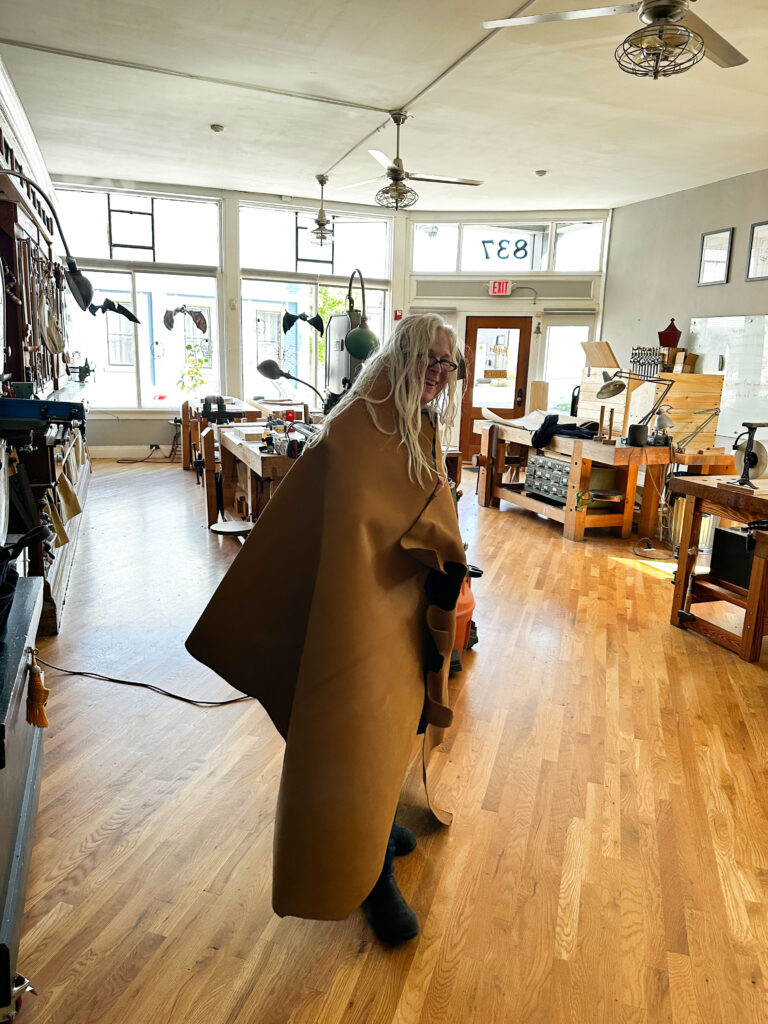
Update: Comments are now closed. Join us again on Nov. 16.
If you have a woodworking question, today is your lucky day. Chris and I are holding Open Wire between now and 5 p.m. Eastern.
How do you ask a question? Leave your question in the comments section, and we’ll do our best to answer it.
The next Open Wire is on Nov. 16.
– Fitz
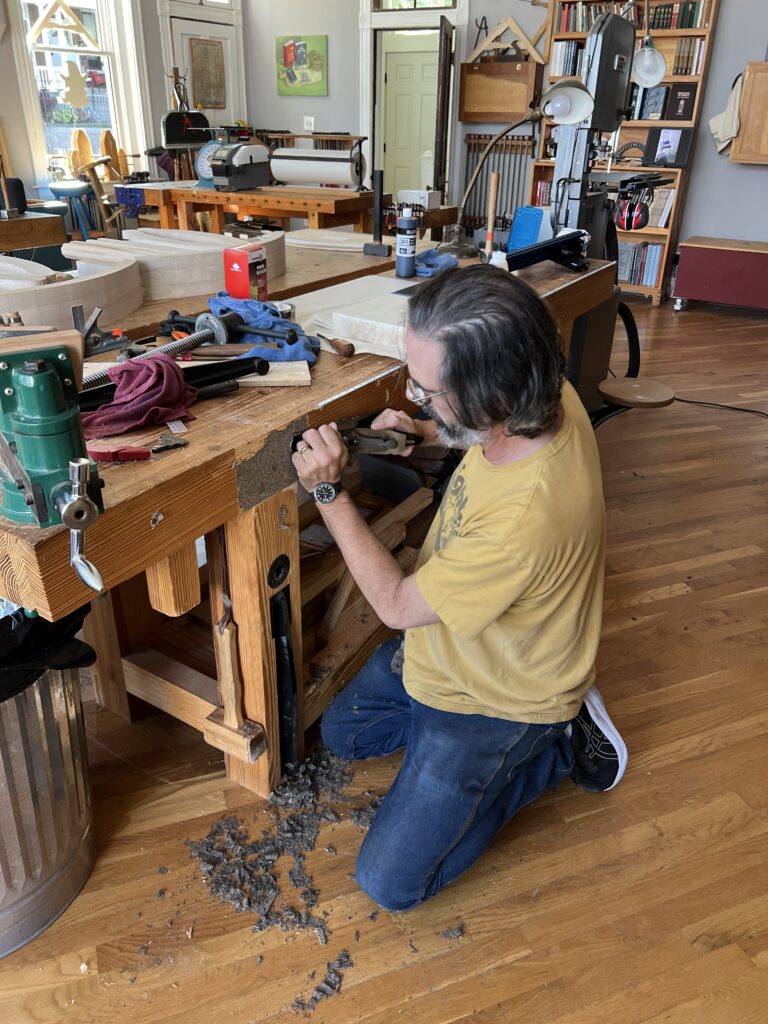
Good morning and thanks again for your generous gift of time for Open Wire.
