the wire for March 9
Some time ago I asked you about making a southern pine stick chair. You said go for it; you’ll learn a lot. It’s turned out great! The two most important things I learned are: 1) The chair is shockingly comfortable, and 2) my daughter really loves the chair. Thank you!!!
About 2 weeks ago I moved to Ireland. I flew over with two checked bags (family to follow in the summer), and while I brought some tools, the majority are going to be replaced. Most are no great loss, but now I need to start to find places to buy new hand tools. Shipping from the UK via Amazon is one option, but I’m curious if the good people at LAP have any information on tool retailers, the second hand market, or a local resource who might know. I’d welcome any good local info on lumber as well. Thank you!
I don’t have any sources for tools or material in Ireland I’m afraid. Readers here might. You might talk to the good people at Classic Hand Tools UK, which carries a wide range of hand tools.
Thank you all! I will do those things.
There is a group called vintage tool patch on FB. I believe I few members are based in Ireland so may be able to help. I’m in UK and have good experience with Classic Hand Tools and Workshop Heaven, not sure about shipping charges/taxes to Ireland. There is also Dieter Schmid Fine Tools based in Germany
Hey Matt – hookup with @marnanewoodwork – does interesting wood and seems to have a huge collection of rescued yools
Hi, I am planning to finish a single bay Dutch tool chest and mobile base with milk paint (blue of course!). Is a one pint container enough, or should I plan to order more?
A pint should be enough.
Perfect, thank you.
Hey team,
Just got and ready my DTC book, thank you for it, I understand so much more now. On that though, are there any gotchas that I need to think about if I don’t use the nail/screws and go for an all wood construction, other then wood movement itself?
I have been thinking about wedged M+T for the upper section bottom and wedged pegs or trenails for all the other nails. Screws are blagh and nails are out of my reach for now per the family accountant, but I have enough random material laying around to make all the pegs I may need and my home center has reasonably priced carcass material. Historically it may not be as accurate, but I am not a tradesman making my livelihood, just a passionate hobbyist starting my hand tool end of my journey.
Huh – I rally haven’t given that much thought, and I haven’t tried it…so I’m speaking out of my backside here, but I would think pegs could work, as long as you drill proper-size pilot holes for them. And I would absolutely test that on the test setup, because you’re gonna be really close to the edge on all of those. Best to find out on a test setup than on the piece itself.
I read your announcement regarding the new pinch rod set. I love the original but I set it up for large work and always wanted to be able to have different lengths. Then I saw your reference to key stock. Brilliant. What type of metal do you prefer? What profile do you put on the business ends?
Mild steel. We put a 35° bevel on the end so it will easily go into corners.
Thanks Megan. Hope you are feeling better.
That’s where I got confused. I didn’t think you could put a Pegas blade on a Knew “fret” saw as it’s a thinner blade. The Knew “coping” saw takes Pegas blades. What am I missing.
I called Lee Valley prior to purchasing and they are now confused as well.
I’m trying to keep a minimal sharpening kit and decided to go with the Shapton stones you recommend. How essential is it to have both the #5000 and #8000 for polishing? If you cut out the #5000 I assume it would take longer to polish out the scratch marks from the honing stone, but I don’t have any qualitative idea what stopping at the #5000 would do for an edge as opposed to the #8000.
This reply could be as long as a chapter. But in short, #1,000 and #8,000 will work with more work. #1,000 and #5,000 will work but you might see some fine scratches on your work while smooth planing. And you’ll be sharpening more frequently.
When edge joining two or more boards for a table, chest top etc, is there any advantage to adding a tongue in groove joint for more strength after first creating a spring joint? Thank you.
Cheers,
Michael
Yes and no. The T&G will aid alignment and it will add strength IF your glue ever fails or you don’t use enough glue or have some other type of glue cock up.
If you have a perfect glue joint, the joint is stronger than the surrounding wood.
So both things are true.
Thank you.
Go watch a video by The English Woodworker (Richard Maquire).
