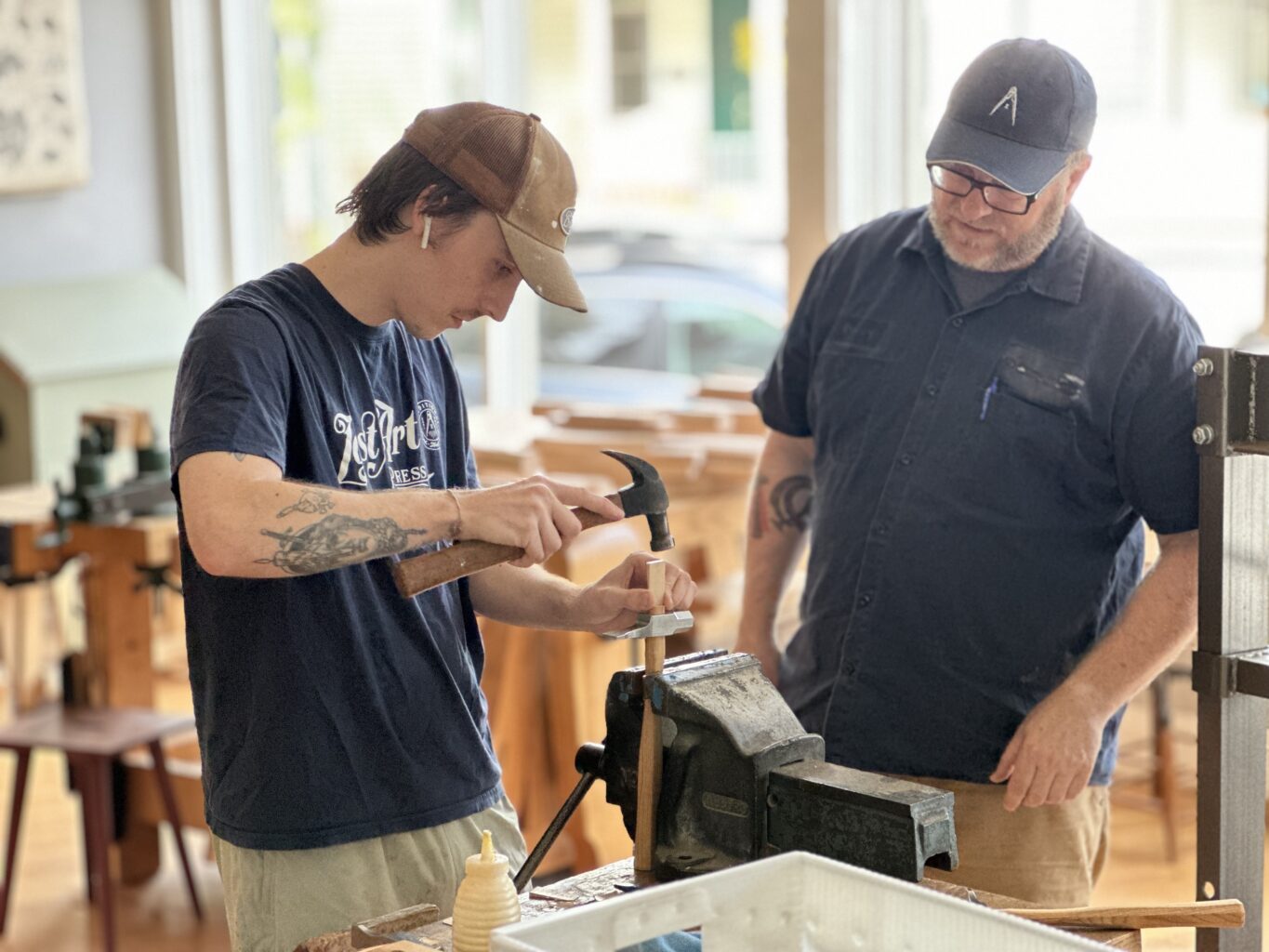
Update: Comments are now closed (if there are questions we’ve missed, we’ll jump into the backend to answer later). Join us again on Oct. 19.
Do you have a woodworking question in need of an answer? Then you’ve come to the right place! Just post your question in the comments section below, and Christopher Schwarz and I shall do our best to answer. As always, brevity is appreciated. We’ll be online on and off today until around 5 p.m., at which time comments will close.
And mark your calendars for the remaining 2024 Open Wire days: October 19, November 16 and December 14. Plus, our holiday Open House on Saturday, Nov. 23, featuring special guest Rudy Everts!
– Fitz
A steaming question: I steamed some (southern) red oak legs and back slats for a chair. After the pieces were out of the steamer and dried, most of them had a blue/green tinge to them. What would cause this? Luckily, this sanded off mostly, and I was ebonizing the oak anyway.
No clue. Could be something in the wood, the water or in the vessel you used to steam it. I’ve gotten black streaks (from iron in the water), but not blue/green. Sorry I’m no help.
Good morning!