I’m thinking of a Gibson or a relaxed Irish stick chair for outdoor patio use – think of the typical use of an Adirondack chair. Would you modify any construction or design for such a purpose?
I’m considering unfinished white oak, or if finished, linseed oil paint. Thoughts on lumber species and finishes?
Thanks
Sam
Those are all fine choices. You might use a Type II or III adhesive (which you probably already thought of). Another possible finish is linseed oil, which you can reapply each year.
Hi Chris,
In a blogpost from 2020 you mention that you like to to keep smaller tools in little metal edge boxes in the sliding tills of your tool chest, and in reply to a question in the comments to that blog post on where to buy such boxes, you link to Hollinger Metal Edge.
Now, I also like to keep smaller tools in cardboard boxes, and have a few of those little metal edge boxes (Chris Vesper used them as packaging for tools I bought from him), but cannot find anything like them on the Hollinger Metal Edge website. All I find there are larger boxes.
(Also, the exact page to which you linked in 2020 is no more.)
Did you buy those small boxes from Hollinger, and they have just stopped making them? Or is it just that I am not looking for them in the right way? I have of course tried googling and other forms of searching but to little avail.
In short: do you happen know of a current source for small metal edge cardboard boxes like the ones in your blog post from 2020?
Cheers and all best,
Mattias
I’m afraid I don’t know another source. They had smaller boxes. Chris Vesper has a source, but he’s not telling. Sorry.
Is it these by chance? https://www.hollingermetaledge.com/inner-packing-boxes-for-record-storage-boxes/
Good morning all. Last week I drilled all the mortises for the “welshy” stick chair covered in your video series (which is really great btw). I was able to get all the drilling done and can fit the arm onto short sticks so that tells me I’m in pretty good shape.
However, I could not find a placement for the front drilling jig that did not block either one of the holes through the arm or the drill path from arm to seat. What am I doing wrong here ?
In the end I drilled enough holes to use short sticks to align the arm and then repositioned the jig but I see that as asking for problems.
Also (and this is a dumb question) for some brain dead reap. I cut all the long sticks to 24” long instead of 27”. How different would the comb look 3” lower ? I’m planning to just make more sticks but didn’t know if I could turn a bug into a feature.
Next up – saddling. Many thanks.
In rare circumstances, the the front drilling jig ends up in a bad place, which you have magically and unfortunately found. It occurs when the stars align and your backrest angle and short stick locations are just so. It’s happened to me maybe three times in my life.
When this happens, I drill everything I can without moving the jig. Then I release the clamp on one end of the jig and carefully rotate it back or forward until I have the clearance I need. Then I return the jig to its original position and repeat on the other side.
Hope this makes sense.
On long sticks: 27″ is a good starting point. You can easily shorten things to 24″. If you follow the directions for locating the mortises in the comb, you’ll be fine.
Good morning,
Do you have any news on the upcoming Walker & Tolpin book? How does it differ/complement Principles of Design? Thanks!
We are reviewing the page design now. When the book is complete (very soon), we’ll announce the contents and explain its relationship to the other books. I can say this: It’s a real good one.
Good morning – I’m in the process of building (2) comb-back stick chairs, and plan to build the Irish Stick Chair from your article in FW (or the version designed for the larger sitter you posted about on the blog). I’m using the CMT tenon cutter for the 1″ tenons. Before I get other sizes I was curious about sharpening. Comparing the CMT to the Lee Valley cutters, is one easier to sharpen or does one last longer between sharpenings? The price difference is negligible and I like the square shoulder the CMT produces, but the differences in geometry and material (and my own lack of experience) have me weighing the two options.
I’m afraid I’ve never sharpened one. The factory edge will likely last long enough for a lifetime of chairmaking. And the carbide ones can’t be sharpened in a typical home workshop.
Do all the crucible hammers come with unfinished handles? If so do you recommend a finish?
All our hammers are finished with a light coat of oil. The oil from your hands and use will continue to polish them.
When making a dovetailed jewelry box using Old Brown hide glue, what is the best way to sand the inside corners after removing excess glue with water?
Typically I would tape off the corners in a fancy box before gluing so that the glue would squeeze onto the tape.
If I have to sand into corners, I put peel-and-stick sandpaper paper on one face of a small scrap (basically making an emery board) and do the thankless job. And I think about flocking.
Is a slab of sugar pine ok for a Roman workbench? There’s a local lumber yard that offers 3″ thick air dried slabs of sugar pine and incense cedar.