He puts splines in his work bench table tops! (He does use wood pins to hold them in place, but similar concept to what you are asking about!).
Also, he has very interesting videos and funny guy! Similar to Chris’s sense of humor and he doesn’t mind telling you to take a sliver of wood off about the thickness is a gnats ass!!!
Thank you!
I used to do a lot of green woodworking, but after moving west and wasting hundreds of hours and dollars trying to material gave it up. I love the approach you and others have taken to making stick chairs with dried wood, especially because it retains the sorta intuitive, low-cost, simple ways of working that comes with these vernacular chairs.
I’m curious how you think making a ladder back in the same way would work? I have my thoughts but would love to hear from others! One of the appeals ladderbacks made green–as opposed to the chunkier, mass-make ones–is the lightness and maybe that’s not possible with dried wood. I know the shrinking of the mortises around the tenons imparts strength, so who knows.
If I were to embark on this quest, I would make the posts’ mortises slightly undersized (or the tenons oversized) by 5-10 thou. Cut a ring depression around the rungs-tenons. Pour boiling water into the mortises at assembly time and drive the rungs in. Elia Bizzarri has done a fair amount of research into this method and finds it works really well.
Good Morning, I’m planning on building the work table from the ADB to use as a kitchen table. Since it’s going to be 8 feet long I’m thinking of increasing the thickness of the top to 5/4. Are there any other changes I should make? I’m curious if anyone else has modified this table to use for dining. Thanks for taking the time to do the open wires I always learn a few things
I think increasing the top to 5/4 is a good call. I you might also glue or screw a couple ribs to the underside that are parallel to the grain of the top to stiffen the middle. Other than that…. I think you’re good.
Lie-Nielsen makes thinner irons for use in old Stanley planes as opposed to replacement irons for their own planes. You can also check Lee Valley for plane irons that fit in old Stanley planes.
Lee Valley has them I just didn’t know if they were series or age dependent for fit. Lie Nielsen seems to only have replacement
Irons for their own planes now and no longer carry thinner replacements. Thanks
Want to build the Bowsaw Chair from your 8/2018 PW article. If I use walnut or cherry instead of the maple you used would you think any change in dimensions would be warranted? I have thought of turning the smaller pieces round to fit loosely in the 1 3/4 holes for a more meaty cross section. Also the drawing for the bottom leather part seems to show inaccurate placement for the rivets and lacks dimensions. I’ll dope out the rivet locations if you don’t have this readily to hand. Thanks.
Definitely thicken up the components. Even in maple, this design pushes the engineering limits. Definitely beef up the cross secion.
I’m afraid I don’t have the original anymore so I don’t know the dimension for the rivet spacing. Sorry.
Perfect. Thanks Megan. All is clear now.
Thanks for doing these. My question: when to use a haunch in a mortise & tenon joint? It seems clear to use it for door construction, especially thinner doors. What about a side table with aprons? I’ve seen many a video and plan without a haunch. Is there general guide on when to invest the extra effort to prevent twisting at the tenon?
In a table you can skip the haunch and make the mortise open at the top of the leg. That’s simpler. Usually the haunch is used to fill a visible groove. The twisting aspect of the tenon isn’t much of a big deal in furniture work with kiln-dried stuff that is dry and stable. I’d only worry if the wood was wet.
Milk paint question from someone who has never used it:
In ADB, you recommend a 2:1 water to powder ratio. In Chairmakers Notebook, Pete recommends a 3:2 ratio.
Obviously, the answer is sample boards, but I don’t have the paint in hand yet (will most likely be Real Milk Paint). What gives and who’s advice should I follow and who’s advice should I “disobey?”
Cheers,
Dan
I go with a thicker mix and like the results (which are sometimes a little streaky). Pete’s finishes look a lot more slick and “professional” (I’m more vernacular, as is Chris)
Adding a bit more: Milk paint is not science. Both my recommendations and Pete’s work and are good starting points. I recommend people mix some up and try it on sample board to get a feel for it before diving in on a finished project. Your experiences will provide the answers.
