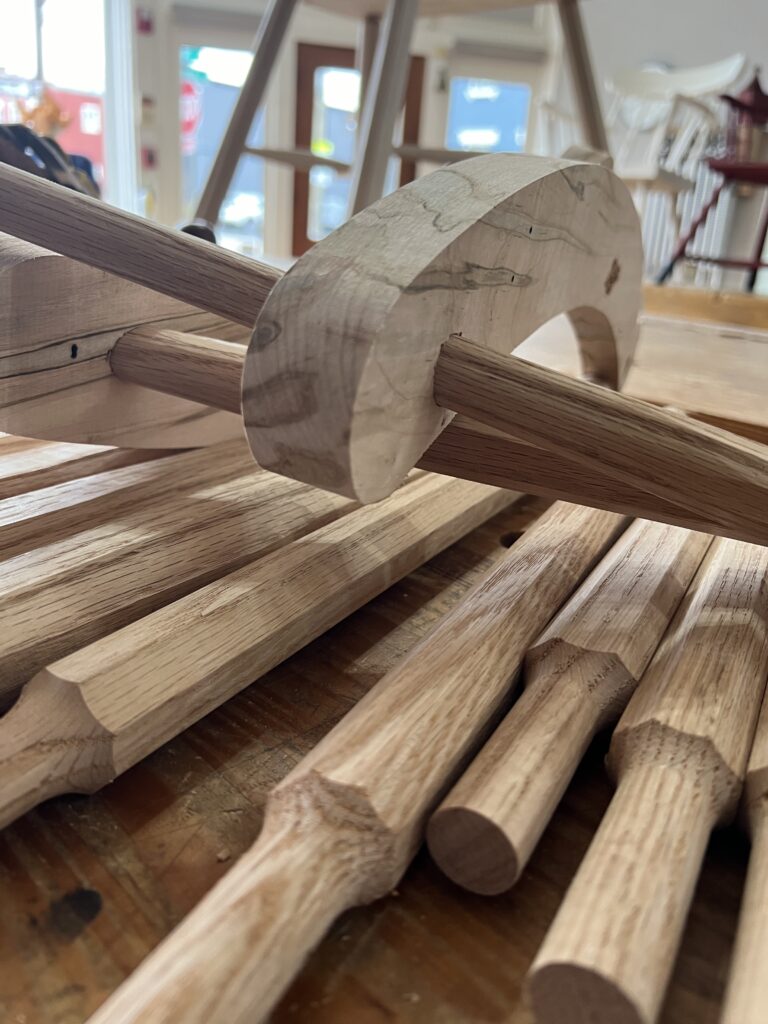
Update: Comments are now closed. Join us again on Dec. 14.
If you have a woodworking question, post it in the comments below. Chris and I are holding Open Wire today between now and 5 p.m. Eastern and will do out best to answer everyone (in between finishing a chair and a tool chest – guess who’s doing which…).
– Fitz
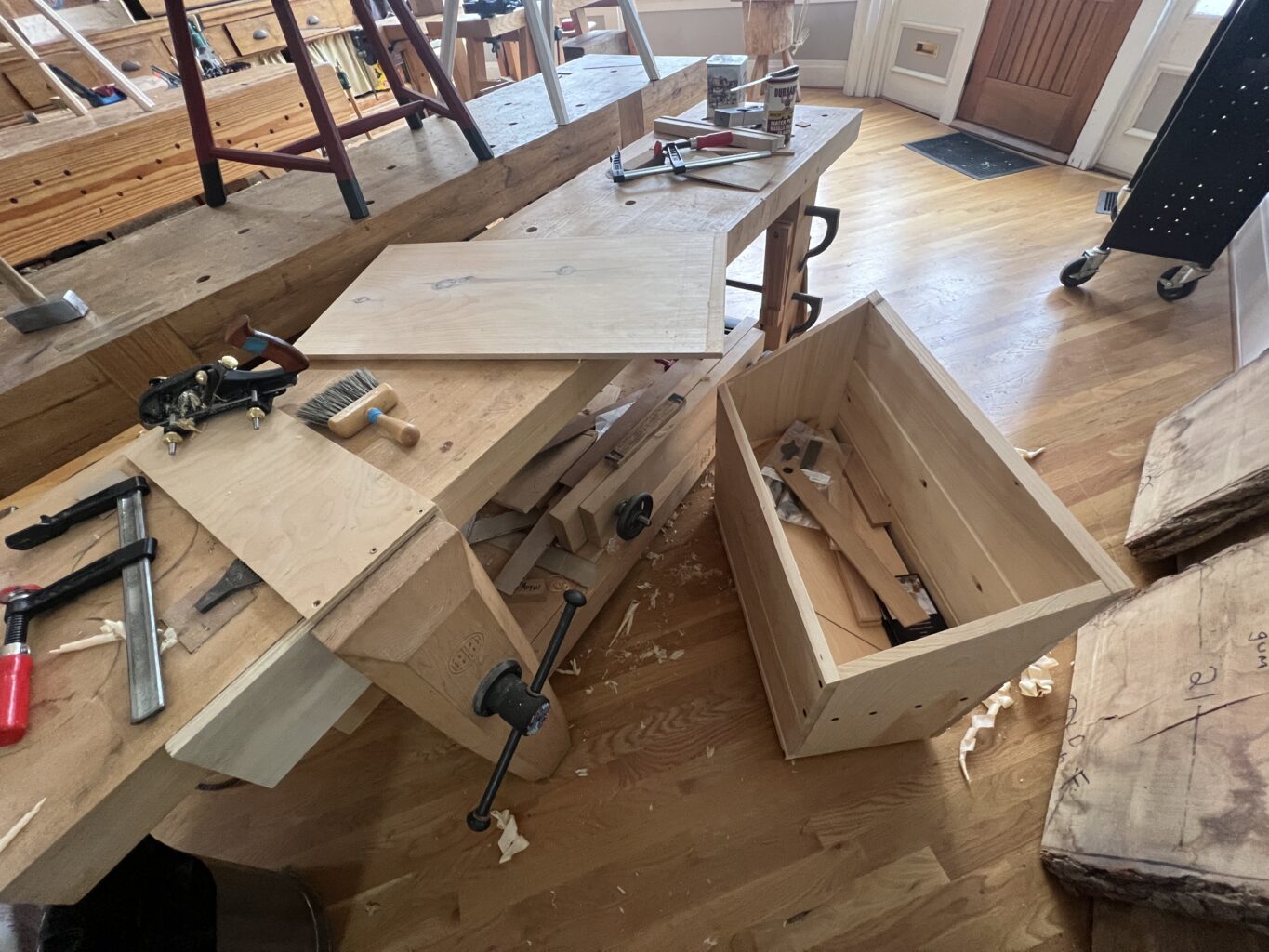
Good Morning, the Christmas light and decorations are beginning to be on display, when will the Annual Tool Gift Buyers guide arrive?
I KNEW there was something I was forgetting to do….
I need to get on that.
I have a good jointer and planer. I know pretty much nothing about maintenance of machines. Any suggestions for a book (or a source) on how to take care of these things ?
Thanks
I read the machine manuals closely and follow their advice on lubrication and alignment. Most of the machines had a dedicated book about the machine that can help with the fine tuning, especially with table saws, band saws and lathes. Jointers and planers are pretty simple machines, and the manual has always been enough to keep ours in good shape.
In your sharpening videos you mention you do not rate the Shapton Ceramic Glass stones as highly as the Shapton Pro stones. Please could you elaborate. Alas the required beers will have to wait for you next trip to the UK.
I do not receive the blog emails as I once did, but I do receive the American Peasant. Is it me?
The glass stones are too thin for the $ – you will use up a 1,000-grit stone in less than a year. (Or at least I would.) Plus, you have to turn them over to see which is what grit – but that’s a minor annoyance.
I don’t see another place on your site to say it, so I say it here. Thanks for putting together the Gibson chair video. I’ve been using it to build a couple, and, as always, your terrific instructions are simple to follow. (I used your Roorkhee chair video to make a couple of those years ago and felt the same way.) My question is about stick chair paint. You use different kinds and brands. If you remove curing time from the equation, what is your favored paint these days for stick chairs? And, again, thanks for the video. Well worth the price.
I love linseed oil paint and would use it on everything if I had the time. It is so humane and beautiful. And it wears amazingly.
But the long cure time makes it difficult for us to use.
Will the Anthe building be open during the open house?
