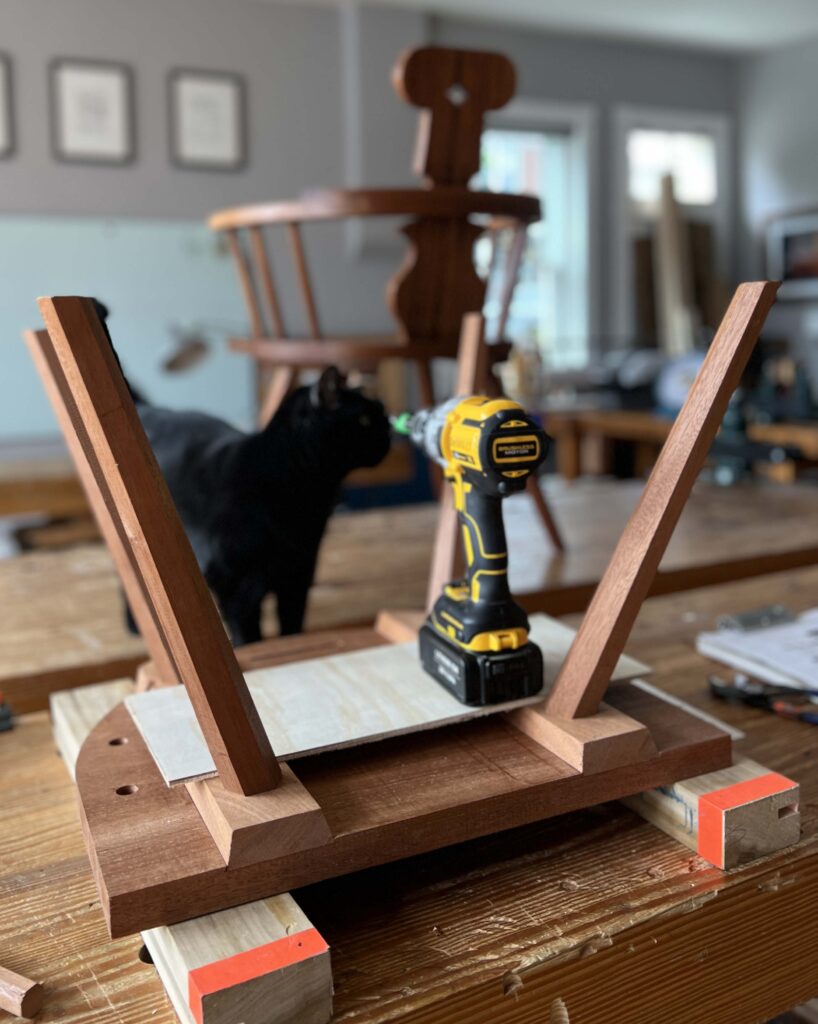
Chris is already hard at work (shocking, I know) on a second LOTR-inspired chair, and I’m belaboring every word in my Dutch tool chest book manuscript. But we’re also here to answer your burning hand-tool woodworking questions. Or cat questions. Or late 19th- early 20th-century Russian literature questions (that’s Chris, not me; he contains multitudes). So post ’em in the comments below, and we’ll answer.
Comments will close at around 5 p.m.
– Fitz
Good morning everyone!
I have an opening question: do you play music while working in the workshop? Or are you a silent woodworker? …no pun intended. 😉
I find myself listening to podcasts more and more these days.
What’s the soundtrack for your day today?
I prefer to have music on 24-7 in my life, but consideration for my coworkers prevents that.
I listen to WMOT (https://www.wmot.org/#stream/0) or a playlist, or something new I’ve found. Or…
I can’t listen to podcasts when I work because if they are good, then I stop work (or slow it) to listen.
If I’m at the bench, I love having music on. But as Chris says, he kindly turns it off when I’m writing or editing (I can’t split my brain between two sets of words).
I like jazz music in the shop. I’ve got a loaded MP3 player (a little bit yesteryear) that I plug into the stereo receiver that I loaded with 30 or 40 albums, or streaming of these two public/community stations: http://www.jazz88.fm in Minneapolis, and http://www.wwoz.org from New Orleans. Sweet sounds! I’ve known some who play classical in the shop- not for me. Neither is rock & roll.
