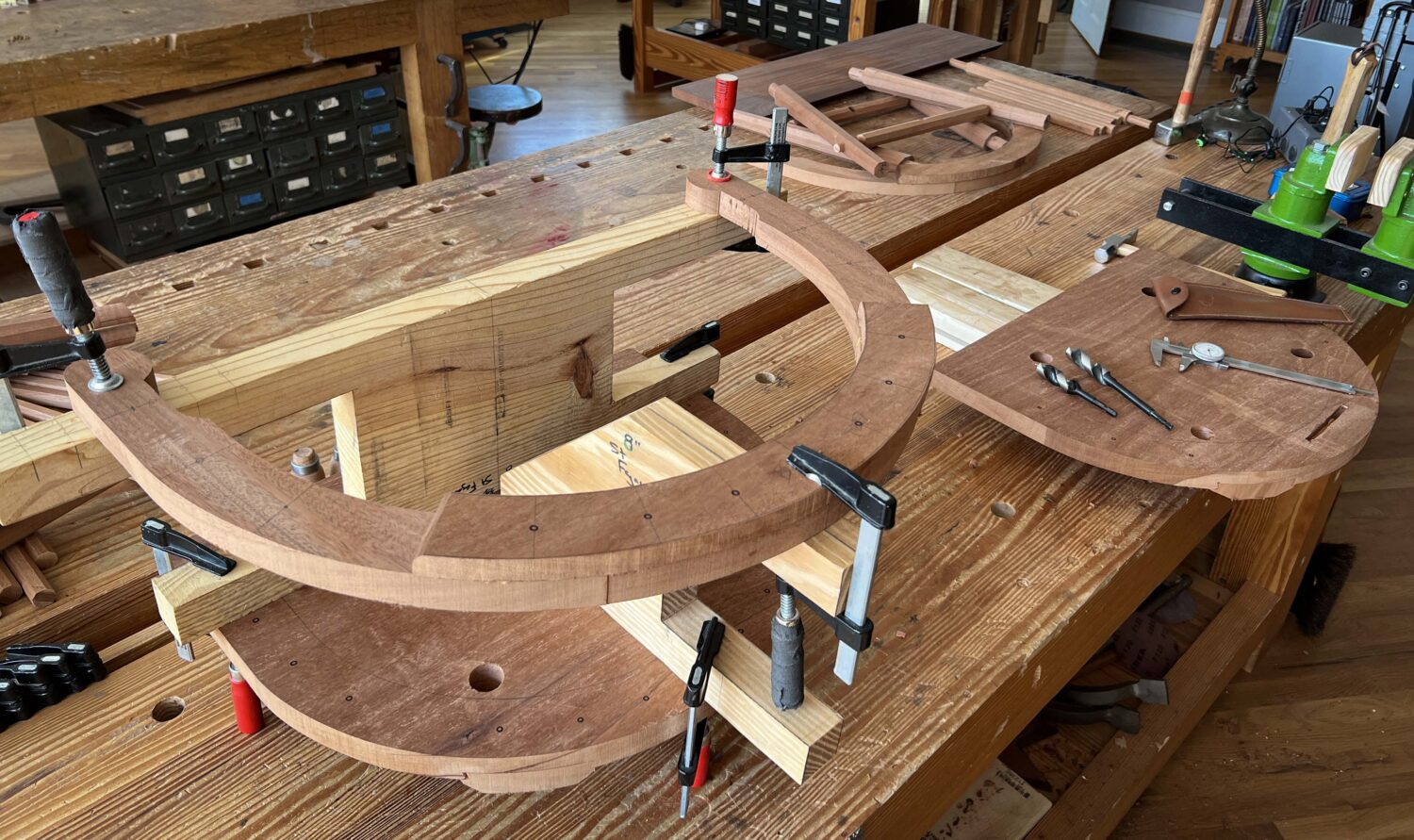
Update: Comments are now closed (We’ll respond shortly to any that are posted and not yet answered). Join us again for Open Wire on Sept. 14.
Chris and I are both working on projects in the shop today – but we’ve reserved time in between chairmaking and dovetails (and both – Chris’s current chair features battens secured in sliding dovetails) to answer your burning Open Wire questions.
You know the drill: Post your woodworking queries below in the comments, and we will answer – and it is much appreciated if you keep the questions succinct. Comments close at around 5 p.m. Eastern.
