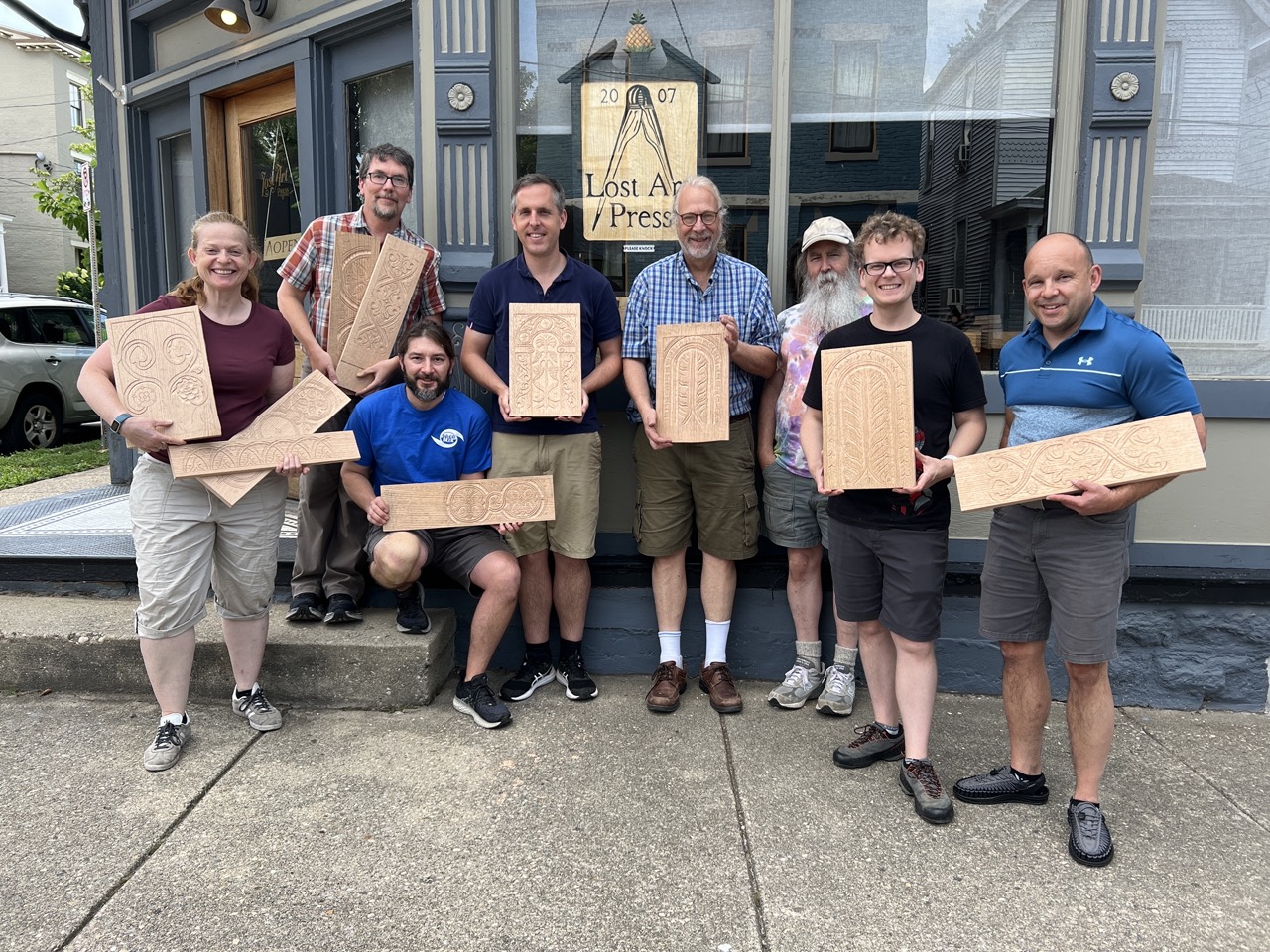
Update: Comments are now closed. Join us next Saturday for more Open Wire fun (and check the schedule at the bottom for the OW dates for the rest of 2024).
Due to a minor “oops” earlier this week when we mentioned we’d have Open Wire this Saturday (and the fact that I’ll be in the “office” anyway) – I decided to hold Open Wire today. But I will not start answering before 9 a.m, and possibly not even before 10 a.m. (Eastern). It’s been a deightful but busy week…so I plan to sleep in a bit on Saturday morning.
