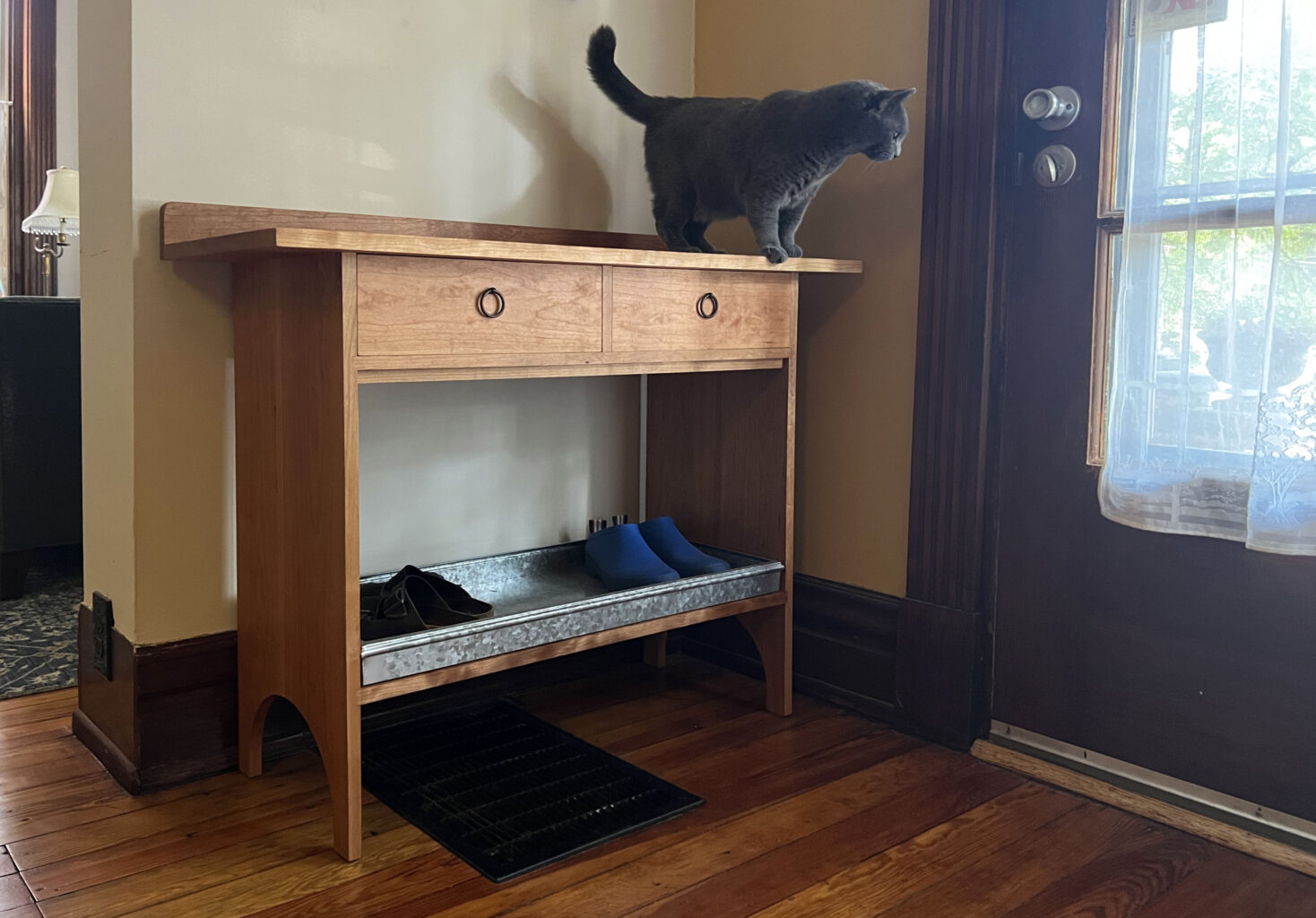
I have a small flower garden in front of my house, and after years of being annoyed by having to sit down on my porch to don an old pair of running shoes for weeding (and checking them for spiders first, because they lived on the porch), I finally broke down and bought myself some garden clogs. They’re easy to slip on and off as I walk in and out the door, which is great, but I don’t want to leave them on the porch (they are much more likely to take a walk than my nasty old running shoes). But then I got annoyed by the amount of dirt I was tracking into the house, and bought myself a galvanized steel boot tray. But…just inside my front door is an HVAC return, so the boot tray had to go across the hall, and well…that was a good excuse to build a piece of furniture* to hold it – something that could fit just inside the door to make it easier to stow my clogs, and provide enough space underneath to allow for air flow.
Before all I built was tool chests, my M.O. was to find a Shaker piece that I like and modify it to suit my space, needs or both. So I went back to my old ways and spent a few days leafing through the various Shaker books in the Covington Mechanical Library.
I had almost settled on a washstand when Will Myers dug up a photograph of a piece illustrated in “The Encyclopedia of Shaker Furniture” by Timothy D. Rieman and Jean M. Burks (Schiffer, 2003), and in volume 2 of Ejner Handberg’s “Shop Drawings of Shaker Furniture and Woodenware” (Berkshire Traveller, 1975) – a “Bake Room Table” that was in the North Family Dwelling House at Mount Lebanon. I liked the drawings, but didn’t fall in love with the form until I saw the (unique) table in a photo.