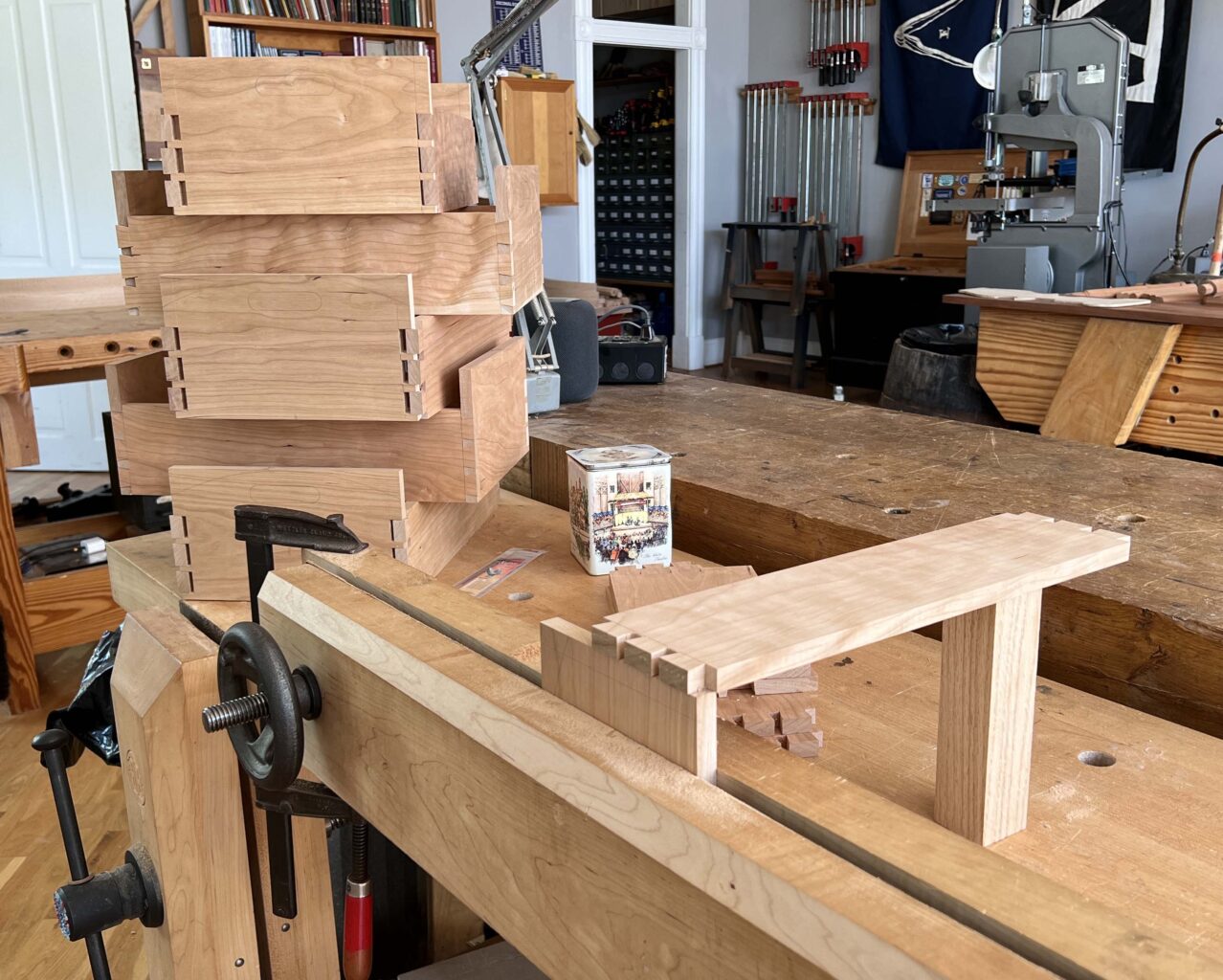
Do you do anything special to keep sunlight from changing the color of project parts during the course of a build, especially on that may go unfinished for a time?
I don’t. The layer of cells affected by UV is very thin. It can be handplaned off (if necessary) with a smooth plane set for a fine cut. I usually do thgat anyway right before assembly.
Your sources for the antique looking nails you use on your projects?
We use Rivierre forged nails mostly. They are French and can be purchased from Lee Valley Tools, Dictum and directly from the source.
https://forgednails.com/
We also use Tremont cut nails.
https://tremontnail.com/
Good morning and thank you again for hosting this.
A question for Megan. A few weeks ago I think you asked about ScienceFiction stories featuring cats. As far as I can recall no one mentioned The Game of Rat and Dragon by Cordwainer Smith. If you haven’t read it it is well worth a download from Project Gutenberg (www.gutenberg.org). I comes complete with the original illustrations from its first publication in Galaxy Magazine
I haven’t read that one –I’ll have a look!
Read it!
For that matter, read any of his work. It has an “epic classic literature” feel I think you’ll enjoy. He based some of his plots on ancient Chinese myth and literature.
–Liz, eternal novice woodworker, science fiction expert
Can Soft Wax go over shellac? I have a cherry table that I would like to add a little color with amber shellac but like the soft wax finish. How about over milk paint?
Thanks.