I’m building several tack boxes for a group of young riders. Wondering what you recommend in terms of finish. I’ve suggested paint, but some in the group really prefer the look of stain. If I do go the stain route, what sort of protective coat would you recommend. I’m using a modified ATC design, and I don’t expect them to be in direct bad weather, but they will live in unconditioned barn, get banged around, and occasionally probably get a few raindrops when being moved (hence why I’ve pushed the paint).
Thanks in advance!
Any sort of film finish will degrade and craze and look bad pretty fast (except for marine varnish, which is expensive). I would opt for an oil/wax finish, which you can refresh/repair in the future with simply more oil/wax. If they really want a film finish, a transparent deck stain would be my choice.
What is the meaning of the symbol, which looks like the letter “E” in the modern English alphabet or maybe the uppercase symbol for sigma, Σ, in the Greek alphabet, in between the divider legs in the logo on the Lost Art Press Ball Cap?
The divider in our logo are from Joseph Moxon’s “Mechanick Exercises.” In the book, dividers are Fig. E.
No mystic symbolism. We’re not that bright.
Good morning everyone,
The topic is soft wax 2.0 and I made a batch using the volume measuring method and that worked okay (maybe luck) so I tried using the weight measuring method. I was careful with the temperature and when the batch cooled, there was maybe 5% of the linseed oil that separated from the wax. Food grade linseed oil, pure beeswax and limonene. Is this a simple case of “I added too much linseed oil?”. Can I re-heat the mix and add more beeswax?
You can reheat it and add a little more wax. Or, if the soft wax is the consistency you like, pour off the excess oil. Or just use the stuff. A little extra oil won’t hurt anything.
I have a suggestion for your Roman bench build video, include more information on using the power tenon cutter. I struggled centering the leg tenons and afterwards found two helpful videos on the blog that I wish I had seen before tenoning the legs. Otherwise the video was great.
Thanks. Glad you found the other videos.
When making long sticks with a rounding plane or Veritas Dowel Maker, how do you approach fitting the sticks to the comb and planing down the untouched octagonal section into a nice entasis? And for the rounding plane, do you have to use the rounding plane for the tenons on the short sticks too, so the sizes match, or you try to match the power tenon cutter to the size that comes out of the rounding plane?
Long sticks
1. Run them through the rounding plane, leaving the bottom 10″ octagonal.
2. Tenon the bottom of the stick with a 5/8″ tenon cutter.
3. Double-taper the octagonal section to the round sections. Clean up the marks from the rounding plane. All with a block plane.
4. Live with the tenon size at the top of the stick. Waller out the mortise sin the comb if necessary. Peg the comb in place.
Short sticks
1. Tenon both ends with a tenon cutter.
2. Double-taper the octagonal section to the tenon shoulders with a block plane.
What battery powered drill do use for drilling leg mortises? My older 18v Makita started smoking when I drilled a 2 3/4″ ash slab (had to switch to brace and bit). Also any suggestions for settings on the drill?
We use the DeWalt 20v drills that are USA made (the model number keeps changing). With Wood Owl augers, we can drill through anything we’ve encountered without a problem. Speed 1, clutch off.
Before I found the DeWalts (thanks Klaus!), we used a corded Milwaukee Hole Shooter, USA made, that is fantastic.
Any thoughts on the stop-loss bags they sell at lee valley for keeping finishes in air-free environment(rather than a jar or can)?
I’m making my first batch of piggly no wiggly glue and I was thinking about storing them in bags rather than bottles so I might keep them at room temperature rather than the fridge.
Anything that prevents them from being exposed to micro organisms will work.
Will you be taking donations soon for your beginner classes? Need tools?
We don’t have another beginner class coming up, I’m afraid. Next year Jerome is going to teach a class here and shoot a video. But it won’t be a scholarship class.
Hey team LAP, I hope to be saved from some remarkable ineptitude. In making my second Drinking Table (The Anarchist’s Design Book, Expanded Edition), my first was in pine and went so well I was overconfident, I glued the cherry top to the subtop and I didn’t get 100% adhesion. I did all the stock prep and surfacing by hand but had difficulty getting the mating surfaces perfectly flush along one quarter of the round. It was close, some days the shop climate was such that is was very close and on other days a slightly larger gap. Always close and closable with pressure so one close day I said heck the what and glued it up using five cauls to clamp them together tight. I left it for a day and upon releasing the clamps my gap was there, smaller area but still there. I probed it with a piece of paper and to my dismay an entire 8×11 sheet fit in that one area. I sense the rest of the top is solid as a rock but this seems like too much for a staked table. What glue did I use, you ask hoping for reversible hide glue? Well, my Piggly No Wiggly was literally in the mail, arrived yesterday, when I impatiently decided to glue up the table with Titebond 3.
Am I lost? Would somehow injecting epoxy glue work? I suspect both mating surfaces are covered with a thin coat of dry Titebond. How to get any glue in such a tight space? Gasp, screws!
I wouldn’t be surprised if you have never encountered this display of woodworking mastery but would love your thoughts. It’s a lot of expensive cherry and time invested so far.
Chris’s answer will likely be different. But I, a philistine, would try to work some more glue in the gap (perhaps with dental floss, and hoping there is some bare wood for it to grab) then clamp the snot out of it, drill pilot holes, and run a few countersunk screws (as long as possible without going through) in from underneath – and maybe use slot screws, and step them out with dividers so it looks like it was the intention all along. (Just don’t put any where the leg mortises will go.) Oh – and strip any zinc from the screws first so they look old.