Probably not – we’re getting some floor work done so we can move the editorial offices there, and it will be underway.
Good Morning. I am wondering if you still recommend fortification of chair seats with pegged loose tenons at glue up. I know the recommendation was in The Stick Chair Book, but have not seen it mentioned much lately. Thanks for the wonderful information and products LAP provides!
I add loose tenons (pegged) whenever possible. Modern glues are probably strong enough. But who doesn’t like overkill?
Forgive me, I’m still very new to woodworking, but I’ve got a new-to-me vintage Stanley No 5 Type 11 jack plane with the original iron, chip breaker and cap iron. Everything appears to be in very good shape, and I’m setting this up for the first time. This is my first hand plane. I’m wondering in about the mouth opening and the positioning of the frog. When I set the plane up, I have the frog aligned so that the slope of the frog is aligned right on the edge of the mouth such that the slope down the frog and out the mouth is a single coplanar slope. Is this the right way to do it? It seems the mouth is quite closed up when I do it this way, meaning there’s not much of a gap between the exposed edge of the iron and the front of the mouth, and while I’m able to get shavings, they are fairly fine, and I’d like to be able to take some bigger bites. When I back the frog up away from the edge of the mouth, I have trouble getting the edge of the iron to come out of the mouth sufficiently to make a cut. I’ve tried backing the frog maybe an 1/8”. I feel I must be doing something wrong. Any advice? Thank you.
Chris has a great series on jack plane setup – here’s the one that talks about the frog position (but in short, he recommends positioning the frog so it is in the same plane as the back edge of the plane’s mouth).
https://blog.lostartpress.com/2019/11/10/clean-true-critical-surfaces-of-a-jack-plane-part-2/
I am having a very bad time using the tapered tenon cutter. Is there a special trick? I have sharpened it, and set it in place against the tapered mortise reamer so that they are in alignment, but it only cuts halfway down and then stops.
It sounds like the blade needs to be rotated counter clockwise in the body of the tool a bit. Use the little cast-in marks on the tool’s body to guide the process.
It’s hard to say without holding the tool in my hand, but this is my best guess.
Good morning! I’m currently working on the AWB and I’m facing a bit of a challenge. My shop floor is made of concrete and has a few cracks and is a bit uneven. I’m looking for some advice on how to make sure the work surface is level. I’ve heard about using shims, attaching the table to a wall, using adjustable feet, and even cutting the legs to different lengths to make it level in a specific spot. But I’m not sure which of these options is the best one, and I’m worried about any potential drawbacks. Any suggestions would be greatly appreciated!
Our shop floor is uneven, and we use shims. It’s the cheapest and easiest solution (and you can ad and take away shims as needed if you move the bench)
Are there any plans to bring Peter Follansbee back next year for another carving class? I am bummed that I missed the one this year.
If he wants to visit, we’d be delighted to have him.
Just to put my mind at ease, can you confirm that page 73 of Kitchen Think, third printing is intended to be blank? It’s just jarring coming upon that expanse of white in the middle of that beautifully printed book, and it’s the only blank page in the body of the book, and the only blank right-facing page so it sticks out like a sore thumb and I can’t help but think “is something supposed to be there?” and it’s bugging me.
Thanks!
That is correct. The chapter ended on the left-hand page, and every chapter opener is on a left-hand page – hence the blank RHP in between in this case.
Thank you…my mind is now at ease.
Good morning, Chris and Megan! I recently received an old Stanley miter box, but the saw could use some TLC. I remember seeing someone mentioned on the blog who restores saws. Do you recall who it was, or can you recommend someone reliable?
Yep! Matt Cianci: https://thesawwright.com/
and Mark Harrell: https://www.sawsharp.com/
Good morning gurus of the ATC!
I am writing this morning for advice on what to do, if anything, about the 1/4” gap between the underside of the lid and the top of the carcass/dust seal at the back of my tool chest build.
Will it let any significant amount of dust in if I am using power tools (bandsaw) in my small shop?
To fix it, would you shave the top of the upper skirt, or the bottom of the edge/skirt of the lid?
I took a class with the illustrious Ms. Fitzpatrick last June (thank you for teaching!) and really want to attach the lid, but have been letting myself get hung up on this question.
Thank you for any help/advice/anecdotes you might share and hoping you are having a great weekend!