Oh, both of those radio station streams offer somewhat jazz-alternative programming on weekends (which are great), but weekdays are true to their mission.
Me also. Lately I have to read a book 3 times. Lonesome Dove wow
I got a nice set of diamond sharpening stones and a Lie Nielsen honing guide. I just noticed that Lie Nielsen states in bold type in its instructions that their guide must not be used on diamond stones. They don’t state why. So, I’m now looking at $300 worth of sharpening equipment I’m afraid to use. What do I do? Buy water stones and eat the cost of the diamonds? Shelve the $150 honing guide and go free-hand on the diamonds? Or ignore Lie Nielsen and use the guide on the diamonds anyway?
This issue came up recently on our Never Sponsored substack. The concern is the wheel will dislodge diamond fragments from the binder of the stone and those bits will foul the wheel. I’m sure it has happened. But we haven’t experienced anything like this in using the guide on diamond (or any other media) over many many years of use.
I would go ahead use what you have. Keep the guide’s wheel clean and lubed – as you should anyway.
I wonder if you could try wrapping the wheel with a single layer of tape to prevent any problems?
After building numerous Stick Chairs since Chris’s book came out, I was curious. Is there such a thing as a Stick Rocking Chair? I was thinking of building one for our home and was wondering if there was such a concept or is it a silly idea? Have a happy holiday weekend, Charlie
Rocking chairs are an American thing. There are stick chairs out there that have been converted to rockers during their lifetime. But I am unaware of any antique stick chair that started out as a rocker (though I am certain one exists).
Sorry to be no help.
In the post picture what is the purpose of the red tape on the battens? Thx.
They stop people from thinking they are scrap/trash and throwing them away.
I think this may have been asked in a previous live wire but I can’t track it down.
When using the Veritas tapered tenon cutter, the leading edge of the cutter tends to butt up against the wider part of the leg preventing it from advancing. I then end up trimming back more of the leg. While not a problem in itself, it moves the leading edge of the tenon way down the leg and makes the transition less crisp. Is this just the nature of the beast or am I missing something? Or am I just making my legs too thick?
Hi Ron,
I’m afraid I’m having trouble visualizing the trouble.
Is the leg you are tenoning octagonal? Tapered at the top? And I’m not sure what he leading edge of the tenon is. The tip? The base? Iff you could rephrase or give me some more data I might be able to help. Sorry.
(this got posted in the main thread, I apologize. Here it is for Ron)
I’ve had this problem.
My solution is that I try to get the area that receives the tenon as close to the tenon shape as possible.
I mark a 5/8″ circle with a compass on the top of the tenon and mark 4″ down (you can experiment with this and find what works for you, you could probably get away with 3″ if you want a really crisp transition to the tenon, in practice I like a little more of an organic feel).
I then use taper cuts with my block plane from my 4″ mark down to the circle I made all around. Then I knock down the arrises and a few spins around the tenon cutter and I’m good to go.
Regarding rough cut lumber, when do you thickness plane the boards? When you get them and then sticker and stack or just as you are going to use them on a project?
These are dry boards.
Thanks
With rough, I’d cut it overlong and let it acclimate. Once it’s at equilibrium, thickness plane. If I can’t do the joinery right away, sticker it.
Depends on their moisture. If they are acclimated, then I surface them right before I begin building the project. If they aren’t acclimated, I don’t touch them until they are. Wood continues to move after you cut is, so getting wood to equilibrium is the key.
Happy Saturday, and thanks again for doing this. I’m anticipating the need for a new office chair in the next year. I have days where I spend 6+ hours at my desk; is there a chair design you’d recommend for that type of use?
At home, I sit in a 6-stick chair much like the one on the cover of “The Stick Chair Book” – the key to long-sit comfort is that it has a thick sheepskin on it. Sometimes, though, I switch it out for my JA-style chair (a la “Make a Chair From a Tree”) – no sheepskin. But if I were going to build myself a new desk chair, I think I’s go for the lowback one in SCB. I find that to the be most comfortable of all the chairs around here.
Living in southern Ontario, maple is widely available and very reasonably priced. Any concerns with using soft maple for stick chair seats?