I would probably not worry too much about the glue. There is likely enough surface contact between the two boards to keep things together. You certainly don’t need 100 percent. I’d drive some screws throught the two boards for insurance and then get on with it.
So I was curious about the origin of the term marriage marks. I checked Roubo’s text that refers to plate 11 and found no descriptors, just a reference to the drawing. Is the origin of the term marriage marks from Lost Art Press or does it come from some obscure French text? Thank you.
I don’t know the origin of that specific term – but it certainly predates LAP. I’ve also seen them called timber marks, assembly marks, witness marks, carpenter’s marks…They all mean the same thing: put these together.
Do you have a recommendation for a book about building beds? I’m interested in something with a headboard and footboard, rather than the platform bed in ADB. Thanks as always for the time you put into this!
I am also thinking about making a bed – designing it myself, but consulted this book to figure out bed rails and the like: Jeff Miller’s “Beds: Outstanding Projects from One of America’s Best Craftsmen” (Taunton) – there are plenty of secondhand copies available. Fine WW has also printed some nice bed articles through the years.
When using the rivière nails are you using tapered or straight bits for the pilot hole?
Ideally, tapered bits. But I usually just use straight ones, and drill a larger hole (a clearance hole) in the top board if it’s near an end. As always, test the setup on like assemblies and wood if you’re not sure!
What’s the shade of nail varnish I’ve noticed you sporting recently in the English tool box videos? Very fetching!
I believe it is Troll Whisper Purple
When I got my shapton karamaku stone set I decided to splurge and get the 12000 yellow stone instead of the 8000 green. Chris I noticed in your sharpen this video series you said you like the green better. I was just wondering what makes the green better than yellow. Thanks!
The yellow doesn’t cut to my satisfaction. If you are happy, I am happy.
Question: Why did my flush cut saw and putty knife tarnish and the redwood get black streaks and splotches?
Background:
Wednesday – Assemble redwood Japanese tool chest (sides, bottom, ends) with hide glue and wood nails.
Friday – Using hot water, rags, putty knife and flush cut saw, disassemble Japanese tool chest because I made an error in the assembly process.
Observations: 1) disassembly is challenging even when using hide glue, 2) it’s easier to do things right the first time than to fix stuff, 3) I might learn more fixing mistakes than when everything goes right.
Redwood is rich in tannic acid, like many oaks. The acid reacts with the steel to make the black streaks.
Odd finishing question. The front of our house faces the rising sun and the finish needs a refresh (hopefully not a sand down and start over…). Suggestions ? it’s a pretty large door with an arched top that is a dark cherry shade.
(Fully expecting to hear take the door off, strip / sand and start over but hoping for something different :-))
It depends on what the current finish is. Bob Flexner has written numerous times that marine varnish is the most protective clearcoat for UV rays…but nothing withstands sun and water for very long. I think your expectation is correct, as it’s likely a film finish: sand and start over. On the LAP front door, we’ve been using linseed oil, over which you can simply add more. But it really ought to be recoated more often than we do it, which is maybe every 9 months to a year? Every6 months would be a lot better… And I guess I know what I’m doing one day next week!
You have suggested using interlocking grain wood such as elm for chair seats to reduce the chance of splitting. Elm is not really available on the west coast. What other domestic woods have interlocking grain?
Poplar and sycamore (London plane) are other options. Mahogany and many of the African variants. (Many tropical hardwoods are interlocked.)
The live oak we have in central Texas has crazy interlocked grain.
Good morning!
I have more of a request than a question. For a future Stick Chair Journal would you feature building a chair like the one you made from old mahogany utilizing sliding dovetails because the seat was too thin? The lines of that chair looked great. It looked really balanced. With the sliding dovetails I thought it might be a good one for the Journal. I’m sure I am not the only one that might like to make one.
Here’s a link to the chair I’m talking about. https://blog.lostartpress.com/2024/08/19/for-sale-comb-back-stick-chair-in-old-mahogany/
I hope you will consider it and thanks in advance!
Patrick
The chair on the cover uses battens and sliding dovetails for the seat. All I did was take that chair below the seat and made the top of the chair a comb-back stick chair.
We will definitely cover different options for making that joint in the future. There is a German plane that makes the dog tail part on the battens. That makes the joint easier.
When fabricating octagon legs, do you use chamfer guides on a plane or spokeshave?
Just a jack plane.
Good morning,
Do you have any experience with the Dubuque aluminum sash clamps? I’m looking to add a few clamps to my arsenal and debating between those and parallel clamps.
Thanks,
Tom
We have a set, and I’ve used them for many years in other shops. They are great clamps. But you will still need some heavy duty clamps if you’re gonna do any heavy duty woodwork, such as building a workbench top.
I recently built the Roman low bench and find it too low for a saw bench at 17″. What’s the best way to remove the legs so I can replace them? I used Old Brown Glue and was thinking drill some of the tenon out, mostly because of the wedges, and then wet them well and try to drive them out.
