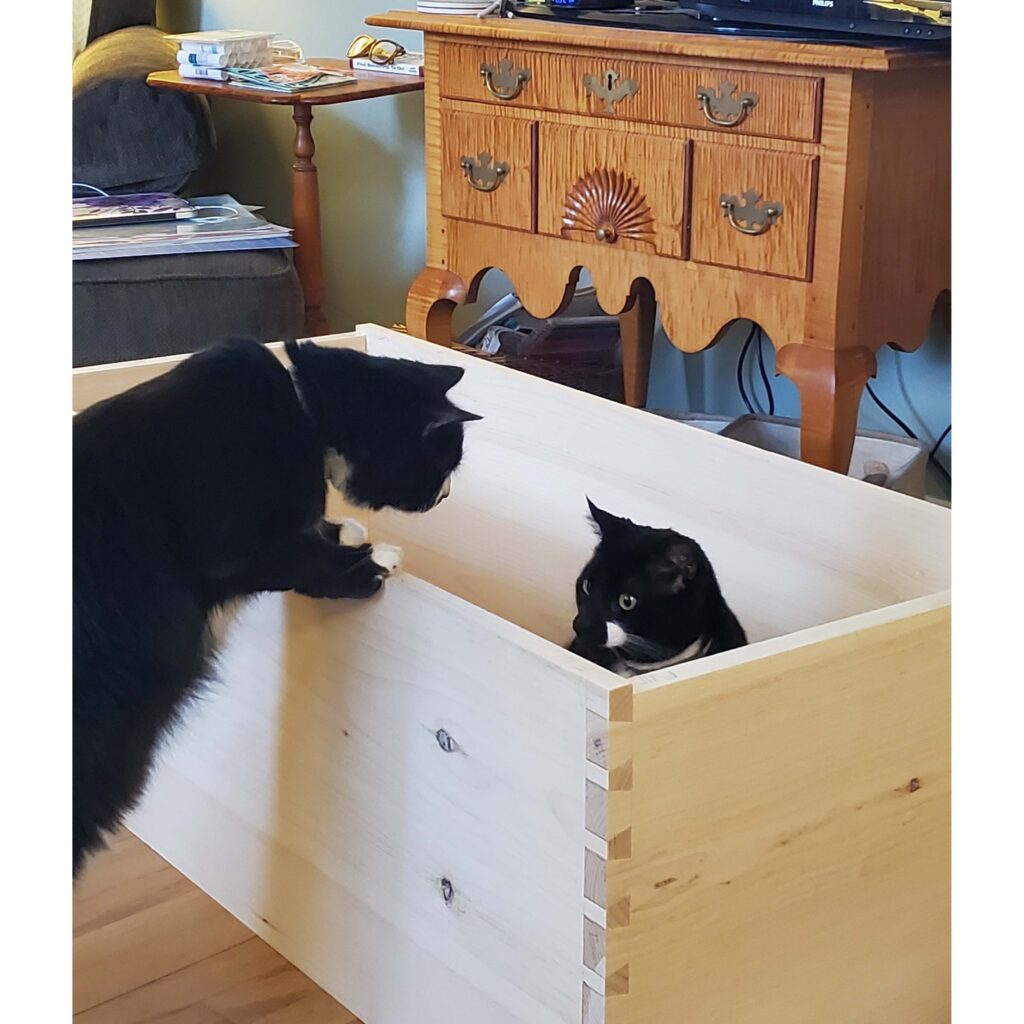
Comments are now closed. Thank you, John, for hosting!
Today’s Open Wire is hosted by our friend John Cashman, a historian long-time woodworker (mostly hand tools) who lives in eastern Massachusetts. He’ll no doubt be assisted by Inigo and Fezzig; all misspellings are theirs.
If anyone has questions on Shaker boxes, now is your chance. Likewise, questions on Queen Anne and Chippendale pieces, any of a million (give or take) woodworking books on topics ranging from birdhouses to Spanish furniture in colonial Peru.
John reminds us that, “I am no chair expert. Not remotely. I’ve made a half dozen or so, and half of those were of the Queen Anne and Chippendale variety. Aside from being seating, they bear no resemblance in construction to stick chairs. You can still ask, but if I’m not sure of the answer, I’ll say so.”