No concerns at all; have at it.
I don’t know when it happened, but it seems Lee Valley has stopped stocking Forstner bits. Shocking and annoying as all get up. Any recommendations on a source for quality bits available to northern North Americans? Thanks!
FWIW penblanks.ca carries very similar sawtooth style forstner bits as LV. I’ve bought a few to build kits from there since they were a touch more affordable than LV and I was curious. LV seems to be going through feast-and-famine inventory these days on stuff (e.g., bandsaw blades in 70 1/2″), presumably a C-word holdover.
Good morning Chris and Fitz! I was wondering how far you let the batten into the underside of the seat in the picture above? Is there guidance for what an appropriate range of depth would be and the factors making that decision, such as maintaining maximum wood thickness, movement, aesthetics, etc.? Thank you!
On the one above, the socket is 1/8″ deep. On the desk at which I’m currently sitting (from the “Anarchist’s Design Book”), it is half the thickness of the wood above it (3/8″). I would not go less than 1/8″, but with tight shoulders, that’s enough.
Thank you, Fitz!
I made 2 Ash “creepies” for my kids, which admittedly got abused. A leg broke on both stools, when the kiddos sat/stood on them sideways. Is that a result of grain runout? Poor stick selection? Or is it inevitable?
It is not inevitable. If the break was at an angle, then it’s likely grain runout. If the break is 90° across the leg, the wood was likely brash.
It’s funny – I’m just the opposite. Never have music on in the shop and always at my desk. Usually loud.
Of all the tools listed in Anarchist’s Tool Chest, drawbore pins have (at least for me) seemed to be the most elusive. Are there any tricks for finding them in the wild, or any new ones you recommend that are easy on the budget?
Thanks as always!
What finish would you recommend for a cabinet going in a small bathroom. I made a bunch of that soft wax which I love. Would that keep out any moisture?
As long as you’re willing to reapply it as needed, it will work fine. We use that on the kitchen counters in the shop kitchen, and have to reapply every three months or so…but those things take a LOT of abuse.
Soft wax is not a strong barrier against moisture. You are better off with varnish or conversion varnish.
I am starting my stick chair journey – do you join two pieces to make the seat or do you actually find 20″ wide material somewhere?
I realize now that I phrazed the question poorly –
Is it acceptable to join 2 (or more) pieces for the seat if you can’t find a single piece that is suitable?
Yes, it is perfectly acceptable. (Do you have “The Stick Chair Book?” It’s a free pdf, and will answers lots of questions along your journey: https://lostartpress.com/products/the-stick-chair-book?_pos=1&_sid=80623ba7e&_ss=r)
Copied from Chris’ post “Dumb Stuff to Ignore:”
For years I was paralyzed by the difficulty of finding wood that is 16” or 20” wide so I could make single-board seats. While a single-board seat might be more attractive if the chair is unpainted, it’s not inherently superior to a glued-up seat.
Single-board seats are usually flat-sawn and therefore more likely to cup dramatically over time. But more importantly, their “holiness” tends to dissuade beginners from making a chair.
Here are the facts:
Seats made from two or three boards are common in the furniture record
You can easily reinforce the seat’s edge joints with floating tenons, splines, pocket screws or dowels
Or you can just use a simple glue joint – just like when gluing up a tabletop
Yes, you can put mortises for the legs and sticks through a joint line. It’s not ideal, but the seat will last a good long time. Don’t let this stop you from making a chair.
…Not to mention the wear on the suface of the wheel. My take is that hard use of any wheel-type guide on a diamond plate will shorten the life of the wheel. If I am honing a new primary bevel I use a cheap wheel and then switch to the LN guide for the micro-bevel, on a much finer stone or plate.
One small component is easier because you only need two points to make contact with the ground and they do not really need to align any special way.
My sister and law was throwing out a broken rocking chair that was made with very similar methods as stick chairs (wedged through tenons in the seat).
I offered to try and rebuild its bottom half. I’ve never done a proper stick chairs before but I figured it would be good practice. Also no consequences.
It’s probably the best thing I’ve ever made. I was sad to see it go.
If I had the skills/tools/dimensions to build an upper half I’d be really stoked to build one. It was super comfortable.