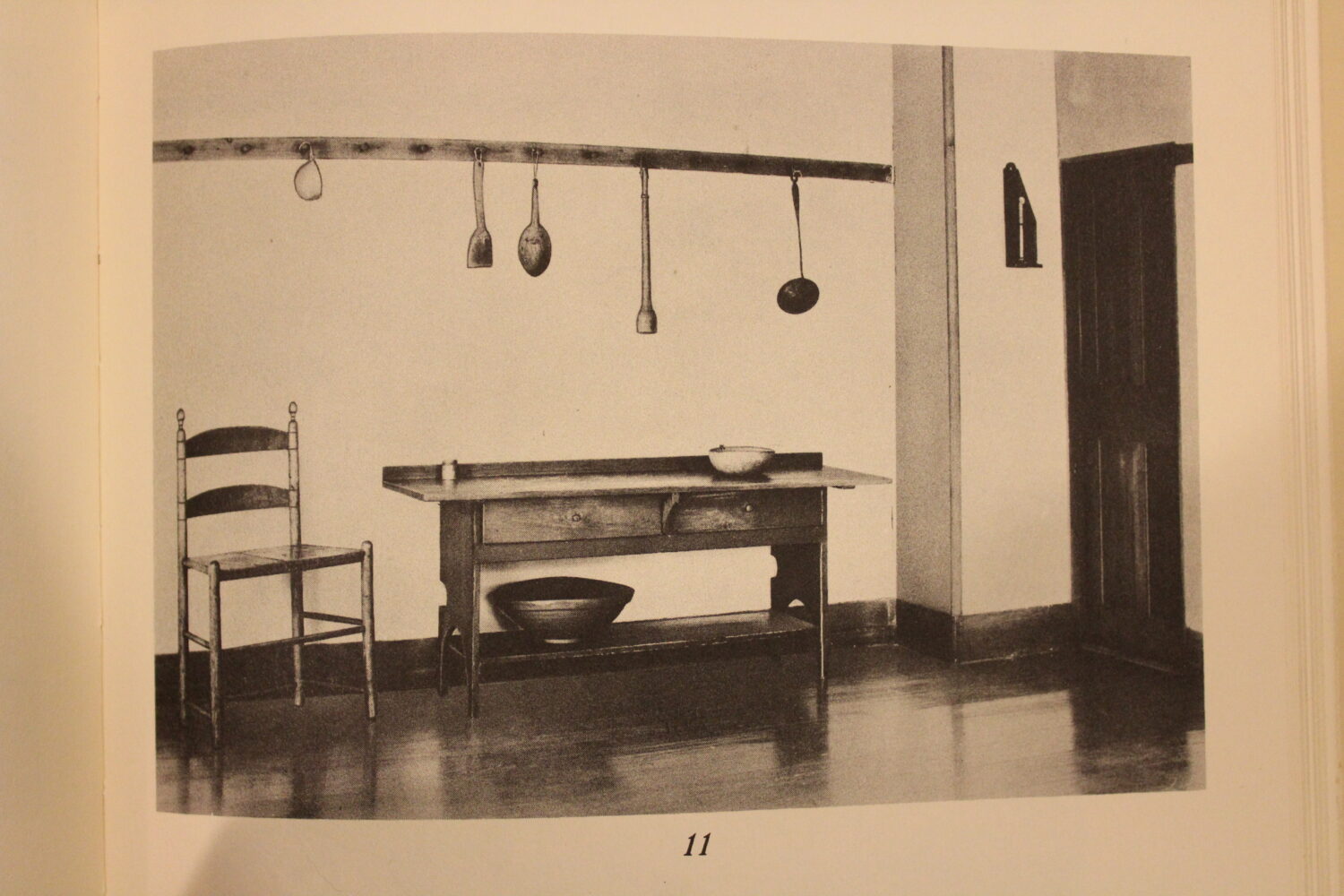
The shelf that cuts across the side cutouts was, according to Handberg, probably added later. And what are those round cutouts at the back? Maybe it fit around a pipe of some kind?
The original, at 66″ long and just more than 28″ high, looks lighter and more graceful than what I made, but I didn’t have the space to copy its size. And I chose to make the cutout at the feet a bit shorter so that I could fit the shelf (my entire reason for building the piece!) above the void. I also skipped the support at the front between the drawers; the overhang on my top wasn’t enough to require it. Still, it was the starting point I needed – that, and the size of the boot tray it was destined to hold.
I also changed the construction, with a 3/4″-thick solid dust board (or perhaps it should be called a drawer support, given there are no drawers below it?), dadoed below the drawers instead of the nailed-on 2-1/4″-wide rails front and back, and nailed-on runners (if Handberg is correct). That last decision was a tactical error; the wider board provides more protection against racking…so I ended up pocket screwing (go ahead – come at me; there are period pocket screws in plenty of Shaker and other period work) a rail behind the drawers and under the back of the shelf (likely overkill, as I am wont to do).
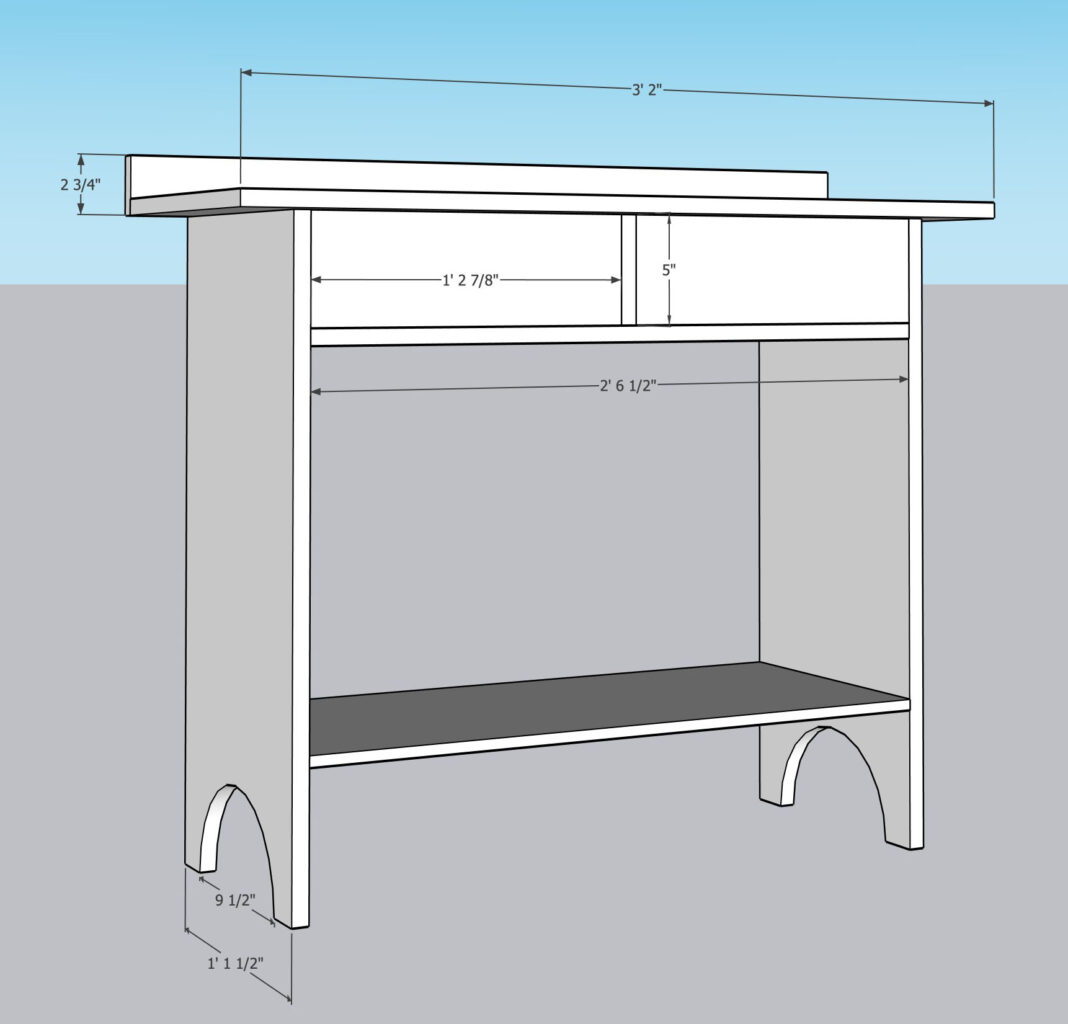
And instead of classic Shaker wooden pulls, I used iron ring pulls, to match the iron nails that attach the top. As a result of its almost-square form, size and metal hardware, I think my result skews a bit Arts & Crafts.
