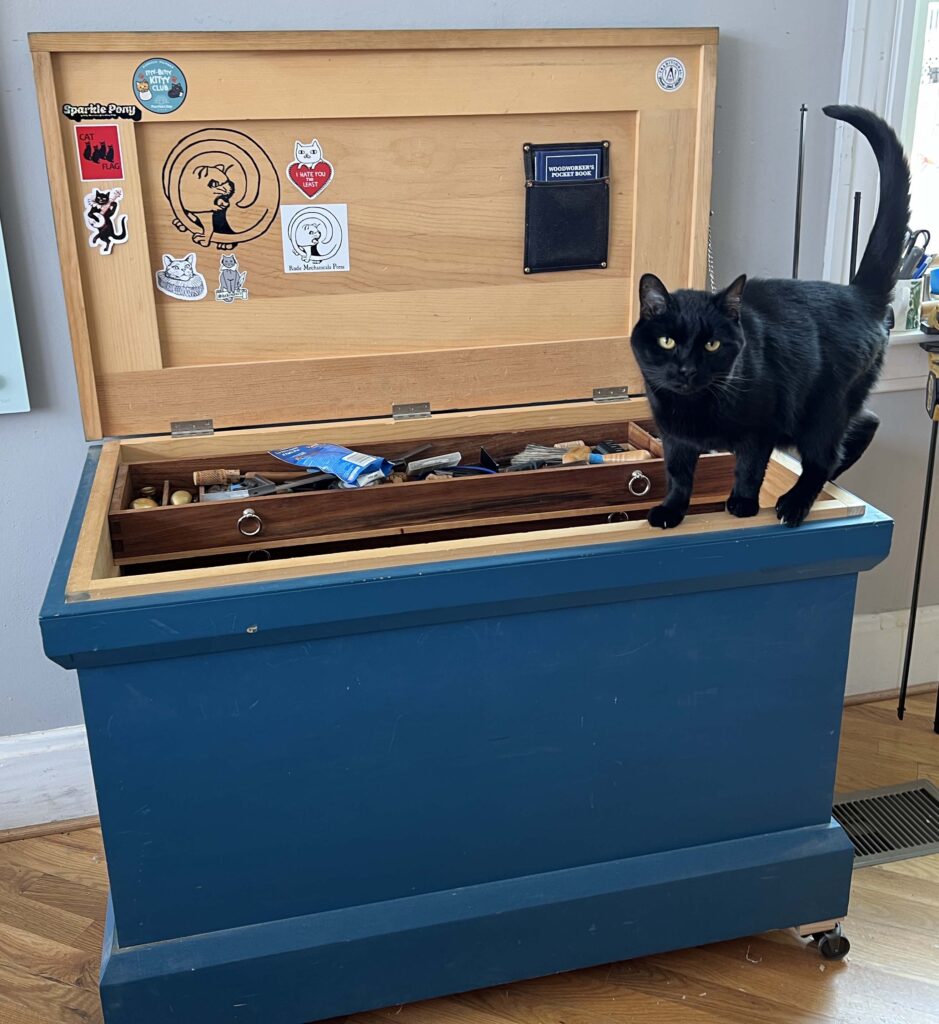
Comments are now closed. Join us again next Saturday!
Chris is out of town this weekend, but Wally and I are here and ready to answer your woodworking and cat-treat-related questions. But unlike Chris, I will not start responding at the buttocks-crack of dawn – I like to sleep in a bit on Saturdays. And every day. (And Wally sleeps about 18 hours per day.)
As you surely now by now, leave a question in the comments and I’ll do my best to answer. You can even ask me about the Dutch tool chest book (now that the manuscript is in Chris’s hands, I’m far less stressed about it).
Comments will close at around 4:30 today.
– Fitz
How’s Bean doing? Sufficiently pampered? Tell him we said Hi.
Overly pampered!
Two ATC questions. When making ATC tills is there a minimum gap you recommend between tills? I already built the shell, and was thinking a bead around the top skirt would have been nice to prevent damage. Seems risky to add a bead once it’s already installed. What do you think? Thanks!
I usually add the bead (or a bevel) after the skirt is on; just make sure to attach “spelch blocks” on the ends to protect the cross-grain exit as you come out of the cut. And on the tills, I have maybe 1/4″ gap between them.