What is UR preferred size for Ray Iles Rounding Planes? Tx.
5/8″ (this is a guess…but because we have two 5/8″ and no others, I feel pretty good about my answer)
Do you know which building the back woods chairmakers seminar is being held in at the Berea College? I have tickets but know idea of location of seminar.
Student Craft
We will send out an email filled with all the information you need to know at the beginning of next week.
I made the one on the cover of the stick chair book for each of my offices. Sits well all day (I’m a psychologist, and sit all day), and a visual and tactile pleasure. I hated my prior chair that had wheels and tilted and felt the the teacup ride that the carnies bring to town
The hobbity part makes me think of “Twentse geveltekens”
great question. as a full time professional musician who spends literally 8+ hours a day actively and critically listening to and playing music, my ears need a break. so most of the time i don’t have anything on in the shop. sometimes I’ll listen to a podcast. during extended professional breaks (summer) when i start itching for music again i listen to a wide and eclectic mix of things: everything from ac/dc, Bela Fleck, Herbie Hancock, the wellerman, and of course a large assortment of classical music. only thing i don’t much like listening to is the taco bell cannon in D and the hippity hop music of milton rabbit.
Good morning! For leather campaign stools: Lee Valley carries 3-way bolts. Do you have experience with those (are they worth the cost)?
I have that very nice bolt on one of the campaign stools at my house. It looks a lot better than the hardware-store bolt on the other campaign stool at my house. But they both have worked great for years. So it comes down to whether the good looks are worth the extra $.
Good morning Lost Artisans. This question is for the community. I seek your recommendations on woodworking locations to visit in/around Brussels, Belgium, and near Geneva and Zurich in Switzerland. Could be museums with furniture collections or displays of old tools. Maybe special homes open to the public or places that show woodworking techniques of the past. Bonus if you know of places to buy old tools. You know, to complete that minimal tool set for my future ATC. ;-). Thanks.
Love WMOT!
Any industrial supply place like McMaster-Carr will have drift pins.
https://www.mcmaster.com/products/drift-pins/
I have used long taper alignment punches for years and they work great and cost around $10. Drawbore pins should be twisted and not hammered in so you need to make wood handles for them.
Given that you use soft wax as a finish on the kitchen counters, what are you thoughts on using for the finish on a dining table that will be used daily?
It is also (now, after stripping the long-failed lacquer) the finish on Chris’s daily-used dining table. (You can see it at the bottom of this post: https://blog.lostartpress.com/2023/11/12/a-finish-for-the-top-of-a-dining-table/)
Blues is my favorite genre, so I usually have my Apple Music Blues station on, or the latest release from one of my favorite artists. Sometimes, I’ll have local sports talk radio on or a baseball game (gotta be careful there, the Rockies have a tendency to make me throw things, either in joy or out of disgust). Today, I’m probably going to have a playlist of late 90’s/early 2000’s rap, hip-hop, and R&B that reminds me of the two years I lived in Miami.
Last week, I dropped by while in town for the Congress for New Urbanism. Thanks for the books and the chat about living and building in a dense urban setting (as also discussed in last week’s Earlywood). That afternoon, a session discussed diseconomies of scale, how agility is lost as people prioritize scale and production (Fremont Assembly Factory under GM and Toyota management was an example), and the application of those ideas to home building, community engagement, and improving public spaces. I think those ideas are also at the heart of your work, for which I’m grateful. Thanks so much for what you do!
Awww. Thanks Nathan!
Is there any problem with using hold-fasts in bench dog holes?
Nope
Is there any significance to the orange tape on the boards under the chair?
Means don’t throw these away
Thanks! My copy of the book is on the way to me – I’ll find the section in the PDF as well – but this helps alot.
Concerning today’s Earlywood, one cannot relate to a tree or it’s products the same after reading Richard Powers’ The Overstory. We are connected.
I know people who use 1/8″ tapered alignment punches as drawbore pins
I have photos to submit to your DTC book. Can I simply share a Google Drive folder to Megans email?
You can – and thank you!
Megan, I shared the folder with you. It has a bunch of photos and a Google doc with a description of the chest.