As always, brevity is appreciated, and comments will close at around 5 p.m. Eastern. Also, for some reason that we can’t figure out, replies are not appearing directly under the comment to which one is replying. Apologies for the annoyance; we’re working on it.
– Fitz
No cat will sit in the bunk with dirty paws. Any cat with dirty pants on sitting on the bunk spends a night in the box. Any cat loud talking spends a night in the box.
Good morning John, first of all thank you for sparing the time to host Open Wire today. I would like to ask two questions if I may.
The first about Shaker boxes. What were they originally intended to store? The large ones look like hat boxes and the middling ones remind me of two boxes in my boyhood home. One in leather and one in lacquered bamboo with silver inlay. My father kept his collar studs in the former (that rather dates me) and the other held postage stamps.
My second question is about the legs of the Queen Anne lowboy pictured in the bio Posted the other day. Are they cut from a single slab or do you glue up several pieces to help avoid short grain?
Good morning. Shaker boxes were used to store anything. I don’t think Shakers had any specific intentions for them. Some have referred to them as “Tupperware of the 19th century.” That’s not far off. Shaker boxes were used to store dry goods in the kitchen, but also nails and tacks in the barn. They really got used for everything.
One clear intent was to provide the Shakers an income. They were very self reliant, but still needed to sell things to raise cash. In the mid 1830s at Mount Lebanon NY they were making almost 4,000 boxes a year. These were mostly for resale to non-Shakers. And boxes could be made inside during the winter, when there was less work to do outside on the farm.
There’s a famous photo of Brother Delmer Wilson at Sabbathday Lake Maine in April of 1923. He’s standing in front of his winter production of 1,083 mostly completed boxes. The sisters did the varnishing, and made fancy satin linings to make them into sewing boxes. They were sold mostly to the rich folks at the Poland Springs resort just a few miles away.
Those legs are solid curly maple, and measured 2-3/4″-ish to start. I’d personally never glue up stock for legs like that. It would make shaping so much more difficult, with changes in grain direction.
Hello from Western Mass!
Loving the photos of your standing desk, and I have a question about the drawers. I see that you left off the lower pin on the half-blind dovetails–I’m guessing to leave more room for the groove that will hold the drawer bottoms? Am I guessing right? I saw that and immediately thought I’m going to try that on my next project with drawers: anything I should be aware of when leaving the lower pin off?
Thanks!
You are correct. Using a half tail on the bottom gives you more leeway for grooves to hold drawer bottoms. I saw some historical examples and was hooked. It’s fascinating (to me), but furniture nerds use details like that to pin down where, and even who, made a particular piece.
For small drawers especially, and with very thin (1/4″ or so) sides, I like to use drawer slips. They don’t use grooves in the side or back, just the front. They also have more bearing surface for runners. There’s a great article by Geremy Coy in the October 2015 issue of Popular Woodworking that explains drawer slips and how to use them.
Hi John, I’m very interested in colonial-era Spanish funiture (whether in Spain itself or abroad). Where is a good place to start as far as literature goes? Thanks very much!
Thank you for a detailed reply. Sewing box, that sounds like a good mini-project for the next gift for my wife.
Shakers made a couple of styles of sewing box. There was the type that had a satin lining, and included a pincushion, emery, wax, and needle holder. But there are also examples that held an insert with lots of spindles for holding thread. If you try that type, a welder’s brazing rods make for very nice and inexpensive holders for the thread bobbins.
By coincidence I just happen to have a couple of brazing rods in my cumin handy stash….
Shouldn’t we all have a few backup brazing rods, really?
De Pena, Maria Campos Carles – A Surviving Legacy in Spanish America – 17th and 18th Century Furniture from the Viceroyalty of Peru (2013) is a historical work, not a woodworking book. Vedder, Alan C. – Furniture of Spanish New Mexico (1982; 1977) is a classic catalogue of sorts of different pieces. Then there’s Katz, Sali Barnett – Hispanic Furniture – An American Collection from the Southwest (1986), Taylor, Lonn – New Mexican Furniture, 1600-1940 – The Origins, Survival, and Revival (1987). Lonn Taylor has two volumes of Texas Furniture that also covers Spanish-derived styles. Williams, Arthur Durward – Spanish Colonial Furniture (2019, 1941), Claret Rubira, Jose – Encyclopedia of Spanish Period Furniture Designs (1984).
