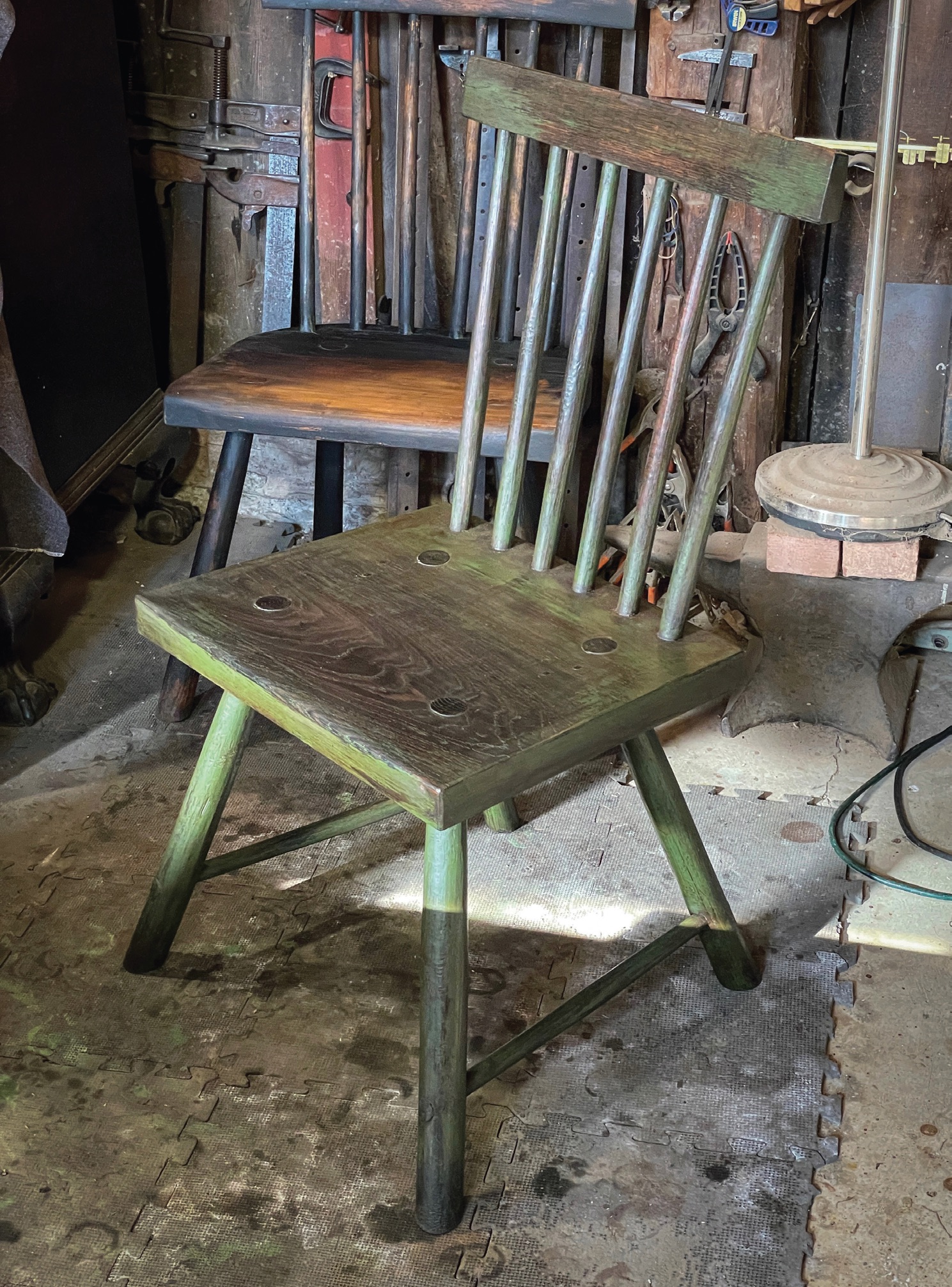
The following is excerpted from John Porritt’s “The Belligerent Finisher.” This shows the first two steps (surface preparation and adding color) before he goes on to burnish, stain, paint, shellac, oil, dent, wax, and add the finishing touches. It sounds overwhelming but the process is such an incredible transformation that you can’t help but to want to give it a try.