Shellac is film-building, so the oil won’t penetrate. If I were wanting to add wax to, say, adjust the sheen (dull it to more of a luster), I’d just use a paste wax. Or you can use the oil/wax, but it won’t look any different I don’t think than just buffed wax (’cause that’s all that will remain after buffing).
Milk paint, though – yes. But make sure it’s completely dry – like a week or more dry, not days, and test it first in an inconspicuous area (or better, do a test board if possible). I’ve found with blue milk paints, the oil in the oil/wax lifts out some of the pigment and makes it look a lot more green.
Soft wax contains a lot of oil. So it should be used on porous surfaces, such as raw wood or a milk paint or a stained or dyed surface.
On shellac, use a paste wax such as renaissance wax.
I am finishing out a space for a workshop. In the meantime, my tools will be exposed to varying temperatures and humidity swings. Any tips for minimizing rust or damage to hand tools in these conditions until I can run power and climate control the space? I am located in Kentucky and the humidity has consistently stayed between 70-80% for the last month or so. Thanks for in advance.
Wipe down the surfaces with a light oil. Then wrap them in VCI paper or VCI poly bags. That can keep them fresh for years.
In Campaign Furniture, you mention that Traveling Bookcases often featured wallpaper, felt, or cloth lining on the inside (I love the wallpaper on the bookcase you built, by the way). I haven’t been able to find any more examples of lined bookcases. Can you point me in the right direction? I’m looking for inspiration at the moment. Thanks!
I’m afraid I don’t have any examples in mind right now. Have you searched the archives at Christopher Clarke?
https://campaignfurniture.com/
That’s where most of the best pieces go.
I used linseed oil paint after having success twice before but this time had some flashing. Made the mistake of adding linseed oil (T&T Danish oil) too soon and it softened the paint and got rather gummy making it hard to get the very very thin coat I wanted. After two weeks of not drying I wiped it all off with mineral spirits. Any tips for evening the finish with linseed oil? Using Allback.
I’m afraid I haven’t yet found the magic formula for thinning the paint/thin coats (we’ve been busy with other stuff, so I’ve not painted anything in a while!). I know Heron Paints was trying to find a solution, too – but I don’t think they’ve found the magic bullet either, yet.
Sorry one more if you don’t mind. What are your favorite casters for an ATC? Don’t mind spending a little. Have tile floors. Thanks!!
I like vintage iron ones, like those often found here: https://www.instagram.com/iconicironandoddities/
But if you want a softer wheel, so as not to scratch up the tile, I’ve used these recently, and they seem nice: https://dhcasters.com/3-swivel-caster-w-brake-polyurethane-wheel.html (But I don’t have any long-term use to report)
I am very happy with Blickle casters on my ATC and several other mobile pieces. The company sells a vast variety of types and sizes. I usually combine two regular swivel casters and two swivel casters with total lock brakes. Only downside is the price.
I found 2 boxes of Tremont 8d clinch rosehead nails at a flea market. Can they be used in place of regular 8d nails or are only good for clinching applications?
I hope so…because I’ve used them a lot! (And nothing has yet exploded.)
Hi Chris. For the Bad Axe panel saw that you recently wrote about, what filing did you choose and what was the reasoning behind the choice? Thank you.
PS. I am guessing that the sliding dovetails mentioned above for your chair setup were done with that saw?
9 ppi crosscut. It’s the most common filing for furniture work.
Good Morning! I finally made it here, with one question.
I have a set of cherry Shaker dining chairs I made from kits, 25 years ago. [Shaker Workshops. They only sell maple now.] They all have tape woven seats. Several of the chairs have wobbly joints — alas! I knew no better and used PVA glue.
Chris said Miller dowels would be good for repair, but I never found details. Could Chris, Megan, or a Helpful Reader tell me a bit more about the process: where to drill, do I need to un-weave the seats, et c.?
Thanks!
I don’t use Miller Dowels to repair wobbly chairs. I usually use them to reinforce a tenon. For repairing wobbly chairs, the only fix I have found is disassembly and cleaning off the majority of the PVA. Don’t remove any wood. Then rough up the tenons with #120-grit sandpaper and reglue with PVA if the joints will go together tightly. If the joints are loose, you can glue shavings around the tenons to beef up the joints.
Sorry I don’t have an easy answer.
I have seen you have a veritas sharpening device ( with the platens and adhesive papers.) I use mine for lapping chisel and plane blades and I’m pretty happy with it, but I don’t think I have seen you do it—is there a down side I haven’t figured out yet or something to watch out for?
(Yes, yes, I know , it it works for me, use it, but I was curious)
We use it occasionally for grinding chores that require a lot of precision, especially for skewed plane blades. It allows us to easily jig up an operation and make it repeatable. I’m sure we could also do this on our dry grinder, but it’s mounted on a post (not a table) so jigging is no fun.