By shockingly comfortable, I mean everyone who sits in it has the expectation that it is a wood chair, unpadded, it’s going to be uncomfortable. They sit down and the expression on their face changes to disbelief/amazement. It is very comfortable. I want it. Time to make more chairs!
This question is prompted by the discussion about shellac above and I was also thinking about what makes a well stocked kitchen at a basic level. We often talk about what tools to have in our shops, but are there certain supplies that people like to buy in bulk and keep in their shops at all times? And why? For example, awhile ago Durhams Rock Hard was a subject which prompted me to buy a big can of the stuff to use in painted repairs. I’d used it years ago so I was familiar with it. It keeps and will last a LONG time.
The answer would be a chapter in a book. We stock:
Screws of all sorts, nails (cut, wire, Roman)
Hinges
Mending plates
wool feet for furniture
tapered pegs and wedges
glue
rags
all the basic finishing ingredients and their solvents
mason jars for mixing finishes
I could go on. Our list evolves and changes as our work changes.
Advice for beginners on how to prioritize in getting started? I’ve done a few very basic projects around the house with a circular saw and my drill kit, but would love to do more with hand tools. I’ve bought several of your books that I’m enjoying reading this winter. I have a small one car garage and currently “negotiating” with the wife on how to make space for more tools and perhaps a work bench. Love the blog and books, thank you!
Vic Tesolin’s “The Minimalist Woodworker” is a good place to get started. Or you can do what I did (I started with a circ saw and drill, too). Buy a block plane and 1/2″ chisel. Learn to sharpen them. Build a small bookcase. Then buy a backsaw and learn to cut dovetails. Build a small box.
If you want to learn fast, take a week-long class in getting started in hand tools (lots of people teach these classes).
I would cut the pith out before putting it to dry. Cut a little off the ends then coat the ends in anchor seal right away. This will prevent it from checking. I think it’s good to get the bark off right away too. Get a hard point rip saw and carefully rip it down the middle. Then you can take more pith out with a hatchet. Alternately you can use a chainsaw. I like to use my battery powered one for this because the chain is narrower. Maybe do some practice cutting on a log you don’t care as much about if you go that route. Good luck with it.
Happy Saturday and thanks for spending part of the day with us! I have a woodworking word question: I’ve been wondering recently about the use of the word “gain” for a hinge mortise. Do you have any idea where this comes from?
I do not know where it came from. Sorry.
I’m finally making a Roorkee Chair and matching foot stool in the Kaare Klindt style. Champaign Furniture shows the stretches at 23”. In the Pop Wood video around the same time, you mention more like 21 3/4 or 22. The stretches are at 1 1/4 diameter. I assume the book length of 23” is the finished length with the tendon cut. Any concerns with using 23” as the finished length? Looking through the posts and original Roorkee Chair article it seemed like the stretcher dimensions evolved some. Thanks for the feedback. Long time reader.
As long as the grain is dead straight in the stretchers, any of those dimensions will work. Small changes like that are common in my work as it evolves to handle different types of people (we are now larger and heavier than before….) Good luck!
Jim Kingshott’s videos are up on line if you haven’t seen them yet. They are simply great and great entertainment even if you aren’t a woodworker. https://www.youtube.com/watch?v=H4Gq91Dcm7o
If you listen closely so they don’t blow past, you will get a lot of one-liner bits of information.
