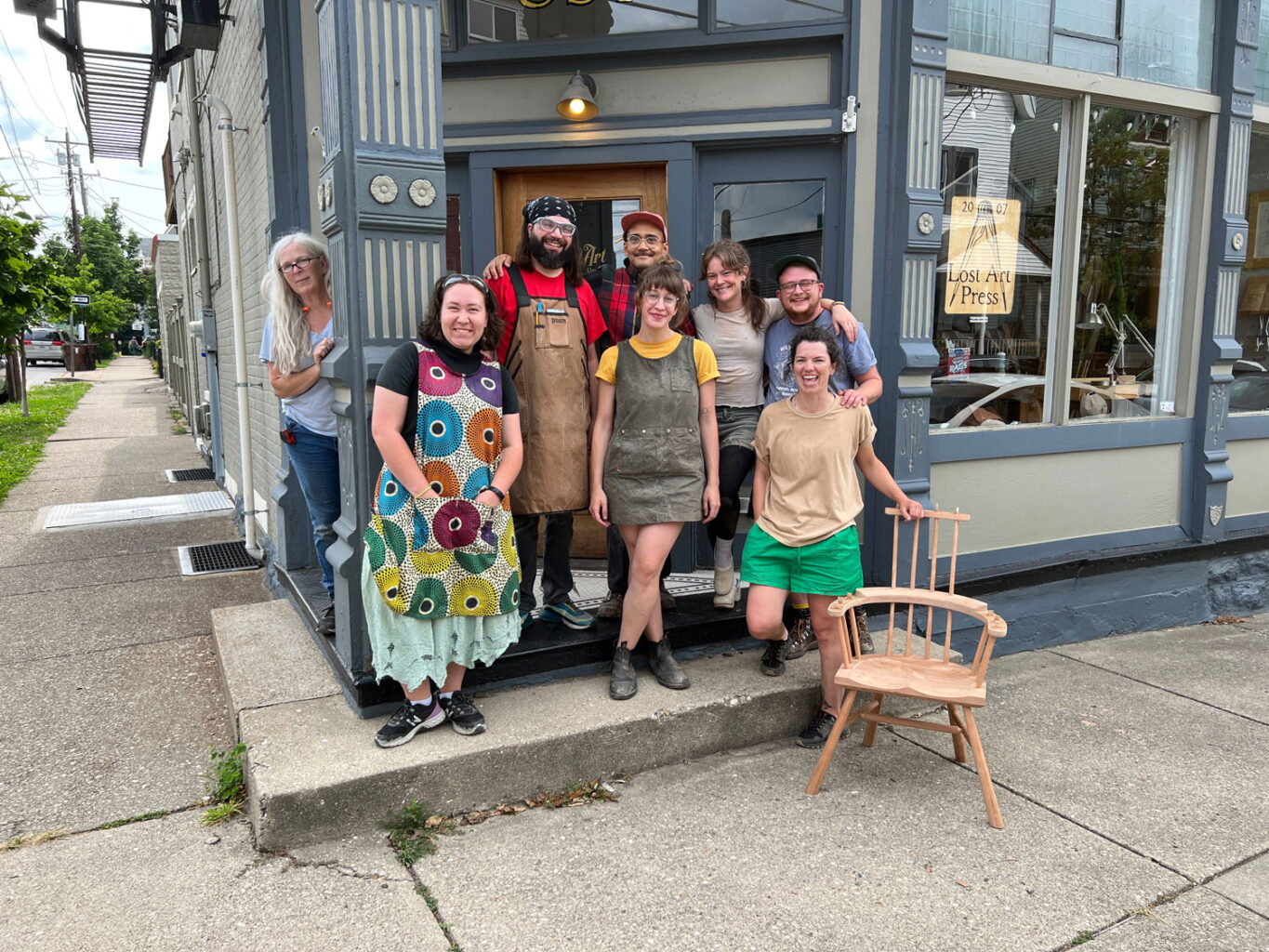
This fall, Megan and I are each teaching scholarship classes for The Chairmaker’s Toolbox, which offers free training for people who have been historically excluded from the trade.
I’m teaching a stick chair class Sept. 16-20. And Megan is teaching a Dutch tool chest class Oct. 11-13. Megan and I both volunteer our time and the workshop here for the classes. We also cover the students’ materials, plus breakfast and lunch during the class.
For that last few years, readers have asked to donate to help cover the materials and the food for these scholarship classes. If you would like to help out, you can send a donation via this link. Any amount helps. (Please note a donation is not tax deductible. We are not a charity or nonprofit.)