If anyone is looking for a new spoke pointer at a reasonable price you might want to try Pine Creek Industries – https://www.pinecreekindustries.com/wheelwright-tools. I just got one and it seems to work fine. The only caution is it that it is made for a electric drill or drill press and may not work in a brace because of the hexagonal shaft. Price is very reasonable at $38 for a 2 inch model.
Thank you for hosting. I submitted this question in the wrong blog/location a few minutes ago- sorry.
Is there a structural or design reason not to make a stick dinning room table with wedge tenons exposed on the top of dinning tables surface? Simply 4 legs and the top- similar to the base of your stick chairs. Some parameters I was considering 8/4 top 32” wide x 84” long (or shorter) with legs sized to hold the weight etc. I have not found many examples of this so i was wondering if table aprons or some other bracing is necessary for stability? Or am I missing some design/structural element that should also be considered?
Thank you
Staked tables were made like this for centuries in Europe, especially during the middle ages. Typically they would affix battens to the underside of the top to thicken the area where the tenons were. Check out “The Anarchist’s Design Book” (a free download here) for details.
I’m working on my first chair based on the book and videos which I’ve read. I’ve made a few live edge benches for practice using the tapered reamer and tenon like Chris demonstrates and have had good results. However, with my chair seat, the tops of the legs seem too small for the mortise. Should I not sweat it at this point and expect that once I scoop the seat and wedge the leg tenons they will expand enough to fill the mortises? For reference, I’m working from the chair plans the “Build a Stick Chair” video. Keep up the great, inspiring work—I hope to return to my hometown of Cincinnati for a chair class as soon as I can get enrolled in the next one!
Thanks,
Josh
I wouldn’t worry about an imperfect fit as long as the tenons seat. Usually the wedging process fills up any cosmetic gaps. You might want to glue and wedge a test joint in scrap to be sure. Sometimes the gap is caused by the reamer and the tapered tenon cutter not making the same shape.
Hi I can get really straight Australian hardwood dowels for stick chairs in 16mm (5/8”) or 19mm (3/4”). For a 6 stick chair would it be best to get the bigger size and trim them down? Or would the 16mm be OK? It’s my first chair and I am cheating a bit! I have made masts with hand tools so I know I can make round things….
We’ve made lots of chairs with 5/8″ (16mm) dowels. The only reason to use 3/4″ is if you want the beefy look.
Good Morning LAP,
I’m about to build my first Roorkee chair and I’m seeing some “evolution” in the dimensions from the original PW article (October, 2010) through my copy of Campaign Furniture and into (I think I recall) some blog posts. Particularly the thickness of the stretchers. I think the latest was to make them 1 7/16″ thick and leave them as octagons for maximum strength yet you warned making them too thick could be an aesthetic blunder (“elephant trunk instead of the sexy aardvark snout”). Is the 1 7/16″ MOL figure still stand as the recommendation? If so, did you have to expand the width of the leather seat material to accommodate the new (beefier) stretcher? Also, do you still recommend still using leather 7 or 8 ounces in weight?
Thanks in advance,
Brian
Hi Brian,
1-7/16″ octagons are still my recommendation. The leather sizes don’t have to change because of the adjustment. The leather weight is a bit of a variable. Some leathers at 7 ounces are fine. Some are too flimsy. It’s a bit of “you’ll know it when you feel it.” This is what I use now:
https://wickett-craig.com/leathers/oiled-latigo/
In the 8-10 ounce range. Fantastic stuff.
Marie from Old Town said they are ceasing production at the end of the year. Because of that they aren’t taking on any new customers or orders. I missed my opportunity to snag one of their unity shirts. With Joyner coming in the future, would you ever consider making a similar over-shirt?
An overshirt is one of the first items on the list.
Labour & Wait still stocks the Old Town overshirt: https://labourandwait.co.uk/collections/clothing/products/utility-jacket-navy
I have a question on the AWB. I work in my basement in an old house with an undulating concrete floor. I am worries I won’t find a stretch of floor level enough to keep a full sized bench from wobbling. Do you recommend adjustable foot levelers in this situation? If so, what type?
Been there. I don’t have any recommendations on levelers. I’ve always used wedges and blocks of wood and I’ve never had a problem.
Same situation for me and have good results heavy duty (5/16″) levelers on two workbenches. I have had no issues with the bench sliding around which was my main concern.
Good morning Chris and Megan. I noticed in American Peasant book that Chris used a carbide scraper to do the turning. I’ve had all of 5 classes (taking spindle class) for wood turning and we’ve been using HSS. Curious on your thoughts on carbide vs HSS. I’m too new to have an opinion. Many thanks.
The carbide tools are easier for beginners to use, but they don’t leave as nice a surface. We use them mostly for joinery or getting things to rough shape.
