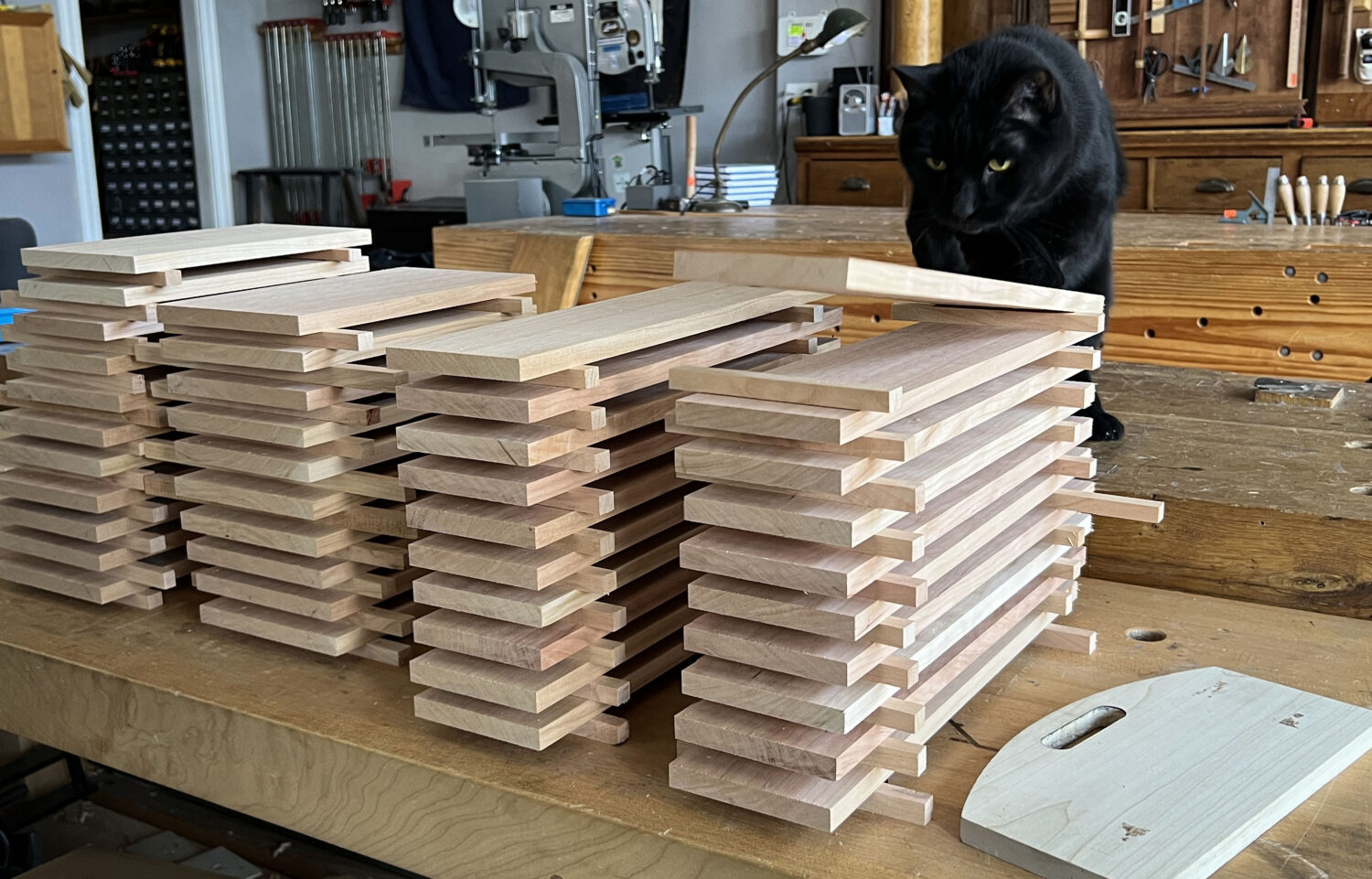
Update: Comments are now closed (thought Chris still might answer later, as needed). Join us again for Open Wire on August 10.
