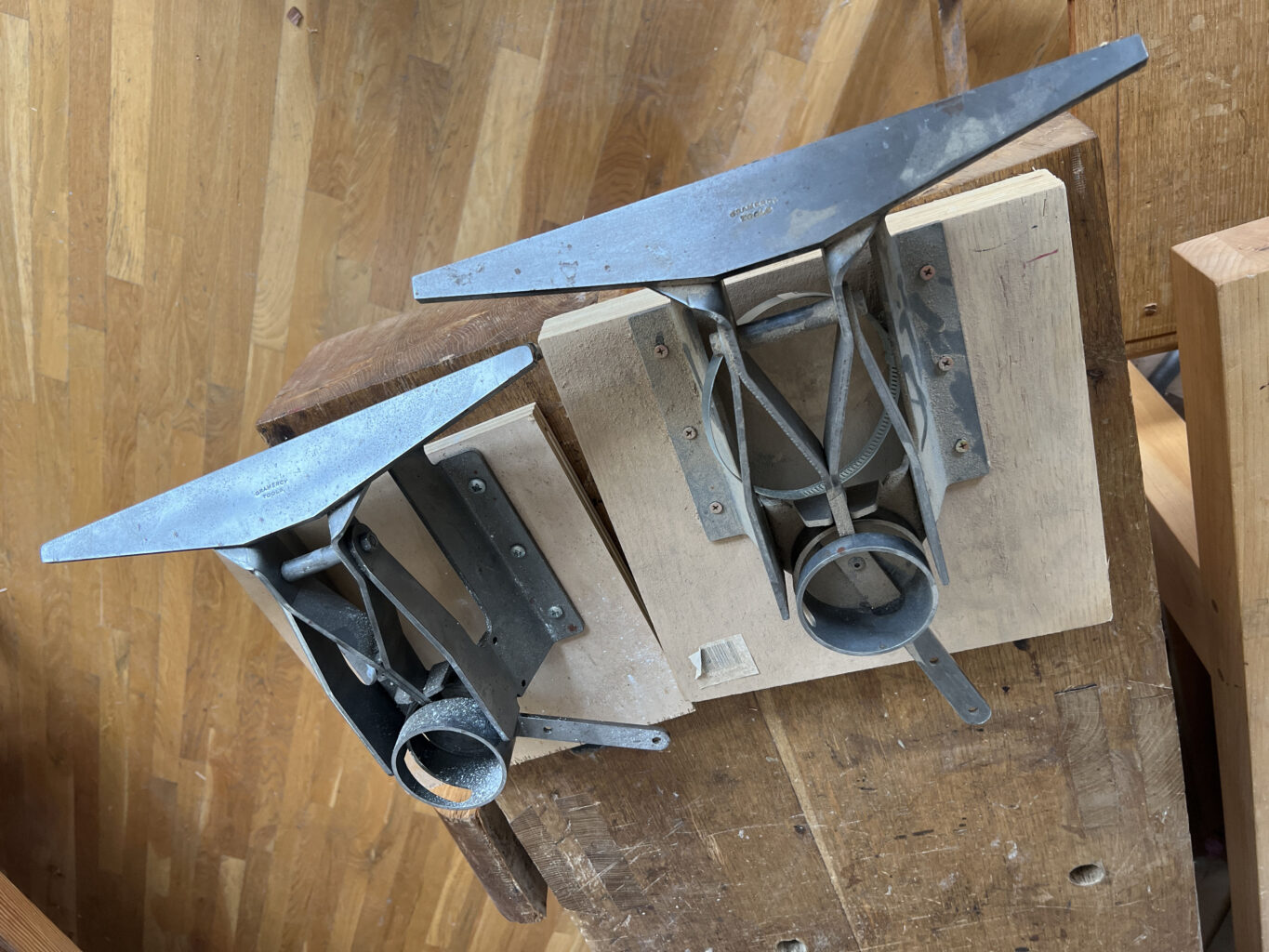
I think the last time these saw vises got used was during Matt Cianci’s last saw sharpening class in our shop. In 2019. We unearthed them from our respective basements for Matt’s class going on today and tomorrow – and we will have our ear plugs at the ready. (It is not a quiet class.) And I will try to talk Matt into taking my super-dull dovetail saw home with him to sharpen. (I have a good saw vise, obviously – but I also have bad astigmatism – I’m not touching my dovetail saw with a saw file!)
Chris and I will be at our computers all day (that’s a lie), ready to answer your woodworking questions (that part is not a lie). You know hos this goes: Post your (succinct) question(s) in the comments field below, and we shall do our best to answer.
Comments have been closed.
– Fitz
My daughter is into equestrian. I was hanging out with her trainer at a show last night and noticed that the tack boxes they use are really not very nice. Plywood mostly with mitered corners that fall apart quickly. These things get used and abused, which made me think that the ATC design would be perfect for a tack box (just need to scale it down). Here is my question.