Good morning, Chris and Megan! Did (do) either of you have a preferred way of processing commission pieces? A particular form the client filled out, deposit, checklist of requests, etc.?
Best to you both,
Jake
I don’t really do commission work, other than an occasional tool chest, so it takes only an email to discuss interior wood, color and hardware. And I don’t require a deposit for those. But if I were doing full custom work, I’d ask for 50 percent up front, I think.
I didn’t use a form. It was a very individualized process. Usually they wanted something I’d built before but with some changes to the wood or size of the item. If the changes were significant, I would produce a quick sketch for them to approve. If they wanted something “new” then I’d make quick (emphasis on quick) pencil sketches. Never measured drawings (customers will take them elsewhere).
As to deposit, at the end of my commission work I was taking a deposit that covered materials and any design fees. But I never got stiffed (though it does happen).
Thanks for doing the open wire! It is valuable info for me. I learn a lot just reading through it.
My question is : on the ATC how thick are the parts for the plinth and dust seal and lid? I’m using 7/8 thick pine for the carcass and bottom. Should I use 7/8 for everything?
Use what you can get. Anything between 3/4″ and 1″ will work great.
Hi Chris,
Another Q about clothing, from your old post about mid-century furniture:
Can you tell us about them? My goat-skin pair were second hand (living in Austria they’re commonly available), but I don’t think that is what you meant!
Fionn
I’m afraid that was a joke. There might be artificial lederhosen out there. But I don’t know of any brands to recommend.
Thanks, I guessed as much, but then again, there are things we don’t know about! Figured that if such a thing existed then somebody at Dictum would probably know of it. Would love to go to one of your classes at Dictum, but it’s a bit of a road trip for us (by Euro standards, by US standards it’s practically the next town over) and toddlers don’t like sitting in the car all day long.
Crack a window. They’ll be fine.
Will do, thanks for the tips!!
I’m working on the Anarchist Tool Chest and I would like your opinion on the lid and the attached skirt. With lid clearance for the dust seal, the lid overhangs the chest side. I am wondering if I should trim the lid for minimal clearance and / or plane down the attached skirt to be flush with the chest. The current overhang may be helpful when opening the lid? Thanks!
How much overhang? I like a little (maybe 1/8″) on both sides and the front. Makes it a lot easier to lift the lid.
Thanks!
More work than I’m up for right now (health), but at least I know how to do it right when I can.
Hi!
I have two questions about the part that is sometimes the most frustrating for me in chairbuilding: the armbow:
I have historically had a really hard time cleaning up and fairing the curve on the inside of curve of the arm. The changing grain directions between the three pieces of the arm proper and the shoe makes this really challenging to approach with edge tools. What’s your process here?
Similarly, cleaning up the top of the arm after glue up is challenging because the doubler really limits any planing. Are you just scraping and sanding up there? Or do you have some voodoo you don’t mind sharing?
Thanks!
The simplest way to fair the interior of the armbow is to make a sanding block that is the reverse of the interior curve. Wrap it with #80 grit (or #60 if you have a lot of waste to remove) and go to it. After I get the interior to shape, I finish with scraping.
Cleaning up the top of the armbow begins before gluing it up. Once the lower arm is assembled (before attaching the shoe, I plane the area where the arm and shoe will meet.
Then I glue up the armbow and vigorously clean any squeeze out where the armbow meets the shoe with a toothbrush. That usually results in little to no work required at that seam.
Hope this makes sense.
Will Meyer’s saw horses feature an angled stretcher with a wedged mortise.
I’m making some in white oak and having a hell of a time getting the exposed side walls of the mortise to be tight and clean with the end of the tenon.
Any tips here?
Oak is splintery, so it is difficult for anyone to do that cleanly by hand. When faced with a difficult job like that, I score the mortise openings DEEPLY with a cutting gauge – as deep as possible. Then (if I’m being extra fussy) I’ll chop and pare the first 1/16″ like it’s a hinge mortise. Then I get to whaling with the mortise chisel.
Thank you
I’m currently making the 4 legged stool from ADB. But being in the UK it’s a struggle to find a decent 5/8″ forstner bit to drill the stretcher mortices that match the Ray Iles tenon cutter.
5/8″ is 15.8mm. So am I better off using a 15mm or 16mm bit?
Yup. A 16mm bit will work great. And is compatible with the Veritas Tenon Cutter (if you are using that)
Thank you. I’m using the Veritas tapered tenon cutter for the legs.
Hello there Chris and Fitz,
So I have a two part question about oil.
First off, I ordered some Jojoba oil from Amazon and wiped it on my brand new badaxe saws before vacation this past summer and when I got back it had solidified, almost as if it was partly mixed with a shellac–it felt and looked like dried shellac.
