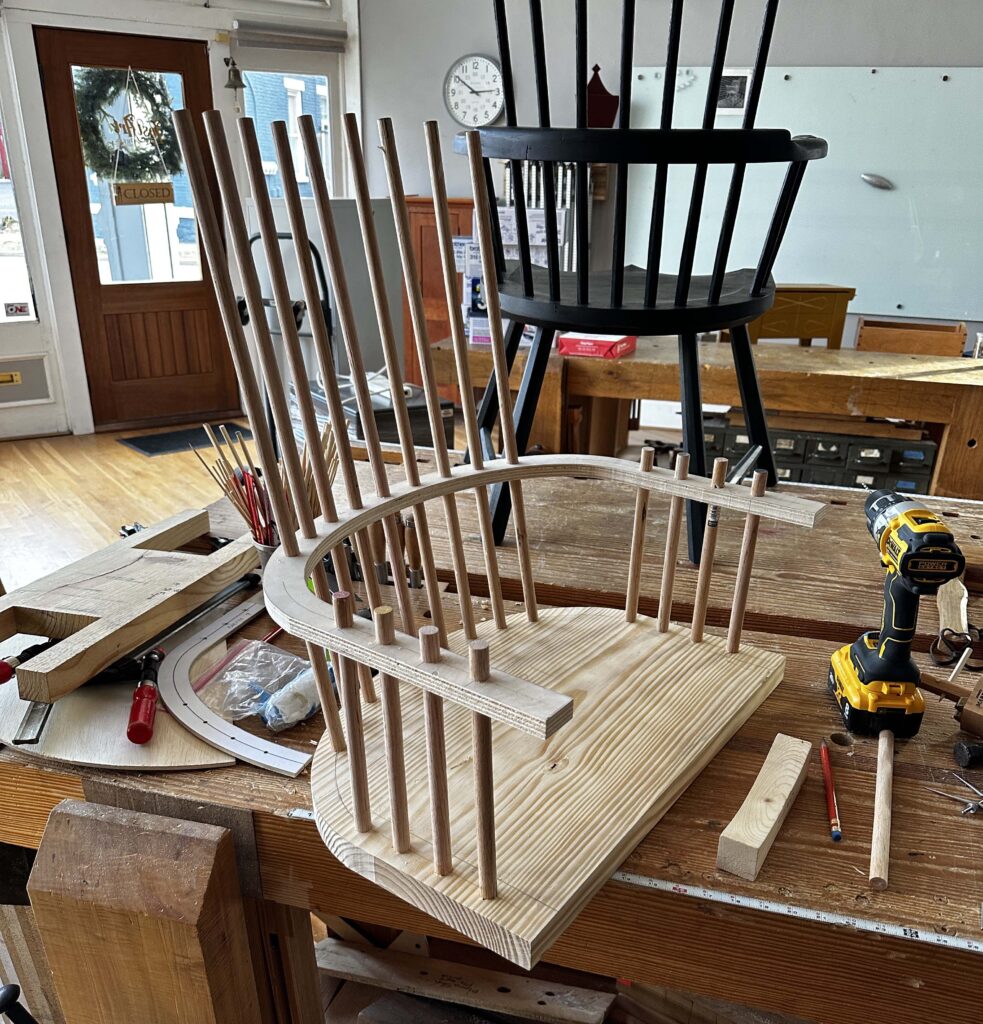
Update: Comments are now closed (we will answer any unanswered questions tonight or tomorrow). Thanks all!
If you have a woodworking question, now is your chance to ask it! Post it in the comments below between now and 5 p.m. Eastern and will do out best to answer everyone (in between working on chairs and a dovetailed blanket chest).
– Fitz
p.s. We’ll announce 2025 Open Wire dates soon…if you think we should keep doing it? NB: We’re thinking about charging for every question that has a word count of more than 50 😉
Good Morning.
I need to ream a hole on the underside of the armbow on a 7 stick chair. Does Chris apply any “English” to move the hole or just enlarge it. I was thinking of leaving the arm in place and mounting the reamer in a right angle short brace or ratchet handle to keep an eye on the upper hole and not making it into an oval. Any suggestions?
Thanks.
Les
I use a tapered reamer to open up holes. No Englishing. And yes, I keep my eye on the exit hole so the reamer doesn’t cut into the show surface.
If you shortened the workbench from the AWB to say 7’, would you shorten the distance between the legs to compensate or shorten the distance from the legs to the bench edge?