Would you still go for the same woods? These, like old tool chests, really DO need to move each weekend and get lifted (they don’t like casters….maybe it’s a weird tradition thing). So, pine is difficult to come by where I live, which means maybe Linden (what I used for my ATC). Still an inch thick? I walked around the stable and noticed most of the others look to be more like 3/4. It doesn’t carry heavy tools, but does get banged around.
Finish….I’m thinking pain here for easy touchup. Would linseed oil paint be good? Seems to be very durable when fully dried and totally non-toxic should a horse decide to eat a bit of a box.
I doubt you have any particular thoughts here, but do you know anything else about tack boxes that would be useful?
My plan is to make one and let them auction it to raise funds for the lesson horses. If people like it, perhaps I can corner the market on anarchist horse boxes.
I’m no expert on tack boxes, but it is a tool box that requires a lot of the same properties as a cabinetmaker’s chest. The old chests were supposed to be moved – a lot. And they took a beating. So I would use whatever wood is lightweight, cheap and strong. Linden is a great choice.
As to thickness, anywhere between 3/4″ a 1″ will be fine. Get whatever is most available.
As to finish, linseed oil is a very durable choice. But latex is also a good choice. Eating a little dried latex is unlikely to hurt a horse or a human.
I have made several tack trunks over the years, to reasonable acclaim. I used birch plywood as a shell, and trimmed with white oak for strength and look. Pressure treated skids on the bottom. User-chosen stain and poly varnish for finish. Nice brass corners and brass handles on the ends for a finished look. Happy to share dimensions and pics as needed.
Still a fan of Rivierre nails? What shape and colour do you usually go for, and what sizes have worked the best for your furniture projects?
Any issues with bending them for clenching two boards together?
(For once I’m lucky with shipping; I live close to the French border, so I can get free shipping. Usually I have to pay through the nose to have things sent from the US or UK.)
I use them a lot – mostly the 40mm and 50mm, and preferably in black (but I’ll use the blued if it’s all I can get!). I think I’ve had maybe one bend on me (which I attribute to hitting it off kilter).
Remember to drill a smaller hole first. You knew that!!
The Rivierre nails bend really nicely with out breaking. I sometimes do what call a half clench to save time. I drive the mail in tight then turn the piece over and with the mail supported on a solid surface below I chisel out a divot to seat the bend and just bend it over. It holds like a honey badger. I did a French cleat this way last week.
Good morning. On the American Trestle Table, is there a rule of thumb for how wide the feet and braces should be based on the length & width of the table top? With general cantilevers I’ve seen that it’s usually a 2/3 supported, 1/3 flying formula. The one I plan to make will be 30″ or 32″ x 72″.
Thanks for the great resource.
What do you folks think of corrugated bottoms on bench planes? Thanks!
They are not worth paying extra for – unless you are a collector. They make the bottom easier to flatten (which is a small thing). They don’t reduce friction (surface area is not a coefficient of friction). I like the corrugations on my jack becase it makes them go faster (like racing stripes, JK). But wax builds up in them , so I don’t have to wax as often…
A quick question on sharpening solution (sounds of peasants sharpening pitchforks). You’ve posted a few times about water stones, water use on diamond stones and the premier snake lube which I still can’t find for sale anywhere despite the catchy logo. I sense a preference against oil as a sharpening solution though I can’t really tell why. Is it simply that water is more widely available?
I would like to switch to the Shapton Pros when my current diamond plates wear out but I work in an unheated shop and oil keeps me working later into the fall and winter. The Shaptons say they’re compatible with oil but one started, must always use oil. In short, why water/Windex/blue mystery fluid over oil and would you consider oil on water stones if in an occasionally frozen shop?
Thanks in advance- I know some people would rather pass a kidney stone than talk about sharpening stones but I would greatly value your opinion before putting about $400 down on new gear.
When using real milk paint, what brushes do you use to get a smooth finish?
The milk paint experts are Travis Curtis and Pete Galbert (who offers a video on it). But I know Travis uses little pieces of sponge. I don’t necessarily for a smooth finish … so you don’t want to ask me. (But if I do want a smooth finish after using a cheap chip brush, I burnish the paint with a white or gray 3M pad after it’s completely dry.)
I have been wondering how the fellow who was hurt helping someone fell a large tree is doing?
You can follow Joel’s progress here on his Instagram:
https://www.instagram.com/13starsfarm/
I bought a nice set of diamond stones and decided, after your Sharpen This book/video to take your advice and use a honing guide. So I bought a Lie Nielsen honing guide, but overlooked the fine print (actually small bold print) that warns against using it with diamond stones (they don’t explain why). So now I’m looking at $300+ worth of sharpening gear I’m afraid to use. What do I do? Use it anyway? Or get water stones?