Since this one is a video about dovetails that I discovered while researching scientific articles on dovetail strength, here are some findings from the scientists. First, most scientific articles are for post and beam construction in Asia so they aren’t relative to dovetails for boxes. Second, back in January 1958 Woodworker magazine posted test results of router cut half-blind dovetails which have been widely misinterpreted. The goal was to find the optimal angle for tails while keeping the tenon part of the tail constant. They used “white wood” and mahogany for comparison and test to failure in tension. The tails were cut with a router so the tips were rounded and not like hand cut dovetails. 7.5 to 17.5 included angles. They tested both unglued tails and glued tails. Surprisingly the glued tails failed first because the wood sheared off parallel to the grain while the glue held the flare of the tails in the joint. The unglued tails were interesting as the fibers compressed and the tails slipped slightly. The failure mode changed as the angle increased. For mahogany, at low angles, the compressed fibers allowed the tails to compress and slip out from between the pins. At high angles the corners of the tails failed. For the white wood the failure was always due to compression of the fibers and the tail slipping out.
But, dovetails holding any kind of a box together aren’t subjected to 1,000 lbs of tension. They get repeated shocks as the wood goes through the humid and dry seasons so this test isn’t relevant. Kingshott says that dovetails made by carpenters, like the shipping boxes made by Frank Klausz, typically have tails and pins of equal size for strength. For the fine work using premium materials that he specialized in, he says that tail angle and tail and pin size is just a matter of aesthetics. So go look at the middle drawers of a lot of antique dressers and see what worked in your area.
FWIW I got a couple maple arm bows from a tree that fell down. Before letting it dry John Porritt advised I draw knife the bark off. I wondered how much work that would be, but it was actually quite easy. First time I’m trying it so I know only that much from experience. John also advised leaving as much material as possible for as long as possible. I imagine because if something funky happens while it dries I’ll have more room to work around any problem spots.
Hello, I’m a fairly beginner woodworker taking on a large glue up for a table top (4 boards of 6/4 beech, about 7ft long). I’m working to edge joint the boards with a 4 1/2 and a 5 bench plane, and I am having some difficulty getting them flush. Am I a little too ambitious taking this on without a jointer plane or more experience? I love building skill and completing projects, so don’t want to get too discouraged trying to get this perfect. If I’m aiming for “workable”, is there a good threshold for how flush these need to be for a successful glue-up? Also, would you recommend the technique of planing edges while clamped together for stock this wide and long? Thanks!
I think most woodworkers would struggle with a 7′ top. That’s no easy task by hand.
Definitely try clamping the two mating boards together and planing them simultaneously (it’s called match planing). It’s good because you don’t have to get the edges square. Just flat and coplanar. As far as how perfect they have to be…. My rule is if you can close the gap with hand pressure, you’re fine. Other people say closing them with clamp pressure is enough. Still others for for airtight.
So there’s no correct answer.
This is super helpful. Thank you!
Hi Chris
Working on a low bench and plan on incorporating a vise and shaving horse and plan to use wooded screws. My question is what tap and die have you found that does a good job at a reasonable price and recommends on size. I see tap/dies from $40-$140. I was planning on going are 1-1/4”. Thanks so much for the generous help to the community.
I haven’t found a new cheap tap and die that works well. You might find a vintage set that is cheap and works. The one I use is German-made and is from Dieter Schmid. https://www.fine-tools.com/gewind.html
There also is a router-based solution that Lee Valley makes.
Hi Chris. I recall a blog post where you had set up a 36” slab of flat granite with belt sander paper. Do you still use it? Besides flattening the soles of vintage planes could you also use it for flattening the back of plane irons? Thank you!
Yup. We use it for flattening soles of planes, the backs of plane irons etc. Cheap and useful.
Take a look at Gunny Juice! It’s a liquid Diamond paste that dries to a powder! Put it on a leather strop and use it after your 5000 grit stone.
30-40 strokes to a side, then two or three alternating finishing strokes and you can see your nostril hairs in the reflection and hairs on your arm will jump off they are so scared of how sharp the blade is!!
Do you have a recommended method to refinish an older chair?
In my case I believe the old finish is danish oil. Current plan is to wipe with mineral oil to break down the finish and use a card scraper or 240 grit w/ orbital sander to remove the finish.
Well Danish oil can be varnish, or oil or something else entirely. If mineral spirits can remove the finish, you are golden. But you might need to try some other solvents, such as alcohol. Refinishing is not something I do a lot (or like to do), so you might check out a book on the topic for some real help. Sorry.