If removing only 1′ from the length, I’d probably shorten the base and leave the overhangs intact. More than 1′, I’d shift the base to keep the overhang intact on the end with the face vise.
Hi, Chris. I’m making a version of your Irish stick chair featured in Fine Woodworking and am looking for tips for positioning the arm over the seat for drilling. How far forward of the front of the seat should the arm be to establish the 25 degree back angle, and is the arm tangent to the front corner of the seat? Once the front is set, should the rear arm mortise just align vertically with the corresponding seat mortise as viewed from the front? Thanks.
Hi Jake,
Check out the Curved Arm Armchair in “The Stick Chair Book Revised Edition” (a free download). The chairs are VERY similar. Page 458 shows the arm in plan view with the seat and should answer your questions (I hope).
I am currently building a dining table of my own design. I am building the base in a timber frame design with large dovetails on each of the end assemblies out of southern yellow pine. There will be a stretcher out of walnut and the tabletop is walnut as well. I am going to paint pine part of the base black. I used 4×4’s for the legs and 2×8’s for the dovetailed boards in the base. I have seen this joint used in timber framed structures as well as a half dovetailed version in old log homes. How prevalent was this joint used in the past and was it ever used much in furniture?
It’s fairly common. I’ve seen it a lot in joining stretchers to legs in workbenches. And adding the top rail to a table (right under the top). The joint is then covered by the tabletop.
Can armless stick chairs be made just by omitting the arms off a regular stick chair or am I just over simplifying it?
Bibbings & Hensby have a couple. The comb is a bit unique, but I have built a few with a standard Windsor comb and omitted the larger diameter outside sticks as they did and they seem comfortable and strong. I have made them with a D shaped seat and a simplified shield seat. Both look nice.
In response to your question, please do keep doing Open Wire in 2025. The information is priceless. Maybe AI could help put together an index for it, even.
Terrific idea about autobuilding an index.
I’ve been slowly stocking up on southern yellow pine to build a workbench. Unfortunately my last trip to the local Home Depot (Cold Spring, KY) all the construction lumber was now fir. Are you seeing the same thing in other parts of greater Cincinnati?
Chris had the same experience (same Depot). Try Lowe’s in Highland Heights; they still have it.
Which sharpening tasks do you use you grinder for? Preferred grinding wheel? Thank you.
We use Norton 3X grinding wheels (#60 or #80). We use it to grind bevels, reshape bevels, repair chips and general workshop grinding chores.
We also have a Veritas sandpaper sharpening gizmo that I like for precision operations. But I wouldn’t call it essential to our work.
Chris/Fitz I am wondering your preferred method of creating raised panels. These were very common on furniture up until recently. I fear the machine shaper and router bit configurations that require easing into the wood and using a table. That’s how everyone in the magazines will make these. I purposely bought a beautiful Leon Robbins panel raiser plane for a cabinet project- excellent, as-new sharp blade, barely used. I could not tune the thing . Too thick a cut, or no cut at all. The plane just didnt seem to have mass enough to cut through the figured maple I was using. Really frustrated, I returned the plane, sadly, it was a work of art. I used a series of jack, shoulder and block planes to make the panels. Schwank will occasionally make a 750$ 10 inch 18th C style panel raiser, but it’s years of waiting for that. Philly Planes makes one to order (6 mos to a year). Im sure Matthew Bickford will make one one asks.Theres almost nothing in your Hayward reproduction books, maybe 1/2 a page showing one or two steps in Vol three.
How do you all do it? Or not at all? Maybe I was doing something incorrect with the Robbins plane, but they all look the same.
Thanks
M. weiss
The few times I’ve done it by hand, I’ve used a jack plane/block plane and smoother. In the Nov 2013 PopWood, there was a Bill Anderson article on making your own panel raiser, if that’s of interest. But I usually use the table saw (run the panel on edge/end with an angled blade) then a smooth pane to erase the table saw evidence.
I don’t use panel-raising planes. They are too much trouble for someone who needs them a few times a year. I kerf the field with a saw (sometimes a table saw). Remove most of the waste with a jack. Finish up to the field with a shoulder plane.
Sorry I’m help here. And that I am super basic.
Good morning – I used your wax recipe for my Gibson chair about year ago and now almost done with a stick chair. The wax is not like peanut butter but very hard. Do you think that I should reheat it and add some more citrus – maybe another two tablespoons?