I don’t speak Spanish, so these are all in English. And I’ve missed a lot, because of that.
Hi John, thank you for giving us your time. I’m curious if in your vast woodworking book collection you have ever come across any books about woodworking in Poland? Or Polish woodworking history?
I’m sorry, but I’m afraid I don’t. The closest geographically is Estonia, Russia, and Sweden. If anyone knows of a woodworking-related title for Poland, I’d love to hear of it.
Thank you, I’ll keep searching.
John – thanks for doing this session.
Are you aware of any resources that detail how the fabric lining for the sewing box version of the shaker boxes were constructed?
I’ve never seen a plan or article detailing the fabric lining. I’ve never been allowed to look under the hood on an original. Some of those sewing boxes had lids, but most did not, and 100 years of air and sunlight have made the fabric extremely brittle. But I am pretty confident that they were made the same way I do.
The bottom is a piece of single layer cardboard (think cereal box or slightly thicker) with a thin layer of cotton batting, followed by your fabric. Make it smooth and neat. Fit that into the bottom. It needn’t be perfect — the perimeter gets hidden. You can use some dabs of hot melt glue to hold it down.
The sides are done exactly the same, but this time you make a long rectangle that circles the inside of the box. There is a slight overlap. Play around with the batting so there isn’t a bulge where the overlap is. Place that seam in the front, so it is less visible. If you make a lid, you can line the inside of that, too. I haven’t Some, but not all, original lids were lined. But a majority weren’t. Personally, I can’t imagine a sewing box with no lid. Not owning cats, (or dusting very often).
No sewing is needed. Unless you make your own pincushions. Those tomatoes are for better sewers than I.
Thanks very much!
John, what guidance would you give to a woodworker who wanted to make their first Shaker box?
The absolute easiest way to get into is to buy a kit from Lee Valley: https://www.leevalley.com/en-us/shop/hardware/project-supplies/wood-parts/53191-shaker-oval-box-kits
Everything that you need, including instructions, is included.
Until he passed in early 2023, John Wilson was the modern master of the Shaker Box. His business is still going strong. He has books and auricles that will keep you busy for a while. They also sell patterns if you don’t care to make your own from the drawings, as well as forms and box sides, etc. And water trays for boiling the parts before bending. Anyone who goes that route should get copper over galvanized if they can afford it. And do not buy a water tray with a lid that isn’t hinged. If you lift the lid off you will spread the condensation all over your shop. A hinged lid lets all that water back down into the tray.
They also sell copper tacks, and are about the only source remaining, anywhere.
That will get you more than started!
https://www.shakerovalbox.com/
Thanks – looking forward to giving it a try!
Its a really great, fun project. People especially delight in nested sets. They are like little children, opening them up one after another.
My rejects get used in the shop to hold all manner of things.
Just getting into the shaker box groove, two questions from me:
– Steaming or soaking? I’ve made (what I hope is) a decent enough steam box to hopefully be of use for shaker boxes and other steam projects, but my first couple bands wound up potato-chipped. Hoping it was an issue with the maple but would I be further ahead to try and find a way to soak the bands instead?
– How did the shakers thickeness their bands? Most things I read these days are of folks using drum sanders but presumably there was not much of an equivalent for the shakers. I’ve tried planing them down but I still find things lift up and end up shattering at some point or another. Did they just get darned good at sawing off the stock then rasping it down?
Thanks in advance!
I’ve never tried steaming. Its a lot more work and mess trying to steam, and I’ve only done steam for chair parts. I’m actually looking forward to trying soaking on some chair legs, to see if it works.