I would call and ask Lie-Nielsen why that is the case because I don’t know. I have not heard that before…
Certainly reach out to Lie Nielsen, but for what it’s worth, I have the Lie-Nielsen guide, use it on EZE-Lap plates, mostly 400/1200 to get a working edge. Have had it for about 3-4 years and it works wonders. I’m only a hobbyist user but I’m still sharpening something almost every weekend. It’s held up fine, if it assuages any fear. Happy sharpening!
Have you had success making your own paint? In anticipation of painting furniture built from The American Peasant, I was looking at linseed oil paint, which is quite costly, and thus was looking into making my own. Do you have any experience or thoughts on this? Thanks!
I’ve messed with it. Muddling pigment and linseed oil on a glass plate. But I haven’t made anything I’m ready to put on a project. Peter Follansbee shows his process in “Make a Joint Stool from a Tree” and the YouTube world of fine art instruction has TONS of infor.
I’m using my Dutch tool chest to hold art supplies and I haven’t built the racks, etc. If you extend the deadline for submitting pictures to 2025 I’ll be good to go.
Ha. No.
(But I’ll post pictures when you’re done)
Good morning!
Currently building a version of the AWB using two 2-1/4″ thick hard maple bench tops; would you recommend keeping the leg mortices at 3″ or making them slightly shorter? Thank you!
You can make them shorter and be OK. Mabe 1-7/8″ so you have some room for (many) future flattenings.
I wasn’t able to attend Matt’s class. I hope he will offer another one.
Sawstop/liquid hide glue question for anyone…
Recently had my saw stop cartridge activate while cutting a piece of wood that had been glued together by homemade liquid hide glue. Used salt when making this glue and was wondering if that might have had just enough similarities to human flesh that it activated the cartridge. Has anyone else come across this? I asked the people at Sawstop but they were not familiar with liquid Hide glue.
I cut through liquid hide glue joints almost every day and have never had a problem. Have you sent the cartridge to them for analysis?
I did, they said it was something conductive (metal?). A double checked and there was nothing on/in the wood. It was very odd. I’ve been using my saw for 10+years. This was the first time it had activated.
Thanks for your input.
Building my first dining table and will use breadboard ends. I know to leave a gap on either side of the tabletop tenon for expansion, but since the breadboard will be perpendicular (duh), when the top expands it would then be wider than the length of the breadboard. This seems obvious, but I’ve never seen it in practice. Am I missing something?
You are not missing something. My breadboard-end dining table is perfectly aligned where the breadboards meet the long boards only twice a year or so. It’s such a minor difference though – unless you’re looking (feeling) for it, it probably won’t be noticeable.
Referencing post from January 21 2024 Even Better Stick Chairs: The bottom of the comb is 8-3/4″ above the arm’s shoe. Chris finished off the post with the idea of moving the comb down to 8″ above the shoe. Have you made a chair at 8″? If so was it as good or better than 8-3/4″? Thank you, Jake
I have not gone lower. Yet.
you’ve written about the festool vacs. do you have any experience or thoughts on the fein turbo vacs?
I’ve used them. We had a couple in our shop at Popular Woodworking. They work well. Fein has always been pretty niche-y in this country. (Festool used to be like this.) I default to Festool because you can get accessories and bags anywhere.
Hi
I have owned two of them for about 20 years and they are still going strong. I have Festool sanders and a router and have switched out a Festool hose for the fein hose and it works great!
They roll easy and have been used for sanding/routing wood to sanding drywall.
You can get accessories, metal extension wands, brushes, etc. and replacement filters for them.
I just empty them periodically and gently tap the dust off the filter. Flies right back to work!
Gibson chair: In your Gibson chair video you explain how you taper the long arm post sticks but not the inner long sticks which appear to have different tapers than the two long arm post sticks. The upper half of the inner sticks looks thicker and the swelling is slightly higher compared to the arm post sticks which have to pass through the mortise in the arm. The inner sticks also have flats in the lumbar region. I’m shooting for aesthetics here but if the flats increase comfort I’ll add them. What rules of thumb or visual cues do you use to taper and shape the two pairs of the inner long sticks for your Gibson chairs?
Veritas tenon cutter: I’ve watched your video and read your blog re how critical it is to control the drill and tenon cutter. My tenon cutter came with shim material and the owners manual suggests that I can use one or more shims to reduce the thickness of the shaving so less torque is needed to make the cut which would give me greater control. I made a few practice pieces for my first tenoning attempt later today but I’d rather not eat through my stock practicing when a technical fix like the shim might give me more control. Have you tried the shim technique?
Q: Why did God command that the backs of Gibson chairs be sawn from a stack of laminated planks?
A: He has a side gig selling oscillating spindle sanders.
Thank you for making time on your Saturdays to answer questions.
The tapering on the back sticks is done the same way as the posts. The difference is that you don’t have to plane the back sticks as much because they don’t have to pass through the arm. So it’s mostly aesthetics. The originals didn’t have flats – they were roundish. I mistakenly put flats on my first Gibson. I like the way it looks and the way it feels against my back. But either way works.