~Carrie
Hi Carrie! I don’t know about illustrious, but thank you. Looking from the back, can you see if the underside of the lid is hitting the lip on the chest? If not, you can plane the dust seal down a bit for a tighter fit/less gap. I usually have about an 1/8″ gap (and because the back is against the wall, I don’t have much trouble w/dust getting in),
Awesome! The underside of the front does not touch the lip so I will plane away. 🙂 Thank you!
Hey guys. Megan congrats on the new book. Lee valley has received my request….they’re pretty good with that.
Newbie questions
Can you talk about edge finishing and how and when you decide to leave them sharp vs round over and how much, vs a chamfer. I like the look of a clean sharp edge, but it’s not durable. Do I just break it or …
and do you keep that same edge treatment throughout the piece.
ie tops and legs.
Proportion.
In design stage, do you build models etc. how do decide that a leg thickness will balance and not look too heavy vs the top or seat.
For a visual example
Lie Nielsen workbench has a 4” thick top and 3” legs whereas Megan’s Benchcrafted has. 3” top and thicker legs
The lie Nielsen looks light and airy and the bench crafted looks chunky and heavy, even though they do the same thing.
When in the design process are proportion decisions made and do you revisit them or change them during a build.
Lastly
Any tips for getting over being paralyzed by perfection.
Example: if I chamfer this edge with my block plane, it won’t be consistent along its length because I’ve only done it 5 times… so I’m tempted to leave it sharp or sand it (which is more forgiving but a crutch) than take a chance and ruin it. Again.
Help.
Thanks
Best
Shawn Austin
Extremely new to woodworking but an old Wilco fan 🙂
Hi Shawn,
On edge treatments: It depends on the style of the piece of furniture and its function. All edges need to be “broken” to be friendly to fingers. Rounded profiles are style-dependent, or necessary for comfort. Look closely at museum pieces and you’ll get the hang of it.
On design: Drawing your pieces to scale is absolutely necessary at first. I rarely make models, unless there is some tricky geometry involved. For more on proportioning, see our books by Jim Tolpin and Geo. Walker. Proportions (simple ones) are literally the thesis of their work.
On paralyzation: Everyone has X number of crappy dovetails, chamfers, tenons, chairs in their hands. The only way to get them out is to make the thing. There is no other path through the woods. Do it on scrap. Or on projects for the shop. But you have to do it.
Good morning Chris and Megan!
Thanks for doing this! It is very generous of you. I know I saw something written about this but can’t find it. I need to make a six stick comb back chair that is 2 or 3″ wider than the plans in the book. Do you have a suggestion for how to accommodate changes in the width with the layout for the arms and sticks in the back?
Thank you!
Josh
Quick fix: I’d add a flat section to the arm between the two curves to make the arm match the seat. Then I’d lay out the sticks from scratch, using putty and bamboo skewers to visualize the layout.
Another great solution is to use this free tool to help you visualize the changes.
https://layout.computer/stick-chairs/
Can’t say enough good things about it.
Any chance of buying a replacement Exeter hammer handle?
Did you break it already?
Hi Chris, Megan!
One of my brothers has repaired an old oak dining room table and added some new leaves. Everything is sanded down to 220, but there are significant differences in how the old and new boards are taking stain (e.g., dark walnut stain or something more “traditional” in appearance), which is to be expected. The boards are a mix of rift and quartersawn, but it seems to be more of an old vs. new issue; or perhaps just normal differences in grain porosity between whatever was the source of the old boards vs. the new ones. Is just a matter of doing test boards with different stain mixtures, or is there some kind of product or other approach (raising grain?) that could help?
Thanks!
Brian
Correction, none of the wood is quartersawn; it’s all rift/flat
There are lots of reasons why the boards are coming out different colors. Too many to list.
My solution has always been to use aerosol toner to correct color differences. I use Mohawk, but there are lots of other brands out there.
https://www.mohawkproducts.com/Toners-s/1174.htm
These go on between layers of the topcoat finish (or on top).
If the color difference is radical, I’d look for a refinisher in your area. Their whole job is to match colors.
I’d like to try out my first chair (made some other staked furniture). Want it to be an armless desk chair for computer use. I like the looks of the “Staked Chair” from Anarchist Design Book (chapter 17). For this chair what angle are the long sticks/spindles for the back rest? Couldn’t find it in the book, but may have missed it. Thanks!