I’d guess that the potato-chipping is from one side getting hotter and wetter than the other. You could try flipping the part in the steambox for a few minutes before bending. With soaking, it’s not an issue. You just need water temperature over 180 degrees F. Which can be a little bit of an unexpected pain. It seems hotplate makers are too afraid of lawsuits, and boiling water is really tough — the heat cuts out before it gets hot enough. I use 2 or three electric hotplates to make sure there’s enough heat. I won’t use open flame in the shop.
Most box sizes only need a few minutes to soak before they’ll bend. Except for the really, really small ones. I actually do those in a skillet on the kitchen stove now, as the longest of the two tiny sizes is 8-3/4″ long. But they boil for a good hour, or they’ll snap. And I wait until they sink. If they float, they’re not ready. Of course a longer soak for larger boxes won’t cause any harm.
If you soak, don’t do maple and cherry together. Color leaches out of the cherry and will stain the maple.
I thickness my bands on a drum sander. Its the only way I can make them in quantity. The Shakers didn’t have access to decent abrasives, so just stuck to powered planers. Mount Lebanon bought a Smith’s revolving timber planer in the early 1830s, which is just when their box industry took off. They used a variety of new designs over the years. You can tell on many original boxes how they were made, because you can still see the planer ridges in between the swallowtails — It’s a lot harder to sand in between those tails.
Brother Delmer kept a journal, and in one passage talked about his planer chewing up bands, until he stated that he solved the problem by using “dull” knives. What? It made no sense. Until I realized he was talking about grinding a steeper angle on his planer blades. Think of a handplane at 60 degrees, rather than 45 or less.
Here’s a little piece on Shakers and early planers:
https://shakerml.wordpress.com/2018/02/01/he-was-not-the-inventor-of-it-he-first-saw-it-among-the-shaking-quakers/
Amazing info, thanks for taking the time 🙂 I’ll have to go hunting for something I can use as a soaking tray here in the north, hearing that it is less messy than steaming is great! Looking forward to the rest of the Open Wire.
In last week’s Open Wire Keaton asked about medieval woodwork other than misericords and green men. I picked it up at 4:40 on the phone which is not good for typing so I hope he sees this today.
Dunno what kind of woodwork you have in mind, in Europe there are still a lot of timber frame buildings, but if you had furniture in mind you might be surprised what can be discovered.
I second St Thomas Guild especially if you want serious reproductions of northern European furniture from late 1300’s. For wider times and places, I play in the Society for Creative Anachronism, which reproduces pre-1600 western Europe and contact cultures. The level ranges from costumed cocktail party to museum quality reproductions, St. Thomas is on the high end of the scale.
Other resourses are https://moas.atlantia.sca.org/archive/wsnlinks/ a link farm about anything that could be considered an art or science, and http://www.larsdatter.com/sitemap.htm a massive collection of links to pictures, which are the usual starting point for someone wanting to make something. You will notice the that “how to make” articles in the Atlantia linkfarm usually start by referencing a picture, many of these pictures are at Larsdatter. Both are massive and link rot is a problem.
At the Atlantia site look at camping as well as woodworking, there is a specialty at making knockdown furniture to take to an event, especially camping events.
The third possibility is to look carefully at online digitised books. For starters check out https://www.themorgan.org/collection/Crusader-Bible I know of two people, one a personal friend, who have made furniture from the pictures. Friend was browsing on a boring zoom call during the plague and spotted a round table in the pic of the adoration of the Magi, and could tell the top was built like a giant shaker box lid, couple months later had a knockdown table that adds to the ambience at events as well as someplace to eat from.
In general search on digitised manuscripts from preferred time and place, an astonishing number are now online for free.
This is fantastic! Didn’t realize there were any furniture books on Texas furniture (where I live). If you don’t mind, how was it that you became interested in Spanish New World / Southerwestern furniture?
I think I’m just interested in all furniture. Books that put furniture into a social and cultural context are more interesting than just a description of the furniture itself. Then there’s the adaptations made in construction, which dictated different aesthetics. The very dry and hot southwest meant that different styles evolved — a Philadelphia high chest would probably have exploded in pre-airconditioning New Mexico.
