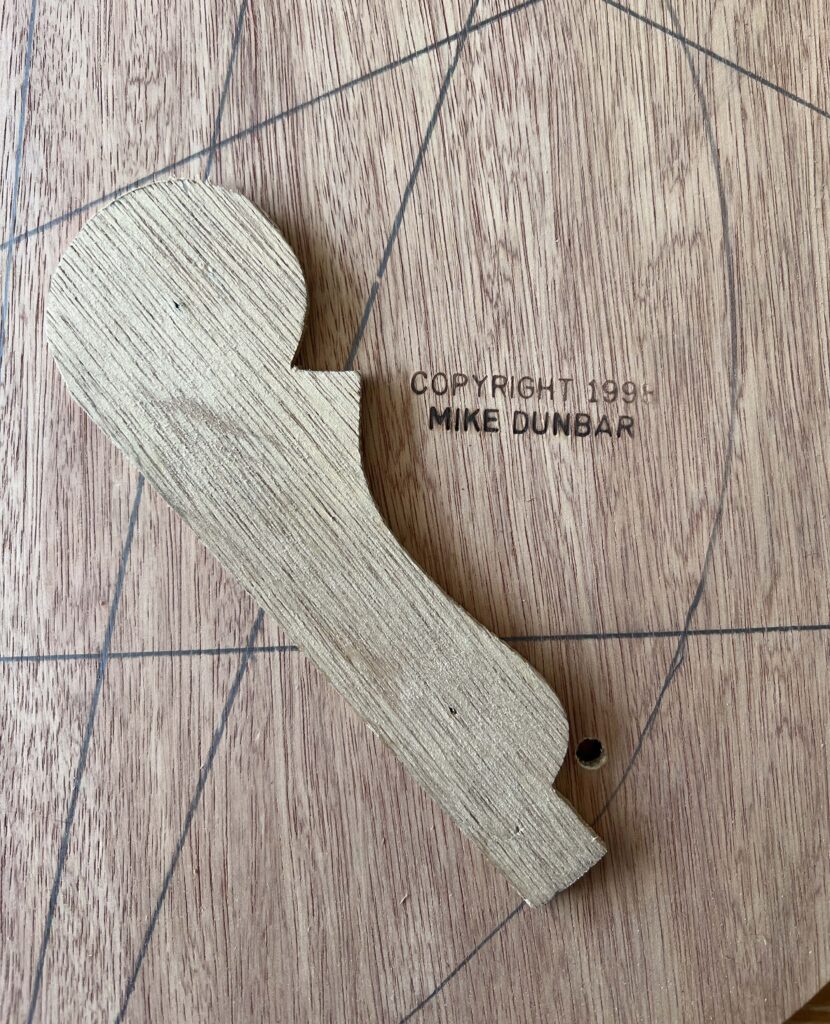
In between rearranging the shop (again) and finally organizing his chair plans in a new (vintage) lateral file, Christopher will be on hand until around 5 p.m. today to answer all your woodworking questions. And I’ll be on hand, too, until around 2 p.m., and am finally happy to answer: “How’s that Dutch tool chest manuscript coming along?” (The answer is: I’m turning it over to Chris at around 2 p.m., then running far, far away.)
Comments are now closed.
– Fitz
Good morning, which of the 2 Crucible Center Square sizes is generally most useful?
I use the large one the most. It can find centers on larger pieces and draw radial lines across wider surfaces. The small square is good for chair work, mostly.
Also, this might be the last run of brass center squares. I think we are going to have to switch to steel because the price of brass is through the roof right now.
Good morning Chris & Megan,
Two ATC-interior related questions, one very practical, easy and down to earth, the other a “but-what-if” piece of anxiousness, straight from the overactive mind of Wussy Worrywart, esq.
Easy first: when you use go-bars to clamp the middle and top runners in place, how much longer are the bars than the space they’re bridging?
As for the second one, is this question really necessary? No, not really, as I infer from the total silence on the subject in all your writings and sayings that it is an absolute non-issue. But still. Worrywarts will worry. So. Again, it concerns the runners for ATC sliding tills, in particular the 6″ (or so) wide middle one. Have you ever given thought to the difference in wood movement when face glueing one species (e.g. oak) to another species (e.g. eastern white pine)? Although the grain directions will be entirely sympathetic, the pine is likely to move rather less than the oak. Using the figures from Chris Becksvoort’s With the Grain, and assuming quartersawn wood (so radial movement) and a maximum MC variation of 8% (e.g. from 6% to 14%), the pine would change in width by +/- 35 thou while the oak would move something like 85 thou, or 50 thou more than the pine. That is not an enormous difference, but it’s not nothing either.