Wally and I are in the shop all day to work on 10 Shaker trays (because someone feels guilty for stepping down from their neighborhood house tour committee and thus agreed to make thank-you gifts as self-imposed penance) and for Open Wire AMAAW&C (Ask Me Anything About Woodworking & Cats).
You know the drill: post your (succinct) queries in the comments field below, and we (Wally and I) shall do our best to answer. Christopher might also pop in with answers from time to time…though I hope he’s spending the day having a grand time with Lucy and friends in Germany, and not paying attention to the internet.
Comments will close at around 4:45 p.m. (Eastern).
And a reminder of the Open Wire dates for the remainder of the year (when both Chris and I – and no doubt Wally – will be in the shop):
August 10
September 14
October 19
November 16
December 14
– Fitz
I’m building an irishy stick chair that will go outside. I plan to paint it with linseed oil paint. Can I use hide glue or should I use Titebond III or gorilla glue?
Also, not sure why but I only get about half the LAP oats to my email?
I’d use Titebond 3 (I know polyurethane glue is also supposedly rated for exterior use, but I hate the way it foams up. I always put too much in then have to scrape it off when it bubbles out of the joint.)
Our new WordPress host doesn’t send an email every time a post goes out. Instead, we are sending “digest posts,” that list what we’ve recently posted… but those are manual, and Chris hasn’t shown me how to do it yet. And he’s on vacation.
Would your Piggly No Wiggly glue (or any hide glue) work for bent laminations? If not, any suggestions on what will?
There is likely too much “creep,” — I haven’t tried it, but my gut reaction is no. Jeff Miller, who does a great many bent laminations, uses Weldwood Platic Resin glue.
Hi Chris and Megan,
What are your thoughts on https://layout.computer/stick-chairs? It’s a tool that lets you quickly tweak a chair interactively and then shows the layout diagrams for sightlines, resultants, stick spacing, etc.
I haven’t tried it – so my opinion would be wholly uninformed.
any recommendation on a paint sprayer (not an all in one system) that can be used with an existing air compressor?
I’m afraid I’m familiar only with the two Apollo systems we’ve had.
This is mostly for Chris, but I’m keen to hear your thoughts too, Megan:
One of the reasons I’m drawn to building stick chairs–beyond their design and history–is the “vernacular” quality of them: the rustic nature that allows for small variations in the chair (somewhat wonky leg, weird stick, etc.). This appeals GREATLY to my lack of perfectionism!
I’m curious, though, if you’ve ever struggled (as I am now), in using that term as a “get out of jail” card for not being more exacting in your work? “Wonky leg? Vernacular. Spelchy mortise? Vernacular.”
You mentioned a few weeks ago that the John Brown chair you received is 5/8″ lower on one side, and that John Brown celebrated character like that. I guess my question is–what’s your tolerance for situations like that?
Sorry–this was longer than I wanted.
Jake
I don’t think I’ve ever used “vernacular” as an excuse. If something is wonky, I chalk it up to my needing more practice, or just bad luck. If it’s for me and wonky, I can live with it. If I’m making a piece for a customer, I cannot (or if it’s a spec piece that I’ll eventually sell, wonky=discounted price).
Good morning LAP. Quick silly question. I have a norton duel grit oil stone. One side is dark gray the other side is brick red-orange, and I can find bupkis about which side is couse/fine. I have an idea but….? Anywho my silly question is do I use oil when I flatten it? Thanks much!….oh also I only use it for knifes.
It does need lubricant for flattening (oil or water). As far as the grits…I’m not sure, but a little googling (a dangerous thing) leads me to guess orange is the finer side.
However, a Jeweller’s loupe is a useful – and inexpensive – thing to have. 20x mag is better than 10 x.