I’ve had the same experience. I was going to double up on the next run.
We’ve recently started adding more of the solvent. In the video from this week (https://blog.lostartpress.com/2024/12/11/how-we-make-our-soft-wax/), it appears 3 TBSP to a quart
Kale cut that shot short. I now use 4 tbs. of citrus solvent. Yes, you can reheat and add solvent.
What’s the final word on using linseed oil paint? Thin, don’t thin. Sun light or not. Oil first, ??
We don’t have a final word…still working with it. Sorry.
I built the Nicholson bench (Naked Woodworker) a few years ago. It works great, so do your holdfasts, and I am thinking of adding a leg vise (Benchcrafted). I’ve started looking at the dimensions of the legs and top of the Nicholson and trying to figure out how to satisfy the leg vise requirements (Thickness, length, etc.) Has anyone done this and is there a path to success and/or is this trickier than it looks ?
Advice appreciated
Thanks
I don’t foresee any problems adding a Benchcrafted vise to a Nicholson. You might have to thicken the leg. You might not. It should be a straightforward job.
Southern yellow pine in a regional wood for availability. I’m just a few states away in MN, and it is not found anywhere other than in the pressure treated preservative form. And I wouldn’t want a bench made from chemically treated lumber. SPF (mixed species spruce/pine/fir) is our prevailing lumber, followed by hem fir (hemlock), and if the lumber gods are kind, every once in a sporatic blue moon some douglas fir shows up. I built a bench in early covid-times (2×4 top, boards standing on edge) from a bundle of douglas fir that showed up, a lucky find. They’ll all work just fine.
Forget Minnesota. I can’t find it even in central and northwestern Indiana. I do not know whether it’s a ‘not enough supply’ issue or it just starts getting more expensive to transport it beyond the deep south.
For you hole-poking chair builders in the room, I came across this drill mfr. a few weeks ago. I’ve been waiting for this Open Wire session to pass it on. I have no affiliation. Maybe LAP staff or other readers have experience with them to share? WL Fuller, in Rhode Island, a 3rd and 4th gen. family business. Augers, forstners, spades, twists, brads, etc.
https://www.wlfuller.com/
I vote to keep Open Wire, but I respect the time suck it causes you. Thank you for your efforts.
Fuller does some awesome work. Love them.
For the 1/2″ woodslicers, do you find that you need to adjust the angle of the fence when they’re brand new to get straight rip cuts, or they will cut without drifting with the fence set perpendicular to the blade? And as they dull do you periodically have to change the fence angle, or you leave it set up how it was when you first installed the blade?
As far as I know, we put them on, they cut, and that’s that. There is a little drift if I move to quickly – but I wouldn’t expect a finish cut off a band saw. I saw just proud of the line and plane it straight/flat.
I find that each blade has a little different drift. I change the fence after changing the blade. It’s slight, but it’s real.
I hope you can keep doing this.
On a more direct topic, recommendation(2) for a specific chamfering cutter? There are way too many on Amazon. Prefer to buy locally but the nearest woodworking tool stores are at least 50 miles from me here in Northern New Mexico. Thanks.
P.S. I’m not above open bribery to get into the stool build class next year…;^)
We both (most often) use a block plane to cut chamfers, freehand. Years ago, I used this fence: https://www.leevalley.com/en-us/shop/tools/hand-tools/planes/maintenance-and-accessories/46296-veritas-chamfer-guide?item=05P2210
But it really doesn’t take long to get good at eyeballing a good 45° bevel.
I came across an old video on the YouTubes where Mr. Schwarz describes reference faces and show faces and classes of cuts.
Can you recommend one of your books that explains or teaches woodworking at this (pseudo-beginner?) level?
Robert Wearing’s “The Essential Woodworker.”
https://lostartpress.com/products/the-essential-woodworker?srsltid=AfmBOoq0FTTQ8kiS4fqT8vXPZypi1t7PCpfbHabqVK5q6UASpTlD5Awa
Yes that is a side chair
Keep this up as long as it pleases you.
The right edge of your blog page used to include your Instagram pics. What happened?
Instagram occasionally disconnects the feed. And I have been unable to reconnected all week.
Hi,
I am embarking on my first stick chair with the help of the book and video to help me along. It turns out I have enough wood for 2 chairs. I plan on making one chair just like the video and one chair with 4 long sticks instead of 6. I have 2 questions:
I don’t have a tapered reamer or tenon maker. I have the straight 1in tenon cutter for the leg tenons. Should I cut my tenons on the legs before or after tapering?