That sounds like a good plan to me
Are folded backsaws worth the upgrade over a glued in or slotted backsaws such as Lie Nielsen?
Here’s how I see it: With folded-back backsaws, the sawplate is much more likely to slip. But the repair is simple. With glued, the sawplate is less likely to slip (I’ve never had one slip, and my LN dovetail saw is 25 years old.) But the repair is more involved.
Choose your poison.
Thank you Megan. Seems like a project I need to get on my calendar..
Question for Megan because I can’t wait for her book: when fitting a dadoed shelf into a carcase that has a dovetailed shelf on one end (like the DTC), the length of the dadoed shelf obviously has to be just right. I can figure this by measuring interior of the dovetailed shelf and adding the dado depths to it t, but your DTC article in FWW suggests I can do something more direct. You wrote that I can “[m]ark the length off the dado bottoms with the carcase dry fitted.” Can you explain that?
Sure – do a full dry assembly and pull it tight with clamps. Make sure the sides are square to the bottom (and if they are not, you can clamp a square block in each corner to make them so). Then use pinch rods to get the exact length from dado bottom to dado bottom. BUT, it’s not the end of the world if the shelf is a hair short; you can use the backboards and nailed-on front to square things up.
I’ve been thinking about dovetailed chests and layout. Is there a certain minimal number of tails per a length. For instance, the ATC has about 12 tails in 24″. Can I go fewer in a similar height? There has to be a point at which there isn’t enough grip strength. It seems most of the historic chests have a lot of dovetails. Maybe it was the style of the time? Maybe they were showing off? Maybe experience had shown them how many were needed and the ones that didn’t did survive?
In ATC classes, we now cut 7 tails per corner. That’s plenty. I don’t know if there’s a “rule” as to how many per X board width, but I typically go by eye (an eye that’s seen a lot of dovetails). Across a 12″-wide tool chest (e.g. the DTC), I usually go with 4 tails. But if I were making a 12″ wide fancy box, I’d probably do more, and use smaller pins.
There are no hard and fast rules. Eastern European countries preferred tails and pins that were equal in width. Some 15th century Italian chests have the skinniest pins you’ve ever seen. I encourage people to page through Mark’s old blog (RIP Mark).
https://thefurniturerecord.wordpress.com/
Mark made a habit of recording the dovetails he encountered in the wild. It will train your eye as to what you like. And what is possible.
I wanted to say thanks! Finished my ATC after asking many questions on Open Wire. It was a ton of fun. Any chance you guys will do more patches like the stick chair patch for other projects? Fun way to spruce up the shop apron.
Those patches cost us about $400 to $500 per batch. They are great fun, and we like them. But we have to have Stupid Money on hand to do them.
Right now is not Stupid Money time.
I had this happen to me. I remelted it and stirred it periodically as it cooled to reincorporate the oil that was floating out.
What is your favorite material for making the templates you use in your chair making video?
We use 5mm underlayment plywood from the home center. We have a lot of scraps of it from making crates. If I were persnickety, I’d use hardboard, which doesn’t warp like the underlayment.
Workbench Question … I want a bench from my tree from my home. It is a maple variety – and I found someone in my county who will mill it for me for drying. It is likely hard maple, but I have to find the book to identify if the tree was hard vs. soft maple. I still have my giant silver maple, so I think this one is the hard maple variety. I think it is about 24″ diameter right now including its bark. Is it an absolute necessity for workbenches to be glued in multiple pieces, or can I have a slab 3 pieces for my bench top. I have the Anarchists Workbench somewhere from 2020 purchase, but can’t locate it… is this covered in the book, slab vs. multiple strips of wood cut up? I want to get my tree milled before he changes his mind. Is the reason we don’t slab a bench top is for stability? or due to the cost of wood? I vaguely remember a post from LAP where large slabs were sourced and posted on line, so I think a large slab was an option for a workbench.
Off to find those workbench book from LAP…. I can find the other books – just not this one.
Thanks – Tamra
P.S. Thank you for keeping my LAP purchase history for me.
Slab benches were once the norm. We have one that I made from 6″-thick oak. The downside to a slab bench is that it takes a long time for the wood to dry. Much longer than one would think. Even when we got the bench close to equilibrium moisture content, it still had a lot of moving to do. About four years after that, it stopped moving and is wonderfully stable.
So yes, you can do it. I love my slab bench. But you have to be patient.
I bought a 90s era 12” cast iron jointer that I later discovered has a 0.5 mm (about 20 thou) hump on both the infeed and outfeed tables, parallel to the cutterhead and starting right next it. Doesn’t sound like a lot, but with a jointer my gut says it could well be a problem, and any error could accumulate when combining components.
I’m thinking of using a belt sander to take out the majority (checking often with a precision steel straightedge and feeler gauges) and finish with a square of thick 12×12” plate glass that I’ll spray glue sandpaper onto. The tables are individually adjustable with bolts on the underside to be parallel.
Does this sound reasonable? I’ve contacted a couple of local metalworking places about them using their CNC to flatten the tables instead, but they’ve said they’re unable to secure them to the machine table. Or am I wrong in thinking this hump will be an issue?