Absolutely yes.
I’m envious. I wish I could get Sugar pine here, for tool chests. I love dovetailing the stuff!
One of my small benches is from Eastern white pine, and it’s pretty lightweight, so we screw battens to the floor to keep it from moving. But that’s my only complaint. And given that you’ll be sitting on the Roman bench while using it, it should be fine.
My dad growing up as a kid used to vacation in the 1940s in Weed and Dunsmuir CA (it grew there and was logged so lots of scraps). All the sugar pine he could want for whittling all day. He loved the stuff.
Good morning Chris and Megan,
I’m trying to build your knockdown Nicholson bench. My goal is to have a set of travel benches to teach with.
I’m struggling to find boards for the top. I bought a few 2x12s that were mostly clear, but they developed twist (I stacked and stickered them for a couple weeks).
Am I just not being selective enough at the big box store? Would 2x8s be less likely to have twist? Do you have any other thoughts or insights on how to get clear-ish, straight material for the top?
This is the issue with construction lumber, I’m afraid. Especially on the West Coast (I don’t know where you live) where they sell Doug fir that is sopping wet. If you can’t afford wood from the lumberyard (which is likely to be drier), use plywood and glue up two layers to make the top.
I have found that the best quality wood is often found in longer lengths and has less to do with width. It takes a bigger tree to make a 14’, 16’ or even 20’ board.
Is it these by chance? https://www.hollingermetaledge.com/inner-packing-boxes-for-record-storage-boxes/
Hmm. This was to be a reply to a post way up the page…
Sorry – we don’t know why direct replies aren’t nesting…except for us.
Good morning,
Will Lee Valley Tools be selling The Stick Chair Journal No. 2?
Thank you!
As always, it’s Lee Valley’s decision. If customers ask for it, they usually order it.
Stick chair finished with milk paint acquired a big olive oil thumbprint on the crest rail. Any options to address?
Try wiping gently with mineral spirits. It removes oil and shouldn’t affect the milk paint.
The photo today of Chris working on an Anarchist Workbench is fortuitous. Thatl’s the topic of my question.
I’m planning to build an 80” long version of the Anarchist Workbench. (Available space in my retirement home abode limits the length.) My available alternatives for wood are yellow pine and Douglas Fir.
Unfortunately, I can only source yellow pine in 2” x 6” x 4’ lengths. Using such stock, I could built the top by making three-board “sandwiches” that use one 48” section plus single sections measuring 32” or two sections measuring 16”. (This utilizes the 4’ boards without waste.) The butt ends would be arranged thusly:
======================= | =============. (
============ | ========================. { six of these would make the bench top
======= | ====================== | ======. (
As it works out, a bench made from 2” x 6” yellow pine would weigh and cost about the same the same as a bench made from 2” x 8” Douglas Fir, which is readily available in many lengths.
My decision seems to come down to a having an easier and “cleaner” build with Douglas Fir versus a slightly more complicated but more durable work surface with yellow pine.
Which would you recommend? I’m leaning toward the Yellow Pine if you don’t think the butt joints along the top would be a problem. Any special considerations for cutting the butt ends other than precisely square?
Chris might disagree, but I’d go with the Doug fir – an easier build and will be entirely suitable. But as far as the butt joints if you go with the SYP, as long as they’re tight, no problem.
Based on an earlier comment to another post, I can add that the yellow pine is quite dry and tolerably straight.
Lew Phelps- regarding butt joints, how about making lap joints at those butts? A 3 or 4 inch lap joint at each butt would create a stable joint without having to worry about the butt joints opening for whatever reason. You could even dowel pin the laps for added stability.
Sorry, that attempted graphic with the equals signs didnt work out because the line returns were eliminated.
Is the Doug fir wet? If so, then I’d opt for the yellow pine.
Good morning.
I sawed up a 2 western maple trees last winter and it’s been air drying for about eight months now. I was planning on getting some of it kiln dried so I could start making some chair seats in a month or so. Just wondering how low to get the moisture content.
Thanks a lot.
I’d ask your local kiln what they want. They probably want it below the fiber saturation point, if I had to make a broad guess.
I have a question about sharpening chisels and plane irons. In your book, Sharpen This, you sharpen a primary bevel to 35° and then add a secondary 25° bevel. Then as the edge dulls, you re-sharpen the 25° secondary bevel. Eventually, you will have to re-grind the 35° primary bevel. I do not own a grinder. I do not plan on purchasing a grinder. What angle would you recommend for a single primary bevel? 30° 25° or 35°? Or does it matter which single angle you choose?
In the book I believe I recommend a 25° primary and a 35° (or whatever) secondary. I use an inexpensive dry grinder to reestablish the primary. If you won’t buy a grinder, stick some #60 grit belt sander paper to a floor tile or steel plate. It’s miserable work, but it works.
Do you have any sort of special air filtration system inside LAP to mitigate dust or do you just open doors / windows?