Secondly, I ordered some Camelia oil a few years ago for my tools and it works great with one exception, when its on my Lie Nielsen block plane and the remnants mix with my hand sweat, it leaves a blackish stain on my hands and thus the wood. It only does it with their products which I assume is because of the steel mixing with water and oil. This is why I tried the jojoba oil and dealt with cleaning up that disaster.
LN sells Jojoba oil for their tools. Are they all the same? Did I get a bad batch from China? 🤷🏻♂️ That being said what do you recommend so that it doesn’t stain my wood?
Thank you from sunny AZ!
There might be some body chemistry at work here. There are some people whose sebum (body oil/moisture) tends to mark ferrous metals.
I’ve never had jojoba harden up on me like that, but it can dry to a film in intense heat and if applied thick. When we wipe our tools down you can’t see there is oil on the surface. It is the thinnest coat we can manage.
You can also try mineral oil (thinned a bit with spirits). Or a light machine oil and see if that causes problems. Finally, if that fails, the last solution for us is CRC 3-36. It’s lubricant and corrosion inhibitor used in machining operations. Expensive, but amazing stuff in my experience.
Well, for your other passion – Shakespeare – have you read “Serpent of Venice” by Christoper Moore? Very funny, a bit bawdy but I thought it was great.
I have; I love his books. “Lamb” is probably my fave, followed by “Fool.”
Do you have a book, video, or blog post on what to look for when buying a vintage wooden plane? I find them all the time at Antique stores but have no idea if they are worth buying. Thanks for all you do!!!
Bill Anderson is the man for this.
https://www.edwardsmountainwoodworks.com/online-classes-videos/
He offers lots of resources on the topic, from choosing to tuning them.
I was drilling a hole in hard maple with a 1/2” brad point bit on my drill press, and it burned the wood inside the hole. What am I doing wrong? The bit is high quality and the press is in good shape. The maple was about 2” thick and I drilled all the way through it. The only thing I can think is that I didn’t clamp the maple down to the bottom table. Is this necessary? I see people drilling much harder materials, such as metals, without clamping them down. Thank you for your help.
Usually the problem is you are feeding the tool too slowly (heat build up as a result) or the bit is not clearing the chips efficiently (the chips retain heat and scorching results. Or the speed is too fast for the bit. Or the bit is not sharp.
When boring hard materials, I frequently pull the bit up during the cut to clear the chips. That usually does the trick.
Thanks again for doing this; you deserved a break but I’m glad you’re back! And, thanks so much for publishing Set & File. I’m learning a lot and starting to get decent at filing saws, but I have a way to go. Might there be a chance for a followup “addendum” or such on more advanced saw filling issues? (Maybe a substack blog?) I’d specifically like to learn more about filing slope – the books says none, but doesn’t say much about why. It appears many other resources do recommend some. Another had to do with making saws easier to start – progressive pitch vs rake.
Holler at Matt Cianci about this. https://thesawwright.com/
Hi, hope you are doing well. Can you recommend a non-toxic method for treating woodworm?
We recommend freezing or high heat. The University of Kentucky cover the process here: https://entomology.ca.uky.edu/files/ef640.pdf
In the Pacific Northwest, furniture restorer guys i talked to , about a large table with woodworm holes, said there isn’t much that can be done. Likely the woodworm are already gone, but reducing the dampness in the. location will persuade them to leave. They need damp to thrive.
Any plans to make a rocking chair – stick chair, like the John Brown one?
I’m sure I will some day. But first I have to tackle the settee form.
Hi there:
I have a traveling question:
How do you pack your tools when you fly to teach or take a class? What do you check and what do you carry on? Do you have recommendations to keep them safe when you need to check them?
Thanks!
I pack everything in a hard-sided case (a Pelican or Nanuk), wrapped in woobies and socks. I put all my tools in the checked luggage. There’s a sticker on the outside that says “tools”… don’t know if that’s helps or not. But I’ve only had trouble once – and that was when the case opened on what I can only assume was a rainy runway. So I bought a new case with better clasps.
Yes, about 1/8″ in front and 1/8″ or 3/16″ on the sides.
I might take a few passes off the sides, then.
In the PNW – specifically Seattle- take your table to Paratex. They use a gas chamber to fumigate for woodworm. Nontoxic, no smell,nice to deal with.
Greetings from a beginner and thanks for holding these Open Wire sessions!
I’ve recently purchased the Naked Woodworker, obtained my lumber, and am starting to slowly build the bench. My question is about attachment of the legs to the aprons with carriage bolts – is this done so that the legs are removable in the future as some sort of breakdown option? Why not a stronger glue and screw connection?
The carriage bolt attachment is one of the last operations in the bench build and I’m wondering if trying to keep that connection clamped for the majority of the bench assembly will be problematic as I move/manipulate/stress the assembly.