Run an edge along one side of the stone, and examine it through the loupe. Then repeat on the other side. The degree of abrasion on each should be visible and will tell you which is the finer.
I had to look up what ‘bupkis’ means…….
Norton stones are fairly soft composite material compared to some natural stones.
Unless the shape of stone’s edge is really distorted, a dead-flat surface for knives is not essential.
Good morning. I am kicking around the idea of starting to sell some of the tables, bookshelves, and (eventually) chairs I build. Not going to quit the day job, just potentially do this on the side. What insurance would you recommend I look into if selling my wares to people? Given that we live in such a litigious society, I’d like to make sure that I am covered as best as I can be. Thank you.
Mike, I’m neither Megan nor Chris, but this thinking is why I didn’t sell any of the turned table lamps I made years ago. (“Your lamp gave me a shock!”) These are very good concerns- the bookshelf tipped over, the chair collapsed… I’d talk to (ouch) either a lawyer or at least an insurance agent who specializes in commercial and/product liability lines of coverage. If you sell it, some lawyer out there will say you do it for profit and you are therefore a business. Get insurance. You don’t want someone going after your home because they got a sliver in their hinder.
I’m afraid I do not know. Any lawyers or insurance agents here who care to weigh in?
I am going to take a run at the staked bed in the ADB, but due to either my stubbornness or thriftiness (you can choose) I am working with what I have, which in this case doesn’t have a ton of stock thicker than 4/4. I think I have some decent pieces for the battens but they’re not quite as beefy as the book suggests. The big question really is does it matter if the battens are a little narrower or a little thinner than suggested in the book (4″ x 2 3/8″)?
I was also planning to do tapered tenons because I have the tools for it. That shouldn’t be an issue either I wouldn’t think?
You’re always generous with your time. And I’m nervous about a larger project. That I will then place my ever increasing in mass 10 year old upon.
How much thinner, and how much narrower? If only a little, it’s probably fine. But much thinner than the specced 2-3/8″, and I’d consider a stack lamination of those 4/4 pieces to get near that thickness.
I think the mortises are stopped in the original, so tapered wouldn’t work for that, but if you do through mortises, I can’t see why tapered wouldn’t work. And you can wedge them to ensure they’ll stay in place.
Thanks Megan! I am sure you haven’t as it’s only been around for a couple of weeks 😅 Let me rephrase.
The Stick Chair Book has been a huge influence on me, and I made this tool in my spare time kind of as a tribute to LAP (and to help with my own chair). I was just hoping for some feedback, it would mean a lot to me! (There are no logins, downloads, installation, paywalls or anything like that.)
I totally understand if that’s not something you want to engage with or inappropriate for Open Wire.
Ah! Well, I’d want to play around w/it before answering…and really, Chris is the better person to use it. I have made only a handful of chairs. So my opinion on the tools efficacy won’t be very informed no matter how long I play with it.
Fair enough! That site also has a similar dovetail calculator (https://layout.computer/dovetails) which is probably more your thing, but I would expect you to scoff at it with a pair of dividers in hand 😆. (Despite being aware of the dividers method and the ruler+chisel method, I still found making the tool useful for quickly experimenting with different spacings, including progressively enlarging ones.)
I will keep my fingers crossed for Chris to try the chair calculator.
Good morning! Working on an AWB & was drilling the peg holes through the leg mortices when the hard/soft grain in the douglas fir got the better of me & the auger bit. I had also drilled from both sides to minimize error but worst holes are about 1/4″ off but that’s mostly vertical not towards/away from the edge of where the tenon will enter. Will extra long tapers & wax on the dowels work or am I going to have to do something else? Thanks for doing the open wires!