With power tools, it’s pretty obvious that the air is dirty since you can see big plumes of dust. I’m beginning to wonder how much dust I’m breathing inside my hand-tool workshop, even though I can barely see any in the air.
In the bench room, we do not (though we vacuum a lot). But we are making a minuscule amount small-particulate dust with hand tools.
Early on, I bought a Dylos particulate meter to measure how much dust I was making working with hand tools. Hand planing and chiseling such as to make a mortise or clean a dovetail didn’t change the air quality. Sawing by hand, raised it a little but still well within the good range. Sanding by hand saw a spike which wasn’t a surprise. I don’t sand that much so for me in my shop, I felt the air was safe. Twice now since putting ductless AC in my garage during the annual maintenance when the workers cleaned the filters they had essentially no dust in them which confirmed what the Dylos had told me. Hope this helps.
I am well underway with my first stick chairs, just need a GoDrilla with a straight hex rod, and an answer to this question. I’ve discovered some small discrepancies between the chair plans and revised book, and even a small error I believe in one of the drawings. Not a dealbreaker, but is there
an errata sheet? Thanks for all you do.
I’m sure there are. I state pretty clearly in the book that there will be inconsistencies because we provided engineering-style drawings for something that is typically made without plans. If you think you’ve found an error, please send it to help@lostartpress.comand we will take a look. Mostly I encourage people to find their own way. It’s just chairmaking.
Good morning! I am somewhat late to the chairmaking game, and am finding the shear amount of information from y’all on drill bits a little overwhelming. What is your current recommendation for bits for a beginner? Thank you!
Use what you can get. Spade bits work fine. Currently we use WoodOwl augers for leg-to-seat joints. And Star M F-type bits (or Wood Owl Overdrives) for everything else.
Curious about your opinion.
I have a lot of 1/2” not-too-great cherry board. Too much. What are your thoughts on riving the boards and laminating them together, then shaping them for say, the Roman workbench legs or stout stools. Lots of mixed opinions out there. Curious about yours.
1/2″ thick? That sounds like entirely too much work for dubious payoff. I’d make Shaker trays or some other small gift-type items from them.
Hello, Chris and Megan! I’m planning to make steam bend arm/comb to my next chair. In addition to dead straight grain, does the orientation of growth rings matter when bending the wood? Like in the ready armbow, should the growth rings go vertically or horizontally? Thanks!
I’m not an expert here. But I have more luck with the rings parallel to the bend. And more success when the heart side of the tree is on the inside radius of the bend.
But I have seen it done all ways.
I have a bunch of 4/4 red oak leftover after a recent project, and an itch to build another chair. My plan was to do a Germanic style battened seat with it and have a 3/4″ thick seat, but I noticed in a lot of your battened chairs you use 5/4 to get a 1″ seat. Do you think 3/4″ will be too thin?
Thank you!
You’ll be fine. Just don’t saddle it.
DTC question…just wondering if anyone has dovetailed the front panel instead of nailing it?…(the upper panel under the lid).
Question #2. Has there been any discussion of creating a ATC/DTC toolchest combining the best of both?…. (ATC/DTC sounds like the highway to hell?)
If you kept the fall front, it would then stick out 3/4″ in front if you dovetailed the top panel. But sure, you could do that (though your tails would be oriented with the grain – I’d be careful at the baseline…easy to tear out there). Seems like a lot of trouble though for not a lot of payoff. I’m not sure what I’d combine from the two chests – the beauty of the DTC is (for me), i9t’s excellent travel size. The ATC, on the the other hand, is perfect for holding ALL my hand tools in the shop. But arguably the Swedish tool chest kinda does both?
Good morning Folks. I have a question about the care & feeding of my Woobie. I switched from keeping it in a Ziplock bag to a fancy Toyo tin (in black to match my ATC of course) and it seems to be getting gummy. I did purchase some jojoba oil from Amazon instead of Lie-Nielsen in an effort to pinch some pennies. Is it possible it’s gone off? Any suggestions? Thanks!
When mine starts to get gummy, I wash it and start over w/adding oil/ I get jojoba from a health food store – I guess it’s possible you got a bad batch, but it’s probably an accretion of dust mixed w/oil and other gunk that’s causing the gummy.
I wash mine when they get gummy. That is the big reset button.
Hey Hi Hello! Lucky day! Can you please point me to a good resource on how to fettle old planes? Online forums make me want to scream.
I know to flatten the sole, and stone the chipbreaker flat, and file the frog so the the iron sits flat as possible, but that’s about the extent of my brain-stuff and I can’t get this thing to stop chattering. I adore old tools and am willing to put in the time.
Thanks for your time!
xoxo
-Steve
Go through Mike Webster’s links (which go to his IG page). He does great work. Overkill. But nice overkill.
I installed a Benchcrafted CrissCross for my leg vise, and after a year or so of use the tapped threads in the leg gave up. I’ve replaced the bolts with #14 screws, but am worried that someday they may break and leave me with a nightmare of metal shards to remove from the leg to get the vise working again. Have you ever had screws fail here? I don’t have a great understanding of the forces on that mounting point…
I think you are worried too much. I have used No. 14 screws in mine (into yellow pine, which does not tap well) and it has been fine through years of asbuse.