As already stated, in reality I already know the answer: because from the record it seems you continue to glue those runners in place, you don’t consider this difference to be problematic. So I guess the real question here is, why don’t you consider this to be a problem? You know it to be well within the limits of what glue and wood can take? You know no ATC of yours has exploded to date? Summat else altogether?
Sorry for the worry, and as always cheers and all best,
Mattias
Hi Mattias,
Fo go-bars/goberge, it doesn’t take much extra length to do the job. Maybe 1/16″ or a little more. The key point is to round over the ends of the bar to allow the bar to seat (I know you know this, but some of our other readers might not).
On the wood movement question, most glues have enough elasticity negate a wood-movement problem such as this. PVA, liquid hide and (most) hide glues are elastic enough to allow for about 6″ of wood movement in a typical cross-grain construction. Yes, the species and the mount of moisture change can push adhesive to its limits. But I don’t think you’ll be near those fence posts.
Mattias, I built a sideboard a while back, following a technique of Will Neptune’s. The two ends are about 15 inches wide, between the front and back legs. The grain funs up and down, same as the legs.
The ends consist of about 1-1/8″ cherry laminated to a slightly thicker piece of white pine. All flat sawn. I used pva. It’s been years now, and it’s dead flat, with no sign of any issue whatsoever.
Hello! How often do you flatten water stones when you’re sharpening? Like, if you had to guess, how many strokes do you go before flattening? Do you flatten higher grit stones less frequently? Thanks in advance!
I flatten my stones after every session. And I try to sharpen three tools per session. I flatten all my stones (coarse, medium, fine) after every session and go until the stone is flat. With the higher grits, it doesn’t take as long to flatten them. But I do flatten them because the maintenance also uncovers new abrasive, making my sharpening chores a lot easier.
Good morning. I bought 6 of your books that were on sale. Is there any risk of damage to the book if I leave it in the clear rap for a few years?
Thanks Dennis
Nope. The plastic is permeable to allow for gradual moisture exchange and will be stable for years to come.
I took an iron to a bench grinder for the first time and it was indeed easier than I thought it would be. When the grinding went all the way to the edge I got a bur on the back. Does that wear off with the honing?
About Onken Morris chair legs:
The cut list in the 06/2000 PW article lists the front & back legs at the same length. With the 7/8″ build-up under the front part of the arm, it seems like there won’t be a 90 degree angle between the legs and the arm. Do I have to cut the tops of the legs and side slats to match the slant of the arm or am I missing something?
This is digging WAY back.
The joints between the arms and legs are 90° – no angled joinery. If you follow the constructing drawings for the mortise locations, the front legs will be longer than the back legs. That’s correct so you can cut the back legs to tilt back 2° (or more). It can be easy to get turned around, but do the layout on the legs, and I think it will all make sense.
I recently had a large bitternut hickory tree fall in my pasture; any suggestions on whether it might make good boards for chairs or other projects? If so, any suggestions for the best length, width, and thickness for when I take it to the sawmill? Or should I just plan on having lots of firewood once it gets cut, stacked and dried?
Can’t speak to how large it’d have to be for sawing up, but if you do go the firewood route consider saving some larger pieces for woodturning (either yourself or by someone else) since it is more forgiving vs lumber wrt wood quality and grain straightness. I’ve honestly pulled some of my nicer projects from my inlaws wood pile.
Hickory rots pretty quickly if left out too long, so you probably want to make a decision sooner rather than later. If the trunk looks straight and not too many knots and the bark doesn’t spiral around the trunk it’s probably worth having it cut for lumber. That said nothing beats an experienced pair of eyes on it. Either ask someone to look at it or take pictures and show them to someone who is experienced with sawing lumber.
As far as what to cut from it, that depends on what you want to build from it. If it’s me I would get some 4/4 boards for furniture, some 5/4 boards for tool handles and some 8/4 boards for chair legs.
When grinding an iron on a bench grinder for the first time recently I got a bur on the back of the iron, is that bad? Would it just come off during the honing steps?