1/4″ seems like a lot to me; I think 1/8″ is the typically timber-frame offset. Doug fir might be soft enough to get away with it, if the peg is straight-grained and a strong species (e.g. oak). I’d probably try it…knowing that it might end in tears. But I would base the offset on the tenon off the hole on the show surface, then taper the snot out of an extra-long peg so it’s smaller at the inside and keep driving it until I’m too scared to hit it again (when the sound changes to an ominous thud). If nothing else, the front side of the joint will be pulled tight.
Good Morning Megan,
If I had the room, I would have three benches like Jim Teplin but I don’t. I have the mid-height one as easier on my back for the most of what I do. The down side is if I have a lot of hand planing it’s tough on my shoulders. My solution is to build a platform I can stand on to effectively lower the bench when I have a lot of hand planing Do you have a feeling on what length and width I should make it? Figured you might have done this or seen this with all the teaching you do. Thanks Megan!
Sincerely
Joe Leonetti
I’d say the length depends on your typical work – and storage space. I’d make it at least as wide as my shoulders plus a few inches (or measure your planing stance side to side and add a few inches), and as long can fit between the legs of my bench, so I could store it underneath.
Can you go over how you do you do touchups with linseed oil paint? I recently painted a chair, let it dry for two weeks then went back to do a few touchups. After they dried you could see some streaking where the paint was 2 coats deep. I’m using the Wooster brushes you recommended and put on as absolutely little paint as possible. I’m wondering if I should have used an artist brush and really tried to only get pain on the bare wood. Thanks!
Those streaks will even out after a little more time – at least to some extent. We haven’t yet found the perfect solution. So I try like heck to not need any touch ups (which so far have also cause us trouble in some instance, but not in others…and I have yet to determine the cause).
Honestly that makes me feel better. I wonder if the specific color plays a roll.
Probably so – it sure does with milk paint!
Hi Megan,
For a first time Tite Mark purchase, would you opt for the 9″ or the 7″ with extension options? For most things I can’t imagine using a marking gauge longer than 7″, but this i don’t want to regret the extra few bucks….any thoughts?
I have the 7″. I have yet to regret not getting a 9″ – but I don’t use the mortise layout attachments. I guess if I were going to use a 1/2″ mortise blade on it, I’d want the longer one, but…
Good.morning LAP and thanks for sharing some of your Saturday with us! I’m slowly succumbing to the draw of building a sitting thing, and I’m more and more perplexed: when does a stool become a chair, or vice versa? E.g., why are the two subsequent chapters in ADB a (back) stool and then a chair?
According to Chris (with apologies if I’ve mis-interpreted his words here), a stool has no back. A backstool has a back (and is now often called a side chair). A chair has a back and arms.
I always thought that was a funny definition, here almost everything I’d call a chair hasn’t got arms.
Hi Megan, thanks for doing this today. Do you use a small router to clean out the tail sockets on half blind dovetails to save time? If yes, do you have a favorite router bit?
Nope. I’m too lazy to find the router…and I find the thought of my having a favorite router bit hilarious. But the few times I’ve used anything other than a chisel, it’s been a Forstner bit at the drill press.
Hey Frank!
Mike Pekovich over at Fine Woodworking uses a router to clean out his sockets. I think he uses a little short stubby 1/2″ flush trim bit, though of course for half blinds that will still leave some corner material.
Wondering if between the Gibson and Stick chairs is one a better/easier first chair to make?
Spitballing here from having watched a bunch of classes in both: I’m going with the Gibson as the easier build, with the caveat that it’s a bad idea to try to force those outside sticks through the arms. Make sure they fit; there is not much wiggle room on that.
Meant to send this weeks ago and maybe you guys already have seen this article by Chris Farrell. I never expected to see Mr. Schwarz mentioned in my local paper.
Making a living as an artisan is hard but not impossible with financial planning
https://www.startribune.com/artisan-furniture-maker-shoe-blacksmith-career-passion-money-financial-planning/600365229/
I don’t know about Chris, but I had not yet seen that. Thanks for the link!
Well, by the time I’m done planing it might get a little sketchy (like, 2″ at a real push). Lamination might work out better.