It’s a simple build for a simple customer. Were I building this for a more discerning end user (i.e. one that is paying me), I’d probably use sliding dovetails to attach the dust board/drawer support (and possibly use a web frame instead of solid wood there) as well as the drawer divider, and inset the back rails in grooves. And my drawer dovetails would be better.
The Build
I started by gluing up the side panels and drawer support. All the wood that shows is cherry, but I glued up the drawer support from a 5″-wide or so piece of cherry on the front, and poplar behind. (I guess it does show at the back to the cats, but they don’t care).
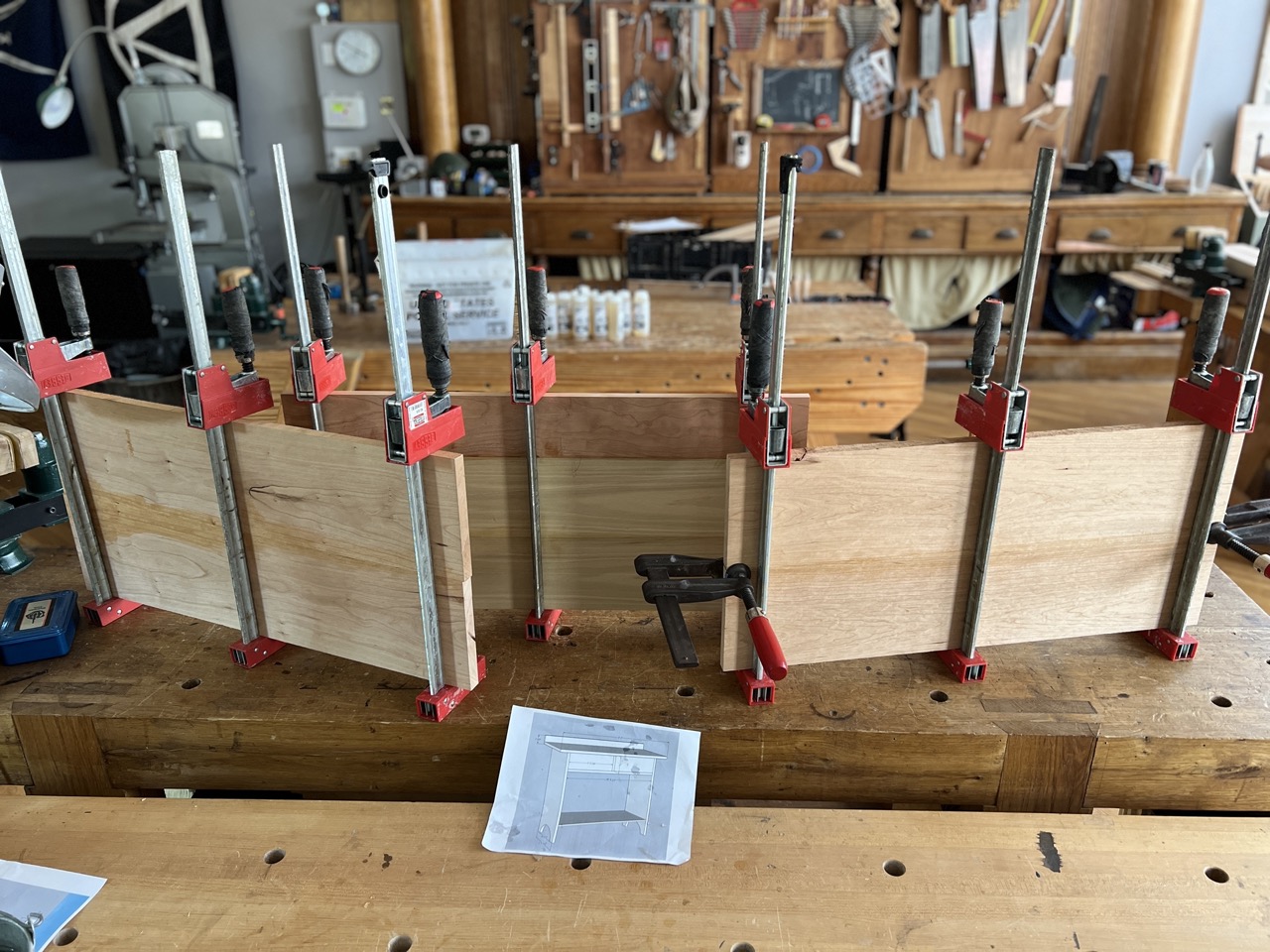
Then I marked out the dado locations, and played around with the curved cutouts at the bottom – and I ended up with curves that are slightly higher than what I drew. I cut them out on the band saw, then cleaned up the cuts with a combination of the spindle sander and sandpaper (#120 and #180) wrapped over a piece of the cutout (a sanding “fid”) to clean up the rough spindle-sander scratches.
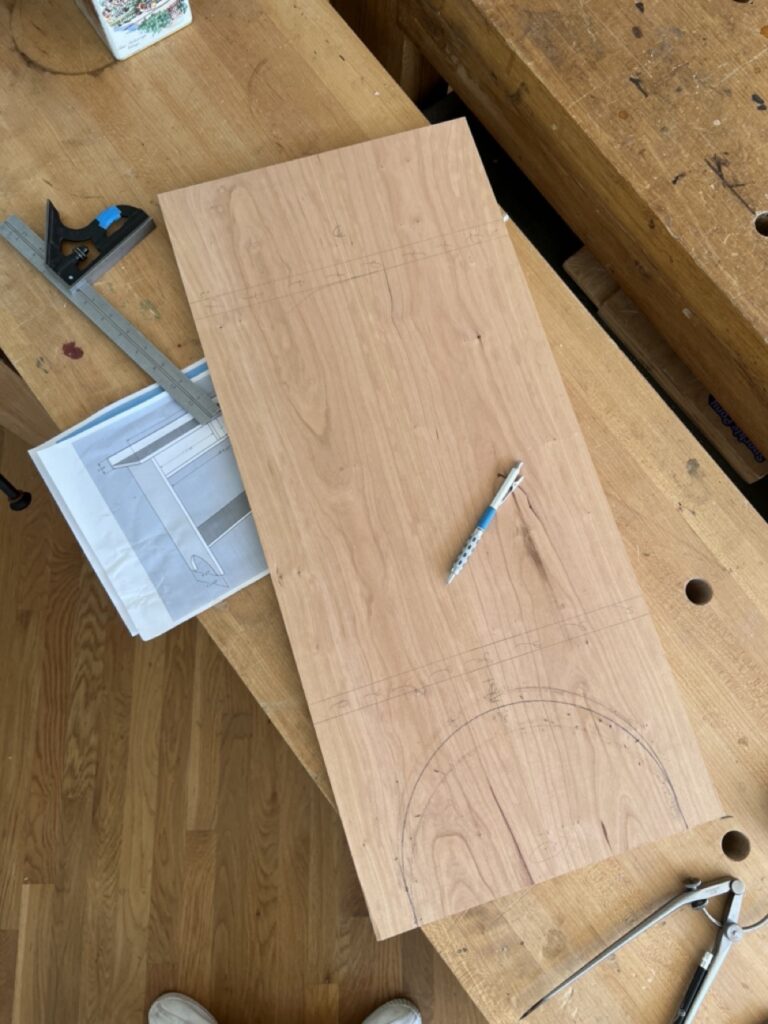
Then, I sawed the walls of the dados (which are a 1/4″ deep), knocked out most of the waste with a chisel and cleaned up the dado bottoms with a router plane (there’s a video here of this process, should you care to watch).