For the 4 long stick chair, is there anything wrong with using the same stick positions on the 6 stick chair form, just omitting the 2 outer long sticks or should I space the 4 out wider?
Thanks!
Corey
Hi Cory,
It is easiest to cut the tenons AFTER you have tapered the legs.
For a four-stick chair, you can use the spacing for the six-stick chair. Check out the spacing I used for the four-stick armchair in “The Anarchist’s Design Book,” which is a free download.
Any chance of an ATC video one day? I know there have been various tweaks in the design since the book came out, and I’d love to see them demonstrated. The dream is to come down for a class one day, but a video would be the next best thing.
Thanks!
FWIW, I have a “traveling ATC” video – on it w/the Wood Whisperer. On it, I use the same methods we now teach for the full-size version. https://thewoodwhispererguild.com/product/traveling-anarchists-tool-chest/
I did the full-on ATC for Popular Woodworking years ago.
https://videos.popularwoodworking.com/courses/make-a-traditional-english-tool-chest-with-christopher-schwarz
If I could ask a couple of questions:
For many ADB projects, is it ok to switch from cylindrical to tapered tenons? I do not have a lathe, but do have the 5/8″ tapered reamer and tenon cutter set from Veritas.
Do you have instructions in one of your books for building a cradle for shaving leg octagons?
The Stick Chair book (revised edition at least) has instructions for a jig to cut octagons at the bandsaw. If you’re looking for hand tool-only, Ingenious Mechanicks has some clever work holding solutions.
“The Stick Chair Book” has plans for a cradle to octagonalize square stock. Or you can clamp it in a face vise (corner to corner). Or a carver’s vise. And skip the jig, which is what I do.
Might be too deep a topic, but do you carry liability insurance on the chairs you sell?
In a sue happy world, I’m scared to sell my work because of it.
I think it’s called the Lump Hammer policy. $137 for lifetime coverage 😜
I do not. I have an umbrella policy for me and my business, which probably would cover issues such as that. But I really refuse to let insurance dictate whether I can eat or not.
Is red Oak a bad idea for any kind of tool storage?
At $ 3.50 a board foot hard to resist.
I can’t see why red oak would have any demerits for storing tools. Other than it being heavy.
Have you used the Real Milk Paint Co. milk paint? Any tips on application and would you recommend it?
Yep. It’s the one I use most often. But I don’t apply it “right” – I like to mix it thick, let it slake for at least a few hours…then I don’t strain it, ’cause I like the streaky bits that are left by the tiny powder clumps. I apply it with a chip brush, usually three coats. But I’d recommend Peter Galbert’s Vimeo video on using milk paint if you want to know a “good” method. https://www.petergalbert.com/blog/2020/4/9/new-milk-paint-video
😄 excellent, thanks.
The Stick Chair book (revised edition at least) has instructions for a jig to cut octagons at the bandsaw. If you’re looking for hand tool-only, Ingenious Mechanicks has some clever work holding solutions.
How does one go about flattening a large panel glue up (as in a table top) that is larger than your workbench surface?
I’ve done this recently building a Dutch pull-out. Scooted the bench away from the wall, put the whole top on the bench, secured with holdfasts, then worked in sections a la the benchtop flattening instructions in AWB (free download). Used a jack, smoother, and scraper. Move the top and holdfasts as needed. Sharp solves everything.
Any idea when you will announce dates for summer classes?
I’m trying to arrange my summer teaching schedule around a potential LAP class.
The ones through June are already announced: https://www.tickettailor.com/events/covingtonmechanicals
July through Dec will be announced in early Feb.
Hi. Have you used a Kanaban to lap the backs of chisels and plane irons? Does it work? Does it take a lot of time to get a mirror polish?
Thanks Tom
In setting up my smoothing plane I have the chip breaker just ever so far back from the cutting edge (Maybe 1/32″?)
It seem doing this makes it very hard to push. It’s as sharp as I can get it.
Is this normal? Am I doing something wrong with the setup? How do you set the chipbreaker on your no 3?
When you set the breaker close (I set it even closer than 1/32″), the resistance increases. To counteract it, I use a light cut, I skew the tool and I oil the sole.
Also, I use that chipbreaer configuration only when dealing with difficult wood.