Might not strictly be in your wheelhouse, but you have a lot more experience with jointers than I do…
I would use the jointer first to see if it will produce flat and true surfaces. I have yet to find a problem with a cast iron machine top that affected the cut.
I probably wouldn’t feel skilled enough to use a belt sander on a top, though it could totally work. I would first try carbide machinist scrapers to scrape the hump out.
But I am not much of a metalworker.
What’s your favorite cereal; Lucky Charms, Special K, or Cookie Crisp?
Raisin Bran
gross
I haven’t eated cereal since I was a kid. I liked Crunch Berries and a weird granola cereal that came in a plain brown wrapper.
Good afternoon. I am building my second real furniture project, a hobbit(ish) chair from Ash and I was wondering if you had any advice for drilling the leg mortises. I’m struggling with boring the holes. I have tried new Irwin stubby augers, they won’t cut crap even in a corded drill. I have a 1″ Auger for a drill brace, that’s hard going though and its a type of auger that doesn’t have spurs (a French? design). A spade bit has wielded the best test result, but I wasn’t expecting drilling holes to be this hard. In my tests I have drilled a 3mm pilot hold at 23 degrees that I am expecting to pull an auger through with. I will be sharpening things and testing again before I go hog wild on the actual seat but is there anything else to try? Any help is always appreciated, thank you.
Wood Owl Smooth-cut augers. The best. Period. That’s what we have always used for leg mortises in chair seats. They cut cleanly, quickly and with surprisingly little effort.
Was it for a special occasion or a regular thing?
Tool chests
The launch of your new video series got me thinking.
Dutch
English
Swedish
Anarchist
Japanese
(have I forgotten any?)
They obviously each have different aesthetics but are there any other ways you would distinguish between them? eg Dutch & Anarchist for use in your workshop, Swedish & Japanese for travelling
Thanks
I use the Dutch for travel, in the shop (at LAP and at home), I have my tools in an ATC. I can pick up my DTC when it’s fully loaded (though not easily these days) and get it in my car. I suppose: if you can get your arms around it, it’s great for site work. If you can’t, it stays home.
Do you have a ballpark for what sizes of Lee Valley’s tapered drill bits would work best with their cut nails? I did some testing with straight holes, stepped by using 2 different bit sizes, and was amazed how big a pilot hole I needed to avoid splitting the wood. It’s oak salvaged from an old dining table, so it’s had a hard life already…
Thanks!
Here’s a post from Chris that will be a good starting point. But in short, for the pilot, match the bit size to the tip of the nail. BUT TEST IT!! In splitty wood, especially out at the end of a board, a clearance hole on the top board is sometimes needed. https://blog.lostartpress.com/2015/07/11/the-bare-bones-basics-of-nail-technology/
In my humble opinion, any well-made tool that has the potential of being properly repaired without serious professional machinery (like folded backsaws) are worth extra expense. It’s one of the reasons why I bought Bad Axe backsaws instead of Lie-Nielsen backsaws. (I emailed Lie-Nielsen about how to fix their saws if an errant stroke kinked the plate and the answer was—you should send it back to us. If you needed ever to straighten the plate, I would follow Bad Axe’s instructions. Rob Cosman has in past bent his Lie-Nielsen backsaws (including the back) to get the plate straight again but I wouldn’t hazard that.)
Good morning, all, I wanted to ask your thoughts on the comparison of the Arkansas stones (soft, hard and Black) compared to the Shapton pro stones (Kuromaku series)? the Arkansas to me seam to take longer to sharpen if the tool really has to be worked back into shape. The pro stones seam to cut faster but have to be flattened a lot. I have them both.
You have them pegged. The only other big difference is the surfactant. Some people don’t like water on their tools. Some people don’t like oil spashing on their wood components. Another small difference: A set of oilstones will last a couple lifetimes in a pro shop. Shaptons…. I get about a decade from a set.
Although I understand and appreciate others’ affection for water stones (especially the Kuromaku that Chris uses), they require consistent maintenance if you want to keep them flat, too much for my preference. (They also are messier to use than I prefer.) As an Arkansas oilstone user, if I find I need to work a old or damaged blade (including the back) into shape, I either go to my hand-cranked grinding friable wheel (80 grit) for the bevel or, for the back, I put a low-grit of sandpaper (down to 80 if the pitting or damage is serious) on perfectly flat float glass (easily and cheaply purchased) and move up from there. One just has to figure out what grit stones or paper to use to remove the least amount of material the quickest to get the blade into a workable shape. (At least that’s what I try to do.) I also am very careful to clean my oilstones as I work (when the oil is becoming black when I wipe the stone with my finger, I wipe off the stone and reapply a couple of drops of fresh oil so as not to chance clogging the stone with swarf). If I choose the right grit, it doesn’t usually take me that long. Longer than waterstones perhaps but not too long.
LOL, me too.
Thank you!
Is there any disadvantage to using an adjustable double square instead of a 6” combination square? Besides the 45 degree angle, they seem very similar, but not nearly as popular. Thanks!