With one side arranged dados-up on the bench, smear a bit of glue in the dados, then put the shelf and support in place. Brush glue in the mating dados then put the other side in place on top. If the shelf and support are held tightly in well-fit dados and not moving around once they’re in their housings, it makes glue-up a lot easier to handle by yourself. If your fit is too loose, knock a wedge or two in on the underside to push out any gap and tighten things up. After the glue is dry, you can use a chisel so cut off the protruding end of a wedge (or, if it’s below the shelf at the bottom where it won’t show, just leave it).
Then, lift the assembly to get clamps across it front and back at the dado location and check it for square … then foolishly move the now-quite-heavy assembly off your bench and onto the floor by yourself because it will look better in a picture that way. Be sure to then complain that your back hurts.
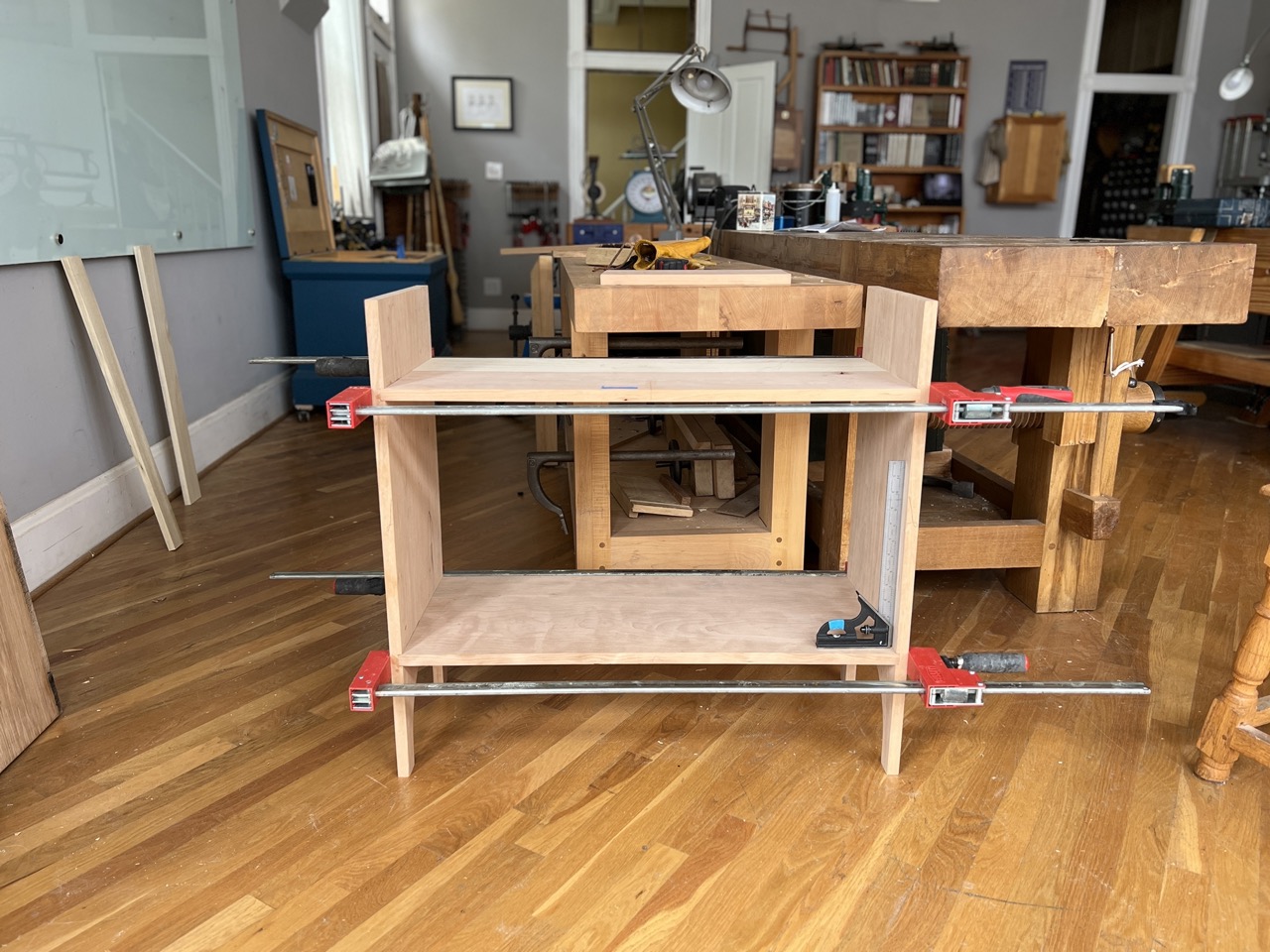
After I took the clamps off, I realized I was being boneheaded; the piece needed some wider horizontal members to keep it from racking. So, I pocket-screwed 3″-wide rails between the sides at the back above the drawer support (poplar) and below the shelf (cherry). Then, the right side developed a slight cup at the top front – and I was afraid it would get worse. So, I pocket-screwed a 3/4″-thick x 3″-wide piece of cherry about 1/2″ back under the front of the drawer support. Uh … it’ll create a nice shadow line.
Tangent: I should have known things would go at least a little bit wrong. Some of the cherry I used for this piece is cursed. I’d bought the 5/4 stuff in mid-2017, with plans to build a Stickley 808 server for a Popular Woodworking article. I was seduced by the wood’s curly grain and remarkably low price … even though I knew curly cherry could be a right royal pain in the butt at the best of times, and that the low price indicated it was already misbehaving. But … so pretty!
I commissioned reproduction hardware from John Switzer at Black Bear Forge, and stickered the wood to acclimate for a month or so in the PW shop. Then I surfaced it to 7/8″ and glued up my panels. It all looked fabulous. For about a week. Then all the panels developed a gentle cup. OK – I could flatten it again, and build the piece out of 3/4″ instead of 7/8″. It happened again. So I put the panels aside and decided to build the server out of white oak, just like the originals. I bought the oak … then I was no longer employed at PW.
Those cherry panels left PW with me, and they’ve been in the basement at Lost Art Press ever since. (John’s gorgeous hardware has been in my basement ever since.) Chris recently used one of the panels as a desktop across trestles. And after flattening it and putting heavy stuff atop it, that panel has remained flat; I thought the curse had been broken. Chris says he’s protected from it there is no joinery involved in his setup.
The curse was not broken – but the addition of a front rail seems to have at least overcome it. For now. But never forget that wood hates you.
After the clamps were off, I marked centerlines on the drawer support and 5″-wide drawer divider, then clamped the divider firmly in place, and countersunk screws to hold it in place from underneath. It is simply butted tight to the underside of the top.