It’s not bad. It means you cut a new edge on the bevel. It’s usually best to avoid doing this because as soon as it happens the tip heats up very quickly and can lose its temper in a half-second. If yours isn’t discolored, then you’re OK.
Hi Chris & Megan – You often recommend getting good quality vintage tools over the new equivalent (eg Stanley No 5). I don’t have access to vintage tool shops or markets where I live (a small island off UK) so have to resort to the internet. To avoid the risks of speculative purchases over eBay, etc are there reputable online vintage tool traders you can recommend where one can source good quality vintage tools for use (rather than collection)?
Re online old user tools in the UK I’ve had some good stuff from:
https://www.oldtoolstore.co.uk/
And
https://www.oldtools.co.uk/
Good quality. Not overly expensive for the quality and especially good customer service from the old tool store.
I don’t know the UK sellers, but in the US, https://hyperkitten.com/store/index.php and http://www.supertool.com/oldtools.htm
Hi, thanks for directing us to the interesting shellac video earlier this week. Fascinating viewing! I am keen to assemble a supply of a reasonable range of flakes to have on hand. What types and colours would you recommend to cover a reasonable range of likely furniture uses? Also, what is the best way to store dry flakes to maximise life? I am lucky to have a small shop fridge. Is it ok to store them there?
We keep our flakes in the finishing cabinet in the zipper bag they come in, but the “rule” is a glass jar, tightly closed, in a cool, dry place (so, fridge). We usually have super blonde (almost clear) and garnet on hand ≠ though I went through an amber on cherry phase.
Just to add onto Megan’s comment: Super blonde is my personal favorite (we get ours from Tools for Working Wood). We use a half-pound cut for furniture. That’s 1/2 lb. per gallon of alcohol. That makes a nice thin coat without a lot of gummy build.
Shapton Kuromaku stones. A late friend left me two- 1000 grit and 5000 grit, both nearly new. Last night, I ordered the 8000 grit. I have an unused 400 grit 8″x3″ diamond plate. As a casual/hobby woodworker sharpening tools at about 2% of the rate that the LAP staff sharpens, would you think the 400 grit diamond (finer than the 120 or 160 grit DMT Dia-Flat plates which run $130-200) can serve as a flatening plate for these three Shaptons? Or is it simply the wrong choice as a lapping plate? Thanks for your guidance.
I say use the diamond plate until it stops working. Then decide what to do next. You might get 10 years out of it.
I recently saddled my first chair seat following instructions in the Stick Chair Book. I found that the bowl is more of a gentle slope from the back of the seat to the center seam, while I have more of a bowl-like profile along the rest of the spindle deck. I think this has to do with working across the left-right running grain with the scorp. Is this bowl shape normal, or would you work harder to profile the extremes of the bowl consistently all around the spindle deck?
Hi Adam,
The shallow bowl at the rear isn’t much of a problem – as long as things don’t look weird. You are correct that it is a challenge to scoop that out compared to the straight parts near the front of the seat. If it bugs you, you can purchase a travisher with a tighter radius iron, which will scoop out the back. Allan Williams makes a great one.
Thanks! If it’s normal to you, then my mind is at ease
To dust off after sanding table legs that I was working on, in between coats of paint, I tried for the first time a “tack cloth”. It turned out to be very sticky and might be actually leaving residue on the piece. Is this something you use or would you avoid it? Thank you.
Chris just wrote about tack cloths – we both use them, with no trouble.
https://neversponsored.substack.com/p/finishing-the-finish-never-sponsored
For boards less than 24” long, do you find a jointer or a Jack plane better for removing twist from the board?
I’d use the jack to take down the high corners, then the jointer.
Hello Helier. There are reputable sellers in England. I have purchased very nice user tools like a Record 5 1/2 plane, Record 405 combo plane, etc from Old Hand Tools. They were as advertised and priced spot on to market. There are others like Tooltique. Good luck
No question, just Huzza! Looking forward to the DTC book.
Thank you! (As am I)
I would like to make my daughters and wife their own stick chair. They are all 4 different heights and let’s say body structure! Is there a good way to measure them for the seat height from floor dimension for the most comfortable seat for their specific heights? Or make the chair taller than I think needed and have them try it out? How do you make chair heights for your daughters or others?