My double square has a 4″ blade, at the risk of sounding rude, sometimes, that extra 2″ in a 6″ square is nice to have. Otherwise, not that I can think of. (Other than the 45°, as you note.)
I can’t think of any other difference that matters. I use the 45° side all the time.
Last night I was slicing celery lengthwise and found myself thinking “I need a celery froe.” Am I ok?
I have not found that celery splits along the grain.
I’d worry only if you then dried the celery and made chairs from it.
Can you share some details on how you apply black wax to your brass tools? I have an older center square that I was going to apply some wax too.
Thanks!
We wipe it in with a huck towel and wipe until most of the excess on the surface is gone. Wait three hours. Buff with a clean towel to remove the excess on the non-engraved areas. We are using Liberon Special Effects Wax in Black.
Other than Peter Follansbee, do y’all know of any other woodworker who froes and then shapes wooden boards with axes? I can sometimes get hardwoods from local backwood sawyers but it’s hit or miss with the quality and variety (I have also had some trees of my own sawn up, the wood drying in the barn), so I’m trying to split and shape the planks out of some harvested trees from our farm. I’d love to ask about techniques to speed up the process of working the boards with axes. Maybe the technique is simply what I see Follansbee does on his videos but I was wondering if there may be different techniques with different woods (as there are with planing different woods). (I have several kinds of axes, including the German winged one with a bent handle preferred by Follansbee, which I had to get all the way from Slovenia.) Unfortunately, I can’t be as choosy as Follansbee and get the perfect oak log.` Thank you! Hope all is well in Covington.
Check out these two guys:
https://www.instagram.com/alex_walshaw_/
https://www.instagram.com/alexandr_pakhotin/
Also, these videos might give you some ideas:
https://acsoltlada.hu/index_en.html
Thank you very much! These are great!
I’ve found that the stop loss bag gets quite nasty fairly quickly. Sticky, aperture is too small, hard to fill up, small cap. A good idea, in theory…
Good morning, Chris and Megan,
In the American peasant book, you have that recipe for beeswax linseed oil and citrus solvent that you have extensively blogged about elsewhere. How full does the container get that you suggest for specific volumes mentioned in the book? I ask because as a chemist, I tend to worry about containers being over full. if you have a rough idea of the percent full for the container that’s listed in the book that would be greatly appreciated. Thank you for all that you both do. Hope all is well. Sincerely, Joe.
I make a batch in a quart paint can. That leaves plenty of room.
Thanks for the response, I can see that happening with the set’s that I have. I use mineral oil (food grade) on the oil stones, and it can get a little messy, so I purchased another boot tray just for them. I use Honerite Gold in my water which helps with corrosion on the tools. Both sets of stones are great, As always thanks LAP for your expertise and input.
Good morning Megan. How did you end up liking that Benjamin Moore Americana paint?
I like it just fine. The sheen is a bit more flat than the matte, when both are fresh. But I don’t notice much sheen difference between my 6-year old matte coat and the now 6-week (I think?) flat old coat, other than the color.
Hi Megan, Do you have any tool chest classes planned for Port Townsend? Thanks.
Not for 2025. (I’m in need of a little less travel next year.)
FYI, the Port Townsend School of Woodworking within the last two weeks released their 2025 schedule of classes.
Is there a reason other than aesthetics for the 1″ tenons on the Gibson chair sticks vs 3/4″ tenons on the irish curved back sticks?
Either will work. The arms for the curved-back chair are narrower than the Gibson’s. So the 3/4″ looks right-er.
Got an old Delta 14″ bandsaw over winter, replaced the belt with a Power Twist V-Link, and got to work all spring no issues. Then this summer after sitting for a few months, found the belt loose enough that the saw bogged down in 3/4″ cherry at times. Took three links out and it’s back to sawing through 4″ oak without an issue. Do I need to add those three links back in when the weather gets cold again or did it just take months for the belt to stretch out a bit?
I don’t know if the belt stretched. Or the screws that hold the motor in tension loosed up and let the motor slide a bit. Might check.
No, it’s not a seasonal thing.
Found Chris’s plans for the folding book stand and made six of them as gifts. It was a fun little project to use up some scrap.
Hi,
I’m in the process of inlaying some abalone shell in a piece of mahogany. What glue would you suggest?
Sorry but I have no clue. I’ve never done that sort of work.
I got a 9′ slab of white oak three years ago. Adjusting for three years of cupping and twisting left me with a flatter and stabler — but thinner — slab. Is 3.75″ or so too thin for a Roubo that will last?
Nope. Should be fine!
You reference the use of yellow pine in several of your publications. I live on southeastern Arizona at the northern edge of the Sonoran desert and I cannot find yellow pine. However, I have found sugar pine. Are you familiar with sugar pine and do you consider a good substitute for yellow pine? Thanks
Sugar pine is great for lightweight projects and for interiors of case pieces. But not for workbenches. Look for Douglas fir or hemlock. Basically whatever the construction industry in your area uses for joists.
Thank you. I can find Douglas Fir
Appreciate
Hi!
You’ve mentioned in a few places that a plane can be used to reliably straighten a piece of work that is twice as long as its sole.
Does that mean if the work is shorter than twice the length of your jack plane, there’s no real advantage to using a jointer plane? Or is it still useful, but just not critical?