Hi John,
Thanks for doing this today. I had a question last week that didn’t get answered, so I thought I’d try again. Is there a good process for drying 3-4 inch diameter (heartwood) tree limbs? I’ve never tried drying wood that is “in the round” before. I have several walnut pieces about 5 feet long, with the bark, from a recently downed tree (so still very wet). I’m hoping to make some “sculptural” pieces, and could either shape them while green and then dry, or dry and then use power tools to shape, if either will reduce the amount of cracking.
Thanks,
Brian
Seal the ends with Anchorseal, End Grain Sealer, or something similar. Remove the bark. Keep it under cover, and definitely not in the direct sun. I like to use pieces as soon as I can, even if it’s just rough shaping. I’ll carve spoons into at least a rough shape — final cleanup is fine even after they’ve dried.
But the biggest issue on yours is that the pith is still there. It’s going to try awfully hard to split. I usually quarter or eighth pieces of a log, and chop out the pith. They’re more likely to dry without serious splitting on their own. Bowl turners turn green wood into a rough but still very thick shape, and then final turn after it dries. But they almost always don’t include the pith in those vessels. As long as the pith is part of your wood, its begging to split. You might be fine with 3-4″ pieces. Only time is going to tell.
But get that bark off and seal the ends ASAP.
To anyone knowledgeable with Woodowl and Star M drill bits. Later today, 1 of each arrive at my house. A Woodowl Ultra Smooth Tri-Cut Auger (1-3/8″), and a Star M F-style (30mm, or ~1-1/8″). I also bought an adapter for the Woodowl to use in a bit brace, if I choose.
My question- for each of these bits, what is the limit in degrees that I can drill off perpendicular to the wood? 10 degrees? 12? 15 or more? Any other advice about drilling them off perpendicular would be welcome. I’ve read other LAP posts, but nothing addressing my question directly comes up. Thanks.
I’ve never tested how far the Woodowl Ultra Smooth can go off perpendicular. But you can drill all the holes for a chair just fine. I don’t know what those angles are, off the top of my head (and they’ll vary, a lot), but I think they are in the 15 to 25 degree range. It can do those just fine. The Star M-F has a long snout, and can tilt even more, and still bite.
In “Chairmaker’s Apprentice”, Peter Galbert shows how to custom grind run of the mill twist bits into brad points with a very, very long lead. Those work great on drilling a Windsor chair back at an extremely steep angle for spindles.
Perfect, thanks John. I’m just making small 3-leg foot stools and low sitting stools (round, and maybe the rectangular cutler-style). The couple I’ve made had legs in the 10-15 degree range.
Thank you for hosting, John – and hello from Jamaica Plain! I’m curious if you can recommend any furniture- and/or woodworking-focused library collections in Eastern Mass or elsewhere in New England.
Hey JP! There really aren’t library collections that have woodworking or furniture-heavy collections. They just don’t have the budgets for that. They normally spend their dough on “fine art,” which to them does not include furniture.
The Boston Public Library is one of the best libraries in the country, so that’s where I would start. The main branch, in Copley Square. Everyone should spend several days there, just walking around and gawking. Bring a stroller and a fake baby, so you can use the family restrooms. You don’t want to use the regular men’s rooms. They are . . . well, just avoid them. But its a great library, though you can only check out part of the collection. The research library has millions of volumes you can only use there.
Some of the wealthier suburbs have more and better materials. Newton and Brookline are very good. You should be able to get a card for any of the above by being a MA resident, not just in the individual towns. You can get an e-card at the BPL by signing up online.
I wish there was a dedicated library.
Hey John, thanks for doing this today.
I have a hand tool dimensioning question. I am prepping a 70″x10″x2.5″ board of southern yellow pine for a Roman workbench. I got the top flat in length and width as gauged by a straightedge but with my winding stick I got a windmill. On smaller boards I have taken out the wind with corner to corner passes of my plane. How to do with a long narrow board? Should I check out wind inside the length to check the middle against the ends?
Thanks,
Bill
I would start off with the winding sticks fairly close together in the middle, and move them incrementally farther apart. that will give you a better look at the whole piece, not just the ends.
Rather than trying to make full passes from high corner to high corner, just limit yourself to the two corners themselves. hog some off and double check.