I’ve never seen them turn up at flea markets and the like. I know Ray Isles, Lie Nielsen, Lee Valley and a few others currently make them. But there are good and less good drawbore pins. Some are just tapered rods. The best are eccentric — they go in easily, then you twist the handle to snug the joint up. The ones I use are by Ray Iles, and they are the eccentric kind. I really don’t know if anyone else makes them that way. But I’m a big fan.
Two toady as I’m in the middle of labor pushing a new stick chair into the world:
I find that when wedging the legs from the top I always get some gap on either end of the wedge when using tapered tenons. I’ve been gluing splinters into the kerf to fix this but I’m wondering how you handle this.
Secondly, I built the undercarriage for this chair in walnut and while working on the arms, noticed a small check opening up in the seat. It’s really maybe a hair thickness or two and tracks maybe an inch or two into the seat.
Should I scrap the whole undercarriage of the seat and start again or let it ride and see what happens?
If the gap by the wedge bothers you, then use wider wedges. Remember that a round tenon intersecting a surface at any angle will show as an ellipse. Small gaps next to a wedge don’t both me.
And small cracks in the seat can be nothing. They can be fatal. Or in between. There’s no way to diagnose them or what they will do (as long as the wood is at equilibrium with your shop). If I get a small crack, I usually put an iron plate across it and hope for the best.
Oil for a woobie. Any reason NOT to use canola oil? Thx
I know people who use olive oil and walnut oil in the shop, so I suppose that canola won’t be much different.
I stick to the drying oils (jojoba, camellia) because there has never been a reason to switch.
It’s odd how this topic is coming up multiple times a week. Is there some unseen force that is pooping on camellia and jojoba oils?
I don’t know if this is connected to your other website problems. But Chris and Megan’s responses to questions all seem to go to the proper spot, while almost all others go to the bottom of the page.
Yup. The blog seems haunted today. Will check with the techies on Tuesday. Sorry.
Fitz: Best wishes on the editing pass. Been there, done that (many times) on my software books. Took a lot of rigor to separate content edit, copy edit, structure, phrasing et al. I’m betting when you’re done you’ll sag against the monitor with a combo of joy and loathing. I know I did. 🙂
Canola oil sits on the kitchen counter! I’ll go track down camelia or jojoba oil. Thanks
I’ve had this problem.
My solution is that I try to get the area that receives the tenon as close to the tenon shape as possible.
I mark a 5/8″ circle with a compass on the top of the tenon and mark 4″ down (you can experiment with this and find what works for you, you could probably get away with 3″ if you want a really crisp transition to the tenon, in practice I like a little more of an organic feel).
I then use taper cuts with my block plane from my 4″ mark down to the circle I made all around. Then I knock down the arrises and a few spins around the tenon cutter and I’m good to go.
I use a tiny Bluetooth receiver connected to Etymotic earphones that do a good job of blocking machine noise and provide very high quality sound. This allows me to stream IDAGIO—a classical music streaming service. I also stream a number of different podcasts. But, if I am doing something complex, I have to turn the music and the podcasts off or I make too many mistakes.
This Spring I’ve had some issues with my hide glue. Both the Titebond and my own mixture with granules purchased from Bjorn Industries and heated to about 130-140 degrees. The Titebond was used before its expiration date on the bottle and my own mix was made about six months prior. With both, the squeeze out never seemed to dry and was still gummy after two or three days. The hot glue especially didn’t “self clamp” on several test glue blocks as well. Could the glue be bad or perhaps the weather was too humid? Doesn’t hide glue dry by loss of moisture? Would running a dehumidifier during glue ups help? Thank you!
It’s a natural product, so it’s natural to have problems on occasion.
Titebond…. can’t say. I haven’t used it in five years because I had some glue failure in a chair. On other kinds of hide glue, I don’t find that humidity has a big role. Temperature seems more important.
When the glue fails to set up, usually the glue has been overheated or attached by mold or is old. Before I use a batch that has been sitting around, I put some on my fingers and see how it tacks up. Long strings of adhesive are a good thing. No strings? Bad thing.
Another thing that slows hide glue is that the wood is a bit wet. The moisture in the wood can prevent the hide glue from getting hard until the water has evaporated.