Glue and screws will work. There is a lot of glue surface. The big carriage bolts give you a knockdown option.
Hi! So glad you are doing these sessions, thanks a ton! I asked this question on the last Open Wire, but Ditt expressed insecurity at her answer, so I am reposting in hopes of getting an opinion from Mr. Sharpen This. Sorry for the repetition!
I got my first Veritas plane (yay!) and want to sharpen it. It’s a PMV-11 if that makes any difference.
I guess the bevel is straightforward. However, in Sharpen This Chris mentions that the back of the iron is ground so amazingly flat that rubbing it on a sharpening medium will usually actually reduce the flatness.
The finest sharpening media I own are a 1000 grit diamond plate or a leather strop. No fine waterstones yet.
Should I just strop the iron after I get a burr from honing the bevel? Or should I use the diamond plate? Should I use an MDF strop instead of the leather strop?
Many thanks in advance!
The 1,000-grit diamond plate is way too coarse for the back. I’d go to the home center and get some #1,500-grit wet/dry sandpaper (or an automotive store). Stick it down to piece of MDF or a cheap tile from the home center with spray adhesive. Use that to polish the bevel and remove the burr on the back.
Thanks a ton for the quick reply! Where I live, very fine sandpaper is difficult to come by – would charging a piece of MDF with honing compound be a viable alternative? I have the green stuff from Lee Valley. Thanks again for your help, it is very much appreciated!
No. Polishing compound cuts too slowly to be effective in my experience. Also, rounding over the edge is a problem because you have to work at it for awhile.
I recommend you order some diamond lapping film from Lee Valley. https://www.leevalley.com/en-us/shop/tools/sharpening/sheets-and-belts/68943-diamond-lapping-film
What nails do you use in the Swedish tool chest video to reinforce the rabbets on the drawers? Are they tremont fine finish nails? And in your new book you talk about brads and headless brads. Are the regular brads fine finish nails? I can’t find anything on their website for regular brads. Thanks!
Regular cut brads. Common, 4d. From Tremont.
Maybe I have missed it in the past, but I just got my first Shapton whetstones. Advice on using and flattening?
Thanks!
Ron
Both Chris and I use a Dia-flat lapping plate to flatten ours.
(I hope this shows up in the right spot in the thread, but if not, this is a comment to Matt’s question about casters for an ATC.)
Another source for vintage casters (and modern casters with a vintagey look) is Iron Anarchy in California; I bought a set of c. 1900 casters from them that, while not inexpensive, I found to be exactly as described, and very nice indeed, but from a functional and from an aesthetic point of view.
So I’m thinking about making a wood body shooting plane but I’m not seeing any good sources of plans for a plane with a blade mounted 20° off perpendicular. (I don’t want to skew the blade just the bed)
Any tips on where I should look to figure out my layout lines for the plane?
Low angles like that can be difficult to achieve in a wooden plane without the bed being fragile. You can shoot with a 45° plane no problem. And if I were making a wooden shooting plane, that’s what I would do
You should be able to keep it clamped little to no problem (depending on your clamps and how much stress you put it under, of course!). The leg structure gives the aprons a ledge to rest on, so the clamp is just giving a little push to keep it upright. I had mine in clamps for a few weeks as I got around to putting the bolts in, no trouble at all.
Also, great choice for a beginner bench! It should offer a great foundation for you. Enjoy!
Thanks for sharing part of your busy Saturday with us! I’m embarking on “30 days of dovetails”, and the first thing I noticed today is that I have a hard time sawing the left side of the tails square across the end (I’m right handed, so the start is all kinds of awkward, somehow). At least the error is into the waste (this itme). Is it worth correcting this before marking the pins?
Yes. I don’t mark the pins until the tails are square. I teach folks to re-mark the tail, and recut. And if you know this is a “problem,” concentrate on fixing that one thing on tomorrow’s joint.
I’m planning to paint a piece I’ve just built in white pine with white General Finishes milk paint. Have you used lighter GF milk paints? Do I need to prime first to keep the resin from showing through? I know it’s latex and not true milk paint.
If I have a particularly sappy piece of wood, I’ll spray a coat of dewaxed shellac first, then lightly sand to give it some tooth. But if it’s just a few area of the wood, I’d brush on shellac where needed to seal, then lightly sand that area before painting. Otherwise, no, I do not use a primer.
Sounds interesting- thank you! 👍
I was planning on a 35° bed angle actually. The 20° is the angle the opening for the blade would be at. So it’s like a slew but I’m not putting a skew on the blade itself.
Does that change anything for you?
Ah. I don’t think the opening angle is critical here. Many wooden miter planes (used for shooting) have a movable 90° block in front of the iron to keep the mouth tight. But making wooden planes isn’t my forte. Might check with Bill Anderson.
https://www.edwardsmountainwoodworks.com/about/
Thanks! I’m slowly but surely learning about the accumulation of errors as my projects get more complex. I’d rather correct them early than be surprised and have to do heroic work at the end!