On the tenon cutter, I have used the shim and it doesn’t seem to make a difference with the drills that I own.
On your Q&A on the Gibson backrest: The originals were cut from one solid piece. But they were definitely bandsawn – you can see the blade marks on the backrests. You can remove most marks with a curved-bottom spokeshave and a sanding fid/form that is the same radius of the backrest. (If you son’t want to buy and OSS)
What are your thoughts on the blade quality of vintage Stanley jack planes? Is it worth keeping? Or would you upgrade to a Veritas blade?
They told me that it’s because of little diamond fragments getting into the wheel of the honing guide. But over the years I have used my honing guide on a mix of diamond stones and now ceramic stones. I haven’t noticed. Regardless, they said it’s about a $5 part. Hope this helps!
Has anyone viewed an example where the breadboard ends are deliberately cut shorter than the with of the table? Maybe, oh about 3/16″ shorter at each end of the breadboard (3/8″ shorter overall than the table width). This would leave a slight reveal of sorts at the table corners. Light, judicious shaping of the respective corners of the table and breadboards (i.e. gently round the corner edges with sandpaper) may create a touch of visual interest and completely conceal any seasonal dimension changes.
Maybe.
I have not seen this. But I’m sure it’s out there. Somewhere.
I think I’ve seen that on British Arts & Crafts tables.
Hi Chris and Megan! I think I’ve read before that you sometimes use a sprayer rather than brushes for finishing a piece. Do you have a dedicated shop space to do so? Or just go outside? And do you notice a difference in results between the sprayer vs. a brush? Would love to hear a recommendation for one–perhaps a Never Sponsored post?
Best to you both from CA,
Jake
My first woodworking job was in a spray booth, so yes, I spray at times. We work outside and spray mostly shellac and acrylic. It is insanely fast and (when you get decent) leaves a very consistent surface.
After I left my job where I had access to a Binks 2000 spray system, I bought an Earlex, which is now sold as the 5500. It is shockingly good for a converted vacuum. I wore than thing out after 10 years and bought an Apollo Eco 5. It has a little more power and is more metal than plastic. So it will last longer. But it doesn’t leave a better finish.
I ripped some red oak for 27″ long sticks on my bandsaw. When ripping the 3/4″ x 3/4″ sticks from the 3/4″ x 1 3/4″ strips, the resulting sticks bowed (if set on a flat surface, about 3/16″ at the worst in the middle). Seems to have been from released tension. Grain is pretty straight and they passed the lump hammer test. I suppose it will make octagonalizing a little trickier. Is this something to worry about? I know long sticks will bend in assembly, but is this a bad sign? Can I use the bow to my advantage?
As long as the grain is straight, I would have no problems using sticks that bowed during ripping. Shaving them is a little bit trickier, but they are not weaker in any way.
LN has added this detail to their honing instructions. When I asked them about it, they said diamond dust gets up into the wheel of the honing guide and stops it from turning, then you get a flat wheel.
We use ours on diamond stones with no problems. Just a data point to consider.
When using tongue and groove boards on a outside project, do the tongues go up or down?
Tongues down (so they don’t collect water).
Yayayayayaya. I got turned around. Of course I meant tongues up.
I am about to build my first stick chair, and have a wide variety of wood to choose from. This chair will be the first in a set of six, for the dining room table. I may or may not paint. I could use maple, cherry, poplar, spruce, white oak, red oak, mahogany, hard tropical woods…
I have the necessary tools, your book, and I am an advanced beginner.
Any suggestion on species? Can I mix woods – I have some straight grained elm I can use for short and long sticks?
If I were a beginning chairmaker jumping into this project I would use:
1. Poplar for the seat (easy to carve, resists splitting)
2. Oak (any species) for the sticks, legs and stretchers.
3. The arms can be made out of whatever you have.
And paint.
My favorite combination is elm for the seat, arm and comb. Ash for everything else.
Awesome. Thanks, Chris!
Good morning.
I just finished up this really cool looking chair that I saw on the inner web a while back. It’s a “Irish hedge chair” with a paneled seat. I really like the design, and I’m super happy with my results,
I’m just curious about your thoughts on the construction. The frame of the seat is built with really big through mortise and tenon joints and the leg mortise’s are drilled through the center of those joints on all 4 corners. I’m guessing that obviously weakens the joint a bit but have you seen those style of chairs before? any thoughts on durability overtime? Thanks a lot
Never noticed that either, interested in LN’s reasoning as well.
Megan and Chris,
Is there a trick to ensuring your SawStop slider remains square? When you put the fence back in, is it square right away, or do you have to fiddle with it?