Chris makes all his chairs lower than what you’d likely find in a store. As he says, tall people can be comfy in shorter chairs, but short people will have their leg circulation cut off in taller chairs. I am 5-5″, and his chairs that are 16-1/2″ off the ground are perfectly comfortable for me (and for him at 6’4″, and Lucy (Chris’s wife), 5’9″ or 10″).
But if they are wildly divergent in height, find out their popliteal height (floor to underside of knees with feet flat on the floor) and don’t go higher than that.
I finally got a Lie-Nielsen 48 and I’m very happy. Well, I will be when it gets here.
This is a quick question about grain direction and T&G joints. Am I right in thinking that when joining two pieces (e.g. panels in the small coffer in The American Peasant) it’s inevitable that one side is against the grain? Maybe my brain is malfunctioning.
If my brain isn’t malfunctioning, is there a better side to go against the grain (i.e. tongue or groove)? I suspect I am massively overthinking this…
Beginner question I know. A few weeks ago I asked a question about old match planes and Fitz’s answer was super helpful and got me better results immediately. But, um… let’s just say I’m happy the Lie-Nielsen is on its way.
You are correct; you will inevitably be planing against the grain at times, but the teraing won’t show (and the straight the grin, the less it will happen.
In AP, Chris writes:
Arrange the pieces on your workbench to create the desired panel. I usually
put the heart side facing up (if the wood is dry). If it’s damp, I’ll alternate heart
side and bark side on each mating board to decrease the chance the panel will
distort as it comes into equilibrium with the humidity level in my shop.
I orient the boards so the grain direction on all the boards is running left (if
you are left-handed, reverse this and have the grain running to the right). This
ensures the No. 48 will be (mostly) working with the grain during the whole
process.
To be fair, a little tear-out on the edges of the tongues or the grooves isn’t a
big deal. The tearing will be mostly hidden. But in boards that have the grain
moving steeply through the board, the tearing can show on the face of the
board. Plus, working against the grain is harder work.
Now draw a giant and bold cabinetmaker’s triangle across all the boards.
Decide which edges will get a tongue and which will get a groove. Mark a T or
a G near that edge to remind you.
Place the first board in your face vise with the edge that will be tongued
facing up. The cabinetmaker’s triangle should face you, the user. If the fence of
the No. 48 runs against the triangle-marked surface on all the boards, then the
panel will end up flat with the surfaces coplanar.
Thank you! Enjoy the weekend!
Hey Chris and Megan – Thanks for the tip on the jointer a couple weeks ago. My wife picked up a Stanley No 8 a few years ago (long story) for free, so I’ll be rehabbing it using Chris’s video on handplane restoration. Now for the question. You did online Q&A sessions a few years ago. during the pandemic. I was just thinking about one of those sessions where I learned about Stephen King’s On Writing which changed my writing and my life. Any chance of the on-air sessions coming back? They were fun (for us) although maybe a hassle for you.
We are always experimenting with different ways to communicate with readers. We enjoyed the live sessions and have been pondering a video podcast or an occasional live “Open Wire.”
The problem is the time suck – both for us and the viewers. Open Wire can be scanned and searched. Video is difficult to skim.
Searchable. It be great if all the Open Wire’s were in one spot and we could search that?
They are all under the open wire category, if that helps
9″ 10 grain Auriou Cabinet Maker’s Rasp or 10″ 9 grain? Or just… yes?
Either is fine.
What does Chris “hit” his froes with, steel will damage the froe on tougher materials?
Lately, he’s used the Garland split head no. 4 (https://garlandmfg.com/mallets-hammers/split/). He used to use a lump hammer – and his froe is still intact. (I teased him that he got the Garland ’cause he was tired of people clutching their pearls when he used a lump hammer on the steel.)
But in short, he hit his LN fore for years with a metal hammer, and it is fine. Maybe a little dinged up on the back edge, but if it gets too bad, well, we have a grinder.
If you had the opportunity to build a personal development library (at someone else’s expense ) do you have any recommendations?
I’m afraid I’ve never read a self-help/personal development book. I don’t have a thing against them (promise). I am just not that interested in me. I can, however, list the books that were the most formative in my life (if that helps)…..
Empathy, suppression of the self: It started with “Siddhartha” by Herman Hesse. Then into studying Buddhism
Humanism, embrace of the ridiculous: “Slaughterhouse Five” and “Breakfast of Champions” by Kurt Vonnegut
Understanding others: “Lying” by Sissela Bok
Becoming a writer: “On Writing Well: by William Zinsser. “On Writing” by Stephen King
Business: “Our Band Could be Your Life” by Michael Azzerad
LAP, what is the difference between a dovetail saw and a blind dove tail saw?