Comments will close at 4:30 p.m.-ish (Eastern)
And a reminder that we’ll be doing Open Wire – where you can ask all your woodworking questions and we’ll do our best to answer them – on the following Saturdays for the remainder of the year:
July 20 (Chris will weigh in if he can – but probably not until after comments close for the day)
August 10
September 14
October 19
November 16
December 14
– Fitz
Do you have any general guidelines are to when to use a chamfer versus a roundover for edge treatments?
I think it’s purely aesthetic. A chmfer usually looks more contemporary. A roundover can look (depending on your point of view) old or 1980s.
For the ATC, is 4 saws the most you would recommend for the saw till, or is it possible to fit more in the main till? Thanks!
On the floor? I probably wouldn’t do anything much wider, or you’ll lose space for planes. But consider a hanging rack behind the hole-y rack for backsaws – that will leave more room for hand saws on the floor.
For a three legged back stool, what is the rake angle of the back leg? I remember a blog post saying it was more than typical, but can’t find an angle anywhere. I assume the front legs are the same rake and splay as a normal back stool. Also, have you ever seen or considered stretchers between the three legs?
The resultant angle is 23°, from Anarachist’s Design Book
I recently finished a chair with black bison wax over GF Milk Paint. Overall the wax went on great, but on the saddle it’s a smeary mess. On the flat of the saddle the wax went on darker than the rest of the chair. Even the curves at the edge of the saddle were much lighter than the flat part.
Any guess what may have caused that? And now that it’s been on for a week, anything I can do to lighten the dark spot?
Are the woods different species? (If you’re talking about the CW chair, I should know…but I can’t remember.) Different woods will behave differently under a given finish, as will the way they’re cut (ie quartersawn or flat sawn). I’m afraid I have yet to successfully lighten the dark wax. We had a similar issue on a recent chair, and the only solution was to strip it and start over, with paint. We wiped the wax off with mineral spirits, then sanded and scraped to remove what was left.
Yeah, it’s all red oak, which was part of whay surprised me. Well, I was afraid that’d be the answer, but glad to confirm before busting out the mineral spirits!
Hi Jacob,
My guess is that some parts of the paint were more porous than others. If you finished the saddle surface differently than the arms (say, sandpaper instead of edge tools), then that’s probably the answer. Mineral spirits will remove some black wax. I’d probably try that and a little sanding. Then some more paint on the saddle.
How well does the mini split work in the machine room to keep things comfortable in the summer?
It’s OK up to a point – but I wouldn’t say it keeps it comfortable when the heat index is more than 90ish, but it keeps it tolerable. It gets clogged a lot from the dust, then doesn’t work at all. We had a repair person out a week or two ago, and we’re now supposed to suction both ends of the drain at least once a month, and clean the filters at least as often. It might, however, still be the best solution for the price – that, I do not know.
When finishing chairs with GF “milk” paint, have you found it desirable to topcoat with wax or anything else?
I just finished a chair with a coat of black over a coat of red and I’m liking it a lot.
Any favorite brush type and size for chairs with this paint?
I only topcoat if a customer demands it; it doesn’t need it. And as far as brushes, for the milk paint (and any acrylic paint), I like a 1-1/2″ or 2″ angled sash brush (smaller size if the sticks are closely spaced) – Chinex bristles from Purdy or Wooster. (I used to use only Purdy…but the company got sold in 2004 and the new ones aren’t the same.)
Any word when the design book Chris mentioned in a post will be available?
We don’t know. It got delayed at the printer (they are still working to find the perfect press settings – it’s a tricky one). When we know, I’m sure we’ll post about it.
Messed up a Mortise… its at the correct location, but the side walls are not straight along the face. Any thoughts, or experience, with plugging a mortise and re-chopping? Unfortunately I don’t have a replacement piece of wood for the whole leg. Thanks
I’m not sure what you mean by not straight. Does the mortise flare out toward the bottom /the walls aren’t 90° to the face? And have you cut the tenon already? if not, can you simply make this mortise a little bigger as you pare the walls flare and cut the tenon to match – or would it be so large as to compromise strength?