When I put mine on I have to spend some time loosening and tightening and using my 12” combo square against the blade, then test cutting, then repeating the process several times before I get it dead nuts. Sometimes more than several times. And it’s more trial and error that getting it more and more dialed in on every test. (The combo square is the biggest accurate square I have; I’d buy something else just for this task if I had a procedure that I had confidence in.)
I mostly use the slider to cut plywood parts for cabinets, but I’d like to use it more for all my crosscuts. But I hesitate because of the fiddliness. It’s worth the fiddle for a built-in, and definitely for a whole kitchen (I’m building my own kitchen now with Nancy Hiller’s book), but not for a couple small parts. And it would be a whole lot cooler if it either was square right away, or if I could get it square in less than 5 minutes. I’ll probably only ever use it for 90° cuts.
I bought it because I known Nancy Hiller used one and you guys use one, and I saw that Nick Offerman really like the one he has. I can think of a way to ensure squareness, but it involves drilling holes in the carriage, and that seems last resort. Hoping you have a solution.
Thank you both for creating this forum, and for the community you’ve created.
All sliders, regardless of brand, require resquaring. If it can go out of square, it will go out of square.
So much fiddling. Always. 🙁
Great, thank you!
I commented a while ago about my travails attempting to make my own soap finish with soap flakes. At this point I have tried both recipes in ADP, and I tried by weight and by volume. I was glad I’d ordered the soap cream or whatever it’s called, because it came out great.
Mostly wanted to let other readers be aware that even carefully following the instructions the soap finish really just inexplicably doesn’t work some times 🤷♀️
(If interested in the final product, see it here https://foolishwood.substack.com/p/i-made-a-chair)
Isn’t that backwards? Tongue (male) goes up into the groove (female) in order to shed water as it sheets down the face? Same as lap siding, just with, essentially, a dado instead of a groove. As we used to say, “like a fish!”
Just a note that (at least for me) the emails for this post were not working. No email this morning.
Hi Michael. I just checked and you are in our database. If you could check your spam folder perhaps? You have defiunitely received one of the emails from the new server and clicked it….
I found two options for resultant leg angles on the low back chair in the SCB. Also found the clarification on this blog. Which angle will work best for use only at a dining table?
Both work. I usually use 23°.
Not woodworking related but I thought I’d pass it along to Megan, (or Chris if he wants to buy Megan something unique for a birthday or Christmas)
https://www.jamescookartworkshop.com/product/william-shakespeare-limited-edition-of-200-hand-signed-print
(FYI I sent this via email to Megan a little while ago but with your DNS problems she might not have seen it so I stuck it here. It’s pretty dang cool how he creates his artwork.)
Check out his entire website. The guy is incredible. There are videos online of him creating all of his work with vintage typewriters.
I don’t remember seeing that – but it’s cool!
I have a splitting Windsor seat, sticks and bow not tight, all appears dry. Thinking linseed oil. Good/bad idea?
Oil won’t hurt it.
I’ve been struggling, recently, with sharpening chisels. Two different problems have emerged:
1) my narrow (5/8 or less) chisels end up skewed. I’m guessing I’ve done something weird to the Eclipse-clone I use, but I can’t figure it.
2) my wide chisels (1, 2″) are … dished? I establish a consistent burr and scratch pattern on the 1000 stone, but when I move to 4000, the polish mostly happens at the center section. I have to polish a looong time to get the whole secondary edge polished. It’s as if the stone is domed in the center – but I flattened it with a dia-flat.
Help? Where to start?
Thanks
Both sound like problems with the meat behind the guide. Keeping chisels stable on the stone – even with a guide – requires deliberate strokes. When I train people to sharpen narrow chisels, I put the index finger of their off-hand on the tip of the chisel. And then work the stone only on the pull stroke. THis helps immensely, but not as much as practice.
On 2) when this happens, investigate the secondary bevel of the tool and the stone with a small metal ruler. Is one bowed? THen that’s your answer. If both are flat, you are the problem. Again, practice like above. Slow and most of all – steady pull strokes only.
Yes, the meat is often the problem, but the meat often can’t figure out the problem. Thanks for the guidance.
Q on English tool chest dust seals: as the hinges create a small gap on the back edge and hold the lid out of parallel, do you slightly taper the dust seals on the sides to allow the front edge of the lid to rest on the rim of the case, or rather keep them straight and have the weight of the lid held by the front seal against the skirt? Thanks!
I do not taper the dust seal sides – and I just looked closely at my LAP shop chest. There’s maybe a 1/16″ gap at the back…and my eye can’t detect a differential on how the side meets the dust seal along its length.
Dust seal touches the top skirt. No tapering.
In all of the edge tools you’ve owned or used (chisel, gouge, scorp, adz, drawknife, etc.), which takes and holds the best edge?
For me it’s the drawknife…because I rarely use it 😉 But among the tools I use, my 1-1/2″ chisel from Barr Tools.
Barr tools. All of them.
One more question for you guys,
Do you have a rec for a high-quality swing arm compass?