(Should this reply end up in the wrong place it is answer to Matt’s question about buying hand tools in Ireland.)
If by “Ireland” you mean the Irish Republic (which is in the EU), rather than Northern Ireland (that isn part of the UK), buying from the UK has the post-Brexit disadvantage of involving customs clearance with fees, duties and sales tax on top of the purchase price and postage, so while both Classic Handtools and Workshop Heaven in the UK are excellent sources for tools, you might also want to look a further afield, to Continental Europe. My four favourite shops in the EU are (in alphabetical order) Baptist in Arnhem in the Netherlands, Dictum in Munich, Dieter Schmid’s Fine Tools in Berlin and Rubank Verktygs AB in Stockholm. They are all excellent, with some overlpping and some unique to each stuff in stock, and very nice and reliable to do business with. Postage to Ireland from the continent can still be a tad on the steep side, but at least there’s no customs clearance.
Cheers,
Mattias
When designing a stick chain seat how to you design an armbow that matches? I’ve been playing around with the layout computer and I’m having a hard time making an armbow that isn’t just a half circle. I’m looking to make something closer to the armbow/seat combo in the stick chair video. Thanks.
There are lots of seat shapes out there for stick chairs (many are shown in the seat section in the Stick Chair Book). Try an ellipse for the back half. Or make a flat back section (6″ long) joined with quarter circles. Round seats work great. As do square ones or pentagonal.
Try these folks on YouTube for planing techniques: calm and grounded. Bob rozaieski and rex krueger
Most of your books you state you prefer modern hollow augers.
Any tips for using a vintage one?
I struggle getting it dead center of the stick/leg, even getting the spoke pointer centered is kicking my butt
It’s a struggle with all tenon cutters. Confidence and practice help. Shaving the tenon close also helps.
I just finished the top of my workbench. After I complete the base, I’m trying to decide what to build next to christen the workbench. What projects do you think offer the most bang for your buck in terms of skill building for newish woodworkers. I started about a year ago and have done a set of saw benches, a Dutch tool chest, a dovetailed stepstool, and a shaker side table.
Some ideas:
picture frames (to learn mitering)
Staked stool (to learn round mortise-and-tenon construction plus rake/splay)
Moravian stool (to learn sliding dovetails)
Keep it small so the wood investment isn’t dear if you screw it up.
Is there a book you recommend for casework? Cabinets, chest of drawers, etc?
Not a lot out there for the traditional ways to put these together joint wise.
“Illustrated Cabinetmaking” by Bill Hylton (easy to find used)
I’ve built two stick chairs from BS ap far, one for myself and I gave away another to a friend. My next goal is a stick chair from the he stick chair book however I’d love to be able to adapt the plans to include sandwich drilling the arm. Any advice on getting the angles right or is my best bet to just make stencils and then prop up the arm 8 inches from the seat and then measure the angles with a protractor? Or should I map it out on paper and do some trigonometry to get the angles right?
Thanks for all you do, there are two more chairs in this world that wouldn’t be here if it wasn’t for this blog and your books.
-Tanner
The biggest challenge in doing what you propose is that the radii of the seat mortises and arm mortises are different. You can’t just use the templates and go merrily along. My advice is make the arm and keep the seat oversized and square (like in the BS book). Drill the mortises for the back sticks sandwich-style. Then shape the seat based on the mortise locations. It will make the seat a little bigger than the 16″ x 20″ format I use in the Stick Chair Book.
Hope this makes sense. And you can save a lot of headaches by mocking things up with junk/scrap and drilling it to find all the snakbites before you use your good wood.
So, I have this Nicholson style bench that I thought would be my BFF, but me and the apron are simply not getting along.
I would love to remove much of the front apron, but am concerned that that might muck up the stability of the bench.
Should I just develop a love/hate relationship with the apron or shout Hold my Beer!! and cut away?
As always, thanks.