Arguably, marketing. But the idea is that the “half-blind” saw is meant for through cuts on thinner material (1/2″, 1/4″), and half-blind cuts in 3/4″, 1 ” material (because the half-blind cut removes less material. The plate is thinner and more delicate. I use a “half-blind” saw in 3/4″ and 7/8″ material all the time. I suppose it could kink easily…but I saw so that it doesn’t.
Fitz, did you mean dove tail saw cut thru 3/4″,1″ not half blind. I found a L/N fine tooth saw in a box, I bought before I found LAP, still in the box, with a dove tail saw also L/N Going to look under my bed see what is there
Through cuts on thin material. half-blind cuts on slightly thicker material.
Good morning y’all, I recently completed a class making a sack back Windsor and I’m hooked. My wife is very pleased and authorized the requisite tool collection, froe arrives Monday. Thank you for your article about riving kiln dried lumber. I’ve a ten foot 8/4 quatersawn white oak that I will attempt to turn into your Irish (ish) chair. Thank y’all again for y’all’s selfless contributions.
age old question, I know, but I just moved to the UK and really miss the LAP store. Who caries your products here? P.S. Megan: Thumbs up! I’m waiting for this book!
Classic Hand Tools: https://www.classichandtools.com/
They are great to deal with!
Classic Hand Tools. They’re also a group of lovely people!
Hi Guys, happy June! I’m looking at a purchase of a scorp to start on my path of chair devotion. Any recommendations regarding size/brand? I don’t want to suffer through a cheap steel that won’t stay sharp. I appreciate your thoughts!
The one Chris uses most is by Lucian Avery, sold through Sawyer Made: https://sawyermade.com/
We also recommend the James Mursell Travisher (Windsor Workshops), as it can be set up to take heavy bites (like a scorp), then light ones (like a travisher): https://thewindsorworkshop.co.uk/product/travisher-deluxe/
Before I used Lucian Avery’s scorp, I used the Barr scorp for many years. Outstanding steel. I just wish the shape was more like the Avery scorp.
Good morning,
I’m trying to ship a chair to a friend through LTL service (Old Dominion) for the first time. I have talked to a rep on the phone and confirmed that I am using their rate calculator correctly and getting accurate rate quote. The rates seem cost prohibitive. For example, if I was to use my crate shipping details (31x31x45, 80 lbs) from your zip (41011)(Commercial pick-up) to my zip in Phoenix (85044) (Residential delivery), the quote is $933. Question: Would this be the type of rate you would expect to see if you were shipping one of your chairs from your shop in Covington to Phoenix? Do you have any other suggestions or helpful tips?
Thanks!
Sounds like you might be using the wrong freight class. I would expect the cost to be about half that.
There are several freight classes that apply to chairs. Our rep instructed us to use freight class 250 for my chairs. Might want to try that.
The other issue might be that you would need a commercial account to get a good rate. Some trucking companies have crazy rates for one-off shipments.
yup. i’m using rate class 250.
probably the commercial account issue. that makes more sense now.
thank you
Hi Chris & Megan,
I have access to some green walnut from a storm-downed tree. In addition to some larger pieces, I’d like to try creating some sculptural pieces out of smaller limbs. These pieces still have the bark, and the heart wood is 3-4 inches diameter. Do you have advice on how to dry this kind of wood while avoiding cracks? Drying wood “in the round” seems like it might be more prone to cracking than flat-sawn pieces because of the differential in shrinking between outer and inner layers, but I’ve never tried this. I’ve coated the ends with AnchorSeal. Removing the bark and sapwood to shape/carve it while the wood is still green would be easier, but I’m not sure how to dry it after that point. Or would drying with the bark on be preferable?
Thanks!
Nathan – I had a portable sawmill come out and mill a pignut hickory for me a few years ago mostly as an “audition” for a walnut tree that I knew was going to fall soon. I do find the hickory much too hard to enjoy working with hand tools (though it did help my sharpening skills). I have made a pair of Krenov style sawhorses, a small end table and several cutting boards as gifts. The next hickory that falls will become firewood.
In the LAP emblem, between the dividers, there is an E.
What does it stand for?
That’s a referrent to the “caption” in the original Moxon plate. “E” is dividers.