Megan I admired your Peter Ross dividers on instagram this week, I’m wondering if there’s anything similar available that’s a compass.
I’m willing to cry once if I only have to buy once.
I use a Starrett. Holds points or pencils.
Those are Chris’, just to be clear. I don’t know of any commercially available exceptionally pretty compasses (compii?) – but maybe Peter Ross or Tom Latane could make them for you.
Red Rose Reproductions also has 5″ and 7 1/2″ dividers that can be converted to pencil-holding compasses. https://redrosereproductions.com/tools/Layout-Tools-c82776200 Not cheap but well-made
Another link unrelated to woodworking, but of great interest to people who love beautiful handmade things and/or people who publish long-lasting books:
https://sfstandard.com/2024/05/18/san-francisco-arion-press/
Makes me wanna haul my ass across Market Street to try to weasel my way in to check it out in person!
H/T to Julie Zigoris, an excellent writer and even better person.
Would you have any reservations on using soft wax as the finish for a cherry book case? Specifically should there be a film finish of some type (shellac) to perfect the books from the oil/wax of the soft wax?
If you wipe off all the excess (as you should – it get sticky otherwise), it will work just fine, and not transfer to the books.
I’ve been experimenting with soap finish on ash. I like that the finish doesn’t turn the wood yellow like other oil finishes. But the finish removes the pink undertones from the wood and brings out a bit of greenish color. Is there some way to preserve the pinkness of the ash? Maybe by adding something to the finish? I’m trying to strike a delicate balance between keeping some warmth to the finished piece and not turning it too yellow.
Soap is water-white, so it has a blue/green cast. My solution is to do nothing: Let the wood age a bit and it will bring forth a warmer undertone.
Curious to know your take on Paul Sellars’ freehand sharpening of kitchen knives, using sandpaper, general ethos of finding affordable solutions rather than buying expensive one-off tools, etc?
I’ve never seen Paul’s method for sharpening knives. But every system works.
Paul has done a lot to bring people into the craft and should be commended for that. The craft is big enough for thousands of different points of view. Paul likes inexpensive solutions. His view is entirely valid.
Me, I like really well-made tools and am happy to support small makers, even if the price is high. Why? Because that’s why I do for a living, too. My furniture is expensive (to most people). So I am overjoyed to be able to support like-minded artisans.
I wish to apply aesthetic anarchy to the creation of new classic homes, which will last 200-500 years. Think “the 1000 year house” with less brick. My first hurtle in this might be heading towards a renewed understanding of framing as a trade? Anyone working on this?
Think timber-framing. Check out the Shelter Institute in Maine for starters.
Thank you! Also deeply grateful for your efforts to make ATC free to the public. I will be buying another copy because of it so I can have it unmolested (and because I loaned out my original edition and then moved).
Probably because the roller will wear down same on the Lie Nielsen. But I think that only happens when one presses down on the roller too hard when sharpening or fail to clean and it seizes up.
Thank you so much! That’s what I was hoping.
Howdy y’all! I’ve been collecting hand tools, and they’ve outgrown the cheap trunk I’ve been keeping them in so I’m building the boarded tool chest in the ADB. I’m using reclaimed wood from our house that’s at least 120 years old. Is there anything I should be aware of or concerned with when using old wood? I’m going to have to do some glue ups to make wide enough panels.
Hi All! This is for you as well as the community.
I have just stumbled into George Nakashima. Until last night, had never heard of him. I love the piece I was able to touch last night!
Are there any good biographies and/or studies of his work and philosophy you can recommend?
Thanks!
His book “The Soul of a Tree” is canon.
Mira Nakashima carries on her father’s work in the same workshop.
https://nakashimawoodworkers.com/
And they have a new book out on their process, which I just now bought.
Fantastic! Thank you!
The soul of a tree
Arm stick question- in the picture of Chris’s first Welsh stick chair, how does the first arm stick (curved) attach to the arm? I couldn’t see a tenon coming through the arm… thank you.
A screw through the stick and into the underside of the arm.
Hey Chris, I grew up watching my father and grandfather have good success in the metalworking business. I spent a few years at the “American college of building arts” in Charleston SC building my woodworking trade. Looking to start my own business now. In your experience, what is the best way to get work, and do you find certain items sell better than others?….or am I just stupid for even trying? 🙂
I went about it in a weird way. I had a full time job and took furniture jobs on the side. Most of those I got by networking. I found a Morris chair design that had been built in Cincinnati. So I built a few. Went to my spouse’s work parties. When asked what I did, I showed them the chair, talked about its history etc. Sold a bunch of chairs that way.
After that, word gets around. It took about 10 years, but I went full-time for myself in 2011. At first I got a lot of work from references from other woodworkers who didn’t have enough capacity. I then focused on a form of furniture that other people didn’t – campaign furniture. Soon, I had years of work ahead of me.
In 2019, I stopped taking commissions and now do spec work only. And it’s great.