I just recieved the Set & File book, which made me think what determines the dimensions of a book when you are laying it out? I assume things like pictures,diagrams,etc but thought I would ask
Efficiency of materials (8-1/2 x 11 and 6×9 are the most economical in terms of paper usage v waste after trimming) and the design needs. With lots of pictures that relate to text, 8-1/2 x 11 is more flexible (if you want the pics with the text). We’ve done a few larger-format books, but they cost more to produce and they waste a fair amount of paper.
Interested in your thoughts on this: https://youtu.be/ZLkco_yr1aw?si=LInBO4PJOgqrC8dS
I genuinely thought it was an April fools joke at first, then I remembered we’re in June…
Erm…I’m begging off comment. I haven’t used it, so …
I’m not one to poo on products I haven’t tried. So I won’t. But I don’t see the form and think: I should try this.
Will you be sending Set and File to Lee Valley Canada?
Also, shoutout to Otelia d’Alsace from last week’s open wire for answering a question I had from 2 weeks ago, greatly appreciated.
Whether or not our distributors carry any/all of our books (and tools) is up to them. We hope LV carries it of course, but that’s a question for LV, not us.
This might be anathema, and force my expulsion from this group, but here goes: thoughts on using 1″ ply for the ATC frame? I have access to a couple free sheets and wood is SO expensive here in CA.
Don’t kill me…
@cravenconservation on Instagram built a traditional plywood tool chest – you may want to have a look.
@Jake Ahronian Chris built a plywood ATC for a pop wood video. https://youtube.com/playlist?list=PLOUEnRdBNW4PsmAENQb-Y9UzrHnXzUjqc&si=8YhwXou_iUHGL6B8
Chris made a video on building a plywood tool chest for Popular Woodworking. You can find it on their YouTube channel
Chris did a video series on this while at PW. It’s all on YouTube: https://www.youtube.com/playlist?list=PLOUEnRdBNW4PsmAENQb-Y9UzrHnXzUjqc
I second all the other commenters on prior ply use (which is to say, use what ya got).
I made one out of plywood following Chris’ video and have been working out of it for years, I love it.
In the stick chair book Chris shows a sled for making octagonal sticks at the band saw. has anyone tried making a sled for hexagonal sticks? i imagine it’s just a case of changing the angle from 45 to 30 degrees?
See pg 169 through 174 or so in “The Stick Chair Book” (free download here: https://lostartpress.com/products/the-stick-chair-book?_pos=1&_sid=8a3fe36c4&_ss=r)
yes i have the book and those pages talk of a sled for octagons. but i see no mention of a similar sled for hexagons. has Chris or anyone made a similar jig for hexagons?
Ha, I look forward to a future “Never Sponsored” review in that case!
In theory, it seems like the ATC tills could be as wide as half the distance from the front of the tool rack to rear of the interior. In practice does that hold up, or are they more usable a little narrower?
Not a tool chest expert, butine are 1/3 the depth of the chest so I can stagger them and see the contents at the same time.
Mine at home has tills of half the f to b measurement…’cause that seemed like a good idea to me, too, when I built my first ATC in 2012 or so. Because of the hanging tool track at the front, however, I can’t easily get into the front 2″ of the second and third tills. The top one can’t slide all the way forward. So it annoys me every time I open it. But not enough to make new tills.
Now, I make them 8″ to 8-1/2″ wide.
I finished a trestle table (the one from essential pine!) with soap finish and my kid left a ring on it from a wet cup. How should I repair the soap finish?
Light scraping/sanding. Then more soap.
thanks!
Good morning, Meghan.
Have you ever heard of or checked out the fantasy series of books about feral tribes of cats living in their own clans? It’s called Warriors. My 9 year old daughter is super into it right now. I just wanna read the Birchbark House and Wrinkle in Time to my girls just waiting.
My daughter Maddy read the ENTIRE series.
I have not read those…but I will!
Good Morning Megan. With your excellent teaching of the ATC construction last week at the Port Townsend School of woodworking, I now have a few new ways to make good through dovetails. Do you have any tips for half blind dovetails? The tail part is the same so it’s really the pin part I’m curious about. Many thanks. Sincerely Joe.
Overcuts – just like most old work I’ve seen. (And thank you.)
Quick question from a newbie on planing a long (6ft) timber:
In Essential Woodworker, Robert Wearing tells you how to get a flat surface by leaving pencil marks on the end of a board and planing between them until a cup is formed and plane stops biting. Then, you plane the ends and take a full-length shaving. This works really well on shorter workpieces. Presumably, it wouldn’t work so well on a long piece, because the cup would have to be really deep before the plane stopped biting, and then correcting the cup would be a pain, too.