Porritt, who works from a small red barn in upstate New York, has been at his trade for many decades, and his eye for color and patina is outstanding. We’ve seen many examples of his work, and it is impressive because you cannot tell that any repair or restoration has been done.
His techniques are simple and use (mostly) everyday objects and chemicals – a pot scrubber, a deer antler, vinegar and tea. How you apply these tools – with a wee bit of belligerence – is what’s important.
The book is lavishly illustrated with color photos that clearly explain the process. With the help of this book, you’ll be able to fool at least some of the people some of the time with your own “aged” finishes.
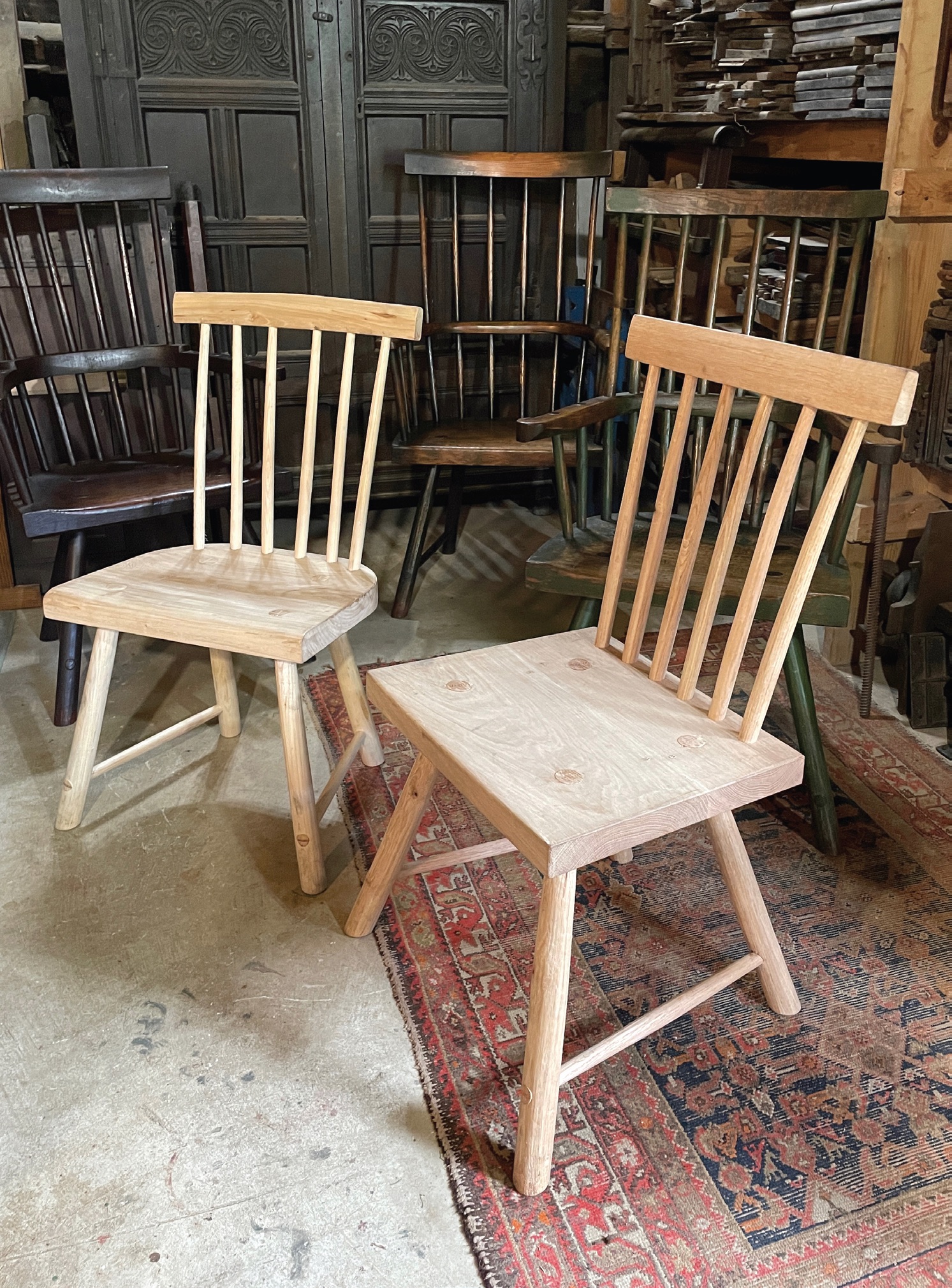
backrest that is straight. Soon, many of these crisp lines will be eased by burnishing.