I personally wouldn’t worry too much about making it perfect. The way I use it, about half the length is for me and my butt. I’m not saying that I don’t share a lot of features with The Princess and the Pea, but my hindquarters isn’t going to care about some twist underneath me. Concentrate on the end where you’re going to be doing most of your work. Get that pretty flat, and you should be happy.
Don’t even think about straightening the bottom of the plank. The legs wont care, and you’ll level them at the end anyway.
One of Charlesworth’s DVDs illustrates his method in detail.
Thanks John! I’ve got Anchorseal on the ends, and I might try halving one while green to get rid of the pith and start shaping and then see how it turns out.
Excellent. I’ve got some Anchorseal coming today myself. I started splitting a bunch of parts, and ran out of my old supply.
Maybe outside of your wheelhouse but it doesn’t hurt to ask: I just finished a new table with a soap finish, and immediately my kid left a cup on it that left a ring. I knew this would happen and don’t mind, but at some point I would like to restore it. Simply adding new soap finish doesn’t remove the ring. I guess sand or even scrape to wood and then add soap finish layers as originally done?
I’ve never used a soap finish, sorry. Maybe someone else knows. But I’d save scraping or sanding for a last resort. Buffing with a scotchbrite pad, then reapplying? Wiping with mineral spirits or alcohol, then reapplying? First rule of finish, medicine, and dating — do no harm. scrape sand or plane last.
No question, just a comment on your “cool” movie reference and to say thank you for hosting today.
I’m very happy to be here, and give Megan and Chris a day off. Not that Chris has the day off — just from this. I hope Megan has a couple of cats piled on her by now.
Two Shaker box questions.
What is your preferred method to cut the swallow tails?
Secondly, what finish do you use on your boxes?
Thanks
Depending on the thickness of the bands, I’ll stack 5 or 6 bands together. I check each one for how pretty the grain is. I put the “good” ends up and to my right. The grain should run straight off the end. If it’s at all slanted, carving one side of the swallowtails will just tear out a chunk and ruin the piece.
Once the good ends are up and to the right, I tape them together, at both ends. Then I cut to length. On the good end, I trace my swallowtail pattern, and tack hole locations. I drill the first two columns of tack holes through all five or six at once, with a 1/16″ bit for most box sizes. Really large or small tacks I’ll go up or down by a 64th.
DO NOT drill the holes near the end of the swallowtails. If you do, and you carve too close to an edge, the band is ruined. I drill those last holes after carving, so they can be centered.
Then I take the marked and drilled (still taped) stack to the bandsaw. I like a 3/16″ blade. I cut the rough shapes for the tails on the bandsaw, then get rid of the tape.
For final carving, I start with a vee tool. A Swiss Made 12-6. It’s not necessary, but I find it helpful. I make one little cut at the apex beteen two swallowtails. I do that with the tails pointed away from me. It’s maybe at a 45 to 55 degree angle? I’ve never measured. I do all this and the next step on a self-healing mat that the sewing people use.
I turn the board around and point the tails toward me. I use a utility knife with a fresh blade, and start at the apex and try to make one continuous slice to the end of the tail. Don’t get greedy. It usually takes me three light passes to get the bevel right and get a nice thin end to the swallowtail. This is where nice straight grain helps.
I usually do all the right sides of each tail, then go back and do all the lefts. It helps to maintain a consistent grip and angle. If you’re happy with the shapes, You can drill the tack starter holes at the ends of the tails, and you’re done.
Then you can bevel the last bit of the opposite end of the band. The length of the bevel varies with the size of the box. Longer bevels for longer bands. Be sure to bevel the side opposite to the side you carved.
Remember: always do the tails first.
The photo of you has a Festool vacuum in the background — other than do you do anything special to control wood dust? One of the “Two Lawyers” (they make beautiful handsaws) is allergic to many kinds of wood now, and Paul Sellers recently wore an air-filtering helmet when bandsawing.
Greetings from the north!
Preference of finish? Oil or film…what is your “go to” application method?
…sorry forgot to add…thanks for sitting in the “big chair” and taking controls for the day…
Hi John
Are you familiar with any books about the building of Biedermeier furniture?