I love the carved figures on the cover of Shop Tails and would like to try my hand at carving figures and small sculptures like this. Do you have any pointers on tools I need, what wood to use, grain orientation, or other guidance on where a beginner might start? Thank you.
Those are by https://www.instagram.com/carol.a.russell/. Go to Australia and take a class with her! (I’m afraid I don’t know…I’d ask her on IG for a book recce)
Good morning
Quick question in finishing a table top. I am replicating a 17h century Swedish farm table I saw on 1st Dibs using Chris guidance from the work table in the ADB. I and building it from southern yellow pine slabs. What would you recommend for a finish? I am thinking of just using soft wax so it ages to a nice mellow yellow.
Posted this question about two hour ago and did not see is go through.
Soft wax is a great choice, as is soap.
(In case this ends up in the wrong place from where I tried to insert it, it is a reply to Chris and to Iain re: my questyio about Hollinger metal edge boxes.)
Thank you Chris! There are indeed various makers around the world of metal edge boxes, although I haven’t yet found one that makes those really small sizes. I’ll keep looking. Who knows? I might by happenstance stumble across Chris Vesper’s secret source …
Thank you, too, Iain, but alas!, the ones you are linking to are considerably larger than what I am after. The closest I can find on the Hollinger website are what they call Artifact Storage Boxes, which are relatively small, but as far as I can see only available in square formats, whereas for small tool storage a rectangular shape is often more useful.
In fact, the sort of size I’m looking for is approximately 6″ x 1-1/2″ x 7/8″, or a little longer and wider, or a little shorter and narrower, but thereabouts.
Cheers,
Mattias
Hi, is the Varnum book going to your EU sellers?
They can stock the title if they wish. It’s not our call. Talk to your dealer and they will know there is demand for it
Hi! I have built a frame assembly with casters to move my ATC around easily. The frame assembly made from 2″X2″ pine.
I am somewhat afraid that I know the answer, but my casters have four screw holes. Is it enough from the point of sturdiness if the casters are affixed with three of four screws?
Thanks a lot in advance!
I’d make a block large enough to fit under the entire plate, and screw through that into 3 frame locations, then use a short screw on the one that doesn’t grab the frame. I used 3 bots on my poly casters for years…but they were 4″ long. On my casters, which are screwed on, I wanted the extra grab/support.
Cheers! Any suggestions on the thickness of that block? Would 1/2″ plywood do? I don’t want to gain too much height if possible…
I used 1/2″ scrap…of I have no idea. But yes, I think ply would be fine.
I’ve been using liquid hide glue for a while and am just dabbling in hot hide glue. I’m a bit confused about the various gram strengths. Is the glue joint actually stronger with higher strength, or does it just set faster? Are there any applications that you prefer hot hide to liquid hide glue? Thanks!!
Gram strength is also called bloom strength. The higher the number the harder or more rigid the dried glue is. “Stronger” isn’t the point. All the bloom strengths produce joints that are stronger than the surrounding wood, so more strength is pointless. Hope this makes sense.
Good morning and thanks for spending some of your Saturday with us. I’m making my first-ever chair, the ADB three legged backstool. When drilling the back mortise, I didn’t realize that the steep angle would cause the drill bit to fight me so much at the start, and the angle is off the sightline.
Would you recommend that I try to correct with the reamer, or plug the hole with a dowel and start again? I’m going to paint it, so not very worried about grain match.
You can try to correct with a reamer, but that can make the mortise over-big. Or you can plug, which might make the re-drilling difficult because it will be into end grain. Or you can live with it. I don’t have better advice without seeing how fsr you asre off your sightline and how deep you have already drilled. Sorry.
Hello, how do you set up your Grizzly carver’s vise? Do you usually have the back jaw stationary and the front jaw rotating or do both rotate? Thanks!
The one currently on Chris’ bench has both jaws moveable. But it’s easy enough to change, when desired.
Good morning, Meghan, Chris, and Kale.
Meghan, good recommendation on the VE Schwaab book A Darker Shade of Magic. It starts off slow but damn it pops off in the second half. I’ll be reading more from that author. Hope you guys are having a fairly chill Saturday.
Jeremy
Will your gelatin glue work for bent lamination’s? I was concerned about creep. BTW I’ve found it to be a great glue for chair work. Thank you Chris for sharing.
It would work OK for a bent lam. But it will creep a bit. I would buy (or make) glue with a higher bloom strength (we use 250; 300 would be a more rigid/still glue bond).
Thanks Chris – that’s what I’d hoped for 🙂
And thanks for the ongoing forum – I learn so much from all the questions I wouldn’t have thought to ask!
Any plans for some instructional videos for American peasant furniture?
We haven’t discussed it. But now we will.
Hell ya
Morning,
Any advice for traveling with tools? Recommendations for cases? Do
you mail them or check the bag?