They’re 10° (page 263). Identical to the three-legged one.
Good morning. If you were building the comb back with bent arm bow stick chair for a dining room table, would you make any changes to your plan in the stick chair book? Should the seat or back angle be more upright?
Thanks for doing these q&a sessions!
As shown in the book, that chair is designed for dining and keyboarding. The arm is too skinny to tolerate much lean.
Hope this helps.
Hi guys!
Two questions, if I may:
For the LAP books that are only available as a physical copy, are you planning to make them available as PDFs as well? It would be appreciated, as I’m not in the US.
I got the book (that is to say the PDF) on door and window making and it’s a really useful book! It also made me realise that the English/US tradidtion has a completely different approach compared to the European continent where I am. In the former tradition, the edges of the door are square and close flush with the frame. To stop it over-swinging, a stop is nailed to the jamb (or a rabbet is cut into the frame).
In Europe, the door has a rabbet going all around it and when closed sits proud of the frame (which may or may not also have a rabbet for the door itself).
I don’t know if you have any experience or thoughts on the advantages of each, I would be happy to hear your thoughts.
Thanks!
If they are available only as physical books, it’s because for one reason or another, we cannot offer it via PDF. (And I’m afraid I don’t have enough window experience to comment on the differences.)
Just to add a little more here. When we don’t offer pdfs, it’s almost always because we cannot obtain the rights to them. Our preference is to have everything available both in print and electronic. But that is rarely our call.
On your question, try asking Richard Arnold, who is a wealth of information about traditional doors and windows. And a sweetheart of a person.
https://www.richarnold.co.uk/
Hi Chris and Megan,
Working on a set of four chairs, and while most of my legs have dead straight grain, a couple of them start to veer slightly away at one end. Would it be best to have that end on the floor or at the tenon? Or just burn it? 🙂
Put it at the bottom of the back legs. Most of that will get cut away when you cut the legs to tilt the seat backward a bit.
Good morning Chris, Megan,
Can one apply multiple coats (say 5) of the soft wax formulation you have written about?
In your writings you often talking about it in context of chairs and putting one just one coat and down the road applying another coat. With my completion of the travel ATC, I am back to working on Becksvoort’s 15 drawer cabinet (carcass done many dovetails to go). Ideally I want to finish it with your soft wax formulation (have purchased ingredients to make it). I have experienced with Tried and True (Becksvoort likes it and so do I but takes a lot of elbow grease) as well as Osmo Polyox (like the results and ease of application but not the 50% VOCs). Both of those require 4ish coats to get the richness I like on cherry. Just want to make sure no surprises if I try four of five coats of soft wax on furniture.
Many thanks for all of your help.
Sincerely,
Joe Leonetti
The oil will take a ong time to cure with subsequent coats. But feel free to add coats until it looks to your liking.
Thanks. I appreciate the reassurance!
Have you ever tried embedding pigment in wax? I am thinking I’ll try mixing soap finish with real milk paint and see how it goes.
Sure. I add pigments to waxes all the time. I’ve never added pigment to soap, but a test board will answer your question.
Are the chairmaking merit badges still available?
I’m afraid we ran out some time ago
Just curious if there are any “modern” furniture designers or builders whose work appeals to you? What are your thoughts on Hans Wegners chair designs?
Thanks,
Shawn
I am not LAP but if you haven’t already check out Peter Galbert. He has an LAP book and his chairs definitely have modern designs. He’s a great teacher, his blog is the only non-LAP blog I pay for, and also his video teaching is excellent.
I love lots of 20th c designers. Too many to name. The Eameses. Hans Wegner. Borge Mogenson. Lots of Swedish designers. Kaare Klint…. Most of the designers I like are people who understood the furniture record and then pushed forward.
Bauhaus (a rejection of historical design principles) doesn’t do it for me.
For the Irish arm chair and Gibson chair, if one has a benchtop bandsaw with 5” of resaw capacity, would you just remove 1” of height from the comb/backrest to still be able to cut out the curve on the bandsaw? Or do something else like laminating 2/3rds and cutting the curve, then glueing the last third after the curve has been cut?
I’ve using a narrower backrest for my Irish chairs of late. It’s 4-1/2″ wide, which will work in your band saw.