From the sound of things, especially the failure of rub joints, my guess is the glue was overheated or is old.
Thank you so much. I will do some tests next time and heat to a lower temperature. I’ve had great luck with the Old Brown Glue from the bottle slightly warmed up.
Have you read “We” by Yevgeny Zamiatin? If so, where do you stand on the theory that both Orwell and Huxley cribbed from it?
I have not.
I reached out to the Pure Soap Flakes folks to ask how the make their pure castille cream soap, since I’ve had trouble with the recipes in ADB. For the interested here it is (almost exactly the same as the second recipe in ADB:)
Equal weights Pure Soap Flakes and Pure Water, for example, 1/4 pound Pure Soap Flakes and 1/4 pound Pure Water (distilled or reverse osmosis). Put in bowl and stir together. Cover and let sit over night. Next day, stir and mash. Let sit for another 6 hours and sir and mash. Use as is or whip with beaters.
Gutentag,
Chairs: ever see an older kneeling stool like for drafting? Or does the history of kneeling chairs start in the padded pews of the Vatican?
Cats: any advice for young daughters mourning a recent coyote event in which we find our pets head and collar? We are too denatured of ancestral culture to have anything prepared. We are deconverted evangélicals and more likely to want alternate perspectives than heaven talk…
Oh my. I’m so sorry about your poor kitty. I have no advice…except that I still miss all my former cats, but the current ones help to assuage some of the sadness.
I’m afraid I have not seen early kneeling stools that are not church-related.
We lost three cats while our daughters were young. For two of them, we built coffins and buried them in the back yard and gave speeches about their fantastic lives. The daughters still talk about how they love that Carrie and Janie are buried in the back yard.
The third was cremated, and our daughters took some ashes with them and distribute them in places they visit (the Grand Canyon, the Alps…..).
These things, while seemingly shallow, have been important to the kids thru adulthood.
Gibson chair: I’m building two without saddling the seat. Any advice on drilling the legs from the top to shift the potential for tear out to the bottom of the seat and spare the top? There is a photo in ACB of you drilling from the top.
I’ve did several practice mortises for the legs in red oak. Even with the Wood Owl auger I’m getting significant tear out. Granted, my practice mortices were not backed up and I got better at sensing when the auger was close to breaking through. But, my powerful corded drill with a handle sometimes just pulled me through the last of the hole with little control. I tried to run it slowly but that is a finesse thing and the motor heated up. My battery powered drill, same model as yours, refused to drill into the oak. There was usually no tear out around the mortices where the auger entered the wood hence the strategy to drill from the top.
You can figure out the offset using the resultant angles and the thickness of the seat.
You do not want me to do any cyphering on your behalf. I was a journalist.
If your 20v DeWalt won’t drill through a seat with a 1″ bit, then
1) Your drill is defective
2) You don’t have it in low speed with the clutch turned off
3) Your bit has problems.
That DeWalt will bore through rock.
Duckfat and the Frites Shack have been sold. Rob and Nancy are retiring to western Maine. The new owners are retaining everything – staff, menu, philosophy. (I live about a mile away)
Larry Barrett here – I have made drawbore pins using alignment pins. Here is a link to one example:
https://www.amazon.com/TEKTON-66177-4-Inch-Alignment-Punch/dp/B00QV2JBTW/ref=asc_df_B00QV2JBTW/?tag=hyprod-20&linkCode=df0&hvadid=693341074248&hvpos=&hvnetw=g&hvrand=12315011417618460730&hvpone=&hvptwo=&hvqmt=&hvdev=c&hvdvcmdl=&hvlocint=&hvlocphy=9008024&hvtargid=pla-570730892831&mcid=e648149c4bb23051834306f27d8a0af0&gad_source=1&th=1
For a flattering plate for sharpening stones, you’ve recommended a DMT diamond plate. Are there any other options that are more affordable for someone who doesn’t need to sharpen everyday?
Wet/dry sandpaper paper stuck to a flat tile is a low-cost entryway to flattening your stones. I have also clamped drywall screen to a tile. And I have used a cinderblock in a pinch.