I am looking for a good bench top planer. I see some with plastic or metal. And different types of cutters. Rpm 8500 to 10,000.
The dollar range I am using is about $400 to $800.
Any suggestions?
The DeWalt DW735 is the best portable planer on the market. We had one for years. It’s loud as heck (all the portables are). But it does a great job.
Hi, my local hardwood dealer has gotten in some nice, straight grain black locust. I have not worked it yet but it appears to be very hard and have good color. Have you ever used it for chair parts?
I picked up a Back/Sash saw the other day and can’t seem to find anything on the company. A. Barr 122 Goldsmiths Row London. It’s a 14″ blade nice handle, should clean up and make a good user. Any chance you have come across the maker?
I don’t know if Chris, knows (I don’t) – but if not, ask on the saws group on Facebook:
https://www.facebook.com/groups/857101454366905
BARR, Alfred
14 (122) (139) Goldsmith’s Row, Hackney Road London, 1873-1950
66 Dove Row, E2 London, 1928-1950
Saw maker; BPM3 reports planes with his mark.*
Another good one is https://www.tooltique.co.uk/. He refurbishes the tools and does a really good job. Highly recommend this site.
Quick question on your sharpening setup. You have shared that you keep your kit in a boot tray under your workbench. Do you do anything special to keep detritus off the kit or do you just brush off shavings and sawdust when you go to use it?
I would love to do something similar and wondering if I am making a mountain out of a mole hill.
I keep mine in the cases usually, but if they’re not closed up, I put a huck towel over them.
Hi Megan/Chris,
I just got a Barr 2″ cabinet chisel and it’s awesome. Thanks for the recommendation!
It looks like they’ve changed the design a bit since both of yours—mine is more like a firmer chisel rather than the bevel edge versions you show in your pictures. It seems like they shortened and put a different handle on their normal timber framing line up. Anything lost in this or is the extra material on the edges immaterial in use? Would you mind sharing the weight of yours if you have your glue scale handy?
Thanks!
Derek
a gnat’s ass under 1 lb (I can’t find the digital scale to be more precise).
Found it: Mine is 15 ou., Chris’s is 13.9 ou. (he’s used and sharpened his more)
Pickup and delivery in “limited access” locations ie residential will require lift gate service as well as being non- commercial locations.
If you can drop your freight at the terminal and your customer can do a dock pickup at their end, it should save a substantial amount of money.
Even one dock visit at either end would save you money.
I drive for a freight company.
Thank you Chris, and John! As I wrote, Calm, Logic and Reason told me it would be alright, but would ol’ Wussy listen to any of those muses? Waddaya want want for 10 cents – gasoline?
So ’twere most reassuring to be reassured by way of explanation, for which again my warmest thanks!
Thanks Megan and Chris for doing the Open Wire!
I was using my DeWalt 12-1/2″ portable thickness planer and got just a little snipe. I used a straight edge to check and adjust the table extensions. I noticed that the bed\main table had a slight crown to it, maybe about 1/4″ difference between the center and edge. I don’t remember ever noticing this before on the few occasions I’ve had to make any adjustments. Holding the straight edge on the center of the bed, I was able to level the extensions and got rid of the snipe. Just wondering if anyone had ever noticed the same with their planer. It works okay, no snipe, but being the anal goof I am, I had to ask.
Adjusting the tables and bed rollers (if your machine has them) is the best way to reduce or practically eliminate snipe. So good work!
Happy Saturday!
Part A…Any experience with sticking goncalo alves together?
Doesn’t seem to like watery adhesives due to no pores.
Part B…typically are dovetails used instead of mitre joints when working with hard dense woods? Or maybe I need to redesign using mechanical fasteners….(bolts)
Try epoxy – that’s the best solution for those hard-to-glue and oily woods.
I’m not a fan of the hard tropicals, I’m afraid. So my experience with them is mostly trying to avoid using them.
Hey LAP,
I have a workshop tool collection influenced in great part by your insights and recommendations and would appreciate some thoughts on best approach to a stock prep issue.
I have a 70″x 10″x 6″ beam that I would like to cut in half to make two Roman workbenches. The material is old growth southern yellow pine that is very hard. The tools I have that I think apply here are a circular saw that gives me a 2.5″ cut, a sawzall, a few hand saws, and a chainsaw. My only workshop power tools are a drill press and a new Jet 14″ wood/metal bandsaw with no riser so 6″ max.