For the Gibson, the backrest width is a design feature of the chair that I would seek to preserve. The methods you suggest will work.
It’s okay to file open the mouth of your jack to take a heavier cut. I waited on this for years to preserve the ‘authenticity’ of my first plane, but it’s not a fine work tool. I’m so glad I eventually did. It’s no different than filing off mushrooming from a wedge or grinding the primary bevel of your iron. Make the tool work as efficiently as possible. A little filing goes a long way.
Hi Chris, Megan,
I just started reading Principles of Design. Great book so far and when I get to the pottery part, I think it will be helpful for wood turning. Do you have any other classical books you are in the process of brining back to life? I have a lot of the ones you had done so far and they are all really good.
Sincerely,
Joe
Not that I can think of at the moment – but I’m sure there will be more in the future.
Greetings, fine folks of LAP,
Help!
My current project incorporates a marquetry top made up of multiple wood species. All is good, except the oak bits have developed black dots after gluing.
I have heard that oxylic (?) acid removes this. I have no experience with this. The adhesive may be leeching through the veneer pores…and may be too thin to sand out.
Q1: would this acid bleach other neighbouring wood bits? (Or only oak?)
Q2: would a different adhesive help reduce the black dots? (I used PVA).
Kind Regards,
I don’t know what would be causing the black dots. I’ve never seen that. Black discoloration is usually iron+water+wood. And oxalic acid will remove that.
It’s worth a try on a small test patch with the oxalic because it’s pretty darn harmless.
I have no idea if the PVA is causing this problem, unless there is iron embedded in the wood. Sorry I’m no help on this.
Hello Megan- Dutch Tool Chests arrived at my house a couple days ago. Wow! What a great looking book. This has to be the best how-to/storytelling/photo project book I’ve ever owned, on any subject. Much more meaningful and inspirational than a simple “step 1, step 2” project guide. Great work, and thank you for your time and effort to put it all together.
-Steve.
Aw – thank you!
The grain direction of my seat offs left to right. The arms are front to back. Should the arm sticks run with the seat grain or the arm grain?
It doesn’t matter in a practical way – the furniture record is clear on this.
If you want to be “correct-est,” the annual rings on the sticks should run front to back.
Hi, Many thanks for doing this again. It’s so helpful and always a fascinating read. I have a query about the Hungarian chest maker you’ve shared info about. Do you happen to know anything about the “smoking process” he uses to colour them. Is he using ammonia fumes or is this something different?
I believe he puts the chests in a real smokehouse. You can send Tamas an email (Google translate helps!) for more details.
Thanks. As a hobby woodworker, time is something I have plenty of. Often for the oils I mentioned, I will wait a week between coats as it is. Don’t mind if it will take longer.
Thanks for your replies.
I’m making my first people sized chair, the Irishy Stick Chair out of Southern Yellow Pine. The grain in the legs is straight, in some of the legs the annual rings are close together say 1/16”, but in others it’s closer to 1/4”. Is this a problem?
Forgot to mention I added battens to the seat.
I’ve seen these chairs made from white pine. Do your best, and it likely will be fine. If it’s not, you will have learned a great deal.
Megan I just wanted to congratulate you on the new book. Your attention to detail and the book layout are well beyond the norm for most publications.
Regards
Bob Bell
You’re too kind. Thank you!
While using the tapered reamer and leaning to tweak the alignment I often end up with holes on the chair bottom that are somewhat out-of-round. The leg taper is usually pretty snug but there’s a small gap around parts of it. I’m ok with less than perfection, but at what point or how big does this gap turn into a problem?
If it’s more than 1/32″, I get worried. Though worrying is the chairmaker’s burden.
You can fill with epoxy. Or small wooden wedges.
Why no stick chairs in ash ever?
I built many many chairs in ash (they are shown on this blog). Ash is hard to come by these days because of the emerald borer. Much of the ash I encounter at the yards has been rotting on the ground before it was planked up. It’s fine for casework but iffy for chairs.
Ash is one of my favorite chair woods. I would use it for stick legs and stretchers on every chair if I could.
I was hoping that was the answer. Thanks.
Hey folks! Hope everyone is well.
Currently finishing a pine chest of drawers and have a couple nagging questions, best finish for unpainted pine? It’s soft so I figure either oil/wax or a softer exterior/spar varnish that won’t crack would be my best options.