This second side chair is made of oak. The seat is white oak and the rest of its parts are red oak. Because I built this chair using American species, the grain is quite straight and regular. With Welsh stick chairs and other vernacular forms, the wood is often quite gnarly. So my goal with this chair is to add quite a bit of texture to make the chair more interesting.
To help the chair look more like an old survivor, I used young, small-diameter trees. These were available to me after the workers came through. Now they’re all using wood chippers, which is most unfortunate – certainly for me. The grain of these small trees has more character than large-diameter trees with long-straight trunks.
In addition to the texture, I want the chair to have a nice chestnut brown color to the wood that looks like it has been covered in green paint – a common color on old chairs. In the areas where the sitter would rub against the seat, the green paint will be worn through. Plus, like all chairs that have had a long and interesting life, this chair will have lots of burnished surfaces.
Just like with the first chair, this chair was finished straight from the tools – no sandpaper. Plus the tenons and any pegs have been left a little proud, which makes them easy to burnish.
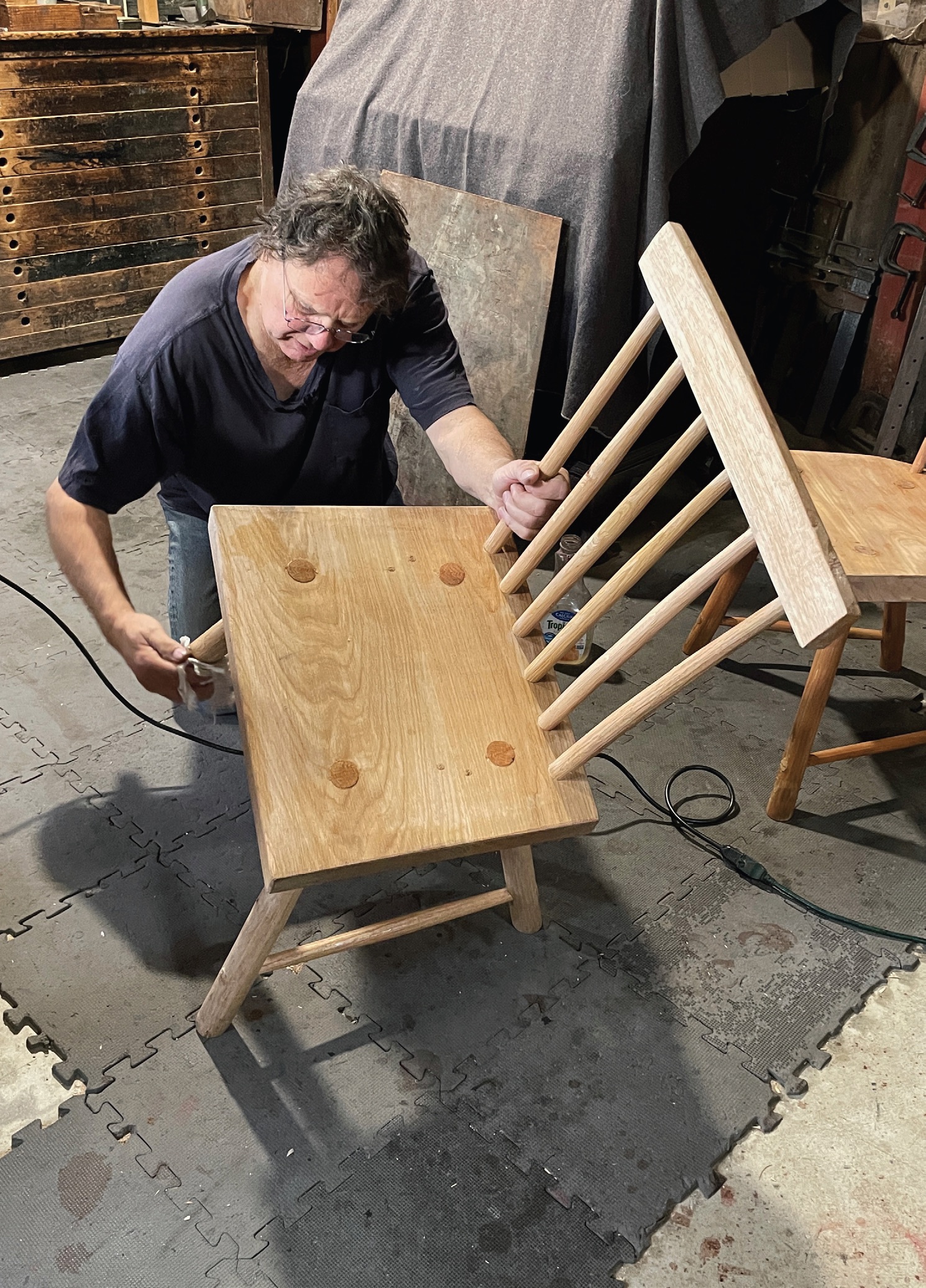
Surface Preparation. I begin this process by giving the chair a good soaking with water, which will raise the grain and soften it. I immediately follow that with the nylon brush, which is chucked into an electric drill. This is the first step to adding texture, as the nylon bristles wear away some of the softer earlywood in the oak.