So, can I divide my workpiece into 2 or 3 ‘arenas’ and plane them separately? I.e. put pencil marks on the ends of my piece, and in the middle, then plane between the marks until the plane stops biting (forming a sort of shallow ‘w’), then plane off ends and middle, then take full length shavings?
Hmmm…. I don’t divide things up. I simply plane end to end, walking alongside the board as I go.
For me, this depends on how close the board is to flat.
If the board is essentially flat and I am mostly smoothing, I make full-length passes.
If the board is far from flat, for example a rough-sawn board, then I often start by traversing the board in the high areas. That divides the board into sections. But the sections are located based on the shape of the board, not by equally dividing the length.
Once twist, cup, and bow are mostly gone on both sides, I move to full-length passes.
Morning Megan. I was watching a seasoned Japanese woodworker make a small box on YouTube. For the glue up, he used rice glue and it looked as if he mashed steamed white rice till it obtained glue like consistency. What do you know about rice glue, its strength relative to PVA and hide glue and its long term durability. Just curious. Thanks, Joe.
I’m afraid I am not familiar enough with rice glue to answer.
Any issues using a linseed oil wax over a fully cured pure tung oil finish? I have several pieces I have finished with Real Milk Paint tung oil that could use a refresh.
Thanks
None.
Okay, I’ll comment, only because I have a permanent congenital case of Sticker Shock about almost everything. He wants $160 for his folding “woodworker’s knife”, which is neither a chisel, nor a knife, but Morakniv sells a fixed-blade version (complete with sheath) of the same thing for $16.81. I happen to know that because I purchased one of them in 2016. I think I’ve used it twice on two occasions when either a knife or chisel would have served as well or better. Of course folding knives can cost a LOT more than $160, but good fixed blade edge tools don’t go much lower than $16.81. Morakniv blades are well-known for their quality and value, and I have several of their more traditional knives as well. You can get a LOT of them for $160. I suppose he will find a market for some of his Bourbon Blades, even at that price, but like many tools, it’s probably a very small niche-market at that price, given the value and Morakniv alternative.
Apologies for asking a question that I know Chris has answered on … one of the blogs before. What websites do you folks use to get inspiration for making things? I think Chris mentioned an auction house (maybe european or something?) I doubt it’s just whatever instagram suggests… I’m interested in any and all links!
Most of my inspiration for personal projects comes from Shaker and other non-fussy furniture. The site Chris mentioned as inspiration for “American Peasant” is https://www.johncornallantiques.com/.
A folding chisel? I’d use one, but only if it came with a folding mallet.
Hi Megan! Is the approach of driving rivierre nails in hard wood the same as soft woods?
If you mean test the setup, yes! (But yes – pilot first, preferably a stepped pilot hole (or a clearance hole in the top board, if necessary)
Megan. I thoroughly enjoyed your photo bombs in Chapters 6 & 7 of the Roman workbench. Maybe should say “video bomb”. Hmmm, maybe shouldn’t type the word “bomb”…… Also, and if I have the “putty tats” correct, Wally’s apparent supervisory position on the other bench was awesome. Finally, Chris, yet another great series….. Many thanks to all.
I’ve found inspiration on a site called ‘1stdibs’.
Hi Megan!
I’m making a lambing chair for my pregnant wife. It’s based on the settle chair in the ADB, and the idea is to make it big and comfortable for my wife to nurse our child in. I might also add rockers, but I’m not sure yet.
I adapted Chris’s design a bit to make it closer to pictures of historical examples with two planks per side instead of one, and I screwed on the back piece from the sides instead of from the back piece as in the ADB.
My question, if you can help: How were the historical ones put together? Did they use screws then, or was it with nails/trenails? I like the idea of nailing the chair together with Rivierre nails (I live on the French border so can get free shipping :-)), but I also don’t want the chair to come apart from repeated use and moving around.
Thanks, and have a nice weekend!
Nails, properly applied, will last for centuries.
Using rice for glue is mentioned in “Japanese Woodworking Tools: Their Tradition, Spirit, and Use” by Toshio Odate.
I presume it msy also be mentioned in Odate’s “Making Shoji” as well, but I’m uncertain.
It’s been a while since I read the first book, but the rice used or suggested is high gluten rice, preferably the highest quality, that has been polished to remove the husk, bran, and germ.