Yeah, through tenons seem the way to go.
Thanks! A little postscript, I bought the hardware already – buying stuff is part of the making part, right? – so I might end up getting out my hacksaw and cutting down the bolts a little.
I’m just riffing now… this is a big challenge for me. I don’t get a ton of time in the shop because of family stuff (no bad thing, I’m not complaining) so I tend to struggle to remind myself I’m not on some huge deadline. So figuring stuff out is a big part of things. That’s been something I’ve learned from reading along with LAP the last few years. But it’s funny how insidious and frustrating it can be!
Thanks
Thanks. Measuring my stance etc makes sense.
PS finished both tills for the ATC. Now making the wooden handles. You’d be proud in that all I’m using for this project is scrap wood I have around the shop. In this case it was some quilted cherry. 🙂
Barr chisels come with a bit of a goofy grind and instructions for sharpening (round-ish profile just prior to the bevel). I’m curious to know whether you all continue with that profile or just sharpen like every other chisel? I’m assuming the latter since the only thing that really matters is the edge. Many thanks..just something that’s bugged me for a bit.
I’m going to hold out for Chris’s answer here. I have only the 2″, and I haven’t used it much. I’ve touched it up once or twice freehand, maintaining it’s stock angle. Chris has several in diffrernt sizes and has almost certainly sharpened his more often.
I just sharpen them at 35° with a honing guide – just like all my chisels.
Only tangentially related to woodworking, but can you recommend any specific resources on learning to take better photos of the things I make? I’m progressing in my woodworking akilla but can’t take a picture to save my life.
I don’t have any outside sources to recommend, but this is a pretty good post from Chris with basics: https://blog.lostartpress.com/2020/08/26/making-book-part-5-cheap-shutterbug/
One caveat – newer iPhone photos are so good now that we use it for most photography rather than an SLR (unless we need a specific lens not offered on the phone)
Two questions:
1. In the 5th video of making a Roman Bench Chris is using a mallet with a green metal band. Could you tell me where this was purchased?
I know you spoke of it before but I cannot find the past post – sorry.
In the Anarchist Tool Chest -appropriate page of 155 you mention holding the blade of a chisel as you would a pencil. I’m just learning to cut dovetails. Do you hold the chisel with your dominant hand? Or is better to hold with less dominant hand and use the dominant hand to control the mallet?
Thank you
Steve Flynn
Garland split head no. 4:
https://garlandmfg.com/mallets-hammers/split/
Chris posted a video some time ago about a new chair drilling technique he’d learned from somewhere, where he’d drill through the armbow and seat with them stacked flat on top of each other, horizontally offset the correct amount, eliminating the need for drill extenders. I haven’t been able to find the video since. I can’t remember if this was for the Gibson chair or the ”normal” stick chair. Could you link to it?
Hmmm… I don’t recall a video, but that was for the chair in “American Peasant.” You can read about it and see still images by downloading the free PDF here: https://lostartpress.com/products/american-peasant-signed-by-the-author?_pos=1&_sid=87f2b1180&_ss=r
I’d like to build a stick chair for my desk. Will a comb back work should it be low back. And what tilts (seat and back) are appropriate for keyboarding? ( I know you have written about this, but I haven’t located it yet :—).
It will. Chris has written “Usually a back lean of 15° is good for keyboarding. Seat slope of 3/4″. Lumbar support (so use an armbow).”
Here’s a dumb one: I have a Dia-Flat lapping plate and I tried to use it on a Shapton stone for the first time last week. One side of the plate is smooth and the other is rough with a bunch of little nubbins. I don’t know which side to use. The smooth side seems like it won’t do anything and the rough side seems like it will etch grooves in the stone.
erm…I feel dumb, but I’m not sure what you mean. Can you tell me more? i.e. is it one of these:
https://www.sharpeningsupplies.com/blogs/articles/dmt-lapping-plate-comparison-chart
Aha! Thanks for the code key. But isn’t the second ADB sitting project a chair, but without arms? 🙃
Sheesh. Made me open a book. And yep – you’re right. So I don’t know. Usually I hear him call a non-armed stick chair a backstool.