You could probably get the same effect with a wire brush. As you go over your chair, spend more time brushing the areas that would contact the sitter, including the seat, sticks, backrest and the leg ends.
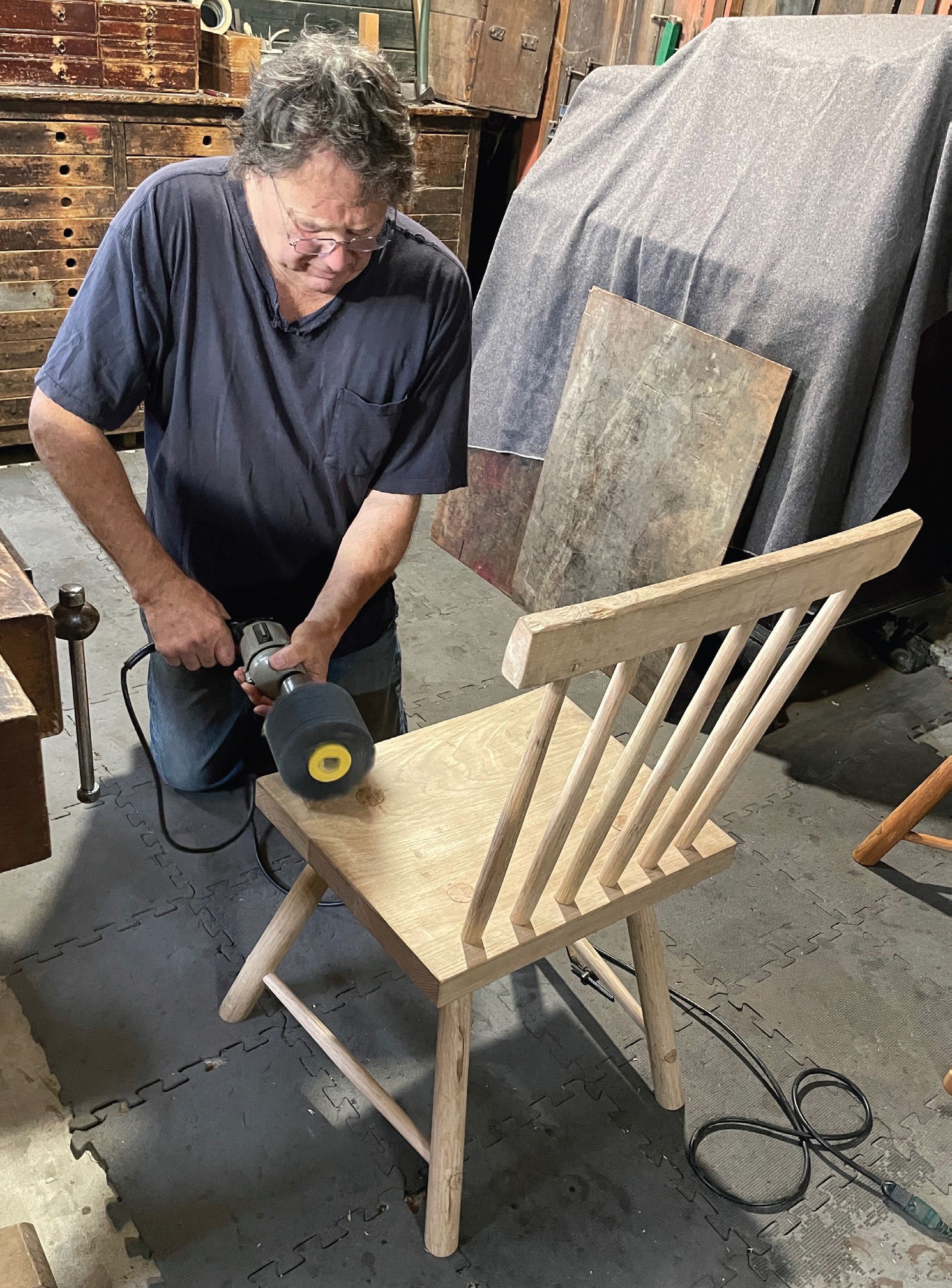
earlywood. Focus your efforts on the areas that contact the sitter.