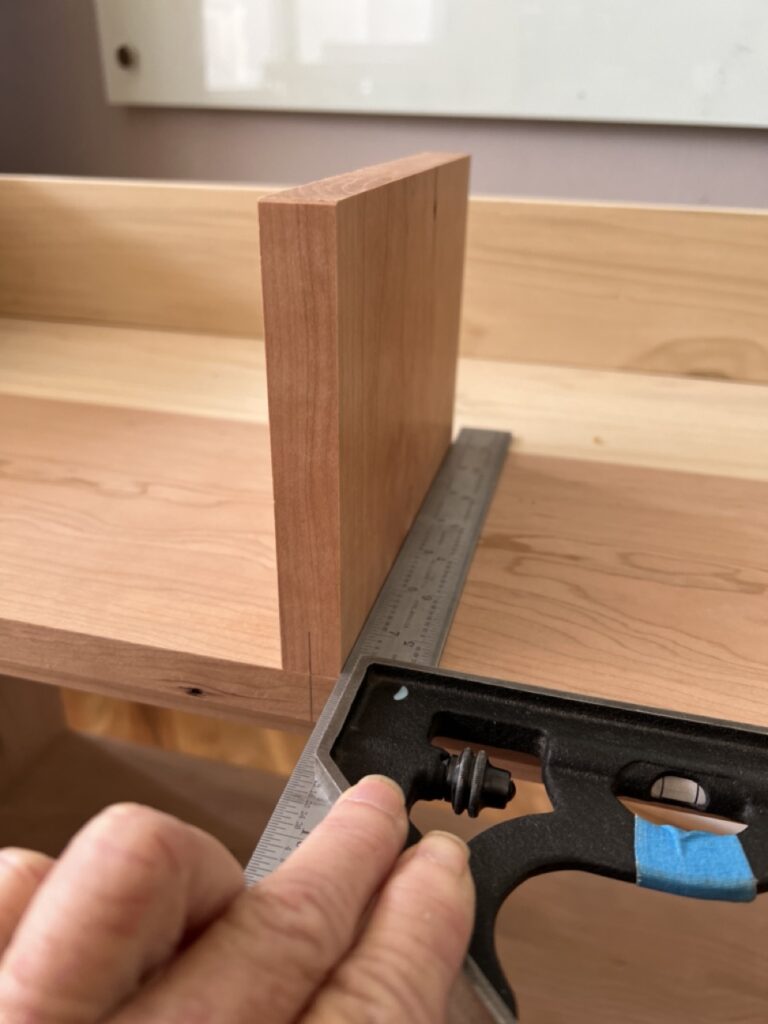
I had a beautiful wide piece of cherry from C.R. Muterspaw for the top that I sure wish I could have used at full length. Not only was cutting it painful, but I think a longer overhang to either side added lightness – but rendered it not fit for purpose.
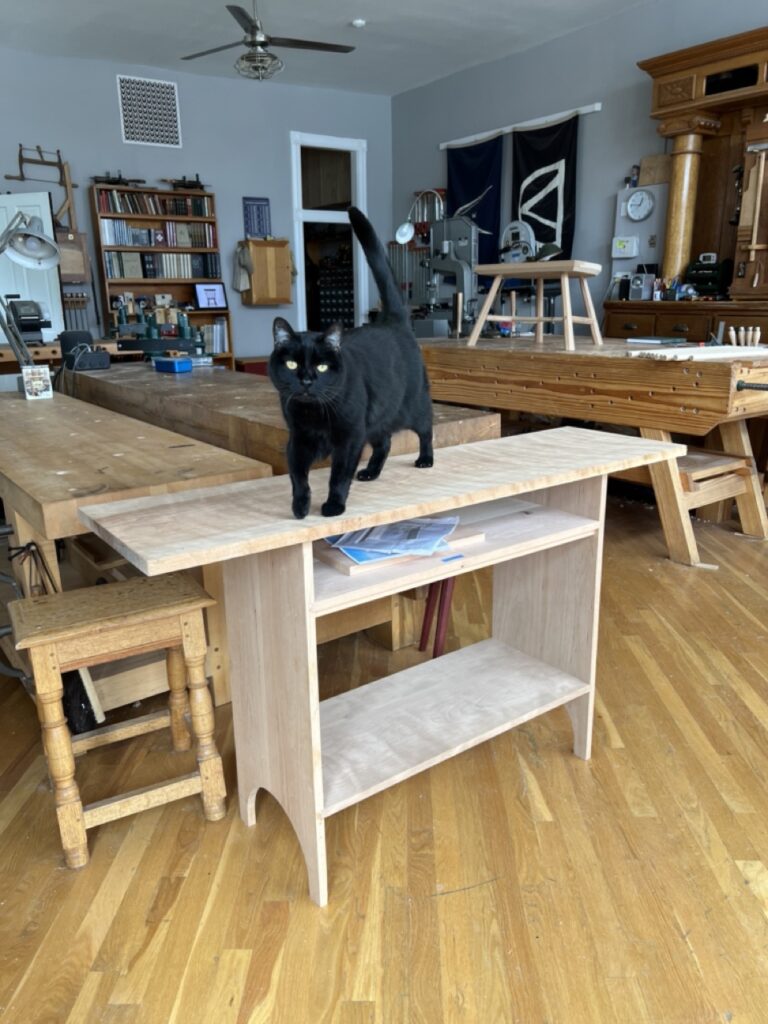
I cut a small roundover on each end of the top’s back rail, sanded it, then glued it in place to the back of the top. I could have gotten away with leaving it off from a functional POV, but I wanted the extra overhang that offered for the front edge.
I then dithered over best to attach the top, and after considering the use of traditional buttons (which would require 1″ shorter drawer sides and backs to accommodate their attachment), had decided on figure-8 fasteners (which would require drawers sides and backs only 1/8′ or so narrower than the fronts), when Chris talked me into using blacksmith-made nails. I liked the way they looked on the cupboard in “American Peasant,” so…
The only great-looking nails we had (they were made by Mark Kelly, a blacksmith at Mt. Vernon) were 2-3/4″ long; I really should have used 2″ nails. It was a bit scary to drill so deeply into the cherry sides. But I got away with it… or so I thought for about 14 hours. I did a test drilling setup for tapered pilot holes, and after successful tests drilled my pilots and hammered the nails in place. They looked great. Whew! By the next morning, a small split developed at one location. But you can’t really see it without bending down and looking closely. And I’m not showing you.
The customer is dismayed but accepting of the flaws. (I blame the curse.)
Further adding to the flaws count: It turns out I didn’t get the divider perfectly centered; the left opening is 1/16″ smaller than the right. So I fit each drawer front and back to its opening with a No. 51 shooting plane. For those who don’t already know, a tightly fit drawer is key to smooth movement. These have maybe a 1/32″ reveal side to side. (And wood movement won’t be an issue, as that will be top to bottom, where I left about 1/16″.)
Another tangent: Years ago, I erred on the side of too loose, and those drawers bug the bejeezus out of me to this day. It’s this piece – the drawers, which have just under a 1/8″ reveal on both sides, rack every time I slide them in. Yes, I have some thin UHMW tape…no, I have not yet applied it even though I know it would likely solve the problem.