If one looks straight down the mortise (a birds eye view) the mortise shape would look like: —__—. Structurally, there is enough wood to afford widening the mortise to fix that. The tenon is rough cut, but I’m not positive there’s enough thickness to fix how wide the mortise would become. Which leads too adding (gluing) new material to the cheeks of the tenon and re-triming with a router plan. Or, cut bait, and plug the mortise and re-chop the now plugged mortise. But I’ve never known any one to plug and re-chop a mortise, which leads to a question of why has that not been done before to fix such a bad mortise? I was wondering if you might have insight into why that approach is not taken more often. Thanks again..
If one were making a 4-inch square cube, how could one plane the end grain? Such a cube is too large to use a shooting board but too small to support a plane. I often struggle to finish the ends of sticks, feet, and posts as I find them awkward to handle.
I’m afraid a sharp block plane, finely set, and some practice is the best way I know. Check for flat every couple of strokes with a square, and concentrate on high spots. You can make the end grain a little easier to plane with either a swipe of canning wax, or a spritz of a 50/50 combination of water and high-proof alcohol (we use 190-proof grain alcohol)
Hi Megan, here’s a follow up question to the one you answered last month. I am adding length -end grain to end grain- to my already cut dining room table legs in q sawn white oak. ( Adding 1 3/4” length.) I suggested screws, you said dowel(s) would be better option. I’d like your opinion on modification: epoxy the extensions to legs to stabilize, then drill four holes. One for a long SS screw in the center, then three bamboo 1/8” dowels around it. FYI, the legs taper to 1 1/2” square, and I will be using long drill bits. Screw is removable. Dowels are cuttable. I think I am ready to go for it….Thoughts?
Um…I’m afraid I don’t quite understand what or why. Wouldn’t it be easier to mate them with a dowel into each part (of the largest diameter that will fit)? My opinion is that, if I do understand what you’re planning, is that it seems complicated and not as effective.
Hi all,
I will be traveling to Edinburgh soon. Any chair/woodworking site that I shouldn’t miss?
Note: I will be doing some excursions to St. Fagan’s in Wales and the chair museum in High Wycombe.
Thanks!
I haven’t been to Scotland except for a short jaunt in a bus that was worthless.
The “chair museum” in High Wycombe is a turner’s shop. It’s a great – but weird – experience. The city’s museum (which had lots of chairs) went defunct. St Fagans is a must.
In Scotland, I have a long list (somewhere) of stuff to do. At the top is Hill House: https://www.nts.org.uk/visit/places/the-hill-house
And I want to get up to Orkney for the chairs from there: https://www.orkneyfurniture.co.uk/orkney-chairs
Highland folk museum: https://www.highlifehighland.com/highlandfolkmuseum/
V&A Dundee: https://www.vam.ac.uk/dundee
Whenever I plane a board along the face, starting from the edge, I notice the first few inches of the cut are scalloped somewhat, as if the plane blade is skipping as I start the cut. I am assured my blade is sharp, and I am planing in the correct grain direction. Is this a matter of plane adjustment, technique, or both?
If you’re talking about “chatter marks” as you start the cut (which I think is the case), I help students avoid that by 1. Taking lighter cuts, 2. Skewing the plane at the start of the cut 3. Starting to push into the cut with less of the planes sole on the board (that is, adding a little room to get up to full speed…like the opposite of follow-through)
Bench related question, I neglected to think about gripping material for my bench dogs (wooden square variety) for the workbench I’m building, and I was curious as to your opinion. I have leather, but it’s not specifically suede leather, it’s sheets of craft leather but it’s worked well on my aluminum bar clamps for grippy-ness and protection. Cork-rubber gasket material is also easy to obtain quickly. My question is, in your opinion, is the leather good-enough as is, should i really consider the gasket material, or is the Crubber brand that much more effective to be worth the extra dollars and time to obtain through the mail?
I’d try what you have. If it doesn’t work, it’s an easy thing to remove it and replace. (I have wooden dogs with no gripping material – also an option.)
The most durable grip surface is thin suede (in my experience). Followed by urethane rubber. Crubber is great, but it can get beat up and ripped to pieces like cork. Thick full-grain leather isn’t great either. Its cushiness tends to pull it off the wood after a lot of use (in my experience).
The only grip surface that hasn’t failed in our shop: thin suede glued on with PVA or hide glue.
That’s exactly what I’m talking about. Thank you!