Short Question: Can I plan to use a hand plane to clean up the hardened squeeze-out from urea-formaldehyde glue? I know that the airborne dust from sanding would be unhealthy.
Background: I’m planning my first steam-bent, laminated top cap for what is essentially a curved pony wall. It’s oak; finished to five inches wide by 3/4 thick by twelve feet long (around circumference). Yes, I’m bending it in the hard (impossible) dimension. The final shape is the long half of an ellipse. The tightest inside radius of curvature is about eight inches (at both ends). The middle is barely curved. I am about to start experimenting with shorter, 1/4 wide strips bent around the tightest radius of the form. It’ll take twenty, 1/4 inch strips to make the cap five inches wide. My finishing steps are to blacken with India Ink, seal with clear shellac, then topcoat with clear matte poly. Do I need UF glue for this lamination, or should I use Titebond III? Is it easier (or required) that I tint either glue? Can I tint either glue with universal black dye (Mixol or TransTint)?
Thanks so much for any advice!
You can, but I’d try scraping it off first. Hardened glue can do a number on a plane blade. (FWIW, my weapon of choice for this would be https://benchcrafted.com/products/skraper)
The resin glue is murder on tools. I usually use carbide tools to get the big chunks off. Then finish with a scraper. In general, I don’t use PVA for bent-laminations because it has too much creep. I’ve used plastic resin glue or hide glue (300 bloom), which sets up as hard as glass. And is easier on your tools.
I’m afraid I have no experience tinting glues. Usually hide glue is more transparent to finishes. But I can’t say for sure in this application.
I came across this https://www.homedepot.com/p/1-3-4-in-x-1-3-4-in-X-36-in-Wood-Square-Dowel-HDW8322U/203378795 at my local big box store. Possible leg material for the B.S. chair? The web site says pine but it doesn’t look like pine in person. Maybe poplar?
Bummer. I was able to get it at the local Home Depot (Cedar Rapids, IA) a few months ago to build a shaving horse, but I haven’t looked recently. It’s a bit like trying to find white oak here; most places have red oak.
Hi, Chris, Megan, and all the LAP team,
Three things today:
1. I looked up your new digs online and found both exterior and interior photos. Really cool building inside and out! Versatile space, too — formerly both an office space and a restaurant, apparently. I hope it works well for you.
2. There’s a Craigslist offering in the Los Angeles area for an Anarchist Workbench-style workbench, finished and ready to use, for $15,000! Made from ipe, padauk, ziricote, mahogany, maple, and red oak. Photos available at https://orangecounty.craigslist.org/tls/d/costa-mesa-custom-woodworking-bench/7805063802.html. This belongs in an art gallery, not a workshop. The seller clearly didn’t heed your advice to use the cheapest wood per pound that he could find.
3. Now a real question: do y’all have any experience with and/or opinions about the wood screw wagon vice kit made by Bryan Furnishings. It’s for sale on Etsy for $169, and looks like it’s good quality. (https://www.etsy.com/listing/1205594438/wood-vise-kit-wood-vise-screw-wooden?gpla=1&gao=1&). A less costly alternative to the Lake Erie vice, if the quality is good. Comments?
Sorry but I’ve never heard of the seller. But it looks like a good piece of equipment. A double-lead screw is always a good thing. The 2″ seems a little small to me, but I’m used the huge screw on my oak ROubo.
Question for Fitz…
Reading your DTC book and enjoying it. Just read the section on the fall front and see you recommend rabbeting the long grain first. That’s opposite of what I’ve always seen recommended. Why for you do it that way?
Because that’s how I was taught. And it makes sense to me…you’re basically removing the material that would blow out as you work across the grain. But I know lots of people who do it your way. Both work.
There’s a chance for disaster using both methods.
I should have been clearer. I was referring to a drill mounted chamfering tool as described by Chris to chamfer and round off chair legs etc.
Oh – that one. https://blog.lostartpress.com/2022/02/24/chairmaking-on-the-cheaper-part-1/
Megan, how do you like your new benchcrafted bench?
I won’t have the new one for at least a month still. I will certainly report on it once I’ve used it!
What is your favorite method of mixing? I’m using the marble in the can and shake method recommended by Real Milk Paint Co. Sort of works
Same.
We use the magnetic mixer for milk paint when possible.
I was complaining to my neighbor how much of a pain mixing milk paint is and he suggested one of those kitchen imersion blenders. I got one on Amazon for $25 and it works really well. Just cover top with a rag.