You can remove the front apron (leave the back apron for stability) and beef up the front of the bench with some boards under the benchtop.
Thanks for the milk paint answers earlier. Last one (for today). I’m assuming whatever ratios you use of water to powder are volumetric not by weight, correct?
Cheers,
Dan
Yup.
Like tapering the stick down even before using the pointer? I’ll give it a try
Ireland (Eire) being in the EU means probably easiest via any of the following. Baptist.nl, Dictum.com, Finetools.com, Rubank.se, willyvanhoutte.com, all available in English and with no customs shipping to Eire (unlike UK thanks to brexit).
I set out recently to make a pair of 14” handscrew clamps — the old fashioned wooden screw kind. I have two questions.
1. My local lumber yard didn’t nave maple dowels, so I bought their “hardwood dowels” sourced from the Philippines, which have a very pale color and grain similar to poplar. The wood turned to mush when I tried to use my thread cutting tool, which has previously functioned perfectly on oak, maple, cherry and walnut dowels. So I’m assuming that the Philippine “hardwood” is the problem. Might anything else be an issue? Would soaking the dowel in oil before thread cutting make a difference?
2. I’m using an old Fine Woodworking article (FW #6) for guidance on making the clamps. The author recommends making the handles from stacks of 1/2” wood scraps, drilled and tapped, rather than simply drilling and gluing handles onto an unthreaded dowel. (He recommends stacked glue-ups to avoid tapping threads in a hole that is parallel to the grain). He says the glue joints will fail unless he uses a threaded shaft and tapped hole in the handle, plus glue —even if the handle is cross-pinned. Have you experienced this problem? Also, do you concur that stacked glue-ups would be preferable for the handle to just using a 2 x 2 x 6” piece of hardwood and shaping it? It seems to me that the thread tap should work fine no matter the grain orientation.
I’m afraid I’ve never made a handscrew. But I have used a lot of tapping/wood threading tools. Yes, the wood is your problem. The overseas mushy stuff is terrible. Hard maple is the answer. Straight and clear.
On the second question: I prefer to thread the entire length of a stick and glue it into a tapped hole. Almost zero chance of glue failure. But I can’t say for certain with this application. Sorry
Wondering if there are any books on carving barley twist. The internet has some instructions but would like a book or a link to research for said book. Thanks
I don’t know of any books dedicated to that. I’ve only seen the occasional magazine article. Sorry.
Chris, did you ever complete your infill miter from this post? https://blog.lostartpress.com/2022/03/25/new-infill-miter-plane-kit/
I bought it and have never started on it. At the time Raney did not have many videos out yet. I tried his website today and it is down. I will try again later. Youtube has, I think, 7 videos showing the assembly progression. The series stops short of installing the wood, but that part is something I can handle with trial and error using cheap wood, before using an exotic.
I have a shop with only an open garage door for natural light. I’ve hung a bunch of Costco LED 4′ tube fixtures and find them lacking when it comes to seeing fine details. Do you have a lighting recommendation?
We use gooseneck lamps on the bench, plus architect lamps embedded in a dowel so you can move them from dowel hole to dowel hole.
Some woodworkers use headgear with lamps on it, but I have enough trouble obtaining sex.
What would be a simple “smarter than physics” way to resaw a board on a Roman workbench? The crochet (even with wedge) feels too loose. I’m adding clamps yo reduce chattering sound when ripping the wood but that’s probably not how it was traditionally done?
All things considered, I suspect planks were split out instead of resawn (except in the case of veneers).
I’ve seen people who have a opening in the middle of their bench wedge the work in there for a variety of operations, including resawing. But I don’t have any magic trick here. Sorry.
Do you have any suggestions for a wood moisture reader that is within a reasonable cost?
We use the Lignomats. And I’ve used Wagners. I don’t have any experience with the pin meters, which are cheap. All the cheap ones I’ve seen feel like a cheap Radio Shack walkie talkie.