When I first got waterstones, I was taught to rub the stones against one another (there was a skewing action to prevent sympathetic curves). Of course, if you do that, the Grit Contamination Police will come and arrest you. But if you can wash the stones after, you won’t have a problem that a normal-headed woodworker can detect….
Afternoon Chris & Fritz:
I combined two things you are passionate about – stick chairs, and SYP! I have TSCB and knew that on my first try to make a chair, I would screw something up. Being budget minded I couldn’t stand the thought of scrapping any good hardwood, so I decided on 2 x 12’s – my total costs was less than $50.
Have you ever tried this? I had some issues, some splits, and blowouts but in the end, I have a chair. And I learned a lot.
I made some stools, and a few ugly chairs, decades ago, ala Drew Langsner’s ‘Green Woodworking’. I think that is my next goal.
Thanks for the inspiration!
DJ
I’ve made many many stools in SYP and several chair prototypes using the material. If it’s slow grown and straight, it’s great.
Don’t want to saddle it….
Too late…It’s saddled.
Greetings!
Thanks again for fielding questions every week.
Q: I’ve used mutton tallow for years on my planes’ sole. As my supply is running out, I’ve been looking to replenish, however it seems to be now a rare commodity.
Just wondering if you’ve heard of some change (e.g due to Covid) or if people are switching to better products? Any insight/recommendations? (I’m not going to make my own…not even giving it a moment’s thought)
I’m finding a fair number of buying options online – mostly through meat suppliers. So first, I’d check with your local butcher.
You can use Crisco. It has the same properties as mutton tallow. I don’t have any insight to the mutton tallow industry I’m afraid. A sheep uprising/unionization perhaps?
I have the same question. The octagon (tapered, which end doesn’t matter, the end you want to insert into the seat) is too big to fit into the business end of the cutter. So you trim/carve/lathe etc it smaller. The cutter blade doesn’t go all the way to the edge of the tool. So there’s a gap between the end of the cut taper and the shoulder I.e. untrimmed octagon part of the leg, ergo “transition less crisp”, the part you hacked to fit the cutter but wasn’t reached by the blade.
If there is part of a tenon that is not getting cut, then you need to remove the offending material that is preventing the leg from entering the tenon cutter.
LAP, Do you do your chair drawings in house, or do you give them to a local firm,
I’ve done the last few. The ones in The Stick Chair Book were done by Josh Cook, an industrial designer.
As a follow-up to a question I asked last week: How many hours cumulatively would you estimate building that oak Roubo bench you, Chris, built with Will would take if you did it basically on your own with hand tools, save for a jigsaw, a bench press, and a circular saw (with rough-cut oak lumber direct from an oak tree, dried out)? (I don’t have a band saw.) 12? 15? More? Thanks!
Likely 80 hours.
Wow. That’s good to know. Need to work on other projects in between bouts of work on the bench.
Do you know, and this is just idle curiosity, was the chair from the movie bought (from an estate sale or whatever), or made new just for the movie?
Ha! There’s a 3D model. https://fbi.cults3d.com/uploaders/16677375/illustration-file/ad9d6e46-b711-4efe-a4e5-a850e13de9f0/Chair.jpg
Doesn’t answer the question, I just thought it was interesting.
I do not know. My guess is it was made for the movie because I have never seen a chair like that before.
Hi, I know you guys are super busy, but .. I think it would be a cool idea. A wood shopping class, just one or 2 days teaching the more dumb of you followers how to choose straight grain lumber for chair parts, at a decent price. I’ll be willing to drive the 17 hours from my place to yours for this chance. I just stopped at a place here in Miami and they charge $ 7.49 per Linear foot of 2 by 4 red oak, it’s s4s it looks kind straight but in my opinion is super expensive, at that price I definitely don’t it to fail the lump hammer test.
Hello LAP,
I am jointing the three top slabs of an anarchists work-bench today for glue up tonight.
Q – What am I forgetting to do to ensure a good fit?
Kidding / not kidding 🙂
-Matt
When you glue up the three chunks, make sure the clamp pressure is equal on the top and bottom while you are intently focusing on closing gaps on the topside during the fog of war, otherwise it will cup. Check it with a straightedge. Don’t ask me how I know. But, my hand planing skills have improved.