Hi Megan! I’m curious, as I am getting starting building a folding bookcase, do you generally avoid using plain sawn lumber for casework? Or do you find that concerns about wood movement are overstated?
Depends on the species. But generally, as long as the wood is at equilibrium before I start taking it to final size, I don’t worry too much about it. For casework, I’m typically more concerned with figure, and straight grain for rails/stiles.
I have to fashion a screwdriver for the split nuts on a Wenzloff saw. The blade will need to be thin, about .036” or so. Modifying a screwdriver is an option, but those blades are very thick. Another option would be to file a .032” scraper from Veritas, very hard metal. Thoughts?
Do you have a grinder? If so, I’d probably just grind the tip of a screwdriver thinner. (Or see if I can find a spanner bit that fits, perhaps.)
Fitz,
Could you please give me the reference or the dimensions for a bending form for chair arms. At least a general idea. Thank you so much for your help and all of your articles
The form pretty much matches the shape of the inside of the finished arm, and will vary by design.
There are two shown here, which I think/hope will give you the idea:
https://blog.lostartpress.com/2023/12/27/cold-bend-hardwood-why-and-how/
and here’s an old video featuring Chris bending a compwood arm:
Page 512 of “The Stick Chair Book,” which is a free download here.
https://lostartpress.com/collections/books/products/the-stick-chair-book
Hi! So glad you are doing these sessions, thanks a ton!
I got my first Veritas plane (yay!) and want to sharpen it. It’s a PMV-11 if that makes any difference.
I guess the bevel is straightforward. However, in Sharpen This Chris mentions that the back of the iron is ground so amazingly flat that rubbing it on a sharpening medium will usually actually reduce the flatness.
The finest sharpening media I own are a 1000 grit diamond plate or a leather strop. No fine waterstones yet.
Should I just strop the iron after I get a burr from honing the bevel? Or should I use the diamond plate? Should I use an MDF strop instead of the leather strop?
Many thanks in advance!
I don’t feel confident enough in my all-thing-sharpening knowledge to answer with authority. But were it me, and I had a choice only between a #1,000-grit stone and a strop, I’d remove the burr from honing on the stone. Or charge a piece of mdf with compound. I’d be worried the leather has too much give.
Two questions about the bookcase in ADB. I’m planning to build a slightly taller version, with a couple more shelves.
1 – Are nails through the sides into the shelves structurally necessary or will dados and glue be enough? I do plan to the ship-lap or T&G back with nails.
2 – if I do nail the shelves and want to leave the nails showing, what’s a best order for assembly, gluing, nailing and painting?
Thanks for doing this!
I’d nail at least the backboard rail and the bottom rail (and perhaps the top shelf, at least at the front)– you want some kind of constraint across both the front and back (I don’t trust just the glue alone ’cause end grain). But if you’re painting, you can use cut nails and punch the head flush to the surface. Those should pretty much disappear with paint and a little time.
If you nail and want to leave them showing, I’d glue, then nail, then paint. The paint wears off the heads pretty quickly under touch, and it is easy to speed up the wear with #300-grit sandpaper.
Hi Megan. Thanks for the open wire today.
For a Roman workbench, how disadvantageous is it to not glue and wedge the legs into the top? Being super limited on space in and apartment I’d like to be able to store it upright, with the legs removed, when not in use.
Also, is there a particular reason the LAP videos and shorts on YouTube have comments disabled?
As long as you scoot it and don’t lift it (so the legs don’t fall out when you don’t want them to, I don’t see why you couldn’t skip gluing and wedging so that the legs can be knocked out. But it also makes a nice coffee table and/or seating bench, FWIW.