I don’t know whether Mochi or mochigome rice was mentioned, and I would have been unfamiliar with Mochi, the desert, back when I read the book, but it sort of sounds like what may be needed.
The rice is prepared similar to making rice, and then smooshed and needed till the rice becomes a smooth paste.
The rice is water soluble, and probably will come apart with long term exposure to moisture, but it is a traditional glue that has been used for a long time.
I don’t know whether specifics concerning long term durability were mentioned in the books.
If the boxes you saw being made on Youtube were lacquered, that may assist durability, since traditional Japanese Urushi lacquer, would help seal the wood surface from moisture, since Urushi lacquer is apparently a very durable plastic when cured.
Curing Urushi usually requires placing the lacquered item in a warm curing box with a high amount of moisture.
Hi! How is Kale pronounced? My Estonian Roots tell me ” Kah Leh” My wife says “Callie”. Are we both wrong? Thanks for all you do, Lost Art Press is an endless source of inspiration! also.. Hammerschlager…no alcohol… got it.
Like the cabbage variety – good and good for you 🙂
I am currently building the Herculanum workbench out of water oak, and I had a question about grain and the legs. The timber is from my in-laws property, and the sawyer who slabbed out the tree did not do as I asked and so I do not have the thickness to be able to turn the legs to more than about 1″ to 1.25″ in diameter. It is old growth oak, the tree was close to 36″ in diameter when it came down, and the grain is fairly figured. Am I asking for trouble using this timber for the legs given the thinness and the that the grain isn’t running straight through? I will also be using the same tree for a Roubo style bench as well, but I am anticipating laminating the legs on that bench would be acceptable since they are significantly larger. Thank you for your input.
I would laminate some stock to get to 2” or so if the grain isn’t dead straight.
I watched the Roman workbench video last week and will be building one. My questions are about minimum length of the workbench. I believe you mentioned 5 feet in the video is a good length. What do you think the minimum would be for building chairs? How about just working legs and sticks? What capability is lost with a shorter length (is it just working longer boards)? Want to take one on long camping trips and have limited space.
For me, about 4’ would be the minimum. You seed to stretch out at times.
I’m looking forward to the DTC book. I’ve always been a “tools on the wall” guy. But I’m reorganizing the shop and may need a chest to hold some things.
Megan. Do you have a favorite chapter or section of the book?
Dados! (I love cutting dados by hand!)
Hi Megan,
I’ve been meaning to ask for some time now, and today’s header picture reminded me: what is the story behind/about the cat-and-banjo sticker on the inside of your tool chest lid?
Cheers,
Mattias
And it’s wearing an Elizabethan ruff. It was a gift from a friend. Possibly because we like bluegrass and cats, and I like Shakespeare.
I noticed on my new Shapton Ha-No Karumaku stones accompanying literature that they can be used as an oilstone???
Any insights on this?
Thanks and Best Regards, Joe F.
They are not porous. So any surfactant will work.
I inherited a fixed blade version sold by Lee Valley. I had the same initial reaction but at some point used it for something and found it useful and have seen grown quite fond of it. It’s something close to Jennie Alexander’s hacking knife. And since it’s not a high end chisel I feel more comfortable abusing it when needed.
That said, the way I use mine I’m not sure I’d want it to be folding. And this version certainly isn’t inexpensive enough to be abused.
I made the “Grocery Store Glue” April 10, 2024 version. I found it way to thin for the way I work (sloppy). The open time was also quite long and I would rather shorten that up. My strength tests went well and I’m a definite convert to the glue having used the original version. I’m thinking I can tweak the recipe by going with 16 ounces of water and maybe 4 ounces of salt. Wanta ya think?
Just finished a low back from your SCB and it worked out very well.
You can cook it down to make it thicker. Add a little gelatin to the current batch. Or add gelatin or reduce water in a future batch.
My question is inspired by last night’s Tite-Mark post on Never Sponsored. I bought mine at toolsforworkingwood.com and I am 92% certain that I am using it like an idiot who doesn’t know what he is doing. I find myself fiddling with both knobs every time I set it and only touching the micro adjustment by accident. I am convinced I am using it like a much simpler marking gauge. I also recognize that I have never seen or read about how to use one and I am just going off of my poor intuition and that is absolutely my issue.
Are there any procedural directions out there for using it? Video or written, I’m just looking for a basic tutorial that tells me when to use each adjustment. Thank you for the free article and all the time you spend hosting this forum on the weekends!