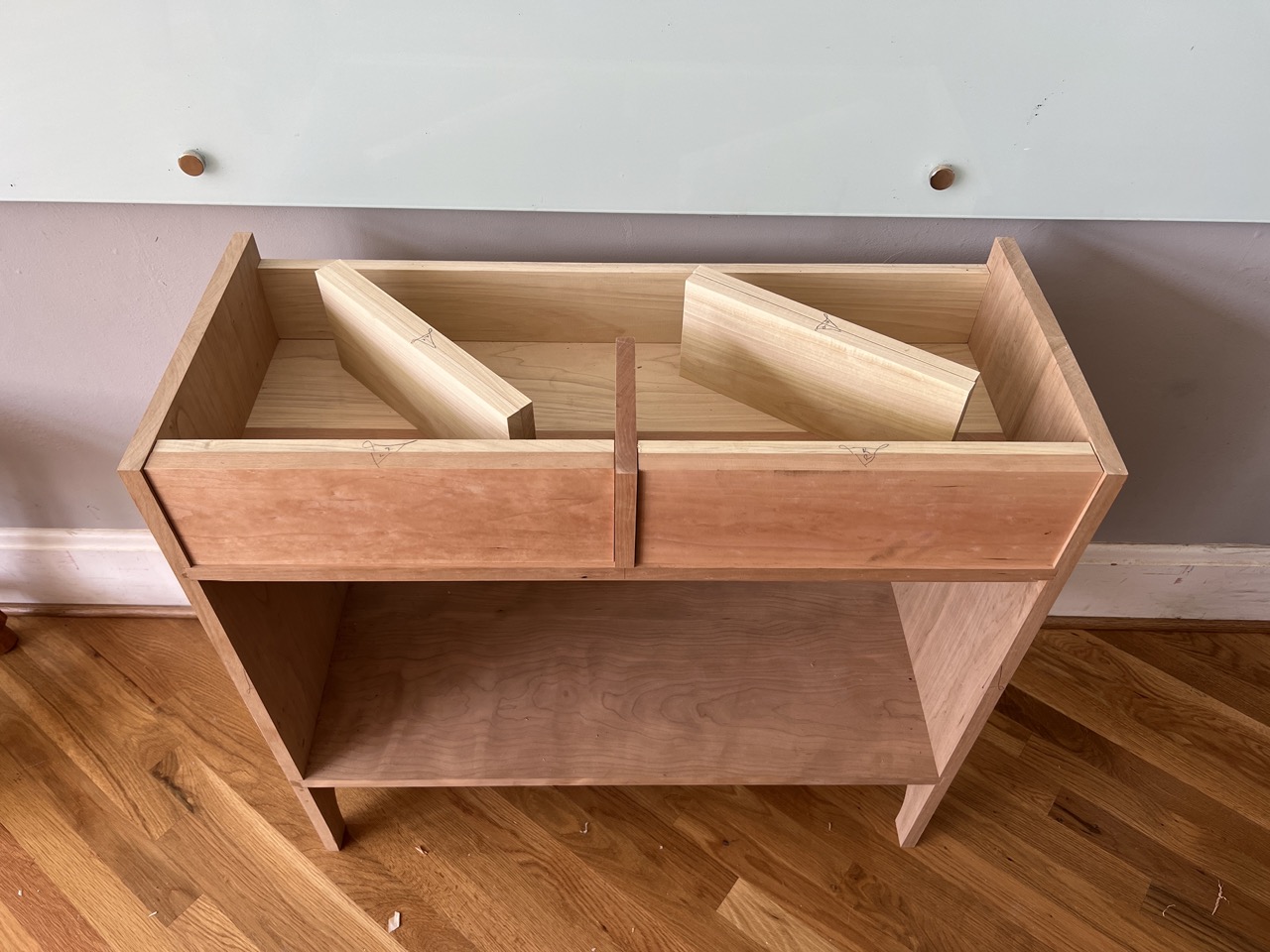
The drawers are half-blind dovetails at the front and through dovetails at the back (the tailboards are on the side, so that the drawers can’t be pulled apart in use). The only advice I have on cutting drawer dovetails is to run the grooves for the drawer bottoms before transferring the tails to the pin boards. That way, you can stick a shim of the right size in the grooves to help align the pieces (a trick I’m pretty sure I learned from a Chris Becksvoort article in Fine Woodworking).
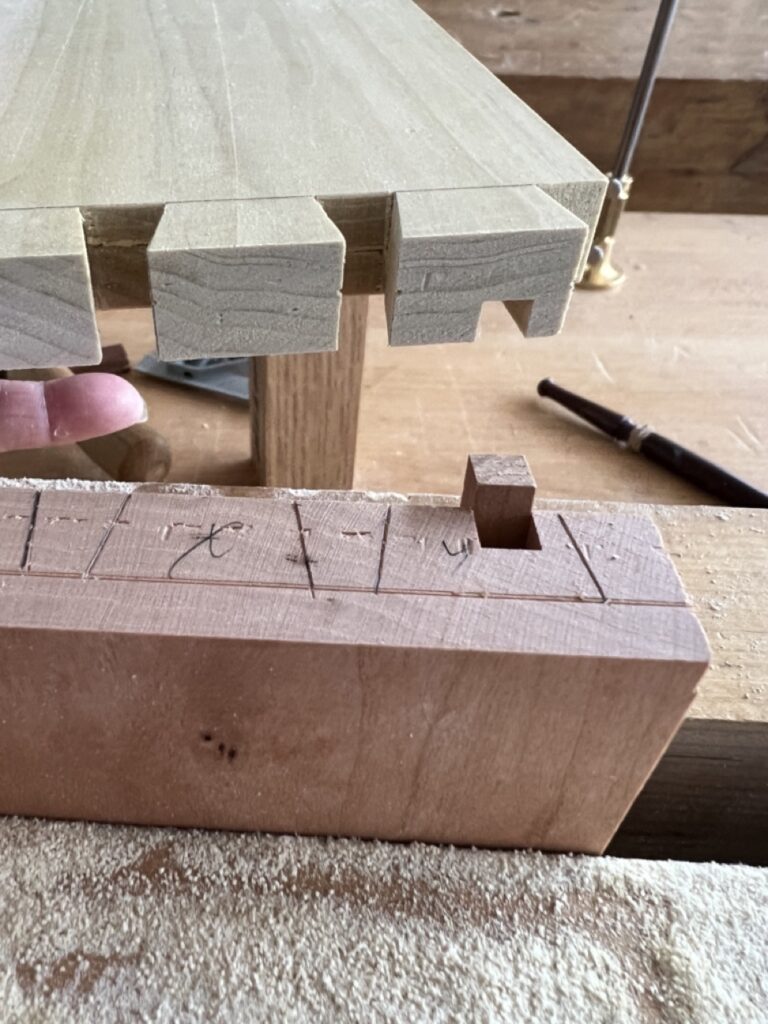
The drawer back is 3/4″ narrower than the front, to allow the bottoms to slide in underneath it. The bottoms are 1/2″-thick paint-grade plywood, rabbetted to fit the 1/4″ wide x 1/4″ deep grooves. I cut a slot in the center back, then nailed it to the underside of the back to keep it from moving. (A more discerning client would get solid wood, sized to allow for expansion and contraction – but that’s not an issue with the plywood.)