If I were going to do it all over again, I’d probably go the more traditional route: Work for a woodworker you admire. Get really good. Then go out on your own. If you do it right, you won’t piss anyone off and you’ll have a good running start – and a reputation in the city.
There are 100 ways to do it. And just as many ways to fail.
Just don’t go into debt or get employees until …. you absolutely have to.
Good luck!
Thanks Chris! More info than I was expecting and extremely inspiring/helpful.
How did the IKEA cabinets go? I may be in need of some storage solutions soon and would like to use LAP as guinea pigs.
Love them. Cheap. Wood. Done.
Where would you look for pictures of book shelf designs? This question reminds me of the time you said “I am really into book shelves”.
Thank you!
I love the new Substacks. Way more unfiltered LAP. I am excited for the next middle finger and will be shocked, outraged and appalled you did that.
There are some books from Popular Woodworking and Taunton on shelving that can teach you the mechanics (loads, different kids of cases, how to make them built-in). Stuff like that. They are widely available at the library.
Also, Bill Hylton’s “Illustrated Cabinetmaking” is a great reference.
Then decide: What kind of style do I want to build in? Then look for websites that focus on that style – Arts & Crafts, MCM, Shaker, Art Noveau, etc. You will soon have endless ideas. And know the variety of techniques you can use to execute them.
I’m glad to hear that the book is coming along well.
I have a question about draw boring pins. I’ve done draw boring without them, but now that I have a pair, I’m not sure how to put them to use.
Thank you for being you!
Follansbee uses a much larger offset than you can get away with without using the pins – a drawbore pin in one hole pulls things together as you drive the first pin/peg – then you can drive the second, as the first peg/pin will hold it.
The pins do two things:
Insert them into the joint through the bores to see if the shoulder pulls up tight.
Press them intot eh joint a bit so they deform the bore through the tenon. The deformation makes the peg go in easier.
I’m building my first (hopefully only?) ATC. I have to glue up a few boards to make the main lid panel. After flattening it’ll be close to 7/8ths thick. Is there any value in doing T&G in this glue up or should I just edge joint it and be done with it?
Edge joint and be done.
I would put tongues facing up and grooves facing down.
I work in a small shop with handtools. A planer and bandsaw are on my shortlist. I also need a bench upgrade and was thinking of a 72-80 inch Anarchist workbench. The problem is going to be planing the board face before running it through the planer. The Anarchist Workbench mentions this could be done by hand or by picking up a jointer. I didn’t have much success handplaning long boards on my previous bench (although I didn’t use a planer). Do you have any tips? And if I should get a jointer, which I’m not adverse to because I think I would do a lot more woodwork if I could reduce the time dimensioning stock, would you recommend a benchtop jointer or looking for a used 6- or 8-inch jointer?
You have to follow your heart here. When I am face-planing boards to get them through the planer, it is NOT a precision operation. Find the high spots and remove them quickly with a jack. Then run it through the planer with the handplaned surface down. Flip the board over and plane it to thickness. You are not trying to make a glue surface – just get the big high spots gone.
I love my jointer, because we run hundreds of board feet over it every month. It pays the bills. I had a 6″, 8″ and now a 12″. Whatever you buy, buy quality and buy once.
Wouldn’t the groove collect water if the tongues are down?
Love the weekly Q&A, thank you both for your time and knowledge.
Lee Valley has a nice one.
https://www.leevalley.com/en-ca/shop/tools/hand-tools/marking-and-measuring/compasses-and-trammels/110169-bench-compass?item=05N2301
OMG, thank you for the link to the Nakashima site.
Hmmm…think horizontal wall siding, the tongue should be on the top long edge of the board, and the groove on the bottom long edge to prevent the groove form collecting water.
Blog tech problem. Twice today I’ve hit the reply buttom on a comment written earlier and my comment shows up at the end of the list, nowhere near the message I’ve replied to, preventing context to my comment.
Will report it to our Blog Masters.
Please share what you find out, I can’t imagine why you shouldn’t use diamond stones.
On the Latane hacking knife, is the edge hard (like file-hard or not) and how sharp do you try to keep it (like a honed knife or a quickly filed edge on a froe)?
It’s chisel-hard and chisel-sharp. And I try to keep it that way. Probably doesn’t need to be that sharp, but…..
Adam,
There’s a little bit of slop in the way the fence attaches to the slider. The trick is to elimate the slop when you put the fence on. When I first put the fence on the slide mechanism I twist the fence counterclockwise (or clockwise if you like, as long as you’re consistent) and tighten tne bolts in front and behind the fence, then align the fence to the blade and tighten the left and right bolts that lock the fence assembly in place. Then whenever you need to replace the fence after removing it, slide the fence back on to the slider and twist it counterclockwise (or clockwise if that’s what you did originally) to remove the slop and tighten the bolts.
I seldom have to recalibrate using this process.