Thanks very much for doing the open wire, love reading it!
We both use hard cases and pack the tools so they won’t move. I tend to use my socks and a T-shirt or two, in addition to foam, which also frees up room in my carry-on bag in which I pack my clothes. Chris uses a Pelican, I have a Nanuk.
Would soft wax be an acceptable finish for a couple of book cases? How long do you think they’d need to sit after application (if the answer is yes) of the wax to be considered safe?
Also, thanks for publishing the soft wax recipe. I’ve used it on turned bowls and other things and have been happy with it.
I’ve used it on bookcases. I waited 48 hours, just to be sure it was completely dry…but that’s almost certainly overkill; 24 is likely plenty
We’ve used soft wax on bookcases with no problems. The oil fully cures in about three weeks (if you want to be on the safe side).
If you had to choose between the Grizzly carvers vise or the Benchcrafted hi-vise for chair making, which would you choose? Already have a leg vise. Thanks!
Probably the Grizzly. Cheaper and both jaws rotate. I still love the Benchcrated Hi-Vise.
Finally getting around to finishing my ADB bookcase. A couple of the shelves have cupped slightly in the interim. I believe I’ve heard Megan Fitzpatrick and others say that’s not a problem. One thing I haven’t seen are tips on getting those cupped shelves into the dado. Help?
If the dado is tight, it will pull out the cup. As long as the cup isn’t too severe, you should be able to knock them in from the back. I would use a lump hammer (or similar), and put a piece of wood over the shelf edge and hit that, rather than the shelf itself. Vary where you’re hitting so as to force it in evenly at each side.
To make sure I’m understanding, hit in from the back and slide it in along the dado (front to back)?
Hit it from the back to slide it in back to front. Hit it in in the center back, in hopes that will make it slide in parallel along it’s length. If it goes in more on one end than the other, shift the block/hammer to even it up again.
You can instead hit it in from the front…but I prefer the back, because any damage will be hidden.
Regarding the archival boxes, there are companies such as Gaylord Archival who will build them to a spec although you may have to settle with a slightly larger size.
Hi Chris and Megan,
Thanks as always for doing this!
First, not a question but a note that https://layout.computer now supports Welsh and Irish chairs and even some in-between. I’ve also added a 🎲 button which is quite fun 🙂
Now to physical chairs: sometimes after fitting a leg into a tapered mortise, I get a gap around the tenon, visible on the surface of the seat. Not all the way around a tenon (which would mean the wrong included angle), but let’s say on two sides, like the hole is oval-shaped.
1) What’s the likely culprit, careless reaming (I use the Veritas drill-powered implement)?
2) What’s the best way to fix the gaps? Glueing in some thin bent pieces of wood?
Thanks. I have drilled through … I figured it would be mostly impossible to get a definitive answer – just checking my thinking. I’ll probably try to set up a jig to ream accurately in a drill press.
Thanks – I didn’t think I’d get a definitive answer, but am happy to have a on my thinking. I have drilled through; I will try to set up a jig to ream in the drill press.
Thanks for sharing your time with us! My question is on edge jointing. Straight is no problem. I hollow the middle like David Charlesworth and then take a few full length shavings. It’s square that I screw up. Even if the edge starts square and just needs band saw marks planed off, I manage to bevel it away from me or, worse, twist it. I am using a LN No. 7. Even projection of the blade and pressure are the variables I think. For those who have figured this out, any tips? Any favorite resources to recommend?
ermmm… practice? If you’re always out of square in the same direction, that tells you what you need to concentrate on correcting. But no shame in using a No. 95 when needed! (Edge-trimming plane)
(If this ends up in the wrong spot, it is in answer to Louis Hannegans question on edge jointing.)
My jointer is also the LN #7, and I, too, started out taking my cues on precison planing from David Charlesworth’s videos, so I kinda know where you’re coming from. Furthermore, I know it can be done, because I have gone from hit-and-miss (tending mainly towards “miss”) to where I can now plane even the thinnest of edges square at the first attempt, at least nine times out of ten.
So, Megan is spot on: it takes practice, practice, practice. And, again just as Megan says, that practice should be conscious. That is to say, first, be sure that you know what the error is; then try to remedy the error; check again; if better, you’re heading in the right direction; if not, you know in what sense you need to compensate.
As with so many other hand tool operations, it is very much a question of building muscle memory (or “feel”, if you like).
Then on a more technical level there are three things that I find essential.
Firstly, to have a slightly cambered blade, so that you can take tapered shavings, and to know where the center point of that blade is. It should be in the middle, but depending on what happens on the sharpening stones, that might not always be the case. Again, practice and experience will teach to you recognise when the center is off-center, and you can adapt your cuts accordingly.
Secondly, to never hold the plane by the front know, but always use the thumb-and fingers grip! If you grab the plane by the knob, it becomes virtually impossible to keep it balanced correctly – the knob grip is much less sensitive and gives way too much leverage left and right.