Would you circular saw the perimeter and sawzall the remaining, circular saw the perimeter and chainsaw the remaining, or chainsaw the entire thing? My concern with the chainsaw is the lack of precision which makes for a whole ton of planing by hand to flatten and square the surfaces.
Thanks for your help.
I’m not precious about the ends of my workbenches. They aren’t reference surfaces. And a chainsaw surface looks cool. I’d probably use the chainsaw alone – work my way around the beam first. Then use that kerf to guide the final cut.
Chris, Meghan, and Kale,
I am teaching some classes at Bright Time Camp near us next week. Ukrainian symbols engraved and and then maybe wood burned as well (the school wanted the wood burning component), ten minute owl carving, and spatula carving, to various age groups. Do you have one or two pieces of advice I should know? I always want to do these things and then get a period of stressed out before being fine again shortly before the thing starts. Do you ever get that way? Peace.
Jeremy
If it were me, I’d hype the “spell” component of the work. These are protection spells for therm and their family (and cats and dogs). I’d show them how to make the fishing net and then add their family members and pets to protect them.
Kids seem to dig the bit of old magic.
Also a witch mark is fun because the story of how the witch gets tangled in it is pretty cool.
I’ve
I’ve got a bunch of red cedar from my Dad that I want to use to build a timber frame cart with drawbores for my Big Green Egg grill. The previous owner built one using screws that’s all kinds of rickety with 160 lbs of grill off center on it. My question is, what’s the best way to finish it to preserve that wonderful bright red color of the wood? Just some standard poly? Should I finish it at all and just let it age naturally? The plan is to make an oilcloth cover for it so it won’t be exposed 100% of the time.
Thank you for making this time for us!
There is not a film finish (except for very expensive marine varnishes) that can protect outdoor wood. And even marine varnishes requires yearly maintenance.
I like to let the wood weather and gray. You can slow the process with linseed oil or tung oil and apply it every year.
If you want low maintenance, you can use an semi-transparent deck stain, which doesn’t create the same film finish as varnish.
Any good sources for medieval woodwork? Seems like it’s all misericords and green men.
Also, some yard tools (rakes, shovels, etc) may or may not have been left outdoors for the better part of 2 years. Anything you recommend for finish to the wood handles?
Guédelon castle in France: building a 13century caste, at present. got a website an can go visit
St. Thomas Guild does a great job:
https://thomasguild.blogspot.com/
I know there are other groups out there. But I can’t recall them off the top of my head….
And for yard tools, I like tung oil or raw linseed oil. You might need to sand away any rotted or overly weathered wood first.
I’ve just acquired some Shapton KUROMAKU stones in the grits that you have recommended. In the one page document that comes with them it says “Before using the fine stone for sharpening, immerse it in water for 5-6 minutes. However, if you leave it in water for too long, the stone will start to soften – the surface, in particular.” I don’t remember you writing about this in your discussion of these stones. Is this a practice that you follow?
Also, I have a DMT Dia-Sharp 120 Micron diamond plate. Would this be suitable for dressing the stones?
Chris/Meghan, I marvel at your ability to keep the pace on this blog, the Substacks, the publishing work, the Crucible tool work, etc. Thank you for all of this!
You don’t have to soak them. I never have. Just splash and sharpen.
Feel free to use your diamond plate to flatten the stones. You might get several years out of it before the binder gives up its diamonds.
Good luck!
Hi Megan and Chris,
Can you recommend any good books on making a woodworking business? Or any good books on making a business that happen to be applicable to woodworking?
And do you have any plans to publish your own on the topic?
Chris Becksvoort’s LAP books have a lot of useful info on this. Chris has a lot of writing oncyhe blog here and at The American Peasant on the topic. Really good stuff.
I wish I did. I learned to run a business by being thrown into it. My first business (a newspaper) failed. Then I worked for corporate publishing for 15 years and learned how to make money by screwing people.
This business (LAP) took all the lessons I learned in corporate publishing and doing them with a humanistic bent. Don’t screw people. Do good work. Don’t go into debt. DOn’t have employees until you have to.
These are lessons you’ll learn if you get some mentoring with the Small Business Administration or one of the many small-business accelerators in cities. We have a bunch here, and I wish I had known about them when I started.
Sorry I don’t have a coherent answer….