And I’m thinking of putting a light coat of shellac on the pine drawer runners to increase longevity, any flaw in this thinking or should I just stick with wax?
Thanks in advance,
Marc
Your suggestions are great for pine. Just stay away from stains, which will reverse the grain colors and blotch. Oils, waxes and varnishes are best.
Shellacking the drawer runners won’t hurt, but it won’t add much life to the pine. Use them until the pine wears, then replace the runners with oak runners.
I cleaned up an old teak coffee table a couple of years ago and finished it with soap. It looked pretty good to start, but it’s getting pretty worn out now and it’s time for more finish. As I see it now, I feel like soft wax would be a better fit than soap; can I go right over the soap with soft wax, or would I need to remove the existing finish? (And how would I do that?) Or should I just go the easy route and rub some more soap on?
Wash the top with hot water. Let it dry. Sand away any raised grain with #320 sandpaper. Then apply the soft wax.
Soft wax looks GREAT on teak.
Chris, you’re written about which of your chair designs are most comfortable and which sell the best. But what is your favorite to make?
It really depends most on the wood. When I work with materials like red elm and oak, that’s heaven. Any chair in those materials is just a joy to build because the species are so complementary.
A rabbet question, if you had to cut a rabbet deeper to fix an out-of-square mistake, would that weaken the joint? Does it depend on the wood? Thanks!
Depends on the overall thickness of the workpiece, as well as the wood. But you could use, say, a shoulder plane (or unfenced rabbet plane), and take down only the high spots to level it out, thereby not making all of the rabbet deeper, if too deep is a concern,
@Roge
I’ve found that the tapered tenon cutter will stop cutting if I haven’t tapered the tenon-end of the leg enough. This may also be worth looking at.
Good suggestion. Thank you!
Hi there.
For a stick chair, what do you consider the minimum acceptable finished thickness of the seat?
I presume a softwood needs to be thicker than a hardwood so it would be great if you could give me an idea on both.
And is it ok to face laminate thinner boards together to achieve a workable thickness?
I like to use seat boards that are 1-5/8″ or thicker. Softwood vs. hardwood doesn’t really make a difference (except at the extremes — white pine and white oak).
I have seen many old seats that are thinner, but it is risky.
If you need to thicken a seatboard, you might consider battens. A commonsense solution in most cultures. Check out the Peasant Chair in “The American Peasant,” a free download. Those are just nailed on.
Face-laminating is an option. But I always prefer battens.
Lump hammer maintenance question: some rust spots showed up (from Piggly glue?). Is it ok to wipe hammers with oil like all other tools?
Well mine hasn’t suffered permanent damage from doing that! (I remove the rust first with a “rust eraser”: https://www.theruststore.com/products/sandflex-rust-erase-3-pack?variant=48122887176514&country=US¤cy=USD&utm_medium=product_sync&utm_source=google&utm_content=sag_organic&utm_campaign=sag_organic&gad_source=1&gclid=EAIaIQobChMIvceN493hiQMVmmBHAR174yRPEAQYBSABEgIMj_D_BwE)
On Chris’s website under the category Workshop, the saw benches are bold with thick legs and through tenons.
They’re beautiful. The photography is good as well 🙂 and highlights the grain and leg strength.
I’m about to build the saw bench for my first real project but prefer the look of these ones to the 2008 version which ive found plans and videos for. Are there plans or any details for this specific version?
I’m confused about mortise chisels vs sash mortis. The pigsticker (I’ve forgotten the brand) aren’t available in Canada. And the US dealer won’t ship here. So what else is a proper mortise chisel as it seems like Nielsen and Lee valley might only have sash.
Thanks
Shawn
The sawbenches are here: https://www.popularwoodworking.com/wp-content/uploads/2010/10/Sawbench.pdf
As far as the mortise chisels, I see that LV carries the Narex – but I don’t know what else is available in Canada, I’m afraid.
Thank you!
I just picked up a lakeside number 3 in pretty decent shape that I’m thinking about converting to a scrub plane. Is your preference still to just use a number 5 with a cambered iron instead? If so, it it just because if the longer sole?
A No. 3 is a fine choice for a scrub plane. Give it a go and see how you like it.
I prefer the longer sole of the No. 5, but there are whole cultures that prefer a shorter plane.