Hi Chris, quite some time ago, you published plans and a few word on how to make a stick chair for big people. Las week I spent almost an hour and I couldn’t find it.
Can you please pass me the link.
Thank you very much.
It’s behind the paywall at American Peasant.
https://christopherschwarz.substack.com/p/plans-for-the-stoutback-chair
I came to your open house last November (2024)and there was an Irish Chair on display and incredibly comfortable. Was that chair dimensioned similar to the Irish chair in your Stick Chair Book page 458?
Yup. The only significant change is the shape of the backrest. It also was in FWW last year.
Paul Sellers has a video(s?) “on processing rough stock”.
Interesting work, rescued tools…sigh
Hello! This is perhaps a more academic question than a practical one. Could a stick chair be possibly made without glue or metal fasteners, relying purely on wooden joints? The only thing I can think of is using dowels at (almost) every connection but in the absence of being covered by paint or something, that might compromise the aesthetic.
Sure. Wedges and pins can go a long way. Just make the joints squeaky tight.
If you have a forged (iron or bronze) planing stop for which you’ve drilled stepped holes but the stop is clearly not going to move further without cracking the (red oak) 3″x3″ post, would you just slowly, carefully hammer it back out and try drilling a larger stepped hole deeper? I assume that’s the best way. Many thanks for any input you may have! And thanks again for holding these Open Wires!
Yup. That is exactly what I would do. Hammer and/or lever it out and try again.
My favorite Welsh stick chair is pictured in the Tim & Betsan Bowen visual record book. The chair’s outermost long sticks bow inward toward the comb giving it a remarkably different look than uniformly straight sticks. Is this a one off or is that common in other Welsh chairs and I just have not seen them?
It’s common. I’ve built several like that. Chris Williams builds them this way today.
Thank you!
Thanks
Jerry – Techniques of Spiral Work by Stuart Mortimer. Excellent explanations of layout and carving numerous examples of spiral work
Have you ever built Drew Lasngner’s hearth chair which he used the Gibson as inspiration?
Nope. But I’ve sat in one. They’re nice!
Chris curious when do you use your 24 oz rectangular wood mallet instead of your lump hammer?
Unrelated, in your Lap book storage area where you have dehumidifiers, do you have to humidify in winter when the heat is on to maintain a set level?
Thanks
You can’t have too many hammers. It has a leather face, so sometimes I grab it when I need a soft blow.
We find that our old leaky building keeps enough humidity around. So we can keep the books at 20 percent to 50 percent MC with our existing equipment..
A quick question. I am building a table 5 ft X 30 and am using sliding dovetail battens based on ADB. I have managed to injure my shoulder will have surgery but don’t expect to be able to get back into the shop till June. I have the first dovetail cut but have not fitted the batten in. I have to top clamped to the top of my bench. The top is three 2 x 12 pieces of S4S southern yellow pine. Should I expect to see much warping or movement when I get back to work?
If the wood hasn’t reached equilibrium, yes you will see some warping. But clamping it to the bench is a great idea. If it does warp, the cross-battens should pull minor warp flat. Good luck.
I’m relatively short, and a workbench around 30” tall seems to fit me well. My current “bench” is 35.5” tall and is far too tall. I’m putting bench-crafted glide and crisscross hardware in the leg vise of my workbench currently under construction, and it looks like with a 30” bench the deepest I can make the vise is about 8”. Would it be possibly be worth making the bench say 2” taller to allow for a deeper vise?
I think 8″ of capacity is good. More than any quick-release vise has. So I’s go with your current plan of 30″.
Can you add your chicken pot pie recipe to the new edition of The Anarchist’s Toolchest? Or find some other way I can buy it off you?
Hey Chris, I am wanting to make some chair legs that are double tapered using my jack plane (so the leg is fattest in the middle). Is there and special tricks or Voodoo for this? Or is it just simply planing the leg from different directions. Apologies if you have already covered this in blog posts or open wires. Also Megan, I hope your leg is feeling better!