I cut half-blinds so rarely that I can’t remember if I prefer to secure the board vertically in a twin-screw vise or flat on the bench to make the cuts. These were cut in the vise – but I think my overcuts end up longer – thereby making the waste in the corners slightly easier to remove – when I clamp it flat to the bench. (Yep, I know lots of folks pooh-pooh overcutting. “Whatev,” as the kids haven’t said for some time, now. There are plenty of period drawers that employ overcuts; I’m in good company.)
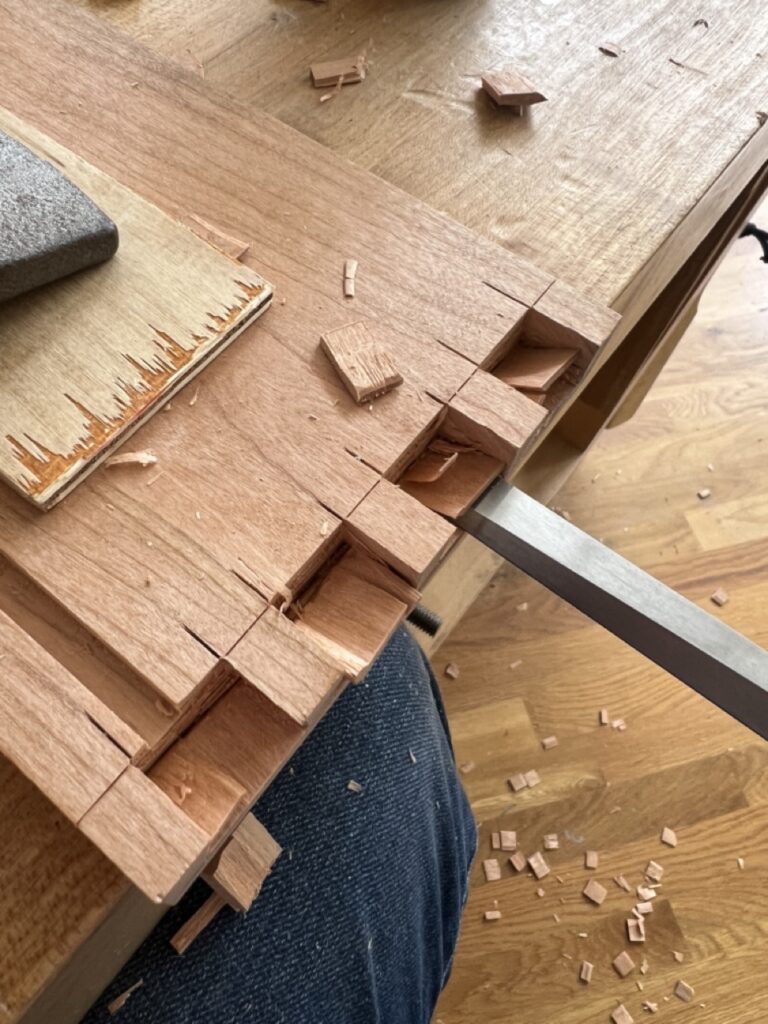
And to finish things off, instead of leaving blue-tape pulls in place for years, I decided on traditional iron ring pulls (32 mm). Simply drill a hole where desired to fit the staple legs, then bend each leg back with a pair of pliers, and hammer the staple legs in place. I decided to locate the pulls slightly above center. I taped off the location, marked the hole, then drilled it over a backer board so as to avoid blowout on the backside.
The finish is soft wax 2.0 – easy to make, safe to use and simple to re-apply if it proves necessary. You’ll find directions for making and using it in Chris’s latest book, “American Peasant” – a free PDF download (see pages 65-7).
Now that my new piece is at home and in use, I’m confident the Curse of the Curly Cherry is finally broken … as long as the drawers and tray stay in place, covering up that cursed wood. (But I remain leery of using the two panels still in our basement!)
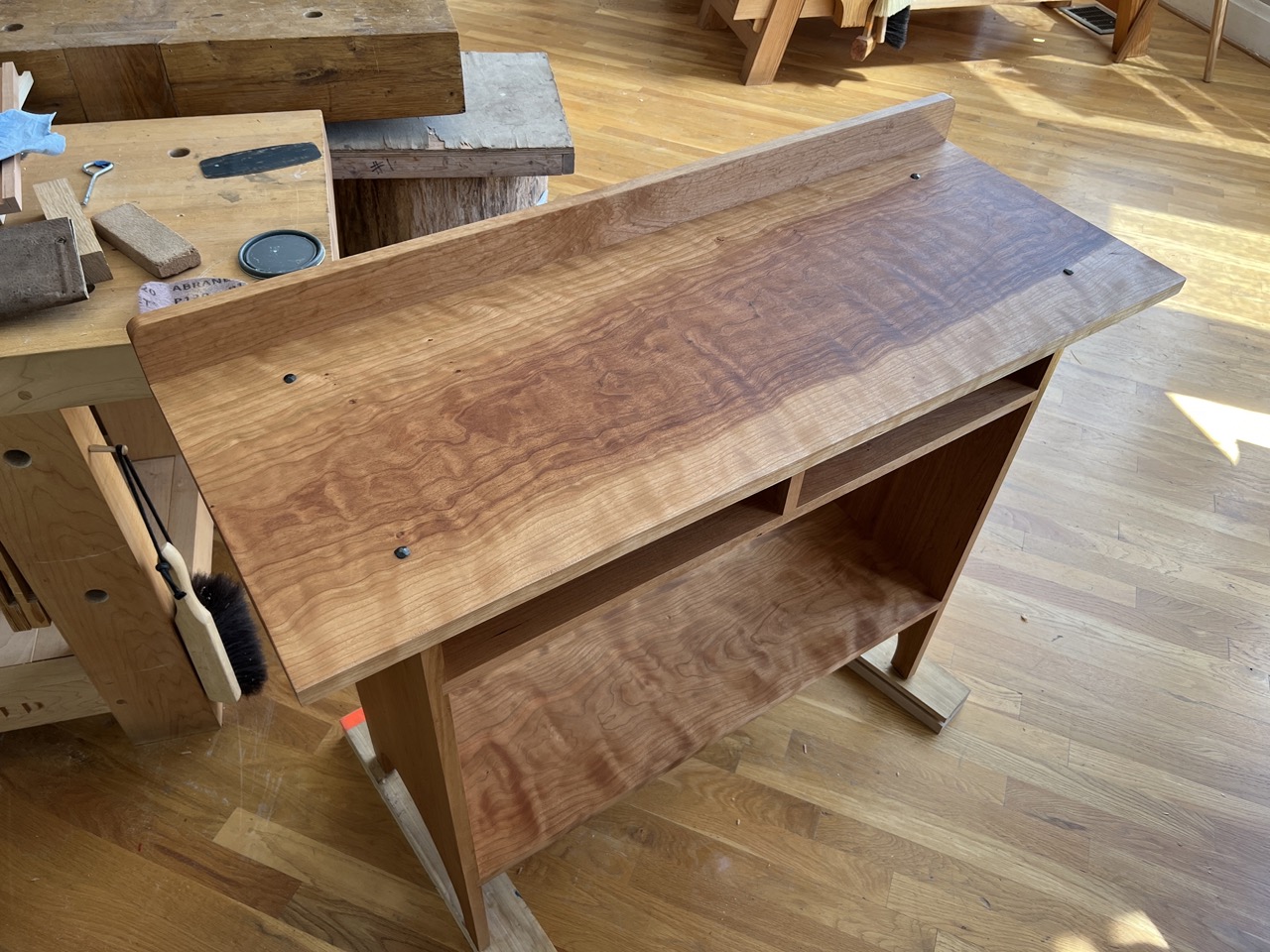
And if I ever get to make this again, well, I’ve identified all the problems! If I call this one a prototype, maybe the mistakes won’t bother me as much. (They will. That is my curse.)