The back one (nearest the non-business end) is the gross adjustment. Loosen both screws, get it close to where you want it, then lock the back screw. Fine-tune the setting by turning the knurled cylinder that’s in between the two screws. Once you have the position dialed in, lock the front knob.
I just posted video on my Insta (@1snugthejoiner) showing how to use it.
Thank you! I think I am beginning all of my operations on the front screw and that is derailing me. I will make the adjustment.
Thank you. I really enjoyed the Tite-Mark post. Please let Chris know.
I have successfully planed stock up to 8’ in length using a slight modification/variation on the technique described by Robert Wearing: instead of taking stop cuts until the plane stops cutting, I just take stop cuts until the piece is ever so slightly concave between the stop points, and then take full length passes until I get full length shavings. For longer stuff I may also make those stop cuts as taper cuts, so start with a shorter stop cut in the middle third, then another through two thirds and a last one all the way between the stops.
Ideally you have a straight edge longer than your stock to check this with. For stock that long I use a 10’ mason’s/bricklayer’s level made from aluminium. It’s inexpensive (mine was maybe $40) and is easy to check for true with the pencil-line-and-flip method. With that, winding sticks and a suitable straight edge (which can be the edge of your plane) to check for flat across, you will know where the stock needs to be worked, and when it is flat and true.
One more thing: this is usually the final step. For getting to flattish and trueish, I will check as I go, and mix in a good bit of traversing.
Good luck and have fun,
Since cat fiction has already been mentioned . . . For good science fiction and friendship between a human and a leonine aliens I recommend the Chanur series by C.J. Cherryh. A good early example of a romantasy (romance-fantasy).
What is a good source for wide pine boards to build the Anarchist Tool Chest? Such as the sugar pine or linden you have mentioned.
I get the linden from Amana, but it’s available at many lumberyards (for my recent class in Port Townsend, e.g., the school got it from Edensaw Woods, right in town there). On the sugar pine…I do not know. I haven’t been able to get it locally for a while.
What happened with the shepherd’s table that didn’t make it into the American Peasant? Was there not enough room in the book anymore, or did it just not fit anymore?
It is an improvement on chisel/rasp design. You can fold it now.
Hi Megan and Chris,
Do you ever model things on a computer before building?
I know for stick chairs Chris likes scale models. Modeling certainly helped me select some angles, but it was harder to visualize other aspects, like whether to taper the legs upwards or downwards.
Similarly, for dovetails I am familiar with the dividers method, but it was harder to quickly imagine different spacings and angles. I ended up making this: https://stanch.github.io/dovetails/.
Is this a non-issue with sufficient experience? Or do you sometimes find virtual models useful, even if tedious?
I drew a SketchUp model of the piece I’m working on right now, because I changed it enough from the original/inspiration that I needed to see it to see if it was worth doing. I made some slight tweaks on the actual wood, but having a SU helped me make some decisions. So, yes.
I have a tall customer. I’m considering adding length to my already cut table legs. I don’t want to mess with the apron. I plan to shoot bottom of each leg, and the 1 inch add on. Then glue end to end. Then verify no wobble, then add one or two screws. is this viable?
A butt joint is weak, and the screws will last only so long. Were it me, I’d add some kind of loose tenon between the two (Domino or dowel). Put the mortise in the center of each piece, then glue the domino/dowel into each. That’ll be stronger.
Does LAP have any plans to publish some books on ‘non-western’ furniture traditions?
Chris said something like he would study eastern woodworking ‘if he had a second lifetime’. Hopefully that doesn’t rule out LAP publishing such a book. The Nakashima Process book has really got me wishing for some LAP quality books on other international styles.
Thanks!
PS Your Slöjd books rock.
We tend not to plan beyond what’s under contract and what’s on our own book-writing lists. At the moment, we don’t have any books under on non-Western work, but if the right combination of proposal and author comes along, we’d of course consider it.
Can you provide some more detail, or a reference for details on shaping the chop for the leg vise in the AWB book? The overall assembly and installation of hardware I’m good with, but what about width at top? Width at bade? Taper or shape? And bevel or curve for the exposed face?
It’s about 8″ wide at the top and 5″ wide below. The bevel on the front starts 1″ from the clamping surface, and down 2-1/2 on the front.
What was the website that you and Chris mentioned for good casters? Thanks.
https://www.instagram.com/iconicironandoddities/