It may seem strange to hear about using the nylon wheel brush to take out the soft earlywood and then burnish it to get a surface skin. The thing with old surfaces is they have undulations. Sometimes these are like a fine ripple, a movement to the surface where the wood has shrunk, expanded with moisture, or been abraded by time so that there are ridges and troughs. It’s not a surface straight from a cutting tool, so the brush action gets movement intothe wood and the burnishing pulls it over to consolidate it. A good, used, worn surface that reflects light in an uneven fashion.
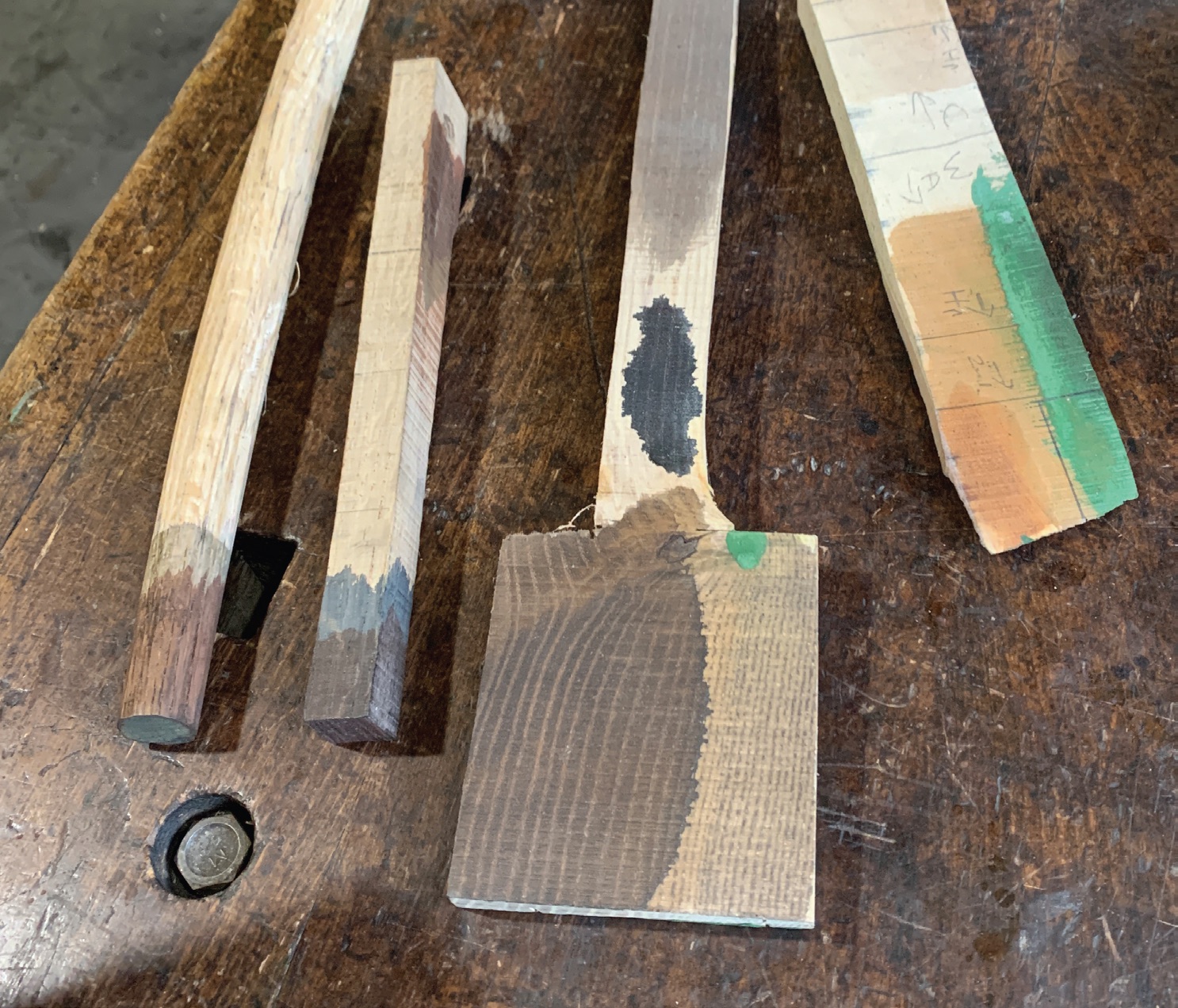
colors and chemicals will interact. It can be helpful to label each sample.