Rudolph Pressler has a good book, “Biedermeier Furniture.” Angus Wilkie’s “Biedermeier.” Linda Chase, “The World of Biedermeier.” I know more about Biedermeier’s brother, Oscar.
PS: For a utility knife I love a Stanley 1299. It’s a fixed blade, not retractable. Beware. The nice ones are cast iron, but at some point they started using aluminum. Skip the aluminum. They are all painted red, but you can usually tell the aluminum version by the brighter color coming through the worn paint.
its a fantastic knife.
The Boston Athenaeum (right on Beacon Hill) has some as well. They require a membership but you can browse the catalog online or get a day membership to look around.
Thanks. I haven’t been there in years.
I have a Jet Vortex dust collector (with canister filter) for most things, and an older and smaller Delta that stays hooked up to a combination disc/belt sander. I have a hanging ambient air filter to try and pick up stray particles. The Festool I use for cleaning out machines, and for a random orbit sander and Domino on the rare occasions it comes out. I have a Sundstrom powered respirator for when I turn, but I don’t turn often. Im a terrible turner, but I scrape and sand my way to the end.
I had a horrible reaction to cocobolo last year, and it came back a couple of times from some small residual dust that must have remained. Cocobolo never bothered me before. I have a few pieces sitting up in between the ceiling joists, and they’ll stay there until after I’m dead and buried. I wont even touch it now.
oops, sorry Rob. I forgot the finish part. Im partial to the look of Viking linseed oil wax. Its very easy to apply, and looks great. But if I’m making nested boxes, I really wait for the finish to dry. Otherwise the odor will get trapped inside other boxes.
But I find most people like a film finish, so I give them what they want. It usually involves two coats of Zinsser Sealcoat, and two coats of General Finishes water based poly, usually in flat. I rub it down with 0000 steel wool at the end to get a soft feel. No sanding in between. I can do all four of those coats in about 24 hours, and the boxes are stink-free.
Sorry folks. All of a sudden my responses aren’t going where they belong.
Thanks for hosting John! What are your favorite books or resources for Queen Anne and Chippendale furniture?
Years ago I fell in love with Norm Vandal’s book on Queen Anne Furniture.
Morrison Heckscher’s “American Furniture in The Metropolitan Museum of Art, Late Colonial Period. Vol. II, The Queen Anne and Chippendale Styles” Is an all time classic. By the way, and titles that the Metropolitan Musem of Art published that have gone out of print, you can download free on their website. The Heckscher book is at https://www.metmuseum.org/met-publications/american-furniture-in-the-metropolitan-museum-of-art-late-colonial-period-vol-ii-the-queen-anne-a You can find others in their collection by starting there.
Patricia Kane’s Art and Industry in Early America – Rhode Island Furniture, 1650-1830 (2016) is just indescribably good. Yale University Press has made that very expensive out of print book free as a download, at https://artgallery.yale.edu/publication/art-and-industry-early-america-rhode-island-furniture-1650-1830
There are just so many excellent books on Queen Anne and Chippendale. But these are my personal favorites.
I’ve never been happy with oil finishes. Maybe I just do them poorly. I’ve tried Osmo a few times, since everyone raves about it. But I hate it. Truly. I’m sure its my fault, but I wont spend any more time with it.
I like Viking linseed oil wax. It just applies and finishes beautifully. I like some of the wiping varnishes, though they all seem pretty much the same. I love how shellac looks, but it gets damaged too easily. I’ve refinished several things I made, years ago, for myself. It just cant take any moisture. These days I like the look of two coats of Zinsser Sealcoat, followed by two coats of General Finishes waterbased poly.
I’m not much of a finish experimenter. I did it enough to find what I like, then stick with it. I generally don’t believe hype (about anything), and when I look at the ingredients of the new finishes constantly coming out, they seem mostly to be snake oil.
Thank you.
Great explanation. Thanks
Thanks. I wasn’t familiar with the Pressler titles. What I’m really looking for is more information about tooling, methods, the makers, apprenticeships.
I can’t say I’ve ever read any details about that. It would be fascinating though.