Thirdly, to watch the shaving! Say you’re too high to the left. You then only want to take a shaving there. If you are strying into the middle or even to the right, you are headed for an erroneous cut. Aghain, this is part of the conscious working idea. Know what needs to be done, watch what you are doing, check the results, and deduce from the results what was right and what was wrong.
And as a final comment, I found it truly surprising to notice just how small and narrow a shaving would be enough to correct what under the egde of the try square looked like a ginormous error. Less is most of the time more in this particular game, I have found.
Cheers and have fun practicing – you will get there!
Mattias
Two questions
My grandfather was a pattern marker for GE back around 1930-1950. He left behind a 1 1/2″ Barton chisel (tang, not socket) that has the back grooved like the back of a toothing plane iron. I can’t find out what it would have been used for. Do you know?
Also, can you tell me the sight line angles for the seven stick chair or should I just print up the plan?
Thanks!
No clue on the chisel. But patternmakers tools can seem foreign to furniture makers.
The sightlines for the seven stick are the same as they are for my other comb-backs. Front legs 38°. Rear legs 65°. Resultant 23° for all legs.
Thank you for your time this Saturday. I’m trying to pick a stick chair plan to start a build. Is there a simple way to think of the differences between the 6 stick and bent arm comb backs in the SCB, the SCJ improved comb back and recent 7 stick comb back plan from substack?
Is it more aesthetic / construction method difference above seat or do the sit differently?
Thank you.
They are all similar chairs. The only major difference is the one that has the bent arm. Bending adds a level of complexity. How they sit is up to you as you choose the angles for the back and seat.
My advice is to pick one that you like the most. You’ll be more motivated to do it.
Good afternoon Chris and Megan,
Question 1. I bought a very nice No. 3 plane from the shop above Roy Underhills former commercial studio. I have noticed that the lateral adjuster is rubbing the rear handle so that I really can’t make lateral blade adjustments. My thought is to take a rasp and remove the part of the wood on the handle where it is rubbing. Is this how you would fix it or is there alternate way one would normally fix it?
Question 2. Just finishing up the red milk paint undercoat for an ATC I had built with Megan at Port Townsend School of Woodworking. Next will go on the black top coat. The blogs you provide and I purchased Peter Galbert’s milk paint video series (super helpful-thank you). From 6 feet away, the red look like a homogeneous coat. When you get close, you start to see wood grain, etc – it’s quite pretty. I suspect top coat of black will produce similar effect. Is this what milk paint normally looks like on a painted chest (homogeneous six feet away and nice subtleties close up)? I don’t have a lot of experience with using it.
Sincerely,
Joe Leonetti
Hi Joe.
I use a hammer (light taps) to adjust my blades. The lateral adjust lever is too gross of an adjustment. So I guess were it me, I’d bend it down slightly so it doesn’t rub (or ignore it).
On the milk paint, yes. I can see the grain through it, unless I use MANY coats. I like this feature of the coating.
I’ll let Megan answer the milk paint question. Milk paint is… endlessly variable.
If the lateral is rubbing the tote then it has probably been bent. Bend it up until it does rub the tote.
Hello and thank you again for doing Open Wire. Question: What are your two favorite hand planes?
router plane and No. 3
my block (LN 60-1/2) and my jack (Stanley No. 5 Type 11)
How large do you think the basic design for the design book drinking table could be scaled? Is a 72” top with three legs crazy?
With thick legs and a thick top…. go for it.
I want to build the bookcase from the anarchist design book, but make it 3 bays long and add a top. If I make it three bays long, would I still make a 1/4” dado on each side? For the top should I add a rail at the top front to support the top? Or if not how would you recommend attaching the top?
Thanks for doing these.
I’m not sure I understand the dado question…are you using uprights (sides) in between your bays? So you’re asking if there would a 1/4″ dado on both sides? If that’s the question, yes. As far as a top, I’d probably cut a rabbet at the top edges on the outside boards to house it, then nail it in to match the shelves. Then the two center boards (if I’m reading the three-bay question correctly) would need to be shorter than the sides by the thickness of the top.
For people trying to sharpen their eye for design in general (furniture, buildings, and beyond), which books would you recommend? Varnum’s Principles of Design seems obvious. Which book or books by Tolpin and Walker? Others?
Scraper plane recommendations? Maybe a Never Sponsored subject?
If I’m honest, no matter how much I try, I don’t love scraper planes. I prefer to get my smoother tuned up high. Then I use a card scraper to finish the job. Scraper planes are ideal for marquetry, but I really don’t see much use for them in my work. Sorry.
Hi Chris and Fitz!
I have a question regarding the Stanley 46 tonguing blade. I recently picked one up that had the tonguing blade! For the life of me I cannot figure out how to get it to cut!! I own 48/49 and various wood and metal planes with tonguing blade and no problems!
The 46 keeps digging into the wood and no matter how light I set the blade it still wants to dig in.
The instructions from Stanley for the 46 refer to the wide rabbit blade and to “do the same thing” as you use the tonguning blade, but I still struggle.
Can anyone help solve this??