– Fitz
*aka a procrastination technique to put off building a pantry cabinet or the bookcase for the bottom of my staircase.
It’s nice to read an article that mentions all the little mishaps and compromises that come up. Every project I’ve ever made has had plenty. In the end, they don’t matter.
Did you size this to fit a stock tray, or was the tray made to fit?
And if I can ask, what fret saw blade do you use for dovetail waste?
That really is a lovely piece.
Thanks, John! I wanted to have a custom copper tray made…but then I came to my senses. That’s a stock tray, so I built the piece to fit it; I think I got it from Plow & Hearth.
Smart.
I poked around at that site but couldn’t find the tray in question. But I think I found it elsewhere?
https://gooddirections.com/products/classic-galvanized-multi-purpose-boot-tray
That looks like the same one (I bought it probably 6 months ago…so I am likely wrong about from where!)
Oh – and on the fret saw blade: Usually a Pegas No 7 skip-tooth
This is such a clever and fun design to replace a boot tray. We all need a Fitz Modified “Bake House Tray” by our front doors. Thank you for such a great post!
Very nice piece. I like the clean lines of the Shaker furniture. My cat Charlie would also find it a good place to nap. Thanks for sharing it with us.
Could you explain the piece of wood that’s mounted under the shelf the draws sit on? It runs the full length of the shelf but seems inset a bit. I can’t tell what the width is. Does this add some stability? Is it glued to the underside of the shelf? Sorry, this is probably explained in the article but my brain just isn’t processing it.
It is in the article – and why. It is pocket-screwed in, and holds the sides tight…because the wood is cursed.
Nice! A lovely and practical solution to a common problem.
Absolutely love it, always loved furniture with a purpose
This reads like a segment of a book. Dutch Tool Chest is done… What are you up to? Love the work and the choice of blacksmith made nails.
My question is on nail placement. Looks like just four nails- I’ve always had a hard time determining the number of fasten points for a top, be it a trestle table, a dresser, or a piece such as this. Assuming that people will inevitably lift it by the top in the future, will 4 nails be enough to hold? How do you determine when is enough and not garish overkill?
To me, it reads like an unedited brain dump, because it pretty much is! (I’d add more detail on techniques for a book or magazine article.)
On the nails: We only had 5, so… that made the decision easier.
Had we 6 on hand, I’d have probably done 3 down each side. And by the time it gets picked up by its top, I (likely) won’t be around to care. But I do think 4 per would be overkill.
Any reason you didn’t cut the nails down to the length you wanted?
They’d be awfully hard to drive w/out the point (the “rule” I follow is drill the pilot about 2/3 the length of the nail; the final third is cut by the nail’s point, and provide a lot of the holding power…I’ve been told)
Very nice piece, clever design and it fits perfectly in the space. Well done! Also great post, and the composition of the pic, the lighting, and Olivia looking out the door is excellent.
Nice piece and blog post…about John’s question about fret saw blade used for waste removal – care to elaborate on that question please.
A few years ago I made a bedside table loosely based on a design by Richard Maguire. Following his advice I overcut the blind dovetails in the table draw. I then completely forgot that I had done it. My wife and I must have opened the drawer thousands of times without noticing the overcut. Now you mention it I specifically went to look. I can’t see the cuts. Maybe if the drawer was not at knee height and with a bright light….. Historical precedent aside I make furniture for my own pleasure and that of the recipient and I don’t give a tinkers cuss for the opinions of “Purists”. End of rant.
Don’t you just hate it when you come to your senses?
Nice piece. It kooks great.
This ☝️was supposed to be up above where you were talking about the copper tray. I replied up there but it showed up down here.
I do love Cherry and that curl is just beautiful, I’m afraid I wouldn’t be able to walk past that stack myself (cursed or no). I bet that top shimmers like crazy when you walk by with any sort of raking light hitting it.
very nice piece fitz! it’s also nice to see an entry about case work for a change. i do enjoy the chair posts and am steadily being brainwashed into making one 🙂 but we need some balance in the force.
Megan, are these the kind of nails you used? I’ve never tried nails before but I like the faceted look of the heads, and I’m thinking about trying them on a box or small cabinet. Any sources you would recommend? https://1drv.ms/i/s!AvFMTCyuN5Xzg6NWkHNd2f0BBJDtTA?e=A2K8q5
These are hand forged by a blacksmith. The Rivierre nails (I think that’s what’s in the picture you included) are machine made, but still nice. I use them on lots of tool chests. They are available from Lee Valley.
Thanks, I should have read more carefully. Nice work! It’s given me some ideas for a small cabinet by my front door.
I love this. Thank you!
Did you ever end up building the Stickley 808? Would love to read that article still.
I did not. Maybe I will, one of these days – the spot in my house for which it was destined is still open.
Nice build. I am going to need to make one. Question: All the links in the article seem to point me to Meet the Designer: Tom Bonamici. Is this something in my browser setting that is making the links generic?
Hmm…that’s odd. I just tested them, and they all go to where I meant them to. So I’m not sure what’s causing that for you.
Great article. Gives me some great ideas for a project I’m way late starting on. It’s a pleasure to read about mishaps and on the fly design mods. Very refreshing and quite helpful. The end result is so nice. I do have one sentence I couldn’t parse in my foggy brain though: “The drawer back is 3/4″ narrower than the front, to allow the bottoms to slide in underneath it.” Would you please enlighten me. I’ve read it over and over, but I must need more coffee to sort it out.
Say the front and sides are 5″ wide – and they have a groove 1/4″ up from the bottom edge. The bottom (in this example) is a 1/4″ piece of plywood. So, you’d make the back piece 4-1/2″ wide, and flush it to the top edge. The 1/4″ drawer bottom can then side in under it, into the groove. (And I typically nail it in place with a single nail at the back center, to keep it from sliding out). I’m sure we have an example on our site…but this is the one that comes to mind for me: https://www.popularwoodworking.com/techniques/four-good-ways-to-build-drawers/