Cliff
Chris,
A few weeks ago someone mentioned getting a scorp from ForgedCraftTools in Ukraine on Etsy. I checked them out and purchased a blacksmith forged scorp like the one you have recommended where the blade has a wide flat curve on the bottom rather than the circular blade most scorps have. Cost was only around $60 including shipping. It took a little less than a month to arrive and it looks good. They also offer the more traditional round scorp along with other items. Worth checking out.
Cliff
Hi Cliff,
I ordered one to check it out, too. It’s too dang tall to be useful for chairs. I plan to reach out and see what application the tool is supposed to be used for. Because saddling a seat with that would be difficult at best.
How can one tell what number a file is? I was sharpening a bit with my smallest bhaco and found it too large for the job. I want to order a smaller file but I have lost track of the # of my smallest file and can’t discern what I should buy… It’s impractical for me to visit a store in person but I will eventually get around to it if I must.
Thanks!
PS I looked around on Bhaco’s site and couldn’t find any guide to the number they stamp on the handle…
I might be an idiot here, but I believe its number is its length from toe to tang….. If I’m wrong, please someone correct me.
Chris, you probably have already answered this before, but in building that Roubo bench for the video you made with Will (in 2017?), you made the tenons on the stretchers 1 1/8″ but in the cut list on the scale drawings, the red oak stretchers are only to be 1 1/2″ thick. The stretchers in the video look to be about 2″ thick, maybe a bit more. (Their thickness wasn’t stated in the video, not that I heard.) With 1 1/8″ stretchers, how thick would you make the single-shouldered (“nekkid”, in your terminology) tenons? About half the thickness? (So about 5/8″ or 1/2″?) I’m building the bench now, all with Southern red oak. Ya’ll are the best for taking all these questions.
Whoops, I meant with 1 1/2″ stretchers, not 1 1/8″. So I assume the single-shouldered tenons should be about 3/4″ thick, half the thickness of the stretcher.
Yeah, about half the thickness will do fine for those tenons. Sorry if it was confusing.
I am building a play kitchen very similar to this one on Etsy (link at bottom) except my vertical members are Douglas Fir 4x4s and horizontal members are 2×4 (ripped down SYP 2×12, Red Oak, whatever scraps I have on hand). Frame is done. All joints are draw-bored M&T. Back slats and tops (upper and lower) for me are African Mahogany, which is finished with Osmo decking oil. Everything else is going to be painted with blue linseed oil paint. Feels like something Mattias would do!
My question: How would you attach that upper top? I could screw it but wonder if that would screw up the look I’ve got going so far. Would nailing down into the post’s end grain work? Could I use Rivierre nails? Any tips on protecting heads from rust?
This piece will live outside and will be abused by my 3 kiddos. It’s going to have working faucet and sink (not the dinky plastic tub thing) so it’s going to get wet.
https://www.etsy.com/listing/1166654633/hand-made-wood-play-kitchen-montessori?gpla=1&gao=1&&utm_source=google&utm_medium=cpc&utm_campaign=shopping_us_-toys_and_games&utm_custom1=_k_CjwKCAjwo6GyBhBwEiwAzQTmc0cqsQFu5ngdfZHQtaOUo8r7_ml_sQek2xhzhoajqoJK8uZrd7BpLRoC3hEQAvD_BwE_k_&utm_content=go_12665398257_121762925993_511610210343_pla-314535279060_c__1166654633_473756086&utm_custom2=12665398257&gad_source=1&gclid=CjwKCAjwo6GyBhBwEiwAzQTmc0cqsQFu5ngdfZHQtaOUo8r7_ml_sQek2xhzhoajqoJK8uZrd7BpLRoC3hEQAvD_BwE
What? Me? Am I Blue?
On a (slightly) more serious note, if you want to nail it on, you could perhaps try rose head copper nails as sold for boat building? While obvisouly softer than a steel nail (and thus more likely to bend if hammered askew), they are square shanked and so should hold pretty well, and will not rust. Ot there are bronze nails …
Lots of options.
Pocket screws from below: This has been used since the 1700s, and you can ream out the screw holes to allow wood movement.
Table buttons (wood or metal): Also very traditional and used for centuries. The slots in the rails allow wood movement.
Nail from above: Also seen a lot in vernacular work. As others have mentioned, bronze nails would be ideal.
Screwing from the top…. wouldn’t do it.
Chris, thanks for the great write up on which dust extractor you use as well as the other pieces to the sanding puzzle. I use my planes as long as the wood cooperates, but as we all know that does not always happen, so the sand paper must come out. I got the small festool dust extractor you suggested and hooked it to my bosch orbital sander. It was so amazing to use a high end extractor that is far less noisy than my shop vac and there was absolutely no dust to speak of. Thanks again!
Glad to hear it. Thanks!
And, I forgot to say, bronze screws as well, if you are looking for weather resistant fasteners.