Add Color. Before I start adding color to a piece, I’ll make sample sticks using scraps from the project itself. This prevents unwanted surprises.
The first coloring step requires us to first add tannin to the wood. Then we’ll add a solution made with vinegar and steel wool, which reacts with the tannins to give a nice, aged color to the wood.
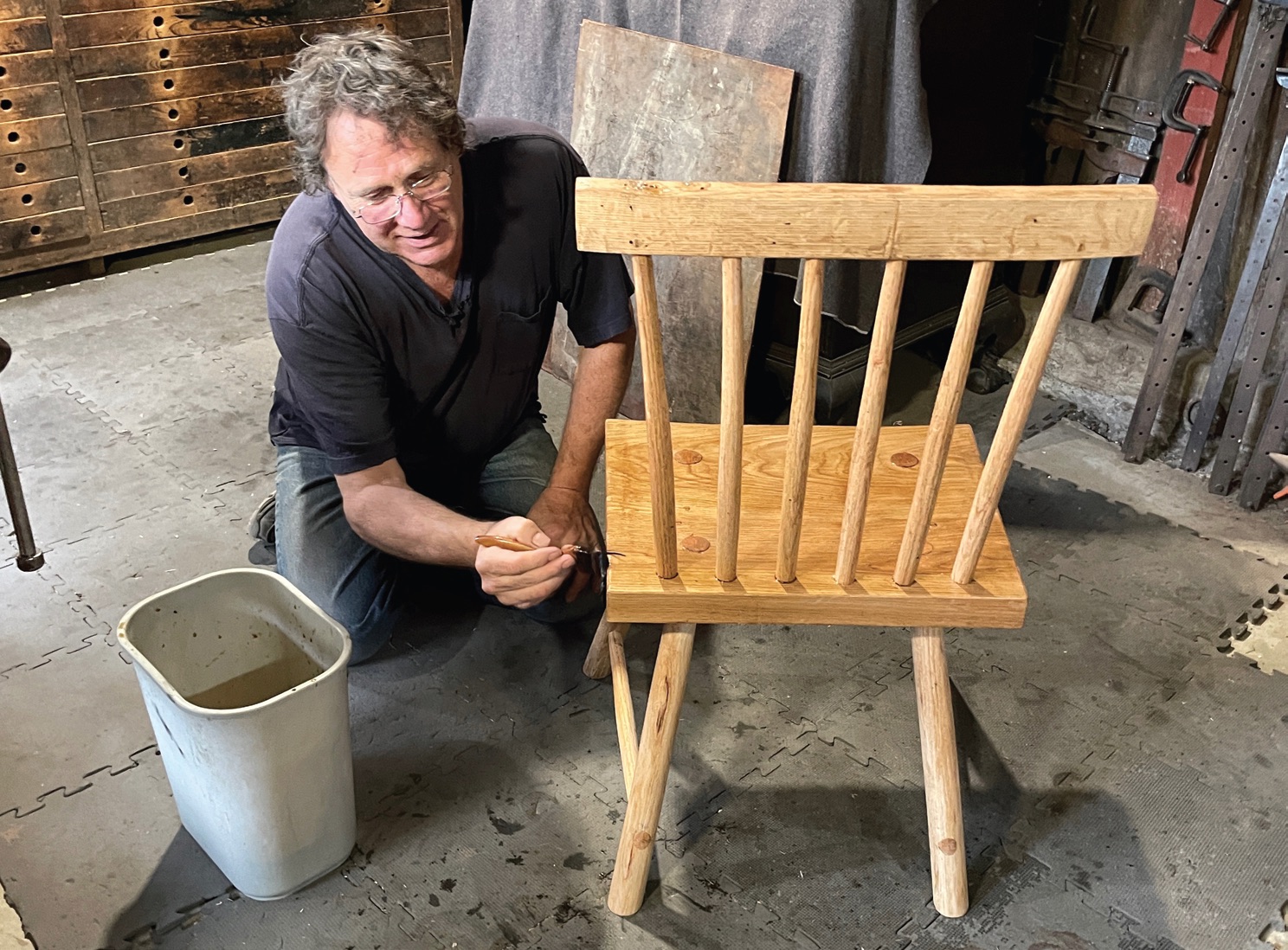
To make the tannic solution, first make a batch of strong, black tea that you steep overnight (do not add milk or sugar). With the tea at room temperature, add some household ammonia – the final mixture should be about 10 percent ammonia and 90 percent tea. (Use ammonia without added soap.)
The ammonia seems to help drive the tannins into the wood.