No tricks to it. The only considerations are where the stretchers will be (they should be near the fat part of the leg) and that you remember that the back legs get cut down more than the front legs. So if you aren’t careful, you cut off most of the double taper at the back.
Do yall feel a block plane is a tool worth going premium on? Leaning towards a LN 60 1/2, but vintage Stanley’s keep tempting me on eBay.
The LN 60-1/2 is COMPLETELY worth it. I’ve had mine for 27 years and wouldn’t trade it for anything.
10-24 screws fit the existing holes (1/4-20 was just a bit big). hacksaw to length, vinegar off the zinc and use gun bluing.
I built a cat littler box enclosure by scaling up the boarded tool chest from the ADB to the correct size and cutting a hole in the end. Construction was basically to plan (rabbits and nails) with no interior fittings.
Outside dimensions of the case are 45 1/4 long, 19 3/8 wide, 22 high. The hole is 8 high, 6 wide about 5 up from the outside bottom, centered on the width.
Thanks as always for doing these! I’m building a workbench in the Anarchist’s Workbench style for my apartment, which limits me to 4 or 5 feet in overall length. What overhang would you have on each side? Could you (and would you) change anything about the undercarriage dimensions? For example, would you make the legs or stretchers thinner/narrower for aesthetic or practical reasons (such as getting a couple more inches of storage space underneath)?
Do you have any experience and/or advice about using India ink to blacken wood? I have just built a stick chair using several different species of wood and would like to see the grain through the finish, but make it black.
Yup. I use two or three coats of India Ink from Blick. Works great. Dries fast.
https://www.dickblick.com/items/blick-black-cat-waterproof-india-ink-pint/
This is a great service – thanks! I have some oddball dining sidechairs that need regluing. They were made by “Walkerbilt” in Bridgton, Maine circa 1950ish. I grew up with them, and having inherited them I still sit on them every day.
Seat is 1.5″ white pine (in Maine, of course), leg wood is unidentified (maybe maple) 1.5″ round with 0.75″ cylindrical wedged tenons. I think I can separate all other joints, loose or not (comb, splat, stretchers) but for the legs and the two sticks, I need to remove the old wedges. Any suggestions on a relatively safe and non-destructive methid for doing that?
I think you would enjoy seeing some pictures of these, I have never seen anything like them. If you have any way that I can share them with you, without opening the floodgates, please let me know.
I built a 6-stick Welsh stick chair from the book – turned out great. Catalpa was hard to find but good for the seat and armbow (and it smells good when you work it), and the similar grain looks nice with the ash legs, sticks and stretchers, if a bit darker.
Hi Russ,
Heat, water and vinegar should loosen up the joints so you can remove the wedges. After that, figure out if the glue is hide glue or something else (it’s probably hide glue). If it’s hide glue, just add more hide glue, re-wedge and clamp. If it’s something else, remove it with care and then re-glue, re-wedge and clamp.
The Dieter was what I was looking at so that’s for the information. What about sizing the screw? What’s your general approach? The top I’m working with is a 3-3/4” slab.
I turn mine to the size required by the threader. I have shaved a few, but the turned ones cut more easily/consistently.
In the PNW, we don’t get much SYP. So I built a workbench with comparably priced construction lumber: what I was able to get is #2 SPF. The thing is solid, but very light. The top will most certainly dent if you look at it wrong.
Concensus (by me) is that it’ll need some ballast as floor attachment isn’t really an option. Any recommendations for adding some weight?
Sandbags can do the trick. Some woodworkers build a compartment for them and then put a shelf above the bags.
Would you know of any books or resources on building upholstered furniture? (Not the upholstery part, just the wood structure 🙂
Thanks.
I’d reach out to Mike Mascelli, the biggest enthusiast for upholstered furniture in the Western World.
https://www.instagram.com/michael_mascelli_upholsterer/?hl=en
For what it’s worth: on mine I found appropriate galvanized hardware, stripped it with a citric acid bath, and then used gun blue to make it black.