Is the W stick configuration on a Gibson chair necessary or decorative? The Irish curved back seems very similar and does not have a W.
After building a dozen of each style (at least), I think the W adds to the rigidity of the back. The whole thing really locks up tight at assembly. The parallel sticks work fine, too. They just aren’t as strong.
Triangles can’t wrack like rectangles do. The angles give the stability of triangles. Very sturdy chairs for my very heaviest clients.
Good Afternoon,
I am about to complete an ADB Drinking Table in cherry and would love to get your idea on a finish. It will likely be a workhorse table in its future home including, yes, cards and drinking.
Thanks.
Soft wax, reapplied as needed. (It’s what’s on the cherry dining table in Chris’s house. And I wish it’s what was on mine.)
Oh this is perfect. Thanks Megan!
Kanaban works well and you’ll have a mirror polished surface. Be careful not to allow blade to rock as you work – easy to make surface convex. Check Odashi or Dale Brotherton’s excellent book “Sharpening and the Japanese Handplane”
Central Illinois, here. Within 10 miles of my house, there are 2 Menards, 2 Lowe’s, and a Home Depot. Anything bigger than 2x4s (so 2×6 and up) at each store is SYP. Just a data point. I’ve built several benches from it and have no complaints.
What is the angle of choice for the dovetail part the Roubo through leg joint? Do you choose by design or function?
Thanks Chris.
Hello, I’ve been using oilstones for sharpening recently and find that bits of cloth fiber are left stubbornly stuck all over the surface after wiping them off. Is this an indication I should be doing something differently, or am I just being fussy? Thanks!
Maybe try a rag with less lint – like a huck-weave towel (sold as surgical towels). Linty cotton cloth will stick to oilstones like mad.
I haven’t seen the PopWood one to compare, but Megan’s video with TWW is excellent.
Thanks for the reply and taking the time to answer questions.
The books are amazing, but sometimes you’ll have questions no matter how many times you read it. Definitely continue the open wires if they aren’t too much a burden.
If use both diamond stones and water stones should I be careful about using my LN honing guide on both, or just wipe it down inbetween?
It’s always good practice to wipe off the wheel and edge when switching grits. I don’t know if honing guides are bad for diamond stones or not. It’s easy to blame a diamond stone’s failings on things that don’t cause the real problem – which is that diamond stones wear out faster than most people think.
I think at one point your jointer plane was a 7, now it’s an 8.
Have you seen any difference in your work with the extra 2 inches of length?
It’s not the length, it’s the mass. The extra weight of the No. 8 keeps it in the cut during heavy cuts. It also helps settle the plane on an edge.
But it’s personal preference – not any real advantage. My joints are just as good as they were with a No. 7. I just like the No. 8 more.
Thanks.
Hello Folks,
I made a 1/2 batch of gelatin glue using the latest recipe from one of your blogs!
I think I did everything right… But even after being in clamps for 24 hours the hour hasn’t cured… I know a bit more salt will allow more open time…
Is there anything a guy can do to a batch that will shorten curing time?
When animal glue won’t cure, I have found that it has been abused in some way – either it’s really old gelatin/pearls. Or the glue was overheated at some point.
The other explanation we have is that there might be a lot of moisture in the wood that is keeping the glue from drying. This happens in deep mortises in wettish wood.
You can take the assembly apart by applying some boiling water to the joints. Or you can put it in a very warm room for a week and see if it dries out.
Natural products, like glue, can have natural problems such as this.
I know the answer is you never have enough, but what would you consider the minimum amount of clamps to glue up the top for the anarchist workbench?
I used about a dozen K-bodies plus four iron panel clamps (Hargraves/Cincinnati Tool/Long Island Tool/Hartford Clamp). That will probably handle all the glue ups.
I have some white oak I am thinking about using for a stick chair. I’ve never made a stick chair before. Would this material be suitable for a beginner? Or should I mix it with other species? Like get something lighter for the seat?
I’m not a beginner, but I try to avoid white oak for seats and arms. All the oaks/ashes/hickories split so easily that they can be trying for even an expert to use in a seat.
White oak is incredible material for the legs, stretchers and sticks. For the seat, arms and comb, get something easier to carve and less likely to split: soft maple, tulip poplar, sycamore, elm.
Hi all!
I recently had to take down a plum tree. It’s only about 10″ at its thickest and not very straight. I want to make the most from the wood. Aside from aesthetics, is there a difference between the sapwood and heartwood? Are the branches useful for anything outside of a smoke pit?