Once the mixture is applied, I follow that by going over all the surfaces with a heat gun. The heat gun raises the grain and speeds the process along. If you aren’t in a hurry, you can let the tea flash off on its own.
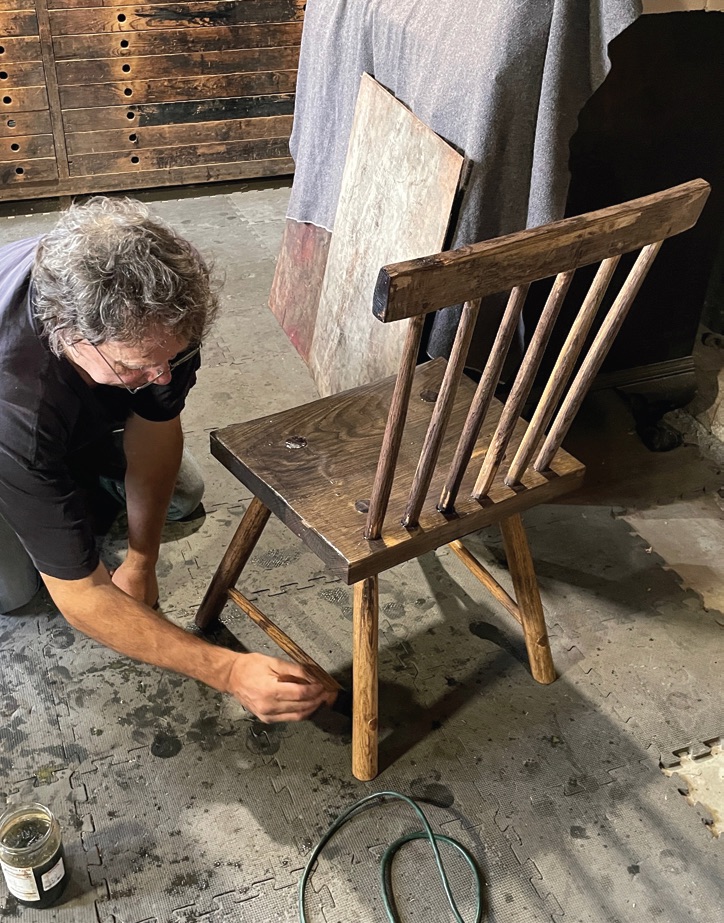
– or it is weak – use a stronger solution.
Now it’s time to add the color. The solution is made by dissolving a pad of oil-free steel wool in a jar of household white vinegar. I make mine in a large lidded jar. It usually takes three days to a week for the metal to dissolve. I also like to make batches in different strengths. You can make a stronger color by adding more steel wool to the solution.
I brush the solution on with a chip brush. If the wood does not quickly turn a brown/black, you should use a stronger solution. Set the chair aside and allow the solution to dry.