Thanks for doing these!
If I am flattening/straightening a board, I use a jointer plane. When the board gets longer that 48″, it becomes a challenge. Anything smaller is cake for the jointer.
And if I don’t have a jointer on hand, I know I can flatten 18″-long boards with my 9″-long smoother.
Hope this makes sense.
Totally! Thanks!
I want to build a 5 board bench as per ADB but I want it to live outside. It will be exposed to rain and snow. I assume cut nails will not survive. What’s the best option? Stainless wire nails? Just PU? Dominoes and PU?
Copper boat nails. White oak wooden pegs. Stainless screws. You’ll sometimes find stainless cut nails on eBay (we have some that were made in West Va.).
If I go for oak pegs, am i making fox-wedged trenails, or am i overthinking it? Also. I should not apply any glue to the crossgrain joints if outdoors…too much movement under those conditions. Correct?
I’d make tapered pegs. Tapered holes. I don’t see a problem with glue. A type II or III PVA had a lot of flexibility. And humidity swings outdoors are not as dramatic as they are indoors (thank you forced air heat and air con).
I’ve been prepping stock for some small picture frames. The kind where small pieces of wood have magnets embedded and pinch the top and bottom of the picture (see example linked below).
My stock is 9 1/2″ x 1/2″ and 1/4″ thick. It is all a bit bowed. I want the corresponding pieces to fit together snuggly. I tried planing them but they flex flat with the pressure of the plane and then spring back to bowed.
I tried supporting the bow with a tiny shim while planing, but it didn’t really work. I also tried rubbing them against sandpaper on a flat surface, but it was hard to get them to sand evenly. I ended up spot sanding to finesse them into kind of fitting together nicely.
Do you have any good techniques for getting thin stock like this nice and flat?
Example: https://www.amazon.com/Artmag-Magnetic-Artwork-Hangers-Hanging/dp/B07QS44BWQ/ref=sr_1_2_sspa?crid=GXP1NE0UU91F&dib=eyJ2IjoiMSJ9.ofpijGYL5iRFp8oYu-4IfUmazUuXVFUXZgESdQuCVRc97otEPtl1nMoMDXOY0T8_Bg9MqiOvzIuqVrKGStRh3zRgAaycaKa2Sae25ZT1bF1lbXMkHUHWXplsPtue_HhZeeDp2GfXfh6elw9rSt2hyJWnpOR250SQ31se3JyNNsVjgIlDUdt2y102nREP7PtapLO-MVuE7QkdWnPiMeEQzmx45gWmYLna_5z_sqsRI_fq_bPGz-DdhmimacgNNdXcANSHlBQjwcykufbl8qqCz1yDjDUUhaFsHto39TrgZ9k.lspQsrSzmVnorPmZBaQ9oV0eF5OoLDgGLhZswD1U0ok&dib_tag=se&keywords=magnetic%2Bpicture%2Bframe&qid=1726338263&sprefix=magnetic%2Bpicture%2Bfram%2Caps%2C128&sr=8-2-spons&sp_csd=d2lkZ2V0TmFtZT1zcF9hdGY&th=1
Getting the bowing out of thin pieces can be folly (because of the things you mentioned). Usually it’s faster and easier to prepare some more stock that is flatter.
But if you do want to try to salvage what you have, here’s what I would do.
Sometimes it’s futile because the planing will release tension in the board, making it bow as you work it.
The best bet is to start with a very stable wood that is quartersawn and dry.
Working with thin stock is tricky!
Any plans to make designs for baby furniture? Or is it a risky proposition given how strict safety regulations for children’s furniture are?
Because the regulations change constantly, I think we’ll leave that to the furniture manufacturers who employ lawyers.
Any news on the shepherd’s table you made at the beginning of the American peasant blog?
Thanks Megan!
Maybe I was just missing the obvious in that article – start with the tapered bit that matches the cut nail’s tip and then go from there? It’d be nice if Lee Valley had a reference to the sizes at both ends of the taper, I’ve got a couple of tapered bits in the mail based on best-guesses.
I think there would be too much variation for the right pilot hole for every nail size. The wood, how close it is to an end, softwood v hardwood…all these can affect the answer. But tell me what size nail and I can give you a starting point.
I have been making and using soft wax and I really like it, thank you for the recipe. How worried do I need to be about combustion from the rags because of the oil content? Thanks
We err on the side of caution. Let the rags dry flat on the edge of a garbage can for 24 hours. Then we launder them to reuse. Spontaneous comunsion of drying oils is uncommon but not unheard of.
Hi, Chris! How do you decide what the rough weight limit is on your chairs? I have a lot of poplar I can use for sticks and I’m wondering how they’ll fare against the cherry and oak that’s usually used in those chair parts. I know your rule of thumb is to add 1/8″ thickness to increase strength when using weaker wood species. Is that just for sticks, or also for legs? (Say yellow pine or doug fir for legs instead of cherry or oak.) Thanks!
Usually it’s like a carnival ride. If the sitter can fit, the chair will almost surely be fine. For a comb-back, that’s going to be about 260 lbs.