A dry run with clamps?
Waiting too long after you joint? (I won’t let a jointed edge sit out for more than 30 minutes before gluing it)
Getting F-styles out to clamp the laminations flush at the ends?
Hopefully, this is clearer (it’s certainly longer):
1) I octagonalize a leg (tapered from about 1 3/4″ where it joins the chair to about 1″ at the foot).
2) I rough taper the top of the leg and then start using the tapered tenon cutter.
3) I want to cut my tapered tenon until the tip enters the narrow part of the cutter. But, before I can cut the full length of the tenon, the leading edge (wide end) of the cutter runs into the part of the leg that doesn’t need to be tapered. [The distance from the edge of the cutter to the blade.]
4) To advance the cutter the full distance, I need to narrow the top of the leg making for an extended narrow section at the top of the leg before it enters the seat and an awkward transition.
Maybe I’m just making the tops of the legs too wide? Maybe I’m making the tenon too long?
I wouldn’t worry too much about this for a stick chair. You will figure out the correct taper so that you do the minimum amount of cutting with the tapered tenon cutter. The skinny bit at the tip of the tenon is cut away. The transition between the tenon and the non-tenon can be finessed. And the legs are cut to final length and no one can really tell if the tapers are slightly off anywhere.
I rough in my tapers from about 4″ from the tip and aim for a fat 5/8″ at the tip. Try slightly different measurements until you get where you want to be.
Sorry I’m not an engineer here.
So, tools, cats and Russian literature? Cool!
Nailed on breadboard ends, what do you think? Doable, or a bit too rustic? Add tongue and groove in addition to help keep it lined up? Would nails (Rivierre for example) have enough flex for wood movement, or would I still need oval holes?
We’ll be moving home with our cat soon, any tips?
Have you read Oblomov by Ivan Goncharov (mid 19th century)? My favourite novel, and Tolstoy also loved it.
Nailed-on breadboards are definitely a thing in vernacular furniture. You can tongue-and-groove them. Or not. I did one once as an experiment. It worked fine.
I have not red Oblomov….
I finished my AWB, 6 ft edition. My sincerest thanks for the decades of research and experience you distilled into the book and plan, and the occasional Q&A support here. The book is a great read and the end product is both beautiful and functional. BTW, I used KDAT (Kiln Dried After Treatment) SYP, which uses MCA (Micronized Copper Azole) treatment and it didn’t run my tools and didn’t kill me (yet). I did use very good dust hygiene practices. A few of the boards have a little Vulcan green tone to them.
Knowing you like to cook…how do you sharpen your kitchen knives? I’ve never really struggled with sharpening my tools, but just can’t seem to keep our kitchen knives sharp or sharpen them successfully. We have Wustoff knives and some Japanese ones. I can’t seem to get an edge or burr on them without using a low grit stone (I think it’s 200) which is rough and not really sharp. Going to finer stones doesn’t seem to do much, and is no where near as effective as sharpening my tools. Is the steel just too hard?
My kitchen knives are all low-rent non-brand-name carbon steel. I sharpen them with this cheap gizmo.
https://www.amazon.com/gp/product/B072HVMYZC/ref=ppx_yo_dt_b_search_asin_title?ie=UTF8&th=1
Does a great job in seconds. I know there are people cringing, but my squash surfaces will not be examined by vegetable conservators in some far flung future. Git it dun.
Gibson Chair: Drilling leg mortices through the top. Yes, I should have said that I did a scale drawing to figure out the offset and just moved the starting point for the “worm” that distance along the sight line towards the center of the chair. Just geometry with lines and no math required. Because it is the center point, the fact that the hole at the bottom and top surfaces is an oval doesn’t matter. I also extended the sight lines on the top of the seat to the edge of the seat so I have a longer sight line to aim at between the mortice and the edge of the seat. I didn’t have the cordless drill set right and I’ll give it another shot. Thank you.
I buy ground lamb and cook it in a frying pan (moderate heat, no burning) to render the fat, pour through a strainer into a clean (heat resistant) container and let it cool. Don’t season the meat until after pouring off the rendered fat. The tallow lasts for years without any cover or refrigeration. I don’t bother with water baths. No need for the added complexity.