My 46 is an older type 2/3. So it doesn’t have the upper and lower mounting holes as the later ones do.
Thank you!
Greetings!
Re: recent chisel reviews…
Have you considered trying a Japanese dovetail chisel? Balanced differently from western styles…in my experience…less tiresome to use over long periods of time…
I have used them and like them just fine. There are millions of chisels w didn’t include in our review.
Hello and thank you for hosting these! I wish I could somehow get a copy of the Book of Plates, but I understand you may not be eager to bring it back in print. Have you ever considered offering it as a PDF and/or another digital format like EPUB? I also wonder about the Woodworker series – I own and love the hard copies, but sometimes wish I could pull them up while I’m in transit.
On the Woodworker series, we don’t own the digital rights to the material, so electronic editions are not possible (this was at the insistence of the rights holder).
On the Book of Plates, they are out there and turn up from time to time. If you really want ot, you can make your own electronic version by downloading one of the many scanned versions of “l’art du menuisier” out there and stitching the plates together in a file. It’s so easy that I could do it.
Try this:
https://www.e-rara.ch/zut/content/structure/4124136
Thanks for taking the time to answer our questions. I’m building the bookcase in anarchist design. I want to use a soap finish, will it cause the nail heads to tarnish/rust?
I have no idea…depends on the nails. I’d coat a nailhead in soap finish and see what happens in a day or 10
Soap finish is mostly water, so bare metal might darken if you don’t wipe the soap off immediately. Coated nails (like Rivierre) don’t tarnish with a soap finish. Like Megan said, a little testing is a good thing.
I was considering starting a chest based on “Campaign Furniture”. But it looks like Horton brasses has much less of a selection of campaign brasses than a few years ago. Any suggestions on alternative sources?
I’d call Orion Henderson at Horton and ask him. He knows how to source hardware and even has brought in on stuff from overseas for me and colored it to match. He’s also as friendly a guy as you could want.
Another source is ebay – boxes of pulls and corner guards turn up regularly.
Question about tapering octagonal legs – I’m building your wood whisperer Guild American Welsh chair. The legs need to be tapered 3/4″, so 3/8″ on each side. If you have a bench top jointer that only takes off 1/8″ per pass, is it ok to taper the legs a little and then redo the tapering operation again on the jointer, or would it not work the second time? Or best to just use a hand plane if the only jointer available is a bench top one?
Thanks!
I’ve never done the operation in two stages, but I don’t know why it wouldn’t work. Try it one a test scrap that is the same size as the leg and you will get your answer.
I inherited a copper lined Hold-Heet glue pot from a neighbor, but it’s half filled with old, very funky glue.
What’s the best way to get it back in working shape?
I’ve rehydrated the glue as best I could and scraped a bunch of the junk out, but it still needs some serious work.
I’d heat it up (outside) and add water. Let it stew all day. It should loosen up the glue.
Thanks, Mattias and Megan! I am tempted by the idea of a long grain shooting board like Terry Gordon’s but I’ll keep practicing. Question—how much pressure are you using as you joint the edge?
You’re welcome, Louis!
As to pressure: very little to none, I’d say; mostly just the weight of the plane. Which, in turn, means that when I’m correcting an out-of-square edge, I do tend to plane a bump onto the middle of the length, so I will mostly work to square first, then sort out straight in the length.
Thanks for the follow up response! I’ll give it some more conscious practice and keep at it. Square edge, slightly hollow length, full length shaving. If I can do the last step without going back to the first, that would make milling by hand much better. I follow Richard Maguire’s approach to face jointing and love how fast and accurately I can flatten a board. The edges are my weakness. Looking forward to refining a process there. I love making shavings—but not when I’m chasing my tail!
The same pressure I use when smooth planing, with more pressure during the middle of the stroke.
Honestly, honestly, this is all fixable by practice. Long-grain shooting boards aren’t necessary. It is frustrating for sure, but it will “click” in time.
Hi all, I’d like your thoughts on laminating boards together for chair legs.
I’m planning on building a couple side chairs with a pile of 6/4 white oak. It passes the hammer test when hexagonalized but I’m worried about it looking anemic.
My other thought is laminating two pieces together to bring it to a more typical size but I also worry about that looking wonky.
The last option and probably the smart one is to buy some wood that’s already sized appropriately for chair legs. I’d like to use what I have on hand but if it’s not going to yield good results I’d rather pony up for the right material from the start.
If you do laminate the legs, try to get an arris on the seam between the boards. This usually hides the fact that you glued things up. You might try making one leg and see how you like it.
Hey, my question is about the wood tap and die set from Germany. Have you sharpened or honed the cutters on either tool, and if so, how did you go about it? I don’t want to mess up the geometry, but I think the quality of the cut could be improved. Thanks.
I have only stropped it, like a carving tool. I’m sure the honing helps. What seems to help the most is using a fine-grain wood (such as maple) and soaking it overnight in linseed oil.
If it’s consistent on one side of the edge, it is probably a body position issue. Try taking a step toward or away from the board.