I’ve had 360 pound people sit in my Gibson chairs (no stretchers!) with no problem. I made a chair called Stoutback Chair (on my American Peasant substack) that explores this issue. I bumped up the sticks, stretchers, legs and arms by 1/8″. Increased the seat width. And it worked great.
I’m curious to the LAP’s thoughts from a preservation perspective on how to pick materials when reproducing work from the past? Some great options out there but they’re often frowned upon or simply not allowed by local historic societies/alliances, especially on the grant-funded historic millwork side. Catch-22!
Any guidance/thoughts are so appreciated.
This is way out of my area of expertise, I’m afraid. I have made only two historic reproductions in my career, and the the organization was happy if I used modern kiln-dried lumber.
People who have worked for the Park Service or other museums would have a better perspective, such as Bob Van Dyke or Peter Follansbee. Sorry.
Hi. What is your procedure and or how do you apply paint into engraved letters/numbers/graduation marks on a metal square or metal ruler etc. that has lost it original paint in those characters?
A black wax such as Liberon Special Effects Black wax will work. Rub it into the engravings and try to get most of the excess off. Let it dry three hours. Buff off the remaining excess.
Curious for tenon saw recommendation. I’m in the market for a new one (made mistake of lending one out and…well….I’m in the market for a new one). I really like my other Bad Axe Saws, so I have might sights on either their standard 16 inch tenon saw or else their “fancy” one, which is a close replica of a Disston no. 9 (with the ogee bit in the front). I already know their saws are great, so I don’t need an endorsement of the company (for anybody reading, by the way, their saws are really great), but just wondering if you were going to choose one of the two for your tendons which you would chose and why? Also, if I can ask a bonus question….they like a “hybrid” filing, which I suspect means it’s hard to keep up at home. Better to stick with crosscut?
Thanks as always
I realize that I said “tendons” rather than tenons. While I have come close to severing several tendons, I’m interested in a saw that cuts tenons
I took a BA hybrid-filed saw on a trip recently, and have come to like it. Took a little getting used to, though. But I don’t sharpen my saws; I send them out (I have bad astigmatism – can’t see the small teeth!). So the maintenance doesn’t really factor in for me. But if I were buying a new tenon saw, I’d probably get a Lie-Nielsen. The price is good, and because I don’t care that the handle is a bit too big for me on a saw I’m not constantly using… (So why not the even less expensive Veritas you might ask? That handle is simply so thick that I can’t grasp it well enough to saw at all comfortably. It’s a personal problem.)
Sorry if this has been answered before. The when assembling the legs for the Anarchist Workbench, the mortises for the long stretchers are cut out. Why isn’t the same thing done for the leg tendons that fit into the benchtop?
You can do it that way. Aligning the two sets of mortises on the benchtop is tricky. Give it a go.
In the previous Open Wire, Megan asked about science fiction books with cats. I was too late to respond, so I’m doing it now. My wife and I highly recommend John Scalzi’s “Starter Villain.”
Public Service Announcement: Chris posted several months ago that Highland Woodworking was selling the discontinued Rikon 10″ bandsaw 10-305 for $299. The Schwarz Effect caused them to be sold out the next day. Menards still has these in their warehouse and I picked up one for $274 with the rebate and I didn’t have to ship it (although shipping is available if you do not live near a Menards). So, there may still be an opportunity to get it.
He’s right! Our Menards even has them in stock. Highly recommended
https://www.menards.com/main/tools/power-tools/power-saws/band-saws/rikon-reg-10-band-saw/10-305/p-1444452321111-c-1537277164161.htm?exp=false
Chris, Megan & Co., I have the 1000, 5000, and 8000 grit Shapton pro stones (Chris’ preferred version). They work lovely. But I’d like to add a course stone for old tool rehab for which I don’t want to resort to powered bench grinder or belt sander. Reviews seem hit and miss on the course stones, but if you wanted to add a course Shapton, which would you consider? Thank you!
I’ve never seen Chris use a coarse stone. For flattening soles and the like, we use #80-grit belt sander paper adhered to a flat piece of granite or marble. And we use it relatively rarely, so it’s cost effective to simply replace the paper as needed. But I guess if ai had to get a stone, I’d get the Shapton #120 grit, as I like my 1k,5k and 8k, too.
I approve of this message. Belt sander paper and granite is better than a stone. WAY better.
Another PSA, this one mostly for Chris… are you aware that Kenji Lopez-Alt has a podcast (The Recipe)?
Yes. I wish I had time to listen to it!
Hello! Was wondering g what your preferred method is for cleaning up the backrest curves after it comes off the bandsaw especially on the taller backrests like for your Gibson chair?
I’ve tried a mix of osculating sanders, spoke shaves, and/or jack plane with mixed results.
My best process currently has been using a flexible 1/8” piece of ply with handholds glued on and some gnarly sand paper stuck to it to ride the curve. While effective, it isn’t terribly pleasant or fast.
Are there better ways?
Thanks!
A sanding “fid” – sandpaper (#120 then #180) wrapped over a piece of the cutout, is how Chris does it.
I actually start with #80 grit Abranet. Then #120. Then a scraper.