Comments are disabled because we already respond to comments on the blog, on three Substacks and on Facebook and IG. There simply isn’t enough bandwidth (or desire) to monitor yet another thing.
That’s it, thanks. My lousy memory hallucinated this having been a video.
Use the rough side against the Shapton stone for flattening. I have the 10″ Dia-Flat 95. Yes, it will leave some small grooves the first several times you use it, but they don’t affect sharpening. Using the plate breaks it in a bit and the larger diamonds wear down. Also, make a grid with a pencil on your stone, and only grind until the pencil grid is just gone.
Oops, this was supposed to be a reply to Steve Nicholson above.
Any Pre-Order Date for the Dutch Tool Chest Book?
Not yet. Chris is editing it now.
Howdy – I am working on a bedroom set for myself and my wife. First pieces are done – stickley 110 nightstands in Walnut. Future pieces are a bed, dresser, and wardrobe. Now I’m stuck deciding on a finish. I re-read Chris’s blog post when he cancelled the finishing book but it’s been a few years since then. I’ve built up some good skill with a shellac/wax finish but I’m concerned that it’s not a “looks great in 20years” category finish. Questions would be 1) can a shellac/wax finish look good long term if I reapply wax on a yearly-ish basis? 2) would some kind of pure oil like Real Milk Paint Tung Oil be a better long term solution? 3) could wax or soap still be applied over a pure oil? I’m trying to stay as non-toxic as possible
As soon as the shellac layer is breached, the scratches show. The top of my coffee table is a testament to that 🙁 But walnut looks FABULOUS with a simple oil and wax finish (like our soft wax 2.0, the recipe for which is online and in a couple of our books now). It’s non-toxic and easy to reapply as needed. That’s what’s on my walnut bedside table; I reapply every 6 months or so. (And I use a coaster for water glasses etc)
Thanks! For some reason I’ve always ignored the soft wax 2.0 and didn’t even realize it had oil in it 🙂 I’m going to make some and give it a go on a test piece
I have a Veritas round spokeshave, and it seems to clog a lot. I’m not sure if I’m just not good at using it yet, but I think I remember seeing that Chris files his. If that’s right, is this something you generally recommend? Or should I keep practicing? I’m very aware it could be the meat and not the tool. Thanks!
Going to have to wait for Chris on this one. I don’t know. It doesn’t look to me as if he filed his (it’s still in his chest here), but I could be wrong. I have not filed mine. I find a light cut and skewing the tool helps me – but I don’t use a shave that often.
Hello! Is it ok to wax the sides of my mortise chisel (similar to how I wax the sole of the hand plane)? It makes chopping the mortise easier but my worry is that the wax inside the mortise will make it less grippy and/or reduce glue adhesion.
Also I was wondering if you knew roughly when the video for the Swedish took chest will be released? I want to make one but I figure I should wait for that.
Thank you!
Probably fine to wax the chisel side (just don’t use too much, and there shouldn’t be much transfer). We hope the Swedish chest video will be out soon! Just awaiting final edits. But I don’t have a date yet.
Hi Megan. For the interior of the travel size atc, I’m putting the panel rip and cross cut saws on the interior of the lid. I will be using the small tool holder hole thingy (your style) inside the front edge. Where would put the dovetail and fine joiner cross cut saws? They won’t fit when the lid is closed in the most front slot of the small tool holder when the chest is closed due to depth of travel ATC. Many thanks. Sincerely, Joe
Id be more inclined to put the backsaws on the lid (where they’re less likely to be run into w/a plane or something else on the floor), and the panel saws on the floor in a till like this one: https://blog.lostartpress.com/2014/12/27/a-simple-saw-till-for-a-tool-chest/. But that same style (more closely spaced) works for backsaws, too. (Or put all on the floor and keep the backsaws protected by the more robust panel saws.)
Thanks. I will noodle on the options. Good problems to have.