The problem seems to be how to keep the saw aligned on the right side of my body while getting my head past the sawplate to see the line. Yes, I’ll work on that tomorrow!
Do you ever use a chisel for a “first class” cut? Or teach people to try that? It seems like a lot more work, but might establish the kerf as square.
Well, you need only see the line as you set the saw in preparation for sawing – then move your body to a position that allows your arm to clear your side, and move straight in, straight out. You can do a first-class saw cut, and I know folks who do. But that takes a lot of extra time to do for each cut. So no, I don’t teach that.
Hi Chris and Megan, Thank you as always!
I am building a low back from the Stick Chair Book and resawed the arm pieces out of 2in+ stock. Since sawing them, they have bowed/twisted slightly, maybe 1/4 to 3/8 of an inch over the length of the arms. Is that still a usable piece? I think it might fit into place between gluing on the comb piece and a little effort. Alternatively, it is red oak and I’m worried it might split/explode trying to pressure it together. Any thoughts?
This is common with resawing arm stock. It’s why I try to use stock that gives me some extra waste to reflatten them. If your arms are 1″ thick, I’d try reflattening them. You can get away with 3/4″-thick arms.
The warp/twist can show in the finished product, so I’d try to work it out (or make new arms).
Hi Chris, Fitz, Thanks for making the time. I was thinking about working with a local blacksmith on a custom plane stop. Mmy bench is way to small for one of yours unfortunately and it would use to dogholes instead of its own mortise (like the veritas planestops only with teeth and won’t slide around)
I was wondering that since you probably researched the heck out of the topic if I might hear about relative hardness and tooth count? what hights do you usually set it to? any suggestions would be welcome.
thank you
They don’t need to be hard. Mild steel or wrought iron will do the trick. I don’t even know what the Rockwell hardness is of our planing stops, but I know I can file them to sharpen the teeth, which is important. As to number of teeth, we use nine. I’ve seen fewer and more – I don’t think it makes a heck of a difference.
The typical planing stop should be able to be adjusted so it is 6″ to 8″ off the bench for edge-planing. But you could get away with as little as 2″ off the bench. Most of the work is done with the stop much lower.
I glued up a couple seat blanks in the early spring to make some chairs this summer as I am a seasonal worker in a different climate where I will be building them. It is very dry here and my glue joint separated on both ends about 2 inches in on each side. I tried using CA glue, but it just separated again. My chair is shaped all mortises drilled, but my intuition is telling me just to junk the seat. It is made out of kiln dried Red Oak and I did not use any loose tenons . One other thought I had is to attach, a couple metal plates along the seam on the bottom. Any thoughts would be appreciated thanks.
Lots of options: Steel plates and paint (the historical approach.
Rip the joint apart using a thin sawblade (like in a band saw or frame saw. Carefully rejoint and glue. It probably won’t make a difference with the sticks and arms and etc. You’ll be removing a tiny amount of wood.
You also could saw a kerf into the split and glue in a red oak spline.
My usual course of action is to rip the seat apart and reglue. It’s easy and fast. (Though it seems like major surgery.)
Hi Chris,
I posted this during the last open wire but you were away 🙂
The Stick Chair Book was a big inspiration. When making my first chair (on a Roman bench — Ingenious Mechanicks was another big inspiration!), I was indecisive between 8 and 10 sticks and found physical prototyping kinda fiddly. Of course, digital prototyping is even more fiddly… unless someone’s done it for you already!
Long story short, I made this calculator in my spare time: https://layout.computer/stick-chairs/. (There are no downloads, sign ups or anything like that — just the calculator.) It lets you play with the chair and then gives you the important measurements (leg angles, stick spacing, etc). Currently, it only supports Welsh-style lowbacks, but I am planning to add highbacks and Irish-y chairs when I get to building them.
As all this started from your book, it would make my day if you shared your thoughts on this tool. (Does it have legs? Haha)
Hi Nick,
I checked it out while I was away teaching. It works great. I’ll post something on the blog shortly about it. I know lots of other people will like to play with it.
Oh, that’s awesome! More than made my day 🙂
By the way, if you are interested in collaborating on this in any way, let me know — you should have my email via these comments, or failing that there is a contact form on the About page.
I looked but I haven’t found anything yet. I’ll keep poking around, thanks!
Watched your recent Roman Workbench video. I’m going to try making one entirely out of Doug Fir, including the legs, and see what happens. In that case, would it make sense to beef up the legs? What would be some reasonable dimensions?
Sure. Make them out of 4x4s. About 3″ would be great. Maybe a little less if the growth rings are tight and the grain is straight.