If one looks straight down the mortise (a birds eye view) the mortise shape would look like: —__—. Structurally, there is enough wood to afford widening the mortise to fix that. The tenon is rough cut, but I’m not positive there’s enough thickness to fix how wide the mortise would become. Which leads too adding (gluing) new material to the cheeks of the tenon and re-triming with a router plan. Or, cut bait, and plug the mortise and re-chop the now plugged mortise. But I’ve never known any one to plug and re-chop a mortise, which leads to a question of why has that not been done before to fix such a bad mortise? I was wondering if you might have insight into why that approach is not taken more often. Thanks again..
Moved this “reply” to correct question… not sure how I got it posted here.
It’s not you – something is screwy with replies that we have as yet been unable to fix.
I’ve seen lots of plugged mortises; you can do that. If one area is significantly wider (as in your -_-), plug that first so it’s filled, then plug to either side with narrower pieces. You want it as solid as possible.
I recently built the staked work table from the ADB in cherry, using hide glue.
I thought I did a good job cleaning up the glue, but now that the cherry is darkening up, I see several large runs that I missed or didn’t do a good enough job removing.
This is, of course, after I already finished the table (which I’m using as a WFH desk) with Tried & True original (oil/wax).
What’s the best way, at this point), to backtrack and clean up the Old Brown Glue (which was maybe a bit too runny that day)?
The only fix I know is to scrape it off (both the finish and glue), then reapply the finish. If it hasn’t been too long, it’s possible a little sunlight will meld the new and old finished areas…but no promises. My approach would depend on where/how much it shows. E.g. if is on a facet that faces out on a leg, I’d scrape that entire facet, then reapply the finish. If it’s in a place that doesn’t show much, I might remove only where the glue drips are before reapplying.
Question using the Wood Owl Spade Bit: I don’t seem to get more than one chair out of a bit, which seems wasteful. By the time I finish drilling my armbow the bit is smoked. I’m sure it’s a technique problem but I’m not sure what I’m doing wrong. Thoughts?
The bits are made from thinner steel than I like, so they heat up too fast. If you can get a feel for them, you might get 2.2 chairs out of one. The trick is to find the feed rate and rim speed that cut efficiently. And to let the bit cool down between deep mortises.
The good news is that most recycling center love to get them….
Thanks Megan, last question on table legs, I promise. You have been persistent that one thickish dowel is the way to go, not multiple small ones.
My concern is that the leg extension, once it is attached to the leg, could loosen and rotate.
If that were to happen, I guess then I just shove the extender with dowel back on with new glue. I think I just answered my own question.
I really don’t think it will fail – at least not in your lifetime. But use hide glue just in case. With it, you don’t have to scrape off the old to add new (as you do w/all other glues I’ve use) – so the joint geometry won’t change!
But if you’re really worried, you could thread the dowels and hole, like campaign furniture feet, and glue them in, a la https://campaignfurniture.com/campaign-furniture/campaign-seating/pair-of-campaign-foot-stools
On the advice of my heat pump guy, I went with a Cooper Hunter for the shop. The blower wheel comes out pretty easily with minimal or no tools. The filter on the top seems to do a good job keeping the heat exchanger free of dust provided I clean it regularly. I try to avoid running it when I’m sanding, and run a ceiling-mounted air filter.
We also have an electrostatic air cleaner, and we clean the filters regularly. I was cleaning out the water port, but it got clogged downstream in the pipe.
Heat pumps can only do so much in extreme weather. We are now investigating other options to help, including an exhaust fan that we can use to blow out the hot air in the mornings to start with a cooler structure.
We do not have the space for a traditional unit, though I wish we did.
Hi all,
I built and have been working on an English workbench for a few years, but it’s gotten to a point where it’s a bit cumbersome to work on due to the width of the front apron and wanting different work holding options. The frame is actually designed around the AWB and the front apron is inset to the legs and bolted on.
With the amount of time and effort it takes to build a laminated top, is it even worth considering retrofitting it to this existing frame/legs or is time better spent working on a new bench?
If you have an AWB base, it seems you are almost there. Add a new top, remove the apron and you are done???
Another option is to thicken your existing top with a couple layers of construction lumber (and removing the front apron).
Are Bean and Funky Winkerbean two different cats, or is Bean merely the short form for the same cat?
They are different cats. Bean is the three-legged cat. He has gone to live with my daughter Katy (inset sad face here). Funky Winkerbean is my wife’s loyal steed.