I’m after advice on how to get that lovely clean edge between a spindle deck and chair seat. I’ve seen routers used, what techniques do you use Chris?
I get very close with my scorp. Then I skim the rim of the saddle with my travisher. It can be a little harrowing. But what works is this.
Establish a curved “track” for the travisher to run in that is about 1/4″ from the rim and parallel to the rim. The track is made by the curved blade. Think of it as a furrow that helps guide the travisher. Once there is a track, I follow it with the tool and tip on side of the tool down toward the rim. This makes the track wider and nibbles material between the rim and the track.
Tiake another stroke and tilt again toward the rim – bit by bit until you reach your pencil line at the rim. The track acts as a path so the travisher doesn’t hit any bumps. THis allows you to sneak up on the rim.
I have a Bad axe “half blind” dovetail saw that’s great for cutting wee dovetails in stock 3/8 or thinner. If I’m cutting tails in 3/4 or thicker, and gang cutting two sides at once, the plate is too thin for me. You’ll never get a coping saw blade in there if you saw out your waste. I actually use a carcass saw for gang sawing dovetails in thicker stock.
If you love well made tools, have enough money, and have an itch to scratch, get the half blind saw now, as Badaxe is discontinuing them. But really it’s a luxury purchase. I could get rid of all my saws except for my 12″ carcass saw and do everything with just that one.
I fear I’ve contracted chair fever. I’ve made 2 stools just to make sure I have my mind around the angles and am collecting wood for my first chair. I’ve started a Google drive folder of pics of stick chairs. I blame (and thank) you all.
The only cure is: More Chairs.
I have been working my way through the new version of the Stick Chair Book and the color photos add so much to the book. If there is a future anniversary edition of the Anarchists Workbench or ATC, is there any chance of getting color photos? Thank you for all of the inspiration.
We are planning an anniversary edition of ATC with color photos and revisons/updates etc.
Have you ever used soft maple for a chair seat? I find it carves pretty well.
Yup. I love it for chair seats. Very consistent. Easy to carve with sharp tools.
Last time (possibly as a joke) you opened the discussion to Russian literature.
What are your favourites? What would you like to tell ys about what you’ve read?
Nikolai Gogol has always been my favorite. “The Government Inspector” and “The Overcoat” prepared me for Kurt Vonnegut.
Outdoor furniture. I have a small house, but a big yard. Any thoughts on books or inspiration for outdoor furniture?
New Yankee Workshop has a lot of good plans for outdoor stuff: https://www.newyankee.com/projects/
WOOD magazine is the undisputed king of outdoor projects in the magazine world: https://www.woodmagazine.com/project-plans/outdoor
Or if you want a book from them on the topic…. https://www.thriftbooks.com/w/wood-magazine-35-great-outdoor-projects-wood-magazine/727678/item/8444256/#edition=5379753&idiq=24118998
Are the collars for pinch rods that Crucible used to make gone forever or will there be another run of them? If gone, does anyone know where to find a pair of them?
I’m pretty sure we’ll have another run soonish
I’m afraid that for now, pinch rods are out of production. The brass price more than doubled, making the product a non-starter. We have been investigating steel, but we have to do some reprogramming.
That was my fault, and Chris is the Russian literature aficionado. So if he doesn’t answer, blame me.
How would you make a slotted screw hole to allow for wood movement to attach a solid tabletop to a frame? With countersink?
If you are making a pocket hole in the apron, then I would use a countersink bit. Drive it at an angle through the apron. Then move the drill laterally while it’s moving to ream the hole to allow for movement.
There’s a good discussion of this topic here:
https://forums.woodnet.net/showthread.php?tid=7316289
I’m not using pocket holes. Is there another method for making slotted screw holes?
Check out jackbadgerlimited on Instagram – they produce midieval style housetrim,doors,windows. Much carving, scratch stock work – nicely done authentic looking work (and most of the crew are “kids” )
Jackbadger recommendation is meant for Keaton who was asking about Midieval woodwork
I recently “borrowed” your line about kindness or absence and used it to clean up a Facebook group I administer. It worked a treat. Thanks for that and thanks in general for the incredibly positive energy that everyone at LAP exudes. I don’t want to gush or get too maudlin but between the world seemingly on fire at times and some personal health issues that I’m still trying to learn to accept I consistently find myself smiling when I read the blogs and the emails so chock full of good and thoughtful information that you all so graciously provide.