I don’t know anything about plum. But in general, the branches are good for spoons and hooks and the like. Not for furniture. Branches have reaction wood and compression wood.
As to the heartwood/sapwood… I’d check the internet. No clue.
Just a few days ago I watched a YouTube vid of a guy who carved a spoon from a bent piece of plum wood. From selecting and cutting the limbs to final product. Search “Plum Eating Spoon” if interested.
Tell us about the India ink finish on that chair, I really like the look. Thanks
It’s two coats of alcohol-based, waterproof India ink from Blick.
https://www.dickblick.com/products/blick-black-cat-waterproof-india-ink/
I applied it with a rag. I applied the second coat about 30 minutes after the first. Then let it dry out (probably not necessary). Then a coat of soft wax applied with a 3M gray pad and buffed with a huck towel.
I did this and it is great. My only caution would be that if you are using the Retro crisscross, the instructions recommend a tap for the bolts. This isn’t great for softwoods. I did it and had to do repair later. There is advice in AWB on how to attach it to a softwood bench with woodscrews instead.
Delving into the philosophical- if you so choose- Do you think that beautiful design is objective?
To a degree, yes. But I don’t believe in free will, so I was probably forced to say that.
Have you ever tried using poplar for a chair seat? Wondering how it would work.
Tulip poplar is a great choice for seats. Carves well and resists splitting compared to ring porous species.
Awesome, thank you!
Thanks Chris and Megan, not sure how I missed the pop wood one! Appreciate your time.
Just received Megan’s DTC book. Love it. One question: I’d like to make a larger stationary version, say 16″ deep, and I’m thinking of using poplar (because I’m in Texas and you should see the crappy big box wood here). Do you hear of people regretting their choice to go larger and heavier?
Only if you’re planning on moving it. If it’s a stationary chest in your shop, no problem with a larger size.
Afternoon Chris and Megan,
For the Becksvoort’s 15 drawer cabinet I am going to sand it. First project I’ve ever sanded in the 9 years I’ve been woodworking as normal finish with a hand plane. Will be using a random orbital sander increasing in progressive grits up to at least what Becksvoort recommends for sanding cherry. Is it only the last grit you would sand by hand so the “scratch marks” line up with the grain rather the ROS swirls?
Thanks,
Joe
Well said
I’ve been enjoying making stools and other staked furniture based on your designs. I bought a reamer, but don’t love using it. Could I get by with just a couple rounding planes and use round tenons on everything? If so, what two sizes do you think would be the most advantageous? Thanks for your time and all the pictures of staked furniture you’ve posted over the years to give me some inspiration.
Cylindrical tenons have worked great for many centuries. I use 1″ tenons for the legs and 5/8″ tenons for everything else.
I used saw benches and later the almost-finished table base. I put shelf liner between the table top and the saw benches to keep it from sliding around. Worked great.
Edge joining with a machine is a lot harder for me than using hand plane.
Any trips for using a power jointer? Otherwise mine is not very useful to me.
A while back you mentioned pulling boards up on the thickness planer to help with snipe. Thanks for that tip.
Electric jointers, like band saws, require setup and finesse.Make sure the tables are co-planar. And that the outfeed table is in line with TDC of the cutterhead.
Technique is very important. Most people just mash down on the work and push it across. And the work ends up bowed or worse.
When face-jointing, keep the board under control on the infeed table and do not let it rock. On the outfeed table, provide good pressure, but not enough to distort/bend the work or rock a high corner against the table. If you are putting your weight down on the board, you are doing it wrong.
Edge jointing is different. LOTS of pressure pushing the work against the fence. But almost no pressure downward. Downward pressure creates a taper cut (and not in a good way). Inconsistent downward pressure makes a bellied edge. You are trying to skim the edge over the cutterhead and onto the outfeed table. Downward pressure is the enemy.
Do you know of a listing of “stick chair” like articles in magazines? I stumbled across Drew’s article on the hearth chair after Chris’s substack post…
2nd question-Do you know if anyone using technique like spoon carving where branch and trunk are used to get grain running at close to 90 degrees to be used for chair arms?
I’m afraid no. There hasn’t been a lot published about these chairs. Hence, my efforts.
On your second question, natural crooks and bends are an integral part of the tradition. Many Welsh and Scandinavian chairs used these branches for the arms. Jogge Sundqvist has written about this in both of his books.