If we collect more money than we need, every penny gets donated to The Chairmaker’s Toolbox to help fund its expenses. We do not make any money off these classes.
Thanks to everyone who has donated in the past. Many of our students from these classes have gone on to teach chairmaking to others or have launched their own businesses. (In other words, it’s working!)
Here’s the link again (because they tell me we are supposed to do that).
— Christopher Schwarz
P.S. Don’t bother leaving a comment that craps on the program or us. No one will ever see it. At Lost Art Press, we help anyone who wants to enter the craft. We teach scholarship classes (and donate money) for need-based students, students who have been historically excluded and those who serve (such as our military). Don’t get ugly about something beautiful.
‘Don’t get ugly about something beautiful.’
It’s a shame that you have to say that.
Are you interested in tool donations? I’ve been trying to thin out (I almost said “pare down”) my assortment of chisels…
We have all the tools we need for a class (and then some). Thanks for asking!
Very happy to kick in a little. But I’d like to crap on something, so if you can point me in a good direction . . .
Lumberjacks.com
I’ve never spent more than a few minutes looking at any of the online forums. There were just too many people I didn’t like. Plenty of good ones. But it just turned me off.
Do you mean Lumberjacks.com?
System “corrected” my answer!
Donated. I love the idea of this existing and that people are learning the craft that we love. Thank you for teaching others and doing more for the woodworking community.
Hey Chris K! CMT is interested in tool donations — shoot an email to tools@thechairmakerstoolbox.com and your old tools will find a new home with someone who will put them to good use!
Oh cool. Any specific things you need?
A query related to the Anarchist’s Workbench design/book/project:
I live in the Southern California area. I’m planning to build a small (6’) workbench to install at our cabin at Big Bear Lake, where I spend a lot of weekends and have been trying to do woodworking over the weekend on a flimsy redwood picnic table. The work area is outside, and the contemplated new bench would be left outdoors, and covered by a tarp, when not in use.
My quandary is that yellow pine is almost impossible to find in this area, even from the big, specialized hardwood yards. It’s Douglas Fir, Douglas Fir, Douglas Fir out here in the West! And a little bit of hemlock at prices comparable to maple.
BUT…Home Depot carries Southern Yellow Pine 2x 6 boards….but only in 4 foot length. So to make a bench top I would need to laminate on both axis. 4 foot and 2 foot sections alternated. My thinking is that it would be butt ugly, but if I am careful squaring the butting ends of the boards (that is, planed square on a shooting board) it would be a functional bench, albeit not aesthetically as pleasing as a normal construction.
Would this approach be functional?
It certainly is my most cost effective option. The 4-foot sticks of Southern Yellow Pine cost about $5, or about 50 cents per pound. An equivalent Douglas Fir bench top would weigh 20% less and cost 25% more. (The undercarriage for the bench would be Douglas Fir in either case.)
Also, I thought about trying to do some sort of joint to hold the butted boards together, and decided that would not be necessary, since the butt joint is constrained from movement by the alternating sandwich of 2 x 6 boards. Do you concur?
Corollary questions:
1. Since the bench will live outdoors, any thoughts on whether I am better off with a wood screw or metal screw for the vice? Either way, I would protect the screw and related nut with oil and/or wax.
2. Which type of glue would you recommend for this outdoor application? I have both TiteBond Type 3 (PVA)and moisture-curing Polyurethane available. I think epoxy would set too fast to make it suitable for the laminations, unless I obtain a very slow-curing version such as is used for making wood canoes.
3. I you are recommending use of the 4’ Yellow Pine boards, any thought on the lamination pattern? I can see two alternatives: 4’ and 2’ sticks alternating left-right, or cut some the sticks to 3’-1’, some to 2’-2’, and go 1-4-1, 3-3, and 2-2-2 combinations of sticks. I think the latter would be more work, with minimal benefits if any. Thoughts?
Lastly, I offer boundless thanks to you and Lost Art Press for making this great book available.
Laying the SYP boards like bricks with glue will work fine. Most countertops are built this way. No joinery necessary on the ends of the boards.
As far as vises go, you’ll have moisture problems with either a metal or wood screw. I’d probably opt for a white oak screw and nut. That would resist the elements and is plenty strong.
On glue, Titebond II or III will do. I prefer these to poly glue or epoxy. PVAs are easier to use and clean up.
On the pattern of boards, I